粉末冶金实验报告_2
粉末冶金实验
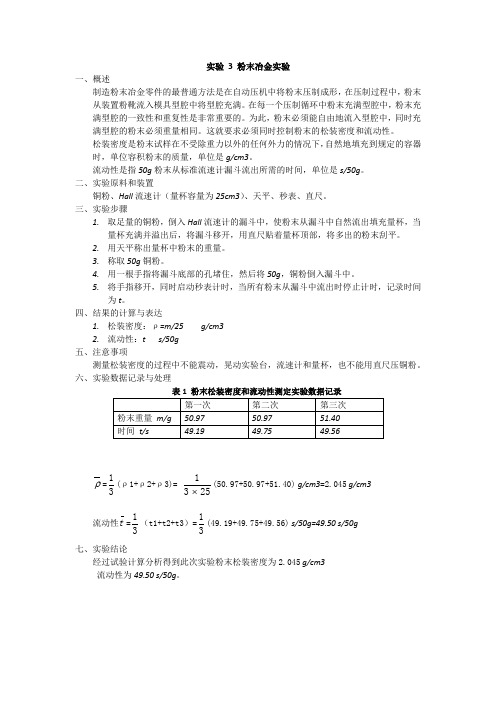
简易 BET 装置示意图 l—u 形管压力计;2~5 一两通阀 6 样品管;7 一液氮浴 测量前应对样品进行真空脱气处理,当真空度达到要求时,充入已知体积的氮气,然后 把液氮浴套在样品管上,当吸附达到平衡时,进行吸附测量,最后移开液氮浴,测量完 毕。 计算公式吸附气体体系中的粉末样品,在低温下,物质表面将发生物理吸附,其各量之 间的关系服从 BET 方程,如下式: p/p0V(1-p/p0)=(C-1)/VmC*p/p0+1/VmC 式中声为吸附平衡时吸附气体的压力, Pa; p0。 为吸附温度下吸附气体的饱和蒸气压, Pa;Vm 为单分层吸附气体量;C 为与吸附热和冷凝热有关的常数。在相对压力 p/p0 为 O.05~O.35 范围内,BET 方程为线性关系。通过一系列相对压力和吸附气体量 的测定,由(p/p0/[V(1 一 p/p0)]对 p/p0。作图,便可得到一条直线,再由直线的斜率和 截距求出样品的单层吸附量,再由下式计算出粉末的比表面积。 S=Vmó N/V0*m 式中 S 为粉末质量比表面积,m /g;ó 为吸附气体分子横断面积,0.16nm2;N 阿佛加 德罗常数 6.022×1023;V0 为标准状态下 1mol 吸附气体的体积,22.414cm3;m 为 试验样品的质量,g。
2
吸附气体选择通常选用氮为吸附气体, 当测量的比表面很小时, 常选用氩或氪作为吸附 气体。 针对本仪器, BET 方程变形为: St=(1-p/p0)*A/Ac*Vc*4.03 P/Po : 被吸附气体的相对压力 (在本实验中,表示氮气的相对压力,为 0.3 ) A : 脱附峰面积 AC : 标准峰面积 VC : 标定体积 St : 总表面积 三、测量方法:流动法 把 30% 氮气 (被吸附物)和 70% 氦气 (载体) 的混合气体不断在样品上进行流动。 当样品冷却到液氮温度时,氮气被吸附,而氦气不被吸附。 吸附过程持续,直到氮气吸附量达到 30%浓度。这时,吸附量接近于单层表面覆盖的体 积。 四、仪器设备 美国 QUANTACHROME 公司生产的 QS-18 型气体吸附表面性质分析仪,气体吸附分析仪 由表面积测定部分和脱气预处理部分构成。 五、实验步骤 1.对样品进行脱气预处理 2.测量 3.记录脱附峰值,标定 4.得出的量结果 六、数据处理 根据 St=(1-p/p0)*A/Ac*Vc*4.03 本实验得出 A=1248,Ac=106, Vc=0.17 p/p0 代入上式得 St=(1-0.3)*1248/106*0.17*4.03=5.64626 m2 m= (12.5460-1/2(12.4730+12.4723))g=0.0734 g S=St/m= 5.64626m2/0.0734g=76.9245 m2/g 八、实验结论 经实验测定计算,样品比表面积为 76.9245 m2/g
粉末成形实验的实验报告

1. 理解粉末成形的基本原理和工艺过程;2. 掌握粉末成形的方法和设备;3. 学习粉末成形过程中可能出现的缺陷及解决方法;4. 培养实验操作能力和数据分析能力。
二、实验原理粉末成形是将金属粉末或金属粉末与其他添加剂均匀混合后,通过一定的压力和温度使其具有一定形状和尺寸的工艺过程。
粉末成形主要包括压制成型和无压制成型两大类。
压制成型:将粉末与添加剂混合均匀后,在一定压力下,粉末颗粒相互压紧,形成具有一定形状和尺寸的坯体。
无压制成型:将粉末与添加剂混合均匀后,通过物理或化学方法,使粉末颗粒相互粘结,形成具有一定形状和尺寸的坯体。
三、实验设备与材料1. 实验设备:粉末冶金实验台、压制成型设备、无压制成型设备、高温烧结炉、显微镜、万能试验机等;2. 实验材料:金属粉末、添加剂、模具、烧结剂等。
四、实验步骤1. 原料粉末的制备和准备:将金属粉末与添加剂按一定比例混合,搅拌均匀;2. 压制成型:将混合好的粉末放入模具中,采用不同的压力和保压时间,使粉末颗粒相互压紧,形成坯体;3. 无压制成型:将混合好的粉末放入模具中,采用物理或化学方法,使粉末颗粒相互粘结,形成坯体;4. 烧结:将压制成型或无压制成型的坯体放入高温烧结炉中,在一定温度下进行烧结,使坯体具有一定的物理、化学和力学性能;5. 性能测试:对烧结后的样品进行力学性能、组织结构等方面的测试。
1. 压制成型:在压力作用下,粉末颗粒相互压紧,形成具有一定形状和尺寸的坯体;2. 无压制成型:在物理或化学作用下,粉末颗粒相互粘结,形成具有一定形状和尺寸的坯体;3. 烧结:烧结过程中,坯体逐渐变硬,颜色变深,体积缩小;4. 性能测试:力学性能测试时,样品断裂,断裂面光滑;组织结构测试时,显微镜下观察到晶粒、孔隙等。
六、实验结果与分析1. 压制成型:在一定的压力和保压时间下,粉末颗粒相互压紧,形成具有一定形状和尺寸的坯体。
通过调整压力和保压时间,可以控制坯体的密度和强度;2. 无压制成型:在物理或化学作用下,粉末颗粒相互粘结,形成具有一定形状和尺寸的坯体。
粉末冶金工厂实习报告

一、实习背景随着科技的不断发展,粉末冶金技术在我国工业领域得到了广泛的应用。
为了深入了解粉末冶金行业的发展现状及生产流程,提高自己的专业技能,我于2021年7月至9月在XX粉末冶金工厂进行了为期两个月的实习。
二、实习目的1. 了解粉末冶金行业的发展现状及市场前景;2. 熟悉粉末冶金生产流程,掌握粉末冶金生产的基本技能;3. 培养团队合作精神,提高自己的沟通能力;4. 为今后从事粉末冶金相关工作奠定基础。
三、实习内容1. 工厂概况XX粉末冶金工厂位于我国某工业园区,占地面积约10万平方米,拥有现代化的生产设备和先进的技术工艺。
工厂主要从事粉末冶金材料的研发、生产和销售,产品广泛应用于汽车、电子、航空航天等行业。
2. 生产流程粉末冶金生产流程主要包括:原料制备、粉末成型、烧结、后处理等环节。
(1)原料制备:将金属粉末、陶瓷粉末、金属粉末等原料进行混合、筛分、除杂等处理,制备出符合要求的粉末。
(2)粉末成型:将制备好的粉末进行压制成型或注塑成型,形成所需形状的坯体。
(3)烧结:将成型后的坯体进行高温烧结,使粉末冶金材料具有所需的性能。
(4)后处理:对烧结后的材料进行切割、打磨、抛光等处理,以满足客户需求。
3. 实习任务(1)参观生产车间,了解粉末冶金生产设备、工艺流程及操作规范;(2)协助工程师进行粉末冶金材料性能测试;(3)参与新产品研发,学习新工艺、新技术;(4)与同事交流,了解粉末冶金行业发展趋势。
四、实习心得1. 粉末冶金行业具有广阔的发展前景。
随着我国制造业的快速发展,粉末冶金材料在汽车、电子、航空航天等领域的应用越来越广泛,市场需求不断增长。
2. 粉末冶金生产流程复杂,涉及多个环节。
在生产过程中,要严格按照操作规范进行,确保产品质量。
3. 粉末冶金材料性能优异,具有高强度、高硬度、耐磨损等特点。
在研发新产品时,要充分考虑材料性能,满足客户需求。
4. 团队合作精神在粉末冶金行业中至关重要。
在生产过程中,要与同事密切配合,共同完成生产任务。
粉末冶金报告
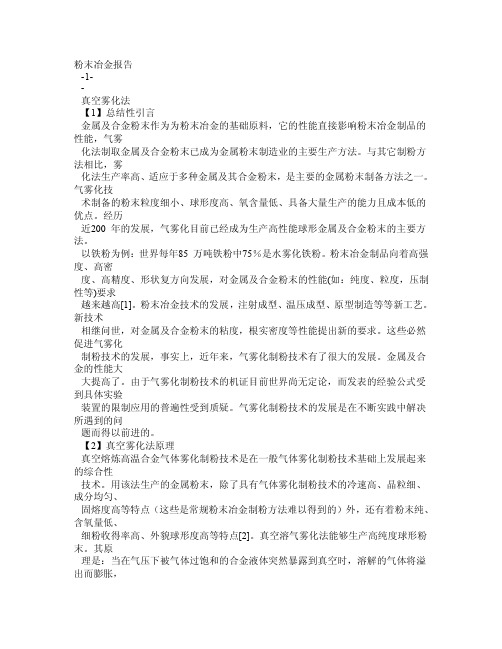
粉末冶金报告-1--真空雾化法【1】总结性引言金属及合金粉末作为为粉末冶金的基础原料,它的性能直接影响粉末冶金制品的性能,气雾化法制取金属及合金粉末已成为金属粉末制造业的主要生产方法。
与其它制粉方法相比,雾化法生产率高、适应于多种金属及其合金粉末,是主要的金属粉末制备方法之一。
气雾化技术制备的粉末粒度细小、球形度高、氧含量低、具备大量生产的能力且成本低的优点。
经历近200 年的发展,气雾化目前已经成为生产高性能球形金属及合金粉末的主要方法。
以铁粉为例:世界每年85 万吨铁粉中75%是水雾化铁粉。
粉末冶金制品向着高强度、高密度、高精度、形状复方向发展,对金属及合金粉末的性能(如:纯度、粒度,压制性等)要求越来越高[1]。
粉末冶金技术的发展,注射成型、温压成型、原型制造等等新工艺。
新技术相继问世,对金属及合金粉末的粘度,根实密度等性能提出新的要求。
这些必然促进气雾化制粉技术的发展,事实上,近年来,气雾化制粉技术有了很大的发展。
金属及合金的性能大大提高了。
由于气雾化制粉技术的机证目前世界尚无定论,而发表的经验公式受到具体实验装置的限制应用的普遍性受到质疑。
气雾化制粉技术的发展是在不断实践中解决所遇到的问题而得以前进的。
【2】真空雾化法原理真空熔炼高温合金气体雾化制粉技术是在一般气体雾化制粉技术基础上发展起来的综合性技术。
用该法生产的金属粉末,除了具有气体雾化制粉技术的冷速高、晶粒细、成分均匀、固熔度高等特点(这些是常规粉末冶金制粉方法难以得到的)外,还有着粉末纯、含氧量低、细粉收得率高、外貌球形度高等特点[2]。
真空溶气雾化法能够生产高纯度球形粉末。
其原理是:当在气压下被气体过饱和的合金液体突然暴露到真空时,溶解的气体将溢出而膨胀,只是合金液体雾化,继之冷凝成粉末。
对于镍铜钴铁盒铝的基体合金均可以采用熔氢的方法实现真空溶气雾化法制粉。
真空雾化制粉装置,是为了满足在真空条件下雾化制粉工艺的研究与小批量生产而设计的装置。
粉末冶金实验
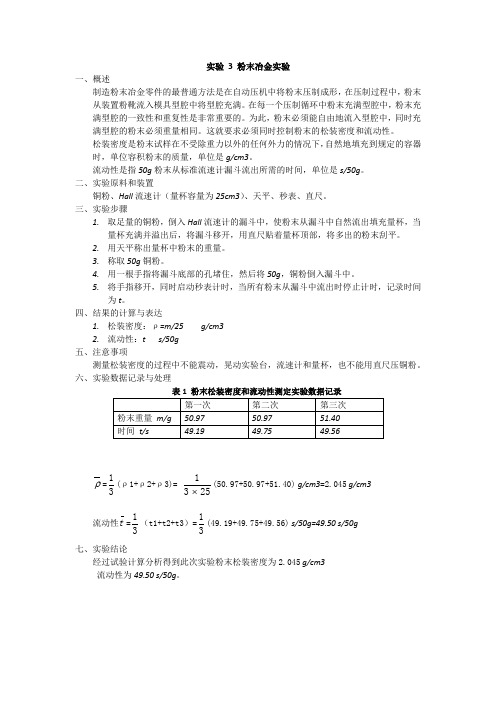
简易 BET 装置示意图 l—u 形管压力计;2~5 一两通阀 6 样品管;7 一液氮浴 测量前应对样品进行真空脱气处理,当真空度达到要求时,充入已知体积的氮气,然后 把液氮浴套在样品管上,当吸附达到平衡时,进行吸附测量,最后移开液氮浴,测量完 毕。 计算公式吸附气体体系中的粉末样品,在低温下,物质表面将发生物理吸附,其各量之 间的关系服从 BET 方程,如下式: p/p0V(1-p/p0)=(C-1)/VmC*p/p0+1/VmC 式中声为吸附平衡时吸附气体的压力, Pa; p0。 为吸附温度下吸附气体的饱和蒸气压, Pa;Vm 为单分层吸附气体量;C 为与吸附热和冷凝热有关的常数。在相对压力 p/p0 为 O.05~O.35 范围内,BET 方程为线性关系。通过一系列相对压力和吸附气体量 的测定,由(p/p0/[V(1 一 p/p0)]对 p/p0。作图,便可得到一条直线,再由直线的斜率和 截距求出样品的单层吸附量,再由下式计算出粉末的比表面积。 S=Vmó N/V0*m 式中 S 为粉末质量比表面积,m /g;ó 为吸附气体分子横断面积,0.16nm2;N 阿佛加 德罗常数 6.022×1023;V0 为标准状态下 1mol 吸附气体的体积,22.414cm3;m 为 试验样品的质量,g。
1 1 (t1+t2+t3)= (49.19+49.75+49.56) s/50g=49.50 s/50g 3 3
七、实验结论 经过试验计算分析得到此次实验粉末松装密度为 2.045 g/cm3 流动性为 49.50 s/50g。
实验 2 放电等离子烧结(SPS) 1、纳米材料 传统的热压烧结、热等静压等方法制备纳米材料,很难保证晶粒的纳米尺寸,又达到完全致 密的要求。利用 SPS 技术,因其加热迅速,合成时间短,可明显抑制晶粒粗化。利用 SPS 技术,因其加热迅速,合成时间短,可明显抑制晶粒粗化。 利用 SPS 能快速降温这一特点来控制烧结过程的反应历程,避免一些不必要的反应发生, 这就可能使粉末中的缺陷和亚结构在烧结后的块体材料中得以保留,在更广泛的意义上说, 这一点有利于合成介稳材料,特别有利于制备纳米材料。 2、梯度功能材料(FGM)是一种组成在某个方向上梯度分布的复合材料,各层的烧结温度不 同, 利用传统的烧结方法难以一次烧成。 利用 CVD ,PVD 等方法制备梯度材料, 成本很高, 也很难实现工业化生产。通过 SPS 技术可以很好地克服这一难点。 SPS 可以制造陶瓷/金属、 聚合物/金属以及其他耐热梯度、 耐磨梯度、 硬度梯度、 导电梯度、 孔隙度梯度等材料。梯度层可到 10 多层,实现烧结温度的梯度分布。 3、电磁材料 采用 SPS 技术还可以制作 SiGe,PbTe,BiTe,FeSi,CoSb3 等体系的热电转化元件,以 及广泛用于电子领域的各种功能材料, 如超导材料、 磁性材料、 靶材、 介电材料、 贮氢材料、 形状记忆材料、固体电池材料、光学材料等。 4、金属间化合物 金属间化合物具有常温脆性和高熔点,因此制备或生产需要特殊的过程。利用熔化法(电火 花熔化、电阻熔化、感应熔化等)制备金属间化合物往往需要高能量、真空系统,而且需要 进行对其二次加工(锻造) 。利用 SPS 技术准备金属间化合物,因为有效利用了颗粒间的自 发热作用和表面活化作用,可实现低温、快速烧结,所以 SPS 技术为制备金属间化合物的 一种有效方法。目前,利用 SPS 技术已制备的金属间化合物体系有:Ti-Al 体系、Mo-Si 体 系、Ni-Al 体系等。 5、高致密度、细晶粒陶瓷和金属陶瓷 在 SPS 过程中,样品中每一个粉末颗粒及其相互间的空隙本身都可能是发热源。用通常方 法烧结时所必需的传热过程在 SPS 过程中可以忽略不计。因此烧结时间可以大为缩短,烧 结温度也明显降低。对于制备高密度、细晶粒陶瓷,SPS 是一种很有优势的烧结手段。 6、其他材料 此外,SPS 技术也已成功地应用于金属基复合材料(MMC) 、非晶合金、生物材料、超导 材料和多孔材料等各种新材料的制备,并获得了较为优异的性能。同时,SPS 在硬质合金 的烧结,多层金属粉末的同步连接(bonding) 、陶瓷粉末和金属粉末的连接以及固体-粉末-
粉末冶金压制实习报告
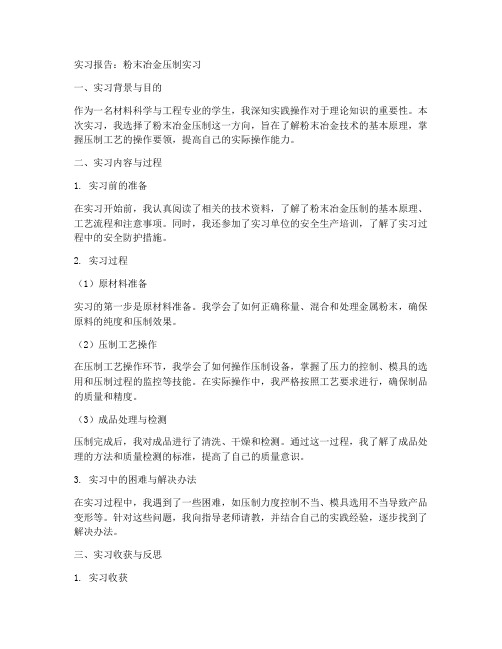
实习报告:粉末冶金压制实习一、实习背景与目的作为一名材料科学与工程专业的学生,我深知实践操作对于理论知识的重要性。
本次实习,我选择了粉末冶金压制这一方向,旨在了解粉末冶金技术的基本原理,掌握压制工艺的操作要领,提高自己的实际操作能力。
二、实习内容与过程1. 实习前的准备在实习开始前,我认真阅读了相关的技术资料,了解了粉末冶金压制的基本原理、工艺流程和注意事项。
同时,我还参加了实习单位的安全生产培训,了解了实习过程中的安全防护措施。
2. 实习过程(1)原材料准备实习的第一步是原材料准备。
我学会了如何正确称量、混合和处理金属粉末,确保原料的纯度和压制效果。
(2)压制工艺操作在压制工艺操作环节,我学会了如何操作压制设备,掌握了压力的控制、模具的选用和压制过程的监控等技能。
在实际操作中,我严格按照工艺要求进行,确保制品的质量和精度。
(3)成品处理与检测压制完成后,我对成品进行了清洗、干燥和检测。
通过这一过程,我了解了成品处理的方法和质量检测的标准,提高了自己的质量意识。
3. 实习中的困难与解决办法在实习过程中,我遇到了一些困难,如压制力度控制不当、模具选用不当导致产品变形等。
针对这些问题,我向指导老师请教,并结合自己的实践经验,逐步找到了解决办法。
三、实习收获与反思1. 实习收获通过本次实习,我掌握了粉末冶金压制的基本工艺流程,学会了操作压制设备,提高了自己的实际操作能力。
同时,我对粉末冶金技术有了更深入的了解,为今后的学习和工作打下了坚实的基础。
2. 实习反思回顾实习过程,我认为自己在以下几个方面还有待提高:(1)对原材料性能的了解不够深入,需要在今后的学习中加强理论学习。
(2)在实际操作中,对压力的控制不够稳定,需要多加练习,提高自己的操作技巧。
(3)在解决问题时,有时过于依赖指导老师,应学会独立思考和解决问题。
四、总结本次粉末冶金压制实习,使我受益匪浅。
我深刻认识到实践操作与理论知识相结合的重要性,决心在今后的工作中,继续努力提高自己的实践能力,为我国材料科学事业贡献自己的力量。
粉末冶金实验报告
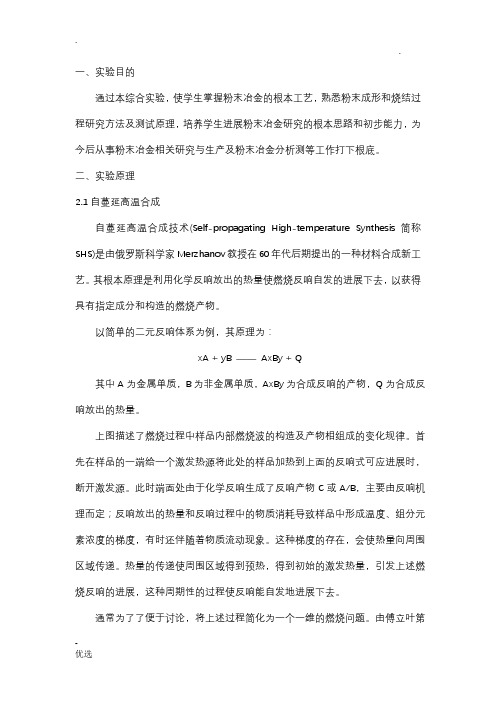
一、实验目的通过本综合实验,使学生掌握粉末冶金的根本工艺,熟悉粉末成形和烧结过程研究方法及测试原理,培养学生进展粉末冶金研究的根本思路和初步能力,为今后从事粉末冶金相关研究与生产及粉末冶金分析测等工作打下根底。
二、实验原理2.1自蔓延高温合成自蔓延高温合成技术(Self-propagating High-temperature Synthesis简称SHS)是由俄罗斯科学家Merzhanov教授在60年代后期提出的一种材料合成新工艺。
其根本原理是利用化学反响放出的热量使燃烧反响自发的进展下去,以获得具有指定成分和构造的燃烧产物。
以简单的二元反响体系为例,其原理为:xA + yB ——AxBy + Q其中A为金属单质,B为非金属单质,AxBy为合成反响的产物,Q为合成反响放出的热量。
上图描述了燃烧过程中样品内部燃烧波的构造及产物相组成的变化规律。
首先在样品的一端给一个激发热源将此处的样品加热到上面的反响式可应进展时,断开激发源。
此时端面处由于化学反响生成了反响产物C或A/B,主要由反响机理而定;反响放出的热量和反响过程中的物质消耗导致样品中形成温度、组分元素浓度的梯度,有时还伴随着物质流动现象。
这种梯度的存在,会使热量向周围区域传递。
热量的传递使周围区域得到预热,得到初始的激发热量,引发上述燃烧反响的进展,这种周期性的过程使反响能自发地进展下去。
通常为了了便于讨论,将上述过程简化为一个一维的燃烧问题。
由傅立叶第一定理和能量守恒法那么,可得到如下方程组:为了得到指定构造的化学组成和产物相分布等,通常需要对反响过程进展控制。
对体系的控制主要是通过改变上述方程中的体系初始物性常数,如比热C,热传导系数K等。
读者有举兴趣,通过上述议程的数学分析,可以对燃烧过程中的动力学形为进展研究,将上述动力学行为与产物构造结合在一起,就形成了自蔓延过程常用的研究方法——构造宏观动力学。
SHS过程也可以是多元反响过程,其根本原理不变,只是反响过程更加复杂。
粉末冶金实验课实验报告总结
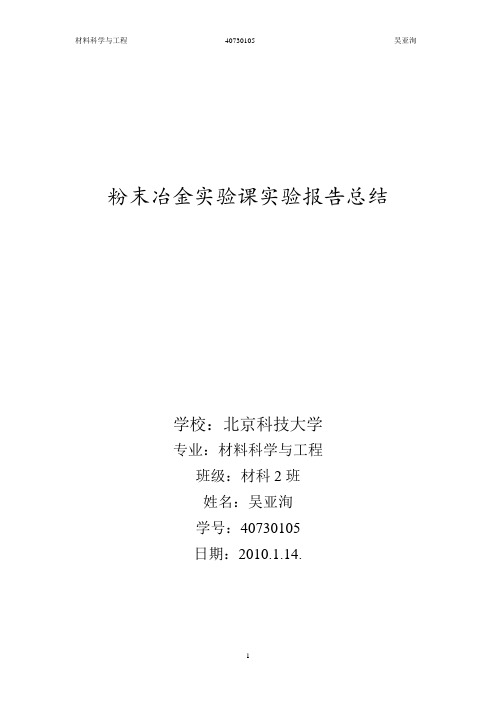
粉末冶金实验课实验报告总结学校:北京科技大学专业:材料科学与工程班级:材科2班姓名:吴亚洵学号:40730105日期:2010.1.14.实验1 可渗性烧结金属材料密度测定1、国家标准号:GB 5163-852、鉴定试样所需的详细说明:试样经过清洗除油干燥,在空气中称量。
防水处理(表面用凡士林覆盖),再次在空气中称量。
可由称重时候适量的减少求出其体积,密度可计算出来。
3、所需要公式及实验结果:'442m m m d -=ρD=试样密度M2=4.8655干燥不含油试样空气中称重的质量;gM4=4.9391浸油试样在空气中称重的总质量;gM4'=4.05052浸油试样在水中称重的总质量;gρ实验温度下水的密度实验结果表达:d=5.484、可能影响实验结果的影响因素环境温度,称量仪器的精度,读数的误差,尼龙绳的质量误差,油没有抹匀的精度误差 实验总结:试样小于0.5cm3时可以把数个试样集中起来测量,可以提高测量精度实验2球星铜粉松散烧结概述:粉末松散烧结,又称松装烧结。
是指金属粉末不经成型而松散或振实装在耐高温的模具内直接进行的粉末烧结,松装烧结主要用来制取透过性较大,精华精度要求不高的多孔材料。
比如用于过滤汽油,润滑油,化学溶液等等。
多孔材料的特征明显,颗粒多位球形颗粒。
松装烧结是由于粉末颗粒间相接触面积小,必须严格控制烧结温度和气氛,是少结成的制品具有足够的强度,又不至于收缩过大而降低孔隙度。
实验材料:100目球形铜粉、石墨模具,管式烧结炉,游标卡尺步骤:1、用游标卡尺测量石墨模具的内径尺寸。
2、将铜粉松装在石墨模具内3、将装有铜粉的模具于管式炉中850度烧结20min ,氮气保护。
4、冷却后把烧结好的铜粉配体从石墨模具内取出,测量尺寸5、计算烧结前后的尺寸收缩率计算结果整个过程分为制粉---成型---烧结,铜粉极易氧化,需要用惰性气体保护气实验3粉末松装比重的测定1、实验目的通过被实验了解粉末松装比重的测定方法,以及影响松装比重的因素。
- 1、下载文档前请自行甄别文档内容的完整性,平台不提供额外的编辑、内容补充、找答案等附加服务。
- 2、"仅部分预览"的文档,不可在线预览部分如存在完整性等问题,可反馈申请退款(可完整预览的文档不适用该条件!)。
- 3、如文档侵犯您的权益,请联系客服反馈,我们会尽快为您处理(人工客服工作时间:9:00-18:30)。
实验十一、铁基粉末冶金
一、实验目的
1、了解粉末冶金零件制备过程。
2、了解烧结温度对烧结过程和制品性能的影响。
3、了解烧结时间对烧结过程和制品性能的影响。
4、了解石墨添加量对烧结过程和制品性能的影响。
二、实验原理
粉末冶金是制取金属或用金属粉末(或金属粉末与非金属粉末的混合物)作为原料,经过成形和烧结,制造金属材料、复合以及各种类型制品的工艺技术。
粉末冶金法与生产陶瓷有相似的地方,因此,一系列粉末冶金新技术也可用于陶瓷材料的制备。
由于粉末冶金技术的优点,它已成为解决新材料问题的钥匙,在新材料的发展中起着举足轻重的作用。
粉末冶金的一般生产过程为:
(1)生产粉末。
粉末的生产过程包括粉末的制取、粉料的混合等步骤。
为改善粉末的成型性和可塑性通常加入汽油、橡胶或石蜡等增塑剂。
(2)压制成型。
粉末在500~600MPa压力下,压成所需形状。
[1]
(3)烧结。
在保护气氛的高温炉或真空炉中进行。
烧结不同于金属熔化,烧结时至少有一种元素仍处于固态。
烧结过程中粉末颗粒间通过扩散、再结晶、熔焊、化合、溶解等一系列的物理化学过程,成为具有一定孔隙度的冶金产品。
(4)后处理。
一般情况下,烧结好的制件可直接使用。
但对于某些尺寸要求精度高并且有高的硬度、耐磨性的制件还要进行烧结后处理。
后处理包括精压、滚压、挤压、淬火、表面淬火、浸油、及熔渗等。
在粉末冶金中,粉末的性能主要包括:粉末的几何性能(粒度、比表面、孔径和形状等);粉末的化学性能(化学成分、纯度、氧含量和酸不溶物等);粉体的力学特性(松装密度、流动性、成形性、压缩性、堆积角和剪切角等);粉末的物理性能和表面特性(真密度、光泽、吸波性、表面活性、电位和磁性等)。
粉末性能往往在很大程度上决定了粉末冶金产品的性能。
三、实验内容
1、采用冷压法制备铁—石墨试样。
2、研究烧结温度对制品性能的影响。
3、研究烧结时间对制品性能的影响。
4、研究石墨含量对制品性能的影响。
四、实验步骤
1、每组压制3个试样,测量尺寸、重量后按实验计划确定的参数进行烧结。
2、烧结结束后,再次测量试样尺寸、重量,比较烧结前后密度的变化,观察金
相组织和检测试样硬度。
五、实验数据整理
实验原始数据见表一、表二。
(表一)冷压烧结试样
排水法测密度公式:ρ固=w1 / (w1- w2)
w1:物体在空气中的质量(克)
w2:物体在蒸馏水中的质量(克)
(表二)测量密度(排水法)及硬度
实验金相组织照片见图一、图二。
冷压烧结试样
图一、2011年铁基粉末冶金实验试样金相组织照片
C:0.2% 1260℃保温:2小时C:0.2% 1260℃保温:2小时
密度:7.37 g/cm3未腐蚀 2~3%硝酸酒精溶液腐蚀 HRB:62.6 放大倍数:200 放大倍数:500
C:0.8% 1260℃保温:2小时C:0.8% 1260℃保温:2小时
密度:7.19 g/cm3未腐蚀 2~3%硝酸酒精溶液腐蚀 HRB:67.0 放大倍数:200 放大倍数:500
C:2.0% 1170℃保温:1.5小时C:2.0% 1170℃保温:1.5小时
密度:6.98 g/cm3未腐蚀 2~3%硝酸酒精溶液腐蚀 HRB:77.6 放大倍数:200 放大倍数:500
冷压烧结试样
图二、2010年铁基粉末冶金烧结试样金相形貌
C:2.0% 1170℃保温:1.5小时C:2.0% 1170℃保温:1.5小时密度:6.77 g/cm3未腐蚀密度:6.77 g/cm3 HRB:75.8 腐蚀
铁基粉末冶金(热压烧结)试样金相形貌
C:0.2% 1150℃保温:1小时C:0.2% 1150℃保温:1小时
加压:1.6吨密度:7.70 g/cm3未腐蚀 HRB:79.8 腐蚀
C:0.8% 1140℃保温:1小时C:0.8% 1140℃保温:1小时
加压:1.6吨密度:7.69 g/cm3未腐蚀 HRB: 101.1 腐蚀
六、实验分析
(1)根据表一,石墨含量不同的粉末在烧结之后均出现了体积减小、重量减小、密度增大的现象。
这是由于未经烧结的坯件气孔率很高,可达百分之几或百分之几十,粉末颗粒之间的接触面积较小。
通过烧结,材料的质点通过扩散产生迁移,颗粒之间的相互接触点逐渐增大,空隙减少,相互连成整体,从而使坯体变得致密。
重量减小则是由于烧结过程中水分的挥发。
(2)根据表二,粉末的石墨含量越高,烧结后其密度越小,硬度越大。
而在粉末含碳量相同的前提下,热压烧结相对冷压烧结能够得到密度和硬度更高的制品。
这是由于石墨本身的密度小于铁粉,并且当石墨含量较高时,烧结后试样中渗碳体的数量也会增多,使得其硬度更大。
(3)根据图一、图二,提高烧结温度或延长烧结时间均可以提高试样的密度和硬度。
这是由于烧结过程实际上是材料质点扩散迁移以及再结晶的过程,温
度越高或者保温时间越长,都能使其扩散迁移的更加充分,从而使颗粒间接触面积不断增大,颗粒间隙减小,导致密度、硬度增大。
七、思考题
问题:不同碳含量的铁、石墨合金粉末烧结后金相形貌与Fe-Fe3C相图中对应碳含量的金相组织有何差别?试分析原因?可采取什么措施减小或消除这种差别?
答:(1)金相组织的差别在于:不同碳含量的铁、石墨合金粉末烧结后,其金相形貌基本上都是在铁基体上分布着点状的石墨以及珠光体;而在铁碳相图中随着合金中碳含量的变化,其金相形貌将显著不同,如铁素体、珠光体、莱氏体等。
(2)产生原因是粉末烧结过程中,分布不均匀的碳颗粒是以固相扩散的方式向基体(铁)中渗透,一部分以点状石墨存在,另一部分与铁基形成有限固溶体,在烧结冷却之后形成珠光体和二次渗碳体。
(3)能够减小或消除这种差别的措施有:进一步细化粉末的颗粒大小;根据理论与实际确定合理的烧结温度和烧结时间;控制冷却速度;采用适当热处理等。