轧钢常见缺陷
冷轧带钢边鼓缺陷产生原因与控制措施

冷轧带钢边鼓缺陷产生原因与控制措施全文共四篇示例,供读者参考第一篇示例:冷轧带钢是一种重要的金属材料,广泛应用于建筑、汽车、机械制造等领域。
在生产过程中,冷轧带钢常常会出现边鼓缺陷,影响产品质量。
本文将从冷轧带钢边鼓缺陷的产生原因和控制措施两方面进行探讨。
一、冷轧带钢边鼓缺陷产生原因:1. 轧辊质量不良:轧辊表面粗糙度大、硬度不足或不均匀,会导致轧件表面质量不良,进而引起边鼓缺陷的产生。
2. 轧辊边缘磨损严重:轧辊边缘磨损加剧,造成轧件边部挤压不平整,易产生边鼓缺陷。
3. 轧件冷却不均匀:冷却水量不足或水压不稳定会导致轧件温度分布不均匀,使得边部冷却速度不一致,进而引发边鼓缺陷。
4. 锯切不准确:如果在冷轧带钢的切割过程中,锯切位置不准确或锯切刀具损坏,容易导致边部挤压变形,产生边鼓缺陷。
5. 压下力控制不好:在轧制过程中,如果压下力控制不好,会造成轧辊与轧件之间的挤压不均匀,容易形成边鼓缺陷。
1. 提高轧辊质量:选用优质的轧辊材料,确保轧辊表面光滑、硬度均匀,减少轧辊对轧件表面的损伤。
2. 加强轧辊维护:定期检查轧辊边缘磨损情况,及时更换或修复磨损严重的轧辊,确保轧辊边缘的平整度。
3. 控制冷却工艺:合理设置冷却水量和水压,确保轧件冷却均匀,避免轧件边部出现温差过大的情况。
4. 加强锯切管理:对切割设备进行定期维护保养,确保切割精度和品质,避免因切割不准确导致的边鼓缺陷。
冷轧带钢边鼓缺陷的产生原因复杂多样,需要生产企业在生产过程中严格控制各项工艺参数,加强设备维护保养,提高操作技术水平,才能有效避免边鼓缺陷的产生,确保产品质量。
希望通过本文的介绍,能够对冷轧带钢生产企业提供一定的参考和帮助。
【以上内容仅供参考】。
第二篇示例:冷轧带钢是一种重要的金属材料,广泛应用于各种领域。
但是在生产过程中,冷轧带钢边鼓缺陷是经常出现的一种质量问题,给生产造成了一定的影响。
本文将从边鼓缺陷的产生原因和相应的控制措施进行探讨,希望对相关行业提供一些参考。
热轧带钢边部翘皮缺陷产生原因及判定研究

热轧带钢边部翘皮缺陷产生原因及判定研究摘要:采用光学显微镜和SEM扫描电镜对热轧低碳钢边部的变形皮进行分析,研究发现,该产品的边沿弯曲缺陷主要表现为:其宏观形貌为舌条,距舌条边缘20-50 mm。
将变形的表皮缺陷试样与轧制方向垂直,用光学显微镜对其进行了剖面观察。
变形皮肤根连接于基质,其变形的表皮组织较正常部位较粗。
而MnO则存在于经改变的皮肤组织中,利用扫描电镜观察。
同时,在轧制过程中出现了分层、弯曲等现象,从而产生了形变的表皮缺陷。
普通低碳钢的边沿弯曲现象主要有两种:一是连铸时的板坯自身的缺陷,二是在热轧时的轧制。
通过对翘曲结皮与正常翘曲的组织形态的差别、有没有明显的粗坯、脱碳层等进行对比,从而判定和分析热轧翘曲的形成过程和成因。
关键词:热轧带钢;边部翘皮;产生原因;判定研究引言热轧和冷轧钢板的表面缺陷是造成板材质量问题的一个重要原因。
由于存在上述缺点,导致了连铸板坯的不合格。
从上世纪90年代以来,尤其是最近几年,连铸坯、连轧、“翘曲”等问题呈逐年上升趋势,造成了较大的经济损失。
表面缺陷对钢板的性能有很大的影响。
常见的表面缺陷有翘曲,裂纹和断裂。
热轧板条的边沿剥离是导致热轧板坯表面质量下降的主要原因之一。
由于带材的边角剥落,使下一工序的边角数量增大,影响板坯的成材率,从而使板坯的成材率下降。
一、边部翘皮的特征(一)边部翘皮宏观形貌边部翘皮的宏观形貌如图1所示,卷曲的边缘距带钢20 mm,不连续地分布于带钢的上部。
当出现较大的缺陷时,可以在热轧表面检测装置中检测到;若有少量的锈蚀,则需要通过酸洗来除去氧化铁。
图1 翘皮缺陷形貌特征(二)边部翘皮微观特征首先,从脱碳层的角度来看,该钢材为低碳钢,因此不存在明显的脱碳现象。
将缺陷区的金相显微结构放大500倍,发现其正常组织为等轴铁素体,而变形区为粗大的铁素体,且晶界不清。
由于变形表皮的厚度较薄,大约在15-20微米之间,组织中有黑色斑点,而大的铁素体晶粒比正常的基体大,表明变形表皮部位的温度升高。
轧钢质量缺陷、产生原因心得

轧钢质量缺陷、产生原因心得
轧钢产生质量缺陷这一问题,我对此有所体会。
我认为轧钢质量缺陷产生的原因主要是:
1.板坯加热制度不合理或加热操作不当生成较厚且较致密的铁皮,除鳞时难以除尽,轧制时被压入钢板表面上。
2.由于高压除鳞水压力低、水咀堵塞、水咀角度安装不合理或操作不当等原因,使钢坯上的铁皮未除尽,轧制时被压入到钢板表面上。
3.氧发生较多,含硅化铁皮在沸腾钢中较高的钢中易产生红铁皮。
4.轧辊表面粗糙。
5.辊形曲线不合理,轧辊磨损不均匀。
6.压下量分配不合理。
7.轧辊辊缝调整不良或轧件跑偏。
8.轧辊冷却不均。
9.轧件温度不均。
10.卷取机前的侧导板开口度过小等。
11.板坯上原有的裂缝、针状气孔等缺陷未清理干净,轧制后残
留在轧件表面上。
12.含铜钢因加热温度控制不当,易产生网裂。
13.因轧辊受热不均、冷却不当及疲劳破坏等,造成轧辊产生裂纹,轧制后在轧件表面上呈凸起的龟纹。
对于轧钢质量问题我总结出以上可能造成的原因,我相信,只要合理规避这些问题,就能很好地解决轧钢质量缺陷的问题。
轧钢常见缺陷

(4)成品入口夹板间隙过大或松动,进钢不稳,易产生双面断续耳子。
扭转
型钢绕其轴线扭成螺旋状称为扭转
(1)卫板安装不良,使轧件出孔时受到力偶的作用产生扭转。
(2)两侧延伸不一致,主要是压下不均或辊子有轴向串动。
(3)方、圆钢由于入口夹板安装不正确,使钢料进孔不正,造成延伸不一致。
(1)钢坯带来的表面非金属夹杂物。
(2)在加热或轧制过程中,偶然有非金属夹杂物(如加热炉的耐火材料及炉渣等),附在钢坯表面上,轧制时被压入钢材,冷却经矫直后部分脱落。
分层
此缺陷在型钢的锯切断面上呈黑线或黑带状,严重的分离成两层或多层,分层处伴随有夹杂物。?
(1)主要是由于镇静钢的缩孔或沸腾钢的气囊未切净。
(1)头太、头小产生的主要原因是轧制温度和轴瓦的磨损及轧机部件的松动等造成。
2)腰厚、腰薄产生的主要原因是:如按孔型设计头部压下量为77—70.3=6.7mm;腰部压下量为16一14.5=1.5mm,如果六孔压下量加大l.5mm,则头部尺寸为75.5mm压下量由6.7mm减少到5.2mm,腰部压下量由1.5mm减少到0,自然头部对腰部有拉伸加之腰部无压下而宽展,所以腰变薄,反之腰部变厚。
(4)孔型磨损严重,也能产生表面轧痕。
折叠
沿钢轨的轧制方向出现的长条形金属重叠缺陷叫折叠。折叠呈直线状,也有呈锯齿状。多出现在钢轨头部、底部边沿等处,沿钢轨全长或局部分布。
(1)主要是由于成品孔前某一道次出现耳子,再轧后形成折叠。
(2)由于轧辊车削不良,锁口过宽。
(3)帽形孔压下量过大,底部宽度过大,进轨形切深孔形成耳子,再轧时形成折叠。
由于钢坯未清理,钢坯原有的结疤经热轧变形后残留在钢勒表面上。
钢板常见质量缺陷及原因分析

钢板常见质量缺陷及原因分析一、热轧钢板1辊印:是一组具有周期性、大小形状基本一致的凹凸缺陷,并且外观形状不规则。
原因:1)一方面由于辊子疲劳或硬度不够使辊面一部分掉肉边凹;另一方面可能是辊子表面粘有异物,使表面部分呈凸出状;2)轧钢或精整加工时,压入钢板表面形成凹凸缺陷。
2表面夹杂:在钢板表面有不规则的点状块状或车条状的非金属夹杂物,其颜色一般呈红棕色、黄褐色、灰白色或灰黑色。
原因:1)板坯皮下夹杂轧后暴露,或板坯原有的表面夹杂轧后残留在钢板表面上;2)加热炉耐火材料及泥沙等非金属物落在板坯表面上,轧制时压入板面。
3氧化铁皮:氧化铁皮一般粘附在钢板表面,分布于板面的局部或全部,呈黑色或红棕色;铁皮有的疏松脱落,有的压入板面不易脱落;根据外观形状不同有:红铁皮、块状铁皮、条状铁皮、线状铁皮、木纹状铁皮、流星状铁皮、纺锤状铁皮、拖曳状铁皮和散状铁皮等,其压入深度有深有浅。
原因:1)压入氧化铁皮的生成取决于板坯加热条件,加热时间逾长,加热温度愈高,氧化气氛愈强,生成氧化铁皮就愈多,而且不容易脱落,产生一次铁皮难于除尽,轧制时被压入钢板表面上;2)大立辊设定不合理,铁皮未挤松,难于除掉;3)由于高压除鳞水管的水压低,水咀堵塞,水咀角度不对及使用不当等原因,使钢板表面的铁皮没有除尽,轧制后被压入到钢板表面;4)氧化铁皮在沸腾钢中发生较多,在含硅较高的钢中容易产生红铁皮。
4厚薄不均:钢板各部分厚度不一致称厚薄不均,凡厚度不均匀的钢板,一般为偏差过大,局部钢板厚度超过规定的允许偏差。
原因:1)辊缝的调整和辊型的配置不当;2)轧辊和轧辊两侧的轴瓦磨损不一样;3)板坯加热温度不均。
5麻点:钢板表面呈现有局部或连续的凹坑叫麻点,其大小不同,深度不等。
原因是加热过程中,板坯氧化严重,轧制时铁皮压入表面,脱落后形成细小的凹坑。
6气泡:钢板表面上有无规律分布的圆形凸包,有时呈蚯蚓式的直线状,其外缘比较光滑,内有气体;当气泡轧破后,呈现不规则的细裂纹;某些气泡不凸起,经平整后,表面光亮,剪切断面呈分层状。
所有钢材常见缺陷及原因
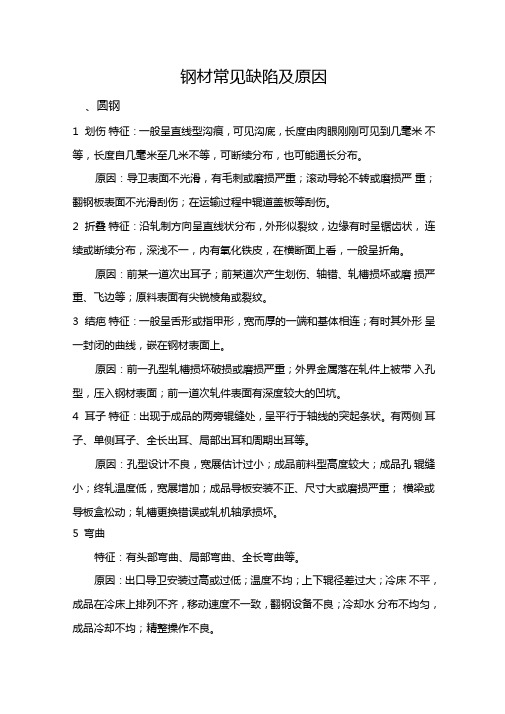
钢材常见缺陷及原因、圆钢1划伤特征:一般呈直线型沟痕,可见沟底,长度由肉眼刚刚可见到几毫米不等,长度自几毫米至几米不等,可断续分布,也可能通长分布。
原因:导卫表面不光滑,有毛刺或磨损严重;滚动导轮不转或磨损严重;翻钢板表面不光滑刮伤;在运输过程中辊道盖板等刮伤。
2折叠特征:沿轧制方向呈直线状分布,外形似裂纹,边缘有时呈锯齿状,连续或断续分布,深浅不一,内有氧化铁皮,在横断面上看,一般呈折角。
原因:前某一道次出耳子;前某道次产生划伤、轴错、轧槽损坏或磨损严重、飞边等;原料表面有尖锐棱角或裂纹。
3结疤特征:一般呈舌形或指甲形,宽而厚的一端和基体相连;有时其外形呈一封闭的曲线,嵌在钢材表面上。
原因:前一孔型轧槽损坏破损或磨损严重;外界金属落在轧件上被带入孔型,压入钢材表面;前一道次轧件表面有深度较大的凹坑。
4耳子特征:出现于成品的两旁辊缝处,呈平行于轴线的突起条状。
有两侧耳子、单侧耳子、全长出耳、局部出耳和周期出耳等。
原因:孔型设计不良,宽展估计过小;成品前料型高度较大;成品孔辊缝小;终轧温度低,宽展增加;成品导板安装不正、尺寸大或磨损严重;横梁或导板盒松动;轧槽更换错误或轧机轴承损坏。
5弯曲特征:有头部弯曲、局部弯曲、全长弯曲等。
原因:出口导卫安装过高或过低;温度不均;上下辊径差过大;冷床不平,成品在冷床上排列不齐,移动速度不一致,翻钢设备不良;冷却水分布不均匀,成品冷却不均;精整操作不良。
6翘皮特征:呈鱼鳞状或分层翘起的薄皮,大部分是生根的,也有不生根的。
原因:导卫装置加工或安装不良,围盘有尖锐棱角,刮伤了轧件表面,再轧后,引起翘皮;输送辊道表面粗糙,刮起伤了轧件表面,再轧后造成翘皮;轧件带有薄耳子;轧槽磨损严重,轧件在孔型内打滑;连铸坯内部有较大的皮下气泡,轧后破裂形成翘皮。
7表面夹杂特征:一般呈点状、条状或块状分布,其颜色有暗红、暗黄、灰白等,机械地粘结在成品表面上,不易剥落,且有一定的深度。
冷轧各种不良分析
因素
发生原因 1. 轧制油的润滑性能不良 2. 轧制油的温度低时 3. 轧制油的喷射量少导致的局部的磨 损 4. W/R 的局部的过热磨损 (1) 乳化液喷嘴的堵塞 (2) 局部的硬度不良
对策
作业者不 熟练及 轧制油
1. 轧制油浓度及温度高时 2. 加大轧制油喷射量(可能时) 3. 保证轧制油温度及润滑性能良好 4. W/R 的局部破裂、 磨损部位的喷嘴确认
轧制油
设备
吹扫 不良
六.辊印(ROLL MARK)
因素 原料 缺陷 发生原因 1. 原材料的不良部分存在结疤等 2. 折边的部位,作业者未确认到时 对策 1. 穿带时确认原材料的不良部位,决定 换辊与否 2. 去除切边不良及折边部位后作业 1. 每次换辊时点检支承辊的表面损伤部 位 2. 确认板面时存在类似辊印时应做纠正 措施 3. 因工作辊的硬度低下发生辊印时确认 其状态后换辊
作业者
十.凹痕(DENT)
因素 发生原因 1. 钢卷鞍座上存在异物 2. 导向辊表面存在异物 3. 钢卷小车鞍座上存在异物 4. 卷取机及卷取部分存在异物 5. 钢卷小车上升时速度太快,对钢卷 形成冲击 对策 1. 最终道次或头部卷取时确认板面后去 除异物 2. 因木制钢卷鞍座的磨损产生时应交换 3. 作业时注意,钢卷小车应缓慢上升
1. 控制轧钢作业量(辊子最少使用限度) 2. 确认板面,严重的应换辊 (在平整时用表面加工来去除) 3. 在上次工作中发生粘辊、勒辊事 故的工作辊应加大磨削量
十五.黑带 (BLACK)
因素 发生原因 1. 轧制油变质 2. 轧制油品质不良 1. 吹扫管道角度不良 2. 压缩空气压力低 3. 支承辊刮水器磨损 对策 1. 确保乳化液管理,按轧制油管理方法 执行 2. 使用清静性轧制油(退火后可完全挥 发) 4. 调整吹扫管道角度至最佳状况 5. 压缩空气压力 >4kg/cm 6. 支承辊刮水器定期检查并更换
钢板常见质量缺陷
钢材销售业务中经常会碰到客户的质量投诉,业务员需要对其进行仔细的了解、分析、判断,并给予正确的反馈,本人根据工作中的经验,对常用的板材会出现的一些质量问题进行了归纳,供有关人员作参考,如有错误的地方请予指正:冷轧钢板1表面夹杂:表面呈现点状、块状或线条状的非金属夹杂物,沿轧制方向间断或连续分布,其颜色为好棕色、深灰色或白色。
严重时,钢板出现孔洞、破裂、断带。
原因:1)炼钢时造渣不良,钢水粘度大,流动性差,渣子不能上浮,钢中非金属夹杂物多;2)铸温低,沸腾不良,夹杂物未上浮;3)连铸时,保护渣带入钢中;4)钢水罐、钢锭模或注管内的非金属材料未清扫干净。
2介在物:缺陷呈点状,一般色泽与钢带不同,多呈白色、灰白色。
长度不是很长,多存在于钢带的头、屋部,程度严重时即形成剥片、孔洞。
分为闭口状和开口状。
原因是由于炼钢时钢水中有夹杂物,或热轧时钢带表面存在刮痕、凿痕等缺陷,经过冷轧时,在钢带表面即形成点状之痕迹。
3轧入污物:缺陷呈块状,一般呈白色,易集中发生在钢带某段长度。
原因是由于外来物(如衬纸、胶粒)被轧入钢带表面,而形成大面积、块状之缺陷。
4气孔和夹层:切断面上呈上下两层裂纹,但无分离。
原因是由于炼钢、热轧时钢带表面残留有气泡。
5结疤:表面出现不规则的“舌状”、“鱼鳞状”或条状翘起的金属起层,有的与钢板本体相连接,有的与钢板本体不相连,前面叫开口结疤,后者叫闭口结疤,闭口结疤在轧制时易脱落,使板面成为凹坑。
原因:1)炼钢方面:锭模内壁清理不净,横壁掉肉,上注时,钢液飞溅,粘于横壁,发生氧化,铸温低,有时中断注流,继续注钢时,形成翻皮;下注时,保护渣加入不当,造成钢液飞溅;2)轧钢方面:板坯表面残留结疤未清除干净,经轧制后留在钢板上。
6氧化铁皮:缺陷呈点状、条状或鱼鳞状的黑色斑点,分布面积大小不等,压入的深浅不一。
这类铁皮在酸洗工序难于洗尽,当铁皮脱落时形成凹坑。
原因:1)板坯加热温度过高,时间过长;炉内呈强氧化气氛,炉生氧化铁皮轧制时压入;2)高压水压力不足,连轧前氧化铁皮未清除干净;3)高压水喷咀堵塞,局部氧化铁皮未清除;4)集鳞管道打开组数不够,除鳞不干净。
轧钢厂质量异议缺陷原因分析与预防措施
连铸坯存在尺寸超差
速度ቤተ መጻሕፍቲ ባይዱ作手、
粗轧操作工等
加强连铸坯和成品检查,加大判二级力度。
起梗
带钢存在局部高点
压下、磨工等
加强CVC轧辊曲线抽查力度,减小F7负荷,保证终轧板形。
拉窄
带钢温度波动导致压下变化大,速度波动引起张力过大。
速度、自动化等
促进经验交流,根据入口温度提前调整辊缝,速度也随之进行相应的调整。
压下操作手、
速度操作手、
加热工等
1.升速轧制,提高加二速度,
2.粗轧板形允许时,放下保温罩,
3.及时投入AGC。
镰刀弯
粗轧中间坯板形不好,横向厚差大。
粗轧操作工等
粗轧及时调整压下,保证头部板形。
超差
厚度超差
1.生产计划少,过渡材比较少,
2.温度波动大,待温时间长。
压下操作手、
加热工等
根据生产计划灵活安排薄、厚、冷、热规格产品入炉,放慢轧钢节奏,减少待温时间。
轧钢厂质量缺陷责任认定细则
缺陷名称
原因分析
责任人
预防措施
波浪
单边浪
1.各机架负荷分配不合理,
2.轧辊曲线精度有误差。
压下操作手、
磨工等
1.根据板形情况随时调整各机架负荷分配,
2.加强检查,保证轧辊曲线精度。
双边浪
中浪
厚度不均
1.出钢速度过快,水梁黑印随不明显,但也存在温度低的情况,
2.精轧速度慢,尾部温降大。
2.根据实际情况对卷曲速度进行调整。
裂边
1.终轧和卷曲温度低,不利于晶粒长大。
2.层流冷却开前端水嘴,晶粒长大时间短。
速度、压下、卷取操作工等
钢铁材料常见缺陷及其产生原因
钢铁材料常见缺陷及其产生原因引言钢铁材料是工业生产中常用的材料之一,具有良好的力学性能和耐久性。
然而,由于制造过程中的各种因素,钢铁材料往往会出现一些缺陷。
本文将介绍钢铁材料常见的缺陷,探讨其产生的原因,并提出相应的解决方案。
一、气孔气孔是钢铁材料中常见的缺陷之一。
它们是由于熔体中的气体无法完全排除而形成的孔洞。
气孔的出现会降低钢铁材料的强度和韧性,导致材料易于断裂。
产生原因气孔的产生主要与以下几个因素有关:1.气体残留:在钢铁制造过程中,熔体中的气体不能完全排除,导致气孔的形成。
2.不良包壳材料:在铸造过程中使用的包壳材料可能含有化学成分,当熔体进入包壳时,会释放出气体并形成气孔。
3.渣浆不均匀:如果熔体中的渣浆没有均匀分布,会导致气孔的形成。
解决方案为了减少气孔的产生,可以采取以下措施:1.加强熔体的搅拌:通过加大搅拌力度,可以促使气体顺利排除。
2.选择合适的包壳材料:使用不含有气体产生物质的包壳材料,可以减少气孔的形成。
3.控制渣浆成分:保证渣浆成分的均匀分布,可以防止气孔的出现。
二、夹杂物夹杂物是钢铁材料中常见的缺陷之一。
它们是由于在钢铁制造过程中,杂质无法被完全排除而形成的。
夹杂物会降低钢铁材料的力学性能和耐蚀性,影响其使用寿命。
产生原因夹杂物的产生主要与以下几个因素有关:1.不纯净原材料:如果原材料中存在杂质,这些杂质可能无法被完全去除,从而形成夹杂物。
2.冶炼过程不当:在冶炼过程中,温度、压力等因素的控制不当会导致夹杂物的形成。
3.金属液流动不畅:如果金属液的流动不畅,如存在死角、漩涡等情况,会导致夹杂物的形成。
解决方案为了减少夹杂物的产生,可以采取以下措施:1.选择优质原材料:使用净化程度高的原材料,能够有效降低夹杂物的含量。
2.控制冶炼参数:严格控制冶炼过程中的温度、压力等参数,确保金属的纯净度。
3.优化液流动态:通过改善冶炼设备的结构和增加搅拌力度,可以改善金属液的流动状态,减少夹杂物的形成。
- 1、下载文档前请自行甄别文档内容的完整性,平台不提供额外的编辑、内容补充、找答案等附加服务。
- 2、"仅部分预览"的文档,不可在线预览部分如存在完整性等问题,可反馈申请退款(可完整预览的文档不适用该条件!)。
- 3、如文档侵犯您的权益,请联系客服反馈,我们会尽快为您处理(人工客服工作时间:9:00-18:30)。
(2)导卫板加工不良,口边不圆滑,或磨损严重,粘有氧化铁皮,将轧件表面划伤。
(3)孔型侧壁磨损严重,当轧件接触时产生弧形划伤。
(4)钢材在运输过程中与表面粗糙的辊道、盖板、移钢机、活动挡板等接触划伤。
缺肉
型钢其一侧面沿轧制方向全长或周期性的缺少金属称缺肉,缺陷处没有成品孔轧槽的热轧印迹,色暗、表面较粗糙。
(2)切深孔切人太深,造成腿长无法消除。
(3)轧辊不水平或有轴向串动,以及800咬入不正,成品孔夹板上偏等都会造成一腿长,一腿短等。
(4)腰的厚、薄主要是成品孔及成品前孔压下量不合理所造成。
划伤(刮伤、擦伤、划痕)
一般呈直线或弧形的沟槽,其深度不等,通长可见沟底,长度自几毫米到几米,连续或断续地分布于钢材的局部或全长,多为单条,有时出现多条。
尺寸超差(尺寸不合、规格不合)
尺寸超差是指型钢截面几何尺寸不符标准规定要求的统称。这类缺陷名目繁多,大部以产生部位以及其超差程度加以命名。例工、槽、角钢的腿长、腿短、腰厚、腰薄及一腿长,一腿短。
(1)对工字钢成品孔腿长往往表现在开口腿上,主要由于腰部压下量不够,角钢和槽钢成品孔压下量的大小,直接影响腿长和腿短。
(1)钢坯带来的表面非金属夹杂物。
(2)在加热或轧制过程中,偶然有非金属夹杂物(如加热炉的耐火材料及炉渣等),附在钢坯表面上,轧制时被压入钢材,冷却经矫直后部分脱落。
分层
此缺陷在型钢的锯切断面上呈黑线或黑带状,严重的分离成两层或多层,分层处伴随有夹杂物。
(1)主要是由于镇静钢的缩孔或沸腾钢的气囊未切净。
(3)成品孔入口夹板向孔型一侧安偏或松动。金属挤人孔型一侧辊缝里,产生单面耳子。
(4)成品入口夹板间隙过大或松动,进钢不稳,易产生双面断续耳子。
扭转
型钢绕其轴线扭成螺旋状称为扭转
(1)卫板安装不良,使轧件出孔时受到力偶的作用产生扭转。
(2)两侧延伸不一致,主要是压下不均或辊子有轴向串动。
(3)方、圆钢由于入口夹板安装不正确,使钢料进孔不正,造成延伸不一致。
轧钢常见缺陷
1、型钢常见缺陷
缺陷名称
缺陷特征
产生原因
结疤
型钢表面上的疤状金属薄块。其大小、深浅不等,外形极不规则,常呈指甲状、鱼鳞状、块状、舌头状无规律地分布在钢材表面上,结疤下常有非金属夹杂物。
由于钢坯未清理,使原有的结疤轧后仍残留在钢材表面上。
表面夹杂
暴露在钢材表面上的非金属物质称为表面夹杂,一般呈点状、块状和条状分布,其颜色有暗红、淡黄、灰白等,机械的粘结在型钢表面上,夹杂脱落后出现一定深度的凹坑,其大小、形状无一定规律。
(4)轧辊安装不正确,上、下轧辊轴线不在同一垂直平面内,即上、下辊成水平投影交叉,使轧件扭转。
(5)矫直机调整不当。
弯曲(弯头)
型钢沿垂直或水平方向呈现不平直的现象称为弯曲,一般为镰刀形或波浪形,仅只头部的弯曲叫弯头。
(1)轧机调整不当,轧辊倾斜或跳动,上、下辊径差大,造成速度差大。
(2)出口卫板安装不正确,卫板梁过低或过高。
裂纹
顺轧制方向出现在型钢表面上的线形开裂,一般呈直线形,有时呈“Y”形,多为通长出现,有时局部出现。
(1)钢坯有裂缝或皮下气泡、非金属夹杂物,经轧制破裂暴露。
(2)加热温度不均匀,温度过低,轧件在轧制时各部延伸与宽展不一致。
(3)加热速度过快、炉尾温度过高或轧制后冷却不当,易形成裂纹,此种情况多发生在高碳钢和低合金钢上。
耳子
在型钢表面上与L型开口处相对应的地方,出现顺轧制方向延伸的凸起部分称为耳子。有单边的,也有双边的,有时耳子产生在型钢的全长,也有局部或断续的,方、圆钢产生较多。
(1)轧机调整不当或孔型磨损严重,使成品前孔来料过大或成品孔压下量过大,产生过充满,多产生双边耳子。
(2)进入成品孔前因事故造成温度过低,进入成品孔时延伸降低,宽展过大,多产生双边耳子。
(2)钢坯的皮下气泡,严重疏松,在轧制时未压合,严重的夹杂物也会造成分层。
(3)钢坯的化学成份偏析严重,当轧制较薄规格时,也可能形成分层。
气泡(凸包)
型钢表面呈现的一种无规律分布的圆形凸起称为凸包,凸起部分的外缘比较圆滑,凸包破裂后成鸡爪形裂口或舌形结疤,叫气泡。多产生于型钢的角部及腿尖。
钢坯有皮下气泡,轧制时未焊合。
(1)孔型设计不良,轧辊车削不正确及轧机调整不当,使轧件进入成品孔时由于金属量不足,造成孔型充填不满。
(2)轧槽错牙或入口导板安装不当,造成轧件某一面缺少金属,再轧时孔型充填不满。
(3)前、后孔磨损程度不一样。
(4)圆轧件弯、扭造成进孔不正。
(5)对于工、槽钢,困钢坯不清理,往往出现结疤掉到闭口腿内,在轧制过程中便会出现周期性的腿尖缺肉。
(3)轧制过程中冷却不当,即因事故浇水时间过长或孔型冷却水开得太大,低温轧制易形成裂纹。
表面夹杂
暴露在钢轨表面上的非金属物质称为表面夹杂。一般呈点状、块状和条状,其大小、深浅无规律,颜色有暗红、淡黄、灰白等。
钢坯有夹杂。
由于钢坯未清理,钢坯原有的结疤经热轧变形后残留在钢勒表面上。
裂纹
在钢轨表面上呈现的与轧制方向一致的直线形缝隙叫“裂纹”,长短不一,多出现在轨头。裂纹通常较深,缝底尖细,有氧化铁皮和非金属夹杂物
(1)钢坯原有的裂纹经热轧变形后,演变在钢轨表面上。
(2)加热工艺不台理,即温度过高或加热速度过快,造成热应力,形成裂纹。
(1)矫直辊孔型设计不合理。
(2)矫直机调整操作不当。
(3)矫直辊磨损严重。
(4)轧辊磨损或成品孔出口卫板安装不良。
2、重轨常见缺陷
缺陷名称
缺Байду номын сангаас特征
产生原因
结疤
在钢轨的头、腰底部等处局部粘附的金属蒲片状疤皮为重轨结疤,外形轮廓不规则,有闭合和不闭合的,有生根和不生根的,结疤下面常有肉眼可见的非金属夹杂物。
(3)轧件温度不均匀,使金属延伸不一致。
(4)冷床拉钢小车不同步或滑轨不光滑。
(5)运输辊道速度过快,容易把钢材头部撞弯。
(6)矫直温度过高,冷却后容易产生弯曲。
(7)成品捆扎长短不齐较大。在运输中装卸不当。
(8)堆垛时不按规定进行。
(9)锯片用的太老,也容易产生弯头。
形状不正
型钢断面几何形状歪斜不正,这类缺陷对不同品种各异,名称繁多。如工槽钢的内并外斜,弯腰挠度,角钢顶角大、小腿不平等。