产品的检验与实验管理程序
产品检验流程管理规定

企业工厂在生产过程中,为了确保产品质量,就要进行品质检验,通过抽查或全检的
方式对产品质量进行检验。
不同的产品根据生产规格以及客户要求,对产品的检验规
格也不同。
品质检验亦称质量检验。
通过各种检验手段,包括感官检验、化学检验、仪器分析、
物理测试、微生物学检验等,进出口产品的品质、规格、等级等进行测试、鉴别。
其
目的就是判别、确定该产品的质量是否符合规定的产品质量条件。
品质检验的标准:
品质检验包括外观品质和内在品质的检验。
相关文章:品质质量管理关键在于提高人
的品质质量意识
外观品质检验指对产品外观尺寸、造型、结构、款式、表面色彩、表面精度、软硬度、光泽度、新鲜度、成熟度、气味等的检验。
外观质量检验主要是对商品的外形、结构、花样、色泽、气味、触感、疵点、表面加工质量、表面缺陷等的检验。
内在品质检验指对产品的化学组成、性质和等级等技术指标的品质检验。
内在质量检
验一般指有效成分的种类含量、有害物质的限量、商品的化学成分、物理性能、机械
性能、工艺质量、使用效果等的检验。
同一种商品根据不同的外形、尺寸、大小、造型、式样、定量、密度、包装类型等而有各种不同的规格。
品质检验的流程:
1.根据产品技术标准明确检验项目和各个项目质量要求;
2.规定适当的方法和手段,借助一般量具或使用机械、电子仪器设备等测定产品;
3.把测试得到的数据同标准和规定的质量要求相比较;
4.根据比较的结果,判断单个产品或批量产品是否合格;
5.记录所得到的数据,并把判定结果反馈给有关部门,以便促使其改进质量。
检验和试验控制程序
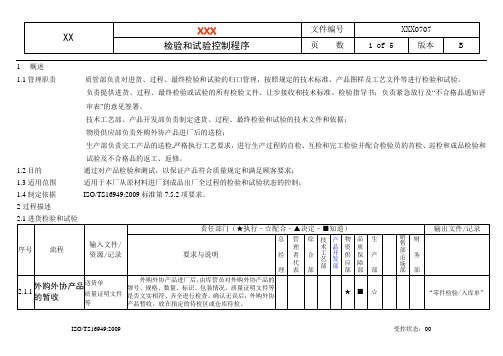
检验和试验控制程序页 数1 of 5版本B1 概述 1.1管理职责质管部负责对进货、过程、最终检验和试验的归口管理,按照规定的技术标准、产品图样及工艺文件等进行检验和试验。
负责提供进货、过程、最终检验或试验的所有检验文件、让步接收和技术标准、检验指导书;负责紧急放行及“不合格品通知评审表”的意见签署。
技术工艺部、产品开发部负责制定进货、过程、最终检验和试验的技术文件和依据; 物资供应部负责外购外协产品进厂后的送检;生产部负责完工产品的送检,严格执行工艺要求,进行生产过程的自检、互检和完工检验并配合检验员的首检、巡检和成品检验和试验及不合格品的返工、返修。
1.2目的 通过对产品检验和测试,以保证产品符合质量规定和满足顾客要求; 1.3适用范围 适用于本厂从原材料进厂到成品出厂全过程的检验和试验状态的控制; 1.4制定依据 ISO/TS16949:2009标准第7.5.2项要求。
2 过程描述 2.1进货检验和试验序号流程输入文件/ 资源/记录责任部门(★执行–☆配合–▲决定–■知道)输出文件/记录要求与说明 总经理管理者代表综合部技术工艺部产品开发部物资供应部品质保障部生产部销售部/市场部财务部2.1.1 外购外协产品的暂收送货单质量证明文件等 外购外协产品进厂后,由库管员对外购外协产品的牌号、规格、数量、标识、包装情况、质量证明文件等是否文实相符、齐全进行检查。
确认无误后,外购外协产品暂收,放在指定的待检区或仓库待检。
★ ■ ☆“零件检验/入库单”检验和试验控制程序页数 2 of 5 版本 B序号流程输入文件/资源/记录责任部门(★执行–☆配合–▲决定–■知道)输出文件/记录要求与说明总经理管理者代表综合部技术工艺部产品开发部物资供应部品质保障部生产部销售部/市场部财务部2.1.2 送检 2.1.2.1库管员填写《零件检验/入库单》通知质检人员进行入厂检验和验证。
☆★“零件检验/入库单”2.1.3 检验进货报检单2.1.3.1检验员根据物料料号和规格,寻找对应的检验指导书,根据检验指导书规定的抽样计划、检验项目、技术要求、检验器具等要求和相关图纸、技术标准及检验文件进行检验或试验。
产品质量检验程序

产品质量检验程序在生产过程中,产品质量检验是确保产品符合质量标准的重要环节。
本文将介绍产品质量检验的程序,包括质量检验的目的、流程、方法和结果评估等方面。
一、质量检验的目的质量检验的主要目的是确保产品的合格率和可靠性。
通过检验,我们可以及时发现并纠正产品制造过程中的问题,提高产品质量,满足客户的需求和期望。
同时,质量检验也可以帮助企业降低成本、增强竞争力。
二、质量检验的流程质量检验的流程一般包括取样、测试、评估和记录等步骤。
1. 取样:根据检验标准和要求,从生产线上随机选取代表性样品。
2. 测试:对取样的产品进行相关的物理、化学、机械等测试,以评估其质量和性能。
3. 评估:根据测试结果和预设的质量标准,判断产品的合格性,并记录合格或不合格的结论。
4. 记录:将检验过程中的相关数据和结果进行记录,包括样品信息、检验结果、检验员等。
三、质量检验的方法产品质量检验可以采用各种方法和工具,下面介绍两种常用的方法:1. 外观检验:通过肉眼观察产品的外观,检查是否有瑕疵、变色、变形等表面缺陷。
2. 功能性检验:根据产品的设计要求,进行相应的功能测试,如电器产品的电流、电压测试,机械产品的运转试验等。
除了以上方法,还可以根据产品的特点和要求,采用其他专业的检验方法,如X射线检测、声波检测、拉力测试等。
四、质量检验结果评估在质量检验中,根据检验结果的合格与否,可以分为合格品和不合格品。
1. 合格品:符合质量标准和要求,可以正常出货或投入市场。
2. 不合格品:不符合质量标准和要求,需要进行相应的处理,如修复、重新制造或报废等。
对于不合格品,企业需要追溯其原因,采取相应的纠正措施,确保类似问题不再发生,并承担相应的责任。
五、质量检验的重要性质量检验在产品生产中具有重要的作用:1. 保证产品质量:通过检验,可以发现和排除产品生产过程中的缺陷和问题,确保产品的质量稳定和一致性。
2. 提高客户满意度:优质的产品可以满足客户的需求和期望,提高客户对企业的信任和满意度。
检验和试验控制程序
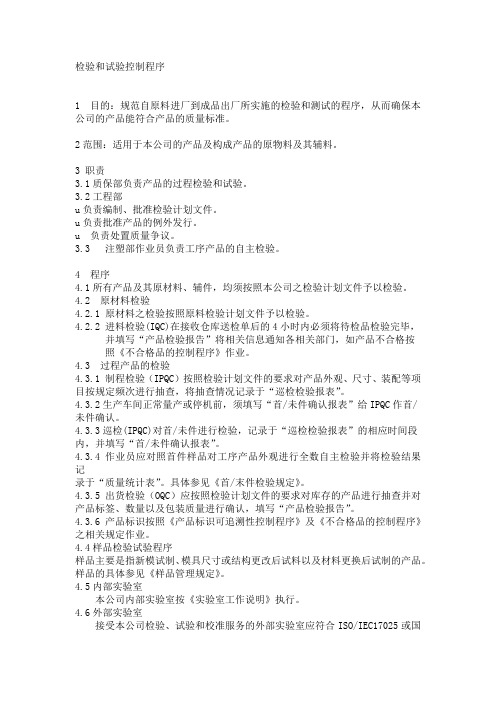
检验和试验控制程序1 目的:规范自原料进厂到成品出厂所实施的检验和测试的程序,从而确保本公司的产品能符合产品的质量标准。
2范围:适用于本公司的产品及构成产品的原物料及其辅料。
3 职责3.1质保部负责产品的过程检验和试验。
3.2工程部u负责编制、批准检验计划文件。
u负责批准产品的例外发行。
u 负责处置质量争议。
3.3 注塑部作业员负责工序产品的自主检验。
4 程序4.1所有产品及其原材料、辅件,均须按照本公司之检验计划文件予以检验。
4.2 原材料检验4.2.1 原材料之检验按照原料检验计划文件予以检验。
4.2.2 进料检验(IQC)在接收仓库送检单后的4小时内必须将待检品检验完毕,并填写“产品检验报告”将相关信息通知各相关部门,如产品不合格按照《不合格品的控制程序》作业。
4.3 过程产品的检验4.3.1 制程检验(IPQC)按照检验计划文件的要求对产品外观、尺寸、装配等项目按规定频次进行抽查,将抽查情况记录于“巡检检验报表”。
4.3.2生产车间正常量产或停机前,须填写“首/未件确认报表”给IPQC作首/ 未件确认。
4.3.3巡检(IPQC)对首/未件进行检验,记录于“巡检检验报表”的相应时间段内,并填写“首/未件确认报表”。
4.3.4作业员应对照首件样品对工序产品外观进行全数自主检验并将检验结果记录于“质量统计表”。
具体参见《首/末件检验规定》。
4.3.5出货检验(OQC)应按照检验计划文件的要求对库存的产品进行抽查并对产品标签、数量以及包装质量进行确认,填写“产品检验报告”。
4.3.6 产品标识按照《产品标识可追溯性控制程序》及《不合格品的控制程序》之相关规定作业。
4.4样品检验试验程序样品主要是指新模试制、模具尺寸或结构更改后试料以及材料更换后试制的产品。
样品的具体参见《样品管理规定》。
4.5内部实验室本公司内部实验室按《实验室工作说明》执行。
4.6外部实验室接受本公司检验、试验和校准服务的外部实验室应符合ISO/IEC17025或国家同等的认可的国家标准。
IATF16949产品检验和试验控制程序(含表格)

产品检验和试验控制程序(IATF16949/ISO9001-2015)1.0目的规范检验和试验,防止未经检验和试验及不合格的产品投入使用、加工和交付。
2.0适用范围适用于对产品的入库检验和试验、过程控制中的检验和试验及产品最终检验和试验。
3.0职责3.1 技质部是检验和试验的管理部门。
负责编制检验指导书,负责生产全过程的检验和试验,对产品的合格与否进行判断。
3.2 生产车间负责实施生产过程的自检、互检,保证不合格的产品不转序,并配合处理不合格品。
4.0管理程序4.1 进货验证(检验):4.1.1 采购回来的原材料、外协加工模具进厂后,由质检人员根据原材料技术要求或与供方签订的供货合同进行验证。
对原材料的验证结果记录在《进料检验报告》中。
4.1.2进货验证内容包括:a.供货方是否为合格供方;b.原材料供应商应提供该批供货产品的合格证明书,必要时要求提供检测数据和检验报告;c.外观检查,包括产品的包装量、数量、商标、品牌、规格型号;4.1.3验证合格后,方可入库或由生产车间投放生产。
如验证不合格,应通知采购人员联系处理。
4.2过程检验:过程检验分为首检、自检、巡检、工序完工检验4.2.1首(末)件检验4.2.1.1在如下情况时应进行首检,防止工序因素的变化导致成批的报废:a.每批加工的首件;b.调整或改进工艺后加工的首件;c.设备维修或工装更换维修后加工的首件;4.2.1.2首检由质检员进行,质检员应将检验合格的首件产品上作出标识,并保留到该批产品完工。
首件检验未经合格,不得继续加工或作业。
首件检验应填写《工序检验记录》。
4.2.2自检操作人员在正常生产时,应按规定的检查频次、检查项目对加工的产品进行自检,将有缺陷的不合格品挑出,与合格品分开放置,对发现的问题及时采取有效的纠正措施。
4.2.3巡回检验4.2.3.1正常情况下,质检员按关键工序抽检所有产品,发现问题,应尽快分析原因,及时指导作业者或联系有关人员加以纠正,问题严重时,应发出《纠正和预防措施处理单》,要求其改进。
GJB9001产品检验和试验控制程序
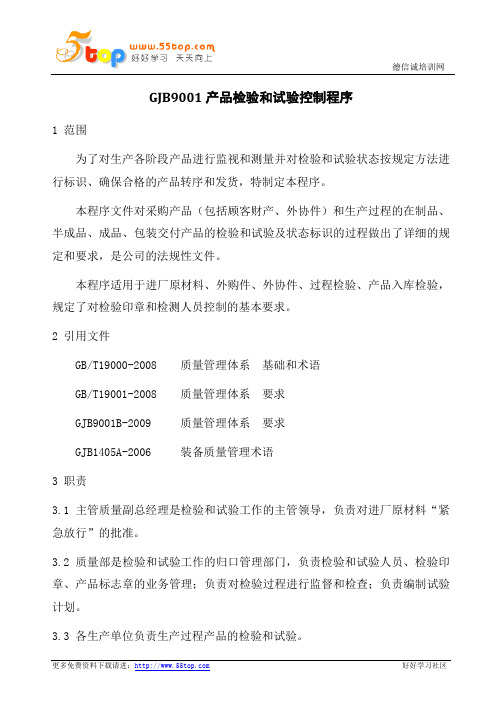
GJB9001产品检验和试验控制程序1 范围为了对生产各阶段产品进行监视和测量并对检验和试验状态按规定方法进行标识、确保合格的产品转序和发货,特制定本程序。
本程序文件对采购产品(包括顾客财产、外协件)和生产过程的在制品、半成品、成品、包装交付产品的检验和试验及状态标识的过程做出了详细的规定和要求,是公司的法规性文件。
本程序适用于进厂原材料、外购件、外协件、过程检验、产品入库检验,规定了对检验印章和检测人员控制的基本要求。
2 引用文件GB/T19000-2008 质量管理体系基础和术语GB/T19001-2008 质量管理体系要求GJB9001B-2009 质量管理体系要求GJB1405A-2006 装备质量管理术语3 职责3.1 主管质量副总经理是检验和试验工作的主管领导,负责对进厂原材料“紧急放行”的批准。
3.2 质量部是检验和试验工作的归口管理部门,负责检验和试验人员、检验印章、产品标志章的业务管理;负责对检验过程进行监督和检查;负责编制试验计划。
3.3 各生产单位负责生产过程产品的检验和试验。
3.4 人力资源部负责对检验和试验人员的培训。
3.5 检验员负责对原材料、外购件、外协件及半成品、成品进行检验,做出判定结论并办理质量证明文件。
当出现重大检验、试验质量事故时检验员有权越级上报主管领导。
3.6 测试人员、理化分析人员负责对原材料、外协件、外购件及生产过程的半成品、成品进行测试、理化分析,做出判定结论并办理质量证明文件。
3.7 检验技术员负责对检验员有争议的判定或误判进行确认或重新判定;负责重大质量问题上报有关领导。
4 控制要求4.1 工作流程4.2 控制要求4.2.1 检验人员、测试人员、理化分析人员,必须经过培训后持证上岗。
4.2.2 检验和试验使用的设备应处于受控状态。
详见《监视和测量设备控制程序》。
4.2.3 生产用的原材料、外协件、外购件、半成品及成品,未经检验或检验不合格不得投入使用(4.5.1.7除外)、转下道工序或交付顾客。
检定、校准检测物品的管理程序

检测和校准物品处置管理程序1 目的确保被检测/校准/检定物品对实验室的任何测量都不产生不利影响,并保证物品的完整性以及维护顾客与实验室的利益。
2 范围适应于本计量中心检测/校准/检定活动中的所有被检物品。
3 职责3.1 技术负责人批准与检测/校准/检定物品有关的意外事故处理意见。
3.2 班组负责人负责对检测/校准/检定物品的安全和保密管理进行监督;必要时对检测校准物品进行确认;组织编写本部门的检测/校准/检定物品标识作业指导书。
3.3 物品管理员负责对顾客提供产品的验证、登记;对检测/校准/检定物品编号和标识;按照顾客要求在符合条件的环境中保存检测和校准物品并记录;及时做好已检物品留样期后的处置工作和校准物品的归还工作。
3.4 检测/校准/检定人员负责在检测/校准/检定过程中对物品进行保管和保护。
4 程序4.1 物品的接收4.1.1 固定实验室的物品接收4.1.1.1 在接收顾客送检物品时,物品管理员应根据委托检测/校准/检定项目,对其是否符合检测/校准/检定要求进行检查,若无问题,请顾客填写实验室《任务委托单》。
4.1.1.2 若对顾客委托的物品是否适于检测/校准/检定有疑问时,应协助顾客填写实验室《检测/校准/检定任务委托单》。
4.1.1.3 物品管理员核对《任务委托单》上顾客填写的内容。
4.1.1.4 当顾客对物品及技术资料的贮存和保密性等有特殊要求时,物品管理员请顾客在《任务委托单》上注明详细要求,并按照顾客的要求对物品和资料进行处理。
4.1.1.5 一般情况下,《检验/校准任务委托单》一式三联,第一联交顾客留存,作为检测/校准/检定后领取报告和领回物品的凭据;第二联由物品管理员留存待查,作为委托任务的统计凭据;第三联作为任务指令随物品一起转交检测/校准/检定人员。
4.1.2 现场物品状态的确认对于在现场检测/校准/检定的物品,项目负责人到现场评估现场环境、检查初始状态是否满足检测条件,并填写《现场技术服务顾客物品状态确认表》相关栏目。
检验与试验管理程序

正常生产中,作业员按照《作业指导书》中的外观要求项目进行产品自检,合格的产品包装或转入下工序,下工序须对上工序生产品进行再检查(互检)。检查时发现的不良品放在指定的不良品箱内,并作好记录,若不良品连续发生,应立即报告班主管或经理处理。作业员将合格产品摆放于“待检区”内,不合格品由IPQC按《不合格品控制程序》进行处理。
5.2来料检验:
5.2.1仓库对采购物料的品名、规格、数量与送货单和订购单进行核对点收一致后,将物料放于待检区后,通知品管部IQC进行检验;
5.2.2 IQC检验员依据《IQC检验作业指导书》和相关检验规范进行检验,检验完后在贴于物料上的来料标识上做好相应的检验标识:原料合格品盖蓝色“IQC合格”印章,不合格品盖红色“IQC不合格”印章,并放于不合格区;来料检验不合格产品,按《不合格品控制程序》规定进行处理。IQC检验完成后须填写《IQC进料检验报告》及《IQC每日检查日报表》;
6.相关文件:
6.1《不合格品控制程序》;
6.2《生产过程控制程序》;
6.3《标识和可追溯性控制程序》;
7.质量记录:
7.1《IQC进料检验报告》;
7.2《IQC每日检查日报表》;
7.3《品管员巡检日报表》;
7.4《成品出货检验报告》;
7.5《首件确认单》;
8.流程图:
无
3.2生产部:负责产品的自检、合格品/不合格品的区分放置,以及合格品的入库;
3.3仓库:负责通知品管部IQC对来料产品进行检验,并根据检验结果进行分区放置和处理。
4.定义:
无
5.程序:
5.1计数型抽样接收准则:
所有计数型数据抽样计划的接收准则必须是零缺陷,所有其它情况的接收准则必须形成文件,顾客有需要时提供给顾客批准。
- 1、下载文档前请自行甄别文档内容的完整性,平台不提供额外的编辑、内容补充、找答案等附加服务。
- 2、"仅部分预览"的文档,不可在线预览部分如存在完整性等问题,可反馈申请退款(可完整预览的文档不适用该条件!)。
- 3、如文档侵犯您的权益,请联系客服反馈,我们会尽快为您处理(人工客服工作时间:9:00-18:30)。
1.0 目的
制订检验与试验管理程序,对产品生产的各个阶段进行检验和试验,确保产品满足规定的要求。
2.0 适用范围
适用于本公司原材料、半成品与成品检验与试验的控制。
3.0 引用文件及术语
3.1 GB/T 19001-2000《质量管理体系------要求》
3.2 GB/T 19000-2000《质量管理体系------基础与术语》
4.0定议
无
5.0 职责
5.1 品管部: a. QE负责制订原材料、制程半成品、成品的检验规范;
b. QC负责来料、制程、成品的检验与试验,各QC组长负责检验与试
验结果的确认与判定;
c. 品保及检测课课长或经理负责检验与试验状况的放行。
6.0 工作内容
6.1 进料检验与试验控制
6.1.1进料时由仓库人员点收原物料品名、规格、数量,无误后将物料放置待检
区,或挂上待检验标牌,并在ERP系统内录入《IQC检验报告》相关项目,
并打印出来通知品保课IQC进行检验及试验。
6.1.2 IQC根据WI-4100-011《进料检验管理办法》运作流程进行检验作业,检
验时参照WI-4100-004《抽样计划作业指导书》及WI-4100-XXX《XXX
类检验规范》进行检验,并将检验结果填写在《IQC检验报告》中,检
验结果需经品保课课长或经理审批。
6.1.3对品管部尚无条件检验的项目,如有必要:
6.1.3.1 可提交生产车间试用确认能否达到相关试用要求。
6.1.3.2 提交化验室试验或委外试验,具体要求根据WI-4100-024《物料试
验作业指导书》执行。
6.1.4检验和试验合格的物料在来料的外包装贴上“合格”标签或加盖“合格”
印章,通知仓库办理入库手续。
6.1.5检验和试验不合格的物料加盖“不合格”印章或贴上“不合格”标签,
按COP8.3-001《不合格品管理程序》处理。
6.1.6当本公司采购原物料需在供货商处验证时,需有本公司制定之检验文
件,或由供货商提供经本公司确认之检验文件作依据,并由IQC担当,
使用检验仪器须经校验合格,经检验合格之原物料须加盖“合格”印章
或贴上“合格”标签。
6.1.7免检物料管理:公司所购进物料有下列情形之一者,可列为免检:
a).组成产品的辅助材料,对产质量量不构成影响;
b).材料质量较稳定,有轻微不良可通过生产过程中全检分选的;
c).免检物料需由品保课填制WI-4100-014《免检物料一览表》,经品管部
经理及生产部经理会签同意后,呈管理者代表批准;
d).免检物料在生产过程中发现不合格按COP8.3-001《不合格品管理程序》
执行。
6.1.8因生产车间急需来不及完成检验放行材料时,填写《直领领料单》,并注
明原因,向品管部经理申请材料临时放行,获批准后放行该批材料。
IQC
需在该批材料上加贴“直领”标签,生产应会同PQC进行分选,对分选使用
之不合格品按COP8.3-001《不合格品管理程序》执行。
6.1.9 所有检验和试验后的物料都需要在ERP系统内进行审核。
6.2 制程检验与试验控制
6.2.1首件检验
6.2.1.1 车间批量生产加工前,需制作首件并自检合格,同时在计算机系
统内录入首件送检数据,然后打印交QC进行首件检验。
6.2.1.2 QC按照WI-4100-XXX《XXX产品检验规范》进行首件检验,并
将检验结果填写于《首件送检单》上反馈车间,同时需将检验结
果录入计算机系统内,并审核完成。
6.2.1.3 首件不合格时车间需对首件进行返工,直至首件确认合格后方可
批量生产。
6.2.2 制程巡检
6.2.2.1 正常生产时,车间PQC需不定时对车间重点工艺环节进行巡查
检验,并将检验结果填写在《PQC巡检日报表》中。
6.2.2.2 PQC巡查过程中发现问题应及时通知车间负责人,以便采取措
施改善;发现重大质量问题需交上级审批后,要求生产车间确定
对策进行改善,PQC需跟踪处理结果,并开具《PQC质量异常
处理单》。
6.2.3移料检验
6.2.3.1 各车间所有产品需转移到下工序加工时,必须在计算机系统内打
印出《工艺送检-移料单》交QC进行移料检验,QC按照检验规
范要求对配件进行检验,并将检验结果记录于《工艺送检-移料
单》中,不合格品不可流入下工序车间。
6.2.4 计件全检
6.2.4.1 根据产品加工特点,对于磨光车间的加工产品需进行计件全检,
全检结果QC应在磨光工序计件单上注明后反馈车间。
6.2.5 试验与安全测试
6.2.5.1 根据相关车间的产品要求及特点,需进行产品试验及安全测试.
a. 烤漆车间需进行甩油测试并作好记录,具体要求参照
WI-4100-032《甩油测试作业指导书》执行。
b. 包装车间需对产品进行100%的安全测试,具体测试项目包括
导通、极性、耐压、亮灯、接地等,并作好《生产线安全测
试记录表》,具体要求参照相应的作业指导书执行。
6.2.6 以上制程检验或试验具体执行流程及方法需依照WI-4100-033《制程检
验管理办法》或WI-4100-010《木制产品检验管理办法》、WI-4100-009
《包装车间制程检验管理办法》执行,发现不合格时需依照COP8.3-001
《不合格品管理程序》执行。
6.3 成品检验与试验控制
6.3.1成品送检必须在进货检验和试验、过程检验和试验均已经检验验收合格
后进行。
6.3.2 成品送检由包装车间在ERP系统内录入《成品送检单》,并打印出来通
知品保课OQC人员实施检验。
6.3.3 品保课OQC根据WI-4100-008《成品检验管理办法》运作流程进行检验
作业,检验时参照WI-4100-025《成品检验规范》进行检验,并将检验结
果填写在《OQC出货检验报告》中,检验结果需经QC组长确认,品保
课课长或品管部经理审核。
6.3.4生产批:原则上以一次入仓为一检验批﹔抽样方式按WI-4100-004《抽样
计划作业指导书》执行。
6.3.5除生产自行完成100%的例行检验外,货品出厂前品保课OQC也要对所
抽取之样办进行100%的功能与安全测试,并填写《耐压测试仪短路检测
记录表》。
6.3.6判定处理:
6.3.6.1 检验合格通知包装车间入仓,OQC则于纸箱外侧加盖QA PASS
章,并同时作好成品“合格”标识,在《成品送检单》上签名或
加盖“合格”印章,OQC要在计算机ERP系统内进行合格审核
入库;
6.3.6.2 不合格批:OQC在《成品送检单》签名并注明不合格结果或加盖
“不合格”印章,生产部按COP8.3-001《不合格品管理程序》实
施。
6.3.7 所有检验与试验完成后的成品都需要在ERP系统内进行审核。
6.4我司所有产品包括原材料、半成品、成品涉及法律法规要求时,各区域检验人
员必须参照相关法律法规标准(如3C、UL、ROHS等)进行检验。
对需供货商提
供的产品,其也需符合相关法律法规要求,同时供货商需提供第三方验证报告
给我司,我司将通过第三方验证报告进行验证。
7.0 支持性文件
WI-4100-011《进料检验管理办法》
WI-4100-XXX《XXX类检验规范》
WI-4100-004《抽样计划作业指导书》
WI-4100-024《物料试验作业指导书》
WI-4100-009《包装车间制程检验管理办法》
WI-4100-014《免检物料一览表》
WI-4100-032《甩油测试作业指导书》
WI-4100-010《木制产品检验管理办法》
WI-4100-033《制程检验管理办法》
WI-4100-008《成品检验管理办法》
WI-4100-025《成品检验规范》
COP8.3-001《不合格品管理程序》
8.0 质量记录
《IQC检验报告》
《首件送检单》
《工艺送检-移料单》
《PQC巡检日报表》
《PQC质量异常处理单》
《生产线安全测试记录表》
《耐压测试仪短路检测记录表》
《OQC出货检验报告》
《直领领料单》
《成品送检单》。