工业工程之生产线平衡与改善共84页文档
生产线平衡的改善-线的改善
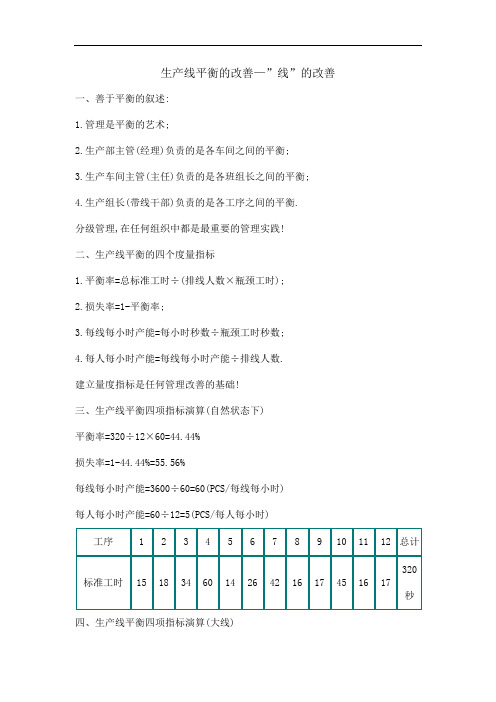
生产线平衡的改善—”线”的改善一、善于平衡的叙述:1.管理是平衡的艺术;2.生产部主管(经理)负责的是各车间之间的平衡;3.生产车间主管(主任)负责的是各班组长之间的平衡;4.生产组长(带线干部)负责的是各工序之间的平衡.分级管理,在任何组织中都是最重要的管理实践!二、生产线平衡的四个度量指标1.平衡率=总标准工时÷(排线人数×瓶颈工时);2.损失率=1-平衡率;3.每线每小时产能=每小时秒数÷瓶颈工时秒数;4.每人每小时产能=每线每小时产能÷排线人数.建立量度指标是任何管理改善的基础!三、生产线平衡四项指标演算(自然状态下)平衡率=320÷12×60=44.44%损失率=1-44.44%=55.56%每线每小时产能=3600÷60=60(PCS/每线每小时)每人每小时产能=60÷12=5(PCS/每人每小时)四、生产线平衡四项指标演算(大线)平衡率=320÷21×18=84.65%损失率=1-84.65%=15.35%每线每小时产能=3600÷18=200(PCS/每线每小时) 每人每小时产能=200÷21=9.5(PCS/每人每小时)五、生产线平衡四项指标演算(小线)平衡率=320÷5×74=86.48%损失率=1-86.48%=13.52%每线每小时产能=3600÷74=48.65(PCS/每线每小时) 每人每小时产能=48.65÷5=9.73(PCS/每人每小时)六、产品订单与产线契合程度论证分析(1)1.订单数量及瓶颈工时分布工时:订单数量级分析,找出最具有代表意义的瓶颈工时是多少?2.设定合理的假设条件做为计算基础:4H换线一次?还是8H换线一次?瓶颈工时以多少作为计算依据?3.模拟分析与计算长/中/短线的最适当订单量:长.中.短线的产能区间划分?4.根据订单分布情况,计算所需的三种生产线数量:长线多少条?中线多少条?短线多少条?5.选择代表款产品进行长/中/短线预排:只有经过实际预排才能论证长.中.短的可行性?6.论证假设条件与模拟分析的正确性:假设的论证条件与模拟分析的结果吻合吗?7.生产线状态与订单形态配备论证结论:方案可行性验状分析.。
生产线平衡分析与改善套路
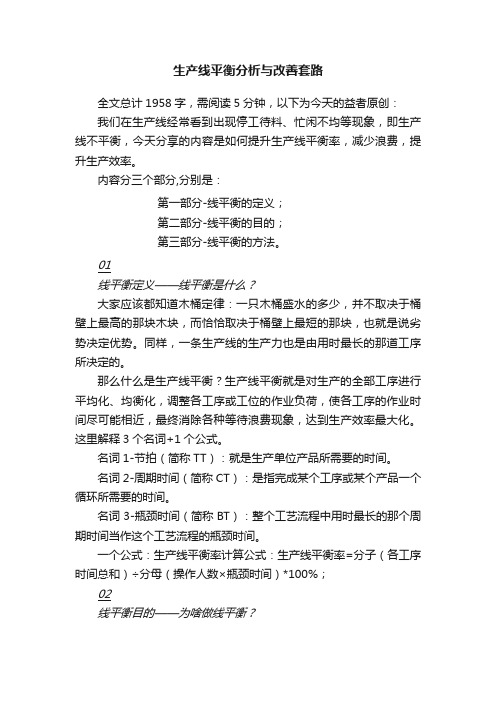
生产线平衡分析与改善套路全文总计1958字,需阅读5分钟,以下为今天的益者原创:我们在生产线经常看到出现停工待料、忙闲不均等现象,即生产线不平衡,今天分享的内容是如何提升生产线平衡率,减少浪费,提升生产效率。
内容分三个部分,分别是:第一部分-线平衡的定义;第二部分-线平衡的目的;第三部分-线平衡的方法。
01线平衡定义——线平衡是什么?大家应该都知道木桶定律:一只木桶盛水的多少,并不取决于桶壁上最高的那块木块,而恰恰取决于桶壁上最短的那块,也就是说劣势决定优势。
同样,一条生产线的生产力也是由用时最长的那道工序所决定的。
那么什么是生产线平衡?生产线平衡就是对生产的全部工序进行平均化、均衡化,调整各工序或工位的作业负荷,使各工序的作业时间尽可能相近,最终消除各种等待浪费现象,达到生产效率最大化。
这里解释3个名词+1个公式。
名词1-节拍(简称TT):就是生产单位产品所需要的时间。
名词2-周期时间(简称CT):是指完成某个工序或某个产品一个循环所需要的时间。
名词3-瓶颈时间(简称BT):整个工艺流程中用时最长的那个周期时间当作这个工艺流程的瓶颈时间。
一个公式:生产线平衡率计算公式:生产线平衡率=分子(各工序时间总和)÷分母(操作人数×瓶颈时间)*100%;02线平衡目的——为啥做线平衡?改善生产线平衡的目的简单来讲就2个:1、资源利用最大化,提升生产效率;2、消除人员等待现象,提升员工士气。
03线平衡方法——怎样做线平衡?工业工程师都应该学过ECRS四大原则,取消、合并、重排、简化;取消不必要的动作,无法取消的想办法合并,重新排列工序,简化作业方法。
生产线平衡采用的方法就是ECRS四大原则。
具体来说,生产线平衡改善,第一步首先要缩短瓶颈时间-提升单位产量;缩短瓶颈的具体方法有三种:1、前后分担转移:相邻间工序工序耗时长的工序,部分作业转移给工序耗时较短的工序;2、作业改善压缩:对瓶颈工序进行作业方法改善,实现工序工时缩短;举个例子:比如以前手机充电要有线接头,现在的无线充电技术,可以省力省时,缩短手机充电操作时间;3、加人改变CT:如果工序时间太长,可以增加人改善工序周期时间,但实际改善中,要求谨慎评估加人改变CT的方法;生产线平衡改善第二步:减少作业人员-产量不变,人员减少;具体方法也有三种:1、工序拆解去除:针对用时最短的工序,进行作业分割转移给其他临近工序,去除该用时最短的工序;2、合并省略工序:在不影响节拍的前提下,可以直接将用时最短的工序与其他临近工序合并,省去该用时最短的工序;3、改善作业合并:先对用时最短的工序进行进一步消除浪费的改善,缩短作业时间,再将该工序合并至其他临近工序,合并该用时最短的工序;一般生产线平衡改善就这两步,先缩短瓶颈时间;再减少作业人员。
生产线平衡分析改善案例

生产线平衡分析改善案例引言生产线平衡是指在生产过程中,通过合理分配各个工序的工作量,使得各个工序的产能能够实现平衡,从而提高生产效率、降低成本,并确保产品质量。
本文将以一个实际案例为例,介绍生产线平衡分析和改善的具体过程。
案例背景某电子产品制造公司拥有一条生产线,生产一种电子产品,该产品的组装工序分为A、B、C、D四个子工序。
在目前的生产线上,工序A的生产能力远超其他三个工序,导致A工序成为瓶颈工序,无法满足后续工序的需求,从而影响了整个生产线的效率和产量。
因此,公司决定进行生产线平衡分析,并制定改善方案,以提高生产线的平衡度。
生产线平衡分析1. 数据收集首先,需要收集工序A、B、C、D的工作时间数据,包括每个工序的加工时间、准备时间和等待时间。
这些数据将作为分析的基础。
2. 流程图绘制根据数据收集到的各个工序的时间,并结合实际生产情况,可以绘制出生产线的流程图。
流程图可以清晰地展示每个工序的工作时间和流程顺序,有助于进一步分析。
3. 生产线平衡计算根据流程图,可以计算出每个工序的工作时间总和。
然后,根据目标产量,计算出每个工序的标准工作时间,即每个工序应该占用的时间比例。
通过比较实际工作时间和标准工作时间,可以评估生产线的平衡度。
4. 分析结果根据生产线平衡计算的结果,可以看出工序A的工作时间远超其他工序,导致生产线的不平衡。
这也解释了为什么A工序成为瓶颈工序。
改善方案1. 调整工序A的产能由于工序A是瓶颈工序,可以考虑通过增加设备或优化工艺,提高工序A的产能,以满足后续工序的需求。
这可以通过增加工序A的设备数量、提高工段效率或优化工艺流程等手段实现。
2. 优化其他工序除了调整工序A的产能外,还可以进一步优化其他工序的流程,减少每个工序的工作时间。
例如,可以通过流程改进、工艺优化、培训员工等方式,提高其他工序的效率,从而平衡整个生产线。
3. 调整生产计划根据生产线平衡分析的结果,可以对生产计划进行合理调整。
工业工程中的生产线平衡与流程优化

工业工程中的生产线平衡与流程优化在现代制造业中,生产线平衡与流程优化是工业工程的重要方面。
通过对生产线的平衡和流程的优化,企业可以提高生产效率,降低成本,提高产品质量,增加竞争力。
本文将探讨工业工程中生产线平衡与流程优化的方法和实践。
一、生产线平衡的概念与意义生产线平衡是指在保证生产线各工序间的协调性和相对稳定性的前提下,根据生产需求分配各工序的工作量,使生产线各工序的工作负荷相对均衡。
生产线平衡的主要目标是最大限度地利用生产线资源,避免资源的浪费和闲置,提高生产效率和降低生产成本。
生产线平衡在工业领域具有重要的意义。
首先,生产线平衡可以提高生产效率。
通过合理分配各工序的工作负荷,可以避免某些工序过于繁忙,而其他工序却空闲的情况,从而达到资源的最大利用。
其次,生产线平衡可以降低生产成本。
生产线平衡可以减少工人的等待时间和机器的空闲时间,进而降低劳动力和机器的浪费,从而降低生产成本。
最后,生产线平衡可以提高产品质量。
通过合理分配工序的工作负荷,可以减少工人的疲劳程度,提高工序操作的准确性,从而提高产品质量。
二、生产线平衡的方法与实践生产线平衡可以通过不同的方法和工具来实现。
下面介绍几种常用的生产线平衡的方法与实践。
1. 流程分析法流程分析法是通过对生产线的各工序进行详细的测量和分析,从而找出生产线的瓶颈工序和不平衡因素,进而通过调整工序的工作负荷和工序之间的关系,实现生产线的平衡。
流程分析法主要包括流程图绘制、工序时间测量、瓶颈工序分析等步骤。
2. 动态调度法动态调度法是通过实时监控生产线的生产情况,根据实际生产需求,在不同工序之间调整工作负荷,以达到生产线的平衡。
动态调度法主要包括生产计划的实时调整、工序的实时变动等。
3. 自动化控制系统自动化控制系统是通过引入自动化设备和控制系统,实现生产线的自动调整和平衡。
自动化控制系统主要包括PLC控制系统、机器人控制系统等。
通过自动化控制系统,可以实现生产线的实时监控和优化调整,提高生产线的灵活性和效率。
工业工程之生产线平衡与改善
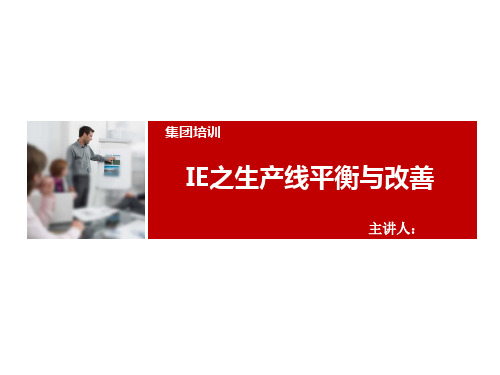
克服能力的障碍 克服意识的障碍 克服组织的障碍
7
2-1-3 标准化作业三要素
8
2-1-3 标准化作业三要素
要素之一:作业节拍(T.T)
T.T(Takt time ),是指生产一件产品所需要的时间 由市场销售情况,客户需求来决定的,与生产线的实际加 工时间、设备能力、作业人数等无关 计算公式如下: T.T= 1日的生产时间(定时) 1日的需要生产量
2-2 标准化作业实施步骤
步骤之二:观测时间 标准作业时间测定、归纳方法: ① 决定作业项目并记入观测纸
② 确定观测位置,记忆观测点
③ 观测时间(观测时间长度为2-3秒) ④ 求出一个循环的时间
⑤ 决定C.T
⑥ 求出各作业项目的时间 ⑦ 决定各作业项目时间
16
2-2 标准化作业实施步骤
对象工序 N O 1 2 3 4 5 6 7 作业项目
8
20 7 31 11 34 3 44 10 47 3 57 10 60 3
9
68 8 78 10 80 2 89 9 92 3 103 11 5 2
10
13 8 24 11 27 3 38 11 42 4 51 9 53 2
11
62 9 72 10 75 3 86 11 89 3 99 10 102 3
14
2-2 标准化作业实施步骤
步骤之一:准备阶段
作业标准
掌握零件 工具名称
工具准备
① 作业内容相同通用 一份作业标准 ② 作业内容有细微差 异通用一份作业标 准标明差异 ③ 作业内容存在大的 差异根据车型,分 别制作
提前进行部件、工 具名称的调查
① ② ③ ④ ⑤
硬纸板 观测用纸 笔 秒表 相机
生产线平衡分析与改善方法
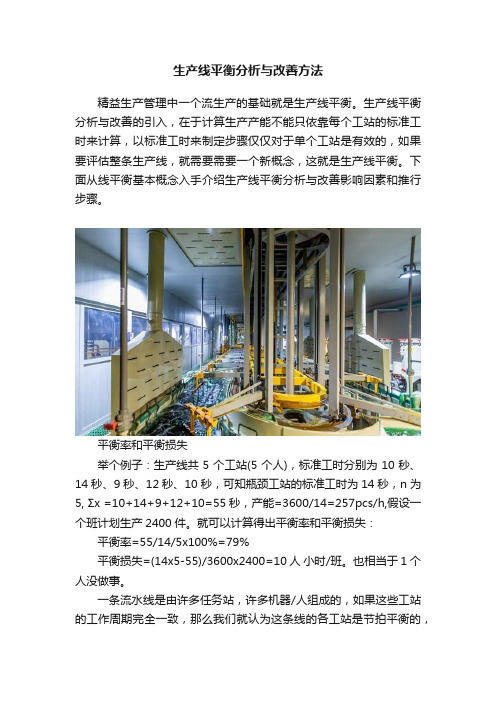
生产线平衡分析与改善方法精益生产管理中一个流生产的基础就是生产线平衡。
生产线平衡分析与改善的引入,在于计算生产产能不能只依靠每个工站的标准工时来计算,以标准工时来制定步骤仅仅对于单个工站是有效的,如果要评估整条生产线,就需要需要一个新概念,这就是生产线平衡。
下面从线平衡基本概念入手介绍生产线平衡分析与改善影响因素和推行步骤。
平衡率和平衡损失举个例子:生产线共5个工站(5个人),标准工时分别为10秒、14秒、9秒、12秒、10秒,可知瓶颈工站的标准工时为14秒,n为5, Σx =10+14+9+12+10=55秒,产能=3600/14=257pcs/h,假设一个班计划生产2400件。
就可以计算得出平衡率和平衡损失:平衡率=55/14/5x100%=79%平衡损失=(14x5-55)/3600x2400=10人小时/班。
也相当于1个人没做事。
一条流水线是由许多任务站,许多机器/人组成的,如果这些工站的工作周期完全一致,那么我们就认为这条线的各工站是节拍平衡的,即这条生产线是平衡的,没有平衡损失;否则就是不平衡的,有平衡损失。
线平衡性的衡量标准是平衡率,平衡率最高是100%,但实际中很难实现。
一条规划不好的线往往只有60%-75%的平衡率,一般我们认为线平衡率至少要达到85%才可以量产,如果要推行精益生产方式的一个流的生产方式,平衡率至少要95%以上。
生产线平衡之工时山积表生产线平衡分析:平衡率低的影响平衡率低带来的影响表现在这几个方面:产生等待浪费;产生WIP浪费;阻碍改替进行;生产效率低下;负荷不均影响士气;不能按客户需求开展节拍式生产,导致对客户需求响应迟钝。
所以生产线平衡率问题值得我们企业多加关注。
生产线平衡分析与改善推行步骤1、动作单元分解产品结构拆分(如果是新产品)或者现场实际观察(对已有产品改善),首先进行动作单元分解,画出动作先行图(动作先后顺序图)。
2、动作单元工时测量制定测量实际工时,进行速度评比及加上宽放。
生产线平衡分析与改善

重可能导致安全、效率和质量问题。 不平衡:导致浪费和负荷过重等.
2023/10/10
17
三、流水生产线平衡的设计方法
3、 单品种流水线平衡方法
②平衡图分析
产能平衡图是以目视的方式对单一产品于各工序所需 的时间进行图示分析。由于平衡图可以识别瓶颈工序的 可能发生工序,并以动作分析进行平衡。通常情况下, 运用平衡图主要对产品于各工序加工所需时间进行分析。
③生产线平衡率的计算:
若对C工序进行动作分析研究,将部分工作分配给闲置的B、D两工序, 则将有助于一产平衡率由64.17%提高至96.25%。产能比30分钟生产一 个成品,提高到20分钟生产一个成品,产能提高50% .
2023/10/10
24
三、流水生产线平衡的设计方法
③生产线平衡率的计算:
若评估上述两方案,对瓶颈工序C进行动作分析的生产线平 衡改善方案较增加作业资源的生产线平衡改善方案的效果为 佳(无须增加一个工位)
生产线通过多道工序完成成品,追求效率的方向应以整体的生产 效率,也就是以最终成品数量和配置的资源(人员、设备)的多 少来衡量
2023/10/10
16
三、流水生产线平衡的设计方法
3、 单品种流水线平衡方法
●木桶理论与项链理论
3M(浪费、负荷过重、不平衡) 浪费:搬运的浪费、不良品浪费、动作浪费、在库浪
凭借增加瓶颈工序的作业资源数,提高平衡率。
分解瓶颈工序的作业内容,并分提给其它工序。
减少非瓶颈工序的作业资源数,以提高平衡率;
合并相关工序,重新排布生产工序。相对来讲,在作业 内容相对较多的情况下容易平衡。在精益生产中,可凭 借U形布局的多能工轻易达到目的。
生产线平衡分析与改善方案

2019/7/14
5
二、流水生产线概述
1、 流水生产的基本概念
● 流水生产的原理
流水生产是在“分工”和“作业标准化”的原理 上发
展起来的 流水生产方式的诞生 必须依赖加工技术的支撑 流水生产方式的基础是流水生产线
2019/7/14
6
二、流水生产线概述
1、 流水生产的基本概念 ● 流水生产的特点
比较B、C两个工作站,将可发现B工作站的产能为C工作站的 2.69倍,B、C两个工作站将积压大量的半成品。若以传统追求 各工作站提升效率的方式进行管理,B工作站的效率提升,只会 恶化B、C站的半成品积压的浪费,而无助于整体产量的提高 (假设B工作站经训练生产效率达100%,则B工作站每小时产量 将达702.35个,产量为C工作站的3.36倍)。
2019/7/14
14
三、流水生产线平衡的设计方法
3、 单品种流水线平衡方法 ● 案例:生产线平衡分析案例
2019/7/14
15
三、流水生产线平衡的设计方法
3、 单品种流水线平衡方法
● 案例:生产线平衡分析案例
由表一可知A、B、C、D四个工序每小时产量处于不平衡的状态, 整体生产线的产量受限于C工序,每小时只能产出209.09个,其 他的工序的产出高于209.09个,只会堆积在生产线上而造成半成 品库存积压,而D工序更将因为C工序的产量,而形成时间的等 候。
IE工业工程
-----生产线平衡
课 程 内容
生产线平衡 一、生产线平衡的概述 二、流水生产线概述 三、生产线平衡的设计 四、生产线平衡的方法及改善原则 5、案例分析