丝杆设计计算
丝杆选型计算公式

丝杆选型计算公式丝杆选型是机械设计中的重要环节,合理的丝杆选型可以保证机械的正常运行和性能的发挥。
丝杆选型的主要目标是确定丝杆的直径、螺距和材料等参数,以满足机械的运动要求,同时兼顾经济性和可靠性。
一、丝杆选型的基本参数1.丝杆直径:丝杆的直径决定了丝杆的承载能力,直径越大,丝杆的承载能力越大。
一般采用密歇根公式或者英国机械工程师协会公式来计算丝杆的承载能力。
2.螺距:螺距决定了每转一圈丝杆前进的距离,也就是丝杆的传动比。
螺距越大,传动比越大,同样的驱动力可以实现更大的位移。
3.丝杆材料:丝杆的材料直接关系到其强度和耐磨性。
常见的丝杆材料有碳钢、不锈钢和合金钢等。
二、丝杆选型的计算公式1.丝杆承载能力的计算公式:丝杆承载能力=π/4*(D^2-d^2)*σc式中,D为丝杆的外径,d为丝杆的芯径,σc为丝杆材料的屈服强度。
2.丝杆的传动比计算公式:传动比=π/p式中,p为丝杆的螺距。
三、丝杆选型的步骤1.确定所需的动力和运动参数,如负载力、转速、加速度等。
2.根据负载力和运动参数计算所需的丝杆承载能力,这时需要根据应力公式计算应力,然后根据选用的丝杆材料查找其屈服强度数值。
3.选择一个合适的丝杆直径,保证其承载能力能够满足需求。
4.根据所需的传动比计算丝杆的螺距,一般选择合理的传动比,既要满足运动要求,又要尽量减小负载力和功率的损耗。
5.最后根据所选的丝杆直径和螺距选择材料,一般根据经济性和耐磨性来选择。
以上就是丝杆选型的基本概念和计算公式,根据不同的应用和需求,丝杆选型的计算方法可能会有所不同。
因此,在实际应用中,需要根据具体情况进行综合考虑和调整,以确保选用的丝杆满足机械设计的要求。
丝杆轴有效径计算

丝杆轴有效径计算
丝杆轴的有效径计算涉及多个因素,包括负载、转速、材料的剪切强度以及丝杆的长度等。
以下是一种常用的计算公式:
d = (16F L) / (πnτ)
其中:
•d:丝杠轴的直径,单位为mm;
•F:系在轴上的负载,单位为N;
•L:丝杠的长度,单位为mm;
•n:丝杠的转速,单位为r/min;
•τ:材料的剪切强度,单位为N/mm²。
这个公式提供了一种根据给定的工作条件和材料属性来确定丝杆轴直径的方法。
然而,实际设计中可能需要考虑更多的因素,如刚性、精度、寿命等。
此外,对于滚珠丝杆的定位精度,还需要考虑各个组成元件的刚性,包括丝杆轴的轴向刚性、螺母的轴向刚性和轴承的轴向刚性。
这些刚性的计算通常涉及更复杂的公式和因素。
请注意,以上信息仅供参考。
在实际应用中,建议咨询专业的机械工程师或参考相关的设计手册和标准来获取更准确和详细的信息。
丝杆计算方法【范本模板】

一、计算折合到电机上的负载转矩的方法如下:1、水平直线运动轴:9.8*µ·W·P BT L= 2π·R·η(N·M)式P B:滚珠丝杆螺距(m)µ:摩擦系数η:传动系数的效率1/R:减速比W:工作台及工件重量 (KG)2、垂直直线运动轴:9。
8*(W-W C)P BT L= 2π·R·η(N·M)式 W C:配重块重量(KG)3、旋转轴运动:T1T L= R·η(N·M)式 T1:负载转矩(N·M)二:负载惯量计算与负载转矩不同的是,只通过计算即可得到负载惯量的准确数值。
不管是直线运动还是旋转运动,对所有由电机驱动的运动部件的惯量分别计算,并按照规则相加即可得到负载惯量。
由以下基本公式就能得到几乎所有情况下的负载惯量.1、柱体的惯量cm)由下式计算有中心轴的援助体的惯量。
如滚珠丝杆,齿轮等。
πγD4L (kg·cm·sec2)或πγ·L·D4(KG·M2)J K= 32*980 J K= 32式γ:密度(KG/CM3)铁:γ〧7.87*10-3KG/CM3=7。
87*103KG/M3铝:γ〧2.70*10-3KG/CM3=2.70*103KG/M3 JK:惯量(KG·CM·SEC2)(KG·M2)D:圆柱体直径(CM)·(M)L:圆柱体长度(CM )·(M)2、运动体的惯量用下式计算诸如工作台、工件等部件的惯量 W P BJ L1= 980 2π(KG·CM·SEC2)P B 2=W2π(KG·M2)式中:W:直线运动体的重量(KG)PB:以直线方向电机每转移动量(cm)或(m)3、有变速机构时折算到电机轴上的惯量1、KG·CN:齿轮齿数Z12JL1= Z2 *J0 (KG·CM·SEC2)(KG·M2)三、运转功率及加速功率计算在电机选用中,除惯量、转矩之外,另一个注意事项即是电机功率计算。
丝杆计算方法完整版

丝杆计算方法HEN system office room 【HEN16H-HENS2AHENS8Q8-HENH1688】一、计算折合到电机上的负载转矩的方法如下:1、水平直线运动轴:*μ·W·PBTL= 2π·R·η(N·M)式 PB:滚珠丝杆螺距(m)μ:摩擦系数η:传动系数的效率1/R:减速比W:工作台及工件重量(KG)2、垂直直线运动轴:*(W-WC )PBTL=2π·R·η(N·M)式 WC:配重块重量(KG)3、旋转轴运动:T1TL= R·η(N·M)式 T1:负载转矩(N·M)二:负载惯量计算与负载转矩不同的是,只通过计算即可得到负载惯量的准确数值。
不管是直线运动还是旋转运动,对所有由电机驱动的运动部件的惯量分别计算,并按照规则相加即可得到负载惯量。
由以下基本公式就能得到几乎所有情况下的负载惯量。
1、柱体的惯量D(cm)L(cm)由下式计算有中心轴的援助体的惯量。
如滚珠丝杆,齿轮等。
πγD4L (kg·cm·sec2)或πγ·L·D4(KG·M2)JK = 32*980 JK= 32式γ:密度(KG/CM3)铁:γ〧*10-3KG/CM3=*103KG/M3铝:γ〧*10-3KG/CM3=*103KG/M3 JK:惯量(KG·CM·SEC2)(KG·M2)D:圆柱体直径(CM)·(M)L:圆柱体长度(CM )·(M)2、运动体的惯量用下式计算诸如工作台、工件等部件的惯量W PB2JL1= 980 2π(KG·CM·SEC2)PB2=W 2π(KG·M2)式中:W:直线运动体的重量(KG)PB:以直线方向电机每转移动量(cm)或(m)3、有变速机构时折算到电机轴上的惯量1、Z2J JOZ1KG·CN:齿轮齿数Z12JL1= Z2 *J(KG·CM·SEC2)(KG·M2)三、运转功率及加速功率计算在电机选用中,除惯量、转矩之外,另一个注意事项即是电机功率计算。
丝杠螺母设计计算

丝杠螺母设计计算丝杠螺母是一种常见的螺旋副传动元件,广泛应用于机械设备和工业生产线中。
其主要作用是将转动运动转化成线性运动。
1.丝杠参数计算:(1)螺纹间距:螺纹间距是指螺纹的螺距,即螺母每转一周,丝杠的前进距离。
螺纹间距的计算公式为:P=πd/n,其中P为螺纹间距,d为螺纹直径,n为螺纹数。
(2)理论前进距离:理论前进距离是指螺母每转一周,丝杠的前进距离,计算公式为:L=P×Z,其中L为理论前进距离,P为螺纹间距,Z为丝杠螺纹的螺纹数。
(3)丝杠传动效率:丝杠传动效率是指丝杠传动的能量损失情况,影响因素包括螺母材料、螺纹质量、润滑情况等。
2.选材计算:(1)强度计算:丝杠螺母的选材应根据实际使用情况的负载要求来确定。
根据载荷大小和工作环境要求,选择合适的强度等级材料。
(2)磨损计算:考虑到丝杠螺母在长时间使用中的磨损情况,需要根据材料的硬度和摩擦系数来估算螺纹副的磨损量。
3.密封设计计算:(1)密封件选型:根据丝杠螺母工作环境和介质要求,选择合适的密封件材料和结构形式。
(2)密封效果计算:在丝杠螺母设计中,需要考虑密封件的可靠性和密封效果。
通过计算密封件的接触压力和挤压量,来评估其密封性能。
4.轴承设计计算:螺纹副中,螺纹副运动较复杂,所以通常需要在螺母内部设置滚动轴承或滑动轴承,以减小摩擦和磨损。
在设计计算中,需要考虑轴承的负荷承受能力、摩擦系数、轴承寿命等因素。
5.补偿设计计算:(1)回程间隙:由于螺纹副传动中的摩擦力和弹性变形,会产生回程间隙。
需要通过计算和实验,确定回程间隙的大小。
(2)补偿控制:通过控制螺母位置和螺纹副的复位力,实现补偿控制作用,以延长螺纹副的使用寿命。
丝杠螺母设计计算的过程中需要综合考虑以上几个方面的因素,并根据实际应用需求来进行精确计算和设计。
只有在设计计算准确无误的前提下,才能确保丝杠螺母在实际使用中具有良好的工作性能和使用寿命。
此外,需要注意加工和安装过程中的工艺要求,以确保丝杠螺母的精度和质量。
丝杆选型计算公式

丝杆选型计算公式
丝杆选型计算公式是机械设计领域中一个重要的公式,用于计算丝杆的选型参数。
其主要目的是根据负载、速度、力矩等因素确定适合的丝杆型号和规格,以保证机械设备的性能、精度和稳定性。
丝杆选型计算公式包括以下几个方面:
1.负载计算公式:根据负载的大小和方向,计算出丝杆的负载能力。
负载能力主要与丝杆的直径、丝距和材质有关。
2.速度计算公式:根据丝杆的转速和径向力,计算出丝杆的最大转速,以确定其适用于的工作环境。
3.力矩计算公式:根据丝杆的长度、直径和转速,计算出所需的扭矩,以保证丝杆能够满足负载情况下的正常工作。
4.噪声计算公式:根据丝杆的规格、转速和材质,计算出丝杆运行时产生的噪声水平,以确保机械设备能够正常工作。
以上几个方面是丝杆选型计算公式的主要内容,通过运用这些公式,可以选择适合的丝杆类型,并保证其在机械设备中的正常工作。
有关丝杠导轨设计计算举例

步骤 9: 按 9.3.2 Fp=Fmax/3=2575/3=860(N)≤0.1Ca=0.1*22329=2233N(满足要求)
步骤 10: 按 6.1及公式 1取 Δt=2℃ Lu=Lx+2La+Ln=1000+2*10+1400=1160mm C=-δt=-α*Δt*Lu=-12*10-6*2*1160=-0.028(mm)
=7.1(N/μm)≤0.8δs=8(N/μm) (5)Kf引起的定位误差
按公式 26δd=F0(1/Ksmin -1/Ksmaxs)=500*(1/305-1/842)=1.1 (μm) 查阅附表 1中 E2:由 Lu=1160,3级精度 Vu=19μ δd=1.1(μm)≤0.8(δg-Vu)=0.8*(25-19)≈4.8(μm) δg是机床全行程上定位误差,δs是失动量 以上数据均符合要求,可选 3级精度 步骤 16 参考 8及图 2确定形位公差(略) 步骤 17 确定货代号 GB3210-3-P3 步骤 18 计算扭距 (1)理论动态预紧转距 Tpo
按 6.4及公式 预拉伸力 Ft=α*△t*E*(πd22/4)=(12*10-6)*2*(2.1*105)*(3.14*24.92/4)=2453N 步骤 11: (1) 选轴承型号
因滚珠丝杠副安装方式为:固定--固定,选背对背 60°接触轴承 (2) 确定轴承内径,确定轴承型号规格
左端轴承内径应略小于丝杠外径,取 φ25,型号规格 25TAC62B。内循环滚珠丝 杠必须有一端轴承内径小于螺纹底 d2。选右端轴承内径 φ20。型号规格 20TAC47B。 步骤 12: 绘制工作图(绘图过程从略) 最大行程:Lx=1000mm 余程:Le=40mm安全行程:La=Ph=10mm 由样本螺母长度 Ln=140mm 由结构设计得到 b1=85mmb2=15mm 罗纹长度:L1=Lx+2La+2Le+140=1240(mm)
(完整版)丝杠的选型及计算
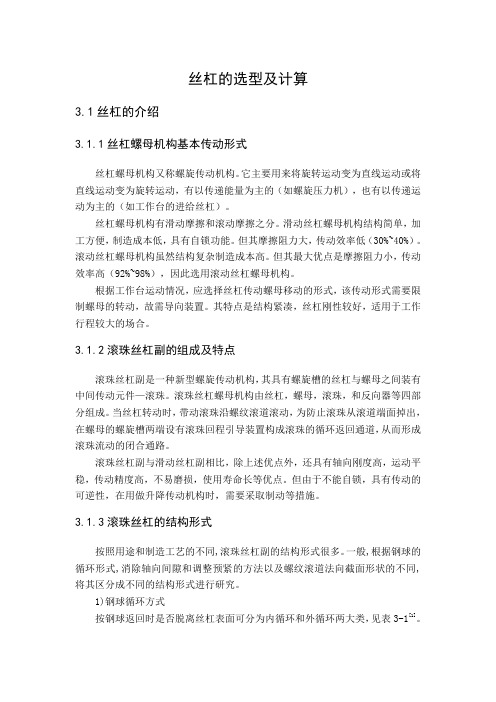
丝杠的选型及计算3.1丝杠的介绍3.1.1丝杠螺母机构基本传动形式丝杠螺母机构又称螺旋传动机构。
它主要用来将旋转运动变为直线运动或将直线运动变为旋转运动,有以传递能量为主的(如螺旋压力机),也有以传递运动为主的(如工作台的进给丝杠)。
丝杠螺母机构有滑动摩擦和滚动摩擦之分。
滑动丝杠螺母机构结构简单,加工方便,制造成本低,具有自锁功能。
但其摩擦阻力大,传动效率低(30%~40%)。
滚动丝杠螺母机构虽然结构复杂制造成本高。
但其最大优点是摩擦阻力小,传动效率高(92%~98%),因此选用滚动丝杠螺母机构。
根据工作台运动情况,应选择丝杠传动螺母移动的形式,该传动形式需要限制螺母的转动,故需导向装置。
其特点是结构紧凑,丝杠刚性较好,适用于工作行程较大的场合。
3.1.2滚珠丝杠副的组成及特点滚珠丝杠副是一种新型螺旋传动机构,其具有螺旋槽的丝杠与螺母之间装有中间传动元件—滚珠。
滚珠丝杠螺母机构由丝杠,螺母,滚珠,和反向器等四部分组成。
当丝杠转动时,带动滚珠沿螺纹滚道滚动,为防止滚珠从滚道端面掉出,在螺母的螺旋槽两端设有滚珠回程引导装置构成滚珠的循环返回通道,从而形成滚珠流动的闭合通路。
滚珠丝杠副与滑动丝杠副相比,除上述优点外,还具有轴向刚度高,运动平稳,传动精度高,不易磨损,使用寿命长等优点。
但由于不能自锁,具有传动的可逆性,在用做升降传动机构时,需要采取制动等措施。
3.1.3滚珠丝杠的结构形式按照用途和制造工艺的不同,滚珠丝杠副的结构形式很多。
一般,根据钢球的循环形式,消除轴向间隙和调整预紧的方法以及螺纹滚道法向截面形状的不同,将其区分成不同的结构形式进行研究。
1)钢球循环方式按钢球返回时是否脱离丝杠表面可分为内循环和外循环两大类,见表3-1[1]。
若钢球在循环过程中,始终与丝杠表面保持接触,称内循环;否则,称外循环。
通常,把在同一螺母上所具有的循环回路的数目,称为钢球的列数,常用的有2~4列。
而把每一循环回路中钢球所经过的螺纹滚道圈数(导程数)称为工作圈。
- 1、下载文档前请自行甄别文档内容的完整性,平台不提供额外的编辑、内容补充、找答案等附加服务。
- 2、"仅部分预览"的文档,不可在线预览部分如存在完整性等问题,可反馈申请退款(可完整预览的文档不适用该条件!)。
- 3、如文档侵犯您的权益,请联系客服反馈,我们会尽快为您处理(人工客服工作时间:9:00-18:30)。
数控滑台进给用滚珠丝杠副的设计计算:
横向与纵向滑台的总重量 W
1=3000N 立柱最大重量W
2
=5000N 工作台最
大行程 L
K
=1000mm 工作台导轨的摩擦系数:动摩擦系数μ=0.1静摩擦
系数μ
0=0.2 快速进给速度 V
max
=8m/min 定位精度20
μ
m /300mm 全行程25μ
m
重复定位精度10μ
m
要求寿命20000小时
(两班制工作十年)。
表1
切削方式纵向切削
力
Pxi(N)
垂向切削
力
Pzi(N)
进给速度
Vi(m/min)
工作时间百
分比
%
丝杠轴向载
荷
(N)
丝杠转
速
r/min
强力切
削
2000 1200 0.6 10 2920 60 一般切
削
1000 200 0.8 30 1850 80 精切削500 200 1 50 1320 100 快速进
给
0 0 8 10 800 1500
1)确定滚珠丝杠副的导程
因伺服电机与丝杠直联,i=1
由表1查得
V
m ax
=8m/min
n
m ax
=1440r/min
代入得,
P
h
≈5.56mm
由于计算出的P
h
值应取较大值圆整,因此
P
h
=6mm
2)确定当量转速与当量载荷
(1)各种切削方式下,丝杠转速
由表1查得
V 1=0.6 V
2
=0.8 V
3
=1 V
4
=8
代入得
n 1=100 n
2
=133 n3=167 n
4
=1333
(1)各种切削方式下,丝杠轴向载荷由表1查得
已知W
1=3000N W
2
=5000N
代入得
(3)当量转速
由表1查得
代入得
≈267r/min
n
m
(2)当量载荷
代入得
=1380N
F
m
3)预期额定动载荷
(1)按预期工作时间估算
按表9查得:轻微冲击取 f
=1.3
w
按表7查得:1~3取
按表8查得:可靠性97%取f
=0.44
c
=20000小时
已知:L
h
代入得
=27899N
C
m
计算:(2)拟采用预紧滚珠丝杠副,按最大负载F
max
=4.5
按表10查得:中预载取 F
e
代入得
取以上两种结果的最大值
=27899N
C
m
4)确定允许的最小螺纹底径
(1)估算丝杠允许的最大轴向变形量
① ≤(1/3~1/4)重复定位精度
② ≤(1/4~1/5)定位精度
: 最大轴向变形量µm
已知:重复定位精度10µm, 定位精度25µm
① =3
② =6
取两种结果的小值=3µm
(2)估算最小螺纹底径
丝杠要求预拉伸,取两端固定的支承形式
(1.1~1.2)行程+(10~14)
已知:行程为1000mm, W
1=3000N ,μ
=0.2
代入得
F
=600N
D
m
2
=20.04mm
5)确定滚珠丝杠副的规格代号
(1)选内循环浮动式法兰,直筒双螺母型垫片预形式
(2)由计算出的在样本中取相应规格的滚珠丝杠副FFZD4008-5
P
h
=8mm
C
a =30700﹥C
am
=27899
6) 确定滚珠丝杠副预紧力
其中
7)行程补偿值与与拉伸力(1)行程补偿值
式中:
=(2~4)
(2) 预拉伸力
代入得
8)确定滚珠丝杠副支承用的轴承代号、规格
(1)轴承所承受的最大轴向载荷
代入得
(2)轴承类型
两端固定的支承形式,选背对背60°角接触推力球轴承(3)轴承内径
d 略小于
取
代入得
(4)轴承预紧力
预加负荷≥
(5)按样本选轴承型号规格
当d=30mm 预加负荷为:≥F
BP
所以选7602030TVP轴承
d=30mm
预加负荷为
9 ) 滚珠丝杠副工作图设计
(1) 丝杠螺纹长度L
s
:
L s =L
u
+2L
e
由表二查得余程Le=40
绘制工作图
(2)两固定支承距离L
1
按样本查出螺母安装联接尺寸
丝杠全长L
(3)行程起点离固定支承距离L
0由工作图得
Ls=1290
L
1
=1350
L=1410
L
=30
10 ) 电机选择(略)
11 ) 传动系统刚度
(1)丝杠抗压刚度
1)丝杠最小抗压刚度
K
= 6.6 ×10
smin
K
:最小抗压刚度 N/m
smin
d
:丝杠底径
2
:固定支承距离
L
1
=575 N/m
K
smin
2)丝杠最大抗压刚度
K
=6.6 ×10
smax
:最大抗压刚度 N/m
K
smax
K
=6617 N/m
smax
(2) 支承轴承组合刚度
1)一对预紧轴承的组合刚度
=2×2.34
K
BO
:一对预紧轴承的组合刚度 N/m K
BO
:滚珠直径 mm
d
Q
Z :滚珠数
Famax :最大轴向工作载荷 N
:轴承接触角
由样本查出7602030TUP轴承是预加载荷的3倍
d
Q
=7.144 Z=17 =60
K
amax
=8700 N/m
K
BO
=375 N/m
2)支承轴承组合刚度
由表13两端固定支承
K b =2 K
BO
K
b
=750 N/m
K
b
:支承轴承组合刚度 N/m 3)滚珠丝杠副滚珠和滚道的接触刚度
K C = K
C
(
K
C
:滚珠和滚道的接触刚度 N/m
K
C
:查样本上的刚度 N/m
F
P
:滚珠丝杠副预紧力 N
C
a
:额定动载荷 N
由样本查得:
K C =1410 N/m;C
a
=3600N;
F
P
=1000 N
得K
=920 N/m
C
12) 刚度验算及精度选择
(1)=
= N/m
= N/m
=
F
已知W
=5000 N ,=0.2
1
1000 N
F
0=
:静摩擦力 N
F
:静摩擦系数
:正压力 N
W
1
(2)验算传动系统刚度
K
min
K
:传动系统刚度 N
min
已知反向差值或重复定位精度为10
K
=222>160
min
(3)传动系统刚度变化引起的定位误差
=1.7m
(4)确定精度
:任意300mm内的行程变动量对半闭环系统言, V
300p
≤0.8×定位精度-
V
300p
定位精度为20m/300
V
<14.3m
300p
丝杠精度取为3级
=12m<14.3
V
300p
(5) 确定滚珠丝杠副的规格代号
已确定的型号:FFZD
公称直径:40 导程:10
螺纹长度:1290
丝杠全长:1410
P类3级精度
/1410×1290
FFZD4010-3-P
3
13) 验算临界压缩载荷
:N
F
c
丝杠所受最大轴向载荷Fmax小于丝杠预拉伸力F不用验算。
14 ) 验算临界转速
n
c
=f ×10
n
c
: 临界转速 n/min f :与支承形式有关的系数
:丝杠底径
:临界转速计算长度 mm 由表14得f=21.9
由样本得d
2
=34.3
由工作图及表14得:L
c2= L
1
- L
4310>n
max
=1500 15 ) 验算:
D n =D
pw
n
max
D
pw
:滚珠丝杠副的节圆直径 mm
n
max
: 滚珠丝杠副最高转速 n/min
D
pw
≈41.4mm
n
max
=1500r/min
62100<70000
16) 滚珠丝杠副形位公差的标注(略)
表1:
支承方式简图K2 λ f
一端固定
一端自由
0.25 1.875 3.4
一端固定
2 3.927 15.1 一端游动
二端支承 1 3.142 9.7 二端固定 4 4.730 21.9。