数控加工工艺的分析和处理
数控车床零件的工艺分析及编程典型实例

数控车床零件的工艺分析及编程典型实例更新日期:来源:数控工作室根据下图所示的待车削零件,材料为45号钢,其中Ф85圆柱面不加工。
在数控车床上需要进行的工序为:切削Ф80mm 和Ф62mm 外圆;R70mm 弧面、锥面、退刀槽、螺纹及倒角。
要求分析工艺过程与工艺路线,编写加工程序。
图1 车削零件图1.零件加工工艺分析(1)设定工件坐标系按基准重合原则,将工件坐标系的原点设定在零件右端面与回转轴线的交点上,如图中Op点,并通过G50指令设定换刀点相对工件坐标系原点Op的坐标位置(200,100)(2)选择刀具根据零件图的加工要求,需要加工零件的端面、圆柱面、圆锥面、圆弧面、倒角以及切割螺纹退刀槽和螺纹,共需用三把刀具。
1号刀,外圆左偏刀,刀具型号为:CL-MTGNR-2020/R/1608 ISO30。
安装在1号刀位上。
3号刀,螺纹车刀,刀具型号为:TL-LHTR-2020/R/60/1.5 ISO30。
安装在3号刀位上。
5号刀,割槽刀,刀具型号为:ER-SGTFR-2012/R/3.0-0 IS030。
安装在5号刀位上。
(3)加工方案使用1号外圆左偏刀,先粗加工后精加工零件的端面和零件各段的外表面,粗加工时留0.5mm的精车余量;使用5号割槽刀切割螺纹退刀槽;然后使用3号螺纹车刀加工螺纹。
(4)确定切削用量切削深度:粗加工设定切削深度为3mm,精加工为0.5mm。
主轴转速:根据45号钢的切削性能,加工端面和各段外表面时设定切削速度为90m/min;车螺纹时设定主轴转速为250r/min。
进给速度:粗加工时设定进给速度为200mm/min,精加工时设定进给速度为50mm/min。
车削螺纹时设定进给速度为1.5mm/r。
2.编程与操作(1)编制程序(2)程序输入数控系统将程序在数控车床MDI方式下直接输入数控系统,或通过计算机通信接口将程序输入数控机床的数控系统。
然后在CRT 屏幕上模拟切削加工,检验程序的正确性。
数控加工工艺的分析与处理

数控加工工艺的分析与处理随着科技的不断进步,数控加工技术在制造业中得到了广泛应用。
数控加工工艺的分析与处理是保证数控加工过程顺利进行的关键环节。
本文将从数控加工工艺的基本原理、分析方法与处理措施三个方面进行探讨。
一、数控加工工艺的基本原理数控加工是利用计算机控制数控机床进行精密切削或造型加工的一种加工方法。
其基本原理是将图纸上的几何尺寸、形状和位置要求转化为数学模型,并通过计算机编程的方式将这些模型转化为数控指令,进而控制数控机床的运动轨迹、切削参数等,实现零件的加工。
数控加工工艺的前提是要了解工件的设计要求和材料特性。
通过分析工件的几何形状、尺寸、表面质量要求以及材料的硬度、可加工性等参数,确定适合的数控加工方案。
在具体加工过程中,还需要根据工件的形状复杂程度、加工精度要求等因素,合理选择数控机床、刀具和切削参数等。
二、数控加工工艺的分析方法1.几何形状分析:对于复杂形状的工件,需要进行多视图的几何形状分析,确定加工的主要特征面、特征线和特征点。
2.加工工艺分析:根据工件的几何形状、尺寸和表面质量要求,结合加工设备和材料,分析出适合的加工工艺路线,并绘制出对应的加工工艺卡。
3.切削力与热量分析:分析切削力和热量对加工过程的影响,根据材料的可加工性和切削力的大小,选择合适的切削参数和冷却液。
4.程序分析:通过工艺分析,确定数控加工的主要工序和加工路径,在制定程序时,遵循合理、简洁、安全、高效的原则。
三、数控加工工艺的处理措施1.加工设备优化:根据工件的加工要求,选择合适的数控机床及其附件,提高加工效率和精度。
2.刀具选择与刀具磨损处理:根据工件材料和切削要求,选择合适的刀具,并进行定期检查和更换,及时处理刀具磨损问题。
3.切削参数调整:根据工艺分析结果,合理调整切削速度、切削深度和进给速度等切削参数,以保证加工质量。
4.刀具路径优化:通过选择合理的切削路径和切削顺序,减少进刀次数和加工时间,提高加工效率。
零件的数控加工工艺分析
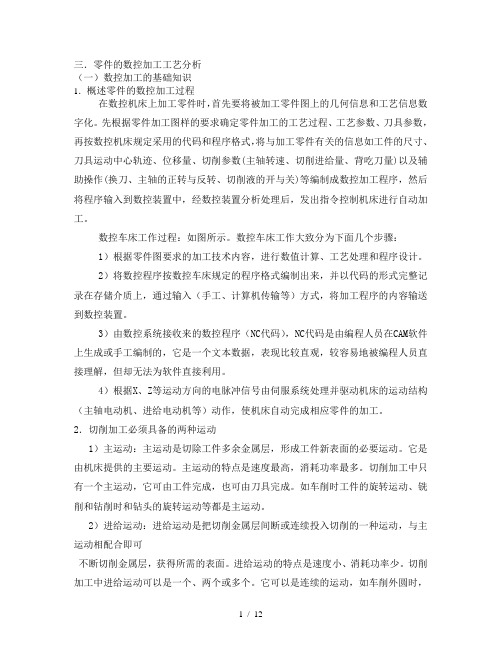
三.零件的数控加工工艺分析(一)数控加工的基础知识1.概述零件的数控加工过程在数控机床上加工零件时,首先要将被加工零件图上的几何信息和工艺信息数字化。
先根据零件加工图样的要求确定零件加工的工艺过程、工艺参数、刀具参数,再按数控机床规定采用的代码和程序格式,将与加工零件有关的信息如工件的尺寸、刀具运动中心轨迹、位移量、切削参数(主轴转速、切削进给量、背吃刀量)以及辅助操作(换刀、主轴的正转与反转、切削液的开与关)等编制成数控加工程序,然后将程序输入到数控装置中,经数控装置分析处理后,发出指令控制机床进行自动加工。
数控车床工作过程:如图所示。
数控车床工作大致分为下面几个步骤:1)根据零件图要求的加工技术内容,进行数值计算、工艺处理和程序设计。
2)将数控程序按数控车床规定的程序格式编制出来,并以代码的形式完整记录在存储介质上,通过输入(手工、计算机传输等)方式,将加工程序的内容输送到数控装置。
3)由数控系统接收来的数控程序(NC代码),NC代码是由编程人员在CAM软件上生成或手工编制的,它是一个文本数据,表现比较直观,较容易地被编程人员直接理解,但却无法为软件直接利用。
4)根据X、Z等运动方向的电脉冲信号由伺服系统处理并驱动机床的运动结构(主轴电动机、进给电动机等)动作,使机床自动完成相应零件的加工。
2.切削加工必须具备的两种运动1)主运动:主运动是切除工件多余金属层,形成工件新表面的必要运动。
它是由机床提供的主要运动。
主运动的特点是速度最高,消耗功率最多。
切削加工中只有一个主运动,它可由工件完成,也可由刀具完成。
如车削时工件的旋转运动、铣削和钻削时和钻头的旋转运动等都是主运动。
2)进给运动:进给运动是把切削金属层间断或连续投入切削的一种运动,与主运动相配合即可不断切削金属层,获得所需的表面。
进给运动的特点是速度小、消耗功率少。
切削加工中进给运动可以是一个、两个或多个。
它可以是连续的运动,如车削外圆时,车刀平行于工件轴线的纵向运动;也可以是间断的运动,如刨削是工件或刀具的横向运动。
数控车削加工工艺分析
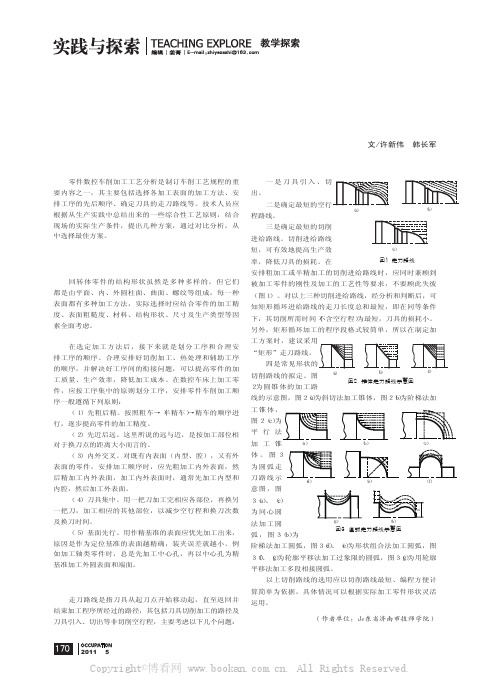
OCCUPATION2011 5170数控车削加工工艺分析文/许新伟 韩长军零件数控车削加工工艺分析是制订车削工艺规程的重要内容之一,其主要包括选择各加工表面的加工方法、安排工序的先后顺序、确定刀具的走刀路线等。
技术人员应根据从生产实践中总结出来的一些综合性工艺原则,结合现场的实际生产条件,提出几种方案,通过对比分析,从中选择最佳方案。
一、拟定工艺路线1.加工方法的选择回转体零件的结构形状虽然是多种多样的,但它们都是由平面、内、外圆柱面、曲面、螺纹等组成,每一种表面都有多种加工方法,实际选择时应结合零件的加工精度、表面粗糙度、材料、结构形状、尺寸及生产类型等因素全面考虑。
2.加工顺序的安排在选定加工方法后,接下来就是划分工序和合理安排工序的顺序。
合理安排好切削加工、热处理和辅助工序的顺序,并解决好工序间的衔接问题,可以提高零件的加工质量、生产效率,降低加工成本。
在数控车床上加工零件,应按工序集中的原则划分工序,安排零件车削加工顺序一般遵循下列原则:(1)先粗后精。
按照粗车→(半精车)→精车的顺序进行,逐步提高零件的加工精度。
(2)先近后远。
这里所说的远与近,是按加工部位相对于换刀点的距离大小而言的。
(3)内外交叉。
对既有内表面(内型、腔),又有外表面的零件,安排加工顺序时,应先粗加工内外表面,然后精加工内外表面,加工内外表面时,通常先加工内型和内腔,然后加工外表面。
(4)刀具集中。
用一把刀加工完相应各部位,再换另一把刀,加工相应的其他部位,以减少空行程和换刀次数及换刀时间。
(5)基面先行。
用作精基准的表面应优先加工出来,原因是作为定位基准的表面越精确,装夹误差就越小。
例如加工轴类零件时,总是先加工中心孔,再以中心孔为精基准加工外圆表面和端面。
二、确定走刀路线走刀路线是指刀具从起刀点开始移动起,直至返回并结束加工程序所经过的路径,其包括刀具切削加工的路径及刀具引入、切出等非切削空行程,主要考虑以下几个问题:一是刀具引入、出。
数控机床的加工工艺分析与优化

数控机床的加工工艺分析与优化随着科技的不断发展,数控机床在工业制造领域中扮演着重要的角色。
数控机床通过自动化技术和计算机控制技术实现了对工件的精密加工。
在进行数控机床加工时,优化加工工艺对于提高生产效率和产品质量至关重要。
本文将对数控机床的加工工艺进行分析与优化探讨。
首先,需要从工件材料的选择入手。
加工工艺的设计必须考虑到工件的材料特性,例如硬度、切削性能等。
不同材料的加工难度不同,因此需要选用合适的刀具和切削参数。
对于高硬度材料,可以选择硬质合金刀具进行加工;对于高粘性材料,可以选择高速钢刀具。
通过合理选择工件材料,可以大幅提高加工效率和产品质量。
其次,对于数控机床的刀具路径进行优化。
刀具路径的优化可以减少机床刀具在加工过程中的移动距离,从而缩短加工时间。
根据工件的形状和尺寸,可以采用合适的刀具路径,如直线插补、圆弧插补、等间距插补等。
通过减少刀具路径的长度,节省了刀具的磨损和加工时间,提高了加工效率。
第三,合理选择切削参数。
切削参数的选择对于数控机床加工中切削力、表面质量、切削温度等方面有着重要的影响。
切削速度、进给速度和切削深度是三个主要参数。
较大的切削速度会造成较大的切削力,适当的切削速度可以在一定程度上降低切削温度。
进给速度的增加可以提高加工效率,但过大的进给速度可能会导致加工质量下降。
因此,需要根据实际情况合理选择切削参数,以达到最佳的加工效果。
此外,对于数控机床的夹具设计也需要进行优化。
夹具的设计直接影响到工件的定位和固定,对于保证加工精度和稳定性至关重要。
夹具设计时需要考虑工件的形状、尺寸和加工要求。
合理设计夹具,可避免工件在加工过程中的振动和变形,提高加工精度和产品质量。
最后,加工过程中的刀具管理也是重要的环节。
切削工具的选择对加工工艺至关重要。
刀具的选择应根据工件材料、尺寸、形状等因素进行。
同时,需要定期对刀具进行维护和检查,包括刀具的磨损程度、刃口是否损坏等。
定期更换刀具,可以保证加工质量和加工效率。
数控铣床零件加工工艺分析与程序设计毕业论文

数控铣床零件加工工艺分析与程序设计毕业论文数控铣床是一种用数控技术控制刀具在工件上进行铣削加工的设备。
在数控铣床零件加工过程中,合理的工艺分析和程序设计对于保证加工精度和提高加工效率至关重要。
本文将以数控铣床零件加工工艺分析与程序设计为研究内容,分析其重要性并提出相应的设计方法。
首先,工艺分析对于数控铣床零件加工至关重要。
工艺分析是指通过对零件特点、材料性能等进行分析,确定合理的加工方法和加工工艺参数。
在数控铣床零件加工过程中,不同的零件要求不同的加工方法和参数,只有通过工艺分析才能确定最佳的加工工艺路线和参数,以保证零件的加工质量和效率。
工艺分析还可以提前预测可能出现的问题,如加工难度较大的区域、切削力较大的位置等,从而采取相应的措施,保证加工的顺利进行。
其次,程序设计是数控铣床零件加工的核心环节。
程序设计是指根据工艺分析的结果,编写数控程序,以实现对数控铣床的控制。
程序设计的质量直接影响加工结果,良好的程序设计可以提高加工精度和效率。
在程序设计过程中,需要根据零件的几何形状、尺寸和加工要求,确定数控刀具的刀补和补偿方案,编写合理的切削路径和切削轨迹,以保证零件的尺寸精度和表面质量。
此外,程序设计还需要考虑加工过程中可能出现的问题,如加工力的控制、材料的选择等,以提高加工的效率和稳定性。
在数控铣床零件加工工艺分析与程序设计过程中,可以采取以下方法:1.对零件进行全面的分析。
包括几何形状、尺寸、材料特性等方面的分析,确定加工目标和要求。
2.根据零件的特点和加工目标,选择合适的加工方法和加工工艺参数。
如铣床的进给速度、主轴转速、切削进给量等。
3.根据工艺分析结果,编写数控程序。
程序要考虑到零件的几何形状、加工道具的特点和刀具的路径。
4.在程序设计过程中,需要进行模拟实验和试加工。
通过试验和实际加工,检验程序的准确性和可行性。
5.对程序进行评估和调整。
根据试加工和实际情况,对程序进行调整和改进,以提高加工效率和质量。
第1章_数控加工工艺分析
零件的数控铣削结构工艺性图例
8
9
10
1.2 加工方法的选择
• 对于外圆面,可采用车削、磨削加工等方法; • 内孔加工可采用钻、扩、铰、镗、磨等加工方法; • 数控铣或加工中心加工零件的表面为平面、曲面、
轮廓、孔和螺纹等,所选加工方法要与零件的表面 特征、所要求达到的精度及表面粗糙度相适应。下 面,作为重点探讨。
• 平面轮廓多由直线和圆弧或各种曲线构成,通常采用 三坐标数控铣床进行两轴半坐标加工。下图为由直线 和圆弧构成的零件平面轮廓ABCDEA,采用半径为R 的立铣刀沿周向加工,虚线ABCDEA为刀具中心的 运动轨迹。为保证加工面光滑,刀具沿PA切入,沿 AK切出 。
12
• 三、固定斜角平面加工 • 固定斜角平面是与水平面成一固定夹角的斜面,
不完全定位中只设置与加工要求有关的 支承点,用较少的元件达到定位要求。
平板工件磨平面: 工件只有厚度和 平行度要求,通 过电磁工作台只 限制三个自由度。
27
六点定位原理的应用
欠定位--按照加工要求应该被限制的自由度没
有被限制的定位称为欠定位。装夹中不允许有
欠定位。
加工部位
圆柱体工件
a
b
c
28
六点定位原理的应用
24
六点定位原理
夹具用合理 分布的六个 支承点,分 别限制工件 的六个自由 度,使工件 在夹具中的 位置完全确 定,称为 “六点定位 原理”。
25
六点定位原理的应用
完全定位--工件的6个自由度全部被夹具中 的定位元件所限制。
26
六点定位原理的应用
不完全定位—根据工件加工表面的不同加工 要求,定位支承点少于6个的定位。
4
• 4. 保证基准统一原则 • 有些零件需要在铣完一面后再重新安装
数控机加工常见问题及分析
数控机加工过程中可能会遇到以下问题:1. 程序问题:包括程序错误、程序不兼容以及程序偏差等问题。
这通常是由于程序编写不当或误操作等原因引起的,解决方法是仔细检查程序,在使用之前进行模拟运行和修改,避免出现错误。
2. 夹持问题:夹持力度过大或过小都会影响零件的加工精度和表面质量。
应严格按照夹具说明进行夹持,并在加工前测量夹具的夹紧力度。
3. 刀具问题:刀具选择不正确、刀具磨损度过高或刀具不平衡等都会导致工件产生尺寸偏差和表面质量不佳。
需要定期更换刀具、检查刀具的平衡性和磨损情况,并选择适合工件加工的刀具类型。
4. 冷却液问题:冷却液对零件加工表面质量和加工速度有直接影响。
若冷却液不能很好地起到冷却、润滑的作用,可能会使工件的表面质量降低,加工速率减缓。
5. 机床问题:机床的导轨、丝杆等部件,若存在磨损或松动等问题,都会对加工精度和表面质量产生影响。
应保证机床的精度和刚性,定期维护和保养机床。
6. 材料问题:材料的质量问题会直接影响加工质量。
7. 刀具磨损:随着使用次数的增加,刀具会逐渐磨损,影响加工质量和效率。
解决方法是定期更换刀具,选择合适的切削参数和加工方式。
8. 加工震动:加工过程中出现的振动现象,可能导致零件表面粗糙度增大、尺寸偏差增大等问题。
解决方法是优化加工工艺,选用合适的夹持方式和刀具,并设置合适的进给量和转速。
9. 运动平稳性差:机床的运动平稳性差,容易导致轮廓不光滑、表面粗糙度高等问题。
解决方法是保证机床的精度和刚性,定期维护和保养机床。
10. 温度变化:温度变化会导致机床和工件的尺寸发生变化,从而影响加工质量。
解决方法是控制车间温度,使用稳定的进给系统和刀具以及优化加工策略。
11. 夹紧力不足:夹紧力不足可能导致工件位置偏差或者变形等问题。
12. 切削参数不合适:切削速度、进给量和切削深度等参数设置不合理,会导致刀具磨损加剧,加工效率低下,甚至可能损坏刀具或机床。
解决方法是根据工件材料、加工要求和刀具特性,合理选择切削参数。
数控机床的加工工艺优化和改进方法
数控机床的加工工艺优化和改进方法随着工业技术的不断发展,数控机床已经成为现代制造业中不可或缺的关键设备。
然而,为了提高生产效率和产品质量,加工工艺的优化和改进是必不可少的。
本文将介绍一些数控机床加工工艺优化和改进的方法。
首先,针对加工工艺的优化,我们可以从刀具选择和切削参数的优化入手。
在数控机床的加工过程中,选择合适的刀具是关键。
刀具的材质、硬度和形状都会直接影响加工质量和效率。
因此,我们需要根据不同的加工要求选择合适的刀具,并确保刀具的刃口清晰锋利,以提高切削效率和表面质量。
另外,我们还可以通过调整切削参数,如进给速度、转速和切削深度等,来优化加工工艺。
合理的切削参数可以有效地降低加工时间和能耗,并提高零件的精度和表面光洁度。
其次,加工工艺的改进可以通过改进加工路径和加工策略来实现。
合理的加工路径可以有效地避免零件表面的残余应力和变形。
利用数控机床的编程功能,我们可以通过优化加工路径来减少切削次数和切削长度,从而减少机床的负荷,降低加工成本。
此外,利用自动化控制技术,如高速切削和高速驱动系统,可以实现更高的加工速度和更精确的加工质量。
第三,数控机床的加工工艺还可以通过引入先进的检测和测量技术来改进。
现代的数控机床通常配备了各种传感器和测量设备,用于实时监测和控制加工过程中的各个参数。
利用这些设备,我们可以实时监测刀具的磨损程度、零件表面的粗糙度和尺寸等,并及时调整加工参数,以确保加工质量的稳定性和一致性。
另外,通过数据分析和统计,我们还可以提取和分析加工数据,发现潜在的问题和改进方向,以进一步优化加工工艺。
最后,为了实现加工工艺的持续优化和改进,企业应该注重技术创新和人员培训。
通过引入新的加工工艺和技术,企业可以不断提高自身的竞争力。
同时,为机床操作人员提供定期的培训和教育,提高他们的技能水平和加工意识,以确保加工工艺的正确执行和效果。
综上所述,数控机床的加工工艺优化和改进是提高生产效率和产品质量的关键。
数控加工零件的工艺分析与数控铣削加工工艺
数控加工零件的工艺分析与数控铣削加工工艺数控加工是指利用计算机数控系统,通过编写程序控制机床工作来加工零件的一种加工方式。
在工业生产中,数控加工因其高精度、高效率、高灵活性等优点而被广泛应用。
其中数控铣削是一种常见的数控加工方式,本文将从工艺分析、数控铣削加工工艺等方面进行探讨。
一、数控加工零件的工艺分析工艺分析是数控加工的一项前置工作,它的目的是确定加工工艺,选择合适的加工设备和刀具,制定加工程序等,从而保证加工质量和效率。
具体而言,工艺分析主要包括以下几个方面:1. 零件的材质和形状:不同材质的加工性能不同,加工时需要选择相应的切削参数和刀具;而零件的形状和结构也会影响加工难度和精度,需要对其进行全面分析和评估。
2. 加工精度和表面质量要求:根据零件的要求,确定加工精度和表面质量目标,制定相应的切削参数和工艺措施。
3. 工序分析:对零件进行逐个工序分析,确定加工顺序、加工方向、加工路径和刀具选择等重要内容,同时把握好每个工序的加工质量和效率。
4. 刀具选择:根据加工材料、零件形状和要求,选择合适的刀具和刀具尺寸,保证零件的加工质量和加工效率。
5. 加工程序制定:通过数控编程软件,编写机床加工程序,包括各种切削参数、刀具路径、指令参数等信息,为数控加工提供参考。
二、数控铣削加工工艺数控铣削是一种高速旋转的刀具在工件表面上进行切削的加工方式,它广泛应用于金属、塑料等材料制件的加工中。
数控铣削在工件制作中具有大量价值和应用,且数控铣削加工工艺也是半自动化和自动化制造中的重要工艺之一。
要把好铣削的关,需要具备以下几点:1. 刀具选择:刀具的选择是影响加工效率和加工质量的重要因素之一。
首先需要考虑切削材料,选择高速钢、硬质合金、陶瓷等材质的刀具;其次要考虑刀具尺寸和形状,根据零件的要求选择合适的刀具。
2. 切削参数:切削参数包括切削速度、进给量和切削深度等,这些参数的选定与零件材料、刀具材料、刀具尺寸和表面质量等因素密切相关。
- 1、下载文档前请自行甄别文档内容的完整性,平台不提供额外的编辑、内容补充、找答案等附加服务。
- 2、"仅部分预览"的文档,不可在线预览部分如存在完整性等问题,可反馈申请退款(可完整预览的文档不适用该条件!)。
- 3、如文档侵犯您的权益,请联系客服反馈,我们会尽快为您处理(人工客服工作时间:9:00-18:30)。
数控加工工艺的分析和处理姓名:专业:机械加工与自动化班级:前言:数控加工作为一种先进的加工方法, 被广泛地用于航空工业、舰船工业以及电子工业等高精度、复杂零件的加工生产。
在数控加工中,影响数控加工质量的因素很多,即工艺系统中的各组成部分,包括机床、刀具、夹具的制造误差、安装误差以及刀具使用中的磨损等都直接影响工件的加工精度。
也就是说,在加工过程中整个工艺系统会产生各种误差,从而改变刀具和工件在切削运动过程中的相互位置关系而影响零件的加工精度及质量。
摘要从加工工艺角度论述了提高数控加工精度,表面加工质量的解决措施,只在提高数控加工质量,利于更高效的使用数控机床,提高数控车床质量,第一要合理考虑工艺因素;第二要掌握数控车床的三大操作技巧,即一刀多尖、刀具圆弧半径补偿和刀具磨损参数的有效运用。
浅谈提高数控车床加工质量的措施一:机床的合理选择数控加工在中国制造业中已经有了较长的使用时间,虽然有严格的数控机床操作规范、良好的机床维护保养,但是其本身的精度损失是不可避免的。
为了控制产品的加工质量,我们定期对数控设备进行检测维修,明确每台设备的加工精度,明确每台设备的加工任务。
对于大批量成批生产的零件加工工厂,应严格区分粗、精加工的设备使用,因为粗加工时追求的是高速度、高的去除率、低的加工精度,精加工则相反,要求高的加工精度。
而粗加工时对设备的精度损害是最严重的,因此我们将使用年限较长、精度最差的设备定为专用的粗加工设备,新设备和精度好的设备定为精加工设备,做到对现有设备资源的合理搭配、明确分工,将机床对加工质量的影响降到了最低,同时又保护了昂贵的数控设备,延长了设备的寿命。
二:图纸分析1确定正确的加工工艺方案(1)合理实际切入切出路线。
在数控机床上加工零件时,为减少接到痕迹,保证轮廓的表面质量,对刀具的切入和切除的程序要仔细设计。
刀具的切入切点要沿零件周边外延,以保证工件的轮廓光滑,如刀具沿零件轮廓直接垂直切入零件,将在零件的外形上留下明显的痕迹,刀具要沿零件轮廓的法线切入和切除。
在轮廓加工过程中应避免进给停顿,否则由于切削力的变化也会产生刀痕,刀具切入过程一般需要采取较小的进给速度,为提高切削效率。
切入时从一个切削层换到另一个切削层,比切除后在突然切入好,这样可以保证恒定的切削参数,包括切削速度,进给量与切削速度的一致性,要尽量的提高毛培的成型精度,使表面加工余量均匀。
(2)例如制定加工顺序一般遵循下列原则:(1)先粗后精。
按照粗车半精车精车的顺序进行,逐步提高加工精度。
(2)先近后远。
离对刀点近的部位先加工,离对刀点远的部位后加工,以便缩短刀具移动距离,减少空行程时间。
此外,先近后远车削还有利于保持坯件或半成品的刚性,改善其切削条件。
(3)内外交叉。
对既有内表面又有外表面需加工的零件,应先进行内外表面的粗加工,后进行内外表面的精加工。
(4)基面先行。
用作精基准的表面应优先加工出来,定位基准的表面越精确,装夹误差越小。
2.选择正确的切削加工方式(1)车削圆钢类零件时尽量使用同一把刀车削不同的外圆,以减少接到痕迹。
一般,应避免车削非连续表面是;要注意选择合适大小的主偏角和副偏角,以避免刀具的干涉而产生刀痕。
此类零件的圆弧表面加工时应选取较小的偏角,并将刀尖倒成圆角,圆角半径应小于表面的半径。
三:编程1.数控车床的编程总原则是先粗后精、先进后远、先内后外、程序段最少、走刀路线最短,编程时常取零件要求尺寸的中值作为编程尺寸依据。
如果遇到比机床所规定的最小编程单位还要小的数值时,应尽量向其最大实体尺寸靠拢并圆整。
2.如图O1234G40G97G99M3S800M25 T0101GOX80.Z80.Z5.X0Z3.G1Z0F0.03G03X10.Z-10.R10.F0.02 GO1X48.Z-70.X60.Z-91.X62.GOX80.Z50.T0202GOX50Z-50.G01X43.F0.01GO4U0.2G01X49.GOX80.Z50.T0303GOX49.0Z0G92X47.1W-47.F2.0X46.5X45.9X45.5X45.4GOX80.Z50.M26M05M303.尺寸为0.026040φ+,则编程时写φ40.013.4.编程时尽量符合各点重合的原则。
也就是说,编程的原点要和设计的基准、对刀点的位置尽量重合起来,减少由于基准不重合所带来的加工误差。
在很多情况下,若图样上的尺寸基准与编程所需要的尺寸基准不一致,故应首先将图样上的各个基准尺寸换算为编程坐标系中的尺寸。
当需要掌握控制某些重要尺寸的允许变动量时,还要通过尺寸链解算才能得到,然后才可进行下一步编程工作。
四:车刀1. 刀具的选材和角度刀具材料在切削中一方面受到高温,高压和剧烈的摩擦作用,要求其硬度高,耐磨性和耐热型好;另一方面又要求受到压力,冲击力和震动,要求强度和韧性足够,但是,强度和韧性的材料其硬度与耐磨性必然较差,反之亦然。
解决方法:车刀的几何角度有主偏角、刀尖角、副偏角、刃倾角、前角、后角和副后角。
主偏角影响刀尖强度和切削层断面形状。
车削细长轴、薄壁套筒零件时,为了防止径向切削分力造成工件弯曲变形,主偏角应取大些(如90。
);端面、台阶面车刀的主偏角取93。
左右为宜;对于一般工件粗车时主偏角为75。
时,刀具的强度和散热性能最好,宜选用。
刀尖角在螺纹车刀中是一个主要角度,作为成形刀具其刀尖角的大小直接决定牙型,对于普通螺纹车刀,刃倾角为10。
时,其刀尖角为59。
16‘圆弧半径r 由公式r =0.144p 计算(式中P 为螺距)。
副偏角对表面粗糙度影响最大,主、副偏角愈小,刀尖圆角半径愈大的车刀加工出的表面粗糙度愈细化。
切削用量切削用量包括a 进给量f 和切削速度u ,其选择原则是:粗车时应该选一个尽可能大的切削深度a ,然后选择一个较大的进给量f ,最后在根据刀具允许的耐用度选一个合理的切削速度v ,而对于精车,因为精车工序直接决定工件的尺寸精度,形状精度和表面粗糙度,选择用量时要避免积屑减少残留面积,减少径向切削力Fy ,避免震动,所以切削深度和进给量要较少而切削速度要高。
例如五.切削液的合理选用切削液的主要作用是:冷却和润滑。
车削中常用的切削液是乳化液,浓度为5—25%;数控车床可以选用10号或20号机油为切削液;当有足够流量的切削液能完全冷却硬质合金刀具时,在车削钢等塑性材料时,以加冷却液为好;车铸铁、黄铜等脆性材料时,一般不加切削液,因为崩碎切屑与切削液混在一起容易阻塞机床拖板的运动;用高速钢刀具切削钢等塑性金属时,要加切削液。
六.工件装夹与切削。
(1)工件装夹方法的合理选择除一般轴类零件用三爪自定心卡盘直接装夹外,对于一些特殊零件,必须合理选择装夹方法,否则对零件的加工质量将带来负面影响,不能发挥数控车床高精度加工的优越性。
例如:细长轴零件在车削时,由于工件散热条件差,温升高,轴向因热变形造成较大的伸长量,如果用“一夹一顶”方法装夹,尾座顶尖就不能用固定顶尖,否则细长轴易产生弯曲变形,科学合理的装夹方法是改用弹性活动顶尖顶轴的右端,并且卡爪部位用钢丝过渡夹紧,另外,在中间可以安装中心架或跟刀架,在跟刀架的支承爪调整中其压紧力要适度,如果有间隙则达不到提高工件刚性的目的,如果压紧力过大,则细长轴加工后,表面必会呈现“竹节”状口],影响圆柱度。
车薄壁工件时为了防止径同夹紧力引起工件变形,可以采用轴向夹紧、开口环过渡夹紧或用软爪夹紧的方法,另外可以在一端预先留较厚的工艺凸缘用来装夹,待套筒加工完毕后再切除工艺凸缘。
车削曲轴时可以在中间搭一个中心架来提高工件的刚度,以防因切削力而引起变形。
(3)切削技巧一刀多尖的运用“一刀多尖”的运用技巧所谓“一刀多尖”,是指一把车刀在一道工序中利用它的多个刀尖来加工不同的工件表面,当多把车刀使用并编程。
如1号位车刀刀号为T01,其中一个刀尖车外圆,另一个刀尖车端面,车外圆刀尖对刀数值输入到偏置号“T0005”中,则外圆车刀编程时用“T0105”指令;车端面刀尖对刀数值输入到偏置号“T0006”中,则端面车刀编程时指令为“T0106”,可见一把车刀可同时充当两把车刀使用,可以间接扩充数控车床的刀库容量,且刀具角度比较好选择。
刀尖圆径的功能的运用数控车床的数控系统目前正在推广“刀尖圆弧半径补偿”功能,刀具在切削过程中会出现磨损,其刀尖点为空间的一个虚点,数控编程时是以这个虚点轨迹来编程的,而实际切削圆弧表面时,刀具实际切削点为刀尖圆弧上各实际分布点,必然会造成一边多切,另一边少切的现象,而运用刀尖圆弧补偿功能(即G41,G42,G40)进行运算,始终保证当前刀尖点是刀具圆弧与理论圆弧轮廓的切点,此功能在数控车床上运用简单有效,其操作要点是测量刀尖圆弧半径值,确定刀尖方位号,一次性在刀补表里对应输入,编程时在精车程序段起点之前和终点之后的程序段中用G41和G42建立刀具圆弧补偿功能,并要求在所在程序段中必须使用G01指令,否则H1无效。
刀具磨损的合理运用不管是成批大量生产还是单件小批量生产,数控车床加工工件时必须有一个加工试件(单件生产为正式件)的过程。
如何快速而准确地保证加工尺寸精度,现在在数控车床系统中增设了刀具磨损的补偿功能(有些老式系统在刀具偏置中用增减参数的方法实现),能够很有效地实现工件尺寸的快速调例如在同一零件上要加工00.0320φ-.00.0424φ-。
00.0326φ-。
00.0428φ-尺寸,首先编程、试切、对刀,如果一次连续自动加工,势必因工艺系统误差或测量误差导致工件报废,而有效的步骤是:首先设定某一磨损量如0.600,然后正常加工,待加工完毕后,取消磨损值,设定为O ,逐段精密测量,则每段理论直径相应增加0.600,与实际测量尺寸比较,如果偏大,则将相应的程序段指令的x 值减小相应的增量值,反之亦 然再精车时,轴径直径对中率极高。
轴向磨损量的运用亦然。
结束语本文从加工工艺的角度探究了提高数控加工质量的一系列方法,并且在实际加工中到到了验证,为数控加工工艺人员提供了一些解决问题的参考方案,有助于更高效的利用数控机床。