数控机床自动换刀系统
数控机床的自动换刀系统操作指南

数控机床的自动换刀系统操作指南数控机床的自动换刀系统是现代机床中重要的工具,它的作用是实现多种刀具的自动切换,提高生产效率和加工精度。
本文将为您介绍数控机床的自动换刀系统的操作指南。
1. 系统概述数控机床的自动换刀系统由控制单元、刀库、刀臂、刀具以及相关传感器组成。
通过控制单元的指令,刀库中的刀具可以自动切换到刀臂上,实现刀具的自动更换。
2. 操作前的准备在操作数控机床的自动换刀系统之前,首先要进行以下的准备工作:- 确认机床的电源是否正常,机床内部是否处理干净。
- 确认自动换刀系统的刀库是否存放有足够的刀具。
- 确认程序中的执行代码是否正确,不会发生刀具碰撞。
3. 操作步骤以下是数控机床的自动换刀系统的操作步骤:(1) 手动操作模式:首先将机床设置为手动操作模式,确保机床处于不会自动运行的状态。
(2) 加载刀具:通过控制单元的操作指令,将所需刀具从刀库中选取出来。
(3) 位置定位:使用机床的控制面板或相关软件对刀臂进行位置定位,使其准确匹配刀具的安装位置。
(4) 刀具安装:将选取的刀具正确安装到刀臂上,确保刀具牢固固定,避免出现松动的情况。
(5) 参数设定:在机床的控制面板或相关软件中设定刀具的相关参数,如切削速度、进给速度等。
(6) 刀具校对:在刀具安装完成后,进行刀具校对的操作,确保刀具位置的准确性。
(7) 确认操作:在进行自动换刀操作之前,要仔细确认刀具的安装是否正确,刀具是否符合加工要求。
(8) 运行程序:确认刀具安装正确后,将机床切换到自动运行模式,在控制单元中选择相应的程序,运行自动换刀操作。
(9) 监测切换:在自动换刀操作过程中,通过机床的控制面板或相关软件实时监测刀具的切换过程,确保刀具的准确切换。
(10) 完成切换:当刀具切换完成后,机床会自动停止,并显示切换完成的提示信息。
4. 常见问题及解决方法在使用数控机床的自动换刀系统时,可能会遇到以下的问题,下面为您提供一些建议的解决方法:- 刀具松动:检查刀具安装是否正确,确保刀具紧固螺母牢固固定。
数控铣床自动换刀化改造(刀库式加工中心)

第一章绪论1.1 数控设备的发展历史>第一代数控系统:1952年至1959年,采川电子管元件。
>第二代数控系统:1959年开始,采刖晶体管元件。
>第三代数控系统:1965年开始,采川集成电路。
>第四代数控系统:1970年开始,采刖人规模集成电路及小型通用计算机。
>第五代数控系统:1974年开始,采用微处理机和微型计算机。
1.2 自动换刀系统的意义从换刀系统发展的历史米看,1956年日本富士通研究成功数控转塔式冲床,美国IBM公司同期也研制成功了“APT”(刀具程序控制装置)。
1958年美国K&T公司研制出带ATC(自动刀具交换装置)的加工中心。
1967年出现了FMS(柔性制造系统)。
1978年以后,加工中心迅速发展,带有ATC装置,可实现多种工序加工的机床,步入了机床发展的黄金时代。
1.1.1 加工中心加工中心机床的出现,加之CAD技术、信息技术、网络控制技术以及系统工程学的发展,为单机数控自动化向计算机控制的多机制造系统自动化方向发展,创造了必要的条件.计算机群控系统即直接数控(Direct NC-DNC)系统,就是这一发展趋向的具体体观。
DNC系统使用一台较大的计算机,控制与管理多台数控机床和数控加工中心,能进行多品种、多工序的加工。
加工中心机床配备有装载多把刀具的刀具库,有自动更换刀具的功能,一次装夹中可以完成钻、镗、铣、铰等工序,特别适用于箱体类零件的多面、多工序加工。
它能完成车削加工的同时,兼有铣、镗、钻孔、攻丝等功能。
1.1.2 柔性制造单元柔性制造单元(FMC)是由中心控制计算机、加工中心与自动交换工件(AWC,APC)装置所组成。
工件一次装夹后可在柔性制造单元中的加工中心上加工,使得加工的柔性(可编程性)、加工精度和生产效率更高。
在柔性制造单元中,中心控制计算机负责作业调度、自动检测与工况自动监控等功能。
工件装在自动交换工件装置(工作台)上在中心控制计算机控制下传送到加工中心上加工;加工中心接收中心控制计算机传送来的数控程序进行加工,并将工况数据送中心控制计算机处理,如工件尺寸自动检测和补偿,刀具损坏和寿命躲控等。
数控机床自动换刀系统的设计与优化方法

数控机床自动换刀系统的设计与优化方法数控机床自动换刀系统作为现代制造业中的关键设备之一,其设计和优化对于提高生产效率和产品质量至关重要。
本文将讨论数控机床自动换刀系统的设计原理、关键技术以及优化方法,旨在指导工程师和研究人员进行相关工作。
首先,数控机床自动换刀系统的设计原理主要包括以下几个方面:刀具库、刀具传递机构和换刀动作控制。
刀具库是存放刀具的地方,通常设计成可自动旋转、抬升和倾斜的结构,以便于刀具的选择和取放。
刀具传递机构用于将所需刀具从刀具库传递到机床主轴上,并确保刀具的正确位置和方向。
换刀动作控制则通过编程和传感器来实现,保证换刀过程的准确性和稳定性。
在设计数控机床自动换刀系统时,我们需要注意一些关键技术。
首先是刀具库的设计,刀具库的容量和结构需要根据实际工作中所涉及到的刀具种类和数量进行合理规划。
其次是刀具传递机构的设计,传递机构需要具备快速、准确的传递能力,同时要考虑到刀具重量对传递机构的负荷影响,确保稳定性。
换刀动作控制需要精确控制刀具的位置和方向,可以采用光电传感器或编码器等传感器,通过编程实现动作的控制和判断。
为了进一步优化数控机床自动换刀系统的性能,我们可以采取一些优化方法。
首先是刀具库的优化,可以采用高效的刀具存放方案,如采用自动尺寸检测技术,将刀具按照尺寸进行分类存放,方便快速选择和取放。
其次是刀具传递机构的优化,可以采用更先进的传递机构设计,如采用电磁吸盘或气动夹持装置等,提高传递速度和准确性。
此外,还可以通过改进换刀动作控制算法,优化换刀过程的稳定性和精度。
在优化设计过程中,还需要充分考虑数控机床自动换刀系统的可靠性和安全性。
可靠性是指系统在长时间运行中的稳定性和故障率,我们可以通过选用高质量的部件和进行严格的测试来提高可靠性。
安全性是指系统在使用过程中的安全保障,我们需要设置安全装置,如机械锁或密码锁等,防止误操作或意外伤害的发生。
总结起来,数控机床自动换刀系统的设计与优化需要考虑刀具库、刀具传递机构和换刀动作控制等关键技术。
数控机床自动换刀系统的设计与优化方法

数控机床自动换刀系统的设计与优化方法随着工业自动化的不断发展,数控机床自动换刀系统的设计与优化成为了现代制造业中的重要课题。
自动换刀系统的设计及其优化将直接影响到机床的生产效率、工件加工质量和操作人员的工作安全。
因此,本文将探讨数控机床自动换刀系统的设计原理以及进行系统优化的方法与技巧。
数控机床自动换刀系统一般包括刀库、刀臂、刀杆及刀具,其工作原理主要通过机械臂或伺服电机的驱动,将机床上的刀具自动更换。
而系统的设计与优化则需要考虑以下几个方面:首先,需要充分考虑机床的具体工艺需求,确定自动换刀系统的基本功能。
例如,切削加工中是否需要进行多种不同刀具的切换,是否需要对不同刀具进行刃磨和测量等。
不同工艺需求将直接影响到自动换刀系统的设计与优化。
其次,需要考虑自动换刀系统的结构设计。
合理的结构设计能够提高系统的稳定性和工作效率,并降低故障率。
一般来说,自动换刀系统的结构主要包括刀库结构、刀臂结构以及刀杆结构。
在设计过程中,需要充分考虑机床的空间限制、刀具数量以及换刀的速度等因素。
同时,需要关注自动换刀系统的动力传递和控制电路设计。
动力传递系统的设计主要包括伺服电机的选型、减速器的设计以及传动链的布置等。
而控制电路的设计则需要考虑自动控制装置和信号传输装置等,以确保系统的稳定性和可靠性。
另外,还需要考虑自动换刀系统的安全性。
刀具在运行过程中可能会产生较大的动力和惯性力,因此在设计过程中需要充分考虑刀具的固定、刀具与工件之间的安全间隙以及系统紧急停机装置的设置等,以确保操作人员的安全。
在完成基本的设计后,系统的优化工作则需从以下几个方面展开。
首先是换刀时间的优化。
通过减少换刀时间可以提高机床的利用率,并减少生产成本。
换刀时间的优化可以从刀具定位、刀具固定方式以及刀具检测等方面进行。
其次是系统的可靠性优化。
这需要考虑到刀库的结构设计、刀具的装卸方式以及系统故障的自我诊断与修复等。
同时,充分考虑刀具的损耗和磨损,合理安排刀具的使用周期,减少系统故障的发生。
数控机床自动换刀系统的故障排查与维修方法

数控机床自动换刀系统的故障排查与维修方法数控机床自动换刀系统在工业生产中扮演着重要角色,然而偶尔会遇到一些故障导致正常的生产工作受到干扰。
本文将介绍数控机床自动换刀系统常见故障的排查方法以及维修方法,帮助读者快速解决问题并恢复生产。
首先,我们来了解一下数控机床自动换刀系统的组成。
该系统由刀库、刀杆、刀座等主要组件构成。
故障通常出现在刀杆与刀座之间的连接部分。
常见的故障有刀杆卡滞、刀座松动、换刀定位错误等。
当遇到故障时,首先要做的是检查刀杆是否卡滞。
刀杆卡滞可能是由于过多的切屑或者油污导致的。
解决方法是清理刀杆和刀座之间的油污,以及及时清理刀座上的切屑。
此外,也应进行润滑保养,确保刀杆顺畅运行。
其次,如果刀座松动,我们可以采取以下步骤来解决问题。
首先,检查螺母是否松动,必要时紧固螺母。
其次,检查刀座与刀杆之间的连接是否紧密,避免松动。
如果刀座已经损坏或磨损,需要更换刀座。
最后,还应该检查刀座的弹簧是否失效,确认刀座的弹性是否符合要求。
换刀定位错误也是常见的故障之一。
如果发生换刀定位错误,首先要检查刀杆的长度和形状是否正常。
如果刀杆口径不匹配,需要更换合适的刀杆。
其次,刀座的定位销是否损坏,需要修复或者更换。
最后,还应检查换刀定位装置的传感器和控制系统是否正常,避免传感器故障导致定位不准确。
除了以上常见故障外,系统中的电气故障也可能导致自动换刀系统的故障。
在排查电气故障时,我们可以通过以下步骤来解决问题。
首先,检查电源线是否接触良好,确保电源正常供电。
其次,检查各个部件的电缆连接是否紧固,排除电线松动或者脱落的可能性。
如果电气故障仍然存在,建议寻求专业技术人员的帮助进行进一步的排查。
总结来说,数控机床自动换刀系统的故障排查与维修是一个复杂而又细致的过程。
在故障排查时,首先要根据故障现象进行针对性的检查,找出问题所在。
然后根据不同的故障类型采取相应的修复措施,如清洁、紧固或者更换部件。
若故障仍未解决,及时寻求专业技术人员的帮助。
基于PLC的数控加工中心自动换刀系统的研究
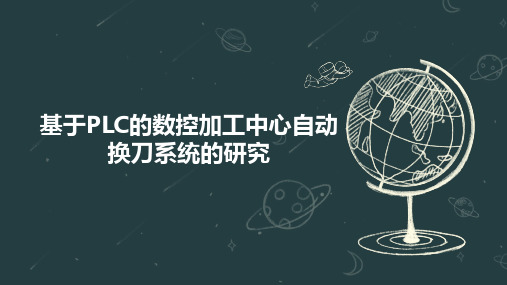
盘式刀库自动换刀控制系统的优势主要体现在以下几个方面。首先,自动换刀 控制系统可以显著提高加工效率,避免了手动更换刀具的繁琐过程,节省了大 量时间。其次,自动换刀控制系统可以降低工人的劳动强度,减少错误操作的 可能性,提高生产安全性。最后,自动换刀控制系统有利于实现工厂的自动化 和智能化,提升整体竞争力。
目前,加工中心自动换刀装置的研究主要集中在换刀方式、刀库设计、夹持机 构和控制系统等方面。其中,换刀方式是自动换刀装置的核心技术之一,直接 影响到换刀的效率和精度。按照换刀过程中是否有旋转动作,换刀方式可以分 为旋转式和非旋转式两种。旋转式换刀方式又可以分为刀具旋转和主轴旋转两 种,而非旋转式换刀方式则可以分为直插式和伸缩式两种。
盘式刀库自动换刀控制系统的工作原理基于计算机数值控制(CNC)技术,通 过接收加工中心的指令,控制机械手臂进行刀具的更换。首先,机械手臂在盘 式刀库中选择需要更换的刀具,然后将其抓取并移动到加工区域。接下来,机 械手臂将旧的刀具从主轴中取出,并将新的刀具安装到主轴上。最后,机械手 臂将更换下来的刀具放回盘式刀库的正确位置。
近年来,随着人工智能、机器学习和计算机视觉等技术的不断发展,加工中心 自动换刀装置的研究也在不断深入。这些技术的应用,可以实现更加智能化和 高效的换刀控制,从而提高加工中心的生产效率和加工质量。
在应用前景方面,加工中心自动换刀装置将会在更多领域得到应用。例如,在 航空航天、汽车制造、模具制造和医疗器械等领域,由于对加工精度和效率的 要求较高,因此对自动换刀装置的需求也将会不断增加。此外,在智能制造和 数字化工厂的建设中,加工中心自动换刀装置也将会成为其重要组成部分之一。
加工中心自动换刀装置的发展历程可以追溯到20世纪80年代,当时该技术还处 于研究和实验阶段。随着计算机技术、机械制造技术和液压气动技术的发展, 自动换刀装置的可靠性、稳定性和效率得到了不断提高。进入21世纪以来,随 着数控技术的快速发展和制造业的不断升级,加工中心自动换刀装置的应用范 围和需求量也不断增加。
数控机床技术中的自动换刀系统故障排解
数控机床技术中的自动换刀系统故障排解自动换刀系统是数控机床技术中的重要部分,它可以实现自动更换刀具,提高加工效率和精度。
然而,在使用自动换刀系统时,也会遇到一些故障问题。
本文将介绍一些常见的自动换刀系统故障,并提供相应的排解方法,以帮助操作者解决问题,保证机床的正常运行。
首先,自动换刀系统可能会出现刀具未正确安装的故障。
在使用自动换刀系统更换刀具时,操作者需要确保刀具正确安装,刀具夹持力适宜。
如果刀具没有正确安装,可能会导致刀具脱落或者加工质量下降。
解决这一问题的方法是通过检查刀具安装是否正确,调整夹持力并重新安装刀具。
其次,自动换刀系统可能会出现刀具不准确对刀的故障。
刀具对刀不准确可能会导致加工精度下降,甚至损坏工件。
产生这一故障的原因可能是夹刀手指和刀夹装配不正确,或者刀具对刀传感器故障。
要解决这一问题,操作者可以检查夹刀手指和刀夹的装配是否正确,并进行调整和更换。
如果是刀具对刀传感器故障,需要进行维修或更换。
另外,自动换刀系统还可能会出现换刀机构动作异常的故障。
换刀机构动作异常可能是由于机械部件损坏或传感器故障引起的。
要解决这一问题,操作者可以检查换刀机构的机械部件是否损坏,进行修复或更换。
如果是传感器故障,需要对传感器进行维修或更换。
此外,自动换刀系统还可能会出现刀具卡滞或卡住的故障。
刀具卡滞可能会导致刀具无法顺利更换,进而影响加工效果。
产生这一故障的原因可能是刀具或刀具接触面不干净,刀具锈蚀或与刀夹接触面不匹配。
要解决这一问题,操作者可以清洁刀具及其接触面,并进行润滑。
如果刀具锈蚀严重或与刀夹接触面不匹配,需要进行更换。
最后,自动换刀系统还可能会出现控制系统故障。
控制系统故障可能导致自动换刀操作失效,无法正常更换刀具。
产生这一故障的原因可能是控制系统的电路板损坏或控制程序错误等。
要解决这一问题,操作者可以检查控制系统的电路板是否损坏,并进行修复或更换。
同时,对控制程序进行检查和修正。
在使用自动换刀系统时,操作者应注意安全操作规程,及时保养和维护系统,并进行定期的系统检查和保养。
数控机床原理、结构与维修 第5章 回转工作台与自动换刀系统
5.1 分度工作台
图5-3 齿盘定位分度工作台 1—螺旋弹簧 2、10、11—轴承 3—蜗杆 4—蜗轮 5、6—减速齿轮 7—管道 8—活塞 9—分度工作台 12—液压缸 13、 14—分度齿盘
5.1 分度工作台
5.1.3 鼠牙盘分度工作台 鼠牙盘式分度工作台主要由工作台面、底座、分度液压缸及鼠牙 盘等零件组成,如图5⁃4所示。鼠牙盘是保证分度精度的关键零件,
图5-8 双蜗杆传动结构 1—轴向固定蜗杆 2—轴向调整蜗杆 3、5—调整垫 4—锁紧螺母
5.2 数控回转工作台
图5-9 数控回转工作台 1—电液脉冲马达 2、4—齿轮 3—偏心环 5—楔形拉紧销 6—压块 7—螺母 8—锁紧螺钉 9—蜗杆 10—蜗轮 11—调整套 12、13—夹紧瓦 14—夹紧液压缸 15—活塞 16—弹簧 17—钢球 18—光栅 19—撞块 20—感应块
5.3 刀架换刀装置
表5-1 自动换刀装置
类
型
回转刀架
特
点
适用范围
各种数控车床,车 削加工中心
转塔式
多为顺序换刀,换 刀时间短,结构简单 紧凑,可容纳的刀具 较少 顺序换刀,换刀时 间短,刀具主轴都集 中在转塔头上,结构 紧凑。但刚性较差, 刀具主轴数受限制
转塔头
数控钻、镗、铣床
5.3 刀架换刀装置
表5-1 自动换刀装置
刀库式
刀具与主轴之间直 接换刀
换刀运动集中,运 动部件少。但刀库容 量受限
用于各种类型的自 动换刀数控机床上, 尤其是对使用回转类 刀具的数控镗铣床类 的立式、卧式加工心。 要根据工艺范围和机 床特点,确定刀库容 量和自动换刀装置形 式
用机械手配合刀库 进行换刀
刀库只有选刀运动, 机械手进行换刀运动, 刀库容量大
数控机床自动换刀系统的使用方法
数控机床自动换刀系统的使用方法数控机床自动换刀系统是一种现代化的工艺装备,它能够自动完成刀具的安装和拆卸,极大地提高了机床的工作效率和自动化水平。
在这篇文章中,我们将详细介绍数控机床自动换刀系统的使用方法,以帮助读者更好地了解和应用这一技术。
首先,数控机床自动换刀系统的基本原理是通过刀库来存放各种不同类型的刀具,并且能够根据加工程序的要求自动选择并安装适当的刀具。
在使用之前,我们需要先对刀具进行合理的编码和分类,并将其放置在刀库中。
接下来,我们需要进行合适的设置和调整。
首先,通过数控系统进入自动换刀的菜单界面,选择相应的刀库和刀具编号。
然后,根据加工零件的要求,选择适当的刀具参数和加工工艺参数,如切削速度、进给速度等。
最后,将设定好的加工程序加载到数控系统中。
在机床开始加工前,我们需要执行一次预热功能,以确保刀库、刀具和机床处于最佳状态。
同时,还需要检查刀具的完好程度,如刀片的磨损情况、刀具的固定性等。
如果存在问题,及时更换和调整刀具,以保证加工质量和安全。
在实际操作中,数控机床自动换刀系统的使用方法还需注意以下几点。
首先,严禁在机床运行状态下打开刀库门,以防止刀库和刀具的损坏。
其次,操作人员必须经过专业的培训和熟悉使用手册,掌握换刀系统的操作要领和注意事项。
再次,要定期对刀具和机床进行保养和维护,以延长其使用寿命。
此外,数控机床自动换刀系统的使用方法还需要根据具体的机床类型和加工要求进行灵活调整。
例如,在加工不同材料的零件时,需要选择适宜的刀具材质和切削参数;在进行复杂轮廓和曲线加工时,需要使用特殊形状的刀具,并调整切削路径和刀具补偿等。
总结起来,数控机床自动换刀系统的使用方法是一个复杂而重要的技术,它能够提高机床的生产效率和一致性。
通过合理设置和调整刀具参数,以及进行正确的操作和维护,可以确保刀具的安全性和加工质量。
然而,在使用过程中还需要注意刀具的选择和切削参数的调整,以适应不同的加工需求。
数控机床自动换刀原理
数控机床自动换刀原理数控机床是一种通过数字指令控制刀具运动和加工过程的机床。
在数控机床加工过程中,常常需要根据不同的工件要求,使用不同类型和规格的刀具进行加工。
而自动换刀系统正是为了实现这一需求而设计的。
数控机床自动换刀系统的原理是通过一系列的动作和控制,完成刀具的自动更换。
下面将详细介绍数控机床自动换刀系统的工作原理。
数控机床自动换刀系统由刀库、刀库传动装置、刀库定位装置、刀库夹紧装置、换刀臂、换刀臂传动装置等组成。
刀库内存放着各种不同类型和规格的刀具,而刀库传动装置可以将刀具送到指定位置。
当数控机床需要换刀时,首先通过数控系统发出换刀指令。
接着,刀库定位装置开始工作,将刀库中所需的刀具定位到换刀位置。
换刀臂传动装置接收到信号后,开始执行换刀操作。
换刀臂传动装置通过一定的轨迹,将换刀臂移动到刀库定位装置定位的刀具位置上。
然后,刀库夹紧装置开始工作,将刀具夹紧在换刀臂上。
此时,刀具已经成功更换,可以进行下一步的加工操作。
在整个自动换刀过程中,数控系统起着关键的作用。
它通过控制刀库传动装置、刀库定位装置、刀库夹紧装置以及换刀臂传动装置的工作,实现刀具的自动更换。
数控系统可以根据加工程序的要求,选择合适的刀具进行加工,提高加工效率和质量。
数控机床自动换刀系统的优势在于提高了加工效率和自动化程度。
相比于传统的手动换刀方式,自动换刀系统可以实现快速、准确地更换刀具,节省了换刀时间,降低了人工操作的难度和风险。
同时,自动换刀系统还可以减少刀具磨损,延长刀具寿命,提高了加工的稳定性和一致性。
数控机床自动换刀系统是一项重要的技术创新,为加工行业带来了巨大的变革。
通过数字指令和自动化控制,实现了刀具的快速、准确更换,提高了加工效率和质量。
随着科技的不断发展和应用,相信自动换刀系统会越来越普及,并在数控机床加工中发挥越来越重要的作用。
- 1、下载文档前请自行甄别文档内容的完整性,平台不提供额外的编辑、内容补充、找答案等附加服务。
- 2、"仅部分预览"的文档,不可在线预览部分如存在完整性等问题,可反馈申请退款(可完整预览的文档不适用该条件!)。
- 3、如文档侵犯您的权益,请联系客服反馈,我们会尽快为您处理(人工客服工作时间:9:00-18:30)。
数控机床自动换刀系统
一.概述
要实现一次装夹多工序加工,在数控机床上必需具备自动换刀功能。
实现刀库与机床主轴之间刀具的装卸与传递功能的装置称为自动换刀系统。
自动换刀已广泛地用于镗铣床、铣床、钻床、车床、组合机床和其它机床。
使用自动换刀系统,协作精密的数控转台,不仅扩大了数控机床的使用范围,削减了生产面积,还可使机加工时间提高到70% ~80%,显著提高了生产率。
由于零件在一次安装中完成多工序加工,大大削减了零件安装的定位次数,从而进一步提高了加工精度。
自动换刀系统应当满意换刀时间短,刀具重复定位精度高,刀具储存数量足够,结构紧凑,便于制造、修理、调整,应有防屑、防尘装置,布局应合理等要求。
同时也应具有较好的刚性,冲击、振动及噪声小,运转平安牢靠等特点。
自动换刀系统的形式和详细结构对数控机床的总体布局、生产率和工作牢靠性都有直接的影响。
二.组成及其形式
自动换刀系统由刀库、选刀机构、刀具交换机构(如机械手)、刀具在主轴上的自动装卸机构等部分组成。
自动换刀系统的形式是多种多样的,换刀的原理及结构的简单程度也不同,但一般可分为以下两大类:
由刀库和主轴的相对运动实现刀具交换。
用这种形式交换刀具时,主轴上用过的刀具送回刀库和从刀库中取出新刀,这两个动作不能同时进行,选刀和换刀由数控定位系统来完成,因此换刀时间长,换刀动作也较多。
由机械手进行刀具交换。
由于刀库及刀具交换方式的不同,换刀机械手也有多种形式。
图1 换刀机械手的形式
图1(a),(b),(c)为双臂回转机械手,能同时抓取和装卸刀库和主轴(或中间搬运装置)上的刀具,动作简洁,换刀时间短。
图(d)虽然不是同时抓取刀库和主轴上的刀具,但换刀预备时间及将刀具还回刀库的时间与机加工时间重复,因而换刀时间也很短。
抓刀运动可以是旋转运动,也可以是直线运动。
图1(a)为钩手,抓刀运动为旋转运动;图(b)为抱手,抓刀运动为两个手指旋转;(c)和(d)为叉手,抓刀运动为直线运动。
由于抓刀运动的轨迹不同,各种机械手的应用场合也不同,抓刀运动为直线时,在抓刀过程中可以避开与相邻的刀具相碰,所以当刀库中刀具排列较密时,常用叉刀手。
钩刀手和抱刀手抓刀运动的轨迹为圆弧,简单和相邻的刀具相碰,因而要适当增加刀库中刀具之间的距离,合理设计机械手的外形及其安装位置。
三.刀具的夹持
刀具必需装在标准的刀柄内,我国TSG刀具系统规定了刀柄标准,有直柄及7∶24锥度的锥柄两类。
分别用于圆柱形主轴孔及圆锥形主
轴孔,其结构如下图2所示。
图中3为刀柄定位及夹持部位,2为机械手抓取部位,1为键槽,用于传递切削扭矩,4为螺孔,用以安装可调整拉杆,供拉紧刀柄用。
刀具的轴向尺寸和径向尺寸应先在调刀仪上调整好,才可装入刀库中。
丝锥、铰刀要先装在浮动夹具内,再装入标准刀柄内。
圆柱形刀柄在使用时需在轴向和径向夹紧,因而主轴结构简单,柱柄安装精度高,但磨损后不能自动补偿。
而锥柄稍有磨损也不会过分影响刀具的安装精度。
在换刀过程中,由于机械手抓住刀柄要作快速回转,拔、插刀具的动作,还要保证刀柄键槽的角度位置对准主轴上的驱动键。
因此,机械手的夹持部分要非常牢靠,并保证有适当的夹紧力,其活动爪要有锁紧装置,以防止刀具在换刀过程中转动或脱落。
图2 圆锥刀柄和圆柱刀柄机械手夹持刀具的方法有以下两类:
柄式夹持(轴向夹持)
刀柄前端有V形槽,供机械手夹持用,目前我国数控机床较多采纳这种夹持方式。
如图3所示为机械手手掌结构示意图。
由固定爪7及活动爪1组成,活动爪1可绕轴2回转,其一端在弹簧柱塞6的作用下,支靠在挡销3上,调整螺栓5以保持手掌适当的夹紧力,锁紧销4使活动爪1坚固夹持刀柄,防止刀具在交换过程中松脱。
锁紧销4要轴向压进,放松活动爪1,以便抓刀或松刀时手爪从刀柄V形槽中退出。
图3 机械手手掌结构示意图法兰盘式夹持
法兰盘式夹持,也称径向夹持或碟式夹持,如图4所示。
在刀柄的前端有供机械手夹持用的法兰盘,图中所示为采纳带洼形肩面的法兰盘供机械手夹持用。
图4 法兰盘式夹持
图(a)上图为松开状态,下图为夹持状态。
采纳法兰盘式夹持的突出优点是:当采纳中间搬运装置时,可以很便利地从一个机械手过渡到另一个帮助机械手上去,如图(b)所示。
法兰盘式夹持方式、换刀动作较多,不如柄式夹持方式应用广泛。
四.工作原理下面以JCS-018A数控立式镗铣床为例,来说明自动换刀系统的工作原理。
该自动换刀系统由盘式刀库和刀具交换装置组成。
刀库安装在机床左侧的立柱上,刀库容量为16把刀具,换刀机械手安装在刀库和主轴之间。
机械手将刀具从刀库中取出送至机床主轴上,然后将用过的刀具送回刀库。
其自动换刀动作过程简述如下:
刀套下转90°:如图5所示,刀库位于立柱左侧,刀具轴线在刀库中的安装方向与主轴垂直换刀前,刀库将待换刀具5送到换刀位置,刀套4连同刀具5向下翻转90°,使刀具轴线与主轴轴线平行。
机械手转75°:图5所示K向视图所示为机械手的原始位置,换刀
时机械手顺时针转75°,两手爪分别抓住刀库上和主轴3上的刀柄。
机械手拔刀:待主轴上自动夹紧机构松开刀具后,机械手下降,同时拔出主轴上和刀库上的刀具。
刀具位置交换:机械手顺时针转180°,使主轴刀具与刀库刀具交换位置。
机械手插刀:机械手上升,分别将刀具插入主轴锥孔和刀库刀套中。
机械手逆时针转75°:待主轴上自动夹紧机构夹紧刀具后,机械手逆时针转75°,回到原始位置。
刀套上转90°:刀套带着换回的旧刀具向上翻转90°,预备下一次选刀。
该机床使用回转式单臂双手机械手换刀。
在自动换刀过程中,机械手要完成抓刀、拔刀、交换主轴上和刀库上的刀具、插刀和复位等动作,这些动作由液压系统来掌握完成。
这种自动换刀系统结构简洁,换刀牢靠,换刀动作也少,得到了广泛应用。
图5 自动换刀过程示意图。