塑料水杯注塑模具设计说明书
塑料水杯模具设计说明书
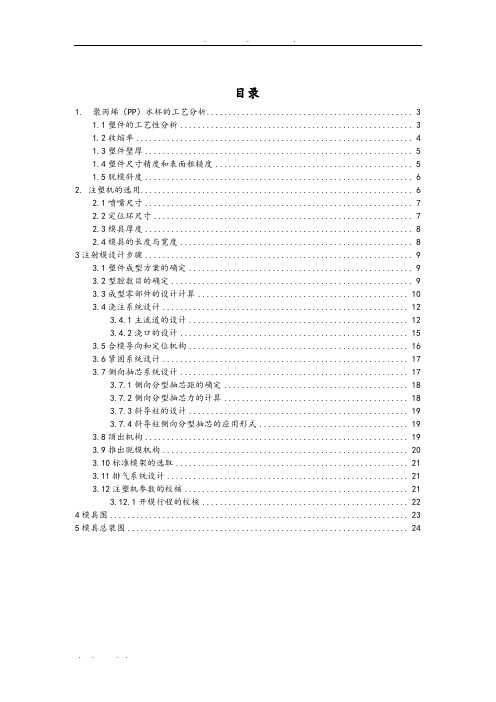
2. 注塑机的选用.............................................................. 6 2.1 喷嘴尺寸 ............................................................. 7 2.2 定位环尺寸 ........................................................... 7 2.3 模具厚度 ............................................................. 8 2.4 模具的长度与宽度 ..................................................... 8
..
..
.
.
.
聚丙烯(PP)水杯注塑模设计
摘 要:本文对水杯的技术要求和工艺结构进行了分析,确定了工艺方案及 模具形式。而且对水杯进行了相关数据的分析与计算, 根据分析结果选注塑机和 注塑工艺,从而确定聚丙烯水杯设计思路及方案,最后在设计过程中运用Pro/E、 Auto CAD软件进行注塑模结构设计与计算并绘制出模具总装图以及部分非标准 图形。从而得出完整的理论设计结果,为今后工程设计打下了基础。.来自..目录
1. 聚丙烯(PP)水杯的工艺分析............................................... 3 1.1 塑件的工艺性分析 ..................................................... 3 1.2 收缩率 ............................................................... 4 1.3 塑件壁厚 ............................................................. 5 1.4 塑件尺寸精度和表面粗糙度 ............................................. 5 1.5 脱模斜度 ............................................................. 6
塑料水杯模具设计说明书
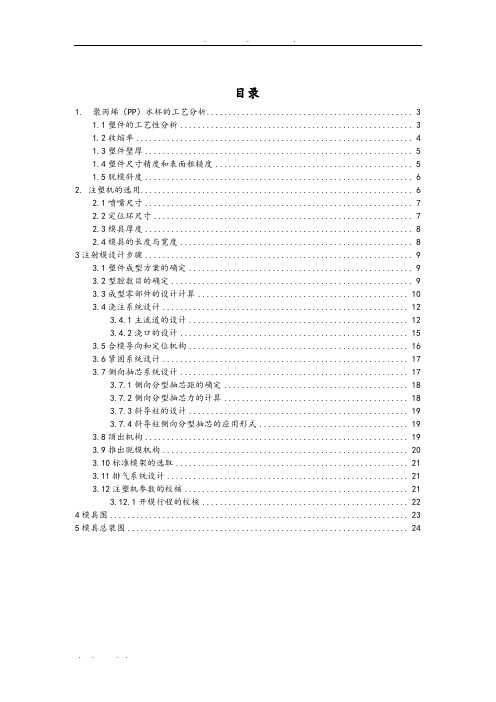
图1-1主要尺寸
..
..
.
.
.
1.2 收缩率
前人已经为我们总结了常用的塑料常用收缩率,对于生产性的塑件,实际已
经证明,这些数据已经能够应付实际的生产要求了。即使对于精密塑件也给予了
其它方面的补偿。故而,对于实际的生产只要按照经验数据就可以满足生产要求
了。表1-3给出常见塑料的收缩率,以备查询:
塑
料 名
4 模具图 .................................................................... 23 5 模具总装图 ................................................................ 24
该产品图反映出,此塑料件最大壁厚为3.0mm,最小壁厚为2mm,壁厚均匀, 在2mm—4mm的推荐值之间。易于成型。
水杯模具设计说明书

课程设计说明书专业:模具设计与制造学生姓名:学号:指导教师:2014年6月26 日摘要本次课程设计课题是PP水杯注塑模设计,本文详细介绍了注射模具模架、成型零部件、浇注系统和脱模系统等模具主要的设计过程,并对模具强度要求做了说明。
设计中对注射机的相关参数进行了验证,包括模具闭合厚度、模具安装尺寸、模具开模行程、注射机的锁模力等。
校核合格后进行了成型零件加工工艺过程的制定,既保证了塑件的质量,又兼顾了经济性。
最后在设计过程中运用Auto CAD、UG 软件进行注塑模结构设计与计算,并绘制出了模具总装图以及部分零件图,从而得出完整的理论设计结果,为今后工程设计打下了基础。
目录前言 (1)一概述 (2)1.1设计目的 (2)1.2 模具设计的主要内容和任务 (2)1.2.1 塑料模具设计任务 (2)1.2.2 收集、分析、消化原始资料 (2)1.2.3 确定成型方法 (3)二塑件成型工艺性分析 (4)2.1塑件的分析 (4)2.1.1外形尺寸 (4)2.1.2 精度等级 (5)2.2 PP性能分析 (5)2.3 PP的注射成型过程及工艺参数 (5)三拟定模具的结构形式 (7)3.1分型面位置的确定 (7)3.2 型腔数量和排列方式的确定 (8)3.3注射机型号的确定 (9)四浇注系统和成型零件的设计 (12)4.1 浇注系统的设计 (13)4.1.1 主流道的设计 (13)4.1.2 分流道的设计 (14)4.1.3 浇口的设计 (15)4.1.4 冷料井的设计 (17)4.2 成型零件的结构设计及计算 (17)4.2.1成型零件的结构设计 (17)4.2.2成型零件钢材的选用 (18)4.2.3成型零件工作尺寸的计算 (18)4.2.4 成型零件尺寸及动模垫块厚度的计算 (19)4.2.5 排气槽的设计 (19)五模架和推出机构的设计 (20)5.1 模架的确定 (20)5.1.1 各模板尺寸的确定 (20)5.1.2模架各尺寸的校核 (20)5.2 脱模推出机构的设计 (21)5.2.1脱模机构 (21)5.2.2推出方式的确定 (21)5.3 导向和定位结构的设计 (22)第6章总结 (23)附录总装图 (24)前言本说明书为PP水杯注塑模设计说明书,是根据塑料模具手册上的设计过程及相关工艺编写的。
注塑-茶杯塑料模具课程设计-说明书

注塑-茶杯塑料模具课程设计-说明书目录任务书 (1)前言 (4)一.产品分析 (5)1. 分析制件原料的工艺性 (5)2. 分析制件的结构.尺寸精度及表面质量 (6)3. 塑件壁厚 (7)4. 脱模斜度 (7)二.塑件成型方案的确定 (7)三.型腔布局与分型面设计.......................................... 71. 型腔数目的确定.......................................... 82.型腔的布3. ................................................................................................................. 分型面的设计. (8)三.成型零件工作尺寸计算........................................... 91. 外型尺寸............................................. 92.型腔尺3 . 型芯尺寸四. 选标准模架131. 型腔强度和刚度的计算架的结构形式和规格。
(13)五. 初选注射机 ................................................. 131.注射量 .................................................. 132.合模 力 .................................................. 133.初选注射机型号 (13)六. ................................................................校核注射机 (13)1. 注射量.锁模力.注射压力.模具厚度的校核 (13)2. 开模行程的校核 (13)3..模具在注射机上的安装 (14)七. ................................................................浇注系统设计 (14)1. 主流道的设计 (14)2、 浇口的设计 (14)3校核流动比 (15)八. 合模导向机构的设计 (16)七. 脱模机构的设计 (18)八. 合模导向机构的设计 (19)九. 冷却系统设计 (19)十.紧固系统设计 ................................................... 20 12 132. 确定模十^一.排气系统的设计 (20)十三.模具零件图 (21)十二.模具总装图 (21)22小结参考文献23、尸、-前言pp塑料聚丙烯英文名称:polypropylene密度:0.9-0.91 克/立方厘米成型收缩率:1.0-2.5% 成型温度:160-220 C干燥条件: 如果储存适当则不需要干燥处理。
塑料水杯注塑模具设计说明书

目录1 塑件的成型工艺分析 (3)1.1 塑件的原材料分析 (3)1.2 塑料件的尺寸分析 (3)1.3 塑件表面质量分析 (3)1.4 塑件结构工艺性分析 (4)1.5 成形工艺参数、工艺卡 (4)1.5.1 塑件的体积及质量 (4)1.5.2 选用注射机 (4)1.5.3 塑件注射成型工艺参数 (5)2 模具结构方案的确定 (6)2.1 型腔数目的确定 (6)2.2 分型面的选择 (7)2.3 浇注系统的设计 (8)2.3.1主流道的设计 (8)2.3.2 浇口的设计 (9)2.4 侧向抽芯系统设计 (10)2.4.1 侧向分型抽芯距的确定 (10)2.4.2 侧向分型抽芯力的计算 (10)2.4.3 斜导柱的设计 (11)2.4.4 斜导柱的材料及安装配合 (11)2.5 推出机构设计 (12)2.5.1 设计原则 (12)2.5.2 推杆材料 (12)2.5.3 推杆的形式 (12)2.5.4 推杆的导向 (13)2.5.5 推杆的复位 (13)2.6 标准模架的选择 (13)2.7 排气温控系统设计 (14)3 成型零件工作尺寸的计算 (14)3.1 成型零部件的磨损 (15)3.2 成型零部件的制造误差 (15)3.3 塑件的基本尺寸计算 (15)3.3.2 型腔深度 (15)3.3.3 型芯高度 (15)3.3.4 壁厚 (16)3.3.5 圆角 (16)3.3.6 柄长 (16)4 注射机有关工艺参数的校核 (17)4.1 注射量的校核 (17)4.2 注射压力的校核 (17)4.3 锁模力的校核 (17)4.4 装模部分有关尺寸的校核 (18)4.4.1 模具闭合高度的校核 (18)4.4.2 模具安装部分的校核 (18)4.4.3 模具开模行程的校核 (18)4.4.4 顶出部分的校核 (18)1、塑件的成型工艺分析1.1 塑件的原材料分析塑件原材料为PP 中文名: 聚丙烯表1.1 塑件的原材料分析结论:干燥处理:如果储存适当则不需要干燥处理。
毕业设计杯子模具设计说明书

1. 塑件的分析脱模斜度0.75度图1.1 塑件结构示意图1.1外形尺寸该塑件壁厚为2mm,塑件外形尺寸不大,塑件熔体流程不太长,塑件材料为无填充材料的PP,流动性好,适合于注射成型。
1.2精度等级本塑件采用一般精度4级。
1.3脱模斜度由于该塑件的脱模高度约为70mm,由脱模斜度表可查得:聚丙烯PP的脱模斜度为0.75°。
2. 成型材料PP的成型特性与工艺参数2.1 PP的成型特性聚丙烯为白色蜡状塑料,外观似聚乙烯,但比聚乙烯更轻,密度为0.9~0.91g/cm3,强度、刚度、硬度、耐热性均优于低压聚乙烯,可在100℃左右使用,具有良好的电性能和高频绝缘性,不受温度影响,但低温时易变脆、不耐磨,易老化,适于制作一般机械零件、耐腐蚀零件和绝缘零件。
PP的主要性能指标如表2.1所示表2.1 PP物理性能参数名称参数密度0.9~0.91g/cm3比体积 1.10~1.11cm3/g吸水率0.03%~0.04%熔点170~176℃收缩率 1.0%~3.0%比热容1930J/(Kg.℃)屈服强度37Mpa拉伸弹性模量 1.65×103Mpa弯曲强度67Mpa弯曲弹性模量 1.45×103Mpa2.2 PP的工艺参数聚丙烯PP是非极性结晶性塑料,吸湿性小,约为0.03﹪~0.04﹪,一般不需干燥,流动性好,溢边料为0.025~0.04mm,收缩范围及收缩值大,并具各向异性,易发生缩孔、凹痕和变形,热稳定性好,成型温度范围较宽,抗氧化能力低,在塑化前应加入一定比例的抗氧剂,塑料壁厚应均匀,避免缺胶、尖角,以防应力集中。
其注射工艺参数如表2.2所示表2.2 PP的注射工艺参数名称参数螺杆转速30~60r/min 料筒温度前段160~180℃中段180~200℃后段200~230℃喷嘴温度180~190℃模具温度40~80℃注射压力70~120Mpa冷却时间20~90s成型时间40~120s3. 设备型号的确定3.1估算塑件一次成型的注射量3.1.1塑件体积和质量的计算塑件的体积按式3.1计算ab a a a d V l l h d h ⋅⋅+⋅⋅+⋅∏+⋅⋅⋅∏=⎪⎭⎫ ⎝⎛222212塑(式 3.1)cm33210264)2161221246227064(-⨯⨯⨯+⨯⨯+⨯⨯∏+⨯⨯⨯∏=⎪⎭⎫ ⎝⎛=36.07cm 3塑件的质量按式3.2计算V 塑塑⋅=ρm(式 3.2)g 82.3207.3691.0=⨯=式中: ρ----聚丙烯的密度,取0.91g/cm 3选择注射机型号为SZ ——100/60,其理论注射量Vc=100cm 3。
塑料杯子设计说明书
塑料杯子设计说明书一、引言塑料杯子作为现代生活中不可或缺的日常用品,其设计与质量直接关系到用户的使用体验和安全性。
本设计说明书旨在介绍塑料杯子的设计原理、材料选择、制造工艺以及相关注意事项,为生产商提供参考和指导。
二、设计原理塑料杯子的设计应遵循以下原则:1. 容量合理:根据用户需求和市场调研确定塑料杯子的容量,通常为200ml、300ml、500ml等常见规格。
2. 结构稳定:塑料杯子应具备良好的结构稳定性,能够承受正常使用过程中的压力,不易变形或破裂。
3. 易于使用:设计应考虑到用户的使用习惯和便利性,例如口径合适、易握持、易清洗等。
4. 安全卫生:材料的选择应符合相关标准,不含有害物质,且易于清洁和消毒。
三、材料选择塑料杯子通常采用食品级聚丙烯(PP)或聚乙烯(PE)作为主要材料。
这两种材料具有良好的耐热性、耐腐蚀性和耐磨性,且符合食品安全标准。
在材料选择时,还需要考虑杯盖、杯底等部件的材料,常见的选择有硅胶、聚乙烯等,这些材料应具备耐高温、耐酸碱腐蚀等特性。
四、制造工艺1. 注塑成型:将选定的材料加热熔融后,通过注塑机注入模具中,冷却后即可得到塑料杯子的基本形状。
2. 吹塑成型:将选定的材料加热熔融后,通过吹塑机将熔融物料吹进模具中,通过气压使其膨胀成型,再经过冷却即可得到塑料杯子。
3. 拔塑成型:将选定的材料加热熔融后,通过拔塑机将熔融物料从模具中拉伸成型,再经过冷却即可得到塑料杯子。
五、注意事项1. 使用时请勿将塑料杯子暴露于高温环境中,以免变形或释放有害物质。
2. 避免将塑料杯子放入微波炉或烤箱中加热,以免引发火灾或杯子破裂。
3. 塑料杯子不宜长时间接触酸性或碱性物质,以免引起杯子变色或起泡。
4. 使用后请及时清洗,避免残留污渍或异味影响下次使用。
5. 塑料杯子在长时间存放或携带时,应避免受到撞击或压力,以免造成变形或破裂。
六、结论通过合理的设计原理、优质的材料选择和先进的制造工艺,塑料杯子可以满足用户的使用需求,并保证其安全卫生性。
塑料模具设计杯子课程设计说明书
目录一、产品的设计及要求 (4)二、塑件的工艺分析 (5)2.1 分析塑件使用材料的种类及工艺特征 (5)2.2 塑件结构、尺寸精度分析 (5)2.3 塑件的结构工艺性分析 (5)2.4 塑件分析 (6)2.5 塑件模塑成型工艺参数的确定 (6)三、初步确定型腔数目和排列方式 (7)四、成型零部件工作尺寸的计算 (7)4.1塑件的平均收缩率 (7)4.2型腔尺寸的计算 (7)4.3型芯尺寸的计算 (8)五、型腔的侧壁和底板厚度的计算 (8)5.1型腔的侧壁厚度计算 (8)5.2型腔的底板厚度计算 (9)六、型芯型腔的设计 (9)6.1型芯的设计 (9)6.2型腔的设计 (10)七、分型面的选择 (10)7.1分型面的选择设计原则 (10)八、导向机构的设计 (11)8.1导柱的设计 (11)8.2导套的结构设计 (12)8.3推出机构的设计 (12)九、台阶型拉杆导柱设计 (12)十、模架的选择 (13)10.1模架类型选择 (13)10.2模架周界计算 (13)10.3模架图示例 (13)十一、注射机的选择 (16)11.1塑件体积的计算 (16)11.2模具最大厚度的计算 (16)11.3开模行程的计算 (17)11.4锁模力的计算 (17)11.5选择注射机 (17)十二、浇注系统的设计 (18)12.1主流道的设计 (18)12.2浇口的设计 (19)十三、结束语 (20)十四、参考文献 (21)前言良好的塑料制品工艺性是获得合格制品的前提,也是模塑工艺得以顺利进行和模具达到经济合理要求的基本条件。
所谓注塑成型(Injection Molding)是指:受热融化的材料由高压射入模腔,经冷却固化后,得到成形品的方法。
一、产品的设计及要求零件名称:杯子生产批量:大批量未注公差:MT 5要求设计一套模具二、塑件的工艺分析2.1 分析塑件使用材料的种类及工艺特征塑件材料结构特点使用温度化学稳定性性能特点成型特点ABS 微黄色固体,有一定的韧性-40~100度良好,溶于酮、醛、酯和某些氯代烃中,热稳定性差。
水杯模具设计说明书
水杯模具设计说明书学院:桂林航天工业学院专业:模具设计与制造学号:Z0137姓名:周礼平指导老师:叶东2014 年1 月3 号I摘要摘要本次课程设计课题是PP水杯注塑模设计,本文详细介绍了注射模具模架、成型零部件、浇注系统和脱模系统等模具主要的设计过程,并对模具强度要求做了说明。
设计中对注射机的相关参数进行了验证,包括模具闭合厚度、模具安装尺寸、模具开模行程、注射机的锁模力等。
校核合格后进行了成型零件加工工艺过程的制定,既保证了塑件的质量,又兼顾了经济性。
最后在设计过程中运用Auto CAD软件进行注塑模结构设计与计算,并绘制出了模具总装图以及部分零件图,从而得出完整的理论设计结果,为今后工程设计打下了基础。
目录前言 ........................................................................... 错误!未定义书签。
一、概述................................................................. 错误!未定义书签。
1.1设计目的 ........................................................ 错误!未定义书签。
1.2模具设计的主要内容和任务........................ 错误!未定义书签。
1.2.1 塑料模具设计任务 ............................. 错误!未定义书签。
1.2.2 收集、分析、消化原始资料............. 错误!未定义书签。
1.2.3 确定成型方法 ..................................... 错误!未定义书签。
二、塑件成型工艺性分析................................... 错误!未定义书签。
塑料水杯盖注塑模具设计说明
塑料水杯盖注塑模具设计摘要:塑料工业是当今世界上增长最快的工业门类之一,而注塑模具是其中发展较快的种类,因此,研究注塑模具对了解塑料产品的生产过程和提高产品质量有很大意义。
本设计介绍了注射成型的基本原理,特别是单分型面注射模具的结构与工作原理,对注塑产品提出了基本的设计原则;详细介绍了冷流道注射模具浇注系统、温度调节系统和顶出系统的设计过程,并对模具强度要求做了说明,通过本设计,可以对注塑模具有一个初步的认识,注意到设计中的某些细节问题,了解模具结构与工作原理。
关键词:塑料模具;分型面;设计Abstract:The plastics industry in the world grows one of now quickest industry classes, but the injection mold is develops the quick type, therefore, the research injection mold to understood that the plastic product the production process and improves the product quality to have the very big significance. This design introduced injection molding's basic principle, specially single is divided the profile to inject mold's structure and the principle of work, to cast the product to propose the basic principle of design; Introduced in detail the cold flow channel injection mold gating system, the temperature control system and goes against system's design process, and has given the explanation to the mold intensity request, through this design, may have a preliminary understanding to the injection mold, notes in the design certain detail question, understands the mold structure and the principle of work.Key word: Plastic;injection mold;Design目录:第一章绪论 (3)课题背景与意义 (3)1.2 本课题与相关领域的国外现状与发展 (3)1.2.1 塑料模功能 (3)1.2.2 国外塑料模现状 (3)1.2.3塑料模发展趋势 (4)第2章产品材料的基本特性与产品工艺分析 (5)2.1.1 注射模设计特点 (5)2.1 注塑模概述 (5)2.1.2 注射模的组成件 (5)2.2 塑件的工艺分析 (5)2.2.1塑料制品的材料 (7)2.2.2分析塑件的结构工艺性 (8)2.2.3 塑件的尺寸精度分析 (8)2.2.4 表面质量分析 (8)2.3 分型面与排气槽的设计 (8)2.3.1 分型面的设计 (8)2.3.2 排气槽的设计 (8)2.4 注射机的选用 (8)2.4.1 型腔数目的确定 (8)2.4.2 注射机的选择 (8)第三章:注塑模的结构设计 (10)3.3 浇注系统的设计 (10)3.3.1 主流道的设计 (10)3.3.2 浇口设计 (10)3.3.3合模导向机构设计 (10)3.3.4 导柱的设计 (11)3.3.5 导套的设计 (11)3.4 成型零件的设计 (11)3.4.1 型腔型芯的设计 (11)3.4.2型腔、型芯径向尺寸计算 (12)3.4.3 型腔、型芯的深度尺寸的计算 (13)3.4.4 螺纹成型零件的工作尺寸计算 (13)3.5 型腔侧壁厚度与底板厚度的校核 (14)3.5.1 刚度条件计算式 (14)3.5.2 强度条件计算式 (15)3.6 模外动力旋转脱模设计 (16)3.6.1 螺纹脱模力矩计算 (16)3.7模温调节系统设计 (17)3.7.1 冷却系统的简略计算 (17)3.7.1.1 热平衡计算 (17)3.7.1.2湍流计算 (18)3.7.1.3 冷却面积计算 (19)3.7.2冷却系统的设计 (19)3.8注射机有关尺寸的校核 (19)3.8.1最大注射量的校核 (19)3.8.2锁模力的校核 (20)3.8.3最大注射压力的校核 (20)3.8.4模具厚度校核 (21)3.8.5开模行程的校核 (21)3.9 模具设计总装图 (21)参考文献 (23)结论 (23)第1章绪论1.1 课题背景与意义市场竞争的日趋激烈,使得产品的功能日趋多元化,产品的生命周期不断缩短,塑料产品结构日趋多样化和复杂化,客户对产品质量的要求也越来越高。
- 1、下载文档前请自行甄别文档内容的完整性,平台不提供额外的编辑、内容补充、找答案等附加服务。
- 2、"仅部分预览"的文档,不可在线预览部分如存在完整性等问题,可反馈申请退款(可完整预览的文档不适用该条件!)。
- 3、如文档侵犯您的权益,请联系客服反馈,我们会尽快为您处理(人工客服工作时间:9:00-18:30)。
目录1 塑件的成型工艺分析 (3)1.1 塑件的原材料分析 (3)1.2 塑料件的尺寸分析 (3)1.3 塑件表面质量分析 (3)1.4 塑件结构工艺性分析 (4)1.5 成形工艺参数、工艺卡 (4)1.5.1 塑件的体积及质量 (4)1.5.2 选用注射机 (4)1.5.3 塑件注射成型工艺参数 (5)2 模具结构方案的确定 (6)2.1 型腔数目的确定 (6)2.2 分型面的选择 (7)2.3 浇注系统的设计 (8)2.3.1主流道的设计 (8)2.3.2 浇口的设计 (9)2.4 侧向抽芯系统设计 (10)2.4.1 侧向分型抽芯距的确定 (10)2.4.2 侧向分型抽芯力的计算 (10)2.4.3 斜导柱的设计 (11)2.4.4 斜导柱的材料及安装配合 (11)2.5 推出机构设计 (12)2.5.1 设计原则 (12)2.5.2 推杆材料 (12)2.5.3 推杆的形式 (12)2.5.4 推杆的导向 (13)2.5.5 推杆的复位 (13)2.6 标准模架的选择 (13)2.7 排气温控系统设计 (14)3 成型零件工作尺寸的计算 (14)3.1 成型零部件的磨损 (15)3.2 成型零部件的制造误差 (15)3.3 塑件的基本尺寸计算 (15)3.3.2 型腔深度 (15)3.3.3 型芯高度 (15)3.3.4 壁厚 (16)3.3.5 圆角 (16)3.3.6 柄长 (16)4 注射机有关工艺参数的校核 (17)4.1 注射量的校核 (17)4.2 注射压力的校核 (17)4.3 锁模力的校核 (17)4.4 装模部分有关尺寸的校核 (18)4.4.1 模具闭合高度的校核 (18)4.4.2 模具安装部分的校核 (18)4.4.3 模具开模行程的校核 (18)4.4.4 顶出部分的校核 (18)1、塑件的成型工艺分析1.1 塑件的原材料分析塑件原材料为PP 中文名: 聚丙烯表1.1 塑件的原材料分析结论:干燥处理:如果储存适当则不需要干燥处理。
熔化温度:220~275C,注意不要超过275C。
模具温度:40~80C,建议使用50C。
结晶程度主要由模具温度决定。
注射压力:可大到1800bar。
注射速度:通常,使用高速注塑可以使内部压力减小到最小。
如果制品表面出现了缺陷,那么应使用较高温度下的低速注塑。
流道和浇口:对于冷流道,典型的流道直径范围是4~7mm。
建议使用通体为圆形的注入口和流道。
所有类型的浇口都可以使用。
典型的浇口直径范围是1~1.5mm,但也可以使用小到0.7mm的浇口。
对于边缘浇口,最小的浇口深度应为壁厚的一半;最小的浇口宽度应至少为壁厚的两倍。
PP材料完全可以使用热流道系统。
1.2 塑料件的尺寸分析塑件零件图图1.2所示,根据零件图,该塑件尺寸精度无特殊要求,所有尺寸均为自由尺寸,可按MT5查取公差(参见课程“附录—模塑件尺寸公差表” )。
其主要尺寸公差标注如下(单位均为mm):高度尺寸:80-0.8678+0.86外形尺寸:ø 38-0.56ø 60-0.74内形尺寸:ø 36+0.56ø 56+0.741.3 塑件表面质量分析塑件是日常使用的水杯,要求外表美观、无斑点、无熔接痕,表面质量一般要求较高,在Ra0.8μm以上。
1.4 塑件结构工艺性分析聚丙烯(PP)水杯的收缩率按照前人经验取20/1000。
塑件水杯是薄壁回转体,为利于脱模,塑件的外壁有2°的脱模斜度,此斜度在常用的脱模斜度范围内,能保证顺利脱模,故无需另行设计。
热塑性塑料的壁厚应该控制在1mm—4mm之间。
此塑料件最大壁厚为4.0mm,最小壁厚为1.2mm,壁厚均匀,在推荐值之间。
易于成型。
1.5 成形工艺参数、工艺卡1.5.1 塑件的体积及质量根据图样尺寸,利用画图软件建立塑件三维模型,经分析得:塑件体积:V塑≈26880mm3塑件质量:M塑=ρV塑=1.04cm/g×26.88cm=27.96g塑件与浇注系统的总质量:M = M塑+ M凝≈ 54(g)1.5.2 选用注射机根据塑件的形状,取一模一件的模具结构,初步选取螺杆式注射成型机:G54-S200/400,表1.2为该注射机的技术参数。
1.5.3 塑件注射成型工艺参数PP塑件注射成型工艺参数如表1.2所示,(参见附录H),试模时,可根据实际情况作适当调整;模塑成型工艺卡如表1.3所示。
表1.2 ABS塑料的注射成型工艺参数中山火炬职业技术学院水杯注射工艺卡片资料编号车间模具教研室共页第页零件名称水杯材料牌号PP 设备型号G54-S200/400装配图号材料定额每模件数 1零件图号单件质量28g 工装号材料干燥设备G54-S200/400温度0C 80~1000C 时间h 4~6h料筒温度后段0C 160~180 中段0C 180~200 前段0C 200~220 喷嘴0C 170~190模具温度0C 80~90时间注射S 20~60 保压S 0~3 冷却S 20~90压力注射70~100 背压后处理温度0C时间定额辅助min 时间h 单件min检验控制校对审核组长车间主任检验组长主管工程师2.1 型腔数目的确定对于一个塑件的模具设计的第一步骤就是型腔数目的确定。
单型腔模具的优点是:塑件精度高;工艺参数易于控制;模具结构简单;模具制造成本低,周期短。
缺点是:塑件成型的生产率低、成本高。
单型腔模具适用于塑件较大,精度要求较高或者小批量及试生产。
多型腔模具的优点是:塑件成型的生产率高,成本低。
缺点是:塑件精度低;工艺参数难以控制。
模具结构复杂;模具制造成本高,周期长。
多型腔模具适用于大批量、长期生产的小塑件。
根据塑件的精度:根据经验,在模具中每增加一个型腔,塑件的尺寸精度就要降低4%。
确定型腔数目的方法:考虑到塑件的技术要求,本设计采用根据注射量方法确定型腔数目。
即:n =(0.8G-m2)/m1式中:G —注塑机的最大注射量(g),取200gm1 —单个塑件的重量(g)取200gm2—浇注系统的重量(g)取14.9g但根据产品结构和尺寸形状来看不起,由于该塑件尺寸形状很大,只能为一模一腔。
根据需要和后续加工的要求我们确定为平行于塑件的最大尺寸方向,中心分布。
2.2 分型面的选择分型面是指分开模具取出塑件和浇注系统凝料的可分离的接触表面。
一副模具根据需要可能有一个或两个以上的分型面,分型面可以是垂直于合模方向,也可以与合模方向平行或倾斜,我们在这里选用与合模方向平行和垂直。
模具分型面的选择原则:1、分型面应选在塑件最大截面处。
2、不影响塑件外观质量,尤其是对外观质量有明确要求的塑件更应注意。
3、有利于保证塑件的精度要求。
4、有利于模具的加工,特别是型腔的加工。
(尽可能使模具结构简便)5、有利于浇注系统、排气系统、冷却系统的设置。
6、便于塑件的脱模,尽量使塑件开模时留在动模一侧。
7、尽量减小塑件在合模平面上的投影面积,以减小所需锁模力。
8、便于嵌件的安装。
9、长型芯应置于开模方向。
分型面的开设如下图:2.3 浇注系统的设计流道设计包括主流道、浇口的设计。
2.3.1主流道的设计主流道通常位于模具中心塑料熔体入口处,它将注塑机喷嘴注出的塑料熔体导入分流道或是型腔。
由于主流道要与高温塑料熔体及注塑机喷嘴反复接触,所以在注塑模中主流道部分常设计成可以拆卸更换的主流道衬套。
在卧式或立式注塑机上使用的注塑模中,主流道垂直于模具分型面。
为了使塑料熔体按顺序的向前凝料能从主流道中顺利的拔出,需将主流道设计成圆锥形,具有2°~4°的锥角,内壁有Ra0.8μm以下的表面粗糙度,抛光时应沿轴向进行。
若沿圆周进行抛光,产生侧向凹凸面,使主流道凝料难以拔出。
同时浇图 2.2 浇口套与注塑机喷嘴关系口套与注塑机喷嘴接触平凡,为防止撞伤,应采取淬火处理使其具有较高的硬度(48HRC~52HRC)。
热塑性塑料的主流道衬套与注塑机喷嘴的尺寸:主流道始端直径φB=φA+(0.5~1)mm,球面凹坑半径R=X+(2~5)mm,半锥角a 为20~40,尽可能缩短长度L(小于60mm为佳)。
如图2.2所示。
本套模具主流道设计要点是:为便于凝料从主流道中拉出,主流道设计成圆锥形,其锥角α=3°,内壁粗糙度为Ra=0.63μm,整个主流道都在衬套中,并未采取分段组合形式。
主流道大端处是根据注塑机的喷嘴头来设计的,呈圆角,其半径R=21mm,以减小料流在转向时过渡的阻力。
为使熔融塑料从喷嘴完全进入主流道而不溢出,应使主流道和注塑机的喷嘴紧密接触,主流道对接处设计成半球形凹坑,其半径R= X +( 2~5 )mm,X=18mm,取R=21mm。
其主浇道小端直径d1= d2 +( 0.5~1 ) mm,取d1=4mm。
流道应保持光滑的表面,避免留有影响塑料流动和脱模的尖角毛刺等。
本套产品浇口套如图2.3。
图2.3 浇口套2.3.2 浇口的设计浇口是连接流道与型腔之间的一段细短通道,它是浇注系统的关键组成部分。
浇口的形状、位置和尺寸对制品的质量影响很大。
浇口的截面积通常为分流道的截面面积的0.03%~0.09%。
浇口截面积通常有矩形和圆形两种。
浇口长度约为0.5~2mm左右。
浇口具体尺寸一般根据经验确定,取其下限值,然后在试模时逐步修正。
在注塑模具中常用的浇口形式有直接浇口、点浇口、潜伏式浇口、侧浇口、重叠式浇口、圆环形浇口、护耳浇口等,浇口开设的位置对制品的质量影响很大,在确定浇口的位置时应注意以下几点:1. 浇口应设在能使型腔各个角落都可以同时填满的位置。
2. 浇口应设置在制品壁厚较厚的部位,使熔体从厚断面流向薄断面,以利于补料。
3. 浇口的部位应选在易于排除型腔内空气的位置。
4. 浇口的位置应选在能避免制品表面产生熔合纹的部位。
当无法避免产生熔合纹的产生时,浇口位置的选择应考虑到熔合纹产生的部位是否合适。
5. 浇口的设置应避免引起熔体断裂的现象。
6. 浇口应设置在不影响制品外观的部位。
7. 不要在制品中承受弯曲载荷或冲击载荷的部位设置浇口,一般制品浇口附近的强度较差。
由于设计零件是表面要求较高的塑件,又因为该模具因其结构复杂为3板模机构,故选择点浇口为佳。
并且表面网格的孔上。
2.4 侧向抽芯系统设计抽芯形式其结构如图2.5所示,此侧向抽芯机构是由(15)斜导柱等构成。
侧向抽芯的实现是在开模时定模底座带动斜导柱运动,而斜导柱又带动(2)定模板运动分开,从而实现侧抽芯。
图 2.4 抽芯形式其结构2.4.1侧向分型抽芯距的确定一般情况下,侧向抽芯距通常比塑件上的侧孔、侧凹的深度或侧凹凸台的高度大2~3mm 。
塑件上侧凹深38mm ,定抽芯距最少为(38+2)mm 即40mm 。