外文翻译--硅酸盐水泥的化学成分(毕业论文外文翻译+中英文对照)
硅酸盐水泥熟料成分
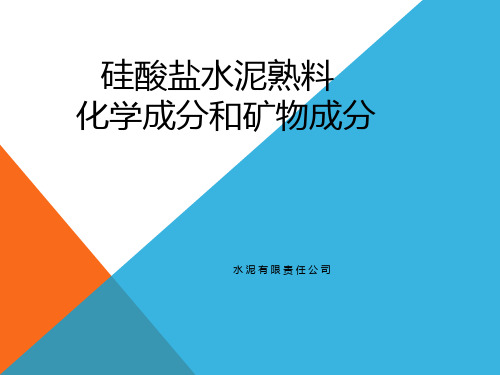
硅酸盐水泥熟料的矿物组成
硅酸盐水泥熟料的矿物组成硅酸盐水泥熟料实际上是 一种结晶细小的人造岩石(工艺岩石),它主要由 四种矿物组成:
1.硅酸三钙C3S:(3CaO·SiO2或Ca3SiO5)44-62%;
2.硅酸二钙C2S:(2CaO·SiO2或Ca2SiO4)18-30%; 3.铝酸三钙C3A:(3 CaO·Al2O3或CaAl2O6)5-18%; 4.铁铝酸四钙C4AF:(4CaO·Al2O3 ·Fe2O3或
(1)熟料中玻璃体对水泥性能的影响1) 影响水泥的颜色;2)玻璃体较多时, 能包围C2S,使C2S不易转化;3)玻璃
体提高时,水泥的抗硫酸盐性能增强。 (2)液相对煅烧的影响1)液量与煅烧 的关系C3A、C4AF在煅烧过程中,熔融 液相可以促进C3S的形成,这是它们的 一个重要作用。
如果物料中熔剂性矿物过少,使熟料易生
较高,主要引起水泥早期安定性不 良
f-CaO的危害与含量控制f-CaO与水反应生 成氢氧化钙时,体积膨胀97.9%,在硬化 水泥石内部造成局部应力,因此,随着fCaO含量的增加,首先抗拉(抗折)强度 降低,进而3天后强度倒缩,严重时引起 安定性不良。在烧成条件下死烧的一次fCaO结构比较致密,水化很慢,活性差, 通常要在加水3天后反应才比较明显,因 此一次f-CaO是引起安定性不良的主要原因; 二次f-CaO部分可能在混凝土拌制过程中已
硅酸盐水泥熟料 化学成分和矿物成分
水泥有限责任公司
硅酸盐水泥熟料的化学成分
一、主要化学成分
硅酸盐水泥熟料主要由CaO、SiO2、Al2O3、 Fe2O3四种氧化物组成。这四种氧化物通常占 95%以上,同时含有5%以下的其他氧化物,如 MgO、TiO2、P2O5以及碱(K2O与Na2O)等。 CaO:62-67%;SiO2:20-24%;Al2O3:4-7%; Fe2O3:2.5-6.0%
水泥专业外文翻译---波特兰水泥

Portland cementPortland cement(often referred to as OPC, from Ordinary Portland Cement) is the most common type of cement in general use around the world because it is a basic ingredient of concrete, mortar, stucco and most non-specialty grout. It is a fine powder produced by grinding Portland cement clinker (more than 90%), a limited amount of calcium sulfate (which controls the set time) and up to 5% minor constituents as allowed by various standards such as the European Standard EN197.1ASTM C 150 defines portland cement as "hydraulic cement (cement that not only hardens by reacting with water but also forms a water-resistant product) produced by pulverizing clinkers consisting essentially of hydraulic calcium silicates, usually containing one or more of the forms of calcium sulfate as an inter ground addition." Clinkers are nodules (diameters:0.2-1.0 inch [5–25 mm]) of a sintered material that is produced when a raw mixture of predetermined composition is heated to high temperature. The low cost and widespread availability of the limestone, shales, and other naturally occurring materials make portland cement one of the lowest-cost materials widely used over the last century throughout the world. Concrete becomes one of the most versatile construction materials available in the world.Portland cement clinker is made by heating, in a kiln, a homogeneous mixture of raw materials to a sintering temperature, which is about 1450 °C for modern cements. The aluminium oxide and iron oxide are present as a flux and contribute little to the strength. For special cements, such as Low Heat (LH) and Sulfate Resistant (SR) types, it is necessary to limit the amount of tricalcium aluminate (3CaO.Al2O3) formed. The major raw material for the clinker-making is usually limestone (CaCO3) mixed with a second material containing clay as source of alumino-silicate. Normally, an impure limestone which contains clay or SiO2 is used. The CaCO3 content of these limestones can be as low as 80%. Second raw materials (materials in the rawmix other than limestone) depend on the purity of the limestone. Some of the second raw materials used are: clay, shale, sand, iron ore, bauxite, fly ash and slag. When a cement kiln is fired by coal, the ash of the coal acts as a secondary raw material HistoryPortland cement was developed from natural cements made in Britain in the early part of the nineteenth century, and its name is derived from its similarity to Portland stone, a type of building stone that was quarried on the Isle of Portland in Dorset, England.The Portland cement is considered to originate from Joseph Aspdin, a British bricklayer from Leeds. It was one of his employees (Isaac Johnson), however, who developed the production technique, which resulted in a more fast-hardening cement with a higher compressive strength. This process was patented in 1824. His cement was an artificial cement similar in properties to the material known as "Roman cement" (patented in 1796 by James Parker) and his process was similar to that patented in 1822 and used since 1811 by James Frost who called his cement "British Cement". The name "Portland cement" is also recorded in a directory published in 1823 being associated with a William Lockwood, Dave Stewart, and possibly others.Aspdin's son William, in 1843, made an improved version of this cement and he initially called it "Patent Portland cement" although he had no patent. In 1848 William Aspdin further improved his cement and in 1853 he moved to Germany where he was involved in cement making. Many people have claimed to have made the first Portland cement in the modern sense, but it is generally accepted that it was first manufactured by William Aspdin at Northfleet, England in about 1842. The German Government issued a standard on Portland cement in 1878.ProductionThere are three fundamental stages in the production of Portland cement:1.Preparation of the raw mixture2.Production of the clinker3.Preparation of the cementTo simplify the complex chemical formulae which describe the compounds present in cement, a cement chemist notation was invented. This notation reflects the fact that most of the elements are present in their highest oxidation state, and chemical analyses of cement are expressed as mass percent of these notional oxidesRawmix preparationThe raw materials for Portland cement production are a mixture of minerals containing calcium oxide, silicon oxide, aluminium oxide, ferric oxide, and magnesium oxide, as fine powder in the 'Dry process' or in the form of a slurry in the 'Wet process'. The raw materials are usually quarried from local rock, which in some places is already practically the desired composition and in other places requires the addition of clay and limestone, as well as iron ore, bauxite or recycled materials. The individual raw materials are first crushed, typically to below 50 mm.Formation of clinkerThe raw mixture is heated in a cement kiln, a slowly rotating and sloped cylinder, with temperatures increasing over the length of the cylinder up to a peak temperature of 1400-1450 °C. A complex succession of chemical reactions takes place (see cement kiln) as the temperature rises. The peak temperature is regulated so that the product contains sintered but not fused lumps. Sintering consists of the melting of25-30% of the mass of the material. The resulting liquid draws the remaining solid particles together by surface tension and acts as a solvent for the final chemical reaction in which alite is formed. Too low a temperature causes insufficient sintering and incomplete reaction, but too high a temperature results in a molten mass or glass, destruction of the kiln lining, and waste of fuel. When all goes according to plan, the resulting material is clinker. On cooling, it is conveyed to storage. Some effort is usually made to blend the clinker because, although the chemistry of the rawmix may have been tightly controlled, the kiln process potentially introduces new sources of chemical variability. The clinker can be stored for a number of years before use. Prolonged exposure to water decreases the reactivity of cement produced from weathered clinker.The enthalpy of formation of clinker from calcium carbonate and clay minerals is about 1500 to 1700 kJ/kg. However, because of heat loss during production, actual values can be much higher. The high energy requirements and the release of significant amounts of carbon dioxide makes cement production a concern for global warming.Cement grindingIn order to achieve the desired setting qualities in the finished product, a quantity(2-8%, but typically 5%) of calcium sulfate (usually gypsum or anhydrite) is added to the clinker and the mixture is finely ground to form the finished cement powder. This is achieved in a cement mill. The grinding process is controlled to obtain a powder with a broad particle size range, in which typically 15% by mass consists of particles below 5 μm diameter, and 5% of particles above 45 μm. The measure of fineness usually used is the "specific surface area", which is the total particle surface area of a unit mass of cement. The rate of initial reaction (up to 24 hours) of the cement on addition of water is directly proportional to the specific surface area. Typical values are 320–380 m2·kg−1 for general purpose cements, and 450–650 m2·kg−1 for "rapid hardening" cements. The cement is conveyed by belt or powder pump to a silo for storage. Cement plants normally have sufficient silo space for 1–20 weeks production, depending upon local demand cycles. The cement is delivered to end-users either in bags or as bulk powder blown from a pressure vehicle into the customer's silo. In industrial countries, 80% or more of cement is delivered in bulkUseThe most common use for Portland cement is in the production of concrete. Concrete is a composite material consisting of aggregate (gravel and sand), cement, and water. As a construction material, concrete can be cast in almost any shape desired, and once hardened, can become a structural (load bearing) element. Users may be involved in the factory production of pre-cast units, such as panels, beams, road furniture, or may make cast-in-situ concrete such as building superstructures, roads, dams. These may be supplied with concrete mixed on site, or may be provided with "ready-mixed" concrete made at permanent mixing sites. Portland cement is also used in mortars (with sand and water only) for plasters and screeds, and in grouts (cement/water mixes squeezed into gaps to consolidate foundations, road-beds, etc.).When water is mixed with Portland Cement, the product sets in a few hours and hardens over a period of weeks. These processes can vary widely depending upon the mix used and the conditions of curing of the product, but a typical concrete sets in about 6 hours and develops a compressive strength of 8 MPa in 24 hours. The strength rises to 15 MPa at 3 days, 23 MPa at 1 week, 35 MPa at 4 weeks and 41 MPa at3 months. In principle, the strength continues to rise slowly as long as water is available for continued hydration, but concrete is usually allowed to dry out after a few weeks and this causes strength growth to stop.Cement plants used for waste disposal or processingDue to the high temperatures inside cement kilns, combined with the oxidizing (oxygen-rich) atmosphere and long residence times, cement kilns are used as a processing option for various types of waste streams: indeed, they efficiently destroy many hazardous organic compounds. The waste streams also often contain combustible materials which allow the substitution of part of the fossil fuel norma lly used in the process.Waste materials used in cement kilns as a fuel supplement∙Paint sludge from automobile industries∙Waste solvents and lubricants∙Meat and bone meal - slaughterhouse waste due to bovine spongiform encephalopathy contamination concerns∙Waste plastics∙Sewage sludge∙Rice hulls∙Sugarcane waste∙Used wooden railroad ties (railway sleepers)Portland cement manufacture also has the potential to remove industrialby-products from the waste-stream, effectively sequestering some environmentally damaging wastes∙Slag∙Fly ash (from power plants)∙Silica fume (from steel mills)∙Synthetic gypsum波特兰水泥硅酸盐水泥(OPC),通常是指从普通硅酸盐水泥)是最常见的一种水泥在世界各地的一般用途,因为它是一种基本成分的混凝土、砂浆、粉刷、最非专业浆液。
外文翻译 (自动保存的)

能源和建筑在MWC的热性能和机械性能研究:提高混凝土制品环境可持续性克里斯蒂娜Becchio ,斯特凡诺保罗Corgnati ,安德烈Kindinis ,西莫内塔Pagliolico能量学系(DENER ),都灵理工大学,科索公爵阿布鲁齐24 ,10129都灵,意大利材料科学与工程化学(DISMIC ),都灵理工大学,科索公爵阿布鲁齐24 ,10129意大利都灵系文章信息文章历史:2009年3月13日修改稿2009年5月13日2009年5月29日关键词:木材聚集轻质混凝土热式质量电导率抗压强度摘要本研究以构成一个更可持续的轻质混凝土,矿化木混凝土(MWC)上,由木工生产废料替代天然骨料的可能性。
利用这种类型的聚集体,三重目的已经达到:保存天然原料,节约能源和废物的再利用。
此外,使用木材聚集的性能,试图建立一个可持续的混凝土具有高的热惯量,高耐热性和低体重。
在本文中,对混凝土的机械性能和热性能的添加木聚集体的影响进行了研究。
机械性能进行了调查与抗压强度的测试,而一维热流模型已被用于预测MWC的热导率。
这个方案具有良好的绝缘围护结构的需求,同时具有高的热质量:使用MWC可以用不同的类型学比较重的建筑围护结构的想法有关。
一系列其他的值可以得出:重量轻,环保,易产业化,便于现场浇注。
因此,在建筑结构木器,混凝土的应用程序可能是为了提高可持续性和建筑节能一个有趣的解决方案。
2009爱思唯尔B.V.保留所有权利。
1 、介绍促进可持续发展带来了压力采取适当的方法,以保护环境各个行业,包括建筑。
在建设过程中需要能量的高支出,并导致广泛的可量化的环境影响,包括气体排放,水资源利用和固体和液体废物。
能源消耗的提取,运输,加工和装配的原材料,以及所连接的二氧化碳和温室气体排放占建设[1-3]所有生命周期的多变,但相当大的比率。
还有一系列既通过施工过程和建设的网站上的存在,包括土地的干扰,生态系统改变,植被破坏,占领一个潜在的资源网站的结果,产生不易量化局部环境的影响地下水干扰。
外文翻译(英文)利用IR,SEM和维尔卡技术检测硅酸盐水泥的早起水化及其制备过程
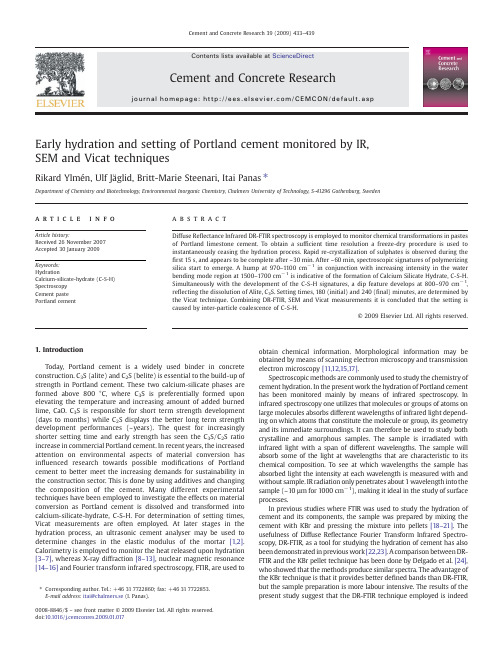
Early hydration and setting of Portland cement monitored by IR,SEM and Vicat techniquesRikard Ylmén,Ulf Jäglid,Britt-Marie Steenari,Itai Panas ⁎Department of Chemistry and Biotechnology,Environmental Inorganic Chemistry,Chalmers University of Technology,S-41296Gothenburg,Swedena b s t r a c ta r t i c l e i n f o Article history:Received 26November 2007Accepted 30January 2009Keywords:HydrationCalcium-silicate-hydrate (C-S-H)Spectroscopy Cement paste Portland cementDiffuse Re flectance Infrared DR-FTIR spectroscopy is employed to monitor chemical transformations in pastes of Portland limestone cement.To obtain a suf ficient time resolution a freeze-dry procedure is used to instantaneously ceasing the hydration process.Rapid re-crystallization of sulphates is observed during the first 15s,and appears to be complete after ~30min.After ~60min,spectroscopic signatures of polymerizing silica start to emerge.A hump at 970–1100cm −1in conjunction with increasing intensity in the water bending mode region at 1500–1700cm −1is indicative of the formation of Calcium Silicate Hydrate,C-S-H.Simultaneously with the development of the C-S-H signatures,a dip feature develops at 800–970cm −1,re flecting the dissolution of Alite,C 3S.Setting times,180(initial)and 240(final)minutes,are determined by the Vicat bining DR-FTIR,SEM and Vicat measurements it is concluded that the setting is caused by inter-particle coalescence of C-S-H.©2009Elsevier Ltd.All rights reserved.1.IntroductionToday,Portland cement is a widely used binder in concrete construction.C 3S (alite)and C 2S (belite)is essential to the build-up of strength in Portland cement.These two calcium-silicate phases are formed above 800°C,where C 3S is preferentially formed upon elevating the temperature and increasing amount of added burned lime,CaO.C 3S is responsible for short term strength development (days to months)while C 2S displays the better long term strength development performances (~years).The quest for increasingly shorter setting time and early strength has seen the C 3S/C 2S ratio increase in commercial Portland cement.In recent years,the increased attention on environmental aspects of material conversion has in fluenced research towards possible modi fications of Portland cement to better meet the increasing demands for sustainability in the construction sector.This is done by using additives and changing the composition of the cement.Many different experimental techniques have been employed to investigate the effects on material conversion as Portland cement is dissolved and transformed into calcium-silicate-hydrate,C-S-H.For determination of setting times,Vicat measurements are often employed.At later stages in the hydration process,an ultrasonic cement analyser may be used to determine changes in the elastic modulus of the mortar [1,2].Calorimetry is employed to monitor the heat released upon hydration [3–7],whereas X-ray diffraction [8–13],nuclear magnetic resonance [14–16]and Fourier transform infrared spectroscopy,FTIR,are used toobtain chemical information.Morphological information may be obtained by means of scanning electron microscopy and transmission electron microscopy [11,12,15,17].Spectroscopic methods are commonly used to study the chemistry of cement hydration.In the present work the hydration of Portland cement has been monitored mainly by means of infrared spectroscopy.In infrared spectroscopy one utilizes that molecules or groups of atoms on large molecules absorbs different wavelengths of infrared light depend-ing on which atoms that constitute the molecule or group,its geometry and its immediate surroundings.It can therefore be used to study both crystalline and amorphous samples.The sample is irradiated with infrared light with a span of different wavelengths.The sample will absorb some of the light at wavelengths that are characteristic to its chemical composition.To see at which wavelengths the sample has absorbed light the intensity at each wavelength is measured with and without sample.IR radiation only penetrates about 1wavelength into the sample (~10µm for 1000cm −1),making it ideal in the study of surface processes.In previous studies where FTIR was used to study the hydration of cement and its components,the sample was prepared by mixing the cement with KBr and pressing the mixture into pellets [18–21].The usefulness of Diffuse Re flectance Fourier Transform Infrared Spectro-scopy,DR-FTIR,as a tool for studying the hydration of cement has also been demonstrated in previous work [22,23].A comparison between DR-FTIR and the KBr pellet technique has been done by Delgado et al.[24],who showed that the methods produce similar spectra.The advantage of the KBr technique is that it provides better de fined bands than DR-FTIR,but the sample preparation is more labour intensive.The results of the present study suggest that the DR-FTIR technique employed is indeedCement and Concrete Research 39(2009)433–439⁎Corresponding author.Tel.:+46317722860;fax:+46317722853.E-mail address:itai@chalmers.se (I.Panas).0008-8846/$–see front matter ©2009Elsevier Ltd.All rights reserved.doi:10.1016/j.cemconres.2009.01.017Contents lists available at ScienceDirectCement and Concrete Researchj ou r n a l h o m e pa g e :ht t p ://e e s.e l s e v i e r.c o m /C E MC ON /d e f a ul t.a s ppreferred in that external physico-chemical interference is minimized,i.e.the hydration products are studied in the proper cement matrix with a minimum of sample tampering,and avoiding contact with foreign chemicals.Differential IR light absorption of samples which have been allowed to hydrate for different times is reported here.Water displays strong absorption in the mid-IR range,which makes it virtually impossible to perform in situ studies of cement hydration.A second draw back of in situ DR-FTIR for the study of cement hydration is that the surface of the cement paste,while hydrating,may become too flat for the diffuse re flectance technique to be ef ficiently used.These considerations validate selection of an ex situ DR-FTIR approach.To study very early hydration using an ex situ technique,it is imperative that the hydration is stopped instantaneously at a predetermined time.To satisfy this requirement,a freeze-dry technique is adopted in this research.The freezing of the sample with liquid nitrogen ensures that all chemical processes are very much retarded,while the subsequent water evaporation step at low temperature minimizes any thermally induced chemical transforma-tions other than water removal while drying.Indeed,earlier microscopy work [25–27]has shown that freezing is a relatively mild method to stop hydration.The drying will of course affect the structures of some phases.Bound water,like in ettringite,could be partially removed,and morphological properties may change upon removal of water.The purpose of the present study is to demonstrate the ef ficiency of the freeze-dry procedure in conjunction with DR-FTIR spectroscopy for studying the complex hydration chemistry of Portland cement.An attempt to correlate relevant spectroscopic signatures to the devel-opment of strength in the system is also made.Strength development is monitored here by means of Vicat measurements.2.ExperimentalThe Portland cement used was a Portland limestone cement,“byggcement Std PK Skövde CEM II/A-LL 42,5R ”,from Cementa AB.An automatic/manual mortar mixer 39-0031from ELE International was used.The cement was mixed with distilled deionized water that was poured into the mixing bowl before adding the cement.The ratio of water to as received dry cement was 0.4by weight in both DR-FTIR and Vicat measurements.The cement was carefully added and the paste was mixed at 140rpm on the mixing blade and 62rpm on the mixing head.The hydration time was measured from the instant when the cement was added to the water.2.1.DR-FTIRThe spectrometer used was a Nicolet Magna-IR 560with an insert cell for diffuse re flectance spectroscopy.The measurement range liesbetween 400and 4000cm −1.The diffuse re flectance technique is utilized,in which the incident beam is allowed to be re flected off the ground sample towards an overhead mirror upon which the diffusely scattered rays are collected and measured in the detector.A more detailed description is given by Fuller and Grif fiths [28].The sample is scanned 64times with a resolution of 2.0cm −1and the presented data is an average value.Each sample was prepared and analyzed 3times and the final spectrum was an average of these 3measurements to minimize differences due to sample preparation.The batch size was 200g of as received dry cement.As the cement hydration was studied from 15s the cement paste was only mixed for 15s.However,the chemical development of the cement paste was found to be insensitive of mixing time as long as the cement was completely wetted [29].Samples were prepared in plastic dishes of 35mm in diameter.The thickness of the paste in the dishes was ~2–3mm.Lids were placed over the dishes while they hydrated to prevent water from evaporating.The samples were hydrated between 15s and 360min in normal laboratory environment,then frozen by immersion in liquid nitrogen and subsequently placed in the freeze drier overnight.Measurements were made the following day.Before measurement the sample was ground and placed in the sample holder of the DR-FTIR spectrometer.To obtain good reproducibility,great care was taken when grinding the samples and placing them in the sample cup to make the samples as similar as possible.2.2.VicatThe batch size was 300g of as received dry cement and the cement paste was mixed for 2⁎90s with a stop in between for 15s to scrape the paste from the inside walls.The Vicat apparatus used was a Vicatronic automatic recording apparatus E040and measurements were performed in a 40mm mould with a calibrated weight of 300g and a cylindrical needle with flat tip area of 1mm 2.2.3.Scanning electron microscopyThe microscope used was a FEI Quanta 200FEG ESEM operated in secondary electron detection mode with high-vacuum and an acceleration voltage of 2kV.Some of the freeze-dried samples were pulverized.Since the freeze-dried samples were barely holding together this was easily done with a metal spoon.Some of the powder was placed on carbon tape attached to the sampleholder.Fig.1.Vicat measurement showing the depth of penetration of the Vicat needle into the cement as function of time.The height of the mould was 40mm.Table 1Possible assignment to some of the peaks observed in Figs.2–5.Wave number [cm −1]Possible assignment Reference656–658υ4of SiO 4[21,40]714υ4of CO 3[22,32,35,37]847–848Al –O,Al –OH [21,35]877–878υ2of CO 3[21,22,35,37]1011–1080Polymerized silica [19]~1100–1200υ3of SO 4[19,22,31,32]1200–1202Syngenite,thenardite [32–34]1400–1500CO 3[19,21,22,35,37]1620–1624υ2of water in sulphates [22,31,33]1640–1650υ2H 2O[21,35,36]1682–1684υ2of water in sulphates [22,31,33]1795–1796CaCO 3Own measurement,[22]2513–2514CaCO 3Own measurement,[22]2875–2879CaCO 3Own measurement,[22]2983–2984CaCO 3Own measurement,[22]3319–3327Syngenite,thenardite [32–34]3398–3408υ3of H 2O,capillary water [36]3457υ1+υ3of H 2O[21,36]3554υ3of H 2O in gypsum [22,31]3611Bassanite [22]3641–3644Ca(OH)2Own measurement,[20,23,24,37]434R.Ylmén et al./Cement and Concrete Research 39(2009)433–439Several regions were examined to make sure that the observed structures were representative of the sample.3.ResultsThe present study attempts to correlate setting with the evolution of spectral features in DR-FTIR spectra during early hydration of cement.The Vicat setting time measurement for the used Portland cement is displayed in Fig.1.Initial andfinal set are seen to occur at 180min and240min respectively.In Section3.1,the overall time evolution of DR-FTIR absorption intensities is presented.Possible assignments of the different bands are shown in Table1,and interpreted in Sections3.1.2–3.1.4.3.1.Time resolved spectra of hydrating cementThe hydration process was monitored for thefirst six hours by applying the freeze dry method,grinding of sample and subsequently acquiring the DR-FTIR spectra.The recorded absolute spectra of dry and hydrated cement are displayed in Fig.2.It shows the spectra of theas received dry cement together with the cement just after it has been mixed(15s),after180min and360min of hydration.Weak signatures of hydration can be seen in the900–1200cm−1region.To enhance these effects,various difference spectra were constructed.In Fig.3,the difference spectra employ as received dry cement as reference.Now, the spectroscopic features can be seen significantly clearer and we observe the development and saturation band at1100–1200cm−1 already after15s.This is complemented by a more slowly growing feature at900–1100cm−1.Because the bands that developed after 15s cannot be associated with the actual hardening of cement paste, the15s spectrum was taken as reference in Figs.4and5.Fig.3 supports the overall procedure in that a smooth background is observed in the relevant spectral regions.Having found this,Fig.5 focuses on the500–2000cm−1interval and the spectra for twelve different hydration times are displayed.3.1.1.Sulphate bandsThe sulphates originally present in Portland cement are gypsum (CaSO4·2H2O),hemihydrate(bassanite,CaSO4·0.5H2O)and anhy-drite(CaSO4).The latter ones are formed when the gypsum is ground with the cement clinker.The heat makes some of the crystal water in the gypsum to dissociate.When water is added to the cement the sulphates react with the aluminate and ferrite phases of the cement to produce AFt phase.This phase in turn reacts further with the aluminate and ferrite phases to form the AFm phase[30].Characteristic sulphate absorption bands are generally found in the range1100–1200cm−1due to theυ3vibration of the SO42−-group in sulphates[19,22,31,32].It is very difficult to interpret this area by studying FTIR-spectra only,since the many forms of sulphates give rise to several peaks here and cause lots of overlaps,but also because the υ3vibration of the SiO42−-group can absorb in this region,especially when it has polymerized[21].Therefore no in-depth analysis of it will be done in this work.In the DR-FTIR spectrum of as received dry cement(Fig.2,bottom spectrum),a broad feature is seen in1100–1200cm−1region reflecting mainly amorphous sulphates.Immedi-ately after mixing with water,some sharp absorption bands develop at 1100cm−1,1200cm−1and3320cm−1,indicative of very rapid dissolution of sulphates followed by crystallization(Fig.2,15s spectrum).This can also be inferred by considering the15s difference spectrum in Fig.3.This spectrum corresponds to the difference between that acquired after15s of hydration,and the spectrum of dry cement.Spectral signatures of sulphate chemistry after15s of hydration,corresponding to re-crystallization are obtained.Appar-ently,crystalline sulphate phases form very early in the hydration process,after which they become inactive spectator phases.The extent to which this holds true can be assessed by replacing the as received dry cement reference spectrum for that of15s hydrated cement(Figs.4and5).From Fig.5we observe significant changes in the sulphate absorption bands up to30min of hydration.Apparently, intermediate phases are formed consistent with theabsorptionFig.2.Absorbance of as received dry cement and cement that has been allowed tohydrate for15s,180min and360min after the cement was added to the water.Thespectra are shown offset forclarity.Fig.3.Difference spectra where the absorbance spectrum of as received dry cement hasbeen subtracted from the absorbance spectra of cement hydrated for15s,180min and360min.The spectra are shown offset forclarity.Fig.4.Difference spectra in the range400–4000cm−1where the absorbance spectrumof the freshly mixed cement(15s)has been subtracted from the absorbance spectra ofcement hydrated for30s,5min,120min and360min.The spectra are shown offset forclarity.435R.Ylmén et al./Cement and Concrete Research39(2009)433–439spectra of syngenite (K 2Ca(SO 4)2·H 2O)and thenardite (Na 2SO 4)or closely related compounds [32–34].At any rate,after 60min,little changes can be seen in the sulphate absorption region of the spectra.3.1.2.Water associated bandsIn the spectrum for as received dry cement there is a peak at 1623cm −1and a smaller one at 1684cm −1.These are caused by the bending vibration υ2of water in sulphates,mainly gypsum [22,31,33].The peak at 3554cm −1is caused by the υ3vibration of water in gypsum [22,31]and the peak at 3611cm −1could be caused by bassanite (CaSO 4·0.5H 2O).As hydration progresses there is a broad feature forming with its centre at ~1650cm −1,caused by the bending vibration υ2of irregularly bound water [21,35,36].The consumption of gypsum can be seen as dips in this feature at 1623cm −1and 1680cm −1(Figs.4and 5).A small increase in gypsum during the first 10min is implied,and may be due to the transformations of anhydrite and bassanite.The “background ”level for wave numbers N 1600cm −1is steadily increasing with increasing hydration times.Since there seems to be no corresponding decrease in any other area,this is probably caused by the incorporation of water.The absorption intensities due to the υ2vibration mode of water at ~1650cm −1and the υ1+υ3modes at ~3450cm −1and results from Mollah et al.and Yu et al.support this observation [21,36].3.1.3.Silica associated bandsAfter about 2h of hydration new spectral intensity shifts are observed from ~900cm −1towards ~1000–1100cm −1(see Figs.3–5),neither associated with sulphates nor water,suggestive of rearrange-ments in the silica subsystem.These dip-hump features are taken to re flect dissolution of alite and simultaneously the polymerization ofsilica [21,23,37,38]to form calcium silicate hydrate C-S-H (vide infra ).In order to focus on the silica chemistry,the 15s reference spectrum is replaced by that acquired after 30min (see Fig.6),i.e.after the sulphate chemistry has stopped.Monotonous growth of the C-S-H associated absorption intensities (970–1100cm −1)is observed.The dip in the absorption spectrum at 800–970cm −1,which deepens with time,is due to the dissolution of the C 3S clinker phase [39].The intensities in the dip (800–970cm −1)and hump (970–1100cm −1)regions in Fig.6were integrated in an attempt to correlate the clinker dissolution with the silica polymerization.A horizontal line at the intensity at 970cm −1was used as baseline.The result is plotted in Fig.7.3.1.4.Hydroxides and carbonatesThe peak at 3643cm −1(see Table 1and Figs.2and 3)corresponds to Ca(OH)2,which is formed as silicate phases in the cement dissolve.The peaks at 1796cm −1,2513cm −1,2875cm −1,2983cm −1and the shoulder at 1350–1550cm −1are due to that portion of calcium carbonate,which is added to the cement by the manufacturer after clinker calcination.The amount of calcium carbonate is seen to decrease as the hydration progresses,i.e.negative absorption bands in the difference spectra of Figs.3and 4.This may partly be due to the reaction of calcite with the aluminate to form less crystalline phases such as carboxyaluminates [40,41]or the carbonate ion can substitute for sulphate ions in Aft and AFm phases [13,30].The peak growing at ~1070cm −1could be the υ1vibration of CO 3-group in the formed carbonates [33,35],but this observation would contradict theoverallFig.6.Difference spectra in the range 500–2000cm −1where the absorbance spectrum of cement hydrated for 30min has been subtracted from the absorbance spectra of cement with hydration times from 60–360min.The spectra are shown offset forclarity.Fig.7.Integrated value of the absorbance in the intervals 800–970cm −1(upper dots)and 970–1100cm −1(lower dots)in Fig.6as function of hydration time of the cement.The lines are drawn on free hand to guide the eye and does not represent a mathematicalmodel.Fig.5.Difference spectra in the range 500–2000cm −1where the absorbance spectrum of the freshly mixed cement (15s)has been subtracted from the absorbance spectra of cement with hydration times from 30s to 360min.The spectra are shown offset for clarity.436R.Ylmén et al./Cement and Concrete Research 39(2009)433–439Fig.8.SEM pictures of cement at different stages of hydration.a)Surface of unhydrated particle.b)Surface of particle hydrated for 15s.c)Surface of particle hydrated for 120min.d)Surface of particle hydrated for 240min.e)Surface of particle hydrated for 480min.f)Surface of particle hydrated for 480min at larger magni fication.437R.Ylmén et al./Cement and Concrete Research 39(2009)433–439reduction of carbonate absorption intensities with time.A more plausible candidate for this absorption band is the stretching vibration of Si–O,which is also found in jennite(Ca8(Si6O18H2)(OH)8Ca·6H2O) [37,38].3.2.SEMSEM pictures of cement grains at different stages of hydration are displayed in Fig.8.The surfaces of the unhydrated particles are bare, with debris lying on top(Fig.8a).After15s and120min of hydration (Fig.8b,c)the surfaces of the cement particles are still found to be bare,but lumps and platelets have formed in addition to the debris present already on the unhydrated particles.Fig.8d shows cement after240min of hydration.Now a carpet is covering the cement particles.The carpet has grown even more after480min of hydration and is seen to consist of needle-like protruding structures(Fig.8e,f).4.DiscussionA longstanding issue concerns the roles of various phases during early hardening of Portland cement.In particular the roles of sulphates,added to the Portland cement as anhydrous(CaSO4), hemihydrate(CaSO4·0.5H2O),and gypsum(CaSO4·2H2O)have been much discussed in this context.Indeed,the general consensus is that the dissolution and re-crystallization of the various sulphate contain-ing phases is completed well before the setting occurs[42,43].Yet,due to the complexity and instability of the early cement chemistry,the sulphates,besides their well known function as water absorbents, have been empirically found to affect the morphology of the hydrating paste both by providing a background ionic strength and by forming intermediate phases,which suppress“flash setting”.In the present study,results show that the sulphate related DR-FTIR absorption bands display large changes in the1100–1200cm−1interval but that this occurs mainly during thefirst10min of hydration,during which the development of sharp bands imply the formation of crystalline phases.The appearing platelets and hexagonal crystals seen with SEM are possibly associated with these phases.After30min,the inter-conversion of sulphate phases has apparently stopped.The sulphates formed are most probably ettringite or monosulphate,as earlier studies on cement hydration have shown that these sulphates are formed during thefirst minutes of hydration[11,43,44].In this study of the evolution of the C-S-H absorption bands,the30min spectrum was chosen as reference.The degree to which the sulphate chemistry is completed at this time can be appreciated by studying1100–1200cm−1region in Fig.6,keeping in mind that C-S-H also displays absorption bands in this interval.By DR-FTIR spectroscopy,detectable amounts of polymerized silica are formed after approximately1h of hydration,as seen in Fig.6in the 900–1100cm−1interval.It is gratifying to note how well the integrated intensities at800–970cm−1as function of time(Fig.7) correlate with the quantitative X-ray diffraction study on C3S hydration by Taylor et al.[45],who interpreted their results to imply C-S-H formation.The fact that the growth of the hump feature at970–1100cm−1follows the C3S dissolution process implies that the signature of polymeric silica indeed corresponds to C-S-H formation.It can be noted how the formation of polymerized silica(970–1100cm−1) is correlated in time with an increased incorporation of water in the structure as seen in the absorption interval at1500–1700cm−1.This supports further that calcium silica hydrate C-S-H is a major product formed upon early Portland cement hydration,as C-S-H consists of polymerized silica and calcium ions with water incorporated.It becomes interesting to attempt to correlate the materials conversion observed with DR-FTIR with morphological changes as seen with SEM.The acceleration phase of C-S-H formation starts somewhere between120and180min(Figs.6and7).Simulta-neously a growth of a needle-like phase is developed on the cement particles(Fig.8).This phase has been attributed to C-S-H in previous studies of alite,C3S,where no other phase than C-S-H and portlandite(Ca(OH)2)is formed[25,46].It is seen in Fig.1that the setting starts after180min,and that it is completed after240min. Since the conversion of the sulphates occurs during thefirst30min, the possibility that the needle-like phase is due to sulphates is ruled out.However,the acceleration phase of C-S-H formation(vide supra) occurs on the same time scale as the formation of the needle-like phase seen by SEM as well as that of the setting process.An identification of C-S-H as the phase responsible for the setting of the Portland cement is thus arrived at.Support is produced to the claim that C-S-H is responsible for the initial development of strength in Portland cement pastes.Also,it is suggested that C-S-H is formed continuously during hydration and in particular so prior to the setting.This implies that the actual setting is due to coalescence of clinker grains and that it is associated with the formation of sufficient amounts of C-S-H,to increase friction and bridge the inter-grain distances.The presentfindings are consistent with those of Chen and Odler [43],who reach the conclusion that setting in ordinary Portland cement is mainly due to the formation of C-S-H as long as the ratio between sulphates and C3A+C4AF is balanced,else“false setting”results due to the formation of ettringite or monosulphate.5.ConclusionsCement is a complex material,and its hydration possibly provides additional complexity.Indeed,as yet no single method exists which completely determines all chemical reactions taking place in a cement structure from the mixing and onward.Therefore several comple-mentary techniques must be used.In the present study,signatures of early setting of an untampered limestone Portland cement were extracted by correlating DR-FTIR,SEM, and Vicat measurements.The objective of this paper was to demonstrate how diffuse reflectance Fourier transform infrared spectroscopy in combination with freeze-drying may add a piece of the puzzle regarding material conversion during the very early stages of cement hydration, down to fractions of a minute.Whereas setting of each unique cement must be addressed separately,a method to monitor the material conversions during early hydration has been presented.Summarizing:•the time evolution of the sulphate chemistry displays very rapid crystallization followed by a slow recrystallization phase,which is completed within approximately30min;•the appearance of a broad absorption hump at970–1100cm−1after 60min of hydration is due to polymeric silica.It is correlated with the development of water bending vibration bands(1500–1700cm−1). This implies the formation of calcium silicate hydrate,C-S-H;•time dependent changes in morphology due to the hydration process,as monitored with SEM,were found to correlate with the DR-FTIR signatures of C-S-H formation,•the growth of a dip feature in the spectra at800–970cm−1,identified as the dissolution of C3S Alite,correlates with the formation of C-S-H.Vicat setting begins after180min and is completed after240min. This occurs well after the sulphate reactions have stopped.However, the C-S-H formation in the acceleration phase of C3S dissolution, displays the same time dependence as that of the setting process.The observations support the understanding of setting in terms of coalescing C-S-H coated Portland cement particles.AcknowledgementsThe support from the Knowledge foundation(KK stiftelsen),the Swedish Research Council,and Eka Chemicals Inc.,Bohus is gratefully acknowledged,as well as valuable discussions with Inger Jansson.438R.Ylmén et al./Cement and Concrete Research39(2009)433–439。
外文翻译(中文)利用IR,SEM和维尔卡技术检测硅酸盐水泥的早起水化及其制备过程
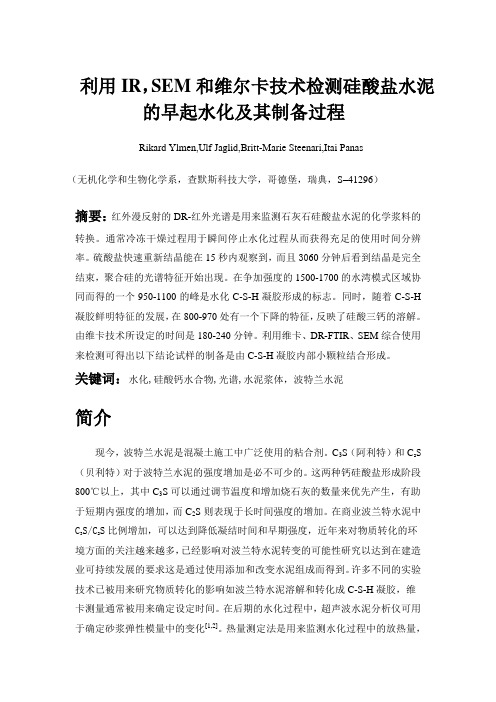
利用IR,SEM和维尔卡技术检测硅酸盐水泥的早起水化及其制备过程Rikard Ylmen,Ulf Jaglid,Britt-Marie Steenari,Itai Panas(无机化学和生物化学系,查默斯科技大学,哥德堡,瑞典,S–41296)摘要:红外漫反射的DR-红外光谱是用来监测石灰石硅酸盐水泥的化学浆料的转换。
通常冷冻干燥过程用于瞬间停止水化过程从而获得充足的使用时间分辨率。
硫酸盐快速重新结晶能在15秒内观察到,而且3060分钟后看到结晶是完全结束,聚合硅的光谱特征开始出现。
在争加强度的1500-1700的水湾模式区域协同而得的一个950-1100的峰是水化C-S-H凝胶形成的标志。
同时,随着C-S-H凝胶鲜明特征的发展,在800-970处有一个下降的特征,反映了硅酸三钙的溶解。
由维卡技术所设定的时间是180-240分钟。
利用维卡、DR-FTIR、SEM综合使用来检测可得出以下结论试样的制备是由C-S-H凝胶内部小颗粒结合形成。
关键词:水化,硅酸钙水合物,光谱,水泥浆体,波特兰水泥简介现今,波特兰水泥是混凝土施工中广泛使用的粘合剂。
C3S(阿利特)和C2S (贝利特)对于波特兰水泥的强度增加是必不可少的。
这两种钙硅酸盐形成阶段800℃以上,其中C3S可以通过调节温度和增加烧石灰的数量来优先产生,有助于短期内强度的增加,而C2S则表现于长时间强度的增加。
在商业波兰特水泥中C3S/C2S比例增加,可以达到降低凝结时间和早期强度,近年来对物质转化的环境方面的关注越来越多,已经影响对波兰特水泥转变的可能性研究以达到在建造业可持续发展的要求这是通过使用添加和改变水泥组成而得到。
许多不同的实验技术已被用来研究物质转化的影响如波兰特水泥溶解和转化成C-S-H凝胶,维卡测量通常被用来确定设定时间。
在后期的水化过程中,超声波水泥分析仪可用于确定砂浆弹性模量中的变化[1,2]。
热量测定法是用来监测水化过程中的放热量,而X射线衍射[8-13],核磁共振[14-16]和傅里叶变换红外光谱,红外光谱用于获取化学信息。
外文翻译(中文)掺有粉煤灰、硅灰的硅酸盐水泥的热分析和微观结构
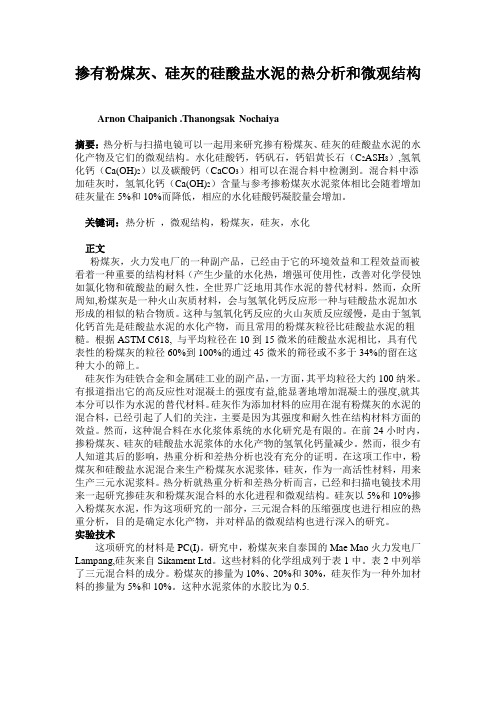
掺有粉煤灰、硅灰的硅酸盐水泥的热分析和微观结构Arnon Chaipanich .Thanongsak Nochaiya摘要:热分析与扫描电镜可以一起用来研究掺有粉煤灰、硅灰的硅酸盐水泥的水化产物及它们的微观结构。
水化硅酸钙,钙矾石,钙铝黄长石(C2ASH8),氢氧化钙(Ca(OH)2)以及碳酸钙(CaCO3)相可以在混合料中检测到。
混合料中添加硅灰时,氢氧化钙(Ca(OH)2)含量与参考掺粉煤灰水泥浆体相比会随着增加硅灰量在5%和10%而降低,相应的水化硅酸钙凝胶量会增加。
关键词:热分析,微观结构,粉煤灰,硅灰,水化正文粉煤灰,火力发电厂的一种副产品,已经由于它的环境效益和工程效益而被看着一种重要的结构材料(产生少量的水化热,增强可使用性,改善对化学侵蚀如氯化物和硫酸盐的耐久性,全世界广泛地用其作水泥的替代材料。
然而,众所周知,粉煤灰是一种火山灰质材料,会与氢氧化钙反应形一种与硅酸盐水泥加水形成的相似的粘合物质。
这种与氢氧化钙反应的火山灰质反应缓慢,是由于氢氧化钙首先是硅酸盐水泥的水化产物,而且常用的粉煤灰粒径比硅酸盐水泥的粗糙。
根据ASTM C618, 与平均粒径在10到15微米的硅酸盐水泥相比,具有代表性的粉煤灰的粒径60%到100%的通过45微米的筛径或不多于34%的留在这种大小的筛上。
硅灰作为硅铁合金和金属硅工业的副产品,一方面,其平均粒径大约100纳米。
有报道指出它的高反应性对混凝土的强度有益,能显著地增加混凝土的强度,就其本分可以作为水泥的替代材料。
硅灰作为添加材料的应用在混有粉煤灰的水泥的混合料,已经引起了人们的关注,主要是因为其强度和耐久性在结构材料方面的效益。
然而,这种混合料在水化浆体系统的水化研究是有限的。
在前24小时内,掺粉煤灰、硅灰的硅酸盐水泥浆体的水化产物的氢氧化钙量减少。
然而,很少有人知道其后的影响,热重分析和差热分析也没有充分的证明。
在这项工作中,粉煤灰和硅酸盐水泥混合来生产粉煤灰水泥浆体,硅灰,作为一高活性材料,用来生产三元水泥浆料。
建筑材料外文翻译--普通硅酸盐水泥中掺入硅灰和石膏对水化反应的影响
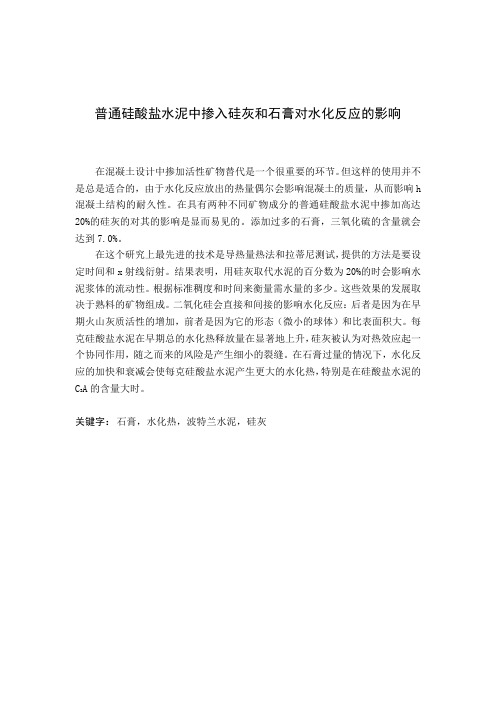
普通硅酸盐水泥中掺入硅灰和石膏对水化反应的影响在混凝土设计中掺加活性矿物替代是一个很重要的环节。
但这样的使用并不是总是适合的,由于水化反应放出的热量偶尔会影响混凝土的质量,从而影响h 混凝土结构的耐久性。
在具有两种不同矿物成分的普通硅酸盐水泥中掺加高达20%的硅灰的对其的影响是显而易见的。
添加过多的石膏,三氧化硫的含量就会达到7.0%。
在这个研究上最先进的技术是导热量热法和拉蒂尼测试,提供的方法是要设定时间和x射线衍射。
结果表明,用硅灰取代水泥的百分数为20%的时会影响水泥浆体的流动性。
根据标准稠度和时间来衡量需水量的多少。
这些效果的发展取决于熟料的矿物组成。
二氧化硅会直接和间接的影响水化反应:后者是因为在早期火山灰质活性的增加,前者是因为它的形态(微小的球体)和比表面积大。
每克硅酸盐水泥在早期总的水化热释放量在显著地上升,硅灰被认为对热效应起一个协同作用,随之而来的风险是产生细小的裂缝。
在石膏过量的情况下,水化反应的加快和衰减会使每克硅酸盐水泥产生更大的水化热,特别是在硅酸盐水泥的CA的含量大时。
3关键字:石膏,水化热,波特兰水泥,硅灰水泥的研究范围从个人分析到每个组件阶段,研究高度复杂的系统以及他们所有的变量,联合研究硅酸盐熟料组件与石膏(CaSO4.2H2O)的交互作用来测量凝结时间,例如,已经发现:• 在硅酸盐水泥中C3A和C4A都会与石膏发生反应,但是由于C3A更容易与石膏反应,所以水泥中大量的C3A被很快反应掉。
石膏的用量会受到所设置的凝结时间的限制,导致所形成的钙矾石会比预期的要少。
•石膏也加快了钙硅酸盐的水化速率,同时在水花过程中争夺硫酸根离子,虑到大量的硫酸盐包含在CSH凝胶中。
2至6%的石膏在加速水化硅酸三钙的形成,2%至4%在促进水泥石的水化。
石膏含量高有助于形成大量的钙矾石,然而这会阻止凝结时间和硬化,这些明显的变化是因为微观结构的膨胀和开裂。
石膏含量低,反过来,会形成更多的硫酸盐,降低了水化反应的强度,从而阻碍了C3A的的分解。
水泥的历史中英文对照外文翻译文献
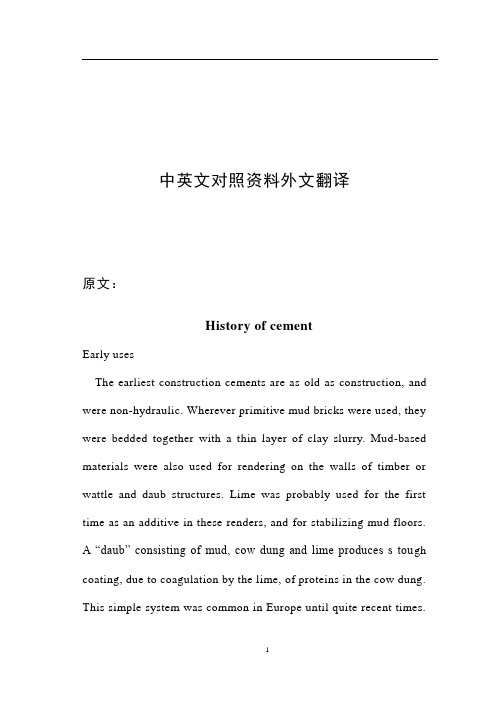
中英文对照资料外文翻译原文:History of cementEarly usesThe earliest construction cements are as old as construction, and were non-hydraulic. Wherever primitive mud bricks were used, they were bedded together with a thin layer of clay slurry. Mud-based materials were also used for rendering on the walls of timber or wattle and daub structures. Lime was probably used for the first time as an additive in these renders, and for stabilizing mud floors.A “daub” consisting of mud, cow dung and lime produces s tou gh coating, due to coagulation by the lime, of proteins in the cow dung. This simple system was common in Europe until quite recent times.With the advent of fired bricks, and their use in larger structures, various cultures started to experiment with higher-strength mortars based on bitumen (in Mesopotamia), gypsum (in Egypt) and lime (in many parts of the world).It is uncertain where it was first discovered that a combination of hydrated non-hydraulic lime and a pozzolan produces a hydraulic mixture, but concrete made from such mixtures was first used on a large scale by the Romans. They used both natural pozzolans ( trass or pumice) and artificial pozzolans (ground brick or pottery) in these concretes. Many excellent examples of structures made from these concretes are still standing, notably the huge monolithic dome of the Pantheon in Rome. The use of structural concrete disappeared in medieval Europe, although weak pozzolanic concretes continued to be used as a core fill in stone walls and columns.Modern cementModern hydraulic cements began to be developed from the start of the Industrial Revolution (around 1800), driven by three main needs:Hydraulic renders for finishing brick buildings in wet climates.˙Hydraulic mortars for masonry construction of harbor works etc, in contact with sea water.˙Development of strong concretes.In Britain particularly, good quality building stone became ever more expensive during a period of rapid growth, and it became a common practice to construct prestige buildings from the new industrial bricks, and to finish them with a stucco to imitate stone. Hydraulic limes were favored for this, but the need for a fast set time encouraged the development of new cements. Most famous among these was Parker’s “Roman cement.” This was development by James Parker in the 1780s, and finally patented in 1796. It was, in fact, nothing like any material used by the Romans, but was a “Natural cement” made by burning septaria-nodules that are found in certain clay deposits, and that contain both clay minerals and calcium carbonate. The burnt nodules were ground to a fine powder. This product, made into a mortar with sand, set in 5—15 minutes. The success of “Roman cement” led other manufacturers to develop rival products by burning artificial mixtures of clay and chalk.John Smeaton made an important contribution to the development of cements when he was planning the construction of the third Eddystone Lighthouse (1755-9) in the English Channel. He needed a hydraulic mortar that would set and develop some strength in the twelve hour period between successive high tides. He performed an exhaustive market research on the available hydraulic limes, visiting their production sites, and noted that the “hydraulicity” of the lime was directly related to the clay content of the limestone from which it was made. Smeaton was a civil engineer by profession, and took the idea no further. Apparently unaware of Smeaton’s work, the same principle was identified by Louis Vicat in the first decade of the nineteenth century. Vicat went on to devise a method of combining chalk and clay into an intimate mixture, and, burning this, produced an “artificial cement” in 1817. James Frost, working in Britain, produced what he called “British cement” in a similar manner around the same time, but did not obtain a patent until 1822. In 1824, Joseph Aspdin patented a similar material, which he called Portland cement, because the render made from it was in color similar to the prestigious Portland stone.All the above products could not compete with lime/pozzolan concretes because of fast-setting (giving insufficient time for placement) and low early strengths(requiring a delay of many weeks before formwork could be removed). Hydraulic limes “natural” cements and “artificial” c ements all rely upon their belite content for strength development. Belite develops strength solely. Because they were burned at temperatures below 1259℃, they contained no alite, which is responsible for early strength in modern cements. The first cement to consistently contain alite was that made by Joseph Aspdin’s son William in the early 1840s. This was what we call today “modern” Portland cement. Because of the air of mystery with which William Aspdin surrounded his product, others (e.g.Vicat and I C Johnson) have claimed precedence in this invention, but recent analysis of both his concrete and raw cement have shown that William Aspdin’s products made at Northfleet, Keen was a true alite-based cement. However, Aspdin’s methods were “rule-of-thumb”:Vica t is responsible for establishing the mix in the kiln.William Aspdin’s innovation was counter-intuitive for manufacturers of “artificial cement”, because they required morelime in the mix ( a problem for his father ), because they required a much higher kiln temperature ( and therefore more fuel ) and because the resulting clinker was very hard and rapidly wore down the millstones which were the only available grinding technology of the time. Manufacturing costs were therefore considerably higher, but the product set reasonably slowly and developed strength quickly, thus opening up a market for use in concrete. The use of concrete in construction grew rapidly from 1850 onwards, and was soon the dominant use for cements. Thus Portland cement began its predominant role.译文:水泥的历史早期应用最早的建筑水泥是和建筑一起起步的,但是这种水泥在水中不会硬化。
- 1、下载文档前请自行甄别文档内容的完整性,平台不提供额外的编辑、内容补充、找答案等附加服务。
- 2、"仅部分预览"的文档,不可在线预览部分如存在完整性等问题,可反馈申请退款(可完整预览的文档不适用该条件!)。
- 3、如文档侵犯您的权益,请联系客服反馈,我们会尽快为您处理(人工客服工作时间:9:00-18:30)。
英文翻译
专业材料科学与工程
学生姓名
班级材料 1班
学号
指导教师
完成日期
原文
.
翻译:
硅酸盐水泥的化学成分
硅酸盐水泥是通过煅烧一些精细混合在一起的由如碳酸钙或硫酸钙、铝硅酸盐、粘土或红土的这些材料组成的石灰石,按一定明确的预定比例,再冷却烧结后的产物,在水泥技术上称之为“熟料”,另外加一定比例的石膏研磨制成的。
硅酸盐水泥看起来很平凡的材料,但不能错误地认为是每种类型都是有相同的明确的化学过程,制造任何种类的硅酸盐水泥都是有需要精细的化学生产,因为事实上,至少有三十种化工单元操作是牵涉在水泥生产中的。
所有的硅酸盐水泥都是由石灰石制造的,只有极少数的工厂是以产品碳酸钙产品、污泥或石膏或酸酐为主要原料。
氧化物的组成成分和限制以及复合硅酸盐水泥熟料(除白水泥熟料及油井水泥熟料)的化合物组成范围在表1中给出。
表1
工厂生产的熟料的确切的化学组成成分将取决于原材料和可用燃料的种类。
钙质原材料可能是石灰石、钙质海砂、贝壳、珊瑚或碳酸钙副产品;泥质原材料可能是粘土、页岩,有时可能添加很小比例的铁矿石或砂岩来提高原混合材料中的化学成分到确切的预定成分。
使用的燃料可能是煤、石油或天然气。
必须记住的是当设计原混合生料时,需考虑在燃烧过程中添加一些存在部分灰的煤到水泥原混合材料中以及提高它的化学组成成分。
下面给出一个设计硅酸盐水泥熟料的经典例子。
熟料必须有如下的限制:
表2
这种类型的熟料是制造普通硅酸盐水泥的典范。
(a)C3S在硅酸盐水泥形成中提供主要强度,它有助于形成早期强度;另一方面,C2S有助于形成后期强度。
然而,C3S含量很高的熟料,在目前工业上可用的传统燃烧设备中是不容易燃烧的。
因此在普通硅酸盐水泥中C3S的比例保持在40%~50%之间,C2S在25%~35%之间。
在快速硬化的水泥和油井水泥中,C3S的比例必须保持在50%以上,大约在50%~60%,这样才会达到较高的早期强度。
为了能使熟料完全燃烧,有必要在原混合物中添加一些助熔剂;Al2O3和Fe2O3可作为助熔剂。
在燃烧中,存在于原混合物中的Al2O3和Fe2O3首先形成C4AF,C3A在水化过程中产生更多的热量,水泥中较高成分的C3A使得抗硫酸性能变弱。
因此,在中等热量硅酸盐水泥中C3S的含量稍低些,C3A的含量应低于8%。
在抗硫酸盐水泥中C3S的含量可以和普通硅酸盐水泥中一样高,但必须保持在5%一下。
在低热量水泥中C3S和C3A的含量都应该尽可能得低一些,大约分别在30%和60%。
在之前提到的油井水泥中,C3S的含量必须保持在50%以上,但是C3A的含量应该在20一下。
在白色水泥中Fe2O3的含量必须在0.4%以下。
(b) 因此可以看出,制造以上任何种类的水泥,首先必须决定水泥的复合组成,从计算出的氧化物成分可以看出。
在氧化物成分的因素中,SiO2/R2O3、Al2O3/Fe2O3、L.S.F,和S.S.F.已经被确认。
这些因素对生料的易烧性有很大影响。
在正确设计的由CaO、SiO2、Al2O3、Fe2O3和MgO组成的混合原料中,在燃烧过程中,所有的Fe2O3和一部分Al2O3首先和CaO形成C4AF;剩下的Al2O3和一部分CaO形成C3A;C4AF和C3A作为作为通量形成硅酸盐。
然后所有的SiO2
存在于原混合物中和一部分CaO来形成C2S,一些CaO仍没被组合。
这些没被组合的CaO然后和一些已形成的C2S一起形成C3S(最终目标化合物)。
在一个正确预期的原混合物中和目前可能的燃烧条件下,熟料中不应有游离氧化钙的存在;但实际上总是有0.5%到2.0%的游离氧化钙存在。
L.S.F(石灰饱和因子)的重要性在于考虑到SiO2、Al2O3、Fe2O3和CaO结合在一起的力量这一点。
在硅酸盐水泥中L.S.F的含量应在0.66到1.02,越高,接近于极限值,越好。
在孰料中如果L.S.F的含量接近于1.0,熟料就很难完全燃烧,特别是对于印度水泥工业中这种类型的可燃煤,最好保持在0.9左右。
SiO2/R2O3这个因素是熟料中衡量的通量,越低(接近于极限值),越容易燃烧。
含量保持在2.0在3.0之间;经过讨论发现在熟料中2.41是一个理想值。
这样MgO必然存在于水泥混合原料中。
一般MgO不和水泥化合物结合在一起,但是起到熔合作用。
另一方面,有个不好的影响,在超高温下燃烧熟料中的镁石晶体时MgO难以形成;在过去几年里这些方镁石晶体水合物在水化时很慢。
因此熟料中MgO如果超过规范中最大值时,水化将不完全。
所以在印度硅酸盐水泥规范中,MgO的最大含量限制在6%。
以Na2O、K2O和SO3形式存在的碱在熟料中小于1%。
在一些水泥混合原料中很少存在P2O5 n2O3、氯化物和氟化物。
对于硅酸盐水泥的化学成分已经做了简要的讨论。
被认为是,硅酸盐水泥本质上是由不同比例的硅酸三钙、硅酸二钙、铝酸三钙和磷酸三钙组成的;再添加一些石膏来控制凝结时间;增加水使得化合物的水化提供水泥凝结和硬化的性能。
这些化学反应包括水泥的凝结和硬化是非常复杂的,有些反应很快,有些很慢。
各种类型的硅酸盐水泥和混合水泥的基本原则(总而言之)是“形成的不可逆的凝胶体和悬浮在液相上的凝结的细小固相形成了两种不同的网络结构,凝固和结晶,以及两个结晶凝结在一起形成网络结构。
”这种网络的一个特点是,他们表现出触变性,或者是粘度的变化,这种变化不是因为时间或者是温度的变化。
在水泥中加水,作用在水泥颗粒上,形成水化硅酸钙超饱和水合物凝胶,像大量的微小晶体沉淀。
水通过形成的表面膜进入水泥颗粒的核心,水化率一开始很快,后来逐渐慢下来。
没有水化的水泥和水首先形成塑性体,接着,由水化硅酸钙组成的细小晶体颗粒的凝胶和由水化钙质、水化铝酸钙和由硫铝酸钙同时形成的大于胶体尺寸的结晶产物。
接着还有部分脱水产品和一些稳定形成的凝胶。
.
从塑性体到同时生成的晶体产物的变化发生在水泥浆体的凝结过程中,水泥浆体的硬化归功于凝胶中大量增长的晶体。
因此,水泥浆体的凝结变化是由于晶体凝结的网络结构或多或少的触变性质的发展;水泥浆体的硬化变化是由于更加强大的不可逆转的晶体结构的发展。
在水泥凝结和硬化过程中,添加的石膏作为一种缓凝剂起着很重要的作用。
代表着通过形成钙磺胺-铝酸盐来制造各种不同的石灰水泥化合物的速度。
因此,凝结和硬化的水泥本质上是由水化硅酸钙浆体和铝酸三钙浆体组成的,这两个不同组成的浆体都取决于水泥的化学成分。
在硬化的水泥中或多或少地存在这些化合物,使得水泥浆有不同的性质,如中等强度,较高的早期强度,较高的终极强度,低的水化热,更好的抗硫酸性能等等。
在以上几行中,硅酸盐水泥和混合水泥浆体的凝结和硬化的原则已经简单明了地阐述了。
进一步的细节需要对水泥浆体水化的更深层的研究。