微粉末注射成型氧化铝通道
金属粉末的注射成型

金属粉末的注射成型金属粉末的注射成型,也被称为金属粉末注射成型(Metal Powder Injection Molding,简称MIM),是一种先进的制造技术,将金属粉末与有机物相结合,通过注射成型和烧结工艺,制造出高密度、精确尺寸、复杂形状的金属零件。
在金属粉末注射成型过程中,首先将金属粉末与有机粘结剂和其他添加剂混合均匀,形成金属粉末/有机物混合物。
其次,在高压下,将混合物通过注射机注射到具有细微孔隙和管道的模具中。
模具通常采用两片结构,上模和下模之间形成的形状即为所需制造的零件形状。
注射机将足够的压力用于将混合物推进模具的每一个细微空间,以确保零件形状准确,毛边小。
注射后,模具中的混合物开始固化,形成绿色零件。
最后,通过烧结处理,去除有机物并使金属颗粒结合成整体,形成具有理想密度和力学性能的金属粉末零件。
相对于传统的金属加工方法,金属粉末注射成型具有以下优势:首先,MIM可以制造复杂形状的金属零件,包括薄壁结构、内外复杂曲面和细小结构,满足了一些特殊零件的制造需求。
其次,MIM的材料利用率高,废料少,可以减少原材料和能源的浪费。
此外,零件的尺寸稳定性好,需要的加工工序少,可以降低生产成本。
最重要的是,对于一些其他制造工艺难以实现的金属材料,例如高强度不锈钢、钨合金和钛合金,MIM可以实现高质量的制造。
然而,金属粉末注射成型也存在应用范围的限制。
首先,相对较高的制造成本使得该技术在一些低成本产品上难以应用。
其次,较大的尺寸限制了MIM在制造大尺寸、高精度的零件上的应用。
此外,与其他成型方法相比,MIM的制造周期较长,对行业响应速度要求较高的场景不适用。
尽管如此,金属粉末注射成型技术已经在汽车、电子产品、医疗器械、工具和航空航天等领域得到了广泛的应用。
随着制造技术的进步和材料属性的改进,金属粉末注射成型有望在更多领域发挥其优势,并带来更多创新的解决方案。
Al2O3陶瓷注射成型工艺实验研究
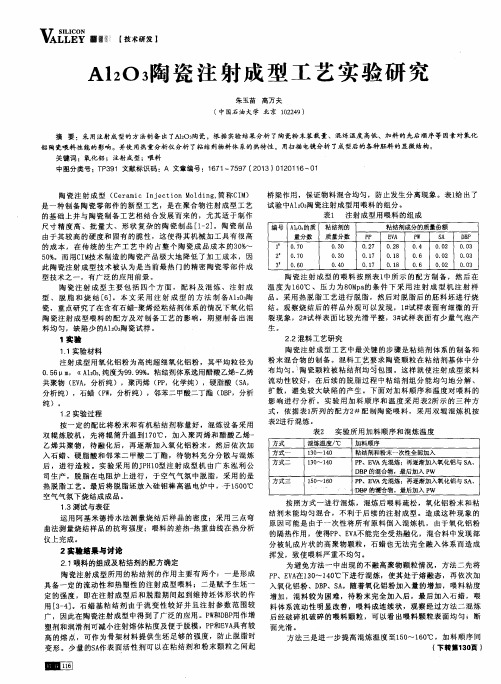
5 0 % 。 而 用C I M 技 术 制 造 的 陶 瓷 产 品极 大 地 降 低 了 加 工 成 本 , 因
表1 注 射 成 型 用 喂 料 的 组 成
编 号 A 1 。 0 。 的质 粘结剂 的
量分数
i 2 0 . 7 0 0 . 7 0
粘结剂成分 的质量份额
是 一种 制备陶瓷零部件 的新型工艺 ,是在聚合物 注射成型工艺 的基 础 上 并 与 陶 瓷 制 备 工 艺 相 结 合 发 展 而 来 的 , 尤 其 适 于 制 作 尺 寸 精 度 高 、批 量 大 、 形 状 复 杂 的 陶 瓷 制 品 [ 卜2 ] 。 陶 瓷 制 品 由 于 其 较 高 的硬 度 和 固 有 的 脆 性 ,这 使 得 其 机 械 加 工 具 有 很 高 的 成 本 , 在 传 统 的 生 产 工 艺 中 约 占整 个 陶 瓷 成 品 成 本 的 3 O % ~
P P
0 . 2 7 O . 1 7
质量分数
O . 3 O O . 3 O
E V A
0 . 2 8 0 . 1 8
P W
O . 4 0 . 6
S A
O . O 2 0 . O 2
D B P
O . 0 3 0 . 0 3
此 陶 瓷 注 射 成 型 技 术 被 认 为是 当前 最 热 门 的 精 密 陶 瓷 零 部件 成 型 技 术 之 一 , 有 广泛 的应 用 前 景 。 陶 瓷 注 射 成 型 主 要 包 括 四个 方 面 ,配 料 及 混 炼 、 注 射 成
MIM粉末注射制造工艺

W-Ni-Fe、W-Ni-Cu、W-Cu 军工业、通讯 Ti、Ti-6Al-4V Fe、Fe14Nd2B、SmCo5 医疗、军工结构件 各种磁性能部件
陶瓷及化合物
氧化铝、氮化铝、铁氧体、羟磷灰石、莫来石
(3Al2O3-2SiO3)、镍铝金属间化合物、氧化硅 、碳化硅、氮化硅、尖晶石、二氧化钛、二氧化钇、 二氧化锆
金属陶瓷及复合材料
3Al2O3-2SiO3、3Al2O3-ZnO2、Mo-Cu、 Nbc-Ni、Ni3Al-Al2O3、Si3N4-SiC、SiO2-Si、 TiC-Ni-Mo、W-Cu、WC-Ni、ZrO2-MgO、ZrO2-Y2O3
四、现有的MIM 材料性能标准: 美国金属粉末产业联合发布MPIF标准35,下表只列材料性能,详见
材料牌号 (状态) 最小值 标准值 拉伸性能 拉伸性能 密度 硬度(洛氏) 3 显微 极 限 抗 屈服强度 伸 长 率 极限抗 屈服强度 伸 长 率 g/cm 拉强度 ( 0.2% ) 表观 ( 换 算 的) ( 于 拉强度 (0.2%) ( 于 25.4mm 25.4mm MPa MPa MPa MPa 内) 内) % % 255 110 20.0 290 125 40 7.5 45HRb 379 255 267 110 20.0 20.0 414 290 255 124 26 40 7.6 7.6 69HRb 45HRb 55HRc
MIM粉末注塑制造
物为原料,通过挤压机注塑成型的一种制造方法。
概述
MIM:Metal powder Injection Molding(金属粉末注塑成型)是 以金属粉末加粘结剂混合
MIM工艺流程: 混料: 金属粉末(雾化粉末)+粘结剂(石蜡等有机物)在100多摄氏度下混合成团面状,然后劈 成薄片形状,通过挤压机挤成面条状,在通过打断机打成混料粒子。 注:A:混料要密封 B:混料怕潮湿
注射成型工艺参数对99%氧化铝陶瓷的影响研究
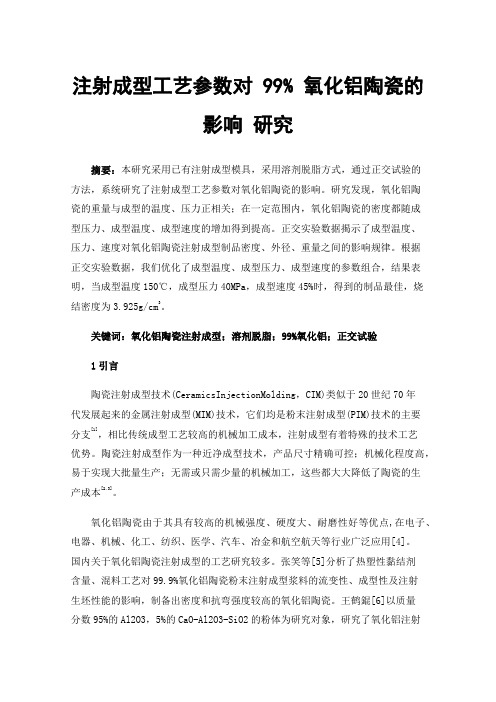
注射成型工艺参数对 99% 氧化铝陶瓷的影响研究摘要:本研究采用已有注射成型模具,采用溶剂脱脂方式,通过正交试验的方法,系统研究了注射成型工艺参数对氧化铝陶瓷的影响。
研究发现,氧化铝陶瓷的重量与成型的温度、压力正相关;在一定范围内,氧化铝陶瓷的密度都随成型压力、成型温度、成型速度的增加得到提高。
正交实验数据揭示了成型温度、压力、速度对氧化铝陶瓷注射成型制品密度、外径、重量之间的影响规律。
根据正交实验数据,我们优化了成型温度、成型压力、成型速度的参数组合,结果表明,当成型温度150℃,成型压力40MPa,成型速度45%时,得到的制品最佳,烧结密度为3.925g/cm3。
关键词:氧化铝陶瓷注射成型;溶剂脱脂;99%氧化铝;正交试验1引言陶瓷注射成型技术(CeramicsInjectionMolding,CIM)类似于20世纪70年代发展起来的金属注射成型(MIM)技术,它们均是粉末注射成型(PIM)技术的主要分支[1],相比传统成型工艺较高的机械加工成本,注射成型有着特殊的技术工艺优势。
陶瓷注射成型作为一种近净成型技术,产品尺寸精确可控;机械化程度高,易于实现大批量生产;无需或只需少量的机械加工,这些都大大降低了陶瓷的生产成本[2.3]。
氧化铝陶瓷由于其具有较高的机械强度、硬度大、耐磨性好等优点,在电子、电器、机械、化工、纺织、医学、汽车、冶金和航空航天等行业广泛应用[4]。
国内关于氧化铝陶瓷注射成型的工艺研究较多。
张笑等[5]分析了热塑性黏结剂含量、混料工艺对99.9%氧化铝陶瓷粉末注射成型浆料的流变性、成型性及注射生坯性能的影响,制备出密度和抗弯强度较高的氧化铝陶瓷。
王鹤錕[6]以质量分数95%的Al2O3,5%的CaO-Al2O3-SiO2的粉体为研究对象,研究了氧化铝注射成型所涉及的喂料制备、注射成型以及脱脂等工艺过程,研究了适合注射成型的95氧化铝粉体和石蜡-聚烯烃粘结剂体系,并对粘结剂组元的相容性进行了判断,针对脱脂过程中易产生的缺陷进行了分析,并提出了相应的解决措施。
粉末注射成型技术的研究与应用
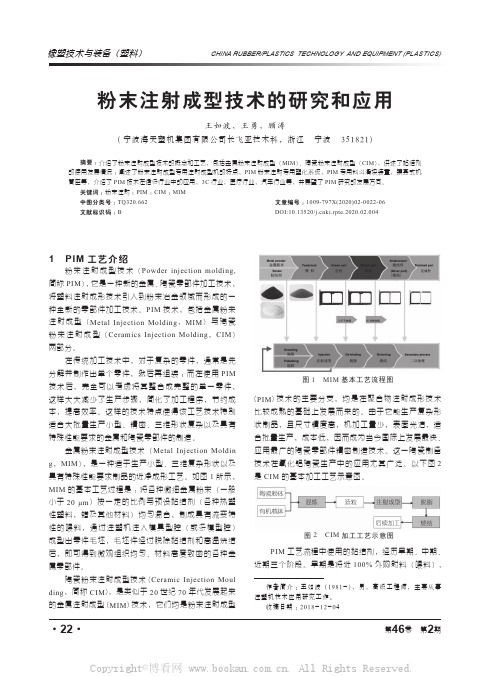
第46卷 第2期·22·作者简介:王如波(1981-),男,高级工程师,主要从事注塑机技术应用研究工作。
收稿日期:2018-12-041 PIM 工艺介绍粉末注射成型技术(Powder injection molding,简称PIM ),它是一种新的金属、陶瓷零部件加工技术,将塑料注射成形技术引入到粉末冶金领域而形成的一种全新的零部件加工技术。
PIM 技术,包括金属粉未注射成型(Metal Injection Molding ,MIM )与陶瓷粉未注射成型(Ceramics Injection Molding ,CIM )两部分。
在传统加工技术中,对于复杂的零件,通常是先分解并制作出单个零件,然后再组装;而在使用PIM 技术后,完全可以考虑将其整合成完整的单一零件,这样大大减少了生产步骤,简化了加工程序,节约成本,提高效率。
这样的技术特点使得该工艺技术特别适合大批量生产小型、精密、三维形状复杂以及具有特殊性能要求的金属和陶瓷零部件的制造。
金属粉末注射成型技术(Metal Injection Moldin g ,MIM ),是一种适于生产小型、三维复杂形状以及具有特殊性能要求制品的近净成形工艺。
如图1所示,MIM 的基本工艺过程是:将各种微细金属粉末(一般小于20 μm )按一定的比例与预设黏结剂(各种热塑性塑料,蜡及其他材料)均匀混合,制成具有流变特性的喂料,通过注塑机注入模具型腔(或多模型腔)成型出零件毛坯,毛坯件经过脱除黏结剂和高温烧结后,即可得到微观组织均匀、材料高度致密的各种金属零部件。
陶瓷粉末注射成型技术(Ceramic Injection Moul ding ,简称CIM ),是类似于20世纪70年代发展起来的金属注射成型(MIM )技术,它们均是粉末注射成型(PIM )技术的主要分支,均是在聚合物注射成形技术比较成熟的基础上发展而来的。
由于它能生产复杂形状制品,且尺寸精度高,机加工量少,表面光洁,适合批量生产,成本低,因而成为当今国际上发展最快、应用最广的陶瓷零部件精密制造技术。
金属粉末注射成型工艺流程

金属粉末注射成型工艺流程
金属粉末注射成型(Metal Powder Injection Molding,简称MIM)是一种先进的制造工艺,它结合了传统塑料注射成型和金属粉末冶金工艺的优点,可以生产复杂形状、高精度的金属零部件。
本文将介绍金属粉末注射成型的工艺流程。
首先,金属粉末注射成型的工艺流程包括原料准备、混合、注射成型、脱模、烧结和后处理等步骤。
原料准备,首先需要准备金属粉末和聚合物粉末。
金属粉末通常是通过粉末冶金工艺制备而成,具有一定的粒度和形状。
聚合物粉末则用作成型时的粘结剂。
混合,将金属粉末和聚合物粉末按一定比例混合,并加入一些添加剂,以提高成型性能和烧结性能。
注射成型,将混合物装入注射成型机,通过高压将其注入模具中,形成所需的零部件形状。
注射成型机通常具有高精度和高压力控制系统,以确保成型零件的精度和质量。
脱模,成型后的零部件需要经过脱模处理,通常是通过加热或
溶剂脱模的方式将聚合物粘结剂去除,得到金属粉末预制件。
烧结,金属粉末预制件在高温下进行烧结,使金属颗粒之间发
生扩散和结合,形成致密的金属零件。
后处理,烧结后的零部件可能需要进行表面处理、热处理、机
加工等工艺,以达到最终的产品要求。
总的来说,金属粉末注射成型工艺流程结合了粉末冶金和注射
成型技术的优势,可以生产出具有复杂形状、高精度的金属零部件,广泛应用于汽车、航空航天、医疗器械等领域。
随着材料和工艺的
不断改进,金属粉末注射成型技术将在未来得到更广泛的应用和发展。
金属、陶瓷粉末注射成型工艺简介

金属、陶瓷粉末注射成型工艺简介:金属、陶瓷粉末注射成型工艺技术是一种将粉末冶金工艺、粉末陶瓷工艺与塑料注射成型工艺相结合的新型制造工艺技术。
该工艺技术适合大批量生产小型、精密、复杂及具有特殊性能要求的金属陶瓷零件的制造。
该工艺的基本过程是:将微细的金属或陶瓷粉末与有机粘结剂均匀混合成为具有流变性的物料,采用先进的注射机注入具有零件形状的模腔形成坯件,新技术脱除粘结剂并经烧结,使其高度致密成为制品,必要时还可以进行后处理。
金属、陶瓷粉末注射成型工艺技术是近年来世界粉末冶金领域发展最快的高新技术。
该工艺技术的研究起始于70年代末,由于它适用性强、市场广阔,而且潜力巨大,所以一出现,便受到普遍重视,发展非常迅速。
美国、日本和西欧等发达国家率先形成产业规模。
1、粉末注射成型工艺特点:1)零部件几何形状的自由度高,制件各部分密度均匀、尺寸精度高,适于制造几何形状复杂、精密及具有特殊要求的小型零件(0.05g-200g);2)合金化灵活性好,对于过硬、过脆、难以切削的材料或原料铸造时有偏析或污染的零件,可降低制造成本;3)产品质量稳定、性能可靠,制品的相对密宽可达92-98%,可进行渗碳、淬火、回火等处理;4)加工零件的典型公差为±0.05mm;5)工艺流程短、生产效率高,易于实现大批量、规模化生产;2、粉末注射成型适用的材料:主要有Fe合金、Fe-Ni合金、不锈钢、Kovar合金、W合金、钛合金、Stellite Si-Fe合金、Hastelloy 合金、硬质合金、永磁合金及氧化铝、氮化硅、氧化锆等陶瓷材料。
3、粉末注射成型技术的应用领域:计算机及其辅助设施:如打印机零件、磁头、磁芯、撞针轴销、驱动零件;工具:如钻头、刀头、喷丸咀、枪钻、螺旋铣刀、冲头、套筒、扳手、电工工具、手工工具等;家用器具:如表壳、表链、电动牙刷、剪刀、风扇、高尔夫球头、珠宝链环、圆珠笔卡箍、照相机用等零件;医疗机械用零件:如牙矫形架、剪刀、镊子;军用零件:导弹尾翼、枪支零件、弹头、药型罩、引信用零件;电气用零件:微型马达、电子零件、传感器件;机械用零件:如松棉机、纺织机、卷边机、办公机械等;。
粉末注射成型

粉末注射成型
粉末注射成型(Powder Injection Moulding,简称PIM)是一种将金属或陶瓷粉末通过加工制造成零件的技术。
这
个过程类似于传统的塑料注射成型,但使用的是金属或陶
瓷粉末。
整个过程包括以下步骤:
1. 材料准备:选择合适的金属或陶瓷粉末,并按照特定的
配方制备成所需的粉末混合物。
2. 注射成型:将粉末混合物装入注射机中,并通过高压将
粉末推入模具中。
模具通常是具有所需形状的两个半球体。
3. 球芯去除:等到粉末充填到模具后,球芯会自动脱落并
迅速冷却固化。
4. 焙烧:固化的零件需要经过焙烧过程,以去除残留的有
机物,并增加材料的密度和强度。
5. 精加工:将焙烧后的零件进行必要的后续加工,例如打磨、抛光等。
6. 检测和质量控制:对成品进行检测,确保其符合规定的
尺寸和质量标准。
粉末注射成型技术具有许多优点,例如可以生产形状复杂的零件,材料利用率高,生产效率高等。
它被广泛应用于汽车、医疗器械、工具等领域的零部件制造。
- 1、下载文档前请自行甄别文档内容的完整性,平台不提供额外的编辑、内容补充、找答案等附加服务。
- 2、"仅部分预览"的文档,不可在线预览部分如存在完整性等问题,可反馈申请退款(可完整预览的文档不适用该条件!)。
- 3、如文档侵犯您的权益,请联系客服反馈,我们会尽快为您处理(人工客服工作时间:9:00-18:30)。
微粉末注射成型氧化铝通道摘要微粉末注射成型氧化铝通道是由亚微米级的氧化铝粉末和特制的粘接剂开发制作而成。
在小规模的搅拌作用下,混合原料在四种不同的力的作用下建立一个合适的粉末载量。
所选的原料的热性能和流变性能必须经过检查以便用于建立大规模的搅拌、脱脂和微通道在不同温度下进行烧结。
结果表明,成型、脱脂和烧结通道具有良好的保形性。
微通道的部分尺寸可以通过不同的处理步骤来改变。
在1350℃以上高度致密的微通道可以通过烧结实现。
超过1350℃,随着温度的升高,晶粒显著增多,从而导致硬度降低。
引言粉末注射成型(PIM)是建立在大规模生产复杂金属和陶瓷零件的基础上的。
在几年前,有越来越多的微型元件从微型PIM中获得利益。
微型元件可分为三种:微细,微结构元件及微型精密部件。
微型零件一般被认为单一或分居在几毫米范围内的外部尺寸的组件,但是尺寸必须在亚毫米的范围内。
有几个毫米的外形尺寸微结构元件一般位于一个或者几个表面区域上。
金属、陶瓷微PIM部件和微结构元件在各个领域的运用都有很大的潜力和市场,比如说医疗技术、微系统技术、微流体、微传感器和微机械等。
微PIM四个主要步骤:混合,注射成型,脱脂和烧结。
在搅拌的过程中,首先是粘接剂和金属粉末或者是陶瓷粉末相混合形成注射成型的原料。
原料必须被制造成合适的大小以便注射成型。
在注射成型期间,通过控制温度以及压力来形成所需要的形状。
在固化之后打开模具并进行脱模处理,一个初步的微结构元件就会从模腔中脱离而出。
下一步就是脱脂处理。
通过脱脂之后,微结构单元就会得到所需要的属性。
由于微型PIM所需要的功能部分或者细节是微米级的,所以粘接剂、粉末和相关的加工过程必须必PIM更加严格。
为了获得成功的微型的PIM,一个重要的先决条件是粘接剂和粉末的量要合适。
粘接剂必须提供一个最低的粘度以便在注射过程中能够轻易的注射到型腔中去,同时必须保证脱模性能好、其次具有良好的保型性和在脱脂和烧结过程中较低的收缩性。
其中必须专门的制定微型PIM原料,以便全面的满足基于传统的粘结剂的原料全过程能力的需要,例如在注射微小结构时的成型限制问题和较大的高宽比以及微型尺寸容易被很小的力破坏的问题。
为了能够得到结构微小、烧结密度高、表面光洁度好、性能优良的微型元件,良好的细粒度是首选条件。
金属粉末平均半径在1-5μm适合大多数情况,尽管良好的细密度来自于更好的表面光洁度。
在陶瓷粉末颗粒更容易获得的情况下,有必要制定开发从亚微米级到纳米级的原料以便全面开发微PIM的潜能。
因为表面积大和凝聚相关,所以必须处理细粒度特别是纳米级的。
通过使用更多更细的粘接剂涂在微粒的表面可以加快烧结后的收缩。
一份可用粉末报告表明,只有一部分的亚微米级的粉末被使用。
例如铁,钨,钴,氧化锆,氧化铝和碳化钨。
一般规则有就是说最低标准是能够10倍的粒子尺寸。
因此生产较小的结构,好的细粒度是必须的。
因为采用了较小的细粒度,所以脱脂必须认真对待。
这是因为粒子之间的空间非常小,较小的细粒度能促进快速脱脂过程中裂纹的形成。
通过烧结的作用粒子的大小减小了100倍。
例如一般PIM是20μm通过烧结增加100倍的压力之后变为200nm。
在致密化、烧结周期包含长时间持续在关键的致密温度,以适应诱导应力和压力的变化,必须提供充足的时间来避免扭曲微型元件。
微通道部件被使用在许多微型系统例如:微反应器、微传感器、微流体器件和微型光学系统。
本文所涉及制造氧化铝通道所使用的为170nm的亚微米级材料。
一种专门配制的粘接剂被使用以便适应高亚微米级的比表面积。
在研究中通过选择不同粉末载量来寻找合适的粉末载量。
注射、脱脂、烧结微通道的特性是可以控制的。
2 实验内容2.1 材料实验中使用的亚微米级的粉末是高纯度的氧化铝粉(TM达)是由日本泰美化工有限公司提供。
不规则形状粉末所示的显微照片(见图1),它是通过场发射扫描电子显微镜(JEOL获得,它的平均粒径为170纳米左右。
使用BET比表面积分析仪测得适用于表面分析的是4.4平方米/每克,粉末的密度测得为3.96克/每平方厘米。
一个多组分的粘合剂包括以下几种成分:低密度聚乙烯、乙烯、醋酸乙烯酯和硬脂酸。
在重量比上低密度聚乙烯:乙烯:醋酸乙烯酯:硬脂酸为35:30:25:10。
其中聚乙烯的成分最多。
粘接剂的热学特性必须得到良好的控制以便适合混合的条件。
表1展示了几种粘接剂组成部分的热学特性。
最高熔融温度是126℃,是粘接剂在Perkin-Elmer差示扫描量测组件(DSC)模型7下测得的。
在Perkin-Elmer热分析仪(TGA)模型7最低的开始降解温度为155◦C的水杨酸。
表12.2原料的制备小规模的粉末和粘合剂混合可以在哈克电阻90转矩流变仪里面进行。
从小规模的混合中我们可以建立适当的粉末载量。
我们研究了从50%体积到56%体积之间以2%体积增量的混合载量。
由此我们得到了从1.63mg/m2到1.28mg/m2硬脂酸的重量和表面积的比。
在粘接剂各成分的热学特性的基础上,混合时温度应该设为150℃,高于熔融温度126℃并低于最低的分解温度155℃。
这将有助于完全融化和防止分解。
搅拌速度设为50转。
在混合的时候,首先向里面加入的是粘接剂的成分,其次再向其中加入粉末,每一分钟向里面加入一勺的量的粉末。
通过加入不同量的粉末我们选择52%体积的粉末载量。
然后对所选用的原来进行热学特性以及流变特性进行测试。
通过Perkin-Elmer热分析仪(TGA)可以对从30◦C至600◦C热降解的原料进行了评估。
从30◦C至600◦C原料的融化和再结晶温度可以通过Perkin-Elmer差示扫描量热(DSC)进行了检查。
对于TGA和DSC测试,可以采用氮气为净化气体,加热速率为10℃/min。
可以通过毛细管流变仪来研究原料的流变特性。
测试流变特性时,可以需要使用一个长度为40mm,直径为1mm的模具。
可以选用130℃、140℃、150℃、160℃进行测试。
所使用的温度应该低于原料的分解温度。
2.3大规模混合通过哈克电阻90转矩流变仪可以进行小规模混合,并且可以得到合适的粉末载量以及流变特性(将在3.3节讨论)。
在此基础上,大型混合是在赫尔曼·林登Z型刀片搅拌机进行。
粉末和粘接剂是在130℃的情况下混合,混合速度为40转。
粘接剂成分按照聚乙烯、乙烯、醋酸乙烯酯和硬脂酸的顺序加入到搅拌机中。
接着在向里面加入2勺粉末每分钟。
最终粉末将被颗粒化以方便注塑成型。
图22.4注塑成型颗粒性的原料在带有往复螺旋杆的巴顿菲尔250 CDC卧式注塑机上注塑到氧化铝通道中去。
在这里将会使用一个双板边缘浇口模具。
一个插入了11根微通道的硅模具被使用。
合适的注射成型参数如表2所示。
表2面向硅片被用来制作规模的插入。
可以通过深反应粒子刻蚀技术来制造标准的8英寸微通道。
将刻蚀好的硅片切成尺寸为6mm×6mm的正方形。
其中每个正方形拥有11各微通道。
每个微通道有PLμ聚焦分析器来测量。
测量的尺寸为宽为200μm,深为135μm,长为4mm。
切成的正方形硅片即插入式硅模具,将其安装在一个可移动的半圆形模腔上。
如图2所示,在JSM-5600LV扫描电子显微镜(SEM)下观测到的在注塑机上的可移动模具的一半。
2.5脱脂和烧结微通道模压零件在95%的氩气和5%的氢气的混合气体的情况的林德伯格管炉中进行热脱脂。
好在空气中或者在氧气中进行通知下相比,氩气和氢气的混合气体能够保证较慢的粘接剂清除率。
这将有利于获得无缺陷、高强度的部件。
根据合适的脱脂资料所显示的时间、温度和升温速度来进行脱脂。
脱脂资料是在早期的316L不锈钢粉末的基础上获得的。
最高的脱脂温度可以设定在600℃以确保所有粘接剂成分被清除和处理。
进过脱脂之后,在进行无压烧结,无压烧结在高温CM箱式炉中进行五种不同温度的烧结。
它的升温速度为5℃/min直到烧结温度,并在烧结温度保持60分钟。
2.6阐述成型、脱脂、烧结微通道的尺寸可以通过一个PLμ的20×放大倍率的物镜焦距来探查。
通过测量微通道的不同的六个点来进行测量。
图3显示的是微通道的微结构部分,本次反应的只是一个平均值。
圆盘的直径也要被测量。
烧结微通道的密度通过阿基米德原理来确定。
成型和烧结的微通道可以通过JSM-5600LV扫描电子显微镜进行观察。
然后进行微通道进行切片处理,将切好的微通道安装在截面抛光的环氧树脂上。
抛光的横截面用于硬度的测量。
将300g的负载放置在微通道上然后在进行显微硬度测试。
热抛光截面的微通道可以在空气中低于各自的烧结温度下刻蚀将近15—30分钟,使用场发射扫描电子显微镜(低轨1550)对蚀刻截面进行观察。
图3a图3b3.结果与讨论3.1合适粉末载量的测定在哈克搅拌机汇中进行小批量混合时,稳定的转矩和混合时间可以获得均匀的粉末。
图4显示了不同粉末载量的转矩和混合时间。
在起初的10分钟里面,将粘接剂加入到搅拌机中去。
当粉末以较小的量加入到搅拌机中时,在10—20分钟之间扭矩显著增加。
经过搅拌约25分钟之后,扭矩达到一个稳定的状态,除了粉末载量为56%体积的。
对于粉末载量为56%体积的,其扭矩会随着时间增加而显著增加。
这表明粉末不能均匀的分布在粘接剂中。
这是因为粘接剂在混合时不能够完全的填充到颗粒之间的间隙中。
在粉末载量为54%体积时,扭矩会在混合90分钟之后又较小的增加。
对于粉末载量是52%体积的和50%体积的,转矩在混合中比较稳定。
然而较低的粉末载量会引起在注塑成型过程粉末粘接剂分离和烧结过程中收缩率较高。
因此选用粉末载量为52%体积的比粉末载量为50%体积的更加有利于注塑成型。
3.2热特性图5a显示了多成分的粘接剂的TGA曲线图和各组分的TGA曲线图。
从TGA图中可以看出从低密度聚乙烯、醋酸乙烯酯到硬脂酸逐渐降低。
然而乙烯的退化分为两个阶段因为在较高的温度下乙烯、乙炔聚合物断链以及侧链醋酸的断链。
同样通过多组分混合而成的粘接剂的TGA曲线也有两个退化步骤。
通过TGA曲线比较可以清晰的看出,醋酸乙烯酯和硬脂酸以及乙烯的第一退化阶段温度范围为(164℃—390℃),然而低密度聚乙烯的第一退化阶段温度范围为(425℃—520℃)。
超过520℃,粘接剂各种成分将会消失。
TGA曲线显示,多步骤的脱脂过程主要是为了逐步消除粘接剂四种成分。
很宽的脱脂温度有助于保留微观结构的完整性和阻止脱脂的负面效应的产生,例如气泡、裂纹和滑塌。
TGA曲线表明流变测试和注塑时的温度应该低于最低粘接剂成分的降解温度(即164℃),以便于预防粘接剂降解。
图5a图5b显示三个吸收峰值在56℃、70℃和119℃,三个放热峰值在50℃、57℃和100℃现在发现的主要原因为粘接剂的融化和再结晶作用。
在56℃高峰时,主要是因为醋酸乙烯酯和硬脂酸的融化。