常减压蒸馏装置操作参数十六大影响因素
影响常减压蒸馏装置能耗的问题分析与节能对策
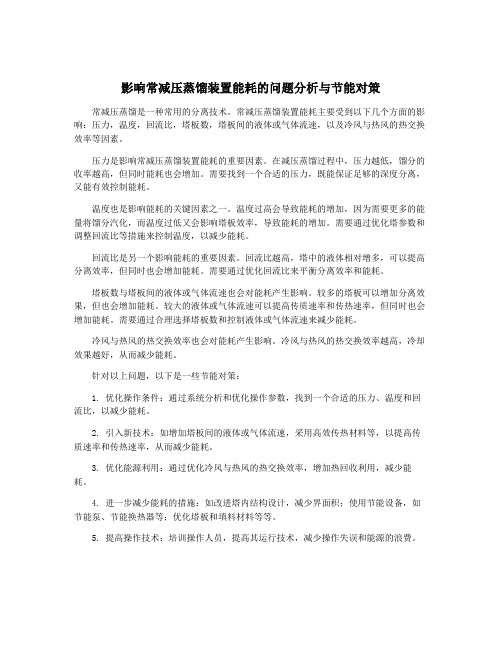
影响常减压蒸馏装置能耗的问题分析与节能对策常减压蒸馏是一种常用的分离技术。
常减压蒸馏装置能耗主要受到以下几个方面的影响:压力,温度,回流比,塔板数,塔板间的液体或气体流速,以及冷风与热风的热交换效率等因素。
压力是影响常减压蒸馏装置能耗的重要因素。
在减压蒸馏过程中,压力越低,馏分的收率越高,但同时能耗也会增加。
需要找到一个合适的压力,既能保证足够的深度分离,又能有效控制能耗。
温度也是影响能耗的关键因素之一。
温度过高会导致能耗的增加,因为需要更多的能量将馏分汽化,而温度过低又会影响塔板效率,导致能耗的增加。
需要通过优化塔参数和调整回流比等措施来控制温度,以减少能耗。
回流比是另一个影响能耗的重要因素。
回流比越高,塔中的液体相对增多,可以提高分离效率,但同时也会增加能耗。
需要通过优化回流比来平衡分离效率和能耗。
塔板数与塔板间的液体或气体流速也会对能耗产生影响。
较多的塔板可以增加分离效果,但也会增加能耗。
较大的液体或气体流速可以提高传质速率和传热速率,但同时也会增加能耗。
需要通过合理选择塔板数和控制液体或气体流速来减少能耗。
冷风与热风的热交换效率也会对能耗产生影响。
冷风与热风的热交换效率越高,冷却效果越好,从而减少能耗。
针对以上问题,以下是一些节能对策:1. 优化操作条件:通过系统分析和优化操作参数,找到一个合适的压力、温度和回流比,以减少能耗。
2. 引入新技术:如增加塔板间的液体或气体流速,采用高效传热材料等,以提高传质速率和传热速率,从而减少能耗。
3. 优化能源利用:通过优化冷风与热风的热交换效率,增加热回收利用,减少能耗。
4. 进一步减少能耗的措施:如改进塔内结构设计,减少界面积;使用节能设备,如节能泵、节能换热器等;优化塔板和填料材料等等。
5. 提高操作技术:培训操作人员,提高其运行技术,减少操作失误和能源的浪费。
常减压蒸馏装置能耗问题是一个综合性问题,需要从多个方面考虑,采取相应的节能对策来减少能耗。
影响常减压蒸馏装置能耗的问题分析与节能对策
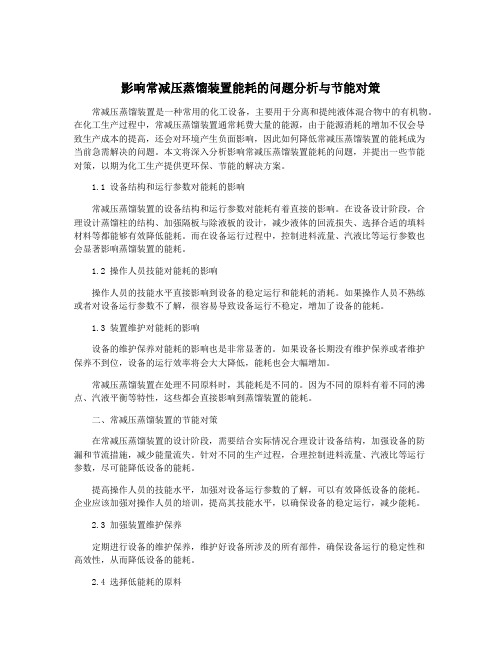
影响常减压蒸馏装置能耗的问题分析与节能对策常减压蒸馏装置是一种常用的化工设备,主要用于分离和提纯液体混合物中的有机物。
在化工生产过程中,常减压蒸馏装置通常耗费大量的能源,由于能源消耗的增加不仅会导致生产成本的提高,还会对环境产生负面影响,因此如何降低常减压蒸馏装置的能耗成为当前急需解决的问题。
本文将深入分析影响常减压蒸馏装置能耗的问题,并提出一些节能对策,以期为化工生产提供更环保、节能的解决方案。
1.1 设备结构和运行参数对能耗的影响常减压蒸馏装置的设备结构和运行参数对能耗有着直接的影响。
在设备设计阶段,合理设计蒸馏柱的结构、加强隔板与除液板的设计,减少液体的回流损失、选择合适的填料材料等都能够有效降低能耗。
而在设备运行过程中,控制进料流量、汽液比等运行参数也会显著影响蒸馏装置的能耗。
1.2 操作人员技能对能耗的影响操作人员的技能水平直接影响到设备的稳定运行和能耗的消耗。
如果操作人员不熟练或者对设备运行参数不了解,很容易导致设备运行不稳定,增加了设备的能耗。
1.3 装置维护对能耗的影响设备的维护保养对能耗的影响也是非常显著的。
如果设备长期没有维护保养或者维护保养不到位,设备的运行效率将会大大降低,能耗也会大幅增加。
常减压蒸馏装置在处理不同原料时,其能耗是不同的。
因为不同的原料有着不同的沸点、汽液平衡等特性,这些都会直接影响到蒸馏装置的能耗。
二、常减压蒸馏装置的节能对策在常减压蒸馏装置的设计阶段,需要结合实际情况合理设计设备结构,加强设备的防漏和节流措施,减少能量流失。
针对不同的生产过程,合理控制进料流量、汽液比等运行参数,尽可能降低设备的能耗。
提高操作人员的技能水平,加强对设备运行参数的了解,可以有效降低设备的能耗。
企业应该加强对操作人员的培训,提高其技能水平,以确保设备的稳定运行,减少能耗。
2.3 加强装置维护保养定期进行设备的维护保养,维护好设备所涉及的所有部件,确保设备运行的稳定性和高效性,从而降低设备的能耗。
影响常减压蒸馏装置能耗的问题分析与节能对策

影响常减压蒸馏装置能耗的问题分析与节能对策常减压蒸馏装置是一种常见的化工装置,广泛应用于石油化工、化工制药等领域。
常减压蒸馏装置的能耗问题一直被广大工程师所关注。
本文将从设备结构、操作参数和控制策略三个方面进行分析,提出一些节能对策。
设备结构对于常减压蒸馏装置的能耗起着决定性的影响。
常减压蒸馏塔的结构可以分为传统型和节能型两种。
传统型塔采用常规的圆形塔筒结构,通常存在流动阻力大、相接触不充分等问题,导致能耗较高。
而节能型塔则采用六边形装料塔盘、曲线设计的塔筒等结构,能够有效降低流动阻力、提高相接触效果,降低能耗。
在设计常减压蒸馏装置时,应优先选择节能型塔的结构,以降低能耗。
操作参数的选择对于常减压蒸馏装置的能耗也有重要影响。
通常常减压蒸馏装置的操作参数包括进料温度、压力、规定流量等。
进料温度的选择应尽量降低,以减少热能消耗。
压力的选择应适中,既要保证蒸馏过程的正常进行,又要尽量降低能耗。
规定流量的选择应根据具体情况进行调整,避免过大或者过小造成能耗的浪费。
在操作常减压蒸馏装置时,应根据实际情况选择适当的操作参数,以降低能耗。
控制策略的制定对于常减压蒸馏装置的能耗起着至关重要的作用。
常减压蒸馏装置的控制策略可以分为传统的比例积分控制和先进的模型预测控制两种。
传统的比例积分控制方法对于装置的能耗控制效果较差,容易造成能耗浪费。
而模型预测控制方法可以根据装置的动态响应情况预测未来的操作状态,并根据优化目标制定最优的控制策略,从而有效降低能耗。
在控制常减压蒸馏装置时,应优先选择模型预测控制方法,以降低能耗。
常减压蒸馏装置的能耗问题需要从设备结构、操作参数和控制策略三个方面进行考虑。
在设计装置时,应选择节能型的设备结构;在操作装置时,应选择合适的操作参数;在控制装置时,应采用先进的模型预测控制策略。
这些措施的采取将有助于降低常减压蒸馏装置的能耗,提高能源利用效率。
常减压蒸馏装置生产中的问题与解答
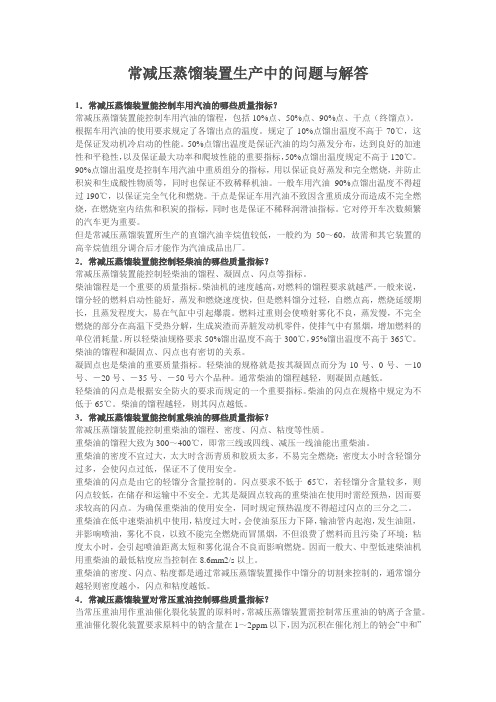
常减压蒸馏装置生产中的问题与解答1.常减压蒸馏装置能控制车用汽油的哪些质量指标?常减压蒸馏装置能控制车用汽油的馏程,包括10%点、50%点、90%点、干点(终馏点)。
根据车用汽油的使用要求规定了各馏出点的温度。
规定了10%点馏出温度不高于70℃,这是保证发动机冷启动的性能。
50%点馏出温度是保证汽油的均匀蒸发分布,达到良好的加速性和平稳性,以及保证最大功率和爬坡性能的重要指标,50%点馏出温度规定不高于120℃。
90%点馏出温度是控制车用汽油中重质组分的指标,用以保证良好蒸发和完全燃烧,并防止积炭和生成酸性物质等,同时也保证不致稀释机油。
一般车用汽油90%点馏出温度不得超过190℃,以保证完全气化和燃烧。
干点是保证车用汽油不致因含重质成分而造成不完全燃烧,在燃烧室内结焦和积炭的指标,同时也是保证不稀释润滑油指标。
它对停开车次数频繁的汽车更为重要。
但是常减压蒸馏装置所生产的直馏汽油辛烷值较低,一般约为50~60,故需和其它装置的高辛烷值组分调合后才能作为汽油成品出厂。
2.常减压蒸馏装置能控制轻柴油的哪些质量指标?常减压蒸馏装置能控制轻柴油的馏程、凝固点、闪点等指标。
柴油馏程是一个重要的质量指标。
柴油机的速度越高,对燃料的馏程要求就越严。
一般来说,馏分轻的燃料启动性能好,蒸发和燃烧速度快,但是燃料馏分过轻,自燃点高,燃烧延缓期长,且蒸发程度大,易在气缸中引起爆震。
燃料过重则会使喷射雾化不良,蒸发慢,不完全燃烧的部分在高温下受热分解,生成炭渣而弄脏发动机零件,使排气中有黑烟,增加燃料的单位消耗量。
所以轻柴油规格要求50%馏出温度不高于300℃,95%馏出温度不高于365℃。
柴油的馏程和凝固点、闪点也有密切的关系。
凝固点也是柴油的重要质量指标。
轻柴油的规格就是按其凝固点而分为10号、0号、-10号、-20号、-35号、-50号六个品种。
通常柴油的馏程越轻,则凝固点越低。
轻柴油的闪点是根据安全防火的要求而规定的一个重要指标。
浅谈常减压蒸馏装置拔出率的影响因素

技术应用与研究当今社会中,石油作为重要资源,各国对石油原油加工制造业越发重视。
石油原油通过装置提炼加工成高品质的油品,可以获得更高的效益。
其中,常减压蒸馏装置在原油加工过程中扮演着十分重要的角色。
目前我国常减压蒸馏装置的技术水平还有待提高,还需提高装置拔出率,增加效益。
需要对影响常减压蒸馏装置的各种因素进行分析,优化改进设备装置,达到较高的常减压蒸馏装置拔出率。
一、影响装置拔出率的因素1.常压拔出率不稳定影响总体拔出率常压系统的拔出率不稳定会对减压系统造成影响,当常压系统拔出率较低时,减压系统会超负荷运行,这样会造成资源能耗的过度使用浪费。
但常压系统的拔出率较高也会造成因油温降低而产生的过多能源消耗。
所以常压装置拔出率的不稳定会造成更多的能源消耗,同时对减压塔内真空状况有所影响,继而导致常减压蒸馏装置拔出率降低。
2.减压塔真空度不稳定当减压塔内真空不足时,石油的汽化率就会降低,大大降低了减压系统的拔出率,影响常减压蒸馏装置的拔出率。
当减压塔内真空度过高时,石油汽化率也会大大提高,但是过高的汽化率会导致原料结焦的风险提高,不利于常减压蒸馏装置长期的运行操作。
减压塔较低不稳定的真空度导致了减压系统拔出率的降低。
3.减压炉出口及减压塔底温度不稳定减压炉出口温度不够高,汽化段温度不够汽化率低,直接导致加压系统的拔出率较低。
二、提高常减压蒸馏装置拔出率的措施1.稳定常压系统拔出率,增加汽油收率 在常压蒸馏中,同样也需要稳定的环境,保持常压系统总体温度,有利于提高拔出率。
提高原油进塔温度,增强换热效果,避免常压系统炉管结焦情况的发生,以免造成加热不均的情况。
同时,要增加汽油收率,提高初常顶冷却能力,稳定常压系统拔出率,不易过高的常压系统拔出率,可提高常减压蒸馏装置整体拔出率,建议可使用先进控制系统提高常压系统蒸馏效果。
2.控制减压塔真空度要注意蒸汽压力需达到要求,水汽配比要恰当,抽空器中不要出现串气和倒气,常压系统拔出率要稳定不能过低,减压塔顶部温度不能过高,循环水不能中断或者温度过高导致水冷器无法冷却,操作要得当达到要求。
影响蒸馏塔平稳操作的主要因素

影响蒸馏塔平稳操作的主要因素作者:白明玉来源:《中小企业管理与科技·下旬》2010年第07期摘要:本文通过多方面查阅文献及日常操作,总结出对蒸馏操作的主要影响因素。
通过原因分析总结出适当的调整方法。
关键词:温度回流量塔顶压力塔顶温度塔底液面吹汽量真空度0 引言常减压蒸馏装置是原油加工的龙头装置,其侧线产品及塔底渣油为下游装置提供加工原料。
初顶和常顶生产石脑油做为催化重整的原料;常三线、减一线、减二线供“中压加氢裂化”做原料;最后的减底渣油送至催化裂化装置。
所以蒸馏操作的稳定与否直接影响下游装置的运行,本文全面分析了影响蒸馏塔平稳操作的因素。
1 进料温度、流量和性质蒸馏塔的平稳操作就是通过对温度、压力、流量和液位四大操作参数的调节,使蒸馏塔最大限度的接近于物料平衡、热量平衡和汽液相平衡的稳定状态。
进料状态的变化会使进塔的汽、液相流量和进塔的热量变化,这就改变了整个塔内的三大平衡,即物料平衡、热量平衡和汽液相平衡。
在操作上,反映在塔顶温度、塔顶压力、侧线温度的变化上。
这是蒸馏平稳操作的重要前提之一。
2 回流量塔内的回流是精馏的必要条件,它有以下两个作用:2.1 提供塔板上的液相回流,创造汽液两相充分接触的条件,达到传热传质的目的;2.2 取走塔内多余的热量,维持全塔热量平衡和汽液相平衡,以利于控制产品质量。
回流量变化不仅改变塔内汽液相负荷,影响每一块塔板上的分馏效果,同时也改变了塔内的热量分布和平衡。
在调整中,原则上是适当增加高中温位的中段回流量,有利于回收余热,节约能耗。
3 塔顶压力塔顶压力反映了整个塔内操作压力的大小。
油品汽化温度与油汽分压有关,一般当塔内吹入蒸汽量一定时,油汽分压与操作压力成正比。
塔压的变化,能够比较灵敏的反映塔内汽液负荷的变化。
因此,在操作中要密切注意塔压指示,遇有异常波动要及时分析原因,进行调节。
4 塔顶温度塔顶温度是塔顶产品在其油气分压下的露点温度。
塔顶温度的变化还反映了塔内汽液相负荷的变化。
常减压装置总拔影响因素及改进措施

16常减压蒸馏是炼油厂原油加工的“龙头”装置,其主要任务是将原油中的轻质油馏分按馏程拔出,输送给下游装置做原料[1][2]。
目前国内采油厂开采出来的原油性质存在着两个发展趋势:劣质化及重质化。
加工原油性质的变化直接导致炼化企业生产成本增加,重质油料难以平衡,减压渣油收率逐年升高,装置总拔下降,最终迫使很多常减压装置降量生产。
1 现状分析玉门炼油化工总厂常减压装置现阶段通过原油罐区岗位调和不同批次的单种原油,以混炼方式进行加工,原料性质波动较大。
由于我厂购进吐哈重质原油,造成原料油密度明显上升,减压渣油收率大幅升高,最终导致装置总拔下降。
因此,进一步提高常减压装置的拔出率,是装置现阶段的关键性难题,也是提高经济效益的重要手段。
2 影响常减压蒸馏装置总拔的因素常减压蒸馏装置总拔即为除去减压渣油以外,装置其余所有产品之和占总产量的百分比。
其中,初馏塔产品收率、常压塔产品收率及减压塔产品收率都是总拔的直接影响因素。
2.1 初馏塔产品收率初馏塔的主要产品有干气和汽油馏分,其产率由原油组成及性质决定,同时,不平稳的操作,也会影响初馏塔的产品收率。
初顶压力和温度是影响初馏塔收率的主要因素,而初馏塔的进料温度是由装置原油二段换热终温直接决定的,过低的进料温度会直接造成初馏塔收率偏低。
因此,良好的原油二段换热终温以及适宜的塔顶温度和压力,是得到较高初顶汽油收率的有效保证。
2.2 常压塔产品收率常压塔设置了塔顶冷回流、常顶循环回流、常一中及常二中2个中段回流,用以平衡塔内汽液相负荷。
主要产品有:干气、汽油、常一线航煤、常二线轻柴以及常三线重柴。
生产运行过程中,原油性质一旦确定,常压塔进料温度、提馏段温度、油气分压都直接影响常压塔的拔出率。
其中,初底油在常压塔提馏段的温度直接由常压炉出口温度与常压塔转轴线的温度决定。
而塔顶压力、进料段压力、提轻塔的汽提蒸汽量和塔底汽提蒸汽量则共同决定了油气分压的大小。
由此看出,提高常压塔轻收的突破点就在提馏段的温度和油气分压上。
常减压蒸馏装置减压深拔的影响因素及改进措施

第28卷 第1期2010年1月 石化技术与应用Petr oche m ical Technol ogy&App licati on Vol128 No11 Jan.2010工业技术(41~43)常减压蒸馏装置减压深拔的影响因素及改进措施刘志刚1,周立岩2(1.中国中化集团公司石油中心,北京100031;2.中国石油锦州石化公司,辽宁锦州121001)摘要:对中国石油锦州石化公司常减压蒸馏装置减压深拔的可行性,减压深拔影响因素,所采取的优化措施及实施效果进行了分析。
结果表明,辽河原油在切割点570℃之前的馏分性质比较稳定,温度、压力和汽提蒸汽量是影响减压深拔拔出率的主要因素。
通过转油线、减压炉管、进料分布器改造,提高减压塔真空度、降低减压塔压降、提高常压系统拔出率、调整减压塔取热分配等措施后,蜡油收率由28.95%提高到30.40%,蜡油残炭质量分数由0.27%提高到0.38%。
关键词:常减压蒸馏;减压深拔;拔出率;温度;压力;汽提蒸汽量中图分类号:TE624.2 文献标识码:B 文章编号:1009-0045(2010)01-0041-03 减压深拔是通过提高现有重质馏分油切割温度,来增加馏分油拔出率的方法,它是提高常减压蒸馏装置拔出率的主要途径。
减压深拔的效益不仅体现在常减压蒸馏装置,而且体现在下游催化裂化、延迟焦化等装置,甚至还体现在整个炼厂的综合效益上,因此探索减压蒸馏装置深拔的可能性、挖掘现有资源潜力并提出相应措施受到国内外炼油界的关注[1]。
目前,国外减压深拔中减压炉分支温度达到420℃以上,原油实沸点切割温度达到565~620℃[2],而国内炼厂原油实沸点切割温度一般在490~535℃[3],与国外相比差距较大,因而,如何提高重质馏分油切割点、提高拔出率仍需进行深入研究。
本工作对中国石油锦州石化公司(简称锦州石化)常减压蒸馏装置减压深拔的可行性,减压深拔影响因素,所采取的优化措施及实施效果进行了分析。
- 1、下载文档前请自行甄别文档内容的完整性,平台不提供额外的编辑、内容补充、找答案等附加服务。
- 2、"仅部分预览"的文档,不可在线预览部分如存在完整性等问题,可反馈申请退款(可完整预览的文档不适用该条件!)。
- 3、如文档侵犯您的权益,请联系客服反馈,我们会尽快为您处理(人工客服工作时间:9:00-18:30)。
常减压蒸馏装置操作参数十六大影响因素((十一)常压塔底液位常压塔底液位发生变化,会影响常压塔底泵出口流量发生波动,如果减压炉没有及时调整火嘴的发热量,会导致减压炉出口温度波动,即为减压塔进料温度发生变化,这样会导致减压塔操作波动,严重时会使减压侧线产品质量指标不合格。
所以,常压塔底液位稳定是减压系统平稳操作的前提条件。
一般,常压塔底液位控制在50%±10%的范围内。
常压塔底液位的影响因素有:常压塔进料量、常底泵出口流量、汽化率(进料温度、进料性质、侧线抽出量多少.塔底注汽量、塔顶压力)。
1.进料量常压塔底进料量主要由初底油泵出口流量控制,进料量增大,则常压塔底液面将升高,进料量减小,则常压塔底液面将降低。
但是,如果改变了初底泵出口的流量,会引起初馏塔底液位的变化,就需要调节原油泵出口流量,这是不可取的,所以,一般不会采取调节初馏塔底泵出口流量来调节常压塔底液位。
2.常底泵出口流量常底泵出口流量增大,则常压塔底液面将降低;常底泵出口流量减小,则常压塔底液面将升高。
但是在调节常底泵出口流量的同时,也要考虑减压系统的操作平稳性,常底泵出口流量波动,一定要提前做好减压炉的相关调节工作,如燃料油火嘴和燃料气火嘴阀门的开度、炉膛负压等,以保证减压塔进料的温度稳定,进而稳定整个减压塔的操作稳定。
3.汽化率常压塔的汽化率主要是指常顶气体、常顶汽油、常一线、常二线、常三线产品的产率总和。
常压塔底的汽化率升高,即为常顶产品和常压侧线产品的产率增加,则常底液面将下降;汽化率降低,则说明本应该汽化并从侧线馏出的组分没有馏出而是留存在塔底,使得常底液面将升高。
常压塔底汽化程度是常压塔底液位影响的很重要的因素。
(1)进料性质保持常压塔底温度不变,进科中轻组分的比例增大,则汽化率将升高。
反之,降低。
保持常压塔底温度、塔顶温度和压力不变,如果进料密度变小,进料中轻组分的比例增大,则常顶产品产量将会增加,汽化率将升高。
反之,降低。
常底进料密度变小,说明本应该在初馏塔汽化馏出的组分没有馏出,而是随初底原油一同进入到了常压塔,这些组分便会在常顶馏出,如果不考虑塔顶压力的影响因素,常底进料性质的变化一般不会影响常压侧线产品的产率。
(2)进料温度进料温度会促进油分的汽化,温度升高,则汽化率将升高;反之,则降低。
常压塔底进料温度与常压炉的加热程度和原油三段换热终温有关,从初馏塔底至常压炉进口这一段原油的换热系统称为原油三段换热系统,此系统换热器的热流为减压侧线、常渣及减渣,热流的流量、正副线的比例,都会对原油三段换热终温造成影响。
(3)塔顶压力塔顶压力也会影响油分的汽化效果,塔顶压力越低,各个组分的沸点也相应降低,则塔内进料整体汽化率将升高;反之,汽化率则降低。
(4)塔底注汽量常压塔底注汽,是为了降低常压塔内部油气分压,促进油分的汽化力度加强,增加侧线产品的产率。
如果加大注汽量,会降低塔顶的油气分压,降低组分的沸点,使汽化的油分增多,汽化率上升;反之,如果减小注汽量,会升高油气分压,则汽化的油分将减少,汽化率降低。
(十二)减压塔顶压力减压塔是在较低的温度和较低的压力下进行物料切割的,温度较低是为了避免发生烃类的裂解反应。
减压塔顶压力的影响因素有:抽真空蒸汽压力、塔底注汽量、侧线注汽量、减压炉出口温度、常压拔出率、塔顶温度、冷却器冷却力度、减底液位。
1.抽真空蒸汽压力抽真空蒸汽压力越高,在混合室侧面形成的真空度越高,形成的从减压塔顶到一级抽真空器混合室的压降就会越大,促使减压塔顶向一级抽真空器混合室的气流流速增大,减压塔顶的压力就会降低;反之,如果抽真空蒸汽压力降低,则减压塔顶的压力就会升高。
2.塔底注汽量殁侧线注汽量减压塔底注汽量和减压侧线注汽量增大,上升到塔顶的水蒸气就会越多,塔顶的气相负荷将会增大,塔顶的压力就会升高,另外减压塔内水蒸气的分压越大,则油气分压减小,会促使油相汽化率增大,汽化上升的气体总量增加。
反之,塔底和侧线的注汽量减小,塔顶的压力就会降低。
3.减压炉出口温度减压炉出口温度不易过高,以不发生裂解反应为界限,但是这个度很难把握。
如果减压炉出口温度过高,炉管内的常渣进入减压塔后,较轻组分汽化上升至塔顶,使塔顶压力升高;反之,减压炉出口温度降低,则组分汽化率将会下降,塔顶的负荷就会变小,塔顶压力降低。
4.常压拔出率常压拔出率指的是常顶气体、常顶汽油、常一线、常二线及常三线的产率总和。
常压拔出率越高,说明应该在常压汽化产出的产品就越多,常渣就会越重,进入减压塔后,组分的汽化率将会下降,塔顶的气相负荷变小,塔顶压力降低;反之,常压拔出率越低,进入减压塔内的轻组分越多,组分汽化率将会增大,塔顶气相负荷变大,塔顶压力升高。
5.塔顶温度塔顶温度越高,达到沸点而汽化的组分就越多,塔顶气相负荷变大,塔顶压力升高;反之,塔顶温度越低,本应汽化的轻组分没有汽化上升至塔顶,塔顶气相负荷变小,搭顶压力降低。
6.减底液位减底液位越高,淹没的格栅和填料越多,提馏的效果就越差,被淹没在液相中的轻组分就会增多,本应汽化上升至塔顶的轻组分就越少,塔顶气相负荷变小,塔顶压力降低;反之,减底液面越低,说明提馏段增多,提馏效果增大,汽化上升至塔顶的轻组分增多,塔顶气相负荷变大,塔顶压力升高。
虽然减压塔底液位是减顶压力的影响因素,但它的影响程度较小,除非减低液位淹没接近到减五线时,塔底液位的影响因素开始变得突出。
7.冷却器冷却力度前冷、中冷、后冷却器的冷却水温度越低,流量越大,冷却效果就越好,从塔顶引出的气相在冷却器内冷却为液相的比例增大,抽真空器的负荷就会变小,抽真空器的工作效能越大,使从减压塔顶到抽真空器的压降增大,气流流速增大,减压塔顶气相负荷减弱变快,塔顶压力降低;反之,前冷、中冷、后冷冷却器冷却力度变小,则会导致减压塔顶压力升高。
(十三)减压塔顶温度减压塔顶温度对于减顶油和减一线油馏程的影响很重要。
减顶油的馏程较宽,一般约为室温~360℃,闪点为室温,如果不影响柴油的闪点,可以作为轻柴油的调和组分输往油库;但如果闪点不允许,或者减顶油产率过大,则须打入原油泵进口进行回炼。
减一线油馏程约为300~370℃,常与常二线、常三线混合生产轻柴油馏分。
其他条件不变,减压塔顶温度过高,本不该汔化的组分汽化上升至塔顶,以减顶油馏分馏出,这样就减少了轻柴油的产率,减小装置效益。
减压塔顶温度一般控制在50~70℃的范围内,减顶温度各个炼油厂有不同,依据塔顶压力和侧线产品要求而定,但必须使水成气态。
减压塔顶温度的影响因素有:减压塔底进料温度,减压侧线抽出量,减一线回流、减一中段回流、减二中段回流温度及流量,减压塔顶压力。
1.减压塔底进料温度经过减压炉加热后来的进料,其提供的热源是减压塔唯一的热源,进料的温度直接影响到整个大塔的温度。
进料温度低,则大塔各个温位均会下降,进料温度高,则大塔各个温位均上升。
2.减压侧线抽出量侧线抽出量越大,则大塔损失的热量就会越多,抽出线上方的各个温位均会下降;反之,侧线抽出量小,则大塔损失的热量少,抽出线上方的各个温位均会上升。
3.减一线回流、减一中段回流、减二中段回流温度及流量减一线回流、减一中段回流、减二中段回流抽出与返塔温差越大,流量越大,则大塔损失的热量越多,其回流上方的各个温位均下降;反之,减一线回流、减一中段回流、减二中段回流抽出与返塔温差越小,抽出量越小,则大塔损失的热量越少,其回流上方的各个温位均上升。
4.减压塔顶压力减压塔顶压力对塔项温度的影响主要表现在:塔顶压力升高,一会降低塔内部上升气速;二使部分组分的沸点升高无法汽化,这样高温的重组分就无法到达塔顶而使塔顶得不到高温,因此就会造成塔顶温度的降低。
反之,如果塔顶压力降低,会增大塔内部上升的气速,增加了汽化率,高温的重组分就会汽化到达塔顶而使塔顶温度升高(热量的载体是上升的油气)。
(十四)减压塔底液位减压塔底液位会不同程度地影响减压塔内汽化率,如果减低液位超高至减五线附近时,将会破坏减压塔顶的真空,进而加大影响减压塔内的汽化率。
一般控制塔底液位高度为40%~60%,减压塔底液位的影响因素有:减压塔进料量、减底泵出口流量、汽化率(进料性质、进料温度、常压塔拔出率、侧线抽出量、塔底注汽量、塔顶压力、裂解率)1.减压塔进料量减压塔进料量主要由常底油泵出口流量调节,进料量增大,则减压塔底液面将升高,进料量减小,减压塔底液面将降低。
常底泵出口流量应根据常压塔底液位的变化而变化,其主要目的是维护常压系统的操作稳定,所以常压塔底泵的出口流量不可作为减压塔底液位的调节手段。
2.减底泵出口流量减底泵出口流量增大,则减压塔底液面将降低;减底泵出口流量减小,则减压塔底液面将升高。
减压塔底泵出口流量的大小除了对于原油一段、二段、兰段换热系统的换热终温有一定的影响外对本装置的平稳操作没有影响,因此一般把调节减压塔底泵出口流量作为调节减压塔底液位的首选手段。
但是,为了兼顾后续装置的平稳运行,在调节其流量时,要及时通知下游装置做好应对准备,尤其当下游装置没有原料罐和减渣直接进入下游装置的缓冲罐加工时,应提前通知其主控室,做好变量操作的前提准备。
3.汽化率减压塔底的汽化率升高,则减底液面将下降;汽化率降低,则减底液面将升高。
减压塔内的汽化率主要与减压塔底进料性质、进料温度、塔顶压力及塔底注汽量有关如果减压炉温度超高,会导致炉管内的常渣发生裂解反应而生成轻组分,进入减压塔的较轻组分的比例增大,汽化率上升,会导致减压塔底液位下降。
但是,在烃类发生裂解反应的同时,也会发生稠环芳烃的缩合反应,生产碳氢比更高的焦炭,聚集在高温部分,腐蚀设备而减小装置的生产周期,因此减压操作的重点是避免发生炉温的超高现象,如果为了提高减压拔出率,应尽可能地提高减压塔顶的真空度。
(十五)常压加热炉出口温度常压(加热)炉出口温度是常减压蒸馏装置的重要操作工艺参数,也是装置实现平稳操作较为重要的控制点,常压炉出口温度过高,将会导致常压塔搡作的紊乱,严重时会导致常压塔侧线产品质量不合格。
常压炉出口温度的影响因素有:常压炉进料温度(原油三段换热终温)、常压炉进料量、燃料气压力、燃料油压力、氧含量、烟气余热利用效率――冷风预热程度等。
1.常压炉进料温度保持其他工况条件不变,加热炉提供的热量一定,加热炉进料温度升高,则炉出口的温度就会上升;反之,加热炉进料温度降低,炉出口的温度就会下降。
常压炉进料温度取决于原油三段换热效果,即换热器热流正线的流量及温度、冷流的正线流量。
一般冷流原油不会走副线,以免因为流量减少而使正副线管线都结垢而造成堵塞。
所以在调节换热终温的时候,一般都是调节热流的副线流量。
2.常压炉进料量保持其他工况条件不变,加热炉提供的热量一定,进料量越少,则炉出口的温度就会越高;反之,进料量越多,则炉出日的温度就会越低。