转动设备常见振动故障频谱特征案例分析
旋转机械设备常见故障特征分析
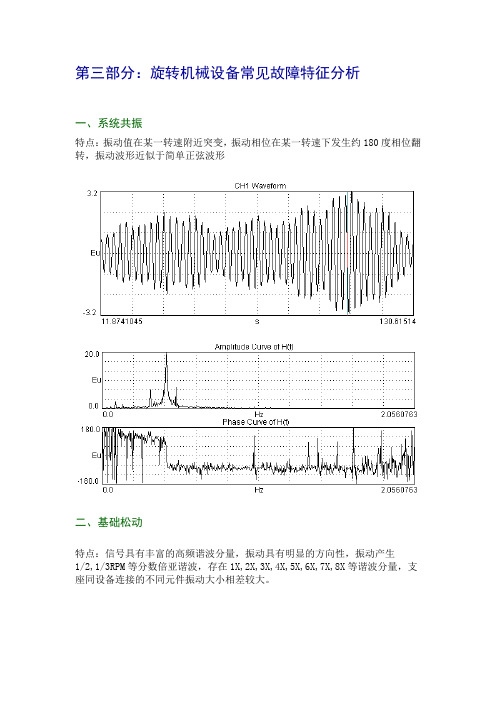
第三部分:旋转机械设备常见故障特征分析一、系统共振特点:振动值在某一转速附近突变,振动相位在某一转速下发生约180度相位翻转,振动波形近似于简单正弦波形二、基础松动特点:信号具有丰富的高频谐波分量,振动具有明显的方向性,振动产生1/2,1/3RPM等分数倍亚谐波,存在1X,2X,3X,4X,5X,6X,7X,8X等谐波分量,支座同设备连接的不同元件振动大小相差较大。
三.质量不平衡特点:1X频率成分大 ,Amp(1X)至少大于总振幅50%,相位稳定,幅值稳定,振幅随RPM的平方成正比,水平与垂直方向约有90度相变(+-30度)。
四.不对中故障特点:振动二倍频较大,负荷升高,振动逐渐增大,轴心轨迹香蕉形。
轴心轨迹正进动。
两轴承油压反方向变化。
五.轴初始弯曲故障特点:轴承1X幅频特性呈丘陵状,振动与负荷无关,相频非单调变化六、齿轮故障1.齿轮特征频率计算2.齿轮断齿故障特点:啮合频率GMF或其谐波两侧出现转速的边带簇,时域信号有明显等间隔冲击,设备有冲击异音,时域波形峭度值大。
3.齿轮不对中特点:存在齿轮高次啮合频率谐波,1GMF较小,但2GMF,3GMF振幅较大,GMF的边频距离可为2RPM,甚至为3RPM。
4.齿面磨损特点:信号存在齿轮自振频率,且该频率处存在边带,啮合频率GMF 或其谐波两侧出现转速的边带簇,存在较大的齿轮啮合频率GMF。
七、滚动轴承故障1.轴承特征频率计算4.轴承部件缺陷(内圈,滚动体剥落,滚道剥落等)特点:轴承缺陷频率和谐波成分丰富,时域波形有冲击,存在轴承内圈特征频率(BPFI),存在轴承外圈特征频率(BPFO),边带成分较明显或突出。
3.轴承间隙不当特点:振动分量1X,2X,3X占主导地位,1X~8X谐波成分丰富,轴承温度偏高,存在明显的(0.4~0.9)X范围的频率值。
轴承新近调整安装,存在轴承外圈特征频率(BPFO)。
4.轴承磨损特点:轴承缺陷频率和谐波成分丰富,存在较宽的随机高频振动带,边带成分较明显或突出,轴承温度偏高。
旋转设备振动案例分析

旋转设备振动案例分析一、水流作用引起的振动1、异常情况简介:7号机1号、2号循环泵并列运行时,2号循环泵电机上机架振动变化不大,1号循环泵电机上机架水平振动最高达到0.17mm;站在电机上机架的平台上有很强的晃动感,1号循环泵电机电流为185A, 2号循环泵电流为225A;两台泵的出口压力均为0.22MPa。
1号循环泵单独运行时的参数:电流225~227A,出口压力0.155MPa(2号泵单独运行出口压力也为0.155MPa),电机上机架水平振动最大0.04mm。
2、振动分析:当1号循环泵单独运行时,电机电流,电机上机架振动,泵出口压力均处于正常状态。
当与2号泵并列运行时,此时1号泵性能不如2号泵性能好,2号泵的出口水压对1号泵产生影响,即水力冲击或1号泵入口产生涡流现象,1号泵的流量大幅度降低,出现1号泵在并列运行时电机上机架水平振动大和电机电流低的现象。
分析原因为1号循环泵的泵体密封环与叶轮密封环由于磨损间隙过大,泵的轴套与导向橡胶轴承间隙由于磨损超标。
3、结论:3个月后利用机组小修的机会对7号机1号循环泵解体检查,橡胶轴承磨损严重与轴套的总间隙达2.5毫米,叶轮密封环间隙达7毫米。
导叶室内积聚有许多细砂。
二、由于处理缺陷工艺程序不正确引起的振动1、详细经过2012年8月30日9时20分,1号机汽泵转速5140r/min,机组负荷280MW,点检员现场点检发现汽泵振动增大,振动产生的声音也很大,用听针进行听诊,驱动端声音比非驱动端声音偏大,由于振动太大,没有听到有摩擦的声音,用点检仪测定振动主要以工频振动为主。
点检员申请降低汽泵转速运行观察,晚上低负荷时停汽泵检查,当转速降低时,振动的振幅值也在下降。
8月31日4时50分停泵检查,解体联轴器罩发现联轴器膜片出现多处对称裂纹,此时由于电泵偶合器润滑油滤网堵塞,润滑油压不断降低,偶合器轴瓦温度在不断上升,切换滤网操作有断油危险,为了防止发生引起停机事故,因此没有进一步检查,更换联轴器膜片后恢复运行。
旋转机械常见振动故障及原因分析
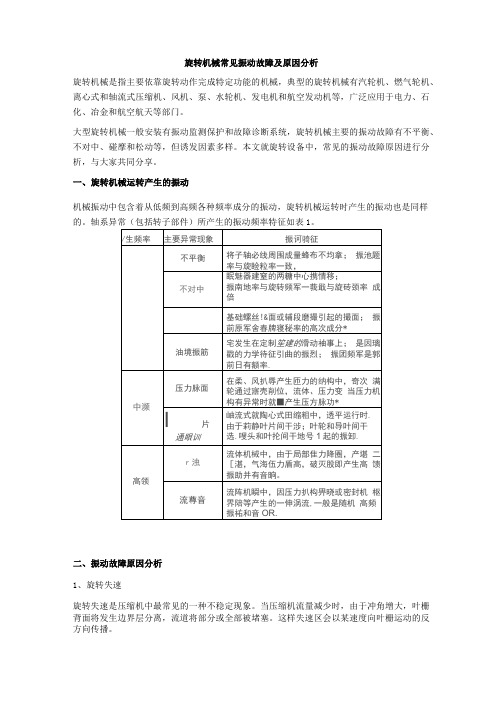
旋转机械常见振动故障及原因分析旋转机械是指主要依靠旋转动作完成特定功能的机械,典型的旋转机械有汽轮机、燃气轮机、离心式和轴流式压缩机、风机、泵、水轮机、发电机和航空发动机等,广泛应用于电力、石化、冶金和航空航天等部门。
大型旋转机械一般安装有振动监测保护和故障诊断系统,旋转机械主要的振动故障有不平衡、不对中、碰摩和松动等,但诱发因素多样。
本文就旋转设备中,常见的振动故障原因进行分析,与大家共同分享。
一、旋转机械运转产生的振动机械振动中包含着从低频到高频各种频率成分的振动,旋转机械运转时产生的振动也是同样的。
轴系异常(包括转子部件)所产生的振动频率特征如表1。
二、振动故障原因分析1、旋转失速旋转失速是压缩机中最常见的一种不稳定现象。
当压缩机流量减少时,由于冲角增大,叶栅背面将发生边界层分离,流道将部分或全部被堵塞。
这样失速区会以某速度向叶栅运动的反方向传播。
实验表明,失速区的相对速度低于叶栅转动的绝对速度,失速区沿转子的转动方向以低于工频的速度移动,这种相对叶栅的旋转运动即为旋转失速。
旋转失速使压缩机中的流动情况恶化,压比下降,流量及压力随时间波动。
在一定转速下,当入口流量减少到某一值时,机组会产生强烈的旋转失速。
强烈的旋转失速会进一步引起整个压缩机组系统产生危险性更大的不稳定气动现象,即喘振。
此外,旋转失速时压缩机叶片受到一种周期性的激振力,如旋转失速的频率与叶片的固有频率相吻合,将会引起强烈振动,使叶片疲劳损坏造成事故。
旋转失速故障的识别特征:1)振动发生在流量减小时,且随着流量的减小而增大;2)振动频率与工频之比为小于1X的常值;3)转子的轴向振动对转速和流量十分敏感;4)排气压力有波动现象;5)流量指示有波动现象;6)机组的压比有所下降,严重时压比可能会突降;7)分子量较大或压缩比较高的机组比较容易发生。
2、喘振旋转失速严重时可以导致喘振。
喘振除了与压缩机内部的气体流动情况有关,还同与之相连的管道网络系统的工作特性有密切的联系。
转动设备常见振动故障频谱特征与案例分析
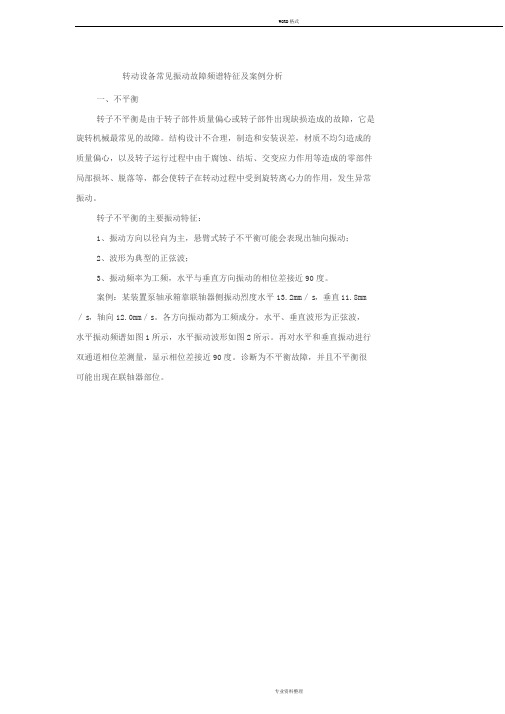
转动设备常见振动故障频谱特征及案例分析一、不平衡转子不平衡是由于转子部件质量偏心或转子部件出现缺损造成的故障,它是旋转机械最常见的故障。
结构设计不合理,制造和安装误差,材质不均匀造成的质量偏心,以及转子运行过程中由于腐蚀、结垢、交变应力作用等造成的零部件局部损坏、脱落等,都会使转子在转动过程中受到旋转离心力的作用,发生异常振动。
转子不平衡的主要振动特征:1、振动方向以径向为主,悬臂式转子不平衡可能会表现出轴向振动;2、波形为典型的正弦波;3、振动频率为工频,水平与垂直方向振动的相位差接近90度。
案例:某装置泵轴承箱靠联轴器侧振动烈度水平13.2mm/s,垂直11.8mm /s,轴向12.0mm/s。
各方向振动都为工频成分,水平、垂直波形为正弦波,水平振动频谱如图1所示,水平振动波形如图2所示。
再对水平和垂直振动进行双通道相位差测量,显示相位差接近90度。
诊断为不平衡故障,并且不平衡很可能出现在联轴器部位。
解体检查未见零部件的明显磨损,但联轴器经检测存在质量偏心,动平衡操作时对联轴器相应部位进行打磨校正后振动降至2.4mm/s。
二、不对中转子不对中包括轴系不对中和轴承不对中两种情况。
轴系不对中是指转子联接后各转子的轴线不在同一条直线上。
轴承不对中是指轴颈在轴承中偏斜,轴颈与轴承孔轴线相互不平行。
通常所讲不对中多指轴系不对中。
不对中的振动特征:1、最大振动往往在不对中联轴器两侧的轴承上,振动值随负荷的增大而增高;2、平行不对中主要引起径向振动,振动频率为2倍工频,同时也存在工频和多倍频,但以工频和2倍工频为主;3、平行不对中在联轴节两端径向振动的相位差接近180度;4、角度不对中时,轴向振动较大,振动频率为工频,联轴器两端轴向振动相位差接近180度。
案例:某卧式高速泵振动达16.0mm/s,由振动频谱图(图3)可以看出,50 Hz(电机工频)及其2倍频幅值显著,且2倍频振幅明显高于工频,初步判定为不对中故障。
振动讲义故障实例分析
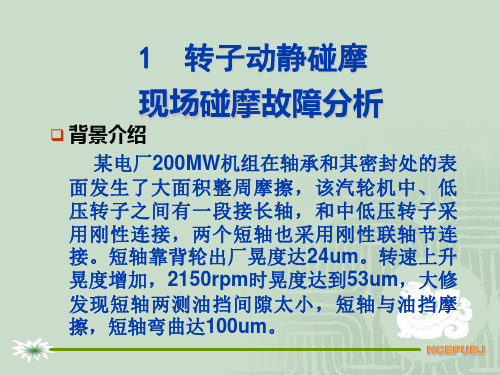
碰摩故障分析
动静碰摩相对改变了轴系的支承刚度,动静部件存 在相互作用,摩擦脱离相互作用消失。碰摩瞬间增大了 转子的支承刚度,脱离时刚度减小,转子刚度在接触与 非接触两者之间变化,变化的频率就是转子的涡动频率。 转子横向自由振动与强迫旋转振动、涡动叠加产生复杂 振动使摩擦振动具有典型的非线性特征。碰摩特征既有 低频成份,也包含2x,3x等高次谐波分量及分数谐波振 动。转子在超过临界转速时,如果发生整周连续接触摩 擦,将会产生一个很强的摩擦切向力,可引起转子的完 全失稳,这时转子的振动响应中具有振幅很大的次谐波 成份。除此之外,还出现基频与谐波频率之间的和差频 率,这些取决于转子自身的固有频率。若转子进动方向 由正向涡动变为向涡动,则表明转子发生了连续接触摩 擦。
0.8
0.4
0.5x 1.5x
0 0
0.9
2x 3x
200
400
Frequency (Hz)
Speed=3518rpm
0.6
600
Amplitude (um)
3.2
1x
Speed=3480rpm
2.4
1.6
0.8
0.5x
0 0
1.5x 2x
200
400
Frequency (Hz)
600
0.3
分别从3个测点采集的频谱图
Amplitude (um)
0
0
200
400
600
Frequency (Hz)
实验现象分析:
在轴刚开始发生摩擦接触的情况下,由于转子的不平衡 或转子的弯曲,振动仍以基频为主,其它(2x,3x)分 量一般并不大,基频幅值高于2x,3x分量;
随着摩擦的扩展,基频幅值有所下降。转速在3800rpm 时加重摩擦力,时域波形出现单边“削波”。并有可能 出现1/2x和3/2x谐波,以及明显的6x,7x和8x非线性分 量;
旋转机械振动及频谱分析

监测和诊断的各种手段
★ 振动:适用于旋转机械、往复机械、轴承、齿轮等。
★ 温度(红外):适用于工业炉窑、热力机械、电机、电器等。 ★ 声发射:适用于压力容器、往复机械、轴承、齿轮等。 ★ 油液(铁谱) :适用于齿轮箱、设备润滑系统、电力变压器等。 ★ 无损检测:采用物理化学方法,用于关键零部件的故障检测。 ★ 压力:适用于液压系统、流体机械、内燃机和液力耦合器等。 ★ 强度:适用于工程结构、起重机械、锻压机械等。 ★ 表面:适用于设备关键零部件表面检查和管道内孔检查等。 ★ 工况参数:适用于流程工业和生产线上的主要设备等。 ★ 电气:适用于电机、电器、输变电设备、电工仪表等。
什么是振动?
什么是振动频率?
考察上图可见,在记录纸上画出的振动轨迹是一条有一定幅值的、 比较标准的正弦曲线。由振动的周期(T)可以计算出振动的频率。如 下图所示:频率的单位是用CPM或用Hz表示(1Hz=60 CPM)。
图6 振动波形的位移和频率
什么是振动相位?
振动相位是一个振动部件相对于机器的另一个振动部件在某一固定 参考点处的相对移动。也就是说振动相位是某一位置处的振动运动相对 于另一位置处的振动运动,对所发生位置变化程度的度量。振动相位是 一个很有用的设备故障诊断工具。如下图所示,给出了两个彼此同相位 振动的系统,即两个振动系统以零度相位差运动。
图10两个相差90度相位角振动 的质量块系统
图11 两个相差180度相位角振动 的质量块系统
什么是振动相位?
振动相位是以角度为单位,通常是利用频闪灯或光电头测量得到。 下图给出了,振动相位与机器振动间的关系。
在左侧图中,机器上的轴承1和轴承2之间的振动相位差为0度(同 相振动),而在右侧图中的机器,轴承1和轴承2之间的振动相位差为 180度(反相振动)。
电厂转动设备振动讲解与案例分析 ppt课件
按振动频率分类 按照振动频率的高低,通常把振动分为三类 低频振动: f <10Hz 中频振动: f =10~1000Hz 高频振动: f >1000Hz
20
PPT课件
常见振动的故障分析
1.各种不同类型的故障所引起的振动都有各自的特征频率。 转子不平衡的振动频率是工频 齿式联轴器(带中间齿套)不对中的振动频率是二倍频 油膜涡动的振动频率是0.5倍频(实际上要小一点) 2.由各频率成分的幅值大小和分布情况,从中查找出发生了异常变化的频率,
3
PPT课件
专业术语解释
振幅:振幅是物体动态运动或振动的幅度。 振幅是振动强度和能量水平的标志,是评判机器运转状态优劣的主要指标 峰峰值、单峰值、有效值 1. 振幅的量值可以表示为峰峰值(pp)、单峰值(p)、有效值(rms)或平均值
(ap)。 2. 峰峰值是整个振动历程的最大值,即正峰与负峰之间的差值; 3. 单峰值是正峰或负峰的最大值;有效值即均方根值。 只有在纯正弦波(如简谐振
态; 当支座的固有频率小于转子轴承系统的固有频率时,为挠性支承状
态
12
PPT课件
专业术语解释
13
PPT课件
振动测量方法
ISO32373和DIN45665 电动机振动标准
1.电动机按其中心高度(H)分为三个类型,中心高度越大,振动阈值越大 2.电动机状态判别分为三个等级:正常、良好、特佳。 3.本标准是指电动机在空转(不带负荷)条件下的阈值。 4.诊断参数为速度有效值(Vrms)。
6
PPT课件
专业术语解释
倍频、一倍频、二倍频、0.5倍频、工频、基频、 转频
倍频就是用转速频率的倍数来表示的振动频率。 一倍频,即实际运行转速频率又称为工频、基频、
转动设备振动频谱分析案例
蚀性气体或液体需要做好防护措施。
同时,由于控制系统含有精密仪器,安装前,还需要对这些仪器仪表进行质量检验和精度校准,保证计量时的准确度,并加装必需的保护装置,保障人身和设备安全,保障电气设备可靠运行。
安装完成后,需要对设备进行合理地维护,针对设备缺陷有有效的应对方案,同时保证设备检修的及时性和效率,提高电力系统的可靠性和稳定性。
参考文献[1]齐书可.电气设备自动化控制中PLC技术的应用研究[J].科技经济市场,2019(1):4-5.[2]李建奇.电气设备自动控制系统中的PLC技术运用[J].无线互联科技,2018,15(24):131-132,135.[3]徐小燕.电气设备的自动控制设计[J].科技资讯,2018,16(33):57-58.[4]董敏.电气设备安装及调试过程中质量控制措施[J].低碳世界,2018(11):38-39.[5]王辉.关于电气调试中电子电路的干扰问题分析[J].计算机产品与流通,2018(9):73.[6]王维平.变电站的电气设备安装和调试经验谈[J].智能城市,2018,4(17):149-150.〔编辑叶允菁〕转动设备振动频谱分析案例韩国良(大庆炼化公司电仪运行中心,黑龙江大庆163000)摘要:旋转机械广泛应用振动信号进行诊断的方法不仅简便可行,而且经过不断实践、研究,积累的经验和技术已经比较成熟。
当一台设备发生振动故障时,为了准确快速地寻找故障原因,解决振动问题,就需要采集振动信号,运用频谱分析方法来进行分析。
本文通过一些实际案例来说明如何进行振动频率分析、故障诊断、处理。
关键词:频谱;不平衡;不对中;基础刚性不足中图分类号:TQ053文献标识码:B DOI:10.16621/ki.issn1001-0599.2019.07D.1350引言在化工生产中由机械振动引起的设备损坏率很高,设备损坏的严重程度又与振动的大小有直接关系。
而振动信号中又包含着丰富的设备状态信息,通过振动采集设备可以采集到设备振动的时域波形,再通过傅里叶变换转换成频域谱图,通过频域谱图就可以发现一些设备运行的特征频率,不同的特征频率往往对应着一定的故障类别。
电厂转动设备振动讲解与案例分析
案例四:风机设备振动故障诊断与处理
总结词
风机设备振动故障通常与叶片质量不平衡、机械结构松动、气流冲击等因素有关,需要进行全面的诊断和处理。
详细描述
风机设备振动故障表现为轴承座松动、叶片振动、机体共振等。诊断过程中,需要利用振动监测、气动测试、机 械分析等技术手段,确定故障原因和位置。处理方法包括修复叶片、紧固机械结构、调整气流方向等,同时需要 加强设备的日常维护和保养,以提高设备的稳定性和可靠性。
和位置。
趋势分析法
将设备在不同时间段的振动数据进行对比 和分析,找出振动的变化趋势,预测故障
的发展趋势。
波形分析法
根据振动信号的波形变化,结合设备的运 行参数和工艺流程,判断出故障的原因和 部位。
故障诊断专家系统
利用计算机技术和人工智能技术,建立故 障诊断专家系统,通过知识库和推理机对 设备振动信号进行智能分析和诊断。
电厂转动设备振动讲解与案例分 析
目录
• 电厂转动设备振动概述 • 电厂转动设备振动检测与分析 • 电厂转动设备振动故障诊断与处电厂转动设备振动概述
定义与分类
定义
电厂转动设备振动是指设备在运行过 程中,由于各种原因引起的设备部件 的周期性运动或非周期性运动,导致 设备产生一定幅度的振动。
转子在制造、运输或安装过程中受到外力 作用导致转子弯曲,在旋转时产生振动。
轴承故障
联轴器不对中
轴承损坏、轴承间隙过大或过小、轴承润 滑不良等都会引起设备振动。
联轴器连接的两轴中心线不重合或不在同 一直线上,导致设备在运转时产生振动。
振动故障诊断方法
频谱分析法
通过对设备振动信号进行频谱分析,确定 振动的频率成分,从而判断出故障的类型
THANK YOU
旋转机械的共振与油膜振荡,附案例说明
共振有的旋转机械在启动升速过程中,当达到某个(或某些)转速时,有时会出现振动急剧增大的现象。
有的机器甚至在工作转速下也会产生比较剧烈的振动。
这有可能是转子处在临界转速下运行而发生共振所致。
机器设备上的每个零部件都有自己的“固有频率”(又称自振频率)。
当机器的转速等于固有频率时,就发生共振。
所以,当机器在某一转速下振动增大时,就要识别是否存在共振。
若属共振,只要改变转速(增大或减小),振幅就会下降。
所以通过三维功率谱分析很容易确诊。
另外,在设备运行时,由于工作系统内存在有与转速同步的激励源,就会产生类似于共振的“拍振”。
比如有台大型水泵的排出管段上截面突然改变而形成流体脉动,其频率与转速十分接近,那么就会产生类似共振的强烈振动。
不过这种现象不会长存,而是处在不断的变化之中。
还有,故障信号的谐波有时也是产生共振的一个因素,即“谐波共振”。
谐波一旦消失(比如故障消除后),谐波共振也就不存在了。
油膜振荡有些高性能机械,如蒸汽涡轮机、汽轮发电机、离心压缩机、高速离心泵等,它们的转子系统多属于高速轻载。
由于设计或使用方面的原因,轴承容易发生油膜不稳定性,在某种工作状态下,有可能发生高速滑动轴承特有的故障——油膜振荡。
为了诊断油膜振荡故障,需要了解油膜振荡产生的条件、故障特征及处理方法。
1)产生条件a)油膜振荡发生在高速运行的设备上,通常转速频率大于转子一阶临界转速2倍以上;b)只出现在使用压力油润滑的滑动轴承上。
2)初始现象滑动轴承发生的油膜振荡,是轴颈的涡动运动与转子自振频率相吻合时发生的大幅度共振运动。
往往来势很猛,瞬间振幅突然升高,很快发生油膜破裂,引起轴颈和轴瓦间互相摩擦,并发生强烈的吼叫声。
如果处理不及时,会严重损坏轴承和转子。
3)频率特征油膜振荡最重要的标志是它发生时的振动频率(Hz)接近转频的一半,即:f=(0.43~0.48)fr某石油化工厂有一台离心式冷冻压缩机,自更换轴承架和主轴瓦以后,曾试车38次,均由于机器出现强烈振动和吼叫声而告失败。
- 1、下载文档前请自行甄别文档内容的完整性,平台不提供额外的编辑、内容补充、找答案等附加服务。
- 2、"仅部分预览"的文档,不可在线预览部分如存在完整性等问题,可反馈申请退款(可完整预览的文档不适用该条件!)。
- 3、如文档侵犯您的权益,请联系客服反馈,我们会尽快为您处理(人工客服工作时间:9:00-18:30)。
转动设备常见振动故障频谱特征及案例分析
一、不平衡
转子不平衡是由于转子部件质量偏心或转子部件出现缺损造成的故障,它是旋转机械最常见的故障。
结构设计不合理,制造和安装误差,材质不均匀造成的质量偏心,以及转子运行过程中由于腐蚀、结垢、交变应力作用等造成的零部件局部损坏、脱落等,都会使转子在转动过程中受到旋转离心力的作用,发生异常振动。
转子不平衡的主要振动特征:
1、振动方向以径向为主,悬臂式转子不平衡可能会表现出轴向振动;
2、波形为典型的正弦波;
3、振动频率为工频,水平与垂直方向振动的相位差接近90度。
案例:某装置泵轴承箱靠联轴器侧振动烈度水平13.2 mm/s,垂直11.8mm /s,轴向12.0 mm/s。
各方向振动都为工频成分,水平、垂直波形为正弦波,水平振动频谱如图1所示,水平振动波形如图2所示。
再对水平和垂直振动进行双通道相位差测量,显示相位差接近90度。
诊断为不平衡故障,并且不平衡很可能出现在联轴器部位。
解体检查未见零部件的明显磨损,但联轴器经检测存在质量偏心,动平衡操作时对联轴器相应部位进行打磨校正后振动降至2.4 mm/s。
二、不对中
转子不对中包括轴系不对中和轴承不对中两种情况。
轴系不对中是指转子联接后各转子的轴线不在同一条直线上。
轴承不对中是指轴颈在轴承中偏斜,轴颈与轴承孔轴线相互不平行。
通常所讲不对中多指轴系不对中。
不对中的振动特征:
1、最大振动往往在不对中联轴器两侧的轴承上,振动值随负荷的增大而增高;
2、平行不对中主要引起径向振动,振动频率为2倍工频,同时也存在工频和多倍频,但以工频和2倍工频为主;
3、平行不对中在联轴节两端径向振动的相位差接近180度;
4、角度不对中时,轴向振动较大,振动频率为工频,联轴器两端轴向振动相位差接近180度。
案例:某卧式高速泵振动达16.0 mm/s,由振动频谱图(图3)可以看出,50 Hz(电机工频)及其2倍频幅值显著,且2倍频振幅明显高于工频,初步判定为不对中故障。
再测量泵轴承箱与电机轴承座对应部位的相位差,发现接近180度。
解体检查发现联轴器有2根联接螺栓断裂,高速轴上部径向轴瓦有金属脱落现象,轴瓦间隙偏大;高速轴止推面磨损,推力瓦及惰性轴轴瓦的间隙偏大。
检修更换高速轴轴瓦、惰性轴轴瓦及联轴器联接螺栓后,振动降到A区。
三、松动
机械存在松动时,极小的不平衡或不对中都会导致很大的振动。
通常有三种类型的机械松动,第一种类型的松动是指机器的底座、台板和基础存在结构松动,或水泥灌浆不实以及结构或基础的变形,此类松动表现出的振动频谱主要为1x。
第二种类型的松动主要是由于机器底座固定螺栓的松动或轴承座出现裂纹引起,其振动频谱除1X外,还存在相当大的2X分量,有时还激发出1/2X和3X振动
分量。
第三种类型的松动是由于部件间不合适的配合引起的,产生许多振动谐波分量,如1X、2X、⋯⋯,nX,有时也会产生1/2X、1/3X、⋯⋯等分数谐波分量。
这时的松动通常是轴承盖里轴瓦的松动、过大的轴承间隙、或者转轴上零部件存在松动。
案例:某引风机振动增大,轴承箱最大振动16.9 mm/s。
该机为悬臂式离心式风机,最大振动在轴承箱靠叶轮侧,倍频丰富,初步判断存在松动。
监测4个地脚,发现其中一个地脚03(靠叶轮侧)振动较大,约9 mm/s,其余三个地脚振动分别为0.5 mm/s、1.8 mm/s和2.0 mm/s,很明显03地脚有松动。
由引风机地脚03垂直振动频谱(图4)可以看出,1X、2X较大,还有较多的谐波成分。
紧固地脚螺栓后轴承箱最大振动降至4.2 mm/s,仍偏大,分析应该还存在轴承或轴上零件配合松动。
2012年8月解体检查引风机,发现轴承与压盖紧力不足,加铜垫片调整压盖紧力后振动降到2.7 mm/s。
案例:某双支撑离心式风机非联轴器端轴承箱振动大幅上升,最大振动轴向方向为14.8mm/s。
现场监测记录列于表1。
水平、垂直、轴向振动均表现出2倍工频显著,且垂直、轴向2倍工频幅值大于工频成分。
风机轴向振动频谱如图5所示。
因轴支承为滑动轴承,据相关振动分析理论,轴瓦松动将使转子产生很大的振动,振动频率一般为1/2或2倍转速频率,初步分析可能存在轴承压盖紧力不足,建议先检查轴承压盖紧力。
检查验证确实存在压盖紧力不足,调整后振动降至B区。
四、流体扰动
高速离心泵中的流体,从叶轮的流道中流出,进入扩压器或蜗壳时,如果流体的流动方向与叶片角度不一致,流道中就产生很大的边界层分离、混流和逆向流动,流体对扩压器叶片和蜗壳隔舌的冲击,将使流体在管道中引起很大的压力脉动和不稳定流动,这种压力波又可能反射到叶轮上,激发转子振动,振动频率为叶轮叶片数乘以转速(称叶片过流频率)或其倍数。
在工艺流量与泵额定流量偏差较大或叶轮出口与蜗壳对正不良时,过流频率振动明显,称流体扰动。
一般把叶轮外缘和开始卷曲处的距离拉大,能够缓和压力脉动并减小振幅。
案例:某泵振动超标,管线振动也大。
监测发现前轴承最大振动19.4 mm/s,4倍工频振幅最大,此成分系泵过流频率,泵振动频谱如图6所示。
经过核算,该泵选型过大,解体切削叶轮后,振动降到标准之内。
五、动静碰摩
在旋转机械中,由于轴弯曲、转子不对中等引起轴心严重变形,或非旋转件弯曲变形,都可能引起转子与固定件的碰摩而引起异常振动。
动静碰摩的振动特征:频谱图上以工频分量为主,存在少量低频或倍频,碰摩严重时,低频和倍频分量都有较明显的反映。
波形图上可出现单边削顶现象或在接近最大振幅处出现锯齿形。
案例:监测发现进料泵振动偏大,监测数据列于表2。
前轴承水平振动波形如图7所示,垂直方向振动波形如图8所示。
该泵各测点振动值与该泵历史良好状况(2 mm/S以内)相比增加较大,倍频成分丰富,且波形图较多波折,尤其是垂直方向存在单边锯齿状,分析存在松动和轻微碰摩。
对该泵跟踪监测,振动值较稳定,运行到2012年4月焦化装置停工检修时,对该泵解体大修,发现后轴瓦巴氏合金层磨损严重,泵轴在喉部衬套部位有磨损痕迹,检修后振动降到1.7 mm/S。
六、滚动轴承故障
有关振动分析理论,出现滚动轴承损伤或磨损时,高频解调值一般会增大,并且往往可见轴承外圈、内圈等部件的故障特征频率。
当轴承磨损到后期时,轴承故障特征频率可能消失,但振动值通常会加大,振动频谱图变成一系列谱线。
案例:气分装置泵振动达18.2 mm/s,由前轴承水平振动频谱图图9可以看出,除工频外,存在密集的高频成分。
由前轴承水平解调谱图(图10)可以看出,突出的频谱成分只有工频,但谱线底线较高。
分析该泵轴承磨损严重,已发展到轴承故障特征频率消失。
解体检修发现靠联轴器侧的轴承保持架已断裂,更换轴承后振动降到B区。
案例:引风机振动增大,最大振动8.1 mm/s。
由引风机前轴承振动频谱图(图11)可以看出,高频成分振幅显著。
由引风机前轴承解调谱图(图12)可以看出,约5.8倍转速频率幅值突出,该成分与该机轴承22316外圈故障特征频率接近,诊断为轴承磨损。
解体验证轴承的确存在磨损,更换轴承后最大振动1 mm/s,解调值最大0.8 g。