柔性工装
柔性软工装在样车试制中的应用

122AUTO TIMEAUTO PARTS | 汽车零部件1 引言前期开发阶段,试制样车目的是为了进行产品设计、性能、零件匹配、产品制造过程等一系列验证,每个阶段样车制造为小批量生产。
如果采用正式工装夹具来定位焊装白车身,不但会增加设计和制造成本,还大大延长了开发制造周期。
因此,在样车试制阶段,采用不太正式的工装夹具来焊装白车身,此种方式缩短了设计时间和制造周期,降低了人员成本和制造成本,且能满足每个零件的定位夹紧状态,称这种工装为软工装。
同一款车型在不同试制阶段,钣金状态存在一定差异性,但是个别位置变动不是太大,有的定位和夹紧点可以沿用上一阶段的软工装夹具焊装,部分夹具改动也不是太大,重新设计和加工这部分夹具都造成了一定资源的浪费。
不同车型试制中,每个车型都独立开发一套专用拼台进行焊装,也会造成很大的浪费。
为实现不同车型、同一车型不同阶段软工装夹具设计和制造的时间、成本都能得到有效控制,本文探讨开发柔性化的软工装夹具应用于样车试制。
2 软工装夹具结构工装夹具应用在焊装过程中,目的是实现不同零件装配的定位和夹紧固定,在工艺指柔性软工装在样车试制中的应用汪红 张正举 黎志梅 张惠立上汽通用五菱汽车股份有限公司 广西柳州市 545007摘 要: 随着汽车行业竞争越来越激烈,缩短汽车研发制造周期,对提升新产品市场占有率至关重要。
在软工装样车试制过程中,可以通过缩短试制周期来对汽车开发周期节省时间。
采用柔性化软工装夹具,可以大量减少软工装夹具制造周期、节约制造成本和人力成本,有效缩短了样车试制周期。
关键词:样车试制;软工装;柔性化导下,进行准确的相对位置定位及各个零件的贴合夹紧,保证了在焊接前,零件间搭接与数模状态的稳定性和一致性。
同样,软工装夹具也能达到相同的效果。
软工装造车过程中,软工装定位可以分为两部分:软工装拼台和软工装夹具。
2.1 软工装拼台软工装拼台主要是固定布局软工装夹具。
根据白车身结构特点,软工装拼台一般可以分为:下车体拼台、侧围拼台、总拼拼台、门盖拼台。
柔性工装平台下位机软件设计
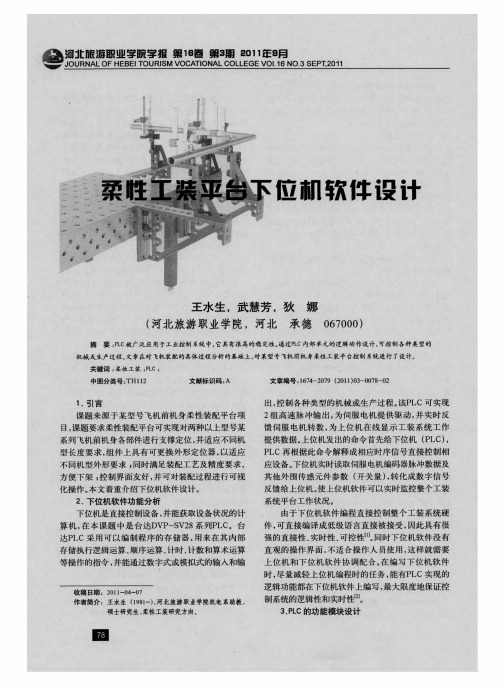
[ 1 】朱熹林等 . 电一体 化设计基础[ 】北京 : 机 M. 科学出版社 , 0 . 24 0 【 2 】汪 晓平 等. 可编 程控制器 系统开 发实例导航[ . MI北京 : 民邮 人
电出版社 , 0 2 4 0
柔性 工装平 台以单 步执行为基本单位 , 下面结合 工艺 需求单步分析 平台工作步骤 。 工装控 制系统首先
实现 自动 进给 , 提高 了系统精 度 , 且降 低 了劳动 强 而 度。
9
手 动微 调模 块 : 由于工 件制 造过 程 的工 艺水平
和工艺 公差 的存在 , 通过工 件数模计算的理论值 不一
定和 实际值 相符 , 需要 进行手动 微调 , 它包括 单轴 手
5 结论 .
本 课题 采 用P C作 为下 位机 , L 通过 对P C软 件 L 功 能模 块分 析 及P C逻 辑 动作设 计 , 编 写 了相应 L 并 模块 的程序。 实验表 明 , 系统满 足工装工艺要求 , 本 实 现 了以单 一工步为基础实现 了整个装配过程控制 , 建 立 了上位机监 控界面的基础 。
第1卷 第3 6 期 王水生 。 武慧芳( 柔性工装 台下位柏软件设计 等)
但作 为飞 机柔性 工装 系统 , 它又有 自己的特点 ,
由于要对飞机 壁板件这种 曲面进行 空间定位 , 需要 多
机加 减速时 间设置及P C通讯 参数设置等 由于各 L 。
个 工 件实 际尺 寸差 异 , 需要 对 各个 装夹 末端 进 行微
工 装 系统 初 始 化
轴协 调控 制来 实现 ; 这种 协调 控制 对 各轴速 度没 而 有特 别要 求 , 际值远低于数 控机床主 轴转速 ; 实 对于 要装 配的 工件理论 数模 , 由于产 品 质量 差异 , 实际情
飞机柔性装配工装关键技术及发展趋势分析

飞机柔性装配工装关键技术及发展趋势分析飞机柔性装配工装关键技术,就是基于数字化技术所开发的新兴飞机尺寸调整方式,能够对飞机设计进行重组,建立出具有参考性的模块,进而形成数字化、自动化的工装系统,能够避免或是减少零部件的使用。
标签:飞机柔性装配;工装关键技术;发展趋势飞机柔性装配工装关键技术在实际应用的过程中,必须要重视飞机制造过程以及制造时间的控制,利用柔性工装可以有效缩短制造周期,提高制造质量,并且减少工装的数量,进而实现较为完善的制造模式。
1 飞机柔性配置工装关键技术现代化飞机柔性配置工装已经不再是单纯的结构工装,而是集成数字化制造方式、现代设计方式、现代化的测量方式等,结合仿真技术实施工装,不断的形成先进性工装研究内容。
此时,关键技术主要包括以下几点:1.1 飞机柔性装配工装模块化技术对于飞机柔性装配工装模块化技术的应用而言,相关技术人员不仅要重视柔性工装的模块化单元构成情况,还要对每个模块进行单独的设计,保证不会出现不符合实际制造的情况。
同时,还要对每个模块的功能加以重视,使设计人员在实施设计工作的时候,能够从装配集中挑选出一个模块单元,快速的实施重组设计工作,进而实现装配工装的柔性化。
由此可见,柔性装配工装设计技术是整个技术体系中最为重要的,每个模块单元,不仅可以单独设计,还能与其他模块相互组合,保证了结构的相似性,同时,设计人员还可以根据飞机结构设计需求,对某个模块重点设计,结合通用模块组,对工装整体装配工作进行优化。
1.2 柔性工装夹紧定位技术工装的柔性化,不仅可以快速的将产品变化情况显现出来,还能突出夹紧定位的应变能力。
对于不同的工装对象,夹紧的方式与结构也是不同的,必须要重视柔性工装夹紧定位方案的实用性,保证能够促进其有效发展,同时,夹紧定位方案还决定着柔性装配工装技术能否有效实现,对其发展就有较为良好的意义。
1.3 柔性装配工装结构优化设计技术与一般工装相比较,柔性工装的结构较为繁琐,合理的设计工作,不仅可以提升飞机结构的强度,還能增强其刚度与稳定性,使飞机装配工作得以有效完成。
铝合金曲面薄壁件柔性工装夹具的加工性能研究
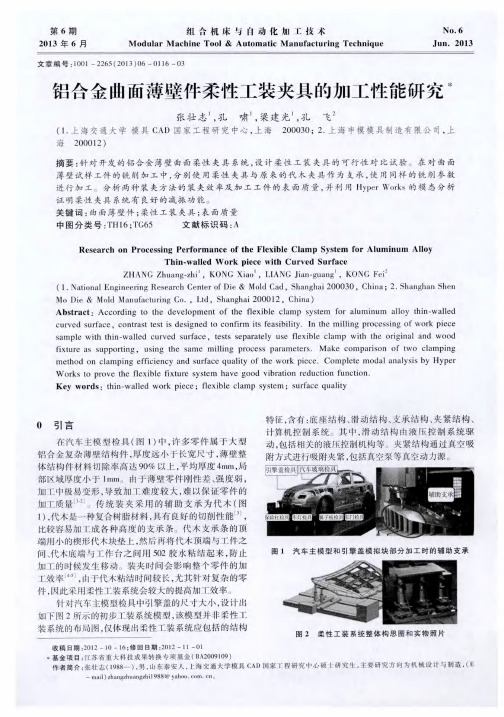
固有频 率 的 降低 更 有 利 于远 离 刀 具 的频 率 , 从 而 避 免 了共 振 的发生 。
表3 柔性 工装 方案 固有 频 率 表
l 3 3 5 5 0 4 1 5 5 7 6 . 4 7
2 高 , 利 用有 限元进 行 振 动状 态 的预 测 越来 越 成 为铣 削参 数 优化
的 有 力 手 段 。
5
l 1 7 0 5 4 2
8 9 l O
3 3 4 9 . 7 7 3 5 7 5 . 2 3 3 6 7 7 . O 5
“ 塞” 进 去的 , 因此不 可能对 工件有着很 大的支承力 。
表 4 代 木 支承 方 案 固有 频 率 表
阶 数
1
2 基 于 Hy p e r Wo r k s 的 模 态 分 析
・
1 1 8・
组 合 机 床 与 自动 化 加 工 技 术
第 6期
在装 夹 时间上 , 代木 由于 需要 不断 调整 、 粘 结等 ,
用时 1 4 m i n , 而柔 性 夹具 仅需 微 调 高度 , 用时 5 a r i n , 为
固有频率 可 以是 多 阶 的 , 当外 激 频 率 和 固 有 频 率 接
1 0
1 6l O 8 . 1 2
鉴 于铣 削 精 加 工 时 余 量 较 小 , 可 忽 略 加 工 后 表 面的壁 厚差 以及 工件 刚度 的 影 响 , 直 接 使 用 工 件 加 T 后 的几何 尺 寸 建 立 模 型 , 这 样 可 以进 一 步 降低 1 二
柔性工装及自动化装配设备在大型飞机装配中的运用
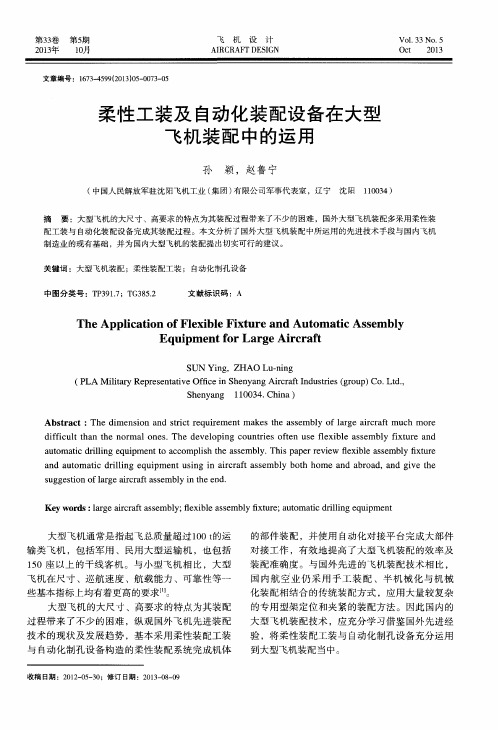
大 型飞 机通 常 是指 起 飞 总质量 超 过 1 0 0 t 的运 输 类 飞机 ,包 括 军用 、民用 大 型运 输 机 ,也 包 括 1 5 0座 以上 的干 线 客 机 。 与小 型 飞 机 相 比 ,大 型
的部 件 装 配 ,并 使 用 自动 化 对接 平 台 完成 大 部件
飞 机 在 尺寸 、巡 航 速度 、航 载 能力 、可 靠性 等 一 些 基本 指标 上均 有着 更高 的要 求 】 。
大型飞机的大尺寸 、高要求的特点为其装配
过 程 带来 了不 少 的 困难 ,纵 观 国外 飞 机 先进 装 配 技 术 的 现状 及 发 展趋 势 ,基 本采 用 柔 性装 配 工 装 与 自动 化制 孔 设 备 构造 的柔 性 装配 系统 完 成机 体
di f ic f ul t t ha n t h e n or ma l o ne s .The d ev e l o pi ng c o u nt r i e s o te f n us e le f xi bl e a s s e mbl y f i x t u r e a nd a u t oma t i c d r i l l i ng e q u i p me nt t o a c c o mpl i s h t h e a s s e mb l y. Thi s p a p e r r e vi e w le f x i bl e a s s e mb l y i f xt u r e a nd a u t o ma t i c d r i l l i n g e q ui p me n t us i n g i n a i r c r a f t a s s e mb l y bo t h h o me a nd a br o a d,a n d gi v e t h e
关于飞机数字化柔性装配工装技术的探索

关于飞机数字化柔性装配工装技术的探索摘要:本文首先对飞机数字化柔性装配工装技术的特点进行总结,对柔性化装配工装关键技术进行分析,对我国飞机数字化柔性装配的发展要求进行研究,对于减少我国飞机数字化装配技术和国外先进水平的差距,实现飞机研发和制造行业的跨越式发展,具有非常重要的意义。
关键词:飞机数字化柔性装配工装技术1、引言飞机数字化柔性装配工装技术是数字化装配技术的重要内容,已经在国内外航空企业得到广泛应用。
到目前为止,飞机装配工装技术已经经历了许多阶段,从最初的手工装配、半自动化装配、自动化装配,再到现在的柔性装配工装技术。
所谓“柔性装配工装技术”,就是基于产品数字量尺寸的,可以进行重组的模块化,以及自动化的装配工装技术。
一方面可以降低制造成本、缩短周期的同时,也提高了装配生产率。
本文对有关飞机数字化柔性装配工装技术进行分析和探讨,不足之处,敬请指正。
2 飞机数字化柔性装配工装技术的特点飞机数字化柔性装配工装技术的最大特点就是能够在产品数字量尺寸传递系统的基础上,以及配合数字化控制技术和系统,对产品装配等工作进行操作。
除此之外,飞机数字化柔性装配工装技术还克服了传统制造方法中模拟量协调系统的基础上装配工装的技术特点,比如说应用单一、生成周期较长、生成成本较高以及生成配合较为困难等。
还有就是,飞机数字化柔性装配工装技术能够实现和自动化制空设备、铆接设备、机器人等设备进行相互集成,达到柔性化装配精确度更高以及提升装配效率的目的。
3 柔性化装配工装关键技术飞机装配主要有以下四个阶段,为:装配设计、装配准备、装配进行以及装配测试,每一个阶段都有一个关键的技术,依次支撑飞机装配工艺技术,能够实现整个飞机装配高质量的同时,保持高效率。
3.1 定位技术飞机装配中柔性化定位技术的使用,可以在一定程度上减少零件结构发生变化的次数,同时也避免传统刚性定位方法中那种定位应力。
框梁类传统装配定位技术是基于工艺孔或者是结构交点孔进行定位,这种方法的工作量较大,而且生成效率较低。
蒙皮件铣切吸盘式柔性工装设计
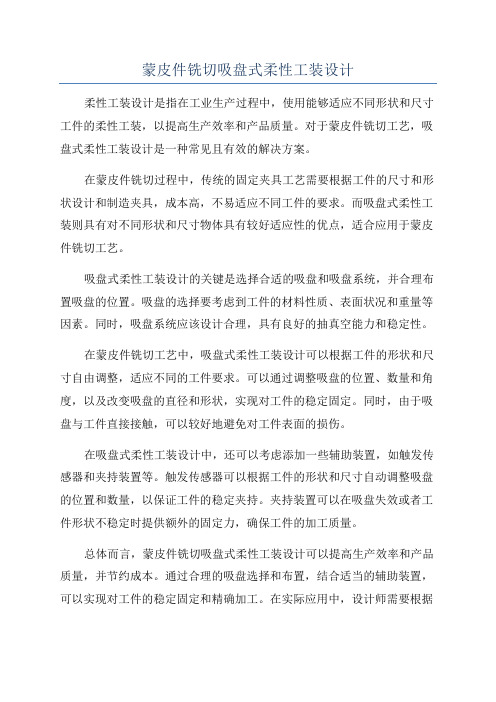
蒙皮件铣切吸盘式柔性工装设计柔性工装设计是指在工业生产过程中,使用能够适应不同形状和尺寸工件的柔性工装,以提高生产效率和产品质量。
对于蒙皮件铣切工艺,吸盘式柔性工装设计是一种常见且有效的解决方案。
在蒙皮件铣切过程中,传统的固定夹具工艺需要根据工件的尺寸和形状设计和制造夹具,成本高,不易适应不同工件的要求。
而吸盘式柔性工装则具有对不同形状和尺寸物体具有较好适应性的优点,适合应用于蒙皮件铣切工艺。
吸盘式柔性工装设计的关键是选择合适的吸盘和吸盘系统,并合理布置吸盘的位置。
吸盘的选择要考虑到工件的材料性质、表面状况和重量等因素。
同时,吸盘系统应该设计合理,具有良好的抽真空能力和稳定性。
在蒙皮件铣切工艺中,吸盘式柔性工装设计可以根据工件的形状和尺寸自由调整,适应不同的工件要求。
可以通过调整吸盘的位置、数量和角度,以及改变吸盘的直径和形状,实现对工件的稳定固定。
同时,由于吸盘与工件直接接触,可以较好地避免对工件表面的损伤。
在吸盘式柔性工装设计中,还可以考虑添加一些辅助装置,如触发传感器和夹持装置等。
触发传感器可以根据工件的形状和尺寸自动调整吸盘的位置和数量,以保证工件的稳定夹持。
夹持装置可以在吸盘失效或者工件形状不稳定时提供额外的固定力,确保工件的加工质量。
总体而言,蒙皮件铣切吸盘式柔性工装设计可以提高生产效率和产品质量,并节约成本。
通过合理的吸盘选择和布置,结合适当的辅助装置,可以实现对工件的稳定固定和精确加工。
在实际应用中,设计师需要根据具体工件的要求和生产工艺的特点,进行合理的柔性工装设计。
同时,应注重吸盘的维护和检修工作,保证吸盘和吸盘系统的良好工作状态。
飞机蒙皮柔性检测工装的应用

飞机蒙皮柔性检测工装的应用甘忠,蒲理华(西北工业大学现代设计与集成制造技术教育部重点实验室)许旭东,袁胜(成都飞机工业(集团)有限责任公司)随着国内外航空技术的不断发展,各种军用和民用飞机更新速度加快,为提高飞机的气动性能,对蒙皮件的成形质量提出了很高的要求。
由于飞机蒙皮件普遍具有多品种、小批量以及单件生产的特点,零件检测、配套的工装生产以及产品的快速响应与降低零件制造成本等因素构成了巨大的矛盾。
以模线、样板、表面样件、正反模型等模拟量为制造依据的传统协调方式不再完全满足现代飞机高精度、低成本、短周期的研制需求,以数字量为制造依据的协调方式逐渐成为现代飞机研制的主流。
在此情况下,柔性快速检测技术开始在飞机研制过程中广泛应用,并成为现代飞机研制过程中不可缺少的一环。
由于飞机蒙皮零件通常是具有自由曲面外形的薄壁壳体,外形尺寸复杂,刚度低,会在自身重力的作用下发生变形。
在检验蒙皮零件的外形是否符合理论外形时,需要设计合理的固持装置,补偿零件由于加紧力、自身重力产生的变形,获得零件在自由状态下的外形,为制造协调提供依据。
因此迫切需要建立一种新的蒙皮检测工装来满足飞机零件制造的要求。
针对现代飞机蒙皮零件在试制阶段高精度、低成本、短周期的制造需求,需要研究一种数字化、柔性、低成本、快速生产的检测工装,飞机蒙皮柔性检测工装恰好符合这种具有小批量、低成本、高精度要求的飞机蒙皮件生产的需要。
传统飞机蒙皮检测手段飞机蒙皮从曲面特征上一般分为单曲度蒙皮和双曲度蒙皮,曲面特征不同,所以检测手段也不同。
单曲度蒙皮零件:需要使用样板或者成套的切面样板、塞尺、直尺、模胎,以检验零件的外形与理论外形的符合情况、母线的直线性以及零件的轮廓尺寸。
检验方法是:使样板对准蒙皮的横切面并且测量它们之间的间隙;使直尺和蒙皮纵切面贴合并测量间隙;使蒙皮边缘对准模胎或样板上的切割线。
双曲度蒙皮零件:需要使用模胎、拉型模、检验架、塞尺来检验零件外形与理论外形的符合情况以及零件的轮廓尺寸。
- 1、下载文档前请自行甄别文档内容的完整性,平台不提供额外的编辑、内容补充、找答案等附加服务。
- 2、"仅部分预览"的文档,不可在线预览部分如存在完整性等问题,可反馈申请退款(可完整预览的文档不适用该条件!)。
- 3、如文档侵犯您的权益,请联系客服反馈,我们会尽快为您处理(人工客服工作时间:9:00-18:30)。
飞机薄壁杆柔性工装技术
0引言
随着航空制造技术的飞速发展,在现代飞机设计中,整体机加铝合金薄璧零件的应用越来越广泛,从框、梁、地板到壁板都大量采用整体机加薄璧结构。
整体机加薄璧零件有许多优势,它既可以减轻结构的重量,提高飞机的有效载重,同时也可以增强结构强度,减少连接件数量,提高飞机的疲劳寿命,提高飞机的承载重量,极大地满足现代飞机设计的要求。
但是超长薄壁结构件由于其结构刚度低,加工工艺性差,在切削力、切削热、装夹力作用下易发生加工变形、切削振颤等现象,很难保证加工精度和表面质量的要求,是飞机研制中普遍存在的难题。
关于大型薄壁件加工变形问题,国内研究人员也进行了大量的探索提出了一些实用的方法,但理论研究工作与国外发达国家相比还存在较大差距,到目前为止对大型薄壁零件的加工仍缺乏十分有效的方法,特别是在以飞机蒙皮为代表的大型薄壁曲面零件加工方面,生产厂家一般采用“先加工后成形工艺”,但该方法存在以下严重问题。
经过成形工序后原先加工好的零件周边轮廓和窗孔部位将产生很大变形,使后续总装工序必须通过人工修整才能完成各零件的装配,这种通过人工修整进行总装的方法,不仅效率低而且更为严重的是难以保证精度,往往造成各零件结合部之间的间隙不均匀,对飞行器的气动性能和隐身性能均造成很大影响。
新发展起来的“先成形后加工工艺”为解决传统的“先加工后成形工艺”存在的问题开辟了新的途径。
但是实施这一新工艺时碰到一大难题成形后的半成品为刚度极差的弹性薄壁件且其表面轮廓为自由曲面,传统的针对刚性体的六点定位原理不适用于这类弹性体曲面零件,无法根据现有理论设计制造相应的工艺装备。
由此严重影响机械加工的正常进行,目前解决此问题的技术途径主要有两条:
1刚性途径。
弹性体曲面刚性定位技术按此得到的工装定位,支承曲面不具有可变性,因此一种工装只能用于一种零件,这将大幅度降低制造柔性和效率,同时也涉及大量刚性工装的存放,维护,管理等问题。
2柔性途径。
弹性体曲面柔性定位技术该方法通过调整,控制等手段来动态生成所需的工装定位。
因此一种工装可用于不同零件的加工,可大幅度提高制造柔性和效率,并可通过信息化手段进行误差校正,从而提高加工精度。
显然柔性途径比刚性途径具有明显优势。
本文要利用柔性工装技术途径实现减小最大加工变形,必须解决柔性工装系统运行模式优化生成算法等关键问题。
1大型薄壁件特点
从加工的角度看,飞机大型薄壁件有如下特点:1)定位面为弹性曲面,不能依据常规的六点定位原理进行定位,而必须通过众多定位点形成的点阵包络进行定位;2)加工中极易变形,必须设置众多支承点;3)定位与支承不能截然分开,两者的实施必须统一考虑。
系统所能提供的最大支承密度将决定工件的最大变形,为保证系统在需要的时候能将更多的支承单元聚集在一个较小的区域内,要求各支承单元占据的空间要尽可能小。
2柔性工装技术自生成问题
柔性工装系统中支承单元是最重要的硬件资源,但其数量是有限的。
因此在系统运行过程中如何最佳利用有限的资源使系统获得最高的运行效益,便成为柔性工装系统运行管理与控制中的关键问题。
解决此问题的有效途径是为系统制订合理的运行模式,并据此对系统的运行实施控制。
柔性工艺装备系统的运行模式是指系统工作时其支承阵列布局的拓扑形态和分布密度。
显然,运行模式对工艺装备系统的运行性能有着直接的影响。
目前,可通过多种方法来生成柔性工装系统的运行模式,如随机方法、均布方法、经验方法、优化方法等。
随机方法和均布方法是最简单的运行模式生成方法,但不能达到好的运行效果。
例如,对于均布方法,所生成的运行模式为各支承单元按等间距均匀排列,形成矩阵形式的支承阵列,此时支承的分布密度在工作空间中任何区域都是相同的,对工件变形不能做到有针对性的重点防控,经验方法则依赖操作人员的经验来生成系统运行模式,并通过外部指令将运行模式信息传递给工装系统的控制计算机,以控制系统的运行,所产生的效果因人而异,因时而异。
而优化方法则是按照规定的优化目标,由控制计算机根据加工现场的状态信息来自动生成支承阵列布局的拓扑形态和分布密度。
因此,该方法是一种不依赖外部操作者
的自生成方法,可以按照自生成原实现系统运行的最优化。
由于基于自生成原理的优化方法,可根据系统的自身状态信息,如重力负荷、加工受力、温度变化等等来合理确定支承阵列布局的拓扑形态,并按需分配定位支承的分布密度,从而使有限的资源得以最佳利用,使整个系统获得最佳综合效益。
因而,它是一种较理想的系统运行模式生成方法。
优化生成系统运行模式,须首先根据系统运行的实际情况确定合理的优化目标,并根据约束条件来建立便于优化求解的数学模型。
考虑飞行器大型薄壁件加工中工件变形是影响加工质量和效率的主要因素,因此,本文在解决工装系统运行模式优化生成时,将工件加工变形最小作为运行模式优化生成的目标函数所考虑的约束条件,主要包括系统结构约束和工艺条件约束。
3运行模式的优化生成算法
考虑到柔性工装系统运行模式的优化生成问题为一多变量、多约束优化问题,而传统的优化算法多为局部优化,且计算量大、收敛速度较慢,对于多变量,多约束的结构优化问题不易取得好的效果。
因此,本文通过有限元算法的途径来解决系统运行模式的优化生成问题,该算基于上述思想所构成的系统运行模式优化生成算法的基本流程如图1所示
图1柔性工装系统运行模式优化生成算法的基本流程
为实现图1算法流程,需建立工件变形的有限元分析模型,并据此计算工件变形量考虑到本文针对的待加工工件为航空薄壁件,材料为铝合金轮廓为自由曲面,故取整个待加工曲面为研究对象曲面应shell 181壳单元,弹性模量为70GPa 泊松比为0.3,在待加工部位施加沿曲面法向的压强大小为0.05MPa,并按照20mm的长度进行网格划分,整个有限元建模和求解过程基于ansys语言实现。
航空薄壁零件样件如图2,航空薄壁件样件有限元模型如图3
为实现该算法,需进一步解决以下关键问题
1)适值函数建立。
优化的目标是减小最大加工变形,所以将最大加工变形的倒数作为适值函数
2)约束的处理
3)算术交叉
4)非均匀变异
图2航空薄壁零件样件图3航空薄壁件样件有限元模型
4结语
运行模式生成是飞行器大型薄壁件柔性工艺装备系统运行管理与控制中的关键问题。
本文提出了这类系统柔性工装技术自生成问题的方法,该方法以工件加工变形最小为目标函数,以工装结构及加工工艺为约束条件建立问题的数学模型,通过有限元分析的途径进行自寻优求解,经过不断自身进化,所生成的运行模式可使柔性工装系统中支承阵列布局的拓扑形态和分布密度处于最优状态,从而使系统资源得到最佳利用,为柔性工艺装备系统的高质高效运行奠定了基础。
理论分析与实例验证表明:所提出的柔性工装系统运行模式优化生成算法具有较强的全局搜索能力,对于本文所针对的多变量优化问题具有良好效果。
5结论
1涂层表面的接触压力和接触面积随着压入深度的增大而不断增大,但由于屈服产生塑性变形,故接触压力峰值趋于平缓。
2保持涂层系统的各层材料特性不变,随着压入深度的增大,最大当量应力值也不断增大,但当材料屈服时,就保持不变,表面涂层厚度的增大有助于减小涂层屈服前表面的应力,在一定厚度和屈服强度条件下,不断增大表面陶瓷涂层和黏结层弹性模量比最大,当量应力也不断增大。
3相比于涂层的弹性模量屈服强度,对于涂层沿深度方向的残余应力有着更为显著的影响,因此,调整材料的屈服强度更容易改变涂层材料的应力幅值。
4各层弹性模量的差异是涂层界面产生应力突变的原因。
因此改变弹性模量比可以有效减小界面的应力突变,改善材料的应力状态。
总之,由涂层材料屈服后产生的塑性变形是涂层材料中残余应力存在的根本,塑性变形的累积和过大的界面应力突变是造成涂层产生裂纹和脱落的主要因素,研究如何减小界面应力、突变的幅度以及塑变区,对工程实际具有重要意义。
[1] 邹冀华, 刘志存, 范玉青. 大型飞机部件数字化对接装配技术研究. 计算机集成制造系统, 2007, 13(7): 1367-1373.
[2] 秦政琪, 范振伟. 飞机薄壁组件数字化柔性装配研究.沈阳航空工业学院学报, 2009, 26(3):l-4.
[3] 邹方. 飞机制造中数字化柔性装配技术的发展. 制造业自动化,2005, 27:263-270.
[4] Williams G, Chalupa E, Rahhal S. Automated positioning and alignment systems. Society of Automotive Engineers, Inc. 2000-01-3014.。