工艺阐述及流程图
焦油加工工艺流程简述及流程图

工艺流程简述焦油I段工艺流程焦油是一种成分复杂的混合物,根据焦油各组分沸点的不同,可通过蒸馏将各组分富集到相应的馏分中,为进一步提纯提供原料。
焦油在焦油大槽中,经过均和、加热、静置、脱水,用焦油泵输送到焦油中间槽。
脱水塔进料泵将焦油从中间槽底部抽出,经焦油加热器与蒸汽换热,加热至115-130℃进入脱水塔。
脱水塔顶部出来的蒸汽和少量轻油经脱水塔轻油冷却器冷却后,经油水分离器将分离水排出,轻油自流至轻油槽,塔底含水<0.5%的焦油由加热炉进料泵抽出经管式炉加热至400±5℃后,打入聚合塔。
聚合塔顶部排出的油气进入分馏塔,进行分离,聚合塔底沥青经化验合格后放料,进入高置槽,再经链板机冷却后堆放外销。
聚合塔顶部出来的油气进入分馏塔第52层(分馏塔由55层浮阀塔板组成),进入分馏塔的油气在上升过程中,与塔顶1层轻油回流液接触,轻油油气由分馏塔顶部排出,经轻油冷却器冷却后进入轻油回流槽。
轻油回流槽内的轻油,一部分用轻油回流泵打入分馏塔1层回流,一部分满流至轻油槽(自轻油回流槽液位600mm处)。
酚萘洗三混馏分自分馏塔26、28、30、32层采出,经三混冷却器进入三混贮槽,三混馏分自三混贮槽底抽出入洗涤工序或装车线外售。
I蒽油馏分自分馏塔47、49层采出,经I蒽油冷却器自流至I蒽油贮槽,I蒽油用泵打入蒽油贮槽或入装车线外售。
塔底排出的II蒽油经II蒽油冷却器进入II蒽油中间槽,再经II蒽油输送泵输送至II蒽油贮槽,II蒽油由槽底装车线装车外售。
二、焦油II段工艺流程本焦油连续蒸馏装置采用单塔常压蒸馏工艺流程。
工艺流程见图所示。
原料焦油用焦油原料泵从焦油贮槽抽出送往焦油加热器,加热至110-130℃后进入脱水塔。
在此蒸出的部分轻油和水经轻油凝缩器(I)冷却,进入油水分离器(I),轻油与水分离进入回流柱,分离出的水排入酚水分离池处理。
脱水塔底部出来的无水焦油通过加热炉进料泵,经管式炉辐射段加热至385-405℃后进入聚合塔,使馏分和沥青分离。
吹瓶车间工艺流程图以及流程说明
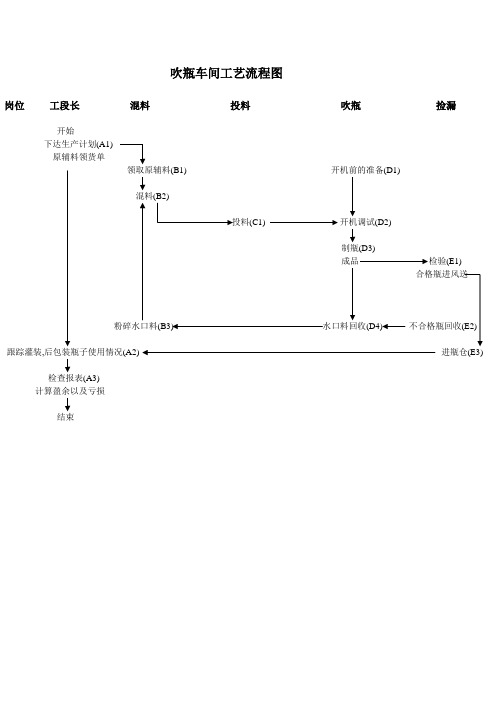
吹瓶车间工艺流程图岗位工段长混料投料吹瓶捡漏开始下达生产计划(A1)原辅料领货单领取原辅料(B1) 开机前的准备(D1)混料(C1) 开机调试(D2)制瓶(D3)成品检验(E1)粉碎水口料(B3) 水口料回收(D4) 不合格瓶回收跟踪灌装,后包装瓶子使用情况(A2) 进瓶仓(E3)检查报表(A3)计算盈余以及亏损结束流程说明开始编号:A1 岗位:工段长工序:下达生产计划,原料领货单.生产主办确认生产计划,工段长明确的对每个岗位下达生产任务,以及注意事项.以生产计划到生产统计处领取原料领货单.编号:B1 岗位:混料工工序:领取原料.原辅料名称:吹瓶机所用原辅料: 5502 色母以原料领货单到仓库领取原料,确认原辅料是否符合工艺和质量要求,以及批次,生产日期,并做好记录.记录填写要求:及时、准确、真实,并且具有可追溯性.编号:D1 岗位:吹瓶工工序:开机前的准备.检查机器是否有零、部件损伤,检查螺钉是否有松脱,检查电线、电缆是否有损坏、脱落,如有损坏,应及时更换或修理;检查挤出机料斗内是否有杂物并清理干净,然后打开下料闸门。
检查各马达是否运转正常,转动方向须与箭头方向一致。
按油泵启动按钮,检查各动作是否正常,是否有漏油现象。
检查各发热圈、风机、热电耦是否正常。
检查冷却水温度、压缩空气压力是否达到规定数值。
机器升温(升温时应注意:13-20升温段要关闭.当1-12升温段达到设定数值时,打开13-20升温段升温).开启车间成品传送带回收料传送带.并调整速度到适当数值.编号:B2 岗位:混料工工序:混料,填报表原辅料之间添加比例:100:1备注:5502色母每袋是25kg.拌料过程添加回收料的比例1)吹瓶回收料添加为33% (废料来源不合格瓶、瓶头、瓶尾)2)灌装回收料添加为30% (废料来源不合格品:漏奶、封口不良等,使用方法切去带有吕膜的瓶口然后清洗干净,晾干最后粉碎)3)后段回收料添加为15% (废料来源使从杀菌车之后捡漏工捡出的不合格品:漏奶、封口不良等,使用方法切去带有吕膜的瓶口然后清洗干净,晾干最后粉碎;)备注:添加回收料之前必须对回收料进行检查,做到无水,无油,无杂质,无铁削.拌料前准备:1)检查是否有原辅料,原辅料是否合格品2)检查拌料机是否正常运转(检查电源、电眼、各个按钮)3)检查拌料时间是否调节到10分钟拌料过程:先将把拌料机盖子扣打开,打开盖子,按上面比例加入原辅料和回收料.加入回收料过程必须加入挑拣后的回收料盖上盖子,上好盖子扣调节时间(在控制箱有一个调节时间按钮时间调节到10分钟)启动拌料机(启动按钮在控制箱为绿色按钮、红色按钮为停止按钮)拌料机运行10分钟之后自动停止(停止之后代表料以拌好).备注:拌料时间10分钟/次报表填写:报表填写要求:及时、准确、真实,并且具有可追溯性.编号:C1 岗位:投料工工序:投料混合料用编织袋卸装出来,放上手拉车.到达料斗处,打开料斗盖, 检查料斗内是否有杂物并清理干净.投入混合料,(投料要求:混合料最多占用料斗空间的三分之二.)盖好料斗盖.通知吹瓶工混合料已到位.编号:D2 岗位:吹瓶工工序:开机调试.开机步骤:打开主油泵,伺服油泵,点击手动并运行一周,打开挤出电机,点击下料键(下料时螺杆应低速运转(5-10),且持续时间不得超过5分钟).点击自动画面,点击自动复位,左右自动.当料胚位置和模具内测底部成水平线时,按下启动键.不合格瓶及排除:不合格瓶:瓶尾过长过短、毛边、瓶壁薄厚不均、瓶子重量太轻或太重、瓶子吹气不足或吹不成形排除:瓶尾过长过短:当出现瓶尾过长或过短时可通过减慢或加快螺杆转速进行调节,如过是单个瓶子尾巴长度不适可调节模头上方的螺母,使其顺时针旋转可减慢下料速度使瓶尾减短,逆时针旋转可加快下料速度使瓶尾加长。
轧钢厂生产工艺流程图及简介
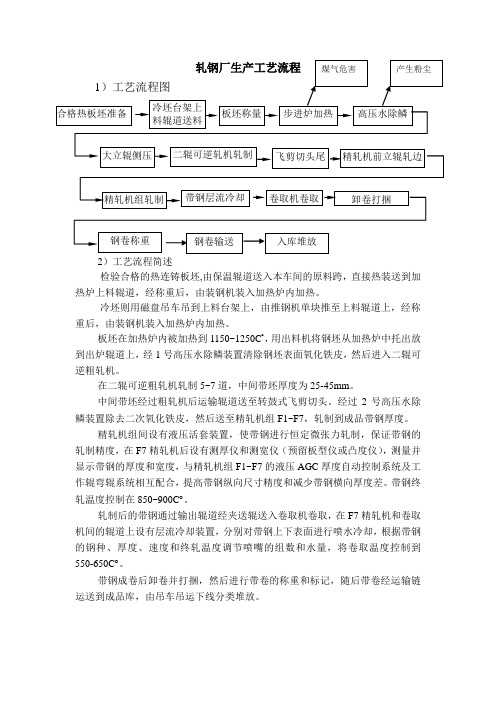
2)工艺流程简述
检验合格的热连铸板坯,由保温辊道送入本车间的原料跨,直接热装送到加热炉上料辊道,经称重后,由装钢机装入加热炉内加热。
冷坯则用磁盘吊车吊到上料台架上,由推钢机单块推至上料辊道上,经称重后,由装钢机装入加热炉内加热。
板坯在加热炉内被加热到1150~1250C︒,用出料机将钢坯从加热炉中托出放到出炉辊道上,经1号高压水除鳞装置清除钢坯表面氧化铁皮,然后进入二辊可逆粗轧机。
在二辊可逆粗轧机轧制5~7道,中间带坯厚度为25-45mm。
中间带坯经过粗轧机后运输辊道送至转鼓式飞剪切头。
经过2号高压水除鳞装置除去二次氧化铁皮,然后送至精轧机组F1~F7,轧制到成品带钢厚度。
精轧机组间设有液压活套装置,使带钢进行恒定微张力轧制,保证带钢的轧制精度,在F7精轧机后设有测厚仪和测宽仪(预留板型仪或凸度仪),测量并显示带钢的厚度和宽度,与精轧机组F1~F7的液压AGC厚度自动控制系统及工作辊弯辊系统相互配合,提高带钢纵向尺寸精度和减少带钢横向厚度差。
带钢终轧温度控制在850~900C︒。
轧制后的带钢通过输出辊道经夹送辊送入卷取机卷取,在F7精轧机和卷取机间的辊道上设有层流冷却装置,分别对带钢上下表面进行喷水冷却,根据带钢的钢种、厚度、速度和终轧温度调节喷嘴的组数和水量,将卷取温度控制到550-650C︒。
带钢成卷后卸卷并打捆,然后进行带卷的称重和标记,随后带卷经运输链运送到成品库,由吊车吊运下线分类堆放。
生产工艺流程图和工艺描述
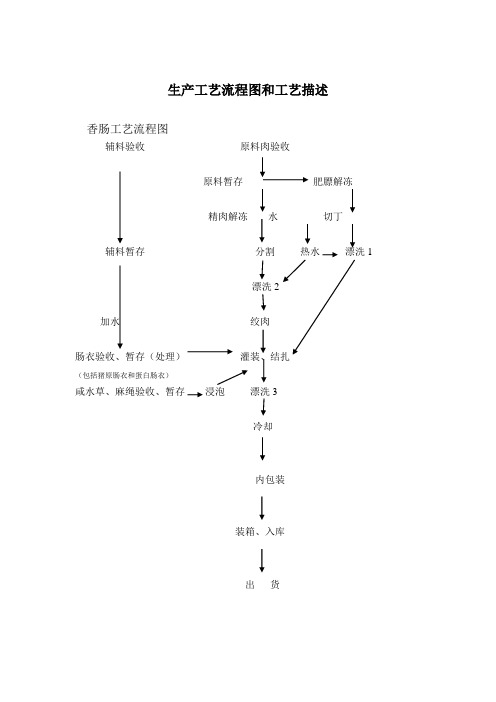
按照原料肉验收程序进行,并要求供应商提供兽药残留达标保证函及兽医检疫检验证明
辅料验收、暂存
化验室、仓库
按验收规程进行验收
肥膘验收、暂存
化验室、仓库
按验收规程进行验收
肠衣验收
化验室
按验收规程进行验收
肠衣处理
腊味加工间
天然猪肠衣加工前需用洁净加工用水冲洗,人造肠衣灌装前需用洁净加工用水润湿
咸水草、麻绳验收
中心温度≦25℃
内包装
真空包装机、热封口机
内包装间
将待包装腊肉去绳后按不同规格称重,装塑料袋、真空包装封口
装产品装彩袋封口,按不同规格装箱、核重、扣扎放入成品库并挂牌标识。
化验室、仓库
按验收程序进行验收
解冻
解冻间
肉类解冻分割间
温度≦18℃、18~20h
分割、修整
分割台、刀具
肉类解冻分割间
挑筋骨、淋巴等杂物,修整边缘。整个操作均在温度≦12℃的条件下进行。
切条
工作台、刀具
肉类解冻分割间
切成原1.5-1.8cm肉条,要求一致,厚薄均匀。温度≦12℃。
漂洗
水池
肉类解冻分割间
生产工艺流程图和工艺描述香肠工艺流程图辅料验收原料肉验收原料暂存肥膘解冻精肉解冻辅料暂存分割热水漂洗加水绞肉肠衣验收暂存处理灌装结扎包括猪原肠衣和蛋白肠衣咸水草麻绳验收暂存浸泡漂洗冷却内包装装箱入库香肠加工工艺说明加工步骤使用设备操作区域加工工艺的描述与说明原料肉验收暂存化验室仓按照原料肉验收程序进行并要求供应商提供兽药残留达标保证函及兽医检疫检验证明辅料验收暂按验收规程进行验收肥膘验收暂按验收规程进行验收肠衣验收化验室按验收规程进行验收肠衣处理腊味加工间天然猪肠衣加工前需用洁净加工用水冲洗人造肠衣灌装前需用洁净加工用水润湿咸水草麻绳验收化验室按验收规程进行验收暂存仓库浸泡腊味加工间咸水草麻绳加工前需用洁净加工用水浸泡使之变软解冻解冻间肉类解冻分181820h恒温解冻间空气解冻分割分割台刀将原料肉筋键淋巴脂肪剔除并分割成约3cm加工步骤使用设备操作区域加工工艺的描述与说明漂洗水池肉类解冻分加工用水漂洗将肉的污血冲洗干净绞肉绞肉机肉类解冻分12以下采用5mm切成05cm长的立方漂洗水池肉类解冻分水温4560洗去表面游离油脂碎灌装结扎灌肠机香肠加工间按产品的不同规格调节肠体长度8001200kgh温度12漂洗水池香肠加工间水温4560清洗肠体表面油脂肉预冷车间12下冷却051小时中心温度25内包装真空机电内包装间将待包装腊肠去绳后按不同规格称重装塑料袋真空包装封口装箱入库外包装间成品仓库将真空包装的产品装彩袋封口按不同规格装箱核重扣扎放入成品库并挂牌标识
工艺流程图(方案流程图和施工流程图)、设备布置图和管路布置图
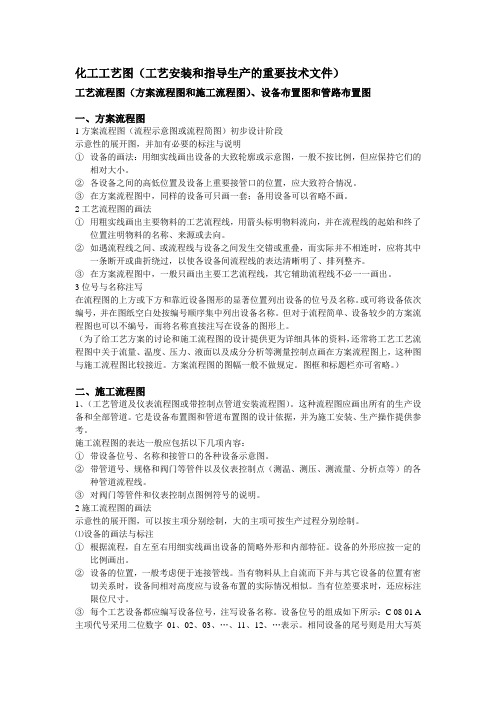
化工工艺图(工艺安装和指导生产的重要技术文件)工艺流程图(方案流程图和施工流程图)、设备布置图和管路布置图一、方案流程图1方案流程图(流程示意图或流程简图)初步设计阶段示意性的展开图,并加有必要的标注与说明①设备的画法:用细实线画出设备的大致轮廓或示意图,一般不按比例,但应保持它们的相对大小。
②各设备之间的高低位置及设备上重要接管口的位置,应大致符合情况。
③在方案流程图中,同样的设备可只画一套;备用设备可以省略不画。
2工艺流程图的画法①用粗实线画出主要物料的工艺流程线,用箭头标明物料流向,并在流程线的起始和终了位置注明物料的名称、来源或去向。
②如遇流程线之间、或流程线与设备之间发生交错或重叠,而实际并不相连时,应将其中一条断开或曲折绕过,以使各设备间流程线的表达清晰明了、排列整齐。
③在方案流程图中,一般只画出主要工艺流程线,其它辅助流程线不必一一画出。
3位号与名称注写在流程图的上方或下方和靠近设备图形的显著位置列出设备的位号及名称。
或可将设备依次编号,并在图纸空白处按编号顺序集中列出设备名称。
但对于流程简单、设备较少的方案流程图也可以不编号,而将名称直接注写在设备的图形上。
(为了给工艺方案的讨论和施工流程图的设计提供更为详细具体的资料,还常将工艺工艺流程图中关于流量、温度、压力、液面以及成分分析等测量控制点画在方案流程图上,这种图与施工流程图比较接近。
方案流程图的图幅一般不做规定。
图框和标题栏亦可省略。
)二、施工流程图1、(工艺管道及仪表流程图或带控制点管道安装流程图)。
这种流程图应画出所有的生产设备和全部管道。
它是设备布置图和管道布置图的设计依据,并为施工安装、生产操作提供参考。
施工流程图的表达一般应包括以下几项内容:①带设备位号、名称和接管口的各种设备示意图。
②带管道号、规格和阀门等管件以及仪表控制点(测温、测压、测流量、分析点等)的各种管道流程线。
③对阀门等管件和仪表控制点图例符号的说明。
焦化厂工艺流程文字叙述及流程图

备煤炼焦所用精煤,一方面由外部购入,另一方面由原煤经洗煤后所得,洗精煤由皮带机送入精煤场。
精煤经受煤坑下的电子自动配料称将四种煤按相应的比例送到带式输送机上除铁后,进入可逆反击锤式粉碎机粉碎后(小于3mm占90%以上),经带式输送机送至焦炉煤塔内供炼焦用。
炼焦装煤推焦车在煤塔下取煤,捣固成煤饼后,按作业计划从机侧推入炭化室内。
煤饼在炭化室内经过一个结焦周期的高温干馏,炼成焦炭并产生荒煤气。
炭化室内的煤饼结焦成熟后,由装煤推焦机推出并通过拦焦机的导焦栅送入熄焦车内。
熄焦车由电机牵引至熄焦塔熄焦。
熄焦后的焦炭卸至凉焦台,冷却后送往筛焦楼进行筛分和外运。
煤在干馏过程中产生的荒煤气汇集到炭化室的顶部空间,经上升管、桥管进入集气管。
700℃的荒煤气在桥管内经过氨水喷洒后温度降至85℃左右,煤气和冷凝下来的焦油氨水一起经吸煤气管道送入煤气回收车间进行煤气净化及焦油回收。
焦炉加热燃用的净化煤气经预热器预热至45℃左右进入地下室,通过下喷管把煤气送入燃烧室立火道,燃烧后的废气经烟道、烟囱排入大气。
冷鼓由焦炉送来的80-83℃的荒煤气,沿吸煤气管道入气液分离器。
经气液分离后,煤气进入初冷器进行两段间接冷却;上段用32℃循环水冷却煤气,下段用16-18℃低温水冷却煤气,使煤气冷却至22℃,然后经捕雾器入电捕焦油器除去悬浮的焦油雾后进入鼓风机,煤气由鼓风机加压送至脱硫工段。
在初冷器下段用含有一定量焦油、氨水的混合液进行喷洒,以防止初冷器冷却水管外壁积萘,提高煤气冷却效果。
由气液分离器分离出的焦油氨水混合液自流入机械化氨水澄清槽,进行氨水、焦油和焦油渣的分离。
分离后的氨水自流入循环氨水中间槽,用泵送到焦炉集气管喷洒冷却荒煤气,多余的氨水(即剩余氨水)送入剩余氨水槽,焦油自流入焦油中间槽,然后用泵将焦油送至焦油贮槽,静置脱水后外售,分离出的焦油渣定期用车送至煤场掺入精煤中炼焦。
脱硫来自冷鼓工段的粗煤气进入脱硫塔下部与塔顶喷淋下来的脱硫液逆流接触洗涤后,煤气经捕雾段除去雾滴后全部送至硫铵工段。
(完整)化妆品生产工艺及流程图
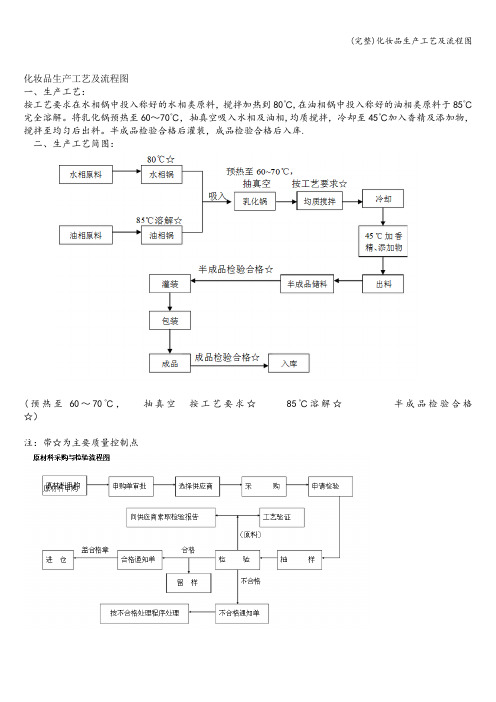
化妆品生产工艺及流程图
一、生产工艺:
按工艺要求在水相锅中投入称好的水相类原料,搅拌加热到80℃,在油相锅中投入称好的油相类原料于85℃完全溶解。
将乳化锅预热至60~70℃,抽真空吸入水相及油相,均质搅拌,冷却至45℃加入香精及添加物,搅拌至均匀后出料。
半成品检验合格后灌装,成品检验合格后入库.
二、生产工艺简图:
(预热至60~70℃,抽真空按工艺要求☆85℃溶解☆半成品检验合格☆)
注:带☆为主要质量控制点
灌装工序流程图:
灌装设备清洗置于温水中用擦子擦洗用去离子水第二次冲洗用75%酒精溶液浸泡十分钟用风筒吹干,不得留有水分。
成品油罐区工艺流程叙述及流程图
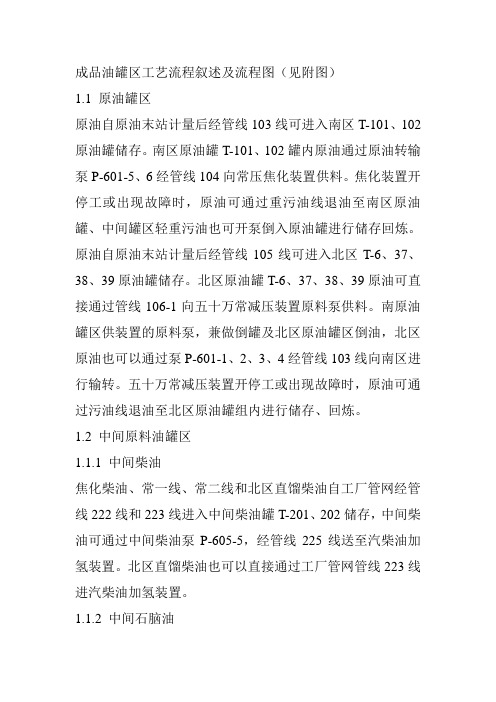
成品油罐区工艺流程叙述及流程图(见附图)1.1 原油罐区原油自原油末站计量后经管线103线可进入南区T-101、102原油罐储存。
南区原油罐T-101、102罐内原油通过原油转输泵P-601-5、6经管线104向常压焦化装置供料。
焦化装置开停工或出现故障时,原油可通过重污油线退油至南区原油罐、中间罐区轻重污油也可开泵倒入原油罐进行储存回炼。
原油自原油末站计量后经管线105线可进入北区T-6、37、38、39原油罐储存。
北区原油罐T-6、37、38、39原油可直接通过管线106-1向五十万常减压装置原料泵供料。
南原油罐区供装置的原料泵,兼做倒罐及北区原油罐区倒油,北区原油也可以通过泵P-601-1、2、3、4经管线103线向南区进行输转。
五十万常减压装置开停工或出现故障时,原油可通过污油线退油至北区原油罐组内进行储存、回炼。
1.2 中间原料油罐区1.1.1 中间柴油焦化柴油、常一线、常二线和北区直馏柴油自工厂管网经管线222线和223线进入中间柴油罐T-201、202储存,中间柴油可通过中间柴油泵P-605-5,经管线225线送至汽柴油加氢装置。
北区直馏柴油也可以直接通过工厂管网管线223线进汽柴油加氢装置。
1.1.2 中间石脑油a) 加氢石脑油自工厂管网经管线233线进入中间石脑油罐T-203、204储存,加氢石脑油可通过石脑油原料油泵P-603-11,经管线235线送至催化重整装置。
也可通过石脑油装车泵P-603-10,经管线234线去火车装车设施进行装车。
b) 汽柴油加氢、催化重整轻石脑油自工厂管网237线经233线进入中间石脑油罐T-203、204储存、出厂。
c) 精制石脑油自工厂管网经管线251线进入精制石脑油罐T-207、208储存,可通过精制石脑油泵P-603-7返送至催化重整装置。
d) 南区常顶油和北区直馏石脑油自工厂管网管线263线和262线进入直馏石脑油罐T-209、210储存,可通过直馏石脑油泵P-603-8,经管线265线送至催化重整装置。
- 1、下载文档前请自行甄别文档内容的完整性,平台不提供额外的编辑、内容补充、找答案等附加服务。
- 2、"仅部分预览"的文档,不可在线预览部分如存在完整性等问题,可反馈申请退款(可完整预览的文档不适用该条件!)。
- 3、如文档侵犯您的权益,请联系客服反馈,我们会尽快为您处理(人工客服工作时间:9:00-18:30)。
工艺阐述及流程图
预处理车间工艺流程说明
米糠由提升机送入车间进行清理,清理后的米糠经提升机糠粞分离筛进行糠粞分离,然后落入比重去石机去除米粞,米粞装袋,米糠由刮板输送机送至调制锅进行调质,调质后的米糠经膨化喂料绞龙、磁选器除铁后落入膨化机,米糠膨化料落入逆流翻板烘干机进行烘干。
烘干后的膨化料经刮板输送机送往浸出车间。
膨化多出部分经冷却后经皮带输送机送往库房散装储存。
浸出车间工艺流程说明
浸出工序
米糠膨化料经进料刮板输送机,送入浸出器,料在浸出器中由进料口到出料口运行一周,在进料口和出料口之间用递减浓度的混合油进行喷淋,在进入沥干段前,再经新鲜溶剂喷淋,沥干后的湿粕从浸出器出料格由拨料器排出进入湿粕刮板。
浓混合油由浓混合油泵打入旋液分离器后再经混合油过滤器除去粕粉后进入混合油罐。
蒸脱工序
浸出器出来的含溶湿粕由湿粕刮板经料封绞龙送入DTDC蒸脱机的预脱层,底部用间接蒸汽加热,脱去部分溶剂;经预脱后的湿粕进入蒸脱层,蒸脱层设自动控制保持一定的料层,底部通入直接蒸汽,脱去全部溶剂,同时部分蒸汽凝结在粕中,粕的水分会部分升高。
脱溶粕由旋转阀定量下落到烘干层,烘干层保持一定的料位,进行去水干燥过程,接着进入冷却层冷却.最后由自动料门控制出料,再由粕刮板送入粕库。
从脱溶机顶部出来的溶剂和水蒸汽的混合汽,通入第一长管蒸发器壳程作为一蒸混合油的加热介质。
蒸发工序
混合油由一蒸喂料泵从混合油罐打入第一长管蒸发器管程,脱溶机的混合汽为一蒸的加热介质。
蒸发的溶剂经分离室进入真空冷凝器,分离室下部设有液位控制装置保持液封,第一蒸发器由低真空喷射泵保持一定的残压,使一蒸混合油中的溶剂在负压下蒸发,可降低溶剂的沸点,提高工作蒸汽利用率。
经一蒸浓缩后的混合油,由二蒸喂料泵打入第二长管蒸发器蒸发。
二蒸也为负压蒸发,壳程用间接蒸汽加热,蒸发的溶剂汽经分离室进入真空冷凝器,分离室下部设有液位控制装置保持液封,出口混合油由真空吸入混合油加热器,混合油加热器设有温度控制装置以保持进汽提塔的混合油达到规定的温度后进入汽提塔。
混合油从汽提塔顶部进到塔内的碟盘中,一层层降下,同时底部喷入直接蒸汽,脱去残留溶剂。
顶部出口接真空冷凝器,由高真空喷射泵保持汽提塔在负压下工作,汽提塔底部安装有液位控制器确保液封和成品油稳定的流量,毛油由汽提塔抽出泵从塔底抽出再经毛油冷却器冷却后进入毛油箱,再由毛油泵送入炼油车间。
溶剂冷凝及分水工序
真空冷凝器、节能器冷凝器、汽提冷凝器的冷凝液汇集到集液罐,然后由节能器喂料泵打入节能器上部。
一蒸壳程未凝汽,蒸水罐混合汽,低真空蒸汽喷射泵喷入蒸汽均通入节能器中,与打入的冷凝液直接进行热交换,节能器的未凝汽进入节能器冷凝器,节能器冷凝液和一蒸壳程冷凝液直接流入分水器。
节能器冷凝器和汽提冷凝器的自由气体,分水器、溶剂库自由气体汇集到一起进入最后冷凝器,最后冷凝器出来的未凝气由尾气风机吸入石蜡回收装置。
分水器的溶剂相由上面流入溶剂库部分循环使用,水相排入蒸水罐中,蒸水罐底部通入直接汽蒸发残留溶剂后排入水封池。
尾气吸收工序
自汽提冷凝器、节能冷凝器、集液罐、综合容器出来的未凝汽体均进入空气平衡罐,再进入最后冷凝器回收溶剂,最后冷凝器不凝结汽体进入矿物油回收装置回收残留溶剂,自由气体由尾气风机经阻火器排入大气。
打包车间工艺流程说明
米糠粕经刮板输送机送入粕库,再由输送设备送入自动打包称中自动称重包装。
打包间设置存料箱,用于自动称重包装秤故障时粕的暂存,暂存与存料箱中的粕可通过台秤计量后手动打包。
工艺流程图
工艺特点
预处理车间
全部工艺设备连续化、机械化操作;
设置电脑自动化控制系统;
采用特殊设计的负压蒸发节能工艺,降低蒸汽消耗;
为保证米糠毛油质量,有利于后序毛油蒸发和精炼,对米糠进行糠粞分离,使糠粞含量在1%以下。
糠粞分离工序设置在糠库内,以防止冬季糠粞分离所使用的刹克龙及管道出现挂蜡现象
浸出车间
全部工艺设备可实现连续化、机械化操作;
设置电脑自动化控制系统;
采用特殊设计的负压蒸发节能工艺,降低蒸汽消耗;
采用国际先进水平的环形浸出器,DTDC蒸脱机,结构合理,运行可靠,从而保证粕残油和溶耗在最低水平;
操作体系要全封闭,以避免油脂氧化,确保浸出毛油品质,使精炼率可以提高;
采用高性能的矿物油回收系统,采用最新型的金属波纹填料,使尾气中的溶剂最大量的得以回收;
对混合油采用两级除杂处理,浓混合油首先经进入旋液分离器除去颗粒较大粕粉、然后再进入混合油过滤器进行二次除杂,要保证过滤后排渣效果,不能出现堵塞现象!经过滤后的混合油基本不含固体杂质,要保持混合油蒸发系统清洁运行和毛油质量。
经过滤后比较清洁的混合油打入混合油暂存罐,经以进一步沉淀,混合油罐底部的沉淀物定期由回渣泵打入浸出器。
混合油的两道过滤和负压
蒸发工艺的运用,大大减少蒸发系统的结垢,蒸发系统的清理周期可延长。
采用负压蒸发工艺,对DTDC出来的混合蒸汽余热要进行二次利用,节约一蒸加热蒸汽,降低蒸发、汽提温度,从而降低毛油残溶和总挥发物,降低毛油色泽。
采用热泵技术,将冷凝水罐中蒸汽喷入二蒸作为热源,减少蒸汽消耗。
将浸出车间的全部蒸汽乏水收集起来用泵打入锅炉房二次利用,乏水的余热要进行有效利用,节省车间生产用水。
各运转设备在电气上都要有过载保护装置,固体物料输送设备都设有轴监视器,并有运行电流检测报警装置以及可靠的连锁控制程序确保安全运转。
在入浸刮板机头部要安装有可燃气体检测器,并在入浸刮板和封闭绞龙之间安装气动插板阀。
当出现异常情况,可燃气体检测器报警时,及时处理故障,如果故障暂时不能及时处理,可以先关闭气动插板阀,可以有效防止溶剂气体倒灌至预处理车间。
在出粕口处要安装有可燃气体检测器,如果出现异常情况会及时报警,防止含溶剂过高的粕进入粕库发生危险。
在浸出器和分水箱底部靠近地面的地方要安装可燃气体检测器,如果发生混合油或溶剂泄漏,可燃气体检测器会报警,提醒启动车间换气风机,迅速降低车间内可燃气体的浓度;
在蒸水罐出水口,水封池的地方均要安装安装有可燃气体检测器,如果发生溶剂泄漏,可燃气体检测器会报警,提醒操作人员及时检查。
打包车间
设计了自动打包和手动打包两种打包方式,以自动打包为主。
当遇到自动打包秤临时故障或维修时,可利用手动打包方式。
减小了对生产车间的影响。
精炼车间工艺流程说明
本车间采用半连续式生产工艺:
米糠毛油—过滤—水化脱胶(必要时碱炼)—脱蜡—脱色—脱酸(臭)—米糠三级油
毛油经过加热后进入到过滤器进行过滤,滤出毛油中的杂质和粘液,滤后的油经加热后经过两道酸洗、水化、加碱脱皂后进行水洗,水洗后的清油经真空干
燥后进入下一工段。
干燥后的清油先进入油结晶罐结晶。
结晶罐由变频调速控制,可以使结晶好而结实,包油少,便于过滤。
过滤机为热卸式过滤机,用热水化蜡,不用拆卸,劳动强度小。
过滤油泵为螺杆泵,保证不破坏结晶体。
脱出的蜡打入蜡干燥器中真空干燥除去水分,由泵打入室外装袋存放。
脱蜡完的米糠油加热后与白土混合,然后进入脱色塔脱色。
白土用风运系统提至暂存罐,生产时经连续计量加入到油中。
脱色后的油泵入叶片过滤机进行过滤,两台过滤机交替使用实现连续生产过程。
过滤中,浊油打回脱色塔后再过滤,脱色清油经二道安全过滤后送至下道工序。
过滤后的白土废渣用小车送出车间。
经脱色的米糠油先进入析气器,然后由泵输送先进入换热器中同脱臭油进行热交换回收热量,换热后的油经导热油加热器加热到脱臭要求的温度后进入闪蒸脱酸塔脱出绝大部分的脂肪酸,然后再用泵将油送到脱臭塔脱臭。
闪蒸脱酸塔为填料结构,脱臭真空由四级蒸汽喷射真空泵产生(保证真空度达到四级真空泵的要求)。
脱臭时油沿各层塔板溢流而下,脱臭塔通有直接蒸汽,油在高温高真空下除去臭味物质。
气体从塔顶和侧排汽管排出经脂肪酸捕集器捕集,不凝气体由真空泵抽出,捕集得到的脂肪酸一部分继续循环捕集脱臭溜出物,另一部分由泵打入车间外贮罐。
闪蒸塔和脱臭塔底部设有液位控制系统,保持稳定的液位。
脱臭油经过与脱色冷油换热后,再经过冷却器冷却至安全温度。
然后经抛光过滤、计量后送入车间外成品油罐贮藏。
不合格油可打到毛油罐重新处理。