微裂纹增韧机理
陶瓷增韧机理
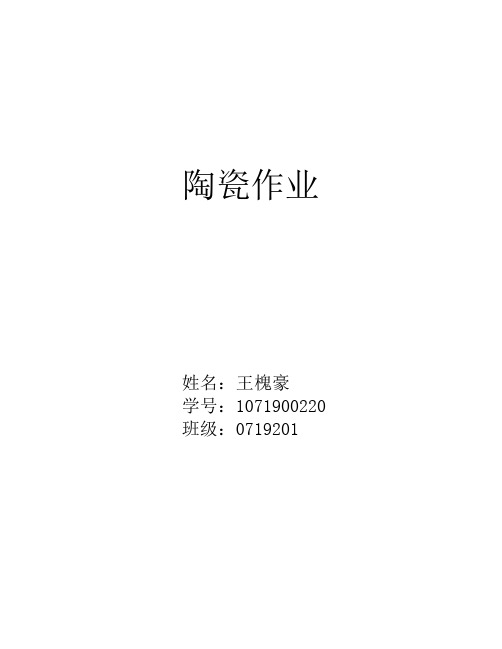
陶瓷作业姓名:王槐豪学号:1071900220 班级:0719201陶瓷韧化机理陶瓷最致命缺点是脆性,低可靠性和低重复性,这些不足严重影响陶瓷材料的应用范围。
只有改善陶瓷的断裂韧性,提高其可靠性和使用寿命,才能是陶瓷真正成为一种广泛应用的新型材料,因此陶瓷增韧技术一直是陶瓷研究的热点。
陶瓷的断裂主要是由于裂纹扩展导致的,阻止间断裂纹的扩展的方法有三种。
其一为分散裂纹尖端应力;其二为消耗裂纹扩展的能量,增大裂纹扩展所需克服的能垒;最后问转换裂纹扩展的能量。
相变韧化受相变诱发塑性钢,即TRIP (transformation induced plasticity)钢的启发,将ZrO 2 t →m 相变M s 点稳定到比室温稍低,而M d 点比室温高,使其在承载时由应力诱发产生t →m 相变,由于相变产生的体积膨胀效应和形状效应,而吸收大量的能量,从而表现出异常高的韧性。
这就是相变韧化(transformation toughening )的概念。
韧化机理分析: 1.相变韧化(∆K ICT ) ;d i <d<d c 应力诱发相变增韧(∆K ICT ) t →m 相变产生新的表面吸收能量 , 同时相变引起的体积膨胀产生压力。
2. 残余应力增韧 (∆K ICS );• 残余应力→ 闭合阻碍裂纹扩展 →残余应力韧化。
3. 显微裂纹增韧 (∆K ICM );4. 复合韧化机理;第二相颗粒增韧第二相颗粒增韧,第二相增韧主要增韧机理为残余应力增韧、微裂纹增韧、裂纹偏转增韧、颗粒桥联增韧、延性颗粒增韧;增韧的主要影响因素为物理相容性和化学相容性(不生成有害化合物合适的界面结合强度 1. 应力场模型颗粒∆a=a p -a m ;∆T=T P -T R ;α-材料的热膨胀系数,10-6/K ; E -材料的弹性模量,GPa ; ν-材料的泊松比;m ,p 分别代表基体和第二相增强颗粒; T P -基体不产生塑性变形的最高温度,K T R -所讨论的状态下的温度,Kp pmm E E TP ννα2121-++∆⋅∆=基体 r -球形颗粒半径,mm ;R -基体中某点距离球心的距离,mm ∆a 的影响:∆a>0,σr >0,σt <0,环向裂纹(收敛型); ∆a <0,σr <0,σt >0,径向裂纹(发散型) ; ∆a =0 ,P=0 ,σ=0; r>r cr c -自发萌生裂纹的邻界第二相颗粒半径2. 临界第二相颗粒尺寸(r c ) 弹性应变能: 颗粒:基体系统 U S =U P +U m =2πkP 2r 3由U S ≥2γmp 得 ;2γmp -萌生单位面积裂纹所消耗的能量,J3. 残余应力增韧 (d<d C )∆a>0∆a>0☺裂纹停止 ☺裂纹穿过第二相颗粒☺裂纹沿颗粒与基体之间的界面扩展颗粒开裂表面能:γp =2πr 2γsp克服阻力做功: W 1=1/2πPr 2u 1W t =γp + W 1=2πr 2γsp +1/2πPr 2u 1界面开裂表面能:b =4πr 2γint克服阻力做功:W 2=1/3πPr 2u 2W i =γp + W 1=4πr 2γint +1/3πPr 2u 2u 1≈u 2≈2r εb =2⨯10-3r3)(Rr P r ⋅=σ3)(21Rr P t ⋅-=σ32)21(2r E P U P P P νπ-=32)1(rE P U mm m νπ+=p P m m E E k νν2121-++=312)2(-∝kP r c πint<1/2γSP∆a≈0E P>E m 裂纹沿界面扩展。
弹性增韧机理2011

弹性增韧机理(1) 多重银纹理论Bucknall等人发展了Mertz等人的微裂纹理论,提出了多重银纹理论。
该理论认为,在橡胶增韧塑料体系中,橡胶相颗粒起着应力集中点的作用。
当材料受到冲击时,在粒子的赤道线附近应力集中会引起小银纹的产生,当橡胶颗粒密集时,所产生的大量银纹间的应力场相互干扰,若生长的银纹前峰的应力集中低于临界值或银纹遇到另一橡胶颗粒时,则银纹终止,橡胶相粒子不仅能引发银纹而且能控制银纹。
结果表明,与纯聚合物中形成的少量大银纹相比,加入橡胶可诱发大量的小银纹,而扩展大量的小银纹比扩展少量的大银纹需要更多的能量,因而多重银纹的产生和发展可以显著地提高材料的冲击强度。
但目前人们对橡胶粒子是否能控制银纹生长,以及只有小尺寸银纹才对材料起增韧作用仍存在争论,且不能解释PVC拉伸过程中细颈的出现并未伴有应力发白现象。
(2) 剪切屈服理论Newman和Strella提出橡胶增韧作用源于基体剪切屈服的观点。
认为橡胶增韧聚合物体系在受外力作用时,作为应力集中点的分散相粒子周围的树脂相中产生三维张力,引起橡胶粒子的空洞化、橡胶粒子与基体的界面脱粘及基体银纹化等体积膨胀过程,降低了粒间基体的剪切屈服应力。
当粒间应力集中超过了基体平面应力状态下的剪切屈服应力时,基体产生与应力方向成450的剪切带。
随分散相粒间距离的减小,粒间应力场相互叠加,剪切屈服区迅速扩大。
该机理可以解释一些实验现象,但不能很好解释剪切屈服时常常伴随的应力发白现象。
(3)剪切屈服一银纹化理论七十年代,Bucknall等人的研究表明,细颈在增韧体系中既可引发银纹又可引发剪切带,同时橡胶粒子还可控制银纹的发展使其及时终止而不至于发展成破坏性裂纹。
银纹与剪切屈服所占的比例与基体的性质有关,基体韧性越高,剪切屈服所占比例越大,而形变速度增加时,则银纹所占比例提高[11]。
这一理论明确指出,银纹的产生不仅消耗大量的能量而且也是材料破坏的先导,橡胶粒子和剪切带的存在则阻碍和终止了银纹的发展,从而达到增韧的目的。
韧化途径

韧化的主要机理有应力诱导相变增韧,相变诱发微裂纹增韧,残余应力增韧等。
几种增韧机理并不互相排斥,但在不同条件下有一种或几种机理起主要作用。
相变增韧:利用多晶多相陶瓷中某些相成分在不同温度的相变,从而增韧的效果,统称为相变增韧。
例如,利用的马氏体相变来改善陶瓷材料的力学性能,是目前引人注目的研究领域。
研究了多种?的相变增韧,由四方相转变成单斜相,体积增大3% 5%,如部分稳定,四方多晶陶瓷(TZP), 增韧陶瓷(ZTA), 增韧莫来石陶瓷(ZTM), 增韧尖晶石陶瓷, 增韧钛酸铝陶瓷, 增韧陶瓷,增韧以及增韧等。
其中PSZ陶瓷较为成熟,TZP,ZTA,ZTM研究得也较多,PSZ,TZP,ZTA等的新裂韧性已达,有的高达,但温度升高时,相变增韧失效。
当部分稳定陶瓷烧结致密后,四方相颗粒弥散分布于其他陶瓷基体中(包括本身),冷却时亚稳四方相颗粒受到基体的抑制而处于压应力状态,这时基体沿颗粒连线方向也处于压应力状态。
材料在外力作用下所产生的裂纹尖端附近由于应力集中的作用,存在张应力场,从而减轻了对四方相颗粒的束缚,在应力的诱发作用下会发生向单斜相的转变并发生体积膨胀,相变和体积膨胀的过程除消耗能量外,还将在主裂纹作用区产生压应力,二者均阻止裂纹的扩展,只有增加外力做功才能使裂纹继续扩展,于是材料强度和新裂韧性大幅度提高。
因此,这种微结构会产生三种不同的增韧机理。
在氧化锆中具有亚稳态四方相的盘状沉淀的微粒,如图1-55所示。
首先,随着裂纹发展导致的应力增加。
会使四方结构的沉淀相通过马氏体相变转变为单斜结构,这一相变吸收了能量并导致体积膨胀产生张应力。
这种微区的形变在裂纹附近尤为明显。
其次,相变的粒子周围的应力场会吸收额外的能量,并形成许多微裂纹。
这些微结构的变化有效地降低了裂纹尖端附近的有效应力强度。
第三,由于沉淀颗粒对裂纹的阻滞作用和局域残余应力场的效应,会引起裂纹的偏转。
裂纹偏转又引起裂纹的表面积和有效表面能增加,从而增加材料的韧性。
ZrO2增韧机理

ZrO2增韧机制ZrO2增韧机制有许多种:应力诱导相变增韧、相变诱发微裂纹增韧、表面诱发强韧化和微裂纹弯曲及分岔增韧。
1)相变增韧ZrO2 颗粒弥散在其它陶瓷基体中,当基体对ZrO2颗粒有足够的压应力,而ZrO2的颗粒度又足够小,则其相变温度可降至室温以下,这样在室温时ZrO2 仍可以保持四方相。
当材料受到外应力时(张应力),基体对ZrO2 的压抑作用得到松弛,ZrO2 颗粒即发生四方相到单斜相的转变,有7%-9%的体积膨胀,从而导致压应力的产生,不仅抵消了外力形成的张应力,而且阻止了进一步的相变。
这就是ZrO2 的相变增韧。
2)微裂纹增韧部分稳定ZrO2 陶瓷在由四方相向单斜相转变,相变出现了体积膨胀而导致产生微裂纹。
这样由ZrO2 陶瓷在冷却过程中产生的相变诱发微裂纹,以及裂纹在扩展过程中在其尖端区域形成的应力诱发相变导致的微裂纹,都将起着分散主裂纹尖端能量的作用。
从而提高了断裂能,称为微裂纹增韧。
3)表面诱发强韧化表面强化增韧陶瓷材料的断裂往往是从表面拉应力超过断裂应力开始的。
由于ZrO2陶瓷烧结体表面存在基体的约束较少,t-ZrO2很容易转变为m-ZrO2 ,而内部的t-ZrO2由于受基体各方向压力保持亚稳定状态,因此表面的m-ZrO2比内部多,而转变产生的体积膨胀使材料表面产生参与的压应力,可以抵消一部分外加的拉应力,从而造成表面强化增韧。
4)微裂纹弯曲及分岔增韧第九章1.烧结:粉末或非致密性物料经加热到低于其熔点的一定范围内,发生颗粒粘结、结构致密性增加,晶粒长大,强度和化学稳定性提高等物理变化,成为坚实集合体的过程,其中无液相时为固相烧结,有少量液相时为液相烧结。
1.烧结与烧成烧成—包括物料的预热、脱水、分解、多相反应、熔融、溶解、烧结等多种物理和化学变化;烧结—仅指粉料经加热而致密化的简单物理过程,是烧成过程的一部分。
2.烧结与熔融相同点:都是在高温下原子热振动引起。
不同点:熔融通过质点迁移其间距增大,并且全部组元都处于液态;烧结时质点间距变小,且至少有一相是固相;3.烧结与固相反应相同点:二个过程开始进行的温度都远低于熔融温度,在Tamman温度开始,并且过程自始至终至少有一相是固态;不同点:固相反应是一化学反应过程,至少有二组元参加,并发生化学反应最后形成化合物;烧结是一物理过程,可以是单组元或二组元,组元间不发生化学反应。
高分子材料中增韧剂定义、机理及种类详解

高分子材料中增韧剂定义、机理及种类详解一、增韧剂定义增韧剂其实就是能增加胶黏剂膜层柔韧性的物质。
某些热固性树脂胶黏剂,如环氧树脂、酚醛树脂和不饱和聚酯树脂胶黏剂固化后伸长率低,脆性较大,当粘接部位承受外力时很容易产生裂纹,并迅速扩展,导致胶层开裂,不耐疲劳,不能作为结构粘接之用。
因此,必须设法降低脆性,增大韧性,提高承载强度。
凡能减低脆性,增加韧性,而又不影响胶黏剂其他主要性能的物质即为增韧剂。
增韧剂一般都含有活性基团,能与树脂发生化学反应,固化后不完全相容,有时还要分相,会获得较理想的增韧效果,使热变形温度不变或下降甚微,而抗冲击性能又明显改善。
一些低分子液体或称之为增塑剂之物加入树脂之中,虽然也能降低脆性,但刚性、强度、热变形温度却大幅度下降,不能满足结构粘接要求,因此,增塑剂与增韧剂是完全不同的。
二、增韧剂的种类可分为橡胶类增韧剂和热塑性弹性体类增韧剂。
橡胶类增韧剂:该类增韧剂的品种主要有液体聚硫橡胶、液体丙烯酸酯橡胶、液体聚丁二烯橡胶、丁腈橡胶、乙丙橡胶及丁苯橡胶等。
热塑性弹性体:热塑性弹性体是一类在常温下显示橡胶弹性、在高温下又能塑化成型的合成材料。
因此,这类聚合物兼有橡胶和热塑性塑料的特点,它既可以作为复合材料的增韧剂,又可以作为复合材料的基体材料。
这类材料主要包括聚氨酯类、苯乙烯类、聚烯烃类、聚酯类、间规1,2-聚丁二烯类和聚酰胺类等产品,目前作为复合材料的增韧剂用得较多的是苯乙烯类和聚烯烃类。
其它增韧剂:适用于复合材料的其它增韧剂还有低分子聚酰胺和低分子的非活性增韧剂,如苯二甲酸酯类。
对于非活性的增韧剂也可称为增塑剂,它不参与树脂的固化反应。
三、增韧机理不同类型的增韧剂,有着不同的增韧机理。
液体聚硫橡胶可与环氧树脂反应,引入一部分柔性链段,降低环氧树脂模量,提高了韧性,却牺牲了耐热性。
液体丁腈橡胶作为环氧树脂的增韧剂,室温固化时几乎无增韧效果,粘接强度反而下降;只有中高温固化体系,增韧与粘接效果较明显。
陶瓷材料的增韧机理

陶瓷材料的增韧机理引言:现代陶瓷材料具有耐高温、硬度高、耐磨损、而侵蚀及相对密度轻等许多优良的性能。
但它同时也具有致命的弱点,即脆性,这一弱点正是目前陶瓷材料的利用受到专门大限制的要紧缘故。
因此,陶瓷材料的强韧化问题便成了研究的一个重点问题。
陶瓷不具有像金属那样的塑性变形能力,在断裂进程中除产生新的断裂表面需要吸收表面能之外,几乎没有其它吸收能量的机制,这确实是陶瓷脆性的本质缘故。
人们通过量年尽力,已探讨出假设干韧化陶瓷的途径,包括纤维增韧、晶须增韧、相变增韧、颗粒增韧、纳米复合陶瓷增韧、自增韧陶瓷等。
这些增韧方式的实施,使陶瓷材料的韧性取得了较大的提高,使陶瓷材料在高温结构材料领域显示出强劲的竞争潜力。
增韧原理:1.1纤维增韧为了提高复合材料的韧性,必需尽可能提高材料断裂时消耗的能量。
任何固体材料在载荷作用下(静态或冲击),吸收能量的方式无非是两种:材料变形和形成新的表面。
关于脆性基体和纤维来讲,许诺的变形很小,因此变形吸收的断裂能也很少。
为了提高这种材料的吸能,只能是增加断裂表面,即增加裂纹的扩展途径。
纤维的引入不仅提高了陶瓷材料的韧性,更重要的是使陶瓷材料的断裂行为发生了全然性转变,由原先的脆性断裂变成了非脆性断裂。
纤维增强陶瓷基复合材料的增韧机制包括基体预紧缩应力、裂纹扩展受阻、纤维拔出、纤维桥联、裂纹。
晶须增韧陶瓷晶须是具有必然长径比且缺点很少的陶瓷小单晶,因此具有很高的强度,是一种超级理想的陶瓷基复合材料的增韧增强体[8]。
陶瓷晶须目前经常使用的有SiC晶须,Si3N4晶须和Al2O3晶须。
基体经常使用的有ZrO2,Si3N4,SiO2,Al2O3和莫来石等。
采纳30%(体积分数)B2SiC晶须增强莫来石,在SPS烧结条件下材料强度比热压高10%左右,为570MPa,断裂韧性为415MPa#m1/2,比纯莫来石提高100%以上。
王双喜等[10]研究发觉,在2%(摩尔分数)Y2O32超细料中加入30%(体积分数)的SiC晶须,能够细化2Y2ZrO2材料的晶粒,而且使材料的断裂方式由沿晶断裂为主变成穿晶断裂为主的混合断裂,从而显著提高了复合材料的刚度和韧性。
增韧原理
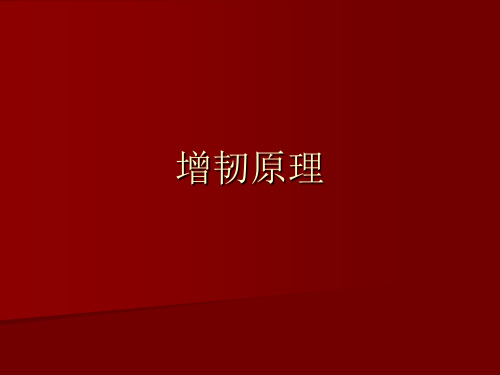
●纤维的拔出(Debonding) 纤维的拔出(Debonding)
每根纤维的脱粘能量∆Q p为:
因此,纤维体积比大、l c大(即界面强度 弱,因l c与界面应力成反比),通过纤维 脱粘达到的增韧效果最大。
●纤维拔出(Pull 纤维拔出(Pull
– out) out)
纤维首先脱粘才能拔出。纤维拔出会使裂纹尖 端应力松弛,从而减缓了裂纹的扩展。纤维拔 出需外力做功,因此起到增韧作用
增强体的长径比越大,裂纹偏转增韧效果就越好 增强体的长径比越大,
●层状结构增韧
裂纹扩展路径的改变, 裂纹扩展路径的改变, 可以明显的增加材料的韧性, 可以明显的增加材料的韧性, 但对于脆性材料的陶瓷, 但对于脆性材料的陶瓷,效果 仍不理想。人们发现, 仍不理想。人们发现,同样为 陶瓷材料的贝壳(羟基磷灰石) 陶瓷材料的贝壳(羟基磷灰石) 具有较为理想的韧性, 具有较为理想的韧性,其结构 为层状。受这种结构的启发, 为层状。受这种结构的启发, 在复合材料结构设计中, 在复合材料结构设计中,将材 料制备成层状, 料制备成层状,每层厚度达微 米级,目前已有的为亚微米, 米级,目前已有的为亚微米, 材料的韧性有了明显的提高。 材料的韧性有了明显的提高。
裂纹弯曲裂纹弯曲crackbowingcrackbowing和偏转在颗粒和短纤维晶须增强复合材料起到使裂纹中裂纹扩展在颗粒和短纤维晶须增强复合材料起到使裂纹中裂纹扩展时会发生偏转从而增加复合材料时会发生偏转从而增加复合材料mmc复合材料复合材料cmccmc中预先存在有微裂纹则这些微裂纹同样起到引中预先存在有微裂纹则这些微裂纹同样起到引导裂纹发生偏转的作用从而增加复合材料的韧性
●纤维桥接(Fiber 纤维桥接(Fiber
Bridge) Bridge)
纤维混凝土增强机理分析

纤维混凝土增强机理分析摘要:钢纤维是一种新型的水泥基复合材料,其抗拉,抗剪,抗弯能力优于普通的混凝土。
因而被广泛应用与工程中。
本文从抑制原始裂缝的发展和阻止微裂缝发展两个方向对钢纤维混凝土的增强原理进行了详细的阐述,得出部分结果可为工程实践提供参考。
关键词:钢纤维混凝土;增强;微裂缝;强度1 引言钢纤维增强混凝土(steel fiber reinforced concrete,SFRC)又简称为钢纤维混凝土,是以水泥浆、砂浆或混凝土为基材,以钢纤维为增强材料组成的一种复合材料。
水泥石、砂浆和混凝土的主要缺点是抗拉强度低、极限延伸率小、性脆,掺加抗拉强度高、极限延伸率大、抗碱性好的钢纤维可以克服上述缺点。
钢纤维混凝土虽然问世时间不久,但应用领域越来越广泛。
在国外钢纤维混凝土被广泛应用于公路路面、桥面、码头铺面、机场道面、刚性防水屋面、工业建筑地面、地下室刚性防水、框架节点等领域。
在我国,钢纤维混凝土的研究和应用开始于20世纪70年代,近20多年,发展非常迅速。
相应规范的颁布和实施进一步推动钢纤维混凝土在我国工程建设领域的应用。
2 钢纤维混凝土工作机理及影响因素2.1 工作机理钢纤维混凝土的工作机理与一般的复合材料机理相似。
在混凝土中掺入适量的高性能钢纤维后,水泥砂浆作为主要的胶凝材料,在包裹住砂,石等骨料的同时,握裹住大量的钢纤维。
钢纤维相互搭接形成大量散乱分布的网状结构,衬托了骨料,减小了骨料的离析和水分的沁出,提高了混凝土的粘结性与保水性,从某种程度上太高了混凝土的抗拉强度和韧性。
试验研究表明,当钢纤维的体积率为1-2%之间时,钢纤维混凝土抗拉强度和抗弯强度较普通混凝土的强度提高了40-80%,抗剪强度提高了50%以上,但对抗压强度提高幅度不大。
2.2 影响钢纤维混凝土的因素大量的试验研究表明,影响钢纤维混凝土强度的因素主要有以下几种:1混凝土材料强度2钢纤维材料本身性质3 钢纤维混凝土的施工方法。
- 1、下载文档前请自行甄别文档内容的完整性,平台不提供额外的编辑、内容补充、找答案等附加服务。
- 2、"仅部分预览"的文档,不可在线预览部分如存在完整性等问题,可反馈申请退款(可完整预览的文档不适用该条件!)。
- 3、如文档侵犯您的权益,请联系客服反馈,我们会尽快为您处理(人工客服工作时间:9:00-18:30)。
微裂纹增韧机理
引言:
在材料科学领域,增强材料的韧性一直是一个重要的研究方向。
微裂纹增韧机理是一种常用的方法,通过引入微小的裂纹来提高材料的韧性。
本文将介绍微裂纹增韧的基本原理和机制,并讨论其在材料设计中的应用。
一、微裂纹增韧的基本原理
微裂纹增韧是一种通过引入微小的裂纹来提高材料韧性的方法。
微裂纹通常是通过在材料中引入细小的裂纹来实现的,这些裂纹可以是自然裂纹,也可以是人工引入的。
当材料受到外力作用时,微裂纹将扩展并吸收部分应力能量,从而减缓裂纹的扩展速度。
由于微裂纹的存在,裂纹的扩展路径变得曲折,使材料更难断裂,从而提高了材料的韧性。
二、微裂纹增韧的机制
微裂纹增韧的机制主要包括拉伸桥式增韧、拉伸开口式增韧和剪切滑移式增韧三种。
1. 拉伸桥式增韧:
拉伸桥式增韧是一种通过拉伸桥的形成来增加材料的韧性的机制。
当材料中存在微裂纹时,应力场会导致裂纹周围的材料发生拉伸变形,形成拉伸桥。
拉伸桥的形成使得应力能够得到分散,并且增加
了裂纹扩展的阻力,从而提高了材料的韧性。
2. 拉伸开口式增韧:
拉伸开口式增韧是一种通过拉伸开口的形成来增加材料的韧性的机制。
当材料中存在微裂纹时,应力场会导致裂纹周围的材料发生拉伸变形,形成拉伸开口。
拉伸开口的形成使得应力能够得到分散,并且增加了裂纹扩展的阻力,从而提高了材料的韧性。
3. 剪切滑移式增韧:
剪切滑移式增韧是一种通过剪切滑移的形成来增加材料的韧性的机制。
当材料中存在微裂纹时,应力场会导致裂纹周围的材料发生剪切滑移,从而使裂纹的扩展路径变得曲折。
剪切滑移的形成增加了裂纹扩展的阻力,从而提高了材料的韧性。
三、微裂纹增韧的应用
微裂纹增韧机理在材料设计中有着广泛的应用。
通过合理设计材料的微裂纹形态和分布,可以显著提高材料的韧性,使其能够承受更大的外力而不断裂。
1. 金属材料的微裂纹增韧:
金属材料通常具有良好的延展性,但其韧性在低温下会明显下降。
通过在金属材料中引入微裂纹,可以有效提高其低温韧性,增强其抗断裂能力。
微裂纹增韧在航空航天、核能等领域有着广泛的应用。
2. 高分子材料的微裂纹增韧:
高分子材料通常具有较好的韧性,但其刚性较差。
通过在高分子材料中引入微裂纹,可以提高其刚性并改善其力学性能。
微裂纹增韧在塑料、橡胶等领域有着广泛的应用。
3. 复合材料的微裂纹增韧:
复合材料由不同的材料组成,具有优良的力学性能。
通过在复合材料中引入微裂纹,可以进一步提高其韧性,增加其抗断裂能力。
微裂纹增韧在航空航天、汽车制造等领域有着广泛的应用。
结论:
微裂纹增韧是一种通过引入微小的裂纹来提高材料韧性的方法。
其机制包括拉伸桥式增韧、拉伸开口式增韧和剪切滑移式增韧三种。
微裂纹增韧在金属材料、高分子材料和复合材料中都有着广泛的应用。
通过合理设计材料的微裂纹形态和分布,可以显著提高材料的韧性,使其具有更好的抗断裂能力。
未来,随着科学技术的不断进步,微裂纹增韧机理将在材料设计中发挥更重要的作用。