外浮顶罐故障分析
探讨外浮顶原油储罐的热能损失原因分析及对策
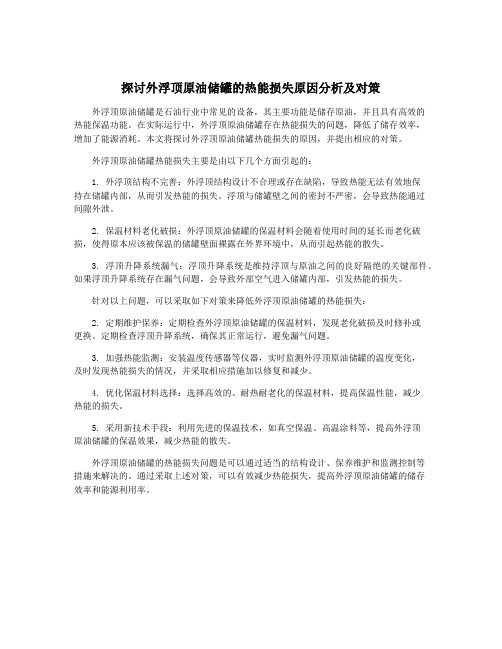
探讨外浮顶原油储罐的热能损失原因分析及对策外浮顶原油储罐是石油行业中常见的设备,其主要功能是储存原油,并且具有高效的热能保温功能。
在实际运行中,外浮顶原油储罐存在热能损失的问题,降低了储存效率,增加了能源消耗。
本文将探讨外浮顶原油储罐热能损失的原因,并提出相应的对策。
外浮顶原油储罐热能损失主要是由以下几个方面引起的:1. 外浮顶结构不完善:外浮顶结构设计不合理或存在缺陷,导致热能无法有效地保持在储罐内部,从而引发热能的损失。
浮顶与储罐壁之间的密封不严密,会导致热能通过间隙外泄。
2. 保温材料老化破损:外浮顶原油储罐的保温材料会随着使用时间的延长而老化破损,使得原本应该被保温的储罐壁面裸露在外界环境中,从而引起热能的散失。
3. 浮顶升降系统漏气:浮顶升降系统是维持浮顶与原油之间的良好隔绝的关键部件。
如果浮顶升降系统存在漏气问题,会导致外部空气进入储罐内部,引发热能的损失。
针对以上问题,可以采取如下对策来降低外浮顶原油储罐的热能损失:2. 定期维护保养:定期检查外浮顶原油储罐的保温材料,发现老化破损及时修补或更换。
定期检查浮顶升降系统,确保其正常运行,避免漏气问题。
3. 加强热能监测:安装温度传感器等仪器,实时监测外浮顶原油储罐的温度变化,及时发现热能损失的情况,并采取相应措施加以修复和减少。
4. 优化保温材料选择:选择高效的、耐热耐老化的保温材料,提高保温性能,减少热能的损失。
5. 采用新技术手段:利用先进的保温技术,如真空保温、高温涂料等,提高外浮顶原油储罐的保温效果,减少热能的散失。
外浮顶原油储罐的热能损失问题是可以通过适当的结构设计、保养维护和监测控制等措施来解决的。
通过采取上述对策,可以有效减少热能损失,提高外浮顶原油储罐的储存效率和能源利用率。
探讨外浮顶原油储罐的热能损失原因分析及对策

探讨外浮顶原油储罐的热能损失原因分析及对策外浮顶原油储罐是储存原油的重要设备,其设计和运行状态直接关系到原油的质量和安全。
在长期使用过程中,人们发现外浮顶原油储罐存在热能损失的情况,这不仅会影响原油的质量,还会导致能源浪费和环境污染。
本文将对外浮顶原油储罐的热能损失原因进行深入分析,并提出有效的对策,以期减少热能损失,保障储罐的正常运行。
一、热能损失原因分析1. 储罐结构设计不合理外浮顶原油储罐通常由钢板焊接而成,而钢板的导热系数较高,使得储罐内外温度差异较大,导致热能损失增加。
一些旧式储罐的设计可能存在漏风或保温不足等问题,也会导致热能损失增加。
2. 储罐设备老化随着储罐设备的长时间使用,其保温层可能会老化变薄、龟裂,导致保温效果不佳,从而造成热能损失。
储罐内部设备也可能存在故障或损坏,导致保温性能下降,加剧热能损失。
3. 天气条件影响恶劣的天气条件如寒冷、风暴等都会增加外浮顶原油储罐的热能损失,特别是在寒冷地区,由于外界温度低,使得原油储罐的保温更为重要。
4. 维护保养不到位外浮顶原油储罐的维护保养决定了其运行状态,一些因疏忽而造成的损坏或故障都会导致热能损失增加。
保温层受到损坏或破损,储罐设备没有及时维修等均可能导致热能损失。
二、对策建议针对储罐结构设计不合理的问题,可以考虑采用新型隔热材料作为保温层,以降低导热系数,减少内外温度差异。
可以加强储罐的密封性,减少风雨天气对储罐的影响。
2. 定期检查维护对储罐设备进行定期检查维护,包括保温层、设备的完好性等。
一旦发现问题,及时进行修复或更换,以保证储罐设备的正常运行状态。
3. 加强保温措施在恶劣的天气条件下,可以加强对储罐的保温措施,例如增加保温层厚度,使用更好的保温材料等,以减少外界温度对储罐的影响。
4. 推广新技术推广新型的保温材料和保温技术,如真空绝热技术、气凝胶技术等,以提高储罐的保温性能,降低热能损失。
5. 完善管理制度建立完善的储罐管理制度,包括定期检查、维护计划、应急预案等,以确保储罐设备的安全稳定运行。
浮顶罐沉盘、卡盘故障浅析

静设 备
P o—工 备 术28Technol3 石r化 emialEqui0nt9)2・ 油 Ch设c技 ,023・gy ,( o e t p me
浮 顶 罐 沉 盘 、 盘 故 障浅 析 卡
赵 红 海 程 丽 芬 赵 东 海 。 , ,
一
旦 失去 浮 力后 支柱 却不 能 同时承受 浮 盘重量 和
漏人储 液 重量 之 和 。 3 1 支 柱 的失稳 .
浮盘 负 重下 降 ( 常是 发 现浮盘 上有 油 , 行 通 进
1 ×1 m。 浮顶 储罐 的沉 盘 事故 。 O 0 外
2 导 向柱 式浮 顶罐 沉盘 、 盘后 的 形态 卡
内浮 顶罐 浮船 或浮 盘 , 里通 称 为“ 这 浮盘 ” 。 沉盘 和卡 盘是 浮 盘 储 罐 独 有 的、 常 危 险 的 非 设 备故 障 。对设 备造 成 严 重 损 坏 、 内物 质 不 易 罐 清除 、 浮舱 内充 人 了介质 、 聚胺酯 密封 结构 体 内吸 附 了油 品等 , 易造 成火 灾 事故 ; 盘后状 态 不稳 极 卡 定 , 盘 随 时 坠 落 ; 复 储 罐 时 需 要 动 用 大 型 设 浮 修 备 , 工 困难 ; 着储 罐 的大 型 化 , 施 随 因检修 停 运 及
够避免沉卡故障的 。 关键词 : 盘 ; 盘 ; 向柱 ; 沉 卡 导 支柱
中 图 分 类 号 : 9 9 文 献标 识码 : 文 章 编 号 : 0 68 0 ( 0 8 0 — 0 30 TE 6 B 1 0 - 8 5 2 0 ) 30 2 -4
本文讨 论 的 是具 有 导 向 柱式 结 构 的外 浮 顶 、
外付倒 罐 操作 ) , 柱 接触 罐 底 、 时 支 介质 离 开 浮 盘
浮顶油罐沉盘原因分析及预防措施
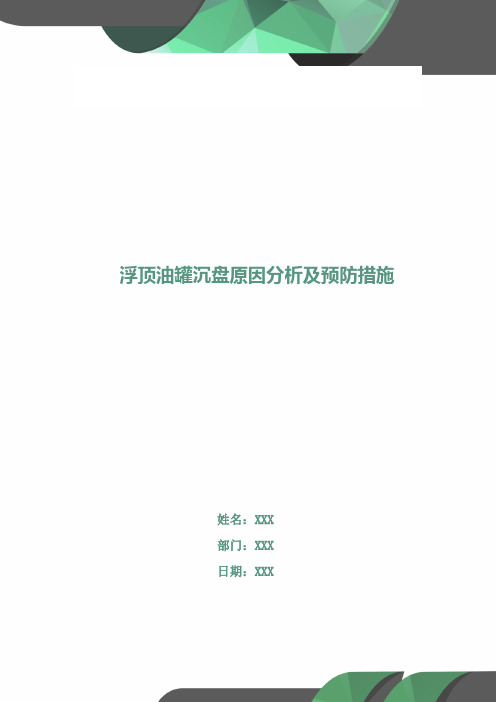
浮顶油罐沉盘原因分析及预防措施姓名:XXX部门:XXX日期:XXX浮顶油罐沉盘原因分析及预防措施1前言浮顶油罐在油库中应用十分广泛,浮顶是一覆盖在油面上,并随油面升降的盘状结构物,又称浮盘。
由于浮顶与油面间几乎不存在气体空间,因而可以极大地减少油品损耗,同时在增加油品储存安全性和保护环境等方面也起到了明显的作用,更可获得可观的经济效益。
浮顶油罐分为外浮顶和内浮顶两种,外浮顶罐是一种全敞口容器,盘状浮顶随油面升降;内浮顶是装有浮盘的拱顶罐。
沉盘事故是浮顶油罐生产作业时非常忌讳的严重恶性设备事故之一,且发生事故后的复原处理十分困难。
该类事故的发生,一方面反映了设计、施工、管理等方面的严重缺陷,另一方面又造成大量油品泄漏,严重影响生产,污染环境,并构成重大火灾隐患。
由于结构等方面的原因,内浮盘沉盘是该类油罐的主要事故,人们比较重视;而因为外浮顶油罐沉盘事故在油品储运事故中较为少见,人们没有给予足够的重视。
2外浮顶油罐浮盘故障资料将某罐区油品车间1997~2005年外浮顶油罐浮盘故障进行统计,在12起浮盘故障中,1起因罐体变形卡盘,1起因浮盘滑梯损坏发生沉盘,2起因来油串气卡盘,4起因浮盘顶中央排水不畅险些造成沉盘,1起因浮盘腐蚀穿孔漏油发生沉盘,3起因浮盘腐蚀穿孔漏油不得不停工。
这表明,日常对浮顶罐及其附件设施的检查和维护十分重要,同时如G104#、G105#、G106#罐使用已有20多年,期间也进行过多次大修,浮舱下底板已严重减薄,该油品车间外浮顶油罐在运行过程中,存在着不少隐患,如果不能及时发现和消除事故隐患,很可能再次发生沉盘事故,第 2 页共 8 页从而威胁到罐区安全生产,也会造成较大的经济损失。
3外浮顶油罐沉盘事故原因分析3.1浮盘和外浮顶油罐的结构特点浮盘的结构形式有双盘式和单盘式两种。
双盘式浮盘是由直径比油罐内径小400mm的顶板、底板和周边的竖向边缘环板焊接而成的,顶、底板之间设有若干竖向安装的环向隔板和径向隔板,将浮盘分隔成若干互不连通的隔舱,以免底板出现局部泄漏时液体漫流到整个浮盘内,导致浮盘沉没。
浮顶储罐事故检修案例

浮顶储罐事故检修案例浮顶储罐是一种常见的储存液体的设备,但由于使用环境恶劣、操作不当等原因,很容易发生事故。
为了保障生产安全和设备的正常运行,定期对浮顶储罐进行检修是非常必要的。
下面列举了一些浮顶储罐事故检修案例,以供参考。
1. 液位计故障导致溢油事故某石油化工厂的浮顶储罐发生了一起溢油事故,造成了严重的环境污染和财产损失。
经调查,事故原因是液位计故障,导致操作人员无法准确监控液位,最终造成溢油。
为了解决这个问题,厂方对所有液位计进行了检修和更换,并增加了液位告警系统,提高了监控的准确性。
2. 漏油检修工作不彻底引发二次事故某化工厂的浮顶储罐在检修过程中发生了漏油事故。
原本检修工作应该彻底清洗和修复罐体漏油点,但由于工期紧张和粗心大意,有几个漏油点没有得到妥善处理。
不久之后,这些漏油点再次出现问题,导致了二次事故的发生。
为了避免类似事故再次发生,厂方加强了检修工作的质量控制,严格要求工作人员按照程序进行作业,并增加了监督和检查的力度。
3. 腐蚀导致罐体漏油某石化企业的浮顶储罐在使用过程中出现了罐体漏油的问题。
经过检修发现,罐体表面存在严重的腐蚀,导致了漏油。
为了解决这个问题,企业采用了防腐涂料进行修复,并增加了定期检查和维护的频率,确保罐体的完整性和安全性。
4. 浮顶沉降导致储罐变形某化工厂的浮顶储罐在使用一段时间后出现了沉降问题,导致了储罐的变形。
经过检修发现,储罐的支撑结构存在问题,无法承受浮顶的重量,导致沉降。
为了解决这个问题,厂方对支撑结构进行了加固,并增加了浮顶的支撑点,确保了储罐的安全运行。
5. 环境温度变化导致浮顶卡死某石化企业的浮顶储罐在环境温度变化较大的情况下,出现了浮顶卡死的问题,无法正常运动。
经过检修发现,浮顶的润滑系统存在故障,导致润滑不良。
为了解决这个问题,企业对润滑系统进行了修复,并增加了定期润滑的频率,确保浮顶的灵活运动。
6. 风力过大导致浮顶脱落某港口的浮顶储罐在遭遇强风天气时,发生了浮顶脱落的事故。
浮顶油罐沉盘原因分析及预防措施
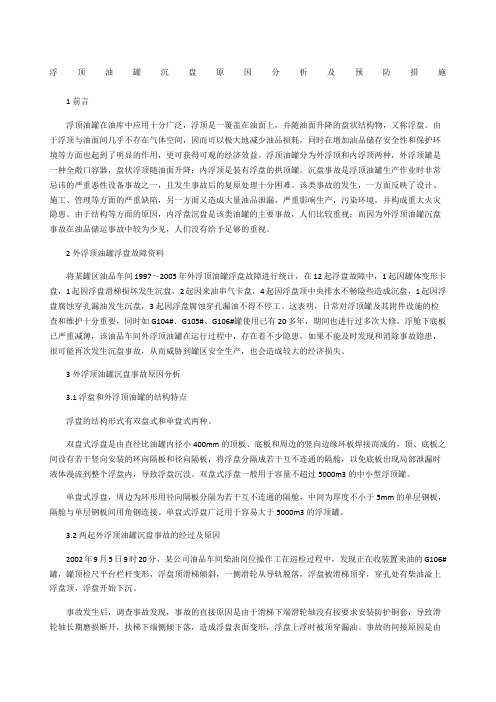
浮顶油罐沉盘原因分析及预防措施1前言浮顶油罐在油库中应用十分广泛,浮顶是一覆盖在油面上,并随油面升降的盘状结构物,又称浮盘。
由于浮顶与油面间几乎不存在气体空间,因而可以极大地减少油品损耗,同时在增加油品储存安全性和保护环境等方面也起到了明显的作用,更可获得可观的经济效益。
浮顶油罐分为外浮顶和内浮顶两种,外浮顶罐是一种全敞口容器,盘状浮顶随油面升降;内浮顶是装有浮盘的拱顶罐。
沉盘事故是浮顶油罐生产作业时非常忌讳的严重恶性设备事故之一,且发生事故后的复原处理十分困难。
该类事故的发生,一方面反映了设计、施工、管理等方面的严重缺陷,另一方面又造成大量油品泄漏,严重影响生产,污染环境,并构成重大火灾隐患。
由于结构等方面的原因,内浮盘沉盘是该类油罐的主要事故,人们比较重视;而因为外浮顶油罐沉盘事故在油品储运事故中较为少见,人们没有给予足够的重视。
2外浮顶油罐浮盘故障资料将某罐区油品车间1997~2005年外浮顶油罐浮盘故障进行统计,在12起浮盘故障中,1起因罐体变形卡盘,1起因浮盘滑梯损坏发生沉盘,2起因来油串气卡盘,4起因浮盘顶中央排水不畅险些造成沉盘,1起因浮盘腐蚀穿孔漏油发生沉盘,3起因浮盘腐蚀穿孔漏油不得不停工。
这表明,日常对浮顶罐及其附件设施的检查和维护十分重要,同时如G104#、G105#、G106#罐使用已有20多年,期间也进行过多次大修,浮舱下底板已严重减薄,该油品车间外浮顶油罐在运行过程中,存在着不少隐患,如果不能及时发现和消除事故隐患,很可能再次发生沉盘事故,从而威胁到罐区安全生产,也会造成较大的经济损失。
3外浮顶油罐沉盘事故原因分析3.1浮盘和外浮顶油罐的结构特点浮盘的结构形式有双盘式和单盘式两种。
双盘式浮盘是由直径比油罐内径小400mm的顶板、底板和周边的竖向边缘环板焊接而成的,顶、底板之间设有若干竖向安装的环向隔板和径向隔板,将浮盘分隔成若干互不连通的隔舱,以免底板出现局部泄漏时液体漫流到整个浮盘内,导致浮盘沉没。
外浮顶原油罐存在问题及改进
外浮顶原油罐存在问题及改进李伯林(中国石化股份有限公司天津分公司炼油部油品作业部,天津市300000)嗡要]近年来,国内原油储罐越来越向大型化发展,其结构型式也多为外浮顶罐。
无论是设计还是施工,都已逐步规范化。
天津石化某库区于92年建成3座3x104m3(46000x19600)外浮顶原油罐,主要用于接卸海上原油,收付油作业比较频繁,从投用至今,都不同程魔地存在一些问题。
p皂键词]浮顶罐;加热器;中央排水管;油罐密封;改进近年来,国内原油储罐越来越向大型化发展,其结构型式也多为外浮顶罐。
无论是设计还是施工,都已逐步规范化。
天津石化某库区于92年建成3座3×104m3(046000X19600)外浮顶原油罐,主要用于接卸海上原油,收付油作业比较频繁,从投用至今,都不同程度地存在一些问题。
如加热器漏油,中央排水管漏油,油罐密封损坏等问题,被迫停运检修,浪费了大量人力、物力。
现将存在问题及处理方法予以分述。
1加热器问题外浮顶原油罐的加热器原设计为管束式加热器(图1)。
该加热器由D N40无缝钢管焊接而成。
存在问题:由于蒸汽及蒸汽中夹带的腐蚀性离子对蒸汽汇总管管壁形成强大的冲刷腐蚀,该处的减薄速度大幅度提高,加之管束式允段加热器结构复杂,管子接头多,3X1O。
m。
原油罐加热器的蒸汽汇总管数量为64个,使管壁穿孔几率增加。
投用一段时间后三座罐相继出现多处穿孔,致使蒸汽回水中混入原油,既损坏设备又污染环境。
改进:将原来的管束式分段加热器改为现在的“Q”形结构,每个罐设两组盘管(D N80),每组进罐后分为双管并联绕罐内一阖(图2)。
该结构的加热器在加热面积不变的条件下有三个方面的优点:1)蒸汽汇总管的直径变大:分汽管由由57×3.5m m增至巾159X7m m,集汽管由巾108x4.5m m增至巾273×9m m。
既减缓了汽流的流速,又增加了管子壁厚,蒸汽对管壁冲刷减薄的速率降低;同时延缓了管壁被冲刷穿孔的时间,延长了蒸汽汇总管的使用寿命:2)蒸汽汇总管数量明显减少,由原来64个减至现在的4个,加热器的安全可靠性提高:3)“Q”结构的加热器,由由89X6m m的无缝钢管弯曲成形,蒸汽在弧形盘管中的流动较平缓,减少了对管壁的冲击破坏。
探讨外浮顶原油储罐的热能损失原因分析及对策
探讨外浮顶原油储罐的热能损失原因分析及对策外浮顶原油储罐是石油储运行业中常见的一种储罐类型,其具有防止储罐内油品与空气接触的作用,有效减少了揮发损失和环境污染的风险。
随着储罐使用年限的增长和环境温度变化等因素的影响,外浮顶原油储罐存在热能损失的问题。
本文将从原油储罐热能损失的原因分析和对策方案两个方面展开讨论,以期为相关行业提供参考和借鉴。
一、热能损失原因分析1. 外浮顶结构缺陷:外浮顶原油储罐的保温性能主要依赖于其结构特点,如果储罐本身存在结构缺陷,如密封不严或者保温材料老化损坏等情况,将直接导致热能的大量散失。
2. 环境温度变化:气候变暖或寒冷的环境温度变化也会对外浮顶原油储罐的热能损失产生影响,特别是在寒冷季节,温差较大,会导致储罐内外的温度差异增大,加速热能损失。
3. 保温材料老化:储罐使用年限增长,保温材料容易发生老化、开裂或者脱落等现象,导致保温效果降低,从而增加热能损失。
4. 正常操作不当:有些操作人员在进行常规维护时,未能及时检查和维护储罐的保温材料或密封情况,或者使用了不合适的维护方法,导致了热能损失的加剧。
二、对策方案1. 定期检查和维护:加强储罐的日常巡检工作,特别是密封情况和保温材料的状况,发现问题及时进行维修和更换,确保储罐的保温效果。
2. 更新和改进保温材料:选用高效保温材料或者利用新的保温技术,提高储罐的保温性能,减少热能损失。
3. 加强操作培训:对储罐操作人员进行培训,提高其对储罐保温材料和结构的认识,确保正常操作不会对储罐的保温性能造成破坏。
4. 安装辅助设备:在必要的情况下,可以考虑在储罐周围安装加热设备,或者建立遮阳设施,减少环境温度变化对储罐热能的影响。
5. 提高保温材料的质量:选择质量可靠的保温材料进行更新或更换,以确保其使用寿命和保温效果。
外浮顶原油储罐的热能损失问题是一个复杂的系统工程,需要多方面的综合对策来解决。
通过对储罐结构的加固改进、保温材料的更新和更换、操作人员的培训和技术支持等方式,可以有效降低储罐热能损失,延长其使用寿命,提高储罐的运行效率,为石油储运行业带来更多的经济和环保效益。
探讨外浮顶原油储罐的热能损失原因分析及对策
探讨外浮顶原油储罐的热能损失原因分析及对策外浮顶原油储罐是一种常用的石油储存设备,它具有良好的密封性能和大容量的储存能力。
由于外浮顶原油储罐的特殊结构,存在一定的热能损失问题。
本文将从外浮顶原油储罐的热能损失原因分析和对策两个方面进行探讨。
我们来分析外浮顶原油储罐的热能损失原因。
外浮顶原油储罐的热能损失主要来自以下几个方面:1. 密封不严:外浮顶原油储罐在长期使用后,密封性能可能会下降,导致热能的外泄。
由于外浮顶原油储罐的周边环境影响,如风力、气温等因素的变化也可能导致密封不严,进而造成能量的损失。
2. 传导传热:外浮顶原油储罐内外的温度差异会导致热能通过传导传到储罐的外表面,然后通过辐射散失到空气中。
尤其是在寒冷的冬季,传导传热是外浮顶原油储罐能量损失的重要原因。
3. 管道和设备:外浮顶原油储罐通常会与其他设备和管道连接,这些连接部位往往存在温度漏风现象。
温度漏风会导致热能的外泄,从而造成能量的损失。
外浮顶原油储罐的热能损失主要来自于密封不严、传导传热和管道设备等方面的问题。
为了减少热能损失,我们可以采取以下对策:1. 加强密封性能:定期检查和维修外浮顶原油储罐的密封装置,确保其密封性能良好。
可以使用密封材料,如橡胶垫片等,增强密封效果,从而减少能量的外泄。
2. 采取保温措施:在外浮顶原油储罐的表面覆盖保温材料,减少传导传热。
可以使用保温材料,如聚氨酯喷涂保温层等,降低外浮顶原油储罐的表面温度,减少能量的散失。
外浮顶原油储罐的热能损失问题主要来自于密封不严、传导传热和管道设备等方面的原因。
为了减少热能损失,可以采取加强密封性能、采取保温措施和加强管道设备维护等对策。
这些对策的实施不仅可以减少能量的损失,降低能源的消耗,还能提高外浮顶原油储罐的能效性能。
探讨外浮顶原油储罐的热能损失原因分析及对策
探讨外浮顶原油储罐的热能损失原因分析及对策外浮顶原油储罐是石油储存系统中常见的一种储罐类型,它利用浮顶设备来与储罐内的原油形成一层隔离空气,以减少原油蒸发和氧化。
即使采用了外浮顶,原油储罐的热能损失仍然是一个无法忽视的问题。
本文将探讨外浮顶原油储罐的热能损失原因分析及对策。
一、热能损失原因分析1.1 储罐结构设计不合理外浮顶原油储罐通常采用双层罐体结构,内层为储存原油的容器,外层为浮顶设备的支撑结构。
而对于一些结构设计不合理的储罐,内外层材料之间的隔热层不够有效,导致热传导效果较差,从而增加了热能损失。
1.2 浮顶设备密封不严外浮顶原油储罐中的浮顶设备需要与罐壁形成良好的密封,以阻止外界空气的进入。
由于设备老化或安装不当等原因,浮顶设备的密封性能可能会下降,导致原油蒸发和氧化增加,热能损失也相应增加。
1.3 外界环境温度变化储罐所处的环境温度变化也会影响热能损失。
当环境温度较低时,储罐内的原油会与外界形成温度梯度,导致热能向外传导;而当环境温度较高时,储罐则会受到热辐射的影响,增加热能损失。
1.4 储罐内原油温度变化原油在储存过程中可能会因为外界温度变化、日夜温差等因素而发生温度变化,温度升高导致原油蒸发,温度降低则增加了储罐与外界的热传导。
1.5 浮顶设备运行失效由于浮顶设备是外浮顶原油储罐中的重要组成部分,一旦发生运行失效,将导致外浮顶的功能受损,无法有效隔离储罐内外的温度差异,增加了热能损失。
二、对策及解决方案2.1 加强储罐结构设计针对储罐结构设计不合理、隔热层效果不佳的问题,可以通过加强隔热材料的选择和加厚隔热层的方式来改善热传导效果,减少热能损失。
2.2 定期检查和维护浮顶设备对于浮顶设备的密封性能,需要进行定期检查和维护,确保设备保持良好的密封状态,及时更换老化的密封件,以减少原油蒸发和氧化,降低热能损失。
2.3 控制储罐内外温差对于外界环境温度和原油温度的变化,可以通过加装隔热材料或者增加外界温度调节设备来降低温度梯度,减少热传导和热辐射,降低热能损失。
- 1、下载文档前请自行甄别文档内容的完整性,平台不提供额外的编辑、内容补充、找答案等附加服务。
- 2、"仅部分预览"的文档,不可在线预览部分如存在完整性等问题,可反馈申请退款(可完整预览的文档不适用该条件!)。
- 3、如文档侵犯您的权益,请联系客服反馈,我们会尽快为您处理(人工客服工作时间:9:00-18:30)。
大型外浮顶罐的故障分析及对策李伟(长岭分公司油品处)摘要:针对长岭分公司近年来大型外浮顶罐故障增加等情况,在调查基础上,分析故障原因,指出存在问题,制定出有效措施,实现大型外浮顶罐的安全平稳运行。
关键词:原料油外浮顶罐故障分析对策近年来,随着大型外浮顶罐技术的广泛应用,石化企业原料油储罐中,大型外浮顶罐数量逐年增加,罐容量越来越大。
它具有收付和储存油品损失少、无污染和操作方便等优点。
随着大型外浮顶罐使用年限延长,运行过程中发生故障也随之增加,若维护不当或处理不及时,会给企业带来巨大经济损失。
本文在对长岭分公司所属大型外浮顶罐全面调查基础上,分析故障原因,指出存在的问题,提出相应对策,以确保其安全平稳运行。
1 大型外浮顶罐现状调查与分析1.1 外浮顶罐的基本情况长岭分公司现有大型外浮顶罐13台,储存介质为原油或重油,分布在王龙坡和北罐区两个罐区,其中30000m3罐9台,10000m3罐4台,油罐的基本情况如表1。
表1 外浮顶罐建设投用及基本情况罐号投用时间密封形式刮蜡板形式防蜡设施中央排水管情况9#、10#1986.10 机械密封装置机械式刮蜡板有一组排水,金属软管3根801#、802#1988.12 机械密封装置机械式刮蜡板无一组排水,金属软管3根1#--3#共3台1992.12 弹性密封机械式刮蜡板有两组排水,金属软管6根4#--6#共6台1996.09 弹性元件密封装置机械式刮蜡板有两组排水,金属软管6根11#--13#共3台1994.06 弹性元件密封装置机械式刮蜡板有两组排水,金属软管6根1.2 外浮顶罐故障调查近年来,长岭分公司所属外浮顶罐发生故障的频次越来越多,可能造成的损失越来越大,每一次故障发生后,给正常生产造成一定的影响,近五年来外浮顶罐故障情况的统计见表2。
1.3 外浮顶罐发生故障原因分析在近年的生产过程中,13台外浮顶罐先后有8台次发生故障,故障率61.54%。
不管是哪一种情况,详细分析,其结果见表3。
从分析结果可以看出,金属软管的损坏和罐内壁沾蜡对油罐造成较大损失,且这两种情况不易及时发现。
加热盘管损坏在日常检查时具有易见性,且较为直观,不会在短时间内造成大的损失。
为此,对金属软管的损坏和沾蜡造成浮顶严重积水两种情况进行详细分析。
收稿日期:2003-10-31作者简介:李伟,1966年12月出生,1987年毕业于兰州石油学校炼油机械专业,2002年湖南大学工业管理工程专业毕业,助理工程师,现为原油车间党支部书记。
表2 近年来外浮顶罐故障统计表时间罐号容量罐内储油情况故障情况处理情况故障原因2003.8.19 801 10000原油、4500t中央排水管突然漏油, 约1t/h,及时对该罐重点检查,杜绝跑油事故。
关闭中央排水管阀,及时倒空油品,更换软管。
罐内活动连接处金属软管疲劳破坏,出现裂逢。
2003.6.20 802 10000蜡油、8500t中央排水管漏油,由小到大,一周后漏油0.5t/h,及时对该罐重点检查,杜绝跑油事故。
及时将该罐内油品倒空,更换金属软管。
罐内活动连接处金属软管疲劳破坏出现裂逢。
2002.10.2 10 10000重油、5000t加热盘管穿孔,加热过程中,大量水进入到油口中。
加热中罐位升高异常,经检查发现加热器的疏水阀不排水。
对该罐进行倒油并清罐后,修复损坏的加热盘管;重油中硫含量较高,加热盘管腐蚀穿孔所至。
2002.5.10 3 3000原油、26000t17:45左右,中央排水突然大量漏油,约15t/h(两组中央排水管,其中一组漏油)。
距该罐20m远处的当班职工听到异常声音,立即跑去关闭中央排水管出口阀门,倒空清罐。
该罐正处于收油状态,中央排水管在上升伸长过程中,集水槽处的金属软管突然裂口所至。
2002.4.23 11 30000原油、9000t20:00天突降暴雨,中央排水管不排水,浮盘上集水槽内单向阀入口处堵塞。
组织人员一方面清除集水槽内油品和杂物,一方面用胶管将水从浮盘顶的水从人孔引入到罐内原油中。
4月21日至23日连续三天,白天气温突然升高,罐内壁蜡油全部融化进入到浮盘顶部,突降暴雨时,成块状的蜡被雨水冲到集水槽内堵塞单向阀入口,部分蜡油进入到中央排水管内所至。
2001.3.16 801 10000原油、9000t21:00左右,当班职工检查时发现该罐中央排水管漏油。
立即关闭中央排水管出口阀。
该罐正在收油过程中,中央排水管处于伸长状态,金属软管裂开所至。
1999.06.19 5 30000原油7:00当班职工发现中央排水管出口有油外溢。
立即关闭出口阀门,联系生产部门,倒空罐内油品,更换金属软管。
罐内金属软管疲劳破坏折断开裂。
1999.06.28 10 10000重油6000t6:00天下暴雨,检查发现中央排水管不排水,浮盘顶积水约3000mm深。
组织人员用蒸汽对中央排水管反顶并加热,将集水槽处蜡油融化排水。
集水槽单向阀处有成块状的蜡油,在浮顶水压作用下,蜡油往排水管挤压,将排水管全部堵死。
表3 故障情况分析项目故障频次比例/%金属软管损坏 5 62.5集水槽堵死 2 25.0加热盘管损坏 1 12.51.3.1 金属软管损坏原因分析金属软管损坏的频次最高,主要是金属软管的使用寿命而决定的,最长的已达15年,最短的也有7年,其理论寿命一般为10年左右。
对损坏更换的金属软管进行分析,全部是在集水槽下第一根金属软管,而且为曲率半径最小处折断或部分折断。
当油罐液位在上升过程中,浮盘带动金属软管上升,故金属软管要承受一定的拉力,同时还有一定扭矩和弯矩作用,首先受力的为集水槽下第一根金属软管,所以,该处软管最容易损坏。
2002年5月10日王龙坡3#罐,罐内油品液位接近安全高度,软管由于有拉力作用,突然严重破裂而出现大量跑油,就证明了这一点。
801#和802#罐金属软管连续损坏,除寿命的原因外,与软管长度有关。
这两台罐的中央排水管原设计为耐油胶管连接,使用一年后更换为金属软管,集水槽底法兰为DN100,中央排水管法兰为DN80,在DN100法兰后安装了一个DN100变DN80长度为350mm的短接,应为长1400mm金属软管,实际安装了长1000mm软管,缩短了软管长度,致使其曲率半径缩小,弯曲应力增大,从而使其寿命缩短。
1.3.2 罐内壁沾蜡情况的分析罐内壁的沾蜡虽然只出现了两次集水槽堵塞,浮顶大量积水现象,但清理浮顶沾蜡的工作随时在进行。
2003年1至6月,就先后对王龙坡1#、4#、6#、11#和13#罐进行了多次浮顶收油,罐内壁沾蜡主要与油品性质和外界环境温度有关。
对近年来长岭分公司几种原油性质进行分析,见表4。
表4 几种常见原油性质统计表原油品种取样时间密度/kg.m-3ρ20粘度/mm2.s-150℃凝点/℃总硫/%(ψ) 特性因素K卡宾达油2003.04.04 868.7 12.96 14 0.26 12.1 西北重油2003.04.04 903.7 68.22 34 0.16 / 哈萨克斯坦油2003.04.21 820.1 3.824 1 0.073 11.1 南巴油2003.03.28 823.2 2.609 1 0.27 11.8 管钱原油2003.02.25 915.0 69.70 1 0.93 11.9 管阿混合原油2003.02.20 919.1 77.82 6 1.01 11.9 阿曼原油2003.02.19 857.3 12.04 -30 1.22 12.3 塞巴原油2003.01.12 868.5 7.987 -10 0.56 11.9 杰诺原油2002.10.08 882.9 21.55 8 0.29巴隆港原油2002.11.16 834.0 4.262 27 0.11管阿混合原油2001.09.19 910.7 89.75 11 0.94管扎原油2001.10.18 909.2 77.82 11 0.96管输原油2000.01.20 925.6 156 13 1.06库尔勒原油2000.08.26 915.5 -27 2.02仪黄原油2000.10.23 907.1 58.45 10 1.06根据原油化学组成并按特性因素(K值)进行分类,原油可以分为石蜡基、中间基和环烷基原油三种,按常规:K值大于12.1为石蜡基原油,蜡含量高,凝点高,密度小;K值为11.5~12..1,属于中间基原油;K值为10.5~11.5为环烷基原油。
从特性因素K值来看,随着K值的增长,蜡含量增加且凝点增高。
从长岭分公司的原油结构来分析,其K 值基本都在11.1以上,属于中间基或石蜡基原油,所以其蜡含量较高。
虽然所有大型外浮顶罐都有刮蜡装置,因浮盘上下运动过程中,浮梯及金属软管等的作用,浮盘存在有一定的扭矩,加上刮蜡板的变形或损坏,罐壁的变形,罐壁沾蜡不可能100%被刮净。
当油罐储存含蜡量较高的原油处于付油状态时,浮顶密封装置靠罐顶一侧的温度,要低于罐内油品温度,特别是在冬春两季或春夏之交季节,加上下雨,该处的温度则更低,罐壁更容易出现沾蜡现象。
长岭分公司地处长江中下游的丘陵山区,春夏之交的气候变化较大,很容易沾蜡。
所以,加强对罐内壁沾蜡情况进行详细检查,防止因气温突然变化出现内壁沾蜡融化进入到浮顶,造成集水槽单向阀堵塞现象。
现场对王龙坡4台30000立方米外浮顶罐内壁不同部位沾蜡情况进行了实测,其实测数据见表5。
表5 罐壁沾蜡厚度测量由表5得:沾蜡的平均厚度为:δ=38.38/30=1.28mm30000m 3外浮顶罐,直径D=46m ,安全高度H=17.1m ,正常情况下收油到80%安高,付油到2.5m起浮高度,此时罐壁的沾蜡总量Q 蜡:Q 蜡=πD(H80%-2.5)δ=2.07 m 3罐内壁沾蜡是分次逐步融化的,随着外界气温升高每次融化量若为沾蜡总量的10%,则被融化进入到浮盘顶部的蜡油为Q 蜡融:Q 蜡融=2.07×10% = 0.21 m 3这一结果与实际生产中定期清除浮盘顶部的沾蜡量基本一致。
1.3.3 集水槽受堵浮顶积水量分析集水槽的作用是将浮盘顶的雨水及时通过中央排水管排出,防止浮盘积水。
浮盘顶部的积水在一定范围内不会造成浮盘下沉,以王龙坡11#罐为例进行分析,对外浮盘浮力进行计算(浮盘结构如图1所示)。
查王龙坡11#罐(30000m 3)图纸可知:R 1=22800mm ,R 2=20300mm ,h=800mm ,h 1=270mm, 则单浮盘至浮仓之间的高度h 2=h-h 1=530mm ,G 0=G 浮盘+G 浮梯+G 轨道 =98.71+1.838+0.370=100.918t30Σδi=38.38 mmi=1图1 浮盘示意图由表4,油品密度取最小值:ρoil = min{ρ20}=0.820 t/m3, ρ水=1 t/m3(1)在正常情况下,设浮仓浸入油中的高度为h oil,根据浮力公式有:π[R12h oil - R22h1]ρoil = G0..........(1)由(1)式得:h oil=0.290m=290mm (大于h1=270mm)(2)在浮盘顶部积水(中央集水槽受堵时),浮盘处于沉没临界状态,设浮盘顶部的积水最大高度为h水,由浮力公式有:πR12(h-h oil )ρoil=πR22h水ρ水......(2)由式(2)得:h水=0.528 m=528 mm (小于h2=530mm)所以,浮盘顶部的积水不能超过单浮板至浮仓之间的高度,否则,浮盘就会沉没。