振动监测与故障诊断系统介绍
振动监控系统

振动监控系统振动监控系统是一种用于实时监测和分析机械设备振动状况的技术方案。
它利用传感器采集机械设备的振动信号,并通过分析这些信号来实现对机械设备的状态进行监测和预测。
振动监控系统广泛应用于各种工业领域,可有效提高设备的稳定性、可靠性和安全性。
一、振动监控系统的原理和组成振动监控系统主要由传感器、信号放大器、数据采集器、分析软件等组成。
传感器负责采集机械设备振动信号,信号放大器用于放大传感器采集到的微弱信号,数据采集器将信号转换为数字信号并传输给分析软件进行处理。
二、振动监控系统的作用和优势1. 实时监测:振动监控系统能够实时监测机械设备的振动状况,及时发现异常振动,提前预警设备故障,避免机械设备的意外停机,减少生产线的损失。
2. 故障诊断:通过振动信号的分析,振动监控系统可以判断设备是否存在故障,并对故障类型进行诊断。
这有助于准确定位和修复故障,提高维修效率。
3. 预防维护:振动监控系统可以实现对机械设备的预防性维护。
通过持续监测设备振动状况,系统可以根据振动特征和变化趋势提前预警设备故障,制定合理的维护计划,避免设备故障带来的生产中断和维修成本。
4. 数据分析:振动监控系统可以对采集到的振动数据进行分析和处理,提取有用信息,为设备运行状态的评估和改进提供依据。
这有助于优化生产过程,提高设备的使用寿命和稳定性。
三、振动监控系统的应用领域振动监控系统广泛应用于各种工业设备的监测和维护中,如发电机组、风力发电机组、泵站、机床、轴承等。
以下是几个典型的应用场景:1. 发电机组监测:发电机组是电力系统的重要组成部分,振动监控系统可以监测其转子和轴承的振动状况,检测轴承的磨损程度,发现故障隐患,确保发电机组的安全运行。
2. 风力发电机组监测:风力发电机组常受到强风和恶劣环境的影响,振动监控系统可以监测发电机组的桨叶振动、转子振动等,提供及时的故障预警和维护建议。
3. 泵站监测:振动监控系统可以监测泵站的水泵、电机等关键设备的振动状况,预测设备的寿命,并提供有效的维护方案,保证泵站的正常运行。
振动监测与故障诊断系统简介
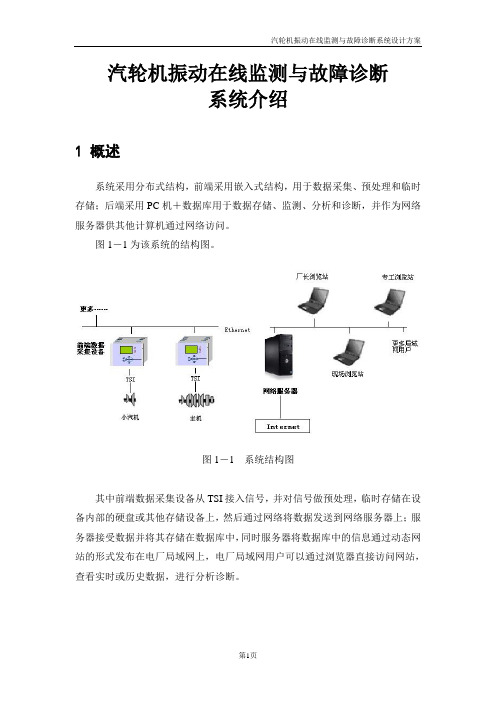
数据采集子系统与气轮机组在线监测故障诊断主系统集成工作的原理如图2-2所示。
图2-2数据采集子系统的工作原理
2.
一体化设计,功能完善,结构合理,商品化的产品。
采用模块化和多CPU主从结构设计,数据采集、处理能力强大,组装、维护方便。
主CPU板和各智能模拟量信号采集板通过内存进行数据交换,数据交换速度高,吞吐量大。
标准VT100终端接口,用户可以方便对装置进行远方检测和在线配置。
工业标准设计,能够工作于各种恶劣环境。
采用电磁兼容(EMC)技术,抗电磁脉冲干扰(EMI)性能强,装置运行稳定可靠。
对敏感信号进行屏蔽。
输入信号采用光电隔离。
内部器件均选用优秀的工业级产品。
不需要特殊的加热器或冷却装置。
充分的可靠性设计,严格的质量检验,为用户提供了可靠的保证。
汽轮机振动在线监测与故障诊断
系统介绍
1
系统采用分布式结构,前端采用嵌入式结构,用于数据采集、预处理和临时存储;后端采用PC机+数据库用于数据存储、监测、分析和诊断,并作为网络服务器供其他计算机通过网络访问。
图1-1为该系统的结构图。
图1-1系统结构图
其中前端数据采集设备从TSI接入信号,并对信号做预处理,临时存储在设备内部的硬盘或其他存储设备上,然后通过网络将数据发送到网络服务器上;服务器接受数据并将其存储在数据库中,同时服务器将数据库中的信息通过动态网站的形式发布在电厂局域网上,电厂局域网用户可以通过浏览器直接访问网站,查看实时或历史数据,进行分析诊断。
键相信号(脉冲信号)接入装置后,需要光电隔离、滤波整形处理。键相信号调理电路由光电隔离器和滤波整形两部分组成。
智能模拟量信号采集板的组成如图2-4所示。
振动检测与故障诊断技术

振动检测是状态检测的手段之一,任何机械在输入能量转化为有用功的过程中,均会产生振动;振动的强弱与变化和故障有关,非正常的震动感增强表明故障趋于严重;不同的故障引起的振动特征各异,相同的振动可能是不同的故障;振动信号是在机器运转过程中产生的,就可以在不用停机的情况下检测和分析故障;因此识别和确定故障的内在原因需要专门的一起设备和专门的技术人才。
1、机械振动检测技术机械运动消耗的能量除了做有用功外,其他的能量消耗在机械传动的各种摩擦损耗之中并产生正常振动,其他的能量消耗在机械传动的各种摩擦损耗之中并产生正常振动,如果出现非正常的振动,说明机械发生故障。
这些振动信号包含了机械内部运动部件各种变化信息。
分辨正常振动和非正常振动,采集振动参数,运用信号处理技术,提取特征信息,判断机械运行的技术状态,这就是振动检测。
所以由此看来,任何机械在输入能量转化为有用功的过程中,均会产生振动;振动的强弱与变化和故障有关,非正常的震动感增强表明故障趋于严重;不同的故障引起的振动特征各异,相同的振动可能是不同的故障;振动信号是在机器运转过程中产生的,就可以在不用停机的情况下检测和分析故障;因此识别和确定故障的内在原因需要专门的一起设备和专门的技术人才。
2、振动监测参数与标准振动测量的方位选择a、测量位置(测点)。
测量的位置选择在振动的敏感点,传感器安装方便,对振动信号干扰小的位置,如轴承的附近部位。
b、测量方向。
由于不同的故障引起的振动方向不同,一般测量互相垂直的三个方向的振动,即轴向(A向)、径向(H 向、水平方向)和垂直方向(v向)。
例如对中不良引起轴向振动;转子不平衡引起径向振动;机座松动引起垂直方向振动。
高频或随机振动测量径向,而低频振动要测量三个方向。
总之测量方向和数量应全面描述设备的振动状态。
测量参数的选择测量振动可用位移、速度和加速度三个参数表述。
这三个参量代表了不同类型振动的特点,对不同类型振动的敏感性也不同。
振动监测及分析系统(VMAS)在发电厂的应用

振动监测及分析系统(VMAS)在发电厂的应用摘要:振动状态监测及分析系统自动连续地采集与设备安全有关地主要状态参数:机组的振动、摆度、键相/转速、轴振、瓦振、轴位移、胀差、偏心、机组轴承负荷及温度、压力和开关量等,并自动形成各种数据库。
它能够自动识别设备的运行状态,预测和诊断设备的故障;能够促进设备维修方式向预知维修(状态维修)的转变,确保设备安全稳定地运行。
关键词:振动状态监测及分析系统(VMAS);信号处理;诊断。
0. 引言随着对发电厂主要设备可靠性、稳定性、以及对电厂设备寿命要求的提高,越来越多的监测和诊断分析系统应用到实际电厂项目中。
汽轮机、发电机、以及主要高压电动机设备作为发电厂的主要运行设备,更是成为监测和诊断的重要对象。
随着先进信号处理技术以及诊断技术的发展,振动监测及分析系统(VMAS)能在故障出现的早期阶段及时地预告故障的存在和发展,避免灾难性事故发生,并可以将现有的周期预防性维修改为预知性的维修, 选择最佳停修时间,提高机组可利用率。
1. 振动状态监测及分析系统(VMAS)的定义振动状态监测及分析系统,英文全称是Vibration monitoring and analyze system ,缩写为VMAS。
振动状态监测及分析系统的主要功能是用于主辅机(通常包括汽轮机、发电机、以及主要的高压设备)状态监测与故障诊断,实现监测、控制、报警、诊断功能。
而在早期,振动状态监测和分析系统主要应用于汽轮发电机组,叫做旋转机械诊断监测管理系统,英文TDM (Turbine diagnosis management) ,在电厂中一般是指汽轮发电机组振动在线状态监测和分析系统。
实际上,这两个叫法是针对一套系统,只是监测的范围不同。
2. 振动状态监测及分析系统基本配置振动状态监测及分析系统是以计算机为平台的旋转机械振动状态在线监测及故障诊断系统,用于对汽轮机、发电机、电动机、风机、泵等设备的振动、转速、压力、流量、温度等信号进行连续监测。
柴油机振动监测及故障诊断系统

Ab t a t T sp p rd s rbe re y t e vb ain mo i rn c a ims o it n ln rwe rn s r c : hi a e e c i s b i f h i r to n t i g me h n s fp so —i e a i g, l o
a n r l av laa c ehutvlel kg n anjun l e igt blg a fut ad ae b oma vl c rn e x a s av a aea d m i o ra b a n r o i l a l e e I e r i oc .H rw r
= . 1 (m O85i) p . ,
= . 5 (m 0 2 5m )
\
= . 2 (m 0 5 5m )
主 撞 击
.
主撞击
1 . 一
\
L
r
1. . - I
0。 丌 T
l
\
L ▲L L 一 ▲I 一
L
罂
振动检测与分析系统方案
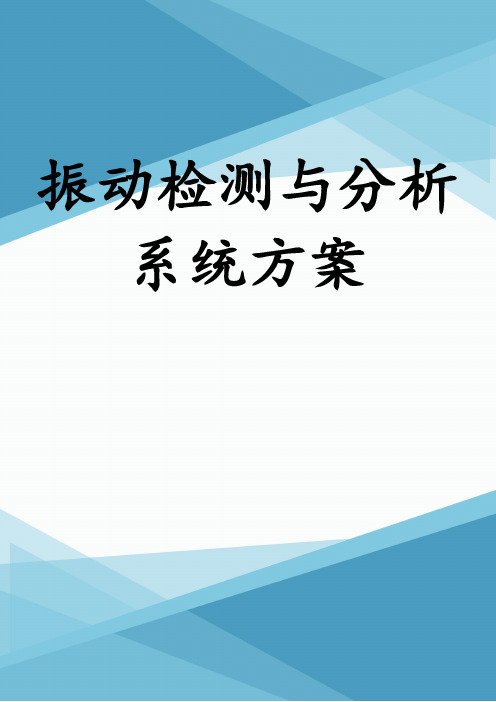
振动检测与分析系统方案振动检测与分析系统方案振动检测与分析系统广泛应用于工程领域,用于监测和分析机械设备、结构物或其他物体的振动情况。
该系统能够提供实时数据,并通过分析判断设备的工作状态,从而实现故障预警和维护计划的制定。
下面是一个振动检测与分析系统的方案,按照步骤逐一介绍。
1. 确定监测目标:首先,需要确定需要监测和分析的目标,例如机械设备、建筑结构等。
根据目标的特点和使用环境,选择适合的振动传感器和数据采集设备。
传感器可以通过接触式或非接触式方式获取振动信号。
2. 安装传感器:将振动传感器安装在目标物体上,并确保传感器与目标之间的接触良好。
对于机械设备,可以选择在关键部位安装传感器,如轴承、齿轮等。
对于结构物,可以选择在梁柱节点或其他关键位置安装传感器。
3. 数据采集:使用数据采集设备将传感器获取的振动信号转化为数字信号,并进行采样和存储。
数据采集设备可以是专用的振动分析仪器,也可以是通用的数据采集器,如传感器与计算机连接的数据采集卡。
4. 数据处理与分析:将采集到的振动数据传输到计算机上,并使用相应的振动分析软件进行处理和分析。
软件可以提供多种振动特征参数的计算和分析方法,如频域分析、时域分析、轴心轨迹分析等,以评估设备或结构的振动情况。
5. 故障诊断与预警:根据振动分析的结果,判断设备或结构是否存在故障或异常情况。
通过设定合适的阈值和告警条件,系统可以实现自动故障诊断和预警功能。
一旦检测到异常振动,系统会发出警报并提供相应的故障诊断结果。
6. 维护计划制定:根据故障诊断结果和预警信息,制定相应的维护计划。
可以根据设备的工作状态和振动特征,确定维护时间和方式,以避免设备故障或减少停机时间。
7. 数据记录和报告:系统可以自动记录和保存振动数据,并生成相应的报告。
报告可以包括设备的振动趋势图、频域谱图、故障诊断结果等信息,为维护人员提供参考和决策依据。
8. 系统优化和改进:根据实际使用情况,对振动检测与分析系统进行优化和改进。
机械振动监测与故障预警
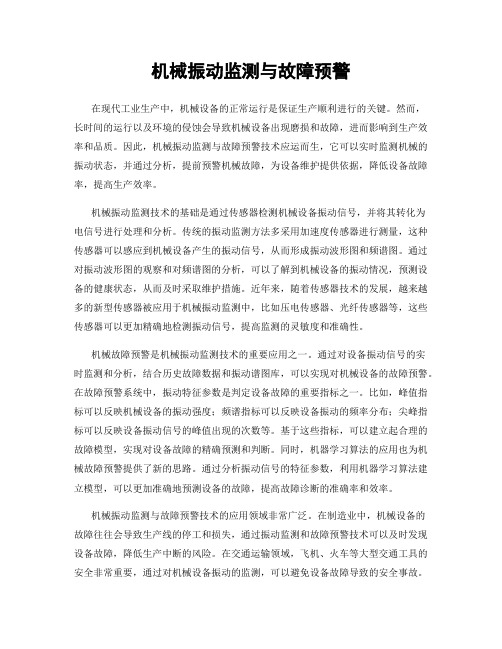
机械振动监测与故障预警在现代工业生产中,机械设备的正常运行是保证生产顺利进行的关键。
然而,长时间的运行以及环境的侵蚀会导致机械设备出现磨损和故障,进而影响到生产效率和品质。
因此,机械振动监测与故障预警技术应运而生,它可以实时监测机械的振动状态,并通过分析,提前预警机械故障,为设备维护提供依据,降低设备故障率,提高生产效率。
机械振动监测技术的基础是通过传感器检测机械设备振动信号,并将其转化为电信号进行处理和分析。
传统的振动监测方法多采用加速度传感器进行测量,这种传感器可以感应到机械设备产生的振动信号,从而形成振动波形图和频谱图。
通过对振动波形图的观察和对频谱图的分析,可以了解到机械设备的振动情况,预测设备的健康状态,从而及时采取维护措施。
近年来,随着传感器技术的发展,越来越多的新型传感器被应用于机械振动监测中,比如压电传感器、光纤传感器等,这些传感器可以更加精确地检测振动信号,提高监测的灵敏度和准确性。
机械故障预警是机械振动监测技术的重要应用之一。
通过对设备振动信号的实时监测和分析,结合历史故障数据和振动谱图库,可以实现对机械设备的故障预警。
在故障预警系统中,振动特征参数是判定设备故障的重要指标之一。
比如,峰值指标可以反映机械设备的振动强度;频谱指标可以反映设备振动的频率分布;尖峰指标可以反映设备振动信号的峰值出现的次数等。
基于这些指标,可以建立起合理的故障模型,实现对设备故障的精确预测和判断。
同时,机器学习算法的应用也为机械故障预警提供了新的思路。
通过分析振动信号的特征参数,利用机器学习算法建立模型,可以更加准确地预测设备的故障,提高故障诊断的准确率和效率。
机械振动监测与故障预警技术的应用领域非常广泛。
在制造业中,机械设备的故障往往会导致生产线的停工和损失,通过振动监测和故障预警技术可以及时发现设备故障,降低生产中断的风险。
在交通运输领域,飞机、火车等大型交通工具的安全非常重要,通过对机械设备振动的监测,可以避免设备故障导致的安全事故。
浅谈风力发电机组振动状态监测与故障诊断

浅谈风力发电机组振动状态监测与故障诊断摘要:随着科技的发展,风电机组单机容量变大,内部的结构越来越复杂,还会受到天气的不可控因素的影响,比如会受到下雨时,打雷闪电等,本文对风力发电机组振动状态监测与故障诊断进行分析,以供参考。
关键词:风力发电;机组振动;状态监测;故障诊断引言风能是自然界中常见的自然现象,特别是在经济不发达,风能资源丰富的山地地区。
考虑到风能对当前社会结构的重要性,它提高了风力发电机运行的可检测性,并允许在整个发电机组运行期间及时发现问题,使整个风力发电机运行更平稳和安全。
1概述近年来国内风电发展迅速,风电机组容量的提升能够有效提高风能利用率和施工效率以及降低后期运维成本。
在机组容量和体型逐渐增大的同时,风电机组的安全成为风电领域内研究的重点。
江苏某风电场安装了多台6.45MW机组,此类型机组是目前国内厂家生产新型大容量机组之一,此机组塔筒高度为110m,叶轮直径达到171m。
国外GE公司生产的12MW风机单支叶片更是长达107m。
机组容量增大的同时叶片也在不断增大。
风电机组叶片成本约占风电机组总成本的15%~20%,风电机组叶片在风电机组运行过程中受风力作用而产生较大的弹性形变,故通常选用质量较轻、强度较大、耐腐蚀、抗疲劳的材料来制作风电机组叶片。
此外,由于结冰或者风力和风向的突变导致叶片振动过大,从而超过设计载荷发生断裂或者扫塔的现象也时有发生,而振动检测是叶片故障识别的常用方法之一,所以研究大型风电机组的叶片振动情况,对于叶片安全检测和监测具有重要的意义,研究结果也可对风电机组的控制策略优化提供重要指导作用。
在风力发电机组中,齿轮箱也存在着异常问题,表面磨损,齿轮轻度裂纹,设备老化等问题,以下对论文展开叙述。
2风力发电机组安全系统2.1分析(1)安全有关停止功能在机组通过安全防护装置(如传感器)检测到风轮转速超过限值、扭缆超过限值、过度振动及控制系统失效等信号时,安全系统起动机组紧急制动进入停止状态。
- 1、下载文档前请自行甄别文档内容的完整性,平台不提供额外的编辑、内容补充、找答案等附加服务。
- 2、"仅部分预览"的文档,不可在线预览部分如存在完整性等问题,可反馈申请退款(可完整预览的文档不适用该条件!)。
- 3、如文档侵犯您的权益,请联系客服反馈,我们会尽快为您处理(人工客服工作时间:9:00-18:30)。
产品介绍 | introduction
系统构成
产品介绍 | introduction
实时监测机舱内 外温度 转速信对故障提取起到辅 助作用 传动链上6个加速度传感 器采集机组振动信号,其 中两个位XY方向双通道
采集发电机定子电压电流信 号,与振动信号相结合,提 高故障诊断准确率 系统结构框图
数据采集 | DA
旋转机械的微小故障一旦发展为严重故障,将会对昂贵的风电机组
造成不可恢复的损坏,引起严重的经济损失。 经过大量的实际数据总结,处于恶劣工况下的风电机组的故障多集 中于旋转机械和啮合机械中,发电机的定子转子的故障也越发的增多。 基于振动信号的旋转机械故障诊断技术的广泛有效应用和在行业内 已经取得的相当有效成果,使得风电机组状态监测系统发展极具战略意 义。
项目内容 | contents
1.风电场振动数据的二次接收及存储
2.振动数据的时域分析,时域振动状态参 数分析,正常、异常、故障报警处理 3.设备特征频率提取及频域分析,对轴 承、齿轮、叶片、发电机及塔架故障的诊 断
项目内容 | contents
4.历史分析,检测主要部件故 障的发生、发展趋势,为设备 维护提供依据 5.软件支持设备参数录入、便 于人员操作,联网后支持远程 诊断分析
创新
基于自主开发的嵌入式处理装置来实现高速信息采集、就地处理
分析功能
基于机组振动、转速、发电机电压/电流状态等实时数据进行 分析,实现对机组旋转连接设备的全面有效监测
该系统具备良好的开放性与可扩展性,多路模拟与开关扩展接口 与信号数据处理通道,方便系统的升级改造。
创新
系统具有光纤网络信息传输、断网自动互联功能。提供完善的网络扩展 功能,在多个风电场远程监控系统技术支持下,能够实现多机联合实时 在线监测。 采用Labview软件支撑平台,开发了基于风电机组实测信息、信号
项目过程 | progress
2013.5 与华能酒泉风电有限责任公司签订项目合同
2013.5~2013.7 调查研究、分析论证、方案设计 2013.7~2013.9 搭建硬件环境与软件开发 2013.9~2013.11 软硬件调试,研究,修改
2013.11-2013.12 现场安装调试,整理资 料,验收
风机振动检测及故障诊断系统与研 究软件开发
吕跃刚 教授
二〇一三年十二月
目录 | list
项目背景 项目内容 产品介绍 成果与创新
目录 | list
传动系统是实现风能转换和传递过程的主要承载部件。 风力发电机组主要部件寿命一般20年. 但是由于风电机组多数安装在西部和沿海地区,环境 条件差,机组经常工作在低温、沙尘、雷电、冰雪、风暴
分析与处理技术、时域与频域相结合的状态监测系统,并具有完全
的自主知识产权。
就地装置具有信号输入隔离、浮地、防雷击等功能,保障 设备安全正常运行。
thanks
控制系统
电气系统
0
2
4
6
8
平均故障停机时间(天)
项目背景 | backgrounds
1.减少风电机组故障发生 2.减少机组故障导致的经济损失 3.改善传统设备检修维护手段 4.提高风电机组运行可靠性 5.满足远程在线诊断要求
项目意义 | prospect
随着风力发电技术日趋成熟和装机容量的大规模增加,对风电机组 安全高效的运行有了更高的要求。
等恶劣环境条件,而且由于风速、载荷和风轮转速变化范
围大,上网要求高,导致机组运行工况复杂,极易造成风 电机组叶片和传动系统在寿命期内出现故障甚至损坏,影 响机组的安全可靠性。
项目背景 | backgrounds
风机各部件故障比例
项目背景 | backgrounds
传动系统 支撑架 发电机
齿轮箱
轮毂 机械刹车 叶片故障 偏航系统 液压系统 传感器
故障诊断 | FD
产品功能
权限管理将区分高级管理人员与一般操作人员
进入主监控界面后将显示整个风场各台风机的振动状态界面,风机按停 机、运行、报警故障、严重故障区分 点击对象菜单进入分析界面,按被测对象及部位分别对主轴承、齿轮箱、 发电机、叶片、塔架等进行时域及频域分析。
引入发电机状态监测部分,可即时监视发电机运行过程各参量变化及潜在故障信 息,通过电机信号输出分析与传统振动分析方法相结合,提高故障诊断的准确性和 可靠性。 数据处理是分析的必要步骤,软件中提供了数据截取、放大、滤波、窗函数等工 具,经过一定训练的操作人员可以掌握这些工具。
采用自主研发HDZTJC-4P 智能数据处理器设备。具
有很好稳定性和扩展性。
该装置集ARM-DSP技术为 一体,采用嵌入式设计理 念,高性能CPU,外扩丰 富外设接口,极大满足风 电场运行状态监测与分析 系统的实际应用需求 基于DSP数据处理器硬件结构
软件设计 | software
采用Labview图形化语言编程
可对指定设备单独进行详细故障分析
故障诊断 | FD
对具体设备的信号进行时、频域等全方面多角度分 析,寻找故障特征,应用到了小波降噪、包络谱、倒 频谱、功率谱密度等多个先进信号处理技术
利用XY振动传感器,结合频域积分技术,绘制主轴、 发电机转轴轴心轨迹图,能够直观地观察轴系运动状 态 加入发电机定子电压电流时、频域分析,在诊断发电 机本身故障的同时,与传统振动分析技术相结合,提 高诊断的准确率
界面整洁美观、简单易懂、人机交 互能力强
具有强大的数据分析和处理功能
软件设计 | software
软件整体框图
软件设计 | software
单台风机界面
主界面
分析界面
软件设计 | software
主界面和单台风机监测界面,可显示整体风机和单台风 机即时状态和数据,后者还可显示任意时间历史趋势
配备常见厂家产品配置库,用户可手动设置风机配置