金属成型新工艺:MIM(金属粉末注射成型)工艺详细介绍
mim工艺技术

mim工艺技术MIM(Metal Injection Molding)是一种综合了传统粉末冶金技术和塑料注塑成型技术的金属成形工艺。
它利用聚合物为载体,在高压注射成型时将金属粉末喷射入模具中,然后通过高温和高压烧结成型。
MIM工艺技术已经广泛应用于各个领域,如电子、汽车、医疗、化工等。
MIM工艺技术的优势之一是可以制造复杂形状的零部件。
相比传统的金属加工工艺,MIM工艺可以制造具有内孔、薄壁、复杂曲线等特殊结构的零部件,而且生产效率高。
MIM工艺的制造工艺是分为四个主要步骤:压注成型、脱模、脱脂和底漆。
通过调整模具的形状和复杂度,可以生产出各种各样的金属零件。
MIM工艺技术的另一个优势是材料的选择性。
根据不同的应用需求,可以选择不同的金属粉末制作零部件。
常用的MIM材料包括不锈钢、合金钢、硬质合金、钴合金等。
这些材料具有高强度、耐磨、耐腐蚀等特点,能够更好地满足各种应用的需求。
MIM工艺技术还具有材料利用率高、成本低等优点。
相较于传统的CNC加工工艺,MIM工艺可以最大限度地减少材料浪费,提高成品率和利用率。
同时,MIM工艺采用批量生产的方式,可以实现大规模生产,降低生产成本。
因此,MIM工艺技术已成为制造业中非常重要的一种生产工艺。
然而,MIM工艺技术也存在一些挑战和限制。
首先,对于一些特殊形状的零件,模具的设计和制造可能会较为困难,需要更高的精确度和工艺控制。
其次,对于一些特殊材料,如高温合金等,MIM工艺可能无法满足其特殊的热处理要求。
此外,MIM工艺在生产过程中也需要严格控制温度、压力等参数,以保证产品质量。
总之,MIM工艺技术通过结合粉末冶金和塑料注塑成型技术,实现了金属零件的高效制造。
其可以制造复杂形状的零部件,材料选择性高,且材料利用率高、成本低。
虽然存在一些挑战和限制,但这种工艺技术在制造业中具有广泛的应用前景。
随着技术的进一步发展,MIM工艺技术将不断改进和完善,为各行各业提供更好的解决方案。
MIM技术介绍
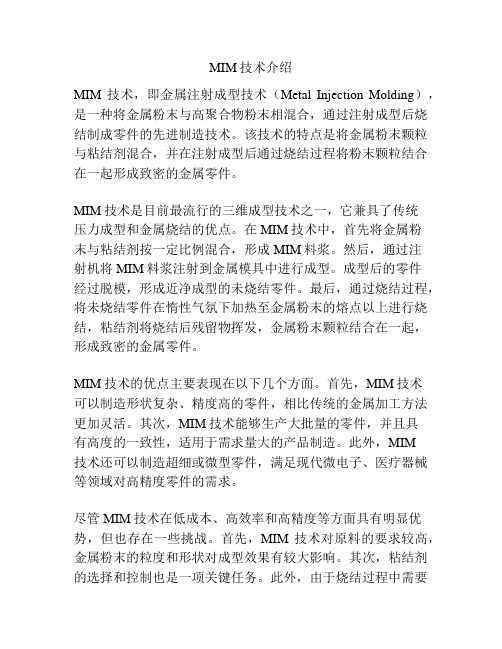
MIM技术介绍MIM技术,即金属注射成型技术(Metal Injection Molding),是一种将金属粉末与高聚合物粉末相混合,通过注射成型后烧结制成零件的先进制造技术。
该技术的特点是将金属粉末颗粒与粘结剂混合,并在注射成型后通过烧结过程将粉末颗粒结合在一起形成致密的金属零件。
MIM技术是目前最流行的三维成型技术之一,它兼具了传统压力成型和金属烧结的优点。
在MIM技术中,首先将金属粉末与粘结剂按一定比例混合,形成MIM料浆。
然后,通过注射机将MIM料浆注射到金属模具中进行成型。
成型后的零件经过脱模,形成近净成型的未烧结零件。
最后,通过烧结过程,将未烧结零件在惰性气氛下加热至金属粉末的熔点以上进行烧结,粘结剂将烧结后残留物挥发,金属粉末颗粒结合在一起,形成致密的金属零件。
MIM技术的优点主要表现在以下几个方面。
首先,MIM技术可以制造形状复杂、精度高的零件,相比传统的金属加工方法更加灵活。
其次,MIM技术能够生产大批量的零件,并且具有高度的一致性,适用于需求量大的产品制造。
此外,MIM技术还可以制造超细或微型零件,满足现代微电子、医疗器械等领域对高精度零件的需求。
尽管MIM技术在低成本、高效率和高精度等方面具有明显优势,但也存在一些挑战。
首先,MIM技术对原料的要求较高,金属粉末的粒度和形状对成型效果有较大影响。
其次,粘结剂的选择和控制也是一项关键任务。
此外,由于烧结过程中需要控制温度和气氛等因素,烧结工艺相对复杂。
因此,MIM技术的成功应用需要综合考虑材料、工艺和设备等多个因素。
总的来说,MIM技术是一种高度灵活、高效率、高精度的金属成型方法,已在汽车、航空航天、电子、医疗器械等领域得到广泛应用。
随着材料科学和制造技术的不断发展,MIM技术将进一步完善和推广,为各个行业提供更多高质量的金属零件。
MIM技术作为一种金属粉末成型技术,具有独特的优势和特点,逐渐成为制造业中不可忽视的一种先进工艺。
MIM金属成型新工艺
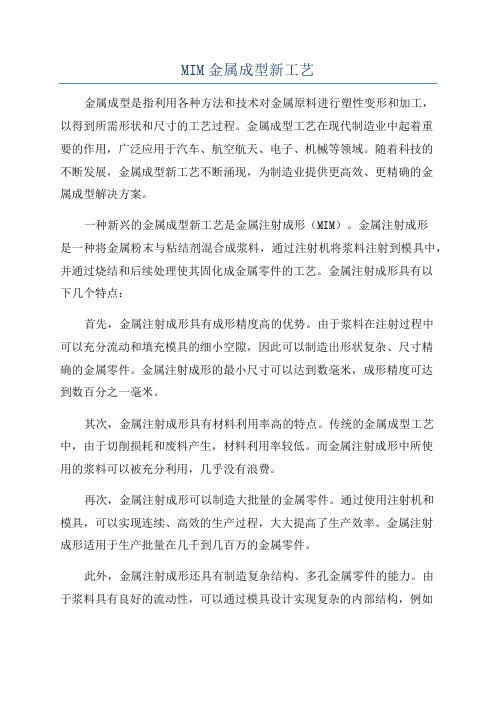
MIM金属成型新工艺金属成型是指利用各种方法和技术对金属原料进行塑性变形和加工,以得到所需形状和尺寸的工艺过程。
金属成型工艺在现代制造业中起着重要的作用,广泛应用于汽车、航空航天、电子、机械等领域。
随着科技的不断发展,金属成型新工艺不断涌现,为制造业提供更高效、更精确的金属成型解决方案。
一种新兴的金属成型新工艺是金属注射成形(MIM)。
金属注射成形是一种将金属粉末与粘结剂混合成浆料,通过注射机将浆料注射到模具中,并通过烧结和后续处理使其固化成金属零件的工艺。
金属注射成形具有以下几个特点:首先,金属注射成形具有成形精度高的优势。
由于浆料在注射过程中可以充分流动和填充模具的细小空隙,因此可以制造出形状复杂、尺寸精确的金属零件。
金属注射成形的最小尺寸可以达到数毫米,成形精度可达到数百分之一毫米。
其次,金属注射成形具有材料利用率高的特点。
传统的金属成型工艺中,由于切削损耗和废料产生,材料利用率较低。
而金属注射成形中所使用的浆料可以被充分利用,几乎没有浪费。
再次,金属注射成形可以制造大批量的金属零件。
通过使用注射机和模具,可以实现连续、高效的生产过程,大大提高了生产效率。
金属注射成形适用于生产批量在几千到几百万的金属零件。
此外,金属注射成形还具有制造复杂结构、多孔金属零件的能力。
由于浆料具有良好的流动性,可以通过模具设计实现复杂的内部结构,例如螺纹、孔洞和腔体等。
同时,金属注射成形可以通过粉末混合调整粉末颗粒的大小和密度,以控制零件的质量和性能。
然而,金属注射成形也存在一些挑战和局限性。
首先,由于注射工艺的复杂性,需要专门的设备和工艺进行生产,成本较高。
其次,金属零件的烧结和后续处理过程需要时间和能源的消耗。
此外,由于浆料中包含有机粘结剂,金属注射成形的零件还需要经过脱脂和烧结等工艺步骤,以去除粘结剂和提高零件的物理性能。
综上所述,金属注射成形是一种具有巨大潜力的金属成型新工艺。
它通过提高成形精度、材料利用率和生产效率,为制造业带来了更多的机遇和挑战。
MIM金属注射成形工艺解析
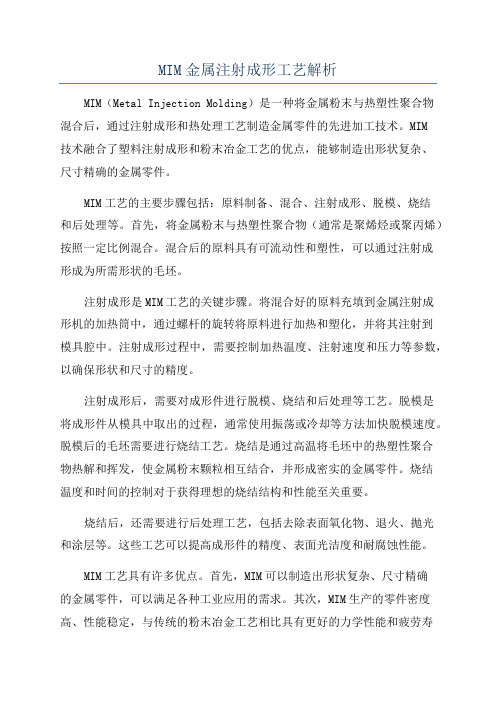
MIM金属注射成形工艺解析MIM(Metal Injection Molding)是一种将金属粉末与热塑性聚合物混合后,通过注射成形和热处理工艺制造金属零件的先进加工技术。
MIM技术融合了塑料注射成形和粉末冶金工艺的优点,能够制造出形状复杂、尺寸精确的金属零件。
MIM工艺的主要步骤包括:原料制备、混合、注射成形、脱模、烧结和后处理等。
首先,将金属粉末与热塑性聚合物(通常是聚烯烃或聚丙烯)按照一定比例混合。
混合后的原料具有可流动性和塑性,可以通过注射成形成为所需形状的毛坯。
注射成形是MIM工艺的关键步骤。
将混合好的原料充填到金属注射成形机的加热筒中,通过螺杆的旋转将原料进行加热和塑化,并将其注射到模具腔中。
注射成形过程中,需要控制加热温度、注射速度和压力等参数,以确保形状和尺寸的精度。
注射成形后,需要对成形件进行脱模、烧结和后处理等工艺。
脱模是将成形件从模具中取出的过程,通常使用振荡或冷却等方法加快脱模速度。
脱模后的毛坯需要进行烧结工艺。
烧结是通过高温将毛坯中的热塑性聚合物热解和挥发,使金属粉末颗粒相互结合,并形成密实的金属零件。
烧结温度和时间的控制对于获得理想的烧结结构和性能至关重要。
烧结后,还需要进行后处理工艺,包括去除表面氧化物、退火、抛光和涂层等。
这些工艺可以提高成形件的精度、表面光洁度和耐腐蚀性能。
MIM工艺具有许多优点。
首先,MIM可以制造出形状复杂、尺寸精确的金属零件,可以满足各种工业应用的需求。
其次,MIM生产的零件密度高、性能稳定,与传统的粉末冶金工艺相比具有更好的力学性能和疲劳寿命。
此外,MIM工艺还具有高效、节能的特点,能够减少生产过程中的材料浪费和能源消耗。
然而,MIM工艺仍然存在一些挑战。
首先,原料的成本较高,这对于大规模生产来说可能增加成本。
其次,MIM工艺对模具的要求较高,模具的制造成本较高。
此外,MIM的工艺周期较长,生产效率相对较低。
总之,MIM金属注射成形工艺是一种先进的金属加工技术,具有制造形状复杂、尺寸精确的金属零件的优势。
MIM工艺介绍及其应用

MIM工艺介绍及其应用MIM(Metal Injection Molding)工艺是一种将金属粉末与热塑性或热固性高分子混合,并通过注射成型和烧结工艺制造出复杂金属零件的技术。
MIM工艺结合了传统金属加工和塑料注射成型技术的优点,能够实现高精度、高复杂度的金属零件制造,并在很多行业得到广泛应用。
MIM工艺的制造过程主要包括以下几个步骤。
首先,将金属粉末与高分子材料混合,并制成类似塑料颗粒的混合物。
然后,将混合物注入金属注射成型机中,通过高压注射将其注射到预先设计好的模具中。
注射成型后,通过烧结工艺将混合物中的高分子材料去除,使金属粉末颗粒相互结合,形成致密的金属零件。
最后,对烧结后的零件进行精加工和表面处理,以实现最终的产品要求。
MIM工艺具有许多独特的优点,使其在各个领域得到广泛应用。
首先,MIM工艺可以制造出具有复杂形状和高精度的金属零件,可替代传统加工如铸造、机械加工等。
其次,MIM工艺可以生产不锈钢、合金、硬质合金等多种金属材料的零件,具有高强度和耐磨损性。
此外,MIM工艺还具有节约原材料、降低成本和提高生产效率的优势。
MIM工艺在汽车、电子、医疗器械、航空航天等行业中得到广泛应用。
在汽车行业,MIM工艺可用于制造发动机配件、承载结构件等关键零部件,提高汽车的性能和可靠性。
在电子行业,MIM工艺可用于制造手机壳、键盘、连接器等微小精密零件,提升产品的外观和功能。
在医疗器械领域,MIM工艺可应用于制造植入式医疗器械如人工关节、牙科支架等,提供定制化解决方案。
在航空航天领域,MIM工艺可用于制造航空发动机内部零部件,提高发动机的性能和可靠性。
总之,MIM工艺通过结合金属粉末和高分子材料,实现了复杂形状和高精度金属零件的制造,并在汽车、电子、医疗器械、航空航天等领域得到广泛应用。
随着材料科学和制造工艺的不断进步,MIM工艺将会在更多领域发挥重要作用,并为各行各业提供更多创新的解决方案。
MIM(Metal Injection Molding)工艺是一种先进的金属加工技术,通过将金属粉末与热塑性或热固性高分子混合,并通过注射成型和烧结工艺制造出具有复杂形状和高精度的金属零件。
mim工艺硬度
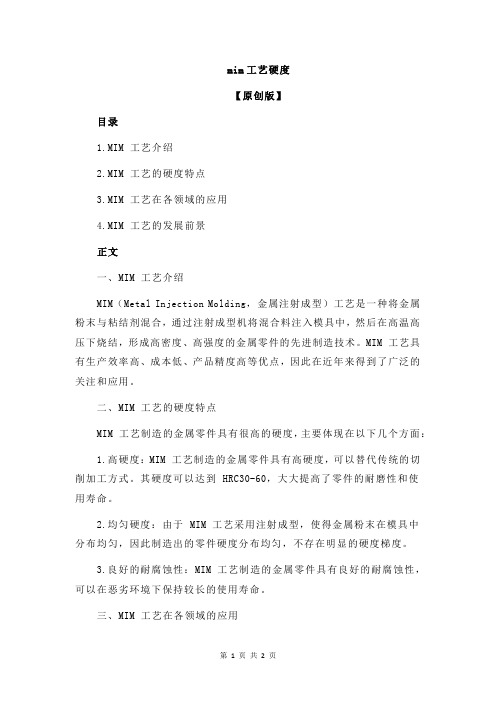
mim工艺硬度【原创版】目录1.MIM 工艺介绍2.MIM 工艺的硬度特点3.MIM 工艺在各领域的应用4.MIM 工艺的发展前景正文一、MIM 工艺介绍MIM(Metal Injection Molding,金属注射成型)工艺是一种将金属粉末与粘结剂混合,通过注射成型机将混合料注入模具中,然后在高温高压下烧结,形成高密度、高强度的金属零件的先进制造技术。
MIM 工艺具有生产效率高、成本低、产品精度高等优点,因此在近年来得到了广泛的关注和应用。
二、MIM 工艺的硬度特点MIM 工艺制造的金属零件具有很高的硬度,主要体现在以下几个方面:1.高硬度:MIM 工艺制造的金属零件具有高硬度,可以替代传统的切削加工方式。
其硬度可以达到 HRC30-60,大大提高了零件的耐磨性和使用寿命。
2.均匀硬度:由于 MIM 工艺采用注射成型,使得金属粉末在模具中分布均匀,因此制造出的零件硬度分布均匀,不存在明显的硬度梯度。
3.良好的耐腐蚀性:MIM 工艺制造的金属零件具有良好的耐腐蚀性,可以在恶劣环境下保持较长的使用寿命。
三、MIM 工艺在各领域的应用MIM 工艺在许多领域都有广泛的应用,尤其在以下几个领域表现突出:1.电子行业:MIM 工艺制造的金属零件广泛应用于手机、电脑等电子产品的壳体、支架等部件,提高了产品的性能和美观度。
2.汽车行业:MIM 工艺制造的金属零件在汽车发动机、变速器、悬挂系统等关键部件中得到应用,降低了生产成本,提高了汽车的整体性能。
3.医疗行业:MIM 工艺制造的金属零件在医疗器械中具有广泛的应用,如骨科植入物、牙科植入物等,其高硬度和良好的耐腐蚀性为医疗器械提供了可靠的性能保障。
4.军工领域:MIM 工艺制造的金属零件在军事装备中具有广泛的应用,如枪支、炮弹等部件,提高了军事装备的性能和可靠性。
四、MIM 工艺的发展前景随着科技的发展和市场需求的不断提高,MIM 工艺在未来有着广阔的发展前景。
MIM金属注射成形工艺

MIM金属注射成形工艺MIM(Metal Injection Molding)金属注射成形工艺是一种集粉末冶金和塑料注射成形技术于一体的先进制造工艺。
它能够将金属粉末与有机粘结剂混合后注射成形,再通过脱脂和烧结工艺将有机粘结剂去除,最终得到具有高密度和良好力学性能的金属零件。
MIM工艺是20世纪70年代初期由美国开发出来的,随后逐渐发展成为一种重要的中小型复杂金属部件加工方法。
MIM工艺具有以下几个特点:1.范围广泛:MIM工艺可以用于加工多种金属材料,如不锈钢、钨合金、硬质合金、软磁合金等,能够满足不同行业的各类零件加工需求。
2. 高精度:MIM工艺能够制造出极其复杂形状的零件,其尺寸精度可以达到0.01mm,能够满足不同行业对于精度要求较高的零件加工需求。
3.高密度:由于MIM工艺采用了高压注射成形和高温烧结工艺,所得金属零件具有较高的密度,接近于纯金属的密度,因此具有良好的力学性能。
4.成本低:相比于传统的加工方法,MIM工艺具有成本低、生产效率高的特点。
同时,由于MIM工艺能够实现零件的复合成形,使得原本需要多道工序制造的零件可以一次性完成,从而节约了生产成本。
MIM工艺的加工过程主要包括原料制备、注射成形、脱脂和烧结四个步骤:1.原料制备:首先需要将金属粉末和有机粘结剂按一定比例混合,得到可以流动注射的MIM料浆。
2.注射成形:将MIM料浆注入MIM注射机中,经过热筒和螺杆的作用,将MIM料浆注射到注射模具中,形成所需形状的零件。
3.脱脂:将注射成形后的零件进行脱脂处理。
脱脂是将有机粘结剂从注射件中去除的过程,通常通过热脱脂和溶剂脱脂两种方法进行。
4.烧结:脱脂后的注射件在高温环境下进行烧结处理。
烧结是将金属粉末粒子相互结合的过程,通过高温使金属粉末颗粒间形成颗粒间结合,从而得到具有高密度和良好力学性能的金属零件。
总结一下,MIM金属注射成形工艺通过将金属粉末与有机粘结剂混合注射成形,然后经过脱脂和烧结工艺,最终得到高密度和良好力学性能的金属零件。
金属粉末注射成型
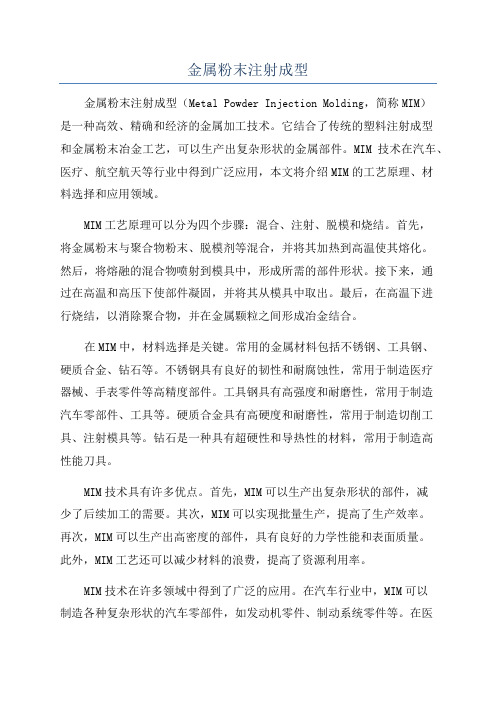
金属粉末注射成型金属粉末注射成型(Metal Powder Injection Molding,简称MIM)是一种高效、精确和经济的金属加工技术。
它结合了传统的塑料注射成型和金属粉末冶金工艺,可以生产出复杂形状的金属部件。
MIM技术在汽车、医疗、航空航天等行业中得到广泛应用,本文将介绍MIM的工艺原理、材料选择和应用领域。
MIM工艺原理可以分为四个步骤:混合、注射、脱模和烧结。
首先,将金属粉末与聚合物粉末、脱模剂等混合,并将其加热到高温使其熔化。
然后,将熔融的混合物喷射到模具中,形成所需的部件形状。
接下来,通过在高温和高压下使部件凝固,并将其从模具中取出。
最后,在高温下进行烧结,以消除聚合物,并在金属颗粒之间形成冶金结合。
在MIM中,材料选择是关键。
常用的金属材料包括不锈钢、工具钢、硬质合金、钻石等。
不锈钢具有良好的韧性和耐腐蚀性,常用于制造医疗器械、手表零件等高精度部件。
工具钢具有高强度和耐磨性,常用于制造汽车零部件、工具等。
硬质合金具有高硬度和耐磨性,常用于制造切削工具、注射模具等。
钻石是一种具有超硬性和导热性的材料,常用于制造高性能刀具。
MIM技术具有许多优点。
首先,MIM可以生产出复杂形状的部件,减少了后续加工的需要。
其次,MIM可以实现批量生产,提高了生产效率。
再次,MIM可以生产出高密度的部件,具有良好的力学性能和表面质量。
此外,MIM工艺还可以减少材料的浪费,提高了资源利用率。
MIM技术在许多领域中得到了广泛的应用。
在汽车行业中,MIM可以制造各种复杂形状的汽车零部件,如发动机零件、制动系统零件等。
在医疗行业中,MIM可以制造高精度医疗器械,如人工关节、牙科器械等。
在航空航天行业中,MIM可以制造轻量化部件,提高了飞机的燃油效率。
此外,MIM还可以应用于电子、军工等领域。
总之,金属粉末注射成型是一种高效、精确和经济的金属加工技术。
通过在MIM中选择合适的材料和工艺参数,可以生产出各种复杂形状的金属部件,并在汽车、医疗、航空航天等行业中得到广泛应用。
- 1、下载文档前请自行甄别文档内容的完整性,平台不提供额外的编辑、内容补充、找答案等附加服务。
- 2、"仅部分预览"的文档,不可在线预览部分如存在完整性等问题,可反馈申请退款(可完整预览的文档不适用该条件!)。
- 3、如文档侵犯您的权益,请联系客服反馈,我们会尽快为您处理(人工客服工作时间:9:00-18:30)。
金属成型新工艺:MIM(金属粉末注射成型)工艺详细介绍
小编备注:结合国内目前MIM现状补充了一些资料。
转载请注明文章来源:金属注射成型网 1 MIM是一种近净成形金属加工成型工艺
MIM (Metal injection Molding )是金属注射成形的简称。
是将金属粉末与其粘结剂的增塑混合料注射于模型中的成形方法。
它是先将所选金属粉末与粘结剂进行混炼,然后将混合料进行制粒再注射成形所需要的形状胚料,然后通过高温烧结,得到具有强度的金属零件。
2 MIM工艺流程步骤
MIM流程结合了注塑成型设计的灵活性和精密金属的高强度和整体性,来实现极度复杂几何部件的低成本解决方案。
MIM流程分为四个独特加工步骤(混合、成型、脱脂和烧结)来实现零部件的生产,针对产品特性决定是否需要进一步的机械加工或进行表面处理.
混合
精细金属粉末和热塑性塑料、石蜡粘结剂按照精确比例进行混合。
混合过程在一个专门的混合设备中进行,加热到一定的温度使粘结剂熔化。
大部分情况使用机械进行混合,直到金属粉末颗粒均匀地涂上粘结剂冷却后,形成颗粒状(称为原料),这些颗粒能够被注入模腔。
CNPIM备注:混炼是MIM工艺中非常重要的一道工序。
目前混炼有几种体系,不同的添加剂,后面对应需要不同的脱脂方法将添加剂去除。
最常用的蜡基和塑基,分别对应热脱脂和催化脱脂。
成型
注射成型的设备和技术与注塑成型是相似的。
颗粒状的原料被送入机器加热并在高压下注入模腔。
这个环节形成(green part)冷却后脱模,只有在大约200°c的条件下使粘结剂熔化(与金属粉末充分融合),上述整个过程才能进行,模具可以设计为多腔以提高生产率。
模腔尺寸设计要考虑金属部件烧结过程中产生的收缩。
每种材料的收缩变化是精确的、已知的。
脱脂
脱脂是将成型部件中粘结剂去除的过程。
这个过程通常分几个步骤完成。
绝大部分的粘结剂是在烧结前去除的,残留的部分能够支撑部件进入烧结炉。
脱脂可以通过多种方法完成,最常用的是溶剂萃取法。
脱脂后的部件具有半渗透性,残留的粘结剂在烧结时很容易被挥发。
CNPIM备注:目前最常用的脱脂方法是BASF推出的Catamold催化脱脂方法,需要用到专用的催化脱脂炉(欲了解详情,请关注本公众号,回复数字19,了解催化脱脂工艺,回复数字20,了解催化脱脂炉的结构和工作原理)
烧结
经过脱脂的部件被放进高温、高压控制的熔炉中。
该部件在气体的保护下被缓慢加热,以去除残留的的粘合剂。
粘结剂被完全清除后,该部件就会被加热到很高的温度,颗粒之间的空隙由于颗粒的融合而消失。
该部件定向收缩到其设计尺寸并转变为一个致密的固体。
对于大多数的材料,典型的烧结密度理论上大于97%。
高烧结密度使得产品性能与锻造材料相似。
CNPIM备注:对于常见的金属注射成型材料,目前常用的是真空烧结炉。
关注本公众号回复数字21,可查看真空烧结炉的工作原理介绍。
机械加工
CNPIM备注:这一段是小编补充加入进来的。
对于外观件或表面要求高、精度要求高的产品,或有些结构没有办法在注塑模具上一次成型的特征,会需要进行二次加工。
最常见的是CNC加工,钻孔攻牙。
这在手机数码产品零件上体现的比较明显。
有兴趣的了解一下苹果手机里面的金属部件的加工工艺。
表面处理
根据具体需求,有些部件烧结后可能需要进行表面处理。
热处理可以提高金属物理性能。
电镀、涂装可以应用于高密度材料。
提供焊接或冷却处理技术。
CNPIM备注:还是补充说外观件。
绝缘性能,不同的颜色,不同的质感,防指纹……等等,通过表面处理工艺,产品更加多姿多彩~~~~~对于外观件,PVD最常见,有兴趣可回复数字07了解PVD相关工艺简介。
3 MIM产品通常具有以下特性
复杂性
MIM和注塑成型一样,形状设计没有限制。
由于MIM是一个成型过程,附加的产品特性不会增加成本,这使得MIM成为将独立零件组合成多功能的产品的理想途径。
MIM设计规则同注塑成型非常接近,从而适用于几乎所有产品。
精密性
MIM净成型精度的参考设计通常是尺寸的±0.5%。
某些特性净成型能达到±0.3%。
如同其它技术一样,精度要求越高成本越高,因此在质量允许情况下鼓励适度放宽公差要求。
MIM一次成型无法达到的公差可以借助表面处理实现。
重量和尺寸
MIM特别适合重量小于100克的零部件,少于50克是最经济的。
然而,重量达250克的零部件也可以处理。
MIM工艺的主要成本是原材料,因此MIM通过新技术来尽可能减少零部件的重量。
同塑料产品一样,可以在不影响产品完整性的条件下,通过内核和支架来减少零部件的重量。
MIM在极小和微型零部件方面表现突出,重量小于0.1克也是可行的。
重量不是限制因素,长度超过250mm的产品也能被处理。
薄型化
小于6毫米的壁厚对于MIM是最适合的。
较厚的外壁也可以,但是成本会由于处理时间长和增加额外材料而增加。
另外,低于0.5 mm 的极薄壁对MIM也是能实现,但对设计有很高的要求
产量
MIM是弹性较大的工艺,年需求量几千到几百万的产量能够非常经济地实现。
和铸造件、注塑件一样,MIM需要客户投资模具和工具费用,所以对小批量的产品而言,通常会影响到成本估算。
原料
MIM能处理很多材料,包括铁合金、超级合金、钛合金、铜合金、耐火金属、硬质合金、陶瓷和金属基复合材料。
虽然有色合金铝和铜在技术上是可行的,但是通常由其他更经济的方式进行处理,如压铸或机加工。
4 MIM设计指导
MIM被广泛运用到各个汽车、医疗、电子、工业、消费等各行业,产品涉及包括汽车配件、航空航天器材、移动电话、牙科仪器、电子散热器和密封包装、电子连接器硬件、工业工具、光纤连接器、喷雾系统、盘驱动器、医疗设备、手持电动工具、手术器械和运动器材等。
内容来源:材料馆整理,补充。
更多MIM技术资料,请访问。