冲压模具设计冲裁模
冲压模具设计
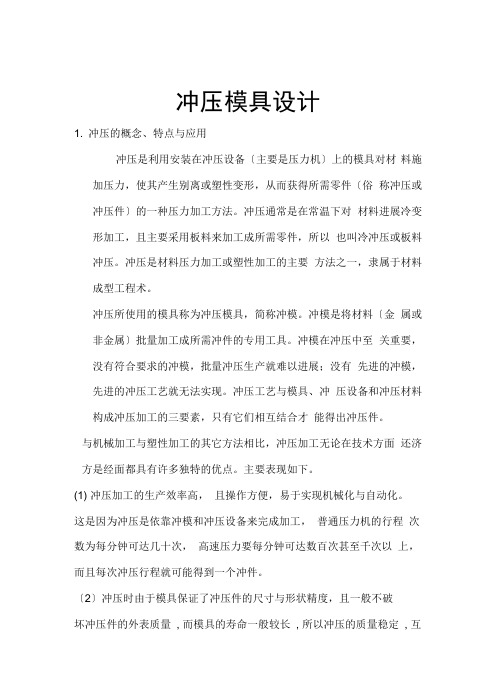
冲压模具设计1. 冲压的概念、特点与应用冲压是利用安装在冲压设备〔主要是压力机〕上的模具对材料施加压力,使其产生别离或塑性变形,从而获得所需零件〔俗称冲压或冲压件〕的一种压力加工方法。
冲压通常是在常温下对材料进展冷变形加工,且主要采用板料来加工成所需零件,所以也叫冷冲压或板料冲压。
冲压是材料压力加工或塑性加工的主要方法之一,隶属于材料成型工程术。
冲压所使用的模具称为冲压模具,简称冲模。
冲模是将材料〔金属或非金属〕批量加工成所需冲件的专用工具。
冲模在冲压中至关重要,没有符合要求的冲模,批量冲压生产就难以进展;没有先进的冲模,先进的冲压工艺就无法实现。
冲压工艺与模具、冲压设备和冲压材料构成冲压加工的三要素,只有它们相互结合才能得出冲压件。
与机械加工与塑性加工的其它方法相比,冲压加工无论在技术方面还济方是经面都具有许多独特的优点。
主要表现如下。
(1) 冲压加工的生产效率高,且操作方便,易于实现机械化与自动化。
这是因为冲压是依靠冲模和冲压设备来完成加工,普通压力机的行程次数为每分钟可达几十次,高速压力要每分钟可达数百次甚至千次以上,而且每次冲压行程就可能得到一个冲件。
〔2〕冲压时由于模具保证了冲压件的尺寸与形状精度,且一般不破坏冲压件的外表质量, 而模具的寿命一般较长, 所以冲压的质量稳定, 互换性好, 具有“一模一样〞的特征。
〔3〕冲压可加工出尺寸X 围较大、形状较复杂的零件,如小到钟表的秒表,大到汽车纵梁、覆盖件等,加上冲压时材料的冷变形硬化效应,冲压的强度和刚度均较高。
〔4〕冲压一般没有切屑碎料生成,材料的消耗较少,且不需其它加热设备,因而是一种省料,节能的加工方法,冲压件的本钱较低。
但是,冲压加工所使用的模具一般具有专用性,有时一个复杂零件需要数套模具才能加工成形,且模具制造的精度高,技术要求高,是技术密集形产品。
所以,只有在冲压件生产批量较大的情况下,冲压加工的优点才能充分表达,从而获得较好的经济效益。
冲压模具设计——第二章

弱区先变形,变形区为弱区
9
第三节 冲压变形理论基础
五、冲压材料及其冲压成形性能
1.冲压成形性能 材料的冲压成形性能:材料对各种冲压加工方法的适应能力。
冲压加工的依据。 成形极限高 材料的冲压性能好 成形质量好 便于冲压加工
成形极限高 冲压成形性能是一个综合性的概念
29
3、间隙对模具寿命的影响
模具寿命分为刃磨寿命和模具总寿命。 失效原因:磨损、变形、崩刃、折断和胀裂。
小间隙将使磨损增加,甚至使模具与材料之间产生粘 结现象,并引起崩刃、凹模胀裂、小凸模折断、凸凹 模相互啃刃等异常损坏。
为了延长模具寿命,在保证冲裁件质量的前提下
1)采用适当或较大的间隙值;
2)减缓间隙不均匀的影响; 3)采用小间隙时必须提高模具硬度与光洁度、精度; 4)改善润滑条件,减少磨损。
3
冲压变形理论基础
一、塑性变形的基本概念
变形:
弹性变形、塑性变形。
塑性:
表示材料塑性变形能力。它是指固体材料在外力作用下发 生永久变形而不破坏其完整性能力。
塑性指标:
衡量金属塑性高低的参数。常用塑性指标为延伸率δ和断
面收缩率ψ。
Lk L0 100 % L0
F0 Fk 100 % F0
成形质量好
10
第三节 冲压变形理论基础
五、冲压材料及其冲压成形性能(续)
2.冲压成形性能的试验方法 间接试验和直接试验
3.板料的机械性能与冲压成形性能的关系
板料的强度指标越高,产生相同变形量的力就越大; 塑性指标越高,成形时所能承受的极限变形量就越大; 刚度指标越高, 成形时抵抗失稳起皱的能力就越大。
c= (DA-dT)/2
冲压工艺与模具设计:冲裁模的主要零部件结构设计

凹模厚(高)度
H=kb (≥15)
k见表2.22 凹模壁厚 C=(
1.5~2)H
(≥30~40)
计算值:
靠用标准,选择模架的依据。
2 工作零 件3.凸凹模
复合模中同时具有落料凸模和冲孔凹模作用的工作零件。
凸凹模的最小壁厚: 正装复合模,内孔不积存废料,胀力小,最小壁厚可以小些; 倒装复合模,若内孔为直筒形刃口形式,且采用下出料方式, 则内孔积存废料,胀力大,故最小壁厚应大些。
导料板的厚度:见表2.24
导料板结构
3 定位零件(续)
2)侧压装置
设置目的:若条料公差较大,为避免条料在导料板中偏摆,使最 小搭边得到保证。
结构形式:①弹簧式侧压装置 ②簧片式侧压装置 ③簧片压块式侧压装置 ④板式侧压装置
不宜设置侧压装置的场合:①板料厚度在0.3mm以下的薄板; ②辊轴自动送料装置的模具。
谢谢!
特殊侧刃:既可定距,又可冲裁零件的部分轮廓 宽度b
侧刃断面尺寸 其他尺寸按标准规定
侧刃凹模按侧刃实际尺寸配制,留单边间隙。
侧刃数量: 一个或两个 侧刃布置: 并列布置、对角布置
侧刃定位误差比较
1-导料板 2-侧刃挡块 3-侧刃 4-条料
尖 角 形 侧 刃
特殊侧刃
3 定位零件(续)
5)导正销
使用目的: 消除送进导向和送料定距或定位板等粗定位的误差。 主要用于: 级进模
1)导料销、导料板 导料销:两个,位于条料的同侧, 从右向左送料时,导料销装在后侧; 从前向后送料时,导料销装在左侧。 结构形式: 固定式、活动式
3 定位零件(续) 1)导料销、导料板(续) 导料板:设在条料两侧 结构形式:一种是标准结构,它与卸料板(或导板)分开制造 一种是与卸料板制成整体的结构。
冲裁及冲裁模设计
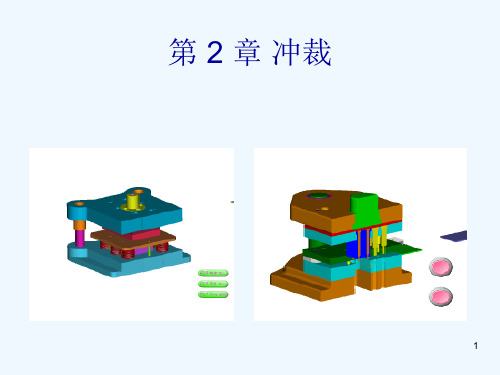
第 2 章 冲裁
2 -2 冲裁模具间隙
2.2.1 间隙对冲裁件质量的影响
冲裁件的质量:断面质量、尺寸精度 a 间隙对断面质量的影响 小间隙、合理间隙、大间隙情况下的剪切过程 断面特征值与间隙的关系图。
17
第 2 章 冲裁
2-2 冲裁模间隙
间隙对断面质量的影响
18
第 2 章 力、变形和冲裁件正常的断面状况 a)冲孔件 b)落料件
第 2 章 冲裁
2 -2 冲裁模具间隙
间隙的概念 模具凸凹模刃口缝隙间的距离。 单边间隙c、双边间隙z。 间隙对冲裁件的质量、模具寿命、冲裁力都有很大 的影响,是冲裁工艺和模具设计中的最重要的工艺参数。 2.2.1 间隙对冲裁件质量的影响 2.2.2 间隙对冲裁力的影响 2.2.3 间隙对模具寿命的影响 2.2.4 间隙的确定
12
第 2 章 冲裁
2-1 冲裁变形机理
2.1.5 断面特征
1)圆角带:冲裁过程中,纤维的弯曲与拉伸形成, 软材料圆角大。 2)光亮带:塑剪变形时,由于相对移动,凸凹模侧 压力将毛料压平形成的光亮垂直断面。
3)断裂带:刃口微裂纹受拉应力不断扩展形成的撕 裂面,导致断面粗糙并有斜度。 4)毛刺:由微裂纹位置与冲裁间隙等引起,是金属 拉断而形成的金属刺残留在冲裁件上
板 坯
F v 1
F v 2
F h 2
F h 2
F v 2
凹 模
板坯受力简图 Diagram of sheet metal under load
10
第 2 章 冲裁
2-1 冲裁变形机理
2.1.3 裂纹的形成与发展 裂纹产生的条件:当变形区的应变达到极限塑性应变值时, 就产生微裂纹 裂纹扩展的方向:沿着最大剪切应变速度的方向扩展 裂纹的成长过程:裂纹首先在低应力区产生,由于变形过 程中最大剪切应变的速度方向发生变化,使得新的裂纹不断产 生,旧裂纹的扩展不断停止,然后在旧裂纹的前端附近重新产 生新的裂纹,不断产生的微裂纹的根部汇成了一条主裂纹 极限塑性应变值除和材质外,还和应力状态、变形历史(损 伤程度)有关。
冲裁模(冲压模具)课程设计 说明书

(a)下模座
(b)上模座 图 4-1
2、 导柱的选取
13
导柱尺寸参数如下: 直径 28mm,长度 150mm。结构如图所示:
图 4-2 导柱
3、 导套 导套结构如下图所示:
图 4-3 导套
4、 模柄 模柄直径 50mm,长度 105。结构图为:
14
图 4-4 模柄
五、 固定、定位零件
固定、定位零件见表 3。
10
橡胶的安装高度:ha=h0-hy=30-0.3×30=21mm3
8、顶件块结构
图 3-8 顶件块
9、定距块
由于小凸模长度 53mm,凹模固定板厚度 17mm,凹模板厚度 15mm,因此需要 定距块,定距块厚度为 20mm,结构如图:
11
图 3-9 定距块
10、顶杆
图 3-10 顶杆
11、导料销
2
图 2-1-2
一个步距内材料的材料利用率: η=985.182/(74.7*21.5)×100%= 61.34%
2、压力中心确定和压力机的选择
(1)、冲裁力的计算 冲裁力 F p=Lt σb Kp 其中: 由图 2-2 知,周长 L=213.057mm; 材料:08F 钢板,查表,σb=900Mpa, 此时,Kp=1,则: Fp=213.057X1X900X1=191.75(kN) 根据以上模具结构类型,采用弹性卸料和漏料出件, 卸料力 F q=KF,取 K =0.05,则: F q =0.05×191.75=9.59(kN) (2-2-3) (2-2-2) (2-2-1)
二、 工序设计及工艺计算
1、 排样
毛坯最大尺寸 70mm,不算太小, 为保证冲裁件的质量,模具寿命和 操作方便,采用有搭边,单排排样,如下图 2-1 所示,冲裁件之间的搭边 值 a1=1.5mm,冲裁件与条料件侧边之间的搭边值 a=2.3mm。
冲裁工艺与模具设计-冲裁模设计步骤及实例
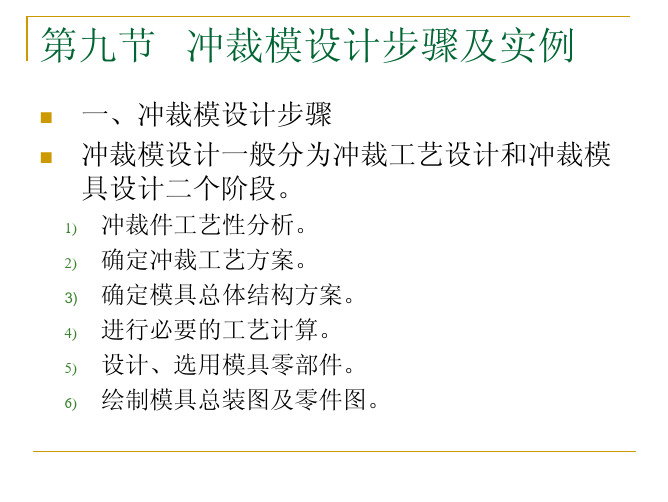
第2章 冲裁工艺及冲裁模设计
实际确定冲裁工艺方案时,通常可以先拟定出 几种不同的工艺方案,然后根据冲件的生产批 量、尺寸大小、精度高低、复杂程度、材料厚 度、模具制造、冲压设备及安全操作等方面进 行全面分析和研究,从中确定技术可行、经济 合理、满足产量和质量要求的最佳冲裁工艺方 案。
或级进冲裁; 冲件尺寸较大时,料薄时可用复合冲裁或单工序冲裁,料厚时受
压力机压力限制只宜采用单工序冲裁; 冲件上孔与孔之间或孔与边缘之间的距离过小时,受凸凹模强度
限制,不宜采用复合冲裁而宜用级进冲裁,但级进模轮廓尺寸受 压力机台面尺寸限制,所以级进冲裁宜适应尺寸不大、宽度较小 的异形冲件; 形状复杂的冲件,考虑模具的加工、装配与调整方便,采用复合 冲裁比级进冲裁较为适宜,但复合冲裁时其出件和废料清除较麻 烦,工作安全性和生产率不如级进冲裁。
《冲压工艺及模具设计》
第2(章1冲)裁模具工类艺型及冲裁模设计
模具类型主要是指单工序模、复合模、级进模三种。有些单件试 制或小批量生产的情况下,也采用简易模或组合模。
模具类型应根据生产批量、冲件形状与尺寸、冲件质量要求、材 料性质与厚度、冲压设备与制模条件、操作与安全等因素确定。
(2)操作与定位方式
《冲压工艺及模具设计》
第2章 冲裁工艺及冲裁模设计
4 进行必要的工艺计算 在冲裁工艺与模具结构方案确定以后,为了进
一步设计模具零件的具体结构,应进行以下有 关工艺与设计方面的计算:
《冲压工艺及模具设计》
第2(章1冲)裁排工样艺设及计冲与裁计模算设计 根据冲件形状特征、质量要求、模具类型与结构方 案、材料利用率等方面因素进行冲件的排样设计。设 计排样时,在保证冲件质量和模具寿命的前提下,主 要考虑材料的充分利用,所以,对形状复杂的冲件, 应多列几种不同排样方案 (特殊形状件可用纸板按冲 件比例作出样板进行实物排样),估算材料利用率, 比较各种方案的优缺点,选择出最佳排样方案。 排样方案确定以后,查出搭边值,根据模具类型和定 位方式画出排样图,计算条料宽度、进距及材料利用 率,并选择板料规格,确定裁板方式 (纵裁或横 裁),进而确定条料长度,计算一块条料或整块板料 的材料利用率。
冲裁工艺与模具设计-冲裁模的典型结构
¾ 冲小孔模具,必须考虑凸模的强度和刚度,以及快速更换凸模的结 构;
¾ 成形零件上侧壁孔冲压时,必须考虑凸模水平运动方向的转换机构 等。
(1)导柱式冲孔模 (2)冲侧孔模 --- 斜楔式水平冲孔模
第二章 冲裁工艺与冲裁模设计
导 柱 式 冲 孔 模
1-下模座 2、18-圆柱销 3-导柱 4-凹模 5-定位圈 6、7、8、15-凸模 9-导套10-弹簧11-上模座 12-卸料螺钉 13-凸模固定板 14-垫板 16-模柄 17-止动销19、20-内六角螺钉 21-卸料板
第二章 冲裁工艺与冲裁模设计
2.7 冲裁模的典型结构
(一)冲裁模的基本类型
1.按工序性质可分为落料模、冲孔模、切断模、切口模、切 边模、剖切模等; 2.按工序组合方式可分为单工序模、复合模和级进模; 3.按上、下模的导向方式可分为无导向的开式模和有导向的 导板模、导柱模、导筒模等。 4.按凸、凹模的材料可分为硬质合金冲模、钢结硬质合金冲 模、聚氨脂冲模等; 5.按凸、凹模的结构和布置方法可分为整体模和镶拼模,正 装模和倒装模。
2.7 冲裁模的典型结构
(二)冲裁模结构组成 上模、下模
根据各零件在模具中所起的作用不同,分为工艺零件 和结构零件: 工艺零件:直接参与完成工艺过程并与板料或冲件直 接发生作用的零件,包括工作零件,定位零件,卸料 与出料零部件等。 结构零件:将工艺零件固定起来构成模具整体,是对 冲模完成工艺过程起保证和完善作用的零件,包括支 撑与固定零件、导向零件、紧固件及其他零件。
2.7 冲裁模的典型结构
虽然冲裁模种类繁多,但生产中通常还是习惯按照 工序组合形式将冲裁模归类。
冲裁模(冲压模具)课程设计说明书
模具设计的具体步骤
确定冲裁模的类型和尺寸 设计冲裁模的轮廓和结构 确定冲裁模的冲压力和冲压速度
设计冲裁模的模具材料和热处理工艺 设计冲裁模的冷却系统和润滑系统 设计冲裁模的模具寿命和维护保养方法
冲裁模的制造工艺
冲裁模的设计:根据产品要求进行设计,包括尺寸、形状、材料等 冲裁模的制造:采用数控机床进行加工,保证精度和效率 冲裁模的装配:将各个部件组装成完整的冲裁模 冲裁模的调试:在装配完成后进行调试,确保其性能和精度达到要求
采用环保材料和工艺, 减少对环境的影响
提高冲裁模的自动化 程度,降低人工成本
提高模具寿命的方法和途径
优化模具设计: 合理选择材料、 结构、尺寸等, 提高模具的强度 和耐磨性
提高加工精度: 采用先进的加工 技术和设备,提 高模具的加工精 度,减少误差
加强维护保养: 定期检查、清洗、 润滑模具,及时 发现并处理模具 的磨损和损坏
冲裁模的使用和维护
冲裁模的使用 步骤:安装、 调试、运行、
停机
冲裁模的维护 方法:定期检 查、清洁、润 滑、更换易损
件
冲裁模的安全 操作:遵守操 作规程,注意
安全防护
冲裁模的常见 故障及处理方 法:如卡模、 漏油、噪音等, 需及时处理, 确保生产安全
常见问题的处理和解决方法
冲裁模调试过程中, 如果出现模具损坏, 应及时更换或修复。
设计前的准备工作
确定冲裁模的用途和功能 收集冲裁模的设计要求和技术参数 确定冲裁模的材料和尺寸 准备冲裁模的设计图纸和工具
模具设计的基本流程
确定冲裁 模的设计 要求
设计冲裁 模的尺寸 和形状
确定冲裁 模的材料 和加工工 艺
设计冲裁 模的装配 和调试方 法
冲裁模的结构与设计
定期检查与保养
定期检查冲裁模的外观和结构, 确保没有损坏或变形。
检查冲裁模的刃口是否锋利, 如需磨刃应及时进行。
定期对冲裁模进行润滑,以减 少磨损和保持其良好的工作状 态。
常见故障与排除方法
冲裁出的工件尺寸不稳定
检查冲裁模的刃口是否磨损或松动,调整刃 口间隙或更换磨损件。
冲裁出的工件表面质量差
检查冲裁模的刃口是否锋利,如需磨刃应及 时进行。
冲裁模的应用领域
汽车制造
汽车面板、座椅、车门等部件 的制造。
家用电器
洗衣机、冰箱、空调等产品的 制造。
电子行业
手机、电脑、平板等产品的制 造。
航空航天
飞机、火箭、卫星等高端设备 的制造。
02
冲裁模的结构
上模
01
上模是冲裁模的主要组 成部分,通常安装在冲 压机上。
02
03
04
上模主要由凸模、卸料 板、上模板和垫板等组 成。
标注模具各零件的尺寸、材 料和热处理要求。
绘制详细的装配图,包括各零 件之间的装配关系、配合尺寸
和连接方式等。
审核与修改设计
对设计完成的模具进行审核,确 保其满足工艺要求和结构形式要
求。
根据审核结果,对设计进行必要 的修改和完善。
与制造部门沟通,确保模具制造 的可行性和经济性。
05
冲裁模的维护与保养
04
冲裁模的设计流程
确定工艺要求
1
确定冲裁件的材料、尺寸、精度和表面质量要求。
2
分析冲裁件的工艺性,评估是否适合采用冲裁工 艺。
3
确定冲裁工艺方案,包括冲裁次数、工序组合方 式等。
确定模具结构形式
01
根据冲裁件形状、尺寸和精度要求,选择合适的模具结构形 式。
冲压工艺分析与模具设计——冲裁模设计 (1)
《冲压工艺分析与模具设计》课程上机设计实验报告题目:冲裁模CAD设计姓名:海志刚学号:20114403班级:11材型(卓越)-1班指导教师:毕大森一、上机设计实验要求1.设计要求:已知如图零件08钢,厚度1mm。
完成外形的单工序落料模设计;完成相关的工艺计算,画出模具装配图(三视图,并采用适当的剖视图)2.参考资料:(1)《中国模具设计大典》(电子版)夏巨湛总主编,中国机械工程学会中国模具设计大典编委会(2)《冲压成形工艺与模具设计》教材,李奇涵主编,科学出版社出版(3)《冲模设计技法及典型实例解析》廖伟编著,化学工业出版社二、上机设计实验过程1、冲裁排样与搭边的设计为了保证冲裁件的质量,模具寿命和操作方便,采用有搭边的单排排样。
经过查阅《冲压成形工艺与模具设计》的表3-8 最小搭边值a得;材料厚度1mm,工件间a1=1.2,侧面a=1.5。
计算料条的宽度:b=48+2×1.5=51(mm)计算料条的步距:s=14+1.2=15.2(mm)如图1所示2、凸凹模刃口尺寸的计算由题目知零件为08钢,厚度为1mm。
查阅《冲压成形工艺与模具设计》表3-5 冷冲模初始间隙值得:Z min=0.100mm,Z max=0.14mm Z max-Z min=0.04mm。
δp=0.4(Z max-Z min)δd=0.6(Z max-Z min)由标准公差表得:480-0.25为IT12等级 X取0.75根据计算原则,落料时以凹模为设计基准。
首先设计凹模尺寸,使凹模的基本尺寸接近或等于工件轮廓的最小极限尺寸,将凹模尺寸最小合理间隙值即到凹模尺寸:设凸凹模分别按IT6、IT7等级加工制造,则落料:D d=(D max-xΔ)δd0=(48-0.75×0.25)=47.8125+0.0250(mm)D P=(D d-Z min)-δp0=(47.8125-0.1)=47.71250-0.016Z max Z min--最大、小初始双面间隙;D d D P——为落料凹凸模尺寸;D max——落料件的最大极限尺寸Δ——冲裁件制造公差X——磨损系数校核:0.025+0.016=0.041〉0.04由此可知,只有缩小δpδd,提高制造精度,才能保证间隙在合理范围内,则δp=0.4(Z max-Z min)=0.4×0.04=0.016δd=0.6(Z max-Z min)=0.6×0.04=0.024故:D d=47.8125+0.0240(mm)D P=47.7125-00.016(mm)3、冲裁模主要零部件设计(1)卸料装置的设计计算冲裁力根据公式F≈Ltσ b ≈124×1×365≈45260(N)F为冲裁力;L为冲裁周边长度;t为材料厚度;σb为抗拉强度。
- 1、下载文档前请自行甄别文档内容的完整性,平台不提供额外的编辑、内容补充、找答案等附加服务。
- 2、"仅部分预览"的文档,不可在线预览部分如存在完整性等问题,可反馈申请退款(可完整预览的文档不适用该条件!)。
- 3、如文档侵犯您的权益,请联系客服反馈,我们会尽快为您处理(人工客服工作时间:9:00-18:30)。
目录一、设计任务书 (2)二、冲压工艺性及工艺方案的确定 (3)三、主要设计计算 (4)四、模具总体设计 (8)五、主要零部件设计 (8)六、冲压设备的选定 (12)七、设计小结 (13)八、参考文献 (13)一、课程设计任务一、题目:冲孔、落料复合模二、零件:材料:Q235厚度:2.0mm批量:大批量三、任务内容:(一)工艺设计1、工艺审查与工艺分析2、工艺计算:①毛胚计算②工序件计算或排样图3、工艺方案的确定①工序的确定②基准和定位方式的选择(二)模具设计1、总图2、零件图二、冲压工艺性及工艺方案的确定一、工艺性分析1、材料零件的材料为Q235普通碳素钢,具有良好的冲压性能,适合冲裁。
2、结构该零件属于较典型冲裁件,形状简单对称。
孔边距远大于凸、凹模允许的最小壁厚(见参考文献①表2.9.5),故可以考虑复合冲压工序。
3、精度零件外形:80±0.07属于10级精度,60±0.05属于9级精度。
零件内形: 16060.00Φ+属9级精度。
孔间距:42±0.08属11级精度(均由参考文献精度②附录一查得)。
因零件边有90o的尖角,应以圆弧过渡,查参考文献①表2.7.1取r=0.5mm。
零件精度较高,模具按六、七级制造可达到尺寸精度要求。
4、结论可以冲裁。
二、冲压工艺方案的确定该零件包括落料、冲孔两个基本工序,可以采用以下三种工艺方案:方案①:先落料、再冲孔。
采用单工序模生产。
方案②:落料—冲孔复合冲压。
采用复合模生产。
方案③:冲孔—落料级进冲压。
采用级进模生产。
方案①模具结构简单,但需要两道工序、两套模具才能完成零件的加工,生产效率较低,难以满足零件大批量生产的需求。
方案②只需要一套模具,冲压件的形位精度和尺寸易于保证,且生产效率也高。
尽管模具结构较方案①复杂,但由于零件的几何形状简单对称,模具制造并不困难。
方案③也只需要一套模具,生产效率高,但零件的冲压精度不易保证。
通过以上三种方案的分析比较,对该冲压件生产以采用方案②为佳。
三、主要设计计算(1)排样方式的确定及计算查参考文献①表2.5.2,查得:取两工件间的最小搭边:a1=2.0mm 侧面搭边值:a=2.2mm 由下表计算可知条料宽度5.8506.0-mm,步距62.2mm。
查参考文献③第8页选取t=2.0mm,950mm⨯2000mm的钢板。
一个步距材料利用率90.3%(计算见下表)。
每条钢板可剪裁为11张条料(85.5mm⨯2000mm)每张条料可冲32个工件,故每张材料利用率为88.9%(计算见2. 2.下表)确定后的排样如下图:(2)冲压力的计算该模具采用倒装式复合模,拟选弹性卸料,刚性出件,冲压力的相关计算见下表。
排样冲压力计算表卸料力卸F卸F =卸K 落F =0.05⨯288.410.92KN查参考文献①表2.6.1取卸K =0.05总冲压力总F总F =落F +冲F +推F +卸F=218.4+78.37+10.92+25.86333.55KN(3)压力中心的确定该工件尺寸,形状对称,因此该工件的压力中心在工件轮廓的几何中心O 上。
(4)工作零件刃口尺寸的计算查参考文献①表 2.3.3取60.30max=Z,246.0m in =Z 磨损系数x=1尺寸及分类计算公式结果 备注 落料60±0.05模具凹模按七级制造,凸模按六级制造。
T A δδ,均由参考文献②附录一查得,且均满足:≤+T A δδZ m ax-Z min80±0.07冲孔中心距42±0.08(5)卸料橡胶的设计计算采用40.51245⨯⨯ JB/T 7650.9-1995聚氨酯弹性体项目公式结果备注四、模具总体设计(1)模具类型的选择由冲压工艺性分析可知,采用复合冲压,所以模具类型为复合模。
(2)定位方式的选择该模具采用的是条料,控制条料的送进方向采用导料销无测压装置。
控制条料的送进步距采用活动挡料销来定距。
(3)卸料、出件方式的选择倒装式复合模,采用弹性卸料,刚性出件。
(4)导向方式的选择为方便安装调整,同时为送料的方便,故采用后侧导柱模架。
五、主要零部件设计一、工作零件的设计(1)落料凹模凹模的厚度:H=kb(≥15mm)=0.30⨯80=24mm(参考文献①表2.9.5)凹模的壁厚:C=(1.5~2)H(≥30~40mm)凹模宽度:B=b+2c=80+2⨯40=160mm凹模长度:L=160mm(查参考文献②表 4.11标准JB/T7643.1-2008取得)凹模厚度:由上计算厚度24mm,将凹模版做成薄板形式并加空心垫板后厚度取14mm。
得凹模轮廓:160⨯160⨯14mm(2)凹凸模高度:L=h+h+2h=20+35+10=65mm1如下图式中:h为凹凸模固定板厚度(查参考文献②表4.111初选160⨯160⨯20mm),h弹性卸料板厚度(初选160⨯160⨯10mm),h2为增加高度(冲压时橡胶高32mm+凹凸模高过卸料板3mm=35mm)。
(3)冲孔凸模结合工件外形考虑加工,将凸模设计成直通式凸模,与凸模固定板按H7/m6配合。
其总长度:L=h+4h+5h=14+12+24=50mm3式中各参数如上图中:h凹模厚度、4h空心垫板厚度(查参考3文献②表4.11初选160⨯160⨯12mm)、h凸模固定板厚(查参考文5献②表4.11初选160⨯160⨯24mm)。
经查圆柱头直杆圆凸模标准,采用:50 JB/T 5825-2008 的凸模。
二、定位零件的设计(1)挡料销:因模具采用橡胶弹性卸料,且卸料橡胶安装高度36mm 较高。
为方便挡料,采用橡胶弹顶挡料销装置。
查参考文献①表2.9.7得挡料销高出卸料板3mm,卸料板厚10mm,故取挡料销H=14mm。
挡料销与卸料板采用H9/d9间隙配合。
(2)导料销:使用两个导料销,采用橡胶弹顶导料装置。
查参考文献①表2.9.7得导料销高出卸料板6~8mm,卸料板厚10mm,故取导料销H=18mm。
挡料销与卸料板采用H9/d9间隙配合。
三、出件装置的设计:采用刚性出件,由推杆直接推动推件块,将凹模内的工件推出。
根据推杆连接的各板高度,和模柄孔径查参考文献②表4.14.4取带肩推杆:A 12X140 JB/T 7650.1-2008。
推件块的周界尺寸和零件的周界尺寸相同,考虑凹模厚度、空心垫板厚度、及推杆安装、凹模修模量等因素,取高度16mm。
四、卸料部分的设计:卸料板:由活动挡料销和导料销安装高度:选用卸料板轮廓160⨯160⨯10mm卸料螺钉:模具采用橡胶弹性卸料橡胶由上可知橡胶孔直径12.5mm,查标准取M8X60 JB/T 7650.5-2008卸料钉尾部有足够的形成空间,卸料螺钉拧紧后,应使卸料板超出凹凸模端面1mm,有误差时通过在螺钉与卸料板之间安装垫片来调节。
五、模架及其它零部件的设计和选用模架:160X160X180~220 GB/T 2851-2008上模座:160X160X40 GB/T 2855.1-2008下模座:160X160X45 GB/T 2855.2-2008导柱:28X170 GB/T 2861.1-2008导套:28X100X38 GB/T 2861.3-2008凸凹模固定板:160X160X20 JB/T 7643.2-2008凸模固定板:160X160X24 JB/T 7643.2-2008上垫板:160X160X8 JB/T 7643.3-2008空心垫板:160X160X12模柄: B 50X110 JB/T 7646.1-2008该模具的闭和高度:H闭=H上模座+H垫+L+H+H下模座-h2=40+8+50+65+45-1=207mm式中:L为凸模长度50mm,H凹凸模厚度65mm,h2凸模进入凹凸模的深度1mm。
六、冲压设备的选定根据总冲压力F=333.55KN,模具闭合高度207mm,冲床工总作台面的尺寸,选用J23-40其主要设计参数如下:公称压力;400KN滑块行程:120mm最大装模高度:220mm工作台尺寸(前后⨯左右):480mm⨯710mm模柄孔尺寸; Φ50mm⨯70mm最大倾斜角度:30o机床工作台孔尺寸(直径⨯前后⨯左右):Φ250⨯150⨯300 Array因下模座外形尺寸(作台孔的尺寸故需加垫板:材料45见如右图的零件图。
七、设计小结作为模具专业的学生,课程设计是我们即将迈入社会的个人作业,也是对我们这专业知识一次总结与检验.设计最终完成,心理有一种说不出的轻松,设计过程中遇到了许多的问题,在老师及朋友的帮助下予以解决。
首先要感谢老师对我的指导和督促,给我指出了正确的设计方向,使我加深了对知识的理解,同时也避免了在设计过程中少走弯路。
总的来说通过本次课程设计还是受益匪浅。
首先,我对模具基本设计步骤以及相关参数的选用、计算及校核有了进一步的加深;其次,本次设计是对我们前面所学的知识的一次巩固与复习过程,使我们对以前所学知识有了更深一步的认识及运用。
本次课程设计也为我们以后走上工作岗位后的设计工作打下了一定的基础。
由于水平有限,难免会有错误,还望老师批评指正。
八、参考文献①李小海、王晓霞主编.模具设计与制造.电子工业出版社.2011②杨关全、匡余华.冷冲模设计资料与设计指导(第二版).大连:大连理工大学出版社,2009。
③模具设计与制造简明手册、冷冲压模具结构图册。
④刘家平主编. 机械制图.武汉理工大学出版社2008。
○5工程材料与热加工基础。
○6公差配合与测量技术。
○7工程力学。