14第十四章 孔加工刀具
点位加工的刀具种类及操作子类型4

点位加工的刀具种类及操作子类型一、点位加工的刀具种类及使用场合刀具类型:Drill(孔加工刀具)(共9种)⑴SPOTFACING_TOOL(键槽铣刀)点-面刀具(键槽铣刀):用于在斜面或曲面上孔口的加工⑵SPOTDRILLING_TOOL(中心钻)中心钻:对于孔位置精度要求高的孔加工,用于钻预钻孔。
⑶DRILLING_TOOL(麻花钻)麻花钻:孔精度要求不高的孔加工,或粗加工孔。
⑷BORING_BAR(镗刀)镗刀:对于直径较大的孔,通常用镗刀对孔进行精加工。
⑸REAMER(铰刀)铰刀:对于直径较小的孔,通常用铰刀对孔进行精加工。
⑹COUNTERBORING_TOOL(沉头孔刀具)沉头孔刀具:用于加工沉头孔(圆柱内六角螺钉安装孔)⑺COUNTERSINKING_TOOL(锪孔钻)锪孔钻:用于孔口锪孔(平肩埋头孔)⑻TAP(攻丝用丝锥)丝锥:用于攻丝(加工内螺纹)⑼THREAD_MILL(螺纹铣刀)螺纹铣刀:用于高速铣螺纹。
二、点位操作子类型⑴SPOT_FACING:(铣孔口平面)。
锪平面,使用键槽铣刀。
⑵SPOT_DRILLING:中心钻,使用中心钻头钻导向位置。
⑶DRILLING:钻孔。
使用麻花钻钻孔。
⑷PECK_DRILLING:(啄孔)深孔钻削。
刀具回退到最小安全平面。
⑸BREAKCHIP_DRILLING: 断削钻。
刀具回退较小的距离。
⑹BORING :镗孔。
使用镗刀镗孔。
⑺REAMING:铰孔。
使用铰刀铰孔。
⑻COUNTERBORING:钻沉头孔。
圆柱(内六角)沉头螺孔。
⑼COUNTERSINKING:锪孔。
平肩沉头孔⑽TAPPING :攻丝。
使用丝攻加工螺纹孔。
⑾THREAD_MILLING :铣螺纹孔。
三、相关参数的设置1、刀具与刀轴设置2、刀轨设置⑴Avoid避让允许你规定部件内夹具或障碍之上的刀具间隙。
⑵切削与速度四、举例工艺流程:⑴钻定位孔(中心孔)⑵钻螺纹底孔φ8.5及攻丝M10⑶钻埋头孔(φ8、φ14)⑷加工φ25孔(钻φ8、扩φ24.5、镗φ25)作业:1、点位加工使用刀具类型有哪些?2、点位操作子类型有哪些?。
通孔加工刀具的探讨

1 大 孔 刀具 设 计 探 讨
3. 0 1并倒 角;1 55± . 0序 2工步 :精铰孔径 ;2 0序 :重新装夹 采用一个普通倒 角刀加工下倒角。这样加工节拍 比较 长 ,加工 成 本 也会 比较 高 ,如 果 工 件 比 较 大 ,还 需 要 采 用 两 台机 床 完 成
加工。
但是换一个角度去考虑 问题 ,改变刀具的结构 ,设计组 合 镗刀 ,只要刀具方案设计合 理 ,可以减少刀具数量 ,减少加 工 节拍 ,提升 加工效 率 ,如 图 2所示 ,刀具 由 3个加 工部 分 组 成 ,前端 由 2个 刀 片 组 成 ,作 为粗 加 工 刀 ,刀 片 选 用 普 通 硬 质
通 孔加 工 刀具 的探 讨
欧 阳森
( 江德 利化 油 器有 限公 司 ,广 东湛江 54 4 ) 湛 2 0 3
摘要 :通孔刀具 的设计应用特别讲究 ,不同的设计方案对加工成本 、质量 的控制 的影 响非常大 。根据孔径 的大小 ,设 计不 同
结构 的刀具 ,减少刀具数量 ,使加工成本降到最低 。 关键词 :加工 ;工艺设计 ;镗刀 ;铰 刀 Thr u h. o e Pr c s e h te s us i n o g h l o e s s t e Cu t r Dic so
m m,最 常 用 的 加 工 方法 是 :第 一 步 :硬 质 合 金 阶 梯 钻 ( 4 图 )
图 5 精 加,设计粗精 加工一体 P D铰 C 刀 ,可 以把通 孔粗精加工合并在 一起 完成 ,减少一把刀具 的使
孔加工(中文)

页码 规格 切削参数
型号
钻头外形
P
软钢 普通钢
M K N S H
不锈钢 铸铁 有色金属 耐热合金 高硬度钢
1534SU03 1534SU03C 1734SU03C 通用加工 麻花钻 1536SU05 1536SU05C 1736SU05C
外冷 内冷 内冷 外冷 内冷 内冷 内冷 外冷 内冷 内冷 内冷 内冷 外冷 外冷 外冷 外冷 内冷 外冷 外冷
2 C
孔加工刀具
钻削刀具
钻削刀具一览表 整体硬质合金钻头
整体硬质合金钻头牌号介绍 整体硬质合金钻头命名规则 整体硬质合金钻头明细表 整体硬质合金钻头推荐切削参数 整体硬质合金钻头技术信息 整体硬质合金钻头非标订制
C4 C5-C94
C5 C6 C7-C71 C72-C82 C83-C89 C90-C94
l3
14 23 23 14 23 23 14 23 23 14 23 23 14 23 23 14 23 23 14 23 23 14 23 23
l4
36 36 36 36 36 36 36 36 36 36 36 36 36 36 36 36 36 36 36 36 36 36 36 36
KDG303
Mechanial Units
2000 1500 1000 500 0 -500
冷却方式:乳化液(内冷)
SU切削力测试图
SU系列麻花钻与国外A公司同类产品的应用情况对比
1250 1000
刀 具 型 号 :1534SU03-1000 尺 寸:Ø10mm 被加工材料:42CrMo(HRC35) 切 削 速 度 :100m/min 转 速:3200r/min 每转进给量:0.20mm/r 进 给 速 度 :640mm/min 钻 削 深 度 :30mm(L/D=3) 冷 却 方 式 :水溶性冷却液(外冷) 加 工 机 床 :Mikron UCP 1000
加工中心刀具怎么选择合适的?

加工中心刀具怎么选择合适的?加工中心刀具怎么选择合适的?加工中心刀具主要分为铣削刀具和孔加工刀具两大类。
铣削刀具的选择主要是铣刀型别和铣刀尺寸的选择。
铣刀型别应与工件表面形状与尺寸相适应。
加工较大的平面应选择面铣刀;加工凹槽或者是较小的台阶及平面轮廓时应选择立铣刀;加工曲面应选择球头铣刀;加工模具型腔或凸模成形表面等多选用模具铣刀;加工封闭的键槽选择键槽铣刀;加工变斜角面应选用鼓形铣刀;加工各种直的或圆弧形的凹槽、斜角面、特殊孔等应选用成形铣刀。
当粗铣或铣不重要的加工平面时,可使用粗齿铣刀;当精铣时,可选用密齿铣刀,用小进给量达到低的表面粗糙度;当铣材料较硬的金属时,必须选用密齿铣刀,同时进给量要小,以防止振动。
铣刀尺寸也应与被加工工件的表面尺寸和形状相适应。
刀具直径的选用主要取决于装置的规格和工件的加工尺寸,另外还要考虑刀具所需功率应在机床功率范围之内。
粗铣时铣刀直径要小些,精铣时铣刀直径要尽量大些,最好能够包容整个加工宽度。
表面要求高时,还可以选择使用具有修光效果的刀片。
而孔加工刀具可分为钻孔刀具、镗孔刀具、扩孔刀具和铰孔刀具。
(1)钻孔刀具较多,主要有普通麻花钻、可转位浅孔钻以及扁钻。
用加工中心钻孔通常都会采用普通麻花钻,普通麻花钻主要由工作部分和柄部组成的。
刀具柄部分为直柄和锥柄两种。
直柄工具的刀柄主要是弹簧夹头刀柄,其具有自动定心、自动消除偏摆的优点,所以小规格的刀具最好选用该型别。
而工作部分包括切削部分和导向部分,所示,麻花钻的切削部分有2个主切削刃、2个副切削刃、1个横刃。
麻花钻的导向部位起导向、修光排屑和输送切削液作用。
麻花钻一般用于精度较低孔的粗加工,由于加工中心所用夹具没有钻套定心导向,钻头在高速旋转切削时容易会发生偏摆运动,而且钻头的横刃长,所以在钻孔时,要用中心钻打中心孔,用以引正钻头。
(2)镗削的主要特点是获得精确的孔的位置尺寸,得到高精度的圆度、圆柱度和表面粗糙度,所以,对精度较高的孔可用镗刀来保证。
4、孔加工(教案)

课题4:孔加工4.1任务:完成图所示零件上2-¢0.01510 孔及2-M8螺纹加工,毛坯为80mm×60mm×36mm长方块(其余面已经加工),材料为45钢,单件生产。
4.2 孔加工的工艺知识1.孔加工的方法孔加工在金属切削中占有很大的比重,应用广泛。
在数控铣床上加工孔的方法很多,根据孔的尺寸精度、位置精度及表面粗糙度等要求,一般有点孔、钻孔、扩孔,锪孔、铰孔、镗孔及铣孔等方法。
2.孔加工的刀具1)钻孔刀具及其选择钻孔刀具较多,有普通麻花钻、可转位浅孔钻、喷吸钻及扁钻等。
应根据工件材料、加工尺寸及加工质量要求等合理选用。
在数控镗铣床上钻孔,普通麻花钻应用最广泛,尤其是加工¢30mm以下的孔时,以麻花钻为主,如图6-2所示。
图6-2 普通麻花钻在数控镗铣床上钻孔,因无钻模导向,受两种切削刃上切削力不对称的影响,容易引起钻孔偏斜。
为保证孔的位置精度,在钻孔前最好先用中心钻钻一中心孔,或用一刚性较好的短钻头钻一窝。
中心钻主要用于孔的定位,由于切削部分的直径较小,所以中心钻钻孔时,应选取较高的转速。
对深径比大于5而小于100的深孔由于加工中散热差,排屑困难,钻杆刚性差,易使刀具损坏和引起孔的轴线偏斜,影响加工精度和生产率,故应选用深孔刀具加工。
2)扩孔刀具及其选择扩孔多采用扩孔钻,也有用立铣刀或镗刀扩孔。
扩孔钻可用来扩大孔径,提高孔加工精度。
用扩孔钻扩孔精度可达IT11~IT10,表面粗糙度值可达Ra6.3~3.2um。
扩孔钻与麻花钻相似,但齿数较多,一般为3~4个齿。
扩孔钻加工余量小,主切削刃较短,无需延伸到中心,无横刃,加之齿数较多,可选择较大的切削用量。
图6-3所示为整体式扩孔钻和套式扩孔钻。
3)铰孔刀具及其选择铰孔加工精度一般可达IT9~IT8级,孔的表面粗糙度值可达Ra1.6~0.8um ,可用于孔的精加工,也可用于磨孔或研孔前的预加工。
铰孔只能提高孔的尺寸精度、形状精度和减小表面粗糙度值,而不能提高孔的位置精度。
孔加工刀具
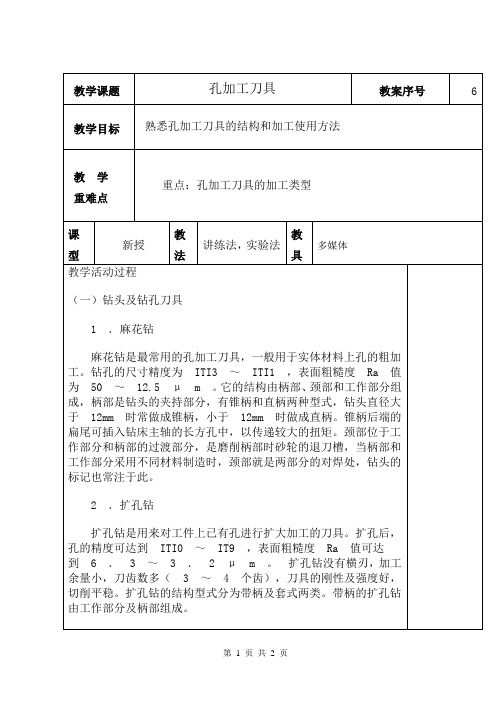
孔加工刀具
教案序号
6
教学目标
熟悉孔加工刀具的结构和加工使用方法
教 学
重难点
重点:孔加工刀具的加工类型
课型
新授
教法
讲练法,实验法教具Fra bibliotek多媒体
教学活动过程
(1)钻头及钻孔刀具
1 .麻花钻
麻花钻是最常用的孔加工刀具,一般用于实体材料上孔的粗加工。钻孔的尺寸精度为 ITI3 ~ ITI1 ,表面粗糙度 Ra 值为 50 ~ 12.5 μ m 。它的结构由柄部、颈部和工作部分组成,柄部是钻头的夹持部分,有锥柄和直柄两种型式,钻头直径大于 12mm 时常做成锥柄,小于 12mm 时做成直柄。锥柄后端的扁尾可插入钻床主轴的长方孔中,以传递较大的扭矩。颈部位于工作部分和柄部的过渡部分,是磨削柄部时砂轮的退刀槽,当柄部和工作部分采用不同材料制造时,颈部就是两部分的对焊处,钻头的标记也常注于此。
3 .铰刀
铰刀是一种半精加工或精加工孔的常用刀具,铰刀的刀齿数多 (4~12 个齿 ) ,加工余量小,导向性好,刚性大。铰孔后孔的精度可达 IT9~IT7 ,表面粗糙度达 1.6~0.4 μ m ,常见的铰刀结构如图。
4 .镗刀
镗孔是常用的加工方法,其加工范围很广,既可进行粗加工,也可进行精加工。镗刀的种类很多,根据结构特点及使用方式,可分为单刃镗刀和双刃镗刀等。
课后记:首先利用视频和图片来引入真实的道具,激发学生的学习兴趣;通过动画播放展示孔加工刀具的结构和安装,让学生掌握各种情况下的孔加工刀具的拆卸方法;并以实际加工特征让学生讨论安装和拆卸刀具。
2 .扩孔钻
扩孔钻是用来对工件上已有孔进行扩大加工的刀具。扩孔后,孔的精度可达到 ITI0 ~ IT9 ,表面粗糙度 Ra 值可达到 6 . 3 ~ 3 . 2 μ m 。 扩孔钻没有横刃,加工余量小,刀齿数多( 3 ~ 4 个齿),刀具的刚性及强度好,切削平稳。扩孔钻的结构型式分为带柄及套式两类。带柄的扩孔钻由工作部分及柄部组成。
孔加工刀具及方法
孔加工刀具及方法一、孔加工刀具的分类1.钻头:用于钻孔,可以分为普通钻头、中心钻头等。
普通钻头主要用于中、小孔径的钻孔,而中心钻头主要用于钻孔前的中心定位。
2.镗刀:用于对孔进行镗削,适用于孔径较大且精度要求较高的加工。
根据镗削的方式,可以分为手工镗刀和机动镗刀。
3.切削刀具:包括铰刀、滚刀等,用于在工件上切削出所需的孔形。
4.攻丝刀:用于在孔内加工螺纹,主要包括手攻刀和机动攻丝刀。
二、孔加工的常用方法1.钻孔法:利用钻头在工件上旋转切削,形成圆形的孔。
2.镗削法:利用镗刀在工件上旋转切削,形成较大孔径和高精度的圆形孔。
3.铰孔法:利用铰刀在工件上切削,形成倒角的肩部和圆形的底面孔。
4.拉床法:利用拉床将工件拉动,完成孔的切削。
5.铣削法:利用铣刀在工件上旋转切削,形成不同形状的孔。
6.手工孔:通过手工工具(如手电钻、手持镗刀等)完成孔的加工。
三、孔加工的注意事项1.材料选择:根据工件材料的不同,选择适合材料的刀具,以及合适的切削速度、进给速度等参数。
2.刀具保养:加工过程中,要定期检查并清洁刀具,保持刀具的尖端锐利,以保证加工质量和效率。
3.加工前的准备工作:加工前需进行合适的夹紧与定位,确保工件的稳定性和精度。
4.加工润滑:加工过程中需要使用润滑剂,减少摩擦和热量的产生,提高刀具寿命和加工质量。
5.审核尺寸:加工后要对孔的尺寸进行检测,以确保加工结果的准确性和合格率。
总之,孔加工是一项常见且重要的加工工艺。
合理选择孔加工刀具和方法,严格执行加工工艺要求,可以达到较高的加工精度和质量要求。
在实际应用中,根据工件的具体要求和加工条件,选择合适的孔加工刀具和方法,可以提高生产效率,降低生产成本。
14-4 加工余量、工序间尺寸及公差的确定
TZ = Zmax – Zmin=Tb+Ta
TZ :工序余量公差; Zmax :工序最大余量;
本道工序基本尺寸
Zmin:工序最小余量; Tb:本道工序的工序尺寸公差;
上道工序基本尺寸
Ta:上道工序的工序尺寸公差。
12
加工方向
共51页
工序尺寸及偏差
一般情况下,工序尺寸的公差按“入体原 则”标注。即 ——对被包容尺寸(轴的外径、实际长、宽、 高),其最大加工尺寸就是基本尺寸,上偏差 为零。 ——对包容尺寸(孔的直径、槽的宽度),其最 小加工尺寸就是基本尺寸,下偏差为零。 ——毛坯尺寸公差按双向对称偏差形式标注。
机床夹具的选择主要考虑生产类型。 (1)单件小批量生产应尽量选用通用夹具; (2)大批大量生产时,应采用高生产效率的专 用机床夹具;
此外,夹具的精度应与零件的加工精度相适应。
42
共51页
3.刀具的选择
刀具的选择主要取决于: 工序所采用的加工方法 加工表面的尺寸大小 工件材料 要求的加工精度 表面粗糙度 生产率 经济性
二、加工余量的确定
3. 经验法
由一些有经验的工程技术人员或工人根 据经验确定加工余量的大小。由经验法 确定的加工余量往往偏大,这主要是因 为主观上怕出废品的缘故。这种方法多 在单件小批生产中采用。
31
共51页
三、工序尺寸与公差的确定
生产上绝大部分加工面都是在基准重合(工艺基准和设计基 准重合)的情况下进行加工。现介绍如下: 1. 确定各加工工序的加工余量
6
共51页
双边余量
2Zi = li–1 – li
式中
Zi——本道工序的工序余量; li——本道工序的基本尺寸; li–1——上道工序的基本尺寸。
第14 UG编程 加工实例
• (3)单击【确定】按钮,进入加工界面。
14.1.4 创建几何体
• 开关盒模板加工所需要创建的几何体有:机床坐标系(MCS_MILL) 和切削几何体(MILL_GEOM)。
14.1.6 铣外壁
• 本小节要加工的内容为精铣零件外壁,深度是5.5,具体内容如下: • 1.创建操作 • 2.指定几何体 • 3.刀轨设置 • 4.操作
14.1.7 半精铣分型面
• 本小节要加工的内容为半精铣分型面,余量是0.2,具体内容如下: • 1.创建操作 • 2.指定几何体 • 3.刀轨设置 • 4.操作
14.1.15 精铣底面与岛顶面
• 由于底面与岛顶面加工区域大,而成型刀具直径 较小铣底面效率低。因此单独使用一个操作来精 铣底面,具体内容如下:
• 1.创建操作 • 2.创建几何体 • 3.刀轨设置 • 4.操作
14.1.16 精铣行位
• 本小节精加工行位使用表面区域铣,如图14.52所 示。精铣行位和精铣底面与岛顶面步骤一样。本 小节可以复制精铣底面操作完成。
• 1.机床坐标系位置设定 • 开关盒模板的外形为长方体,坐标系最适合的位置为表面中心。 • 2.创建铣削几何体 • 创建铣削几何体(WORKPICEC)需要指定的是:部件和毛坯。
14.1.5 创建刀具
• 本例子所需要的刀具比较多,这里只示范创建精铣底部侧壁所需要的成型刀具 CO5D6R0.5。具体步骤如下:
• (1)在插入刀具条,单击创建刀具图标,弹出【创建刀具】对话框。 • (2)在刀具子类型栏,单击铣刀图标。在名称栏下面输入CO5D6R0.5,如图14.9所示。 • (3)单击【确定】按钮,弹出【铣刀-5参数】对话框。参数按照图14.10设置。 • (4)单击【确定】按钮,完成退出【铣刀-5参数】对话框。
金属切削机床(第2版)——第十四章 机床的安装验收及维护
机床负荷试验在于检验机床各机构的强度, 以及在负载下机床各机构的工作情况。
(三)机床的精度试验
1.床身导轨的精度检验 订身导轨的精度检验包括导轨在垂直平面内
直线度和导轨应在同一平面内两个项目。
卧式车床精度标准见表14-1。
表14-1 卧式车床精度标准
序号 G1 G2 G3
G4 G5 G6
金属切削机床
(第二版)
吴国华 主编
第十四章 机床的安装验收及维护
第一节 机床的安装及验收 第二节 机床的日常维护及保养 第三节 通用机床常见故障及排除 习题
返回主目录
第一节 机床的安装及验收
一、机床的地基
机床地基一般分为混凝土地坪式(即车间水 泥地面)和单独块状式两大类。
X6132型万能卧式铣床的地基 返回本章首页
(1)溜板箱的纵走刀小齿轮与齿条啮合不正确 (2)光杆弯曲,或光杆、丝杆、走刀杆等三孔不在同一平 面上 (3)溜板箱内某一传动齿轮损坏或由于节径振摆而引起的 啮合不正确 (4)主轴箱、进给箱中的轴弯曲或齿轮损坏
(1)主轴上的传动齿轮齿形不良啮合不良 (2)主轴轴承的间隙太大或太小 (3)主轴箱上的带轮外径振摆过大
a)0.02/300(只许向上偏) b)0.015/300(只许向前偏) 0.015
序号 G9
G10 G11 G12 G13 G14 G15 P1
检验项目
D——尾座 尾座套筒轴线对溜板移动平行度 a)在垂直平面 b)在水平面内 尾座圆锥孔轴线对溜板移动的平行度 a)在垂直平面 b)在水平面内 E——两顶尖 床头和尾座两顶尖等高度
1.主轴及传动轴的修复 (1)主轴的修复
主轴的精度测量
(2)传动轴的修复 2.轴承的修复 (1)滚动轴承的修复 1)对滚动轴承加以合适的预加载 2)进行选配以提高轴承的回转精
- 1、下载文档前请自行甄别文档内容的完整性,平台不提供额外的编辑、内容补充、找答案等附加服务。
- 2、"仅部分预览"的文档,不可在线预览部分如存在完整性等问题,可反馈申请退款(可完整预览的文档不适用该条件!)。
- 3、如文档侵犯您的权益,请联系客服反馈,我们会尽快为您处理(人工客服工作时间:9:00-18:30)。
2、麻花钻的角度
(1)切削平面和基面 (2)螺旋角 (Spiralling angle) (3)顶角 2 (Double lip angle) (4)端面刃倾角和主偏角 (5)前角和后角 (6)横刃角度 (7)副偏角和副后角
(1)切削平面和基面
切削平面: 过主切削刃上一点与轴线相垂直的平面
基面:通过主切削刃上一点和轴线的剖平面
(2)螺旋角 (Spiralling angle) 定义:钻头外圆柱与螺旋槽表面的交线(螺旋线) 上任意点的切线和钻头轴线之间的夹角
tg
d 0
pz
tg m
dm d0
tg
(3)顶角 2 (Double lip angle) 定义:两主切削刃 在与其相平行的平 面上投影的夹角 作用:顶角小, 切削刃长,刀尖 角增大,有利于 散热, 耐用度提 高。
后刀面自然汇交形成横刃,其角度 包括横刃斜角、横刃前角、横刃后角 横刃切削时产生很大的轴向力
切削速度v
进给量f和每齿进给量fz
背吃刀量ap
切削厚度ac 切削宽度aw 切削层面积Acz
三、钻削力
T 9.81C M d 0x M f
yM
KM
F 9.81C F d 0x F f
yF
选择:黄铜,铝合金等
2 130 0 ~ 140 0
中硬铸铁、硬青铜等 大理石
2 80 0 ~ 90 0
2 90 0 ~ 100 0
钢、铸铁等标准麻花钻
2 118 0
(4)端面刃倾角 端面刃倾角:主切削刃在轴端面中的投影 与M点的基面间的夹角
s in stm dc dm
(4)刀尖处速度最高,副后角为零度,
易磨损,影响加工尺寸
2、麻花钻的修磨方法 (1)修磨横刃:直接缩短 修磨前角 综合修磨 (2)修磨多重顶角
(3)修磨前刀面 (4)开分屑槽 (5)修磨刃带
(1)修磨横刃:直接缩短(减小工作长度)
修磨前角(增加横刃的前角) 综合修磨
注意修磨位置!
(2)修磨多重顶角
(5)主偏角 主偏角:主切削刃在过该点基面上的投影 和钻头进给方向之间的夹角
tgkrm tg cos stm
(6)前角 后角
o
p
(圆柱剖面中的轴向后角)
(7)副偏角和副后角 副偏角由钻头导向部分的外径向柄部缩小而形成 副后角:副后刀面(刃带)与圆柱孔面的夹角
(8)横刃角度
镗杆
拖板
专用镗模镗孔
(3)刀具旋转并作进给运动
主 轴
镗杆 镗刀 工件 工件台
按不同结构,镗刀可分为单刃镗刀和双刃 镗刀。
通孔单刃镗刀
盲孔单刃镗刀
(双刃镗刀)
8.复合刀具
二、麻花钻的结构和角度 1、麻花钻的结构
结构特点: (1)两条主切削刃和两条副切削刃; (2)两条螺旋槽钻沟形成前刀面; (3)主后刀面在钻头端面上; (4)钻头外缘上两小段窄棱边形成的 刃带是副后刀面; (5)两主切削刃通过横刃相连接; (6)麻花钻的中心有一定的厚度,形 成钻心,钻心直径向柄部方向递增。
2、麻花钻
3、扩孔钻 4、深孔钻
7、锪钻
8、复合刀具
1. 扁钻
2. 麻花钻
3. 扩孔钻
4. 深孔钻
5. 锪钻
加工沉头座孔
加工锥面
锪平端面
6.铰刀
7. 镗刀
(1)工件旋转,刀具作进给运动
镗圆柱孔
镗锥孔
(2)刀具旋转,工件作进给运动
主轴 镗杆 镗刀 工件 工件台 镗床上镗孔 工件 镗刀 镗模
第十四章 孔加工刀具 (reaming and boring)
一、孔加工刀具介绍 二、麻花钻的工作角度 三、麻花钻的修磨 四、 群钻 重点和难点: 掌握麻花钻的工作角度与修磨方法, 以及群钻的特点。
孔加工刀具-用于在工件实心材料中形 成孔或将已有孔扩大的刀具。
钻头旋转
工件旋转
一、孔加工刀具的种类和用途 1、扁钻 5、铰刀 6、镗刀
KF
钻削力的影响因素:
(1)螺旋角:↑,前角↑,切削力↓ (2)顶角: ↑,轴向力↑; 切削层宽度↑,切向分 力↓ ,切削扭矩↓ (3)横刃: 横刃斜角↓ ,轴向力↑ (4)切削液
四、麻花钻的修磨
1、麻花钻的结构缺点 (1)前角沿主切削刃变化很大
(2)横刃为负前角切削,且宽度较大
(3)主切削刃很长,卷、排屑困难
切削刃长度增加,负荷减小; 顶角减小,ห้องสมุดไป่ตู้向力较小; 刀尖角增加,散热改善。
Double-cone drill
(3)修磨前刀面
改变前角的大小和前刀面的 形式。
(4)开分屑槽
(5)修磨刃带
减少磨损和提高耐用度。
3、群钻 三尖七刃锐当先,月牙弧槽分两边 一侧外刃宽分屑,横刃磨低窄又尖