壳牌气化炉的现场组焊技术
壳牌煤气化炉的设备特性及技术管理探讨

壳牌煤气化炉的设备特性及技术管理探讨摘要:国家的发展离不开技术的应用及创新,壳牌煤气化炉技术的应用在我国社会发展中产生了极大的积极影响作用。
本文主要对壳牌煤气化炉当前的应用情况以及经常出现的问题进行阐述,着重说明激冷气压缩机、飞灰过滤器及煤粉输送系统的盘阀等关键设备的国产化,彻底改变了壳牌煤气化装置运行不稳定、运行周期短,设备损坏频繁等制约装置运行的问题。
关键词:壳牌煤气化炉;设备特性;技术管理探讨壳牌煤气化炉技术引入中国历时已久,在传统化工、发电、煤炭清洁高效利用相关生产活动得到了广泛应运,但在其发展过程中也面临着着诸多的考验与问题。
经过相关技术人员的消化吸收创新,特别是关键设备的国产化、工艺流程的优化创新让壳牌煤气化炉技术的发展有了新的征程,更加高效环保。
1壳牌煤气化的工艺发展历程壳牌煤气化的工艺较为复杂,其主要原理为:在加压以及高温作用下,将氧气和蒸汽混合在一起,与煤粉共同送入气化炉中,在很短时间内,这些混合成分温度剧升,其挥发成分将脱除出来,经过裂解、转化等化学反应。
因为气化炉具有很高的温度,只要存在一定的氧气,则碳物质和各种挥发、反应产物都会燃烧,当氧耗尽时,就开始发生物质转化的反应,也就是进入到气化的阶段,生成煤气,其主要成分是一氧化碳和氢气。
在上世纪五十年代开始,就出现了壳牌石化燃料的气化技术,当初的原料主要是渣油,这种工艺又称为SGP。
经过二十年的时间,在渣油作为主要气化原料的基础上,重新开发出一种新的原料,即粉煤。
这种技术叫做SCGP,这种技术从试行开始到投入商业生产,其技术开发历程有三十多年。
煤气化的技术最开始是从炼焦炉、水煤气炉和煤气的发生炉作为主要的煤气化设备,其原料主要是小粒煤或者是块状煤,经过了几十年时间,其发展逐渐向洁净煤气化的技术过渡,这种新的技术能够防止因为直接燃烧而排放污染物,该技术的反应器主要是气流床,其原料是干煤粉或者水煤浆,其生产规模巨大。
在这种新生产技术滋生出很多的煤气化工艺。
壳牌煤气化气化原理技术说明(翻译版)

壳牌煤气化气化原理技术说明(翻译版)目录气化原理 ............................................................................................................ 错误!未定义书签。
一、总论 (2)1.1 概述 (2)1.2 主要反应方程式 (2)1.3 环境方面 (3)2壳牌煤气化工艺(SCGP) (4)2.1 概述 (4)2.2 工艺步骤 (5)3煤的起源和煤的成分对煤气化工艺SCGP的影响 (13)3.1煤的起源 (13)3.2 与shell煤气化工艺相关的煤的特性 (13)3.3 煤/煤灰特性对操作和设计的影响 (15)一、总论1.1 概述气化是一种将碳氢原料转变为CO和H2为主要气体成分的工艺。
其它气体成分如CH4、CO2、H2S、苯酚、烟和微量的氨、HCl、HCN以及在特殊工艺下基于原料和工况产生的甲酸盐。
气化产出的气体既可作为发电用的燃料,又可作为化工原料。
对气化工艺的选择,以及气化介质(O2或空气),取决于气化进料的类型和产品的要求。
壳牌专利/操作两大气化技术1. 壳牌气化工艺(SGP)壳牌气化工艺(SGP)原料范围从天然气到重油。
此工艺合成出来的气体广泛用于H2、Cl2、甲醇的制造,或作为发电用的燃料。
自1956年来,壳牌气化工艺(SGP)技术被广泛应用,现已经有150套气化炉。
壳牌气化工艺(SGP)采用有耐火衬里的单个烧咀和一个特别设计的气管式废热锅炉(合成气冷却器SGC)。
2. 壳牌煤气化工艺(SCGP)壳牌煤气化工艺(SCGP)原料范围从焦油和无烟煤到褐煤。
间接煤液化(气化伴随着合成气接触反应的变换)是发展此工艺的最初原因。
现在,此工艺主要应用于发电和化工原料生产。
1972年,开始壳牌煤气化工艺(SCGP)的开发。
1976年阿姆斯特丹壳牌实验室委托一个工厂——GASCO化工厂烧煤6t/d;1978~1983年在德国汉堡壳牌总厂,一个烧煤150t/d的工厂投产;1986~1991年在美国壳牌Deer Park总厂,一个烧煤250-400st/d的示范厂投产。
壳牌煤气化技术介绍
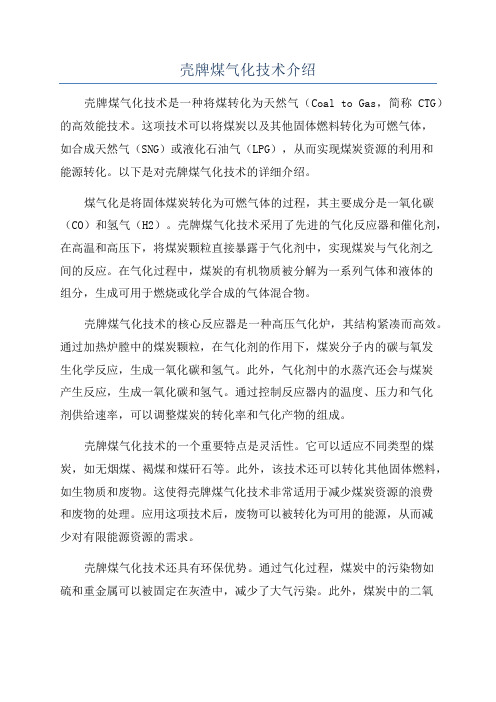
壳牌煤气化技术介绍壳牌煤气化技术是一种将煤转化为天然气(Coal to Gas,简称CTG)的高效能技术。
这项技术可以将煤炭以及其他固体燃料转化为可燃气体,如合成天然气(SNG)或液化石油气(LPG),从而实现煤炭资源的利用和能源转化。
以下是对壳牌煤气化技术的详细介绍。
煤气化是将固体煤炭转化为可燃气体的过程,其主要成分是一氧化碳(CO)和氢气(H2)。
壳牌煤气化技术采用了先进的气化反应器和催化剂,在高温和高压下,将煤炭颗粒直接暴露于气化剂中,实现煤炭与气化剂之间的反应。
在气化过程中,煤炭的有机物质被分解为一系列气体和液体的组分,生成可用于燃烧或化学合成的气体混合物。
壳牌煤气化技术的核心反应器是一种高压气化炉,其结构紧凑而高效。
通过加热炉膛中的煤炭颗粒,在气化剂的作用下,煤炭分子内的碳与氧发生化学反应,生成一氧化碳和氢气。
此外,气化剂中的水蒸汽还会与煤炭产生反应,生成一氧化碳和氢气。
通过控制反应器内的温度、压力和气化剂供给速率,可以调整煤炭的转化率和气化产物的组成。
壳牌煤气化技术的一个重要特点是灵活性。
它可以适应不同类型的煤炭,如无烟煤、褐煤和煤矸石等。
此外,该技术还可以转化其他固体燃料,如生物质和废物。
这使得壳牌煤气化技术非常适用于减少煤炭资源的浪费和废物的处理。
应用这项技术后,废物可以被转化为可用的能源,从而减少对有限能源资源的需求。
壳牌煤气化技术还具有环保优势。
通过气化过程,煤炭中的污染物如硫和重金属可以被固定在灰渣中,减少了大气污染。
此外,煤炭中的二氧化碳(CO2)也可以进行捕集和储存,减少了温室气体的排放。
这有助于应对气候变化和环境污染问题。
总结而言,壳牌煤气化技术是一项高效能、灵活性强、环保的能源转化技术。
它可以将煤炭和其他固体燃料转化为可燃气体,减少对有限能源的需求,并降低大气污染和温室气体排放。
这项技术在能源转型和可持续发展中具有重要作用,并将在未来得到广泛应用。
壳牌煤气化装置(SCGP)操作规程精品完整版

壳牌煤气化装置(SCGP)操作规程1、煤气化装置各岗位的岗位职责1.1 磨煤岗位本岗位的职责是将电厂燃料车间送来的碎煤贮存在碎煤仓V-1101A/B中,石灰石贮存在V-1102A/B中,两者混合配比加入到中速磨A-1101A/B中,〉在微负压和惰性气体条件下被磨粉干燥,干燥所需的热量由热风炉F-1101A/B中燃烧合成气或柴油提供,出来的煤粉要求直径范围0.005mm〈 D〈0.09mm,煤粉被输送到袋滤器S-1103A/B,之后送往低压粉仓V-1201A/B。
1.2 现场岗位本岗位的主要职责是做好现场巡查工作,,做好开车前后设备的运行、调试,让每件现场设备具备一次开车成功能力;在开车期间,协助中控岗位做好设备的运行监护,准确无误的做好数据记录,并对未运行设备进行维护、保养,使设备随时处于可备用状态。
(现场设备包括压缩机,汽包,破渣机,火炬系统,各种高低压泵等)。
1.3 分析岗位本岗位的职责是对煤气化工艺所需各种原料进行及时准确的分析,对正常生产中的气体,液体,固体进行取样分析,并把分析结果及时反馈给中控岗位,以协助中控岗位控制好整个煤气化装置的运行。
1.4 中控岗位本岗位的职责是维持磨煤系统(U-1100),煤给料系统(U-1200),气化系统(U-1300),除渣系统(U-1400),干法除尘系统(U-1500),湿法除尘系统(U-1600).初级水处理系统(U-1700)及公共系统(U-3000至3600)的正常运行,并协调与电厂燃料车间,氨厂净化车间,空分车间的生产关系。
磨煤系统(U-1100)的职责是与现场磨煤岗位的协调,将合格的粉煤送往煤给料系统。
煤给料系统(U-1200)由2套完全相同的锁斗加压系统组成,本系统的职责是将磨煤送来的粉煤经煤锁斗加压,再送往气化炉的四个煤烧嘴。
气化系统(U-1300)的职责是将加压后的粉煤以及氧蒸汽混合物通过2对相对的煤烧嘴送入气化炉,使粉煤和氧蒸汽混合物在一定条件发生反应,同时控制好炉内的温度,压力,出口合成气的温度及气化炉内的渣层厚度.并将产生的中压饱和蒸汽导入管网。
石化加热炉炉管焊接专项方案

加热炉炉管焊接专项方案1.焊前准备A.现场施焊的焊工必须具有相关部门颁发的与焊接材质相同的有效的焊工证件,并具有相应操作的合格项目。
对与本工程,焊工必须具有多年石化管道丰富焊接经验和焊接能力很强的焊工投入现场操作,从焊接技能上确保焊接质量。
B.焊件组对前应将坡口及其内外侧表面不小于20mm范围内的油、漆、垢、锈、毛刺等清除干净,且不得有裂夹层等缺陷,现场采用手工锂刀和磨光机机械清理。
管子或管件对接焊缝组对时,内壁应齐平,内壁错边量不宜超过管壁厚的10%,且不大于2mm。
C.焊接采用V型坡口,坡口用机械加工或砂轮机打磨,做到光滑平整.对坡口两侧20mm范围内将油污、铁锈和水份去除,且保证露出金属光泽。
采用多层焊,焊时应严格控制层间温度。
对于A335Pll和A335P22这两种材质,经过火焰切割的坡口表面,进行渗透检测,I级合格,检测范围为坡口及其两侧各20mm。
坡口加工尺寸可按图5进行。
图5炉管焊接坡口加工尺寸D.管子、管件组对时,应使内壁平齐,其错边量不应超过壁厚的10%,且不大于2mm。
2.焊接方法及焊材选择A.焊接方法炉管焊接采用氨弧焊打底结合手工电弧焊填充和盖面的方式。
定位管与炉底板和炉管的焊接采用电弧焊焊接,支撑板、加强版与炉壁和炉管的焊接也采用电弧焊焊接。
氮弧焊应采用锦鸨极,使用筑气纯度应在99.96%以上。
焊接应采用小线能量、短弧焊、小摆动的操作方法,采用多层多道焊,层间温度宜控制在200℃以上。
每层焊道完成后均应彻底清除焊道表面的熔渣,并消除各种表面缺陷再进行下一层焊接,每层焊道接头应错开。
焊接中应确保引弧与收弧处的质量,收弧应填满满弧坑,并用砂轮将收弧处修磨平整。
B.焊材选择具体采用的焊接材料选用见表2o2C.炉管焊接工艺参数F-5051炉管(20G)的焊接工艺参数见表3。
3F-5051F-5001(P22)炉管的焊接工艺参数见表4o4F-500F-7001(Pl1)炉管的焊接工艺参数见表5o5F-7()(H3.焊接材料的存储、烘干与发放A.焊接材料的储存、保管应符合下列规定:存放焊接材料的库房应通风良好,配有温、湿度计和去湿机,并有温、湿度记录,相对湿度要控制小于60%,温度控制以10—35C为宜;焊接材料应按照牌号、规格、批号分别堆放,与地面、墙面的距离在0.3米以上,并做好相应的标识,以便取出。
壳牌煤气化气化原理技术说明

壳牌煤气化气化原理技术说明壳牌公司是世界上最大的能源和化工企业之一,致力于研究和应用先进的技术来满足能源需求。
其煤气化技术是一项重要的能源转化技术,将煤炭等碳质原料转化为可燃气体,如合成气、液化石油气和水煤气,以提供清洁能源。
壳牌煤气化技术基于可持续发展的原则,通过控制和优化过程参数,最大程度地减少对环境的影响。
其核心原理是将煤炭与氧气或氧气和水蒸气混合在高温高压下,通过化学反应产生一种富含氢气和一氧化碳的气体,即合成气。
煤气化过程主要包括煤炭的干燥、预先处理、高温气化和气体净化四个步骤。
首先,煤炭被干燥以去除其中的水分。
然后,煤炭经过预处理,如粉碎和研磨,以增加其表面积,提高反应效率。
接下来,煤炭在高温(超过1000℃)高压(10-40兆帕)的条件下与氧气或氧气和水蒸气反应。
这个过程被称为气化反应,产生的气体主要包括一氧化碳(CO)、二氧化碳(CO2)、氢气(H2)和甲烷(CH4)。
最后,通过气体净化技术,如脱硫、脱碳和脱氯等,去除气体中的杂质,以获得高纯度的合成气。
壳牌煤气化技术的优势在于其高效率和灵活性。
它可以利用各种不同种类和质量的煤炭作为原料,并且可以灵活地调节反应条件以适应不同的工艺要求。
此外,壳牌煤气化技术还可以实现废弃物和生物质的气化,有效利用资源,并减少环境的污染。
在煤气化产生的气体中,合成气是最常见和重要的产品。
合成气可进一步转化为多种化工产品和能源。
例如,通过催化剂的作用,合成气可以转化为液化石油气,用于取代传统的天然气和液化石油气。
此外,合成气还可以通过催化反应转化为甲醇、氨和液体燃料等有机化合物,用于化工生产和能源供应。
壳牌煤气化技术的应用非常广泛。
它可以用于化工、能源和环保等领域。
在化工领域,煤气化技术可以产生丰富的化学原料,用于合成塑料、纤维和精细化学品等。
在能源领域,煤气化技术可以生产清洁能源,如液化石油气和合成燃料等。
在环保领域,煤气化技术可以减少传统能源的使用和环境污染。
炉壳焊接要求
炉壳焊接热风炉炉皮焊接的关键是高温区段的焊接,要点是防止近缝区的应力腐蚀裂纹的产生。
当壳体的焊接残余应力较大时,由于生产过程中聚集在高温区段的硫化氢等腐蚀性气体的浸润,会使近缝区产生细小的应力腐蚀裂纹,这种晶间腐蚀型的龟裂裂纹常常会随着应力的大小而扩展,严重影响了热风炉的正常工作与使用寿命。
作为炉皮制作的壳体分瓣热压成型后,制作方在出厂前进行整体消除应力退火。
而施工方现场安装焊接的要点是采取正确的焊接方法和合理的焊接顺序,确保焊接质量并要强调焊缝表面的质量,以及焊后消除或减缓焊缝区的焊接残余应力,这些都是防止高温区段壳体内近缝区产生应力腐蚀裂纹的有效措施。
能够确保热风炉良好的使用性能和寿命。
(1) 焊接方案1)方案的原则:①能在结构制造厂车间内焊接的尽量在有良好工作环境的车间内焊接,能在地面上焊接的构件尽量不上高空。
②能在地面上进行焊缝退火处理的,尽可能在地面处理。
③在起重能力与运输条件允许的范围内,尽可能在结构制造厂车间或现场地面组装平台上焊接成部件,成带成段起吊安装,以减少高空焊接作业工程量。
2)焊接方法的选择按上述方案原则,结合我公司的实际情况和目前国内热风炉焊接的成功经验,横焊逢全采用手工电弧焊。
焊接时,先焊内焊逢,由8-12位焊工按逆时针方向、用长肉法一层一层地焊接;内焊逢焊满后焊外焊缝,焊外焊逢时,先用气刨清根、打磨清理干净平整后,同样用长肉法一层一层焊接,直至满焊。
3) 焊接设备确保建设具有一流先进水平的热风炉系统焊接质量,必须配备一流的焊接设备。
针对新钢热风炉的工艺特点,炉皮材质和我公司所采取的焊接方法,特选如下焊接设备:○1ZX5-500可控硅整流弧焊机,其最大特点是无论大小电流焊接均很稳定,焊把线长时压降很小,较适宜现场安装,焊接。
○2 ZEF-1000硅整流碳弧气刨机,用此种焊机刨缝特别光滑平整,可提高碳弧气刨清根的刨缝质量,确保根部焊接质量。
○3焊条烘烤箱,此烘烤箱温度稳定,容量较大,能满足大批量的焊接任务。
试论壳牌气化炉的结构特点及操作维修
试论壳牌气化炉的结构特点及操作维修作者:齐云飞来源:《科技视界》2016年第23期【摘要】随着时代进步和社会各方面的发展,我国在煤化工这一行业领域取得了进一步的飞跃,这主要得益于一项新型设备的引进与使用,这项关键的技术设备就是本篇论文所要讨论的重点内容,壳牌气化炉。
目前我国对壳牌气化炉的引进还处于初级探索的试运行阶段,运行的过程还不稳定,究其原因是壳牌气化炉的结构特点和操作维修特点,因此本篇论文接下来将就这两方面的问题展开论述[1]。
【关键词】壳牌气化炉;结构特点;操作维修最近几年以来,新兴的煤气化技术随着我国壳牌气化炉的引进得到了越来越广泛的应用与发展,这决定了对煤气化技术的安全性问题,包括安全运行与管理,可持续性应用与操作维修等提出了更加严格的要求。
本文不仅对壳牌气化炉的结构特点以及操作维修方面进行了基本的介绍,还发现了在壳牌气化炉在试行过程中出现的问题并提出一些需要注意的地方。
接下来论文将按照这种逻辑依次展开论述。
1 化炉及其结构介绍了解气化炉之前,应该先清楚煤的气化过程。
煤的气化过程是指对煤的一项热化学加工处理过程,这一过程需要在特定的压力和温度环境下进行,利用气化剂,将煤中含有的有机物质转化为煤气[2]。
煤的气化过程要保证反映的温度高,速度快,停留时间长,这样才能保证煤中含有的有机物质得到最充分的转化,最大程度的减小损耗。
接下来将简单介绍关于气化炉的内容。
气化炉有其最大化的壁厚,高度和最大内经限制。
以部件功能划分,气化炉可分解为分化反应段,急冷段,输气管段,气体反向段,合成器冷却段和一部分辅助设备,例如烧嘴、敲击器、恒立吊等[3]。
气化炉内部器件的总体结构是水冷壁型式,在膜式水冷壁的内侧有一层耐火性极强的里衬,保护膜式水冷壁不易受到热侵蚀。
1.1 气化炉的气化反应段简介气化炉的气化反应段的组成主要有热裙,内件渣池,承压壳体,反应段膜式壁和挡渣屏。
承压壳体由耐热性能极好的一种耐热钢制成,在膜式壁的内侧喷涂了耐火性能极好的耐火材料,这些耐火材料会在气化过程中被产生的渣水和冷凝液等腐蚀。
壳牌煤气化技术介绍
壳牌煤气化SCGP表二) 壳牌煤气化SCGP-1用煤一览表(表二) SCGP
名 称 • 抒复科 • 扭兰赤 • 埃•色拉洋 • 阿尔沟瓦 • 斯凯来 • 罗宾森•克雷克 • 普卡红塔斯3号 • R§F • 石油焦 种 类 烟煤 烟煤 烟煤 褐煤 烟煤 烟煤 烟煤 烟煤 焦 产 地 美国(犹地) 澳洲 哥伦比亚 美国(微尔可斯特任德) 美国(中阿帕拉齐亚) 美国(中阿帕拉齐亚) 美国(中阿帕拉齐亚) 美国(北阿帕拉齐亚) 炼油厂
6.3. 设备
气化炉:重量约210吨/台。 操作压力 3.5MPa 内径 3680mm 炉管 (铬钼钢) φ38×6.3 废锅 : φ2900×40000
6.3.粗合成气 粗合成气CO+H2成本(元/NM3) 成本( 粗合成气
项目 原料煤 添加剂 燃料及动力 人工费 制造费 销售及管理费 合计 成本 0.081 0.003 0.061 0.02 0.105 0.014 0.264
5.投资及单位成本 投资及单位成本
单炉日投煤量2000吨SCGP气岛投资. 范围:空分(4.8万Nm3/h)、煤气化装置(含煤贮 运及粉体工程) 投资: 空分装置: 2.3亿元 煤气化装置(含软件): 4.6亿元(全套引进) 气岛总投资: 8.6亿元
6. 湖北双环壳牌煤气化炉示 范装置的情况
6.1. 规模 日处理煤量1000吨,一台炉,产气量 CO+H2:5.5×104Nm3/时。补充氧气, 建1万Nm3/时空分(投资约为4000万元)。
壳牌煤气化技术简介
主流煤气化技术及市场情况系列展示(之五)壳牌煤气化技术技术拥有单位:壳牌全球解决方案国际私有有限公司壳牌是世界知名的国际能源公司之一。
壳牌煤气化技术可以处理石油焦、无烟煤、烟煤、褐煤和生物质。
气化炉的操作压力一般在4.0MPa,气化温度一般在1400~1700摄氏度。
在此温度压力下,碳转化率一般会超过99%,冷煤气效率一般在80~83%。
对于废热回收流程,合成气的大部分显热可由合成气冷却器回收用来生产高压或中压蒸汽;如配合采用低水气比催化剂的变化工艺,在变换单元消耗少量蒸汽即可保证变换深度要求,剩余大量蒸汽可送入全厂蒸汽管网,获得可观的经济效益。
目前,壳牌全球解决方案国际私有有限公司负责壳牌气化技术的技术许可,工艺设计以及技术支持。
2007年壳牌成立了北京煤气化技术中心,2012年初,壳牌更是将其全球气化业务总部也从荷兰移师中国,这充分体现了壳牌对中国现代煤化工蓬勃发展的重视,同时壳牌也能更好地利用其全球气化技术能力,贴近市场,为中国客户提供更加快捷周到的技术支持。
目前,在北京的壳牌煤气化技术团队可提供从研发、工程设计、培训、现场技术支持以及生产操作和管理的全方位技术支持和服务。
一、整体配套工艺根据不同的煤质特性以及用户企业的不同生产需求和规划,壳牌开发了下面3种不同炉型:壳牌废锅流程是当前工业应用经验最丰富的干粉气化技术。
它的效率和工艺指标的先进性已经得到了验证和认可,而且在线率也在不断创造新的世界纪录,大部分客户已实现满负荷、长周期、安全、稳定运转。
如果业主比较关注热效率,全厂能效和环保效益的话,采用壳牌废锅流程并配合已成功应用的低水气比变换技术应该是最合适稳妥的方案。
壳牌上行水激冷流程特别适合处理有积垢倾向的煤种;适合大型项目,此外投资低,可靠性高。
对于比较关注在线率和低投资的业主,采用壳牌上行水激冷流程应该是最合适稳妥的方案。
壳牌下行水激冷流程在煤种的适应性方面与市场上其它下行水激冷技术相似,特别适合处理有积垢倾向的煤种;由于其采用了壳牌废锅流程成熟的对置多烧嘴布置,气化炉内流场分布合理,温度场均匀,使得碳转化率高,负荷调节灵活。
- 1、下载文档前请自行甄别文档内容的完整性,平台不提供额外的编辑、内容补充、找答案等附加服务。
- 2、"仅部分预览"的文档,不可在线预览部分如存在完整性等问题,可反馈申请退款(可完整预览的文档不适用该条件!)。
- 3、如文档侵犯您的权益,请联系客服反馈,我们会尽快为您处理(人工客服工作时间:9:00-18:30)。
石油化工建设10.03图1气化炉整体模型1气化炉概况近年来,随着煤化工的兴起,煤液化技术、煤制甲醇、油改煤在国内大批推进,其中壳牌气化炉(以下简称:气化炉)是采用最多的设备之一,如神华煤制油、中原大化50万t 甲醇装置、大唐多伦168万t 甲醇46万t 煤基烯烃均采用壳牌专利技术。
壳牌气化炉一律为专利设备整体引进,并由外商进行总体设计,其壳体部分大致分由两个国家制造:西班牙、印度L &T 公司;内件部分由荷兰SEG 公司设计,分别由西班牙和L &T 公司制造;其结构形式为膜式水冷壁结构。
1.1气化炉总体介绍气化炉主要由壳体和内件组成。
其中壳体分为反应器(Re-actor )+激(急)冷管(Quench Pipe )(位号:V1301),合成气冷却器(Syngas Cooler )+气体返回室(Gas Return Chamber )(位号:V1302),输气管(Transfer Duct )(位号:V1303)。
内件分为渣池(位号:V1401)、激冷管中压蒸汽发生器(位号:E1301)、输气管中压蒸汽发生器(位号:E1302)、合成气冷却器中压蒸汽发生器(位号:E1303)、气化炉反应器中压蒸汽发生器(位号:E1320)以及气体返回室内的立管(主管)和斜管(支管)等七部分。
1.2设备材料及设备规格气化炉整体重量约1300t 。
壳体主要材质为SA387GR11CL2;在反应器段、合成气冷却器段有一部分材质为复合材料SA387GR11CL2+NO8825;最大壁厚285mm ;壳体最大内径Φ4630mm ;需要现场组对焊缝处的壁厚为65~90mm ;整体长段50.2m 。
气化炉整体模型如图1所示。
1.3设备分段(以2000t 炉子为例)为了满足设备内陆道路运输及组焊吊装要求,在初步设计期间,技术方案的讨论必须有制造厂商参加,他们必须充分考虑管口方位、外壳外部尺寸等因素,并按照以下尺寸和重量极限进行设计分段:(1)组件高度最高5.1m ;(2)组件宽度最大7m ;(3)组件长度最长25.00m ;(4)组件重量最大150t 。
具体的设备分段情况列表如表1、表2所示:(注大唐3000t 炉子分段的几何尺寸及重量略大些)壳牌气化炉的现场组焊技术■肖晓磊中国化学工程第十一建设公司河南开封475002摘要通过与壳牌公司技术交流,借鉴国外压力容器组焊的先进经验,在国内中石化油改煤工程投料调试的经验基础上,结合大型气化炉组焊技术的工程实例,阐述一项成熟的气化炉现场组焊技术。
本文着重于描述施工程序(组装流程)、组对与焊接、内件安装。
对于无损检测、消除应力热处理、液压试验、衬里等仅做一般性介绍。
关键词壳牌技术气化炉现场组对焊接中图分类号TG44文献标识码B文章编号1672-9323(2010)03-0035-0835石油化工建设10.03图4输气管+气体返回室拼装工艺流程图图3反应器+激冷管组装工艺流程图表2内件分段一览表分段号位号分段名称规格(mm )φi ×L 净重(kg )安装部位1V1401渣池φ3700×31002900反应器内底部2E 1320中压蒸发器φ3900×1180051500反应器内3E 1301中压蒸发器φ3200×1400013500激冷管内4E 1302中压蒸发器φ2100×1230012500输气管内5支(斜)管φ1700×55003600气体返回室内6主(立)管φ2200×70508500气体返回室内7E 1303-2中压蒸发器φ3100×1900069500合成气冷却器内8E 1303-1中压蒸发器φ2700×1940068000合成气冷却器内2拼装工艺流程2.1反应器+激冷管组装工艺流程(如图3所示)2.2输气管+气体返回室拼装工艺流程(如图4所示)2.3合成气冷却器拼装工艺流程(如图5所示)三大部分的分段组对及内件安装工作全部完成之后,按照“反应器+激冷管”、“合成气冷却器”、“气体返回室”的顺序把三大段吊装至装置框架上就位,然后在装置框架上完成最后两道黄金焊缝的组对焊接以及其它内部接口工作。
3现场组焊对设备的制造要求3.1焊接坡口要求及长度预留焊接均采用双面坡口形式,即通常所说的偏“X ”形坡口,长度预留端不需要坡口。
分段号分段名称规格(mm )φi ×L ×δ坡口形式净重kg 备注Section -1反应器底部φ4644×3650×(75+5)偏“X ”57300SA387G R 11CL 2+SB 424-U N S-N O8825Section -2反应器中部φ4630×3950×(85+5)偏“X ”49600Section -3反应器中部φ4630×3500×90偏“X ”61300SA387G R 11CL 2Section -4反应器中部φ4630×5700×90偏“X ”71500Section -5反应器顶部φ4630×3000×90偏“X ”40200Section -6激冷管φ4630/φ3020×11100×90/80偏“X ”85600SA387G R 11CL 2上端为带余量毛边Section -7输气管φ3020×11670×80偏“X ”73900SA387G R 11CL 2弯管Section -8气体返回室φ3400/φ3020×5450×200/70偏“X ”143100SA387G R 11CL 2带一斜管Section -9气体返回室顶部φ3400×3950×65偏“X ”22200SA387G R 11CL 2封头段Section -10合成气冷却器上部φ3400×20900×70偏“X ”149810SA387G R 11CL 2Section -11合成气冷却器中部φ3400×5000×75偏“X ”58100SA387G R 11CL 2带恒力吊支座Section -12合成气冷却器下部φ3400×14900×75偏“X ”101000SA387G R 11CL 2表1外壳分段一览表施工技术准备→施工场地准备→施工资源准备→卸车验收及摆放壳体组对、焊接、无损检测、热处理→水压试验→耐火衬里地面安装内件→壳体分段吊装→在框架上空中组对→黄金焊缝焊接衬里及内件完善(内件陶瓷衬里,安装敲击装置、开工烧嘴、点火烧嘴等)→煮炉烘炉图2拼装工艺流程图36石油化工建设10.03图5合成气冷却器拼装工艺流程图表3各段之间焊缝坡口一览表3.1.1各段之间焊缝的坡口详情(如表3所示)3.1.2长度预留本设备在设计制造时,为了保证所有分段筒体在现场组对后整体尺寸能够满足设计要求,在反应器外壳上端(第5段上端)、激冷管上端(第6段上端)、合成气冷却器上端(第10段上端)预留有约50mm 的长度余量,其目的是用来调整确保整体长度不变(充分考虑焊接时的收缩量和修整坡口的余量)。
3.2组对的吊耳要求设备在组对过程中,需要不断地变换位置,这就需要全盘考虑整个施工工艺,设计出合理的吊耳,以满足设备组对时的吊装要求。
具体要求如表4所示。
同样,内件的吊装也要充分考虑。
比如反应器和激冷管内件为了满足安装要求,需要设置合适的满足垂直吊装的吊点。
3.3筒体上的预焊件因为设备外壳上分布有诸多的管嘴,在筒体位置上不一定有满足SAW 焊接转动要求的位置,于是考虑在不能满足转动要求的筒体上的适当位置安装支撑圈,高出设备管口,通过转动支撑圈来满足筒体的转动要求,这就要求在设备筒体上焊接一些“支撑板”以安装固定支撑圈。
支撑板的焊接在设备出厂前由制造厂完成。
3.4内件安装滑道的预焊件考虑到内件安装的可行性和便利性,在设计时,特别为在水平状态下安装的内件设计了水平滑道,以方便水平方向的推进。
需要水平滑道的内件包括输气管的内件中压蒸发器E1302,GRC 主管的内件、合成气冷却器的内件中压蒸发器E1303Ⅰ和Ⅱ,分别涉及的壳体为输气管、GRC 主管、合成气冷却器。
为了安装滑道,在设备壳体内表面上预焊一定高度的钢板。
衬里喷涂后外露一部分,在外露部分上焊接钢板或者H 型钢来组成滑道。
预焊的钢板高度要以内件在滑道上时内件中心线和外壳中心线重合为宜。
4现场施工准备4.1场地准备现场组对工作对场地有两个必须满足的条件:(1)面积要满足单位筒节摆放和施工的需要;(2)场地的地基处理(因为吊装和水压试验等相关工作对地面地耐力要求较高),要求达到35t/m 2。
所以施工前要对组焊场地进行地基处理。
若地面耐力能满焊缝名称焊接部位焊接位置状态母材厚度焊接方法备注SW11+2水平转动85+5mm SAW+SM AWX 坡口,外22.5°+22.5°,内30°+30°SW22+3水平转动90mm SAW X 坡口,外22.5°+22.5°,内30°+30°SW33+4水平转动90mm SAW X 坡口,外22.5°+22.5°,内30°+30°SW44+5水平转动90mm SAW X 坡口,外22.5°+22.5°,内30°+30°SW55+6水平转动/垂直90/95mm SAW/SM AW 液压试验时V 坡口10°+35°间隙8mm ,黄金焊口时V 坡口10°+35°间隙<2mmSW66+7框架上垂直80mm SM AW 外坡口25°+10°,内坡口45°+45°深5mm SW77+8水平固定65/70mm SM AW X 坡口,外22.5°+22.5°,内30°+30°SW88+9水平固定65mm SM AW X 坡口,外22.5°+22.5°,内30°+30°SW98+10水平固定/框架上垂直70mm SM AW 液压试验时X 坡口,外7.5°+5°。
黄金焊口时V 坡口12.5°+12.5°SW1010+11水平转动65mm SAW X 坡口,外22.5°+22.5°,内30°+30°SW1111+12水平转动65mmSAWX 坡口,外22.5°+22.5°,内30°+30°表4各段吊耳需要满足吊装要求一览表段号吊耳要求1满足垂直吊装、1+2段放倒、1~5段竖起时辅助2满足垂直吊装、1+2段放倒3满足垂直吊装、水平吊装4满足垂直吊装、4+5段放倒5满足垂直吊装、4+5段放倒、1~5段竖起、1~6段整体垂直吊装6满足水平吊装、单独垂直吊装和1~6段整体垂直吊装7满足水平吊装、7+8+9整体垂直吊装8满足水平吊装、7+8+9竖起时辅助9满足水平吊装、单独垂直吊装和7+8+9整体垂直吊装10满足水平吊装、10+11+12整体垂直吊装11满足水平吊装12满足水平吊装、10+11+12整体垂直吊装时辅助37石油化工建设10.03足技术要求,作技术处理即可;若不能满足则要考虑打桩处理。