自动化项目升级改造方案
第二水厂自动化升级改造实施方案
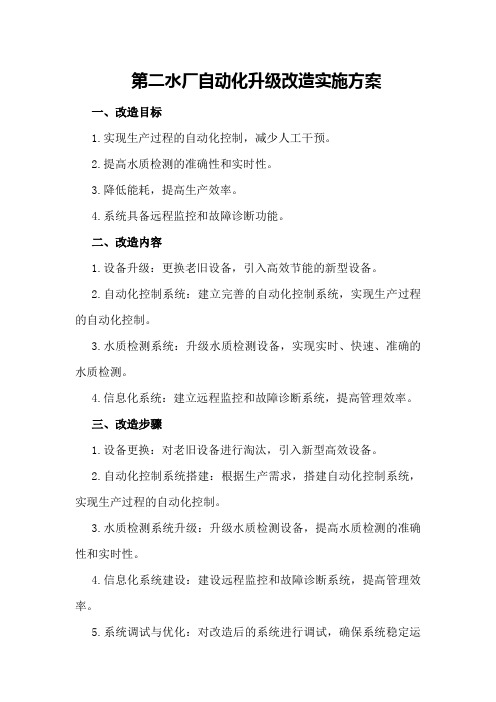
第二水厂自动化升级改造实施方案一、改造目标1.实现生产过程的自动化控制,减少人工干预。
2.提高水质检测的准确性和实时性。
3.降低能耗,提高生产效率。
4.系统具备远程监控和故障诊断功能。
二、改造内容1.设备升级:更换老旧设备,引入高效节能的新型设备。
2.自动化控制系统:建立完善的自动化控制系统,实现生产过程的自动化控制。
3.水质检测系统:升级水质检测设备,实现实时、快速、准确的水质检测。
4.信息化系统:建立远程监控和故障诊断系统,提高管理效率。
三、改造步骤1.设备更换:对老旧设备进行淘汰,引入新型高效设备。
2.自动化控制系统搭建:根据生产需求,搭建自动化控制系统,实现生产过程的自动化控制。
3.水质检测系统升级:升级水质检测设备,提高水质检测的准确性和实时性。
4.信息化系统建设:建设远程监控和故障诊断系统,提高管理效率。
5.系统调试与优化:对改造后的系统进行调试,确保系统稳定运行,并根据实际情况进行优化。
四、改造时间安排1.设备更换:预计用时3个月。
2.自动化控制系统搭建:预计用时4个月。
3.水质检测系统升级:预计用时2个月。
4.信息化系统建设:预计用时3个月。
5.系统调试与优化:预计用时2个月。
总计:14个月五、预期效果1.生产效率提高30%。
2.人力成本降低20%。
3.水质合格率提高20%。
4.设备故障率降低30%。
六、风险评估及应对措施1.设备更换风险:设备更换期间,可能影响正常生产。
应对措施:提前做好备用设备,确保生产不受影响。
2.系统调试风险:系统调试期间,可能出现故障。
应对措施:组织专业团队进行调试,确保系统稳定运行。
3.人员培训风险:新技术的引入,需要对员工进行培训。
应对措施:组织专业培训,提高员工的操作技能。
七、改造经费预算1.设备更换费用:500万元。
2.自动化控制系统搭建费用:300万元。
3.水质检测系统升级费用:200万元。
4.信息化系统建设费用:150万元。
5.人员培训费用:50万元。
制造业工业自动化生产线升级改造方案
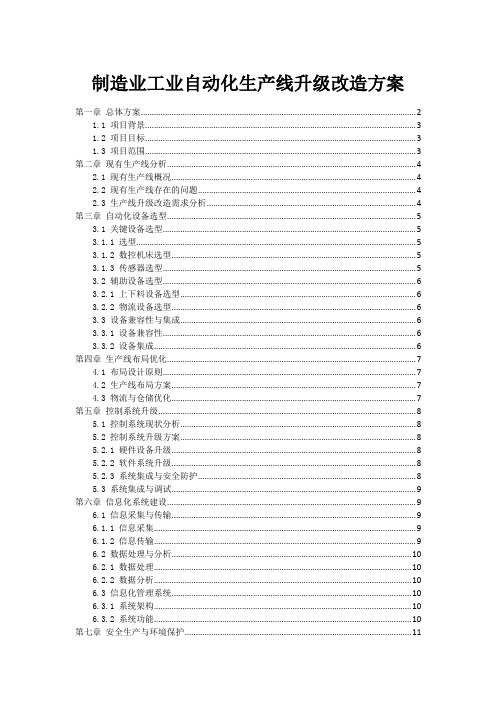
制造业工业自动化生产线升级改造方案第一章总体方案 (2)1.1 项目背景 (3)1.2 项目目标 (3)1.3 项目范围 (3)第二章现有生产线分析 (4)2.1 现有生产线概况 (4)2.2 现有生产线存在的问题 (4)2.3 生产线升级改造需求分析 (4)第三章自动化设备选型 (5)3.1 关键设备选型 (5)3.1.1 选型 (5)3.1.2 数控机床选型 (5)3.1.3 传感器选型 (5)3.2 辅助设备选型 (6)3.2.1 上下料设备选型 (6)3.2.2 物流设备选型 (6)3.3 设备兼容性与集成 (6)3.3.1 设备兼容性 (6)3.3.2 设备集成 (6)第四章生产线布局优化 (7)4.1 布局设计原则 (7)4.2 生产线布局方案 (7)4.3 物流与仓储优化 (7)第五章控制系统升级 (8)5.1 控制系统现状分析 (8)5.2 控制系统升级方案 (8)5.2.1 硬件设备升级 (8)5.2.2 软件系统升级 (8)5.2.3 系统集成与安全防护 (8)5.3 系统集成与调试 (9)第六章信息化系统建设 (9)6.1 信息采集与传输 (9)6.1.1 信息采集 (9)6.1.2 信息传输 (9)6.2 数据处理与分析 (10)6.2.1 数据处理 (10)6.2.2 数据分析 (10)6.3 信息化管理系统 (10)6.3.1 系统架构 (10)6.3.2 系统功能 (10)第七章安全生产与环境保护 (11)7.1 安全生产措施 (11)7.1.1 安全管理制度 (11)7.1.2 设备安全防护 (11)7.1.3 人身安全措施 (11)7.2 环境保护措施 (12)7.2.1 污染防治 (12)7.2.2 节能减排 (12)7.2.3 环保宣传教育 (12)7.3 应急预案与培训 (12)7.3.1 应急预案 (12)7.3.2 培训与演练 (12)第八章项目实施与进度安排 (13)8.1 项目实施计划 (13)8.2 项目进度安排 (13)8.3 项目验收与评价 (13)第九章成本预算与投资回报 (14)9.1 成本预算 (14)9.1.1 预算编制原则 (14)9.1.2 成本预算内容 (14)9.2 投资回报分析 (14)9.2.1 投资回报期 (14)9.2.2 投资回报率 (15)9.2.3 投资收益分析 (15)9.3 项目经济效益评估 (15)9.3.1 直接经济效益 (15)9.3.2 间接经济效益 (15)第十章项目风险与应对措施 (15)10.1 项目风险识别 (15)10.1.1 技术风险 (15)10.1.2 管理风险 (16)10.1.3 市场风险 (16)10.2 风险评估与分级 (16)10.2.1 风险评估 (16)10.2.2 风险分级 (16)10.3 风险应对措施及预案 (17)10.3.1 技术风险应对措施 (17)10.3.2 管理风险应对措施 (17)10.3.3 市场风险应对措施 (17)10.3.4 风险预案 (17)第一章总体方案1.1 项目背景科技的飞速发展,制造业工业自动化已成为提升生产效率、降低成本、提高产品质量的关键途径。
工业自动化生产线的升级改造方案

工业自动化生产线的升级改造方案第一章总体升级改造规划 (3)1.1 项目背景 (3)1.2 项目目标 (3)1.3 项目范围 (3)第二章现有生产线分析 (4)2.1 生产线现状 (4)2.1.1 设备状况 (4)2.1.2 生产流程 (4)2.1.3 信息化水平 (4)2.2 存在问题 (4)2.2.1 设备老化 (4)2.2.2 自动化程度低 (4)2.2.3 信息孤岛现象 (5)2.2.4 安全隐患 (5)2.3 优化需求 (5)2.3.1 设备更新 (5)2.3.2 提高自动化水平 (5)2.3.3 加强信息化建设 (5)2.3.4 安全生产 (5)第三章设备更新与升级 (5)3.1 设备选型 (5)3.2 设备安装与调试 (6)3.3 设备维护与管理 (6)第四章自动化控制系统升级 (6)4.1 控制系统设计 (7)4.2 控制系统实施 (7)4.3 控制系统优化 (7)第五章生产线流程优化 (8)5.1 流程分析 (8)5.1.1 现状评估 (8)5.1.2 流程分类 (8)5.1.3 流程关键节点分析 (8)5.2 流程改进 (8)5.2.1 原材料准备流程改进 (8)5.2.2 加工制造流程改进 (8)5.2.3 质量检测流程改进 (9)5.2.4 物流配送流程改进 (9)5.2.5 售后服务流程改进 (9)5.3 流程监控 (9)5.3.1 建立流程监控指标体系 (9)5.3.2 实施流程监控 (9)5.3.4 持续改进 (9)第六章质量管理系统升级 (9)6.1 质量检测设备更新 (10)6.2 质量控制策略优化 (10)6.3 质量数据管理 (10)第七章生产效率提升 (11)7.1 生产节拍优化 (11)7.1.1 节拍优化背景 (11)7.1.2 节拍优化方法 (11)7.1.3 节拍优化实施 (11)7.2 设备利用率提升 (11)7.2.1 设备利用率现状分析 (11)7.2.2 设备利用率提升方法 (12)7.2.3 设备利用率提升实施 (12)7.3 生产调度优化 (12)7.3.1 生产调度优化背景 (12)7.3.2 生产调度优化方法 (12)7.3.3 生产调度优化实施 (12)第八章安全生产与环境保护 (12)8.1 安全生产措施 (12)8.1.1 遵循国家安全法规 (12)8.1.2 设备安全防护 (13)8.1.3 人员安全防护 (13)8.2 环境保护设施升级 (13)8.2.1 废气处理设施 (13)8.2.2 废水处理设施 (13)8.2.3 噪音治理 (13)8.3 安全生产培训与监管 (14)8.3.1 安全生产培训 (14)8.3.2 安全生产监管 (14)第九章人员培训与技能提升 (14)9.1 培训计划制定 (14)9.1.1 需求分析 (14)9.1.2 培训目标 (14)9.1.3 培训内容 (14)9.1.4 培训方式 (15)9.1.5 培训周期 (15)9.2 培训实施与考核 (15)9.2.1 培训实施 (15)9.2.2 考核与评估 (15)9.3 技能提升策略 (15)9.3.1 持续学习 (15)9.3.2 交流与合作 (15)9.3.4 激励机制 (15)9.3.5 职业发展 (15)第十章项目实施与验收 (15)10.1 项目实施计划 (16)10.1.1 实施目标 (16)10.1.2 实施阶段 (16)10.1.3 实施步骤 (16)10.2 项目进度监控 (16)10.2.1 进度计划 (16)10.2.2 进度监控 (16)10.2.3 进度调整 (16)10.3 项目验收与评价 (17)10.3.1 验收标准 (17)10.3.2 验收流程 (17)10.3.3 验收结果处理 (17)第一章总体升级改造规划1.1 项目背景科技的飞速发展,工业自动化已成为推动我国制造业转型升级的重要力量。
机械行业自动化生产线改造升级方案
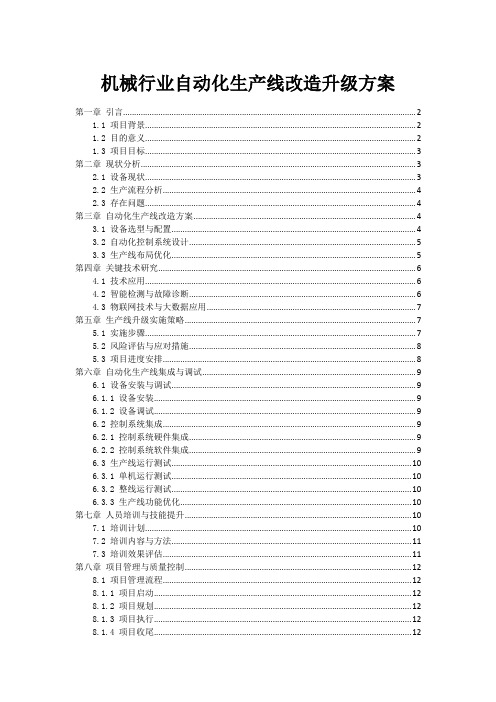
机械行业自动化生产线改造升级方案第一章引言 (2)1.1 项目背景 (2)1.2 目的意义 (2)1.3 项目目标 (3)第二章现状分析 (3)2.1 设备现状 (3)2.2 生产流程分析 (4)2.3 存在问题 (4)第三章自动化生产线改造方案 (4)3.1 设备选型与配置 (4)3.2 自动化控制系统设计 (5)3.3 生产线布局优化 (5)第四章关键技术研究 (6)4.1 技术应用 (6)4.2 智能检测与故障诊断 (6)4.3 物联网技术与大数据应用 (7)第五章生产线升级实施策略 (7)5.1 实施步骤 (7)5.2 风险评估与应对措施 (8)5.3 项目进度安排 (8)第六章自动化生产线集成与调试 (9)6.1 设备安装与调试 (9)6.1.1 设备安装 (9)6.1.2 设备调试 (9)6.2 控制系统集成 (9)6.2.1 控制系统硬件集成 (9)6.2.2 控制系统软件集成 (9)6.3 生产线运行测试 (10)6.3.1 单机运行测试 (10)6.3.2 整线运行测试 (10)6.3.3 生产线功能优化 (10)第七章人员培训与技能提升 (10)7.1 培训计划 (10)7.2 培训内容与方法 (11)7.3 培训效果评估 (11)第八章项目管理与质量控制 (12)8.1 项目管理流程 (12)8.1.1 项目启动 (12)8.1.2 项目规划 (12)8.1.3 项目执行 (12)8.1.4 项目收尾 (12)8.2 质量控制体系 (13)8.2.1 质量策划 (13)8.2.2 质量保证 (13)8.2.3 质量控制 (13)8.3 项目验收与评价 (13)8.3.1 项目验收 (13)8.3.2 项目评价 (13)第九章经济效益分析 (14)9.1 投资估算 (14)9.1.1 设备投资估算 (14)9.1.2 软件投资估算 (14)9.1.3 工程建设投资估算 (14)9.1.4 总投资估算 (14)9.2 成本分析 (15)9.2.1 直接成本 (15)9.2.2 间接成本 (15)9.3 效益评估 (15)9.3.1 产能提升 (15)9.3.2 成本降低 (15)9.3.3 投资回收期 (16)9.3.4 盈利能力 (16)第十章总结与展望 (16)10.1 项目成果总结 (16)10.2 项目不足与改进方向 (16)10.3 行业发展趋势展望 (17)第一章引言科技的不断进步和工业4.0时代的到来,我国机械行业正面临着前所未有的发展机遇。
工业自动化生产线升级改造方案

工业自动化生产线升级改造方案第一章总论 (2)1.1 项目背景 (3)1.2 项目目标 (3)1.3 项目意义 (3)第二章现状分析 (4)2.1 现有生产线概况 (4)2.2 现有生产线存在的问题 (4)2.2.1 设备老化 (4)2.2.2 生产流程不合理 (4)2.2.3 自动化程度有待提高 (4)2.2.4 信息化水平不高 (4)2.3 现有生产线的优势与劣势分析 (4)2.3.1 优势 (4)2.3.2 劣势 (4)第三章升级改造方案设计 (5)3.1 整体方案设计 (5)3.2 设备更新与升级 (5)3.3 自动化控制系统升级 (5)3.4 生产线布局优化 (6)第四章设备选型与配置 (6)4.1 关键设备选型 (6)4.2 辅助设备配置 (6)4.3 设备功能参数分析 (7)第五章自动化控制系统设计 (7)5.1 控制系统架构设计 (7)5.2 控制系统硬件配置 (8)5.3 控制系统软件设计 (8)第六章生产线布局与物流优化 (8)6.1 生产线布局设计 (8)6.1.1 设计原则 (8)6.1.2 设计方法 (9)6.2 物流系统优化 (9)6.2.1 物流系统概述 (9)6.2.2 物流系统优化策略 (9)6.3 生产线平衡分析 (9)6.3.1 生产线平衡概述 (9)6.3.2 生产线平衡分析方法 (9)6.3.3 生产线平衡实施策略 (10)第七章节能减排与环境保护 (10)7.1 节能措施 (10)7.1.1 提升设备能效 (10)7.1.2 优化生产流程 (10)7.1.3 管理措施 (10)7.2 减排措施 (10)7.2.1 减少有害气体排放 (10)7.2.2 减少废水排放 (11)7.2.3 减少固体废物排放 (11)7.3 环境保护措施 (11)7.3.1 噪音治理 (11)7.3.2 环境监测 (11)7.3.3 环保设施建设 (11)第八章项目实施与进度安排 (12)8.1 项目实施步骤 (12)8.1.1 需求分析与评估 (12)8.1.2 设计方案制定 (12)8.1.3 设备采购与安装 (12)8.1.4 控制系统升级与集成 (12)8.1.5 人员培训与考核 (12)8.1.6 系统验收与交付 (12)8.2 项目进度安排 (12)8.2.1 项目启动阶段(12个月) (12)8.2.2 设计方案制定阶段(34个月) (12)8.2.3 设备采购与安装阶段(57个月) (12)8.2.4 人员培训与考核阶段(89个月) (13)8.2.5 系统验收与交付阶段(1011个月) (13)8.3 项目风险与对策 (13)8.3.1 风险识别 (13)8.3.2 风险对策 (13)第九章投资预算与经济效益分析 (13)9.1 投资预算 (13)9.1.1 项目投资总额 (13)9.1.2 投资分配 (13)9.2 经济效益分析 (14)9.2.1 生产效率提升 (14)9.2.2 成本降低 (14)9.2.3 市场竞争力提升 (14)9.3 投资回报期分析 (14)第十章结论与建议 (14)10.1 项目总结 (14)10.2 项目建议 (15)10.3 未来发展展望 (15)第一章总论1.1 项目背景我国经济的快速发展,工业自动化技术在生产领域的应用日益广泛。
工厂生产线自动化改造方案

工厂生产线自动化改造方案第1章项目背景与目标 (3)1.1 项目背景 (3)1.2 项目目标 (3)1.3 项目意义 (4)第2章现有生产线分析 (4)2.1 生产线现状 (4)2.2 现有问题 (5)2.3 改造需求 (5)第3章自动化技术概述 (5)3.1 自动化技术发展历程 (5)3.2 自动化技术分类 (6)3.3 自动化技术在生产线中的应用 (6)第四章自动化设备选型 (7)4.1 设备选型原则 (7)4.1.1 适用性原则:设备应满足生产线工艺要求,适应生产规模,并具有良好的可扩展性。
(7)4.1.2 先进性原则:设备应选用国内外先进、成熟的技术,保证生产线的先进性。
(7)4.1.3 可靠性原则:设备应具有较高的稳定性和可靠性,保证生产过程的顺利进行。
74.1.4 经济性原则:在满足技术要求的前提下,设备选型应充分考虑投资预算,力求实现投资回报最大化。
(7)4.1.5 安全性原则:设备应具备完善的安全防护措施,保证生产过程中的人身安全和设备安全。
(7)4.1.6 易维护原则:设备应便于维护和维修,降低维修成本和停机时间。
(7)4.2 常用自动化设备介绍 (7)4.2.1 :用于搬运、装配、焊接、喷涂等工序,提高生产效率,降低劳动强度。
(7)4.2.2 自动化输送设备:如皮带输送机、链板输送机、滚筒输送机等,用于实现物料的输送和搬运。
(7)4.2.3 自动化仓储设备:如立体仓库、自动化货架、堆垛机等,提高仓储效率,降低仓储成本。
(7)4.2.4 自动化检测设备:如视觉检测系统、传感器等,用于实时监测产品质量,保证产品质量稳定。
(7)4.2.5 自动化控制系统:如PLC、DCS等,实现对生产过程的实时监控和自动化控制。
74.3 设备选型与配置 (7)4.3.1 根据生产线的工艺要求,分析各工序所需设备类型和数量。
(7)4.3.2 结合设备选型原则,进行设备选型,保证设备满足生产需求。
制造业自动化生产线升级改造方案

制造业自动化生产线升级改造方案第1章项目背景与目标 (3)1.1 现有生产线状况分析 (3)1.1.1 自动化程度 (3)1.1.2 生产效率 (4)1.1.3 稳定性与可靠性 (4)1.1.4 智能化水平 (4)1.2 升级改造目标与预期效果 (4)1.2.1 提高自动化程度 (4)1.2.2 提升生产效率 (4)1.2.3 提高稳定性与可靠性 (4)1.2.4 提升智能化水平 (4)第2章自动化技术与设备选型 (5)2.1 自动化技术发展趋势 (5)2.2 设备选型依据与标准 (5)2.3 主要设备介绍 (5)第3章生产线布局优化 (6)3.1 现有布局分析 (6)3.1.1 生产线布局现状 (6)3.1.2 布局问题原因分析 (6)3.2 优化方案设计 (6)3.2.1 优化目标 (6)3.2.2 优化措施 (6)3.3 布局实施与调整 (7)3.3.1 实施步骤 (7)3.3.2 调整策略 (7)3.3.3 监控与评估 (7)第四章控制系统设计与集成 (7)4.1 控制系统架构设计 (7)4.1.1 系统概述 (7)4.1.2 控制系统层次结构 (7)4.1.3 控制系统硬件设计 (8)4.1.4 控制系统软件设计 (8)4.2 传感器与执行器选型 (8)4.2.1 传感器选型 (8)4.2.2 执行器选型 (8)4.2.3 传感器与执行器接口设计 (8)4.3 控制系统集成与调试 (8)4.3.1 系统集成 (8)4.3.2 系统调试 (8)4.3.3 系统优化与升级 (8)第5章数据采集与分析 (9)5.1.1 采集目标 (9)5.1.2 采集方法 (9)5.1.3 采集频率 (9)5.2 数据传输与存储 (9)5.2.1 数据传输 (9)5.2.2 数据存储 (10)5.3 数据分析与挖掘 (10)5.3.1 设备故障预测 (10)5.3.2 生产优化 (10)5.3.3 质量控制 (10)5.3.4 人员绩效分析 (10)第6章智能化升级 (10)6.1 智能化技术应用 (10)6.1.1 传感器技术 (11)6.1.2 数据通信技术 (11)6.1.3 控制系统升级 (11)6.2 机器视觉与识别 (11)6.2.1 机器视觉系统 (11)6.2.2 识别技术应用 (11)6.3 人工智能在生产线上的应用 (11)6.3.1 机器学习 (11)6.3.2 自适应控制 (11)6.3.3 人工智能 (12)第7章设备故障预测与维护 (12)7.1 故障预测方法 (12)7.1.1 数据驱动法 (12)7.1.2 模型驱动法 (12)7.1.3 混合驱动法 (12)7.2 设备维护策略 (13)7.2.1 预防性维护 (13)7.2.2 预测性维护 (13)7.2.3 应急维护 (13)7.3 预测性维护实施 (13)7.3.1 设备数据采集与处理 (13)7.3.2 故障预测模型建立 (13)7.3.3 预测结果分析 (13)7.3.4 预测性维护实施 (13)7.3.5 预测性维护效果评估 (13)第8章信息安全与网络安全 (14)8.1 信息安全风险分析 (14)8.1.1 数据泄露风险 (14)8.1.2 系统入侵风险 (14)8.1.3 设备安全风险 (14)8.2.1 数据加密与访问控制 (14)8.2.2 网络隔离与防火墙 (14)8.2.3 安全审计与日志分析 (14)8.2.4 安全更新与漏洞修复 (14)8.3 安全措施实施与评估 (14)8.3.1 安全措施实施 (14)8.3.2 安全措施评估 (15)第9章人员培训与能力提升 (15)9.1 培训需求分析 (15)9.2 培训课程设置与实施 (15)9.3 人员能力评估与持续提升 (16)第10章项目实施与评估 (16)10.1 项目进度管理 (16)10.1.1 制定详细的实施计划 (16)10.1.2 建立进度监控机制 (16)10.1.3 及时调整进度计划 (16)10.1.4 加强沟通协调 (17)10.2 项目质量管理 (17)10.2.1 制定严格的质量标准 (17)10.2.2 强化过程控制 (17)10.2.3 加强质量评估 (17)10.2.4 提高人员素质 (17)10.3 项目评估与优化建议 (17)10.3.1 效益评估 (17)10.3.2 技术评估 (17)10.3.3 过程评估 (17)10.3.4 优化建议 (17)第1章项目背景与目标1.1 现有生产线状况分析我国制造业的快速发展,自动化生产线在提高生产效率、降低生产成本、提升产品质量方面发挥着重要作用。
自动化项目升级改造方案doc
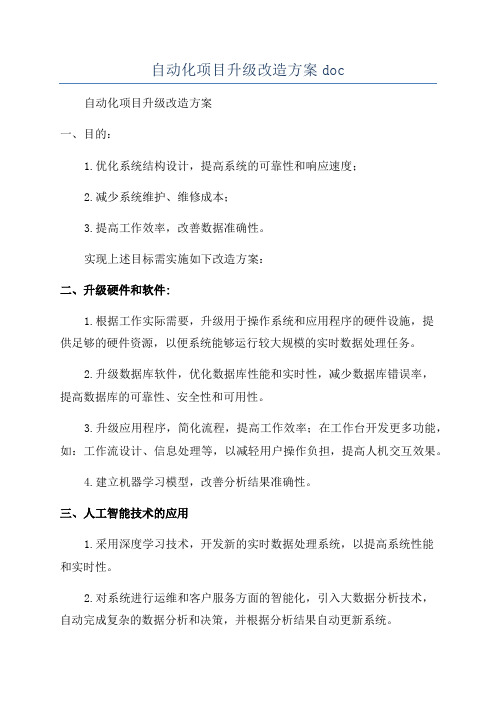
自动化项目升级改造方案doc
自动化项目升级改造方案
一、目的:
1.优化系统结构设计,提高系统的可靠性和响应速度;
2.减少系统维护、维修成本;
3.提高工作效率,改善数据准确性。
实现上述目标需实施如下改造方案:
二、升级硬件和软件:
1.根据工作实际需要,升级用于操作系统和应用程序的硬件设施,提
供足够的硬件资源,以便系统能够运行较大规模的实时数据处理任务。
2.升级数据库软件,优化数据库性能和实时性,减少数据库错误率,
提高数据库的可靠性、安全性和可用性。
3.升级应用程序,简化流程,提高工作效率;在工作台开发更多功能,如:工作流设计、信息处理等,以减轻用户操作负担,提高人机交互效果。
4.建立机器学习模型,改善分析结果准确性。
三、人工智能技术的应用
1.采用深度学习技术,开发新的实时数据处理系统,以提高系统性能
和实时性。
2.对系统进行运维和客户服务方面的智能化,引入大数据分析技术,
自动完成复杂的数据分析和决策,并根据分析结果自动更新系统。
- 1、下载文档前请自行甄别文档内容的完整性,平台不提供额外的编辑、内容补充、找答案等附加服务。
- 2、"仅部分预览"的文档,不可在线预览部分如存在完整性等问题,可反馈申请退款(可完整预览的文档不适用该条件!)。
- 3、如文档侵犯您的权益,请联系客服反馈,我们会尽快为您处理(人工客服工作时间:9:00-18:30)。
自动化项目升级改
造方案
伟星自动化项目升级改造
建设方案
浙江中创科联智能装备技术有限公司哈工大工研院智控所
1.系统研制背景 (2)
1.1系统的行业应用背景介绍 (2)
1.2系统的国内外现状 (2)
1.3我们的产品、行业及技术优势 (2)
2.客户对项目的需求描述 (4)
2.1 功能需求 (4)
2.2 性能需求 (6)
3.项目需求分析 (7)
3.1 功能需求分析 (7)
3.2 性能需求分析 (7)
4. 系统设计 (7)
4.1系统介绍 (7)
4.2布局示意图 (8)
4.3系统操作流程设计 (9)
4.4系统组成 (11)
4.5重要模块设计 (12)
5.供货范围 (15)
6.关于我们 (22)
1.系统研制背景
1.1系统的行业应用背景介绍
随着加工企业生产发展的需要,劳动力市场人员紧缺,人力成本逐年攀升,不可预见的风险因素,为企业的生产带来了不必要的制约因素。
能否减人增效,增加企业经济效益,同时保证生产质量,实现批量化、批次化,已经成为当今企业发展的一大难题。
1.2系统的国内外现状
根据调研信息的掌握和了解,当前国内外企业生产模式,主要采取以下几种工作方式:
人工手动作业
由人工完成全部的作业,比如将生产的货物进行灌装、封包,经过叉车、推车等辅助设备,将加工货物运送到下一工位,该种工作方式为。