双频容性耦合等离子体刻蚀工艺的物理基础
双频容性耦合等离子体物理特性的研究

u i
e me
E νinui
Poisson equation :
2 V e
0
ne ni
E V
离子在鞘层中受鞘层电场的运动
Solving the Newtonequations
dx j dt
vj(xj,t)
dv j dt
e mi
E(xj,t)
j 1,....N
Se 2en0uB e c
Using the energy balance, Se S ohm S stoc , one can get:
n0
me
vcd 2ve
e2uB e c
1/ 2
J l2
J
2 h
or
n0
E(x,t)
x j0, v j0 x j (t),v j (t)
xj, vj
Ion positions xj(t) and velocities vj(t) between two contiguous collisions.
s(t) s sl sin(lt) sh sin(ht)
w here
sl
Jl
en0l
,
sh
Jh ,
en0h
sheath voltage drop:
s
sl
s h
Vsh
(t)
en0
2 0
sl
1
s in(l t )
sh 1
sin(ht)2
高频电源----快速振荡 低频电源----振荡的轮廓线
0 等离子刻蚀工艺原理介绍

Feed Gases
BCl3/Cl2 HBr/Cl2
Comments
Cl etches Si, B improves passivation HBr provides passiviation and selectivity to PR, Cl2 providdes main etchants O2 improves selectivity to SiO2 Higher etch rate, good oxide selectivity, isotropic High etch rate, but isotropic Good profile control for deep trench
--- Process Time
工艺控制和结果
工艺可控变量 Plasma 参数 结果
Temperature Gas Flows
Gas density Residence time
Etch Rate Uniformity Selectivity
Pressure
Power Time (Magnetic Field) BSC He (Gap)
Bias 功率的作用: 离子能量
功率 --> 控制离子浓度/能量。提高 Bias 功率,提高腐蚀速率。
Bias 低离子能量
--> 低的碰撞速度。
离子能量影响方向性
--> 高离子能量意 味着离子更少偏离原来运动方向。
问答
Q&A
HBr/Cl2/O2 SF6 NF3 HBr/NF3/O2
Metal Etch平衡图
物理
离子轰击
BCl3+
化学腐蚀
Cl*
化学淀积
双频容性耦合等离子体简介.

4
双频容性耦合电源示意图
双频容性耦合等离子体源示意图
5
双频容性耦合等离子体
在电源偏压 Vrf 一定的条件下,等离子体密度 n 正 比于电源频率ω 的平方,即
n Vrf
2
结论:DF-CCP源中高频电源的频率决定了等离子 体的离子密度。
6
双频容性耦合等离子体
在极板相邻的区域会产生等离子体鞘层,形成一 个电场强度E很大,方向从等离子体区域指向极板 的鞘层电场,由于离子运动速度慢,其穿越鞘层 电场所用时间大于高频源的周期,因此离子只响 应高频平均电场,故而高频源对离子能量的控制 有限。为有效控制鞘层区域中离子的运动,需要 降低电源的频率。
•双频容性耦合等离子体
1
容性耦合和感性耦合等离子体放电
CCP:放电空间相对于电源 为电容区域,依靠两端形成 的电场供电
ICP :放电空间相对于电源 处在电感内,依靠激发磁场 感应出的环形电场供电
2
研究双频容性耦合等离子体的意义
在传统的单频容性耦合等离子体 中,如果想要提高等离子体密度, 就需要提高施加的偏压,这样会 导致离子获得更高的能量,高能 离子轰击到用于刻蚀的基片上时 会损害基片。但不施加高偏压, 会使等离子体密度不高,刻蚀速 率低。 寻求解决办法:
12
实际应用中所用DF-CCP源频率和其他发展
工程应用中常用到的频率组合为60MHz/2MHz、 27.1MHz/2MHz、和160MHz/13.56MHz 在 研 究 内 容 中 , 除 上 述 , 对 工 频 ( 50Hz ) 、 9600Hz的交流电乃至直流电源,脉冲电源的耦合 也有研究。进一步有对于三源供电CCP的研究
VLF VHF
等离子体蚀刻技术

等离子体蚀刻技术等离子体蚀刻技术是一种常用的微纳加工技术,广泛应用于半导体、光电子、微电子等领域。
本文将从等离子体蚀刻技术的基本原理、设备和工艺参数的选择以及应用领域等方面进行介绍。
一、等离子体蚀刻技术的基本原理等离子体蚀刻技术是利用高能粒子或分子束对材料表面进行刻蚀的一种方法。
其基本原理是通过在低压气体环境中产生等离子体,利用等离子体中的离子轰击材料表面,使其发生化学反应或物理过程,从而实现对材料表面的刻蚀。
等离子体蚀刻技术具有高精度、高选择性和高均匀性等优点,能够实现微纳米级的加工。
二、等离子体蚀刻设备等离子体蚀刻设备主要由气体供给系统、真空系统、射频功率源、电极系统以及控制系统等组成。
其中,气体供给系统用于提供刻蚀气体,真空系统用于提供蚀刻环境,射频功率源用于产生等离子体,电极系统用于加速和聚焦离子束,控制系统用于控制蚀刻过程的参数。
三、等离子体蚀刻工艺参数的选择等离子体蚀刻工艺参数的选择对于实现理想的加工效果至关重要。
其中,气体种类和流量、工作压力、射频功率和电极系统的设计等是需要考虑的关键因素。
不同材料的刻蚀速率和选择性不同,需要根据具体材料的特性和加工要求进行合理选择。
四、等离子体蚀刻的应用领域等离子体蚀刻技术在半导体、光电子、微电子等领域具有广泛的应用。
在半导体行业中,等离子体蚀刻技术常用于制备集成电路和光刻掩膜等工艺步骤。
在光电子领域,等离子体蚀刻技术可以用于制备光波导器件和微结构等。
在微电子领域,等离子体蚀刻技术可以用于制备微机械系统(MEMS)和纳米加工等。
等离子体蚀刻技术是一种重要的微纳加工技术,具有广泛的应用前景。
通过合理选择蚀刻工艺参数和设备设计,可以实现高精度、高选择性和高均匀性的加工效果。
随着科技的不断进步,相信等离子体蚀刻技术将在微纳加工领域发挥更加重要的作用。
icp刻蚀工艺
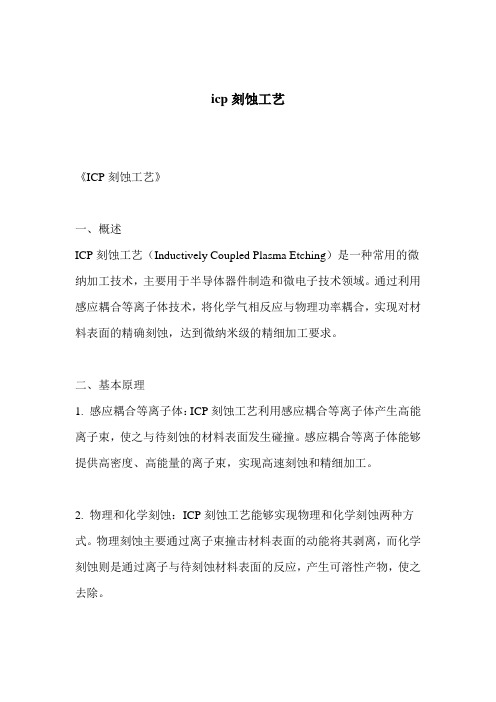
icp刻蚀工艺《ICP刻蚀工艺》一、概述ICP刻蚀工艺(Inductively Coupled Plasma Etching)是一种常用的微纳加工技术,主要用于半导体器件制造和微电子技术领域。
通过利用感应耦合等离子体技术,将化学气相反应与物理功率耦合,实现对材料表面的精确刻蚀,达到微纳米级的精细加工要求。
二、基本原理1. 感应耦合等离子体:ICP刻蚀工艺利用感应耦合等离子体产生高能离子束,使之与待刻蚀的材料表面发生碰撞。
感应耦合等离子体能够提供高密度、高能量的离子束,实现高速刻蚀和精细加工。
2. 物理和化学刻蚀:ICP刻蚀工艺能够实现物理和化学刻蚀两种方式。
物理刻蚀主要通过离子束撞击材料表面的动能将其剥离,而化学刻蚀则是通过离子与待刻蚀材料表面的反应,产生可溶性产物,使之去除。
三、工艺参数与优势1. 工艺参数:a. 感应耦合功率:控制等离子体的产生与稳定;b. 气体流量与压强:控制刻蚀速率和刻蚀副产物的清除;c. 工艺时间:控制刻蚀深度和精度。
2. 优势:a. 高选择性:可实现不同材料之间的精确刻蚀,避免交叉感染和混合。
b. 高加工精度:微纳米级的刻蚀精度,可满足高精度的器件制造需求。
c. 高刻蚀速率:ICP刻蚀工艺的高功率和高能离子束能够实现高速刻蚀,提高生产效率。
d. 低表面损伤:在刻蚀过程中,ICP蚀刻工艺可以减少表面损伤和变形,保持器件性能稳定。
四、应用领域ICP刻蚀工艺在微电子器件、光学器件、MEMS(微机电系统)等领域有着广泛的应用:1. 半导体器件制造:可用于晶圆制程中的多种工艺步骤,如图案形成、沉积物去除等。
2. 光学器件制造:用于光栅、波导等光学元件的制备,实现高精度的微纳米级加工。
3. MEMS制造:用于微结构的制备,如微机械系统的零件刻蚀、多层刻蚀等。
五、总结ICP刻蚀工艺作为一种高精度、高效率的微纳加工技术,在半导体和微电子领域扮演着重要角色。
通过精确控制工艺参数,ICP刻蚀工艺可以实现各种材料的精细刻蚀,满足各类器件的制造需求。
等离子体刻蚀工艺的物理基础

等离子体刻蚀工艺的物理基础一、本文概述等离子体刻蚀工艺,作为一种先进的微纳加工技术,在半导体工业、纳米科学、生物医学以及众多其他高科技领域中发挥着日益重要的作用。
本文将深入探讨等离子体刻蚀工艺的物理基础,以期帮助读者更好地理解这一技术的核心原理和应用价值。
等离子体,作为物质的第四态,具有独特的物理和化学性质,如高活性、高电离度和良好的导电性等。
这些特性使得等离子体在刻蚀过程中具有优异的定向性和可控性,从而能够实现对材料表面的高精度、高效率的刻蚀加工。
本文将从等离子体的基本性质出发,介绍等离子体刻蚀的基本原理和过程,包括等离子体的产生、传输、与材料表面的相互作用等。
同时,我们还将讨论影响等离子体刻蚀效果的关键因素,如等离子体参数、气体种类、刻蚀环境等,并探讨如何优化这些参数以提高刻蚀质量。
本文还将对等离子体刻蚀在不同领域的应用进行概述,包括半导体集成电路制造、微纳器件加工、生物医学材料制备等。
通过对这些应用案例的分析,我们将进一步展示等离子体刻蚀工艺的重要性和潜力。
我们将对等离子体刻蚀工艺的未来发展趋势进行展望,探讨新技术、新材料和新工艺对这一领域的影响和推动,以期为读者提供一个全面、深入的等离子体刻蚀工艺物理基础的认识。
二、等离子体基础知识等离子体,通常被称为物质的第四态(除固态、液态和气态外),是一种高度电离的气体,其中包含大量的正离子和电子,且整体呈电中性。
等离子体的特性使其成为许多先进工艺,包括等离子体刻蚀工艺的重要工具。
等离子体的形成:等离子体可以通过多种方式形成,包括加热气体使其部分或完全电离,或通过施加电场或射频场来激发气体。
在刻蚀工艺中,通常使用射频放电或直流放电来产生等离子体。
电中性:尽管等离子体中包含大量的带电粒子,但由于正离子和电子的数量大致相等,所以整体呈电中性。
高导电性:由于含有大量的可动带电粒子,等离子体具有很高的导电性。
集体行为:等离子体中的粒子行为通常表现出集体性,即大量粒子的行为可以看作是一个整体。
双频容性耦合等离子体刻蚀工艺的物理基础
100%
化学反应
等离子体中的活性粒子与材料表 面发生化学反应,生成挥发性物 质。
80%
离子注入
高能离子注入材料表面,引起晶 格畸变和缺陷形成。
双频容性耦合等离子体刻蚀的增强机制
双频共振
通过双频电源激发等离子体, 使电子在两个频率下共振,提 高等离子体密度和活性。
耦合效应
两个频率的电场在空间上产生 叠加,增强电场强度,促进电 子碰撞和激发。
等离子体刻蚀技术简介
等离子体刻蚀是一种广泛应用的微纳 加工技术,利用等离子体中的活性粒 子与材料表面发生化学或物理反应, 实现材料的去除或改性。
等离子体刻蚀技术具有高精度、高效 率、低损伤等特点,被广泛应用于微 电子、纳米科技、光电子等领域。
等离子体刻蚀技术简介
等离子体刻蚀是一种广泛应用的微纳 加工技术,利用等离子体中的活性粒 子与材料表面发生化学或物理反应, 实现材料的去除或改性。
主题简介
双频容性耦合等离子体刻蚀工艺是一种先进的半导体制造工艺, 用于在硅片上刻蚀微细结构。
该工艺利用高频电场激发的等离子体进行刻蚀,具有高精度、高 效率和高一致性的特点。
研究背景和意义
随着半导体技术的不断发展,对微细结构刻蚀的要求越来越高,传统的刻蚀方法 已经难以满足需求。
双频容性耦合等离子体刻蚀工艺作为一种新兴技术,具有广阔的应用前景和市场 价值,因此对其物理基础进行研究具有重要的理论意义和实际应用价值。
研究成果总结
成功实现了双频容性耦 合等离子体刻蚀工艺, 提高了刻蚀速率和均匀 性。
深入研究了等离子体中 各种粒子的行为,揭示 了刻蚀过程的物理机制 。
通过实验和模拟相结合 的方法,验证了理论模 型的正确性和有效性。
等离子体刻蚀工艺的物理基础
等离子体刻蚀工艺的物理基础随着科技的不断发展,等离子体刻蚀工艺已经成为微电子、纳米科技、光电子等领域中不可或缺的关键技术。
本文将深入探讨等离子体刻蚀工艺的物理基础,包括基本概念、应用领域、技术细节以及未来发展趋势等方面。
等离子体刻蚀工艺是一种利用等离子体中的高速粒子对材料进行物理轰击,从而去除表面污染或刻蚀特定图形的工艺方法。
刻蚀过程中,目标材料表面的原子在等离子体粒子的撞击下获得足够的能量,从表面脱离或被溅射,最终形成刻蚀图案或去除污染物。
等离子体刻蚀工艺的基本原理是能量传递。
当高速的等离子体粒子撞击目标材料表面时,会将其能量传递给表面原子。
当这些原子的能量超过其结合能时,便会从表面脱附或被溅射。
这一过程可在气体辉光放电或电感耦合等条件下进行。
在等离子体刻蚀工艺中,有几个基本概念需要理解。
首先是刻蚀速率,它表示单位时间内材料表面的去除速率;其次是选择比,指不同材料在同样的刻蚀条件下,刻蚀速率的比值;还有刻蚀均匀性和刻蚀终止层厚度,它们分别表示刻蚀过程中材料表面受影响的均匀程度和刻蚀深度。
等离子体刻蚀工艺广泛应用于微电子、纳米科技、光电子等领域。
在微电子领域,等离子体刻蚀工艺被用于制造集成电路和半导体器件,如动态随机存储器(DRAM)和互补金属氧化物半导体(CMOS)等。
在纳米科技领域,等离子体刻蚀工艺被用于制造纳米材料、纳米器件以及纳米结构的加工。
在光电子领域,等离子体刻蚀工艺被用于制造光电子器件,如激光器、光电检测器等。
随着科技的发展,市场对等离子体刻蚀工艺的需求也在不断增加。
为了满足市场需求,业界不断研发新的等离子体刻蚀技术,以提高刻蚀速率、选择比、刻蚀均匀性和终止层厚度等指标。
在等离子体刻蚀工艺的发展历程中,出现了多种技术,如反应离子束刻蚀(RIBE)、磁控溅射刻蚀(MSPE)、电子回旋共振刻蚀(ECR)等。
这些技术在不同的应用领域有着各自的优势和局限。
高质量的等离子体刻蚀工艺需要精确控制技术参数,如等离子体的密度、温度、电场强度等。
电容耦合等离子体刻蚀
电容耦合等离子体刻蚀
电容耦合等离子体刻蚀(Capacitively Coupled Plasma Etching,CCP)是一种常见的半导体微电子加工技术,其基本原理是在气体中产生等离子体,利用等离子体的化学反应和化学剥蚀作用来实现对半导体材料的加工和刻蚀。
CCP刻蚀技术主要由以下几个步骤组成:首先,将要加工的半导体样品放入到一个真空室内,并注入加工气体,通过加热、电子轰击等方式激发加工气体产生等离子体。
等离子体中的离子和电子将对半导体材料表面进行反应,并与表面的原子或分子结合,形成一种新的化合物。
最后,通过控制等离子体的参数,如电场强度、气体流量、温度等,实现对半导体样品表面的精确刻蚀。
CCP刻蚀技术有许多优点,例如可以实现高速、高精度的半导体加工,可以实现对复杂结构的微细加工,还可以对不同的材料进行加工。
同时,CCP刻蚀技术也有一些缺点,如需要高度专业的技术支持和昂贵的设备成本,同时还有一些安全风险问题,如氢气爆炸等。
CCP简介
12ቤተ መጻሕፍቲ ባይዱ
专心 专业 专注
目录
射频容性耦合等离子体(CCP)源介绍 Plasma系统构成 单频CCP源 双频CCP源
13
专心 专业 专注
Plasma系统构成
Gas
Power
Pump Operation
Plasma系统结构五大块: 1. 2. 3. 4. 5.
14
H2线Plasma系统
电源系统 真空系统 供气系统 执行装置 PLC控制
Target
Ion Source
Ion beam
Substrate
Substrate
Deposite d materials
PECVD:有机金属化合物的气体 形成等离子体状态作用于材料表 面,并在材料表面反应产生一薄 层沉积物。
10
PVD 溅射:等离子体在电场作 用下轰击靶材,溅射出的原子 沉积在基片表面形成薄膜。
26
专心 专业 专注
单频CCP在OLED基板方面的应用
ITO性能分析 掺杂比例 光 ITO性能 优 优 载流子浓度 大 电 优 载流子速率 大 载流子浓度 小 膜厚 掺杂比例 膜厚 结构缺陷 形貌 锡铟比1:9最优 反应磁控溅射 薄
锡铟比1:9最优
厚 少 粗糙度小
背底真空度 氩氧比例及流量 电源功率 膜厚控制
未处理
机械抛光 Ar等离子体 O等离子体 王水 王水/O等离子体
16.1
16.3 16.7/17.3/17.0 16.4/15.0/16.4 18.5/23.5/28.6 27.7
4.5
4.2 4.5 4.35/4.75/4.65 4.6/4.3/4.7 4.6
2.6
2.3 10.9/15.4/23.0 1.4/1.4/2.1 3.8/8.4/8.8 6.0
- 1、下载文档前请自行甄别文档内容的完整性,平台不提供额外的编辑、内容补充、找答案等附加服务。
- 2、"仅部分预览"的文档,不可在线预览部分如存在完整性等问题,可反馈申请退款(可完整预览的文档不适用该条件!)。
- 3、如文档侵犯您的权益,请联系客服反馈,我们会尽快为您处理(人工客服工作时间:9:00-18:30)。
王 友年
* 国家自然科学基金重点项目资助课题
内容
一、等离子体刻蚀技术的发展趋势及存在的问题 二、几种有代表性的等离子体源 三、描述 DF-CCP物理过程的解析模型 四、描述 DF-CCP物理过程的混合模型 五、直流偏压效应 六、有关实验工作进展
一、等离子体刻蚀技术的发展趋势及问题
2、微波电子回旋共振(ECR)/RF偏压等离子体刻蚀源
3、射频感应耦合等离子体( ICP)/RF偏压刻蚀源
平面线圈感应耦合等离子体源
coil
wafer
RF biased electrode Insulating plate
• 主电源(连接在线圈)控制等离子体的状态; • 偏压电源(施加在芯片台上)控制离子轰击晶片上的能
500-3000 W • discharge pressure p ~30-300 mTorr
驻波效应:
在超高频情况下,电磁波的波长l可以与放电装置的反应腔 室(或电极半径)R相当,从而可以在等离子体腔室内部激 发一个径向传播的电磁波,即驻波,引起等离子体密度径向 不均匀性。这对芯片刻蚀的均匀性影响很大。
根据熟知的定标关系可知:等离子体密度正比于驱 动电源频率的平方和施加的偏压,即
n 2Vrf
当电源频率w一定时, 要提高等离子体密度,唯一的 途径是增加施加偏压。但增加施加的射频偏压时,轰 击到晶片上的离子能量也随着增加。太高的离子能量, 将对晶片造成不必要的介质损伤。
早期使用的都是单一频率射频电源(13.56MHz) 驱动放电的CCP源,很难实现对等离子体密度(正比 于刻蚀率)和入射到晶片上离子的能量分布的独立控 制。
目前一些半导体设备制造公司已经研制出或正在 研制这种等离子体刻蚀设备,如: 1)美国的Lam(泛林)公司 2)美国Applied Materials公司 3)日本Tokyo Electron 4)中微(上海)半导体设备制造有限公司(AMEC )
DF-CCP sources
SCCM-TE (TEL)
▶ PR Selectivity : Heated top electrode
▶ VHF Dual-CCP : Very High Freq. 3.2cm, 30mT
▶ High E/R & PR Sel. :
目前对这种双频CCP放电的物理过程和相应的刻蚀 机理,仍有很多问题需要研究, 如: 1)两个电源的频率匹配问题,
• 实验 (或工艺) 研究 • 计算机仿真模拟
二、几种有代表性的等离子体刻蚀源
1、平板式是射频容性耦合等离子体(CCP)源
抽气
进气
介质
plasma
电极
RF power 13.56MHz
开始于上个世纪70年 代,主要用于反应性 等离子体刻蚀工艺。
单频CCP源的主要优点: 1.工作气压比较低(mTorr) 2.能够产生比较均匀的 plasma 3.结构简单,造价低 .
Exelan-CFE (Lam)
Enalber (AMT)
D92 SAC Etcher
~ 60MHz
~
▶ Dual-CCP 4.5cm, 30mT
▶ Uniformity : - Dual cathodeFra bibliotek2MHz
D92 SiN mask Etcher
-
~
162MHz
~ 13.56MHz
▶ Narrow Dual-CCP : 2.0cm, 40mT
对等离子体源的要求:
•高的刻蚀率 •高度的均匀性 •高度的各向异性 •高度的选择性 •较低的介质损伤
• 均匀性
刻蚀的均匀性包含两层意思: 1)宏观的不均匀性:在晶片的径向上造成的刻蚀率和刻蚀剖 面的不均匀 性。 2)微观不均匀性:在每个微槽的底部和侧面造成的刻蚀不均匀性。
等离子体密度
0
R
为了适应纳电子器件的制备工艺,必须要: 1)提出大面积、高密度、均匀等离子体的新方法; 2)提出优化刻蚀工艺的新方法。
27MH/1MHz, 27MH/2MHz,60MHz/2MHz? 2)两个电源的施加方式,
施加在同一个电极,还是分别在两个电极? 3)高频电源的频率到达多高为好?
驻波效应?如何匹配电源的频率和腔室的半径?
Typical operating conditions for dielectric etching on 200-300 mm silicon wafers are:
4、双频电容耦合等离子体(DF-CCP)源
Upper electrode
Plasma
lower electrode
LF source
HF source
DF-CCP 源
(2000年---)
1)高频电源控制等离子 体密度、低频电源控制 离子的能量。
2)产生高密度、大面积 均匀等离子体;
3)实现对绝缘体SiO2的刻 蚀。
低温等离子体刻蚀技术在微纳制造工艺中得到广泛地应 用,如超大规模集成电路、微机械系统、微光学系统的制
备。
1)半导体芯片加工 2)微电机系统(MEMS)加工 3)平板显示器的加工 4)衍射光栅的制备
微结构
微齿轮
等离子体刻蚀工艺的趋势
集成电路发展趋势:
•加工晶圆的面积更大 •特征尺寸越来越小 •集成度越来越高
• discharge radius: R~15-25 cm • plate separation l~1-5cm • high frequency fh ~27.1-160 MHz • low frequency fl ~ 2-13.6 MHz • high-frequency voltage amplitude |Vh| ~250-1000 V • low-frequency voltage amplitude |Vl| ~500-3000 V • powers for both low- and high-frequency sources:
量分布。
感应耦合等离子体(ICP)源的特点
特点
解决的问题
•工作气压低( < 2Pa )
•提高各向异性刻蚀
•等离子体密度高(1011 cm-3~1012cm-3)
•提高离子流密度 •提高刻蚀率
•产生等离子体的射 频源与基片台射频源 独立控制
•提高刻蚀的选择性 •降低晶圆介质损伤
问题: 1)适于刻蚀金属、半导体材料; 2)产生大面积的均匀性等离子体比较困难。