常减压蒸馏装置的主要问题和应对措施
影响常减压蒸馏装置能耗的问题分析与节能对策
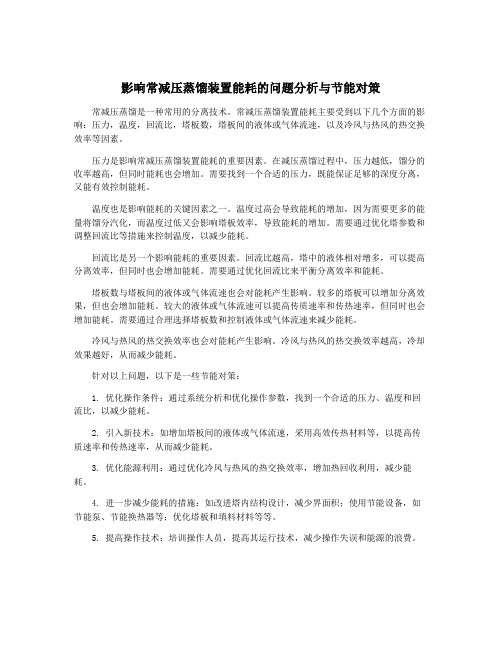
影响常减压蒸馏装置能耗的问题分析与节能对策常减压蒸馏是一种常用的分离技术。
常减压蒸馏装置能耗主要受到以下几个方面的影响:压力,温度,回流比,塔板数,塔板间的液体或气体流速,以及冷风与热风的热交换效率等因素。
压力是影响常减压蒸馏装置能耗的重要因素。
在减压蒸馏过程中,压力越低,馏分的收率越高,但同时能耗也会增加。
需要找到一个合适的压力,既能保证足够的深度分离,又能有效控制能耗。
温度也是影响能耗的关键因素之一。
温度过高会导致能耗的增加,因为需要更多的能量将馏分汽化,而温度过低又会影响塔板效率,导致能耗的增加。
需要通过优化塔参数和调整回流比等措施来控制温度,以减少能耗。
回流比是另一个影响能耗的重要因素。
回流比越高,塔中的液体相对增多,可以提高分离效率,但同时也会增加能耗。
需要通过优化回流比来平衡分离效率和能耗。
塔板数与塔板间的液体或气体流速也会对能耗产生影响。
较多的塔板可以增加分离效果,但也会增加能耗。
较大的液体或气体流速可以提高传质速率和传热速率,但同时也会增加能耗。
需要通过合理选择塔板数和控制液体或气体流速来减少能耗。
冷风与热风的热交换效率也会对能耗产生影响。
冷风与热风的热交换效率越高,冷却效果越好,从而减少能耗。
针对以上问题,以下是一些节能对策:1. 优化操作条件:通过系统分析和优化操作参数,找到一个合适的压力、温度和回流比,以减少能耗。
2. 引入新技术:如增加塔板间的液体或气体流速,采用高效传热材料等,以提高传质速率和传热速率,从而减少能耗。
3. 优化能源利用:通过优化冷风与热风的热交换效率,增加热回收利用,减少能耗。
4. 进一步减少能耗的措施:如改进塔内结构设计,减少界面积;使用节能设备,如节能泵、节能换热器等;优化塔板和填料材料等等。
5. 提高操作技术:培训操作人员,提高其运行技术,减少操作失误和能源的浪费。
常减压蒸馏装置能耗问题是一个综合性问题,需要从多个方面考虑,采取相应的节能对策来减少能耗。
影响常减压蒸馏装置能耗的问题分析与节能对策

影响常减压蒸馏装置能耗的问题分析与节能对策常减压蒸馏装置是一种常用的分离工艺装置,广泛应用于石油、化工、医药等行业。
常减压蒸馏装置在操作过程中存在能耗较高的问题,需要进行问题分析并采取节能对策来降低能耗。
影响常减压蒸馏装置能耗的主要因素是能源消耗和热量损失。
在装置的操作过程中,常减压蒸馏塔需要提供足够的热量以实现物料的汽化分离。
这需要大量的能量供应,而能量消耗的多少与设备设计、操作参数以及热和质量调控等因素密切相关。
常减压蒸馏装置在蒸汽产生和与外界环境的热量交换过程中存在热量损失,增加了能耗。
针对以上问题,可以采取以下节能对策:1. 设备改进:通过改进常减压蒸馏装置的结构和设备设计,减少能源消耗和热量损失。
可以采用增设换热器、改进冷凝器设计、提高传热效率等方法来优化装置的能源利用率。
2. 操作优化:合理选择操作参数,提高装置的工作效率。
优化进料控制、调整塔底温度、分馏液回收等操作,使得装置在保证分离效果的同时减少能耗。
3. 热能回收利用:在常减压蒸馏装置操作过程中,通过回收废热和余热来提供能量,减少能源消耗。
可以通过安装热交换器、采用余热回收技术等方式,将废热再利用,降低热量损失。
4. 技术优化:引入先进的分离技术和装置,如新型填料、膜分离技术等来替代传统分离方法,提高分离效率,减少能耗。
5. 节约水资源:在常减压蒸馏装置操作过程中,需要大量的水作为冷却剂、冷凝剂等。
合理利用水资源,减少水的消耗,也是降低能耗的一个重要方面。
6. 做好设备维护:定期对常减压蒸馏装置进行检修和维护,确保设备正常运行,减少能源消耗和热量损失。
常减压蒸馏装置能耗较高的问题可以通过改进设备、优化操作、回收利用能源等多种节能对策来解决。
这既可提高设备的经济效益,也符合可持续发展的要求,减少对环境的影响。
化工生产中常减压蒸馏装置火灾危险性及对策

化工生产中常减压蒸馏装置火灾危险性及对策 常减压蒸馏装置,由于在化工生产中处于显著的环节,物料易燃易爆,且工作环境是密闭的高温、高压,具有较大的火灾爆炸危险。
为此,要加强对其火灾危险性的研究,并采取可靠的消防安全措施。
一、工艺部分 1.常减压蒸馏装置主要有原油电脱盐、常减压蒸馏、直馏产品精制、四注防腐等部分组成。
一般主要生产汽油、煤油、柴油、腊油、减压渣油和少量的轻烃,其大部分产品为二次加工装置的原料。
2.主要设备(3.5Mt/d): 减压塔直径6.4米,高54m,体积约1100m3,设计压力0.005MPa,进料温度400℃。
塔体材质为复合钢板,壁厚16—20mm。
二、火灾危险性分析: 装置火灾危险性属甲类。
易发生灾害性事故的部位:加热炉、初馏塔、常压塔、减压塔、分馏塔。
1. 物料、产品 (1)原料油、腊油:自燃点低(240℃左右)。
(2)汽油、液态烃、干气:闪点低,易燃易爆。
(3)硫化氢(H2S):液态烃、干气中含有6-12%的H2S。
H2S无色,低浓度时有臭鸡蛋味气体,浓度高时反而无气味。
极易燃,自燃点260℃。
爆炸极限;4.0—46.0(V%)高毒类、具有强烈的神经毒性,对粘膜有强烈的刺激毒性。
侵入途径;吸入、经皮肤吸收。
接触高浓度(1000mg/m3)可发生电击死亡,毒性分级:巨级。
(4)加热炉烟道气中含有少量的co,为无色无味气体,吸入会引起中毒,表现为头痛、眩晕、恶心、耳鸣、眼花等症状。
(5)中压蒸汽:3.5MPa,温度440℃,泄漏后呈无色,易造成人员的烫伤。
2.工艺过程 (1)常减压蒸馏装置具有石油化工典型的高温、高压的特点,操作温度高达396℃。
(2)高温的油品和油气(350℃),设备密封部位发生泄漏有冒烟现象。
减压渣油部位发生泄漏,因油品的自燃发生火灾;柴油、汽油、富气等部位发生泄漏,油气与空气很容易形成混合性爆炸性气体。
事故发生后,容易扩大蔓延,且发展速度较快。
常减压蒸馏装置运行中存在的问题及对策

常减压蒸馏装置是炼油工业中常用的重要设备,它通过将原油加热至高温并将其分解成不同的组分来生产高价值的产品。
然而,在运行中常常会遇到各种问题,这些问题不仅会影响装置的正常运行,还可能对安全和环境造成严重影响。
对常减压蒸馏装置运行中存在的问题及对策进行全面评估至关重要。
1. 运行问题分析在常减压蒸馏装置的运行过程中,可能会出现以下一些常见的问题:1.温度控制不稳定:由于原油的成分复杂,不同组分的沸点不尽相同,因此需要严格控制温度才能确保分馏过程的有效进行。
然而,受原油成分变化、换热器堵塞等因素影响,温度控制不稳定是常见的问题。
2.泄漏和腐蚀:常减压蒸馏装置中存在大量高温、高压的气体和液体,并且原油中含有硫、氯等腐蚀性成分,这容易导致设备的泄漏和腐蚀问题。
3.运行过程中的噪音和振动:由于设备本身的结构和工况的特殊性,常减压蒸馏装置在运行中可能会有较大的噪音和振动,这既会影响生产效率,也会对设备的健康造成威胁。
2. 对策分析针对常减压蒸馏装置在运行中存在的问题,可以采取以下一些对策:1.完善温度控制系统:通过对温度控制系统进行全面检修和升级,使用先进的传感器和控制技术,可以更好地控制温度,确保常减压蒸馏装置的正常运行。
2.设备的定期检修和维护:定期检查和维护设备,保持设备的完好状态,及时更换老化部件,可以有效防止泄漏和腐蚀问题的发生。
3.完善减震和降噪措施:通过加装减震设备和使用吸声材料,可以有效减少设备运行过程中的噪音和振动,改善工作条件,提高生产效率。
3. 个人观点和理解在我看来,针对常减压蒸馏装置运行中存在的问题,应该注重预防为主,采取长期有效的措施来降低问题的发生率。
应该加强设备运行过程中的监测和管理,及时发现并处理潜在问题,确保设备的安全、稳定运行。
4. 总结与回顾在本文中,我们对常减压蒸馏装置运行中存在的问题及对策进行了全面评估。
在分析了运行问题和对策后,我们得出了对设备温度控制、设备定期检修和维护、以及设备的减震和降噪措施等方面的建议。
常减压蒸馏装置加热炉存在问题及改造措施
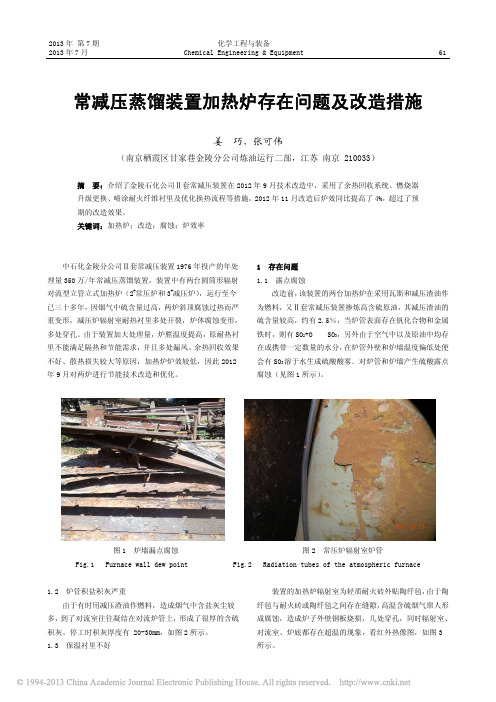
姜 巧:常减压蒸馏装置加热炉存在问题及改造措施 61 常减压蒸馏装置加热炉存在问题及改造措施姜 巧,张可伟(南京栖霞区甘家巷金陵分公司炼油运行二部,江苏 南京 210033)摘 要:介绍了金陵石化公司Ⅱ套常减压装置在2012年9月技术改造中,采用了余热回收系统、燃烧器升级更换、喷涂耐火纤维衬里及优化换热流程等措施,2012年11月改造后炉效同比提高了4%,超过了预期的改造效果。
关键词:加热炉;改造;腐蚀;炉效率中石化金陵分公司Ⅱ套常减压装置1976年投产的年处理量350万/年常减压蒸馏装置,装置中有两台圆筒形辐射对流型立管立式加热炉(2#常压炉和3#减压炉),运行至今已三十多年,因烟气中硫含量过高,两炉斜顶腐蚀过热而严重变形,减压炉辐射室耐热衬里多处开裂,炉体腐蚀变形,多处穿孔。
由于装置加大处理量,炉膛温度提高,原耐热衬里不能满足隔热和节能需求,并且多处漏风、余热回收效果不好、散热损失较大等原因,加热炉炉效较低,因此2012年9月对两炉进行节能技术改造和优化。
1 存在问题1.1 露点腐蚀改造前,该装置的两台加热炉在采用瓦斯和减压渣油作为燃料,又Ⅱ套常减压装置掺炼高含硫原油,其减压渣油的硫含量较高,约有2.5%,当炉管表面存在钒化合物和金属铁时,则有SO2+O SO3,另外由于空气中以及原油中均存在或携带一定数量的水分,在炉管外壁和炉墙温度偏低处便会有SO3溶于水生成硫酸酸雾.对炉管和炉墙产生硫酸露点腐蚀(见图1所示)。
图1 炉墙漏点腐蚀 图2 常压炉辐射室炉管Fig.1 Furnace wall dew point Fig.2 Radiation tubes of the atmospheric furnace1.2 炉管积盐积灰严重由于有时用减压渣油作燃料,造成烟气中含盐灰尘较多,到了对流室往往凝结在对流炉管上,形成了很厚的含硫积灰。
停工时积灰厚度有 20-30mm,如图2所示。
1.3 保温衬里不好装置的加热炉辐射室为轻质耐火砖外贴陶纤毡,由于陶纤毡与耐火砖或陶纤毡之间存在缝隙,高温含硫烟气窜人形成腐蚀,造成炉子外壁钢板烧损,几处穿孔,同时辐射室、对流室、炉底都存在超温的现象,看红外热像图,如图3所示。
常减压蒸馏装置生产运行的主要问题及对策

考论与综述清洗世界Cleaning World第36卷第12期2020年12月文章编号:1671-8909 (2020 ) 12-0108-002常减压蒸馏装置生产运行的主要问题及对策田海川(中海石油中捷石化有限公司,河北黄骅061101)摘要:随着我国能源工业的快速发展,现阶段常减压蒸馏装置在化石能源生产中的应用规模与技术水平都获得了长足发展。
在这个过程中,由于设备工艺等方面的问题,依然导致常减压蒸馏装置生产运行过程中产生了许多的阻力。
本文首先介绍了常减压蒸馏装置的定义与基本特征,其次探讨了常减压蒸馏装置生产运行过程中的常见问题,最后則结合具体的问题,提出了常减压蒸馏装置生产运行的优化策略,希望可以进一步解决生产发展问题,促进行业的稳定高速发展。
关键词:常减压蒸馏装置;生产过程;常见问题中图分类号:TE96 文献标识码:A〇引言随着环保标准的不断提升,汽油、柴油产品的技术 标准也在持续上调,这对于常减压蒸馏装置的科学应用 也提出了更高的要求。
为了最大限度的满足经济效益与 环保效益的双重要求,实现方案的优化与企业长远发展,就必须要做好常减压蒸馏装置的生产运行规划,确保设 备的可持续应用,现就常减压蒸馏装置的定义与基本特 征分析如下。
1常减压蒸馏装置概述常减压蒸馏装置主要包括常压蒸馏与减压蒸馏两种 设备,统称常减压蒸馏装置,该装置主要遵从物理原理 来完成物质分离的目标。
一般来说,原料油在蒸馏塔当中可以根据沸点的范 围来完成油品的调整,经过调和、添加等工艺后可以获 得最终的市场产品,所以常减压蒸馏装置是原油一次加 工必不可少的装置类型,其工序主要包括有脱盐脱水、常压蒸馏以及减压蒸馏三个主要环节。
由于该设备涉及到最初的生产步骤,所以无论是从 产品质量还是生产安全性方面都具有较高的要求。
另外,其生产的精度也会直接影响到后续的产品质量水平,决 定了企业的核心竞争力,对于整个行业的生产效益也会 起到巨大的影响。
常减压蒸馏装置加热炉运行分析及改进措施

文章 编 号 :1 6 7 1 — 0 7 1 1( 2 0 1 3 )0 3 — 0 0 5 4 ~ 0 2
改造 与更 新
常减压蒸馏装置加热炉 运行分析及 改进措 施
张 可 伟
( 中石化金陵分公
要 :介绍了 中石化金陵分公司 Ⅱ套常减压装 置加热炉在运行 中存在 的问题 ,采取改进措施后 ,取得
1 1 8
装置 的加 热炉辐射室 为轻质耐 火砖外贴 陶纤毡 ,由于 陶纤毡与 耐火砖或 陶纤 毡之间存在 缝隙 ,高 温含硫 烟气窜 入形成腐 蚀 ,造成 炉子外壁钢板 烧损 ,几 处穿孔 ,同时辐 射室 、对 流室 、炉底都存在超温的现象 。
另外 ,在炉子看火 门和防爆 门等处 ,因施工难度 较大 ,
一
、
存在 问题
个主要原因。
二 、 改 造措 施
1 . 露点腐蚀 改造前 ,该装 置 的两 台加热炉 采用 瓦斯 和减压 渣油作 为燃料 ,Ⅱ套常减压 装置掺炼 高含硫原 油 ,其减压 渣油 的 硫含量约2 . 5 % ,当炉管表面存在钒 化合物和金 属铁时 ,则
会发生 S O + O - -  ̄ S O , 的化学反 应 ,另 外 由于空气及原 油 中均
.
1 . 采用高效节能燃烧器 该 炉原 设计 燃料 为油 气混烧 ,并 燃 用 自产瓦 斯( 三顶
气) ,考 虑到油含硫量高 、燃烧不易控制 ,燃后灰分 烟尘增
加炉 管热 阻 ,降低 传热效果 。此 次改造 中 ,去掉 了进 油喷
嘴 ,同时 ,为 了使燃 料完全燃烧 ,常减压加 热炉 的燃 烧器
热炉 ( 2 常压炉和 3 减压 炉) ,运 行至今 已3 0 多年 ,因烟气 中 硫含量 过高 、两炉斜 顶腐蚀 、过热而严 重变形 ,减 压炉 辐
常减压蒸馏装置生产中的问题与解答
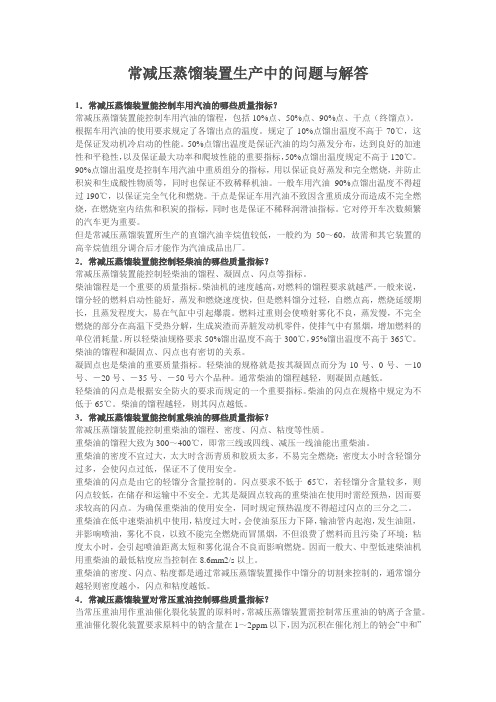
常减压蒸馏装置生产中的问题与解答1.常减压蒸馏装置能控制车用汽油的哪些质量指标?常减压蒸馏装置能控制车用汽油的馏程,包括10%点、50%点、90%点、干点(终馏点)。
根据车用汽油的使用要求规定了各馏出点的温度。
规定了10%点馏出温度不高于70℃,这是保证发动机冷启动的性能。
50%点馏出温度是保证汽油的均匀蒸发分布,达到良好的加速性和平稳性,以及保证最大功率和爬坡性能的重要指标,50%点馏出温度规定不高于120℃。
90%点馏出温度是控制车用汽油中重质组分的指标,用以保证良好蒸发和完全燃烧,并防止积炭和生成酸性物质等,同时也保证不致稀释机油。
一般车用汽油90%点馏出温度不得超过190℃,以保证完全气化和燃烧。
干点是保证车用汽油不致因含重质成分而造成不完全燃烧,在燃烧室内结焦和积炭的指标,同时也是保证不稀释润滑油指标。
它对停开车次数频繁的汽车更为重要。
但是常减压蒸馏装置所生产的直馏汽油辛烷值较低,一般约为50~60,故需和其它装置的高辛烷值组分调合后才能作为汽油成品出厂。
2.常减压蒸馏装置能控制轻柴油的哪些质量指标?常减压蒸馏装置能控制轻柴油的馏程、凝固点、闪点等指标。
柴油馏程是一个重要的质量指标。
柴油机的速度越高,对燃料的馏程要求就越严。
一般来说,馏分轻的燃料启动性能好,蒸发和燃烧速度快,但是燃料馏分过轻,自燃点高,燃烧延缓期长,且蒸发程度大,易在气缸中引起爆震。
燃料过重则会使喷射雾化不良,蒸发慢,不完全燃烧的部分在高温下受热分解,生成炭渣而弄脏发动机零件,使排气中有黑烟,增加燃料的单位消耗量。
所以轻柴油规格要求50%馏出温度不高于300℃,95%馏出温度不高于365℃。
柴油的馏程和凝固点、闪点也有密切的关系。
凝固点也是柴油的重要质量指标。
轻柴油的规格就是按其凝固点而分为10号、0号、-10号、-20号、-35号、-50号六个品种。
通常柴油的馏程越轻,则凝固点越低。
轻柴油的闪点是根据安全防火的要求而规定的一个重要指标。
- 1、下载文档前请自行甄别文档内容的完整性,平台不提供额外的编辑、内容补充、找答案等附加服务。
- 2、"仅部分预览"的文档,不可在线预览部分如存在完整性等问题,可反馈申请退款(可完整预览的文档不适用该条件!)。
- 3、如文档侵犯您的权益,请联系客服反馈,我们会尽快为您处理(人工客服工作时间:9:00-18:30)。
中国常减压蒸馏装置的主要问题和应对措施凌逸群中石化公司炼化部门,北京1000291 引言虽然在过去的几十年里,中国的直流催化裂化技术已取得了突飞猛进的成就,将来加氢处理,加氢裂化,加氢精制,催化重整技术也将随着环境规则的越来越严格,汽油、柴油燃料标准的越来越精确而经历飞速的发展。
尽管如此,常减压蒸馏装置作为原油加工的第一道工序有着非常大的处理能力,它影响着炼油厂的工艺流程,对经济效益也有着重要影响。
最近几年,随着实用技术和高效设备的发展及应用,关于常减压塔操作的问题引起了高度重视。
2 生产和操作上的主要问题到2001年底,中石化拥有的48套常减压蒸馏装置,其总设计处理量为139百万吨,包括一个8百万的装置,六个5百万吨的装置,14个3-4百万吨的装置和一些处理量少于3百万吨的装置。
47套蒸馏装置是在2001年开始运行的并以平均72.7%的负荷率加工了总共104.42百万吨的原油。
目前,在蒸馏装置的操作上存在四个主要问题。
2.1 总能量消耗量较高总能量消耗量是常减压蒸馏装置的一个重要的经济技术困难。
2001年中石化的蒸馏装置的总能量消耗量是11.85千克SOE/吨(包括荒废的减压蒸馏装置的能量消耗),变化范围在10.47到16.41千克/吨,与国外先进装置的能量消耗水平相比,中国总的能量消耗量更高些,这种现象的原因归咎于以下几个方面。
2.1.1 小型装置检修率低国外独立蒸馏装置的处理量一般在5百万吨/年到1千万吨/年,这些装置的维修率超过85%,在2001年,中石化的独立蒸馏装置的平均处理能力在290万吨/年,其平均负荷率为72.7%,导致了更高的原料和能量消耗。
2.1.2 加热炉燃料消耗量高常减压蒸馏装置中加热炉的燃料消耗量占蒸馏装置总燃料消耗量的70% 以上。
加热炉的燃料消耗量过高是造成常减压蒸馏装置总消耗量高的主要原因。
在生产和操作方面的两个主要问题会导致加热炉燃料消耗量高,蒸馏装置的总能量消耗量也高。
(1)加热炉热效率低以54个加热热效率的平均比重来说,中石化的24个常减压装置的热效率为88.1%,然而实际上,热效率才达到85.2%,比近期少了3个百分点,总体上说,国外加热炉的热效率超过90%,最多的可达到94%。
加热炉热效率低的主要原因是:●烟道气的温度过高导致烟道气温度过高的主要原因是:炉管上的灰沉积,盐沉积和污垢,空气的余热效率低,热回收系统的设计参数不恰当。
●烟道气中的氧含量高空气流速按需要调整的不精确和空气漏进加热炉都会导致烟道气中氧含量过高。
●辐射管和对流管表面灰沉积严重烟气吹扫的效率低下,执行缓慢是不可控制的,另一方面,加热炉燃料油质量恶化,杂质增加。
混合着直流催化裂化淤浆油的燃料油燃烧时,其中的硫和盐增加了灰沉积的趋势。
●露点温度低增加了腐蚀情况的发生过去几年里,随着原油逐年加重,炼厂中原油加工深度的逐渐加大,炼厂气中的硫含量和燃烧自己生产的燃料油的情况也逐渐增加,导致了烟道气中SO2和SO3的含量也逐渐增加。
据调查,烟道气中的最大硫含量已达到1266ppm,会使加热炉的低温部位发生低温腐蚀。
●已经破损的加热炉的不恰当的维修和加热炉的维护与处理加热炉炉体老化和炉体部分过热,加热炉的仪表失灵或出现故障,加热炉的维修系统缓慢都将使加热炉的热效率降低。
(2)原油热交换后的终温较低明确原油拔出率后,原油热交换后的终温越高,常压加热炉的热负荷就能减少并大幅度减少加热炉的燃料消耗。
通过优化换热流程,换热后终温由230-240℃上升到285-310℃。
常压加热炉燃料消耗效率能减少36%-48%。
因此,不可避免的,原油热交换终温对加热炉燃料消耗有重大影响,2001年,中石化的43套常减压蒸馏装置中只有总数35%的装置,它们的原油换热终温高于290℃。
原油换热终温受很多因素的影响,包括原油性质,拔出深度,常减压塔之间的热带出率,原油换热的电脑程序,原油换热类型和工作条件。
在中石化造成原油热交换终温下降的主要原因如下:●原油的换热程序不是最优的。
●原油热交换的效率低。
●常减压塔的热带出率不合理。
●原油性质和对产品的严格性发生了重大变化。
2.1.3 蒸馏装置的高能量消耗电力消耗占常减压蒸馏装置能量消耗的15% ,而且电力消耗在整个装置总能量消耗中排到了第二位。
到2001年,中石化的43套常减压装置中,有65%的装置的电力消耗少于7千瓦吨/吨,而且据统计:28%的装置的电力消耗高于8千瓦时/吨,而且28%的装置的物消耗高于8千瓦时/吨,在电力消耗上的不同是很明显的。
加工同种原油时,常压装置的负荷率是影响电力消耗的主要因素,装置负荷率越低,装置的电力消耗越高。
2.2 低分馏精确度和减压塔拔出率2.2.1 分馏精确度侧线分馏精确度在润滑油产品生产储备时是非常重要的。
足够的分离精确度能保证减压塔侧线的“窄沸程和浅颜色”,而且第一个馏分馏出体积为90% 时的温度与第二个馏分馏出5%体积时的温度不应该超过10℃。
目前,分馏精确度还未引起应当受到的重视,关于常压塔侧线的分离,常压塔塔顶和一侧线间的分馏精确度,第二和第三侧线之间的分馏精确度,常压塔拔出率都需受到重视。
当常压塔塔顶馏分用作重整原料时,塔顶馏分和第一侧线产品之间的分馏精确度高,具有相当可观的经济效益。
重整原料中重组分过多可能导致重整催化剂上积炭增加;减少催化剂活性,导致固定床一半再生重整装置的运转周期减短。
目前,高达40% 的常压塔塔顶馏分和第一侧线的蒸馏温度重叠超过10℃。
第二侧线产品可以直接作为已完成的柴油燃料的调和组分或作为柴油加氢处理的原料,当第三侧线产品用来作加氢裂化或直流催化裂化原料时,从柴油产率增加和减少生产费用角度看,常压塔二,三侧线之间的分馏精确度越高越有利。
目前,大多数蒸馏装置表明:常压塔第二侧线和第三侧线产品的恩氏蒸馏馏程的重叠大于15℃,而TBP的重叠部分超过25℃。
常压塔拔出率的增加有利于减压蒸馏塔拔出率的增加,常压蒸馏塔中渣油(重油)的收率是计算常压塔拔出率的重要指标。
2.2.2 减压蒸馏拔出率与国外蒸馏装置相比较,我国常减压蒸馏工艺的主要差距之处在于减压蒸馏拔出率低。
既然直流催化裂化是馏分油深加工的主要工艺流程装置,那么减压蒸馏深拔对提高直流催化裂化原料能起到很大作用。
在国外,加工轻原油,如布伦特原油,或含硫阿拉伯轻原油,切割温度可以达到706.6-593.3℃。
对于确定的原油来说,减压塔顶汽化段的温度和压力是影响减压塔拔出率的两个重要因素。
减压塔维护是减压塔拔出率低的主要原因。
气化段压力降低可以增加间压塔拔出率,在一定的汽化段温度下,操作压力从13.33kpa减小到2.0kpa。
阿拉伯重油的减压渣油产率能从37%到25%,减少了12%。
汽化部分压力的降低受到总压降(即汽化部分到塔顶)和减压塔塔顶的限制。
国外先进设备能实现汽化部分为1.33-2.0kpa。
中石化的调查数据表明:一般说来,减压蒸馏的装置汽化部分正常工作时的操作压力为7.64MPa。
减压拔出率随着汽化段温度的升高而升高。
尽管如此,气化段温度的升高受到加热炉中的焦化和高温原料会过度裂化两个条件的限制。
汽化段在固定压力下,生产燃料型的炼厂可以最大限度的提高汽化段的温度,因为在加热炉中不会发生焦化和过度裂化,在中石化的炼厂中汽化段的温度范围高温端约为390-392℃,低温端约为360-365℃。
2.3 电脱盐装置的非理想操作和控制电脱盐装置不仅仅是一种防腐措施,它以其成熟的脱盐,脱水,脱重金属技术成为一种重要的原油预处理过程,为下游装置提供质量良好的原料。
中石化的精炼部门在2002年2月对石化公司做了一个关于原油脱盐装置的调查。
实现44%电脱盐的原油含盐超过3mg/l,而实现17%电脱盐的原油含有超过5mg/l的盐。
造成电脱盐非理想操作条件的主要原因如下:破乳剂slste和处理水平不会有规律地随着原油slate的改变而作出回应,导致了反乳化作用和脱盐效果降低。
电脱盐装置的操作没有随着原油slate(的要求)和物料通过率的改变而改变。
与常减压蒸馏装置的扩大相比,电脱盐装置的能力没有扩大,导致原油在脱盐时的线速度变高,停留时间缩短。
处理能力变慢会使脱盐污水中盐含量的分析和检验不合格,在常减压蒸馏装置中原油的盐含量没有被作为一个重要的过程参数被仔细考虑。
2.4 加工含硫原油的适应性质与进口原油相比我国内陆原油较重些,含蜡,低硫,为加工内陆原油而设计的常减压蒸馏装置很难适应加工含硫原油。
最近几年,进口原油量随着国内蒸馏能力的增加而增加了。
同时,国内原油的硫含量也有明显的上升趋势(如胜利原油,华北原油),国内蒸馏装置的适应能力低也成为了一个有压迫性的议题。
2001年中石化常减压蒸馏装置出现了7次非计划停工,总共持续了36天,原因是:原油中硫含量增加导致设备发生了腐蚀。
3 采取的主要应对措施3.1 不遗余力地保存能量减少消耗炼厂中常减压蒸馏装置是主要消耗能量的装置之一,该装置消耗的能量占总能量消耗的13%-15%,在其他装置中能排到第二位。
因此,蒸馏装置的能量消耗减少将对炼厂的能量保护有重大影响,并减少原材料消耗。
3.1.1 减少燃料消耗(1)提高加热炉热效率提高加热炉热效率能有效地减少加热炉燃料消耗,为了解决加热炉操作中存在的问题,采用以下措施:有必要提高加热设备的现有情况以提高机械的可利用性。
注重修理和维护加热炉和辅助设备。
对烟道气热效率系统,吹扫(灰尘)系统,燃料烧嘴,炉体内表面,炉体的空气严密度和计算控制设备也应予以受到重视,应用些先进的高效的设备使加热炉的工作负荷要求。
提高燃烧的加热炉的操作水平是非常必要的,先进的操作控制参数(如烟道气温度和烟道气中的氧含量)和可靠的操作方法都应根据由中石化所编导的«管式加热炉操作处理系统»中的规定来确定。
因该采用通过DCS系统来控制加热炉以提高对燃烧着的加热炉的操作水平。
应该加强对燃烧的加热炉的职业操作,有必要建立一个针对加热炉燃料中的硫含量的每日检查和处理系统以避免因为燃料中杂质含量引起的烟道气的露点腐蚀。
有必要控制一个合理的烟道气出口的温度以扩大空气预热循环的操作。
(2)热交换存在下提高原油终温先进的过程设计,高效的热交换设备,和优化操作控制都能有效地提高原油热交换后的终温,并减少常压加热炉的能量消耗,过去几年里,由于微量分析软件的传播应用,原油热交换的设计水平已经有了很大的提高。
因为热流潜在的温度和流率将随着原油的重大改变和产品的调整而改变,所以应该在原油一次次试探性的减少流量时使用这种微量分析控制技术来检测产品质量,以便调整换热程序,从而达到提高原油热交换终温的目的。
应该使用高效换热器以提高热传递效率。
目前,许多新颖的换热器,如螺旋式换热器,转动流换热器,双弓型盘式热交换器,波纹状的管式热交换器都出现了u nitermittently。