余热回收系统设计方案
焦化热管余热回收系统的结构设计

焦化热管余热回收系统的结构设计一、系统组成及工作原理焦化热管余热回收系统主要由余热管、换热器、热交换介质以及管道系统等组成。
其工作原理主要是利用焦化炉高温废气中的热能,通过余热管将废气中的热量进行直接传导或对换,传递到换热器中,最终转移给待加热介质,提高介质温度,实现能量的回收和利用。
二、系统结构设计1. 余热管设计余热管是焦化热管余热回收系统中的核心组件,其设计质量直接关系到系统的运行效率和安全性。
在余热管的设计中,需要考虑以下几个方面的因素:(1)材料选取:余热管应选用能够耐高温、耐腐蚀的优质材料,如不锈钢、合金钢等。
(2)管壁厚度:余热管壁厚度需满足系统工作压力和温度的要求,通常应采用均匀壁厚的管材。
(3)管道连接:余热管与系统中的其他部件进行连接时,需要采用焊接、法兰连接等方式,确保连接处的密封性和稳固性。
2. 换热器设计换热器是焦化热管余热回收系统中用于接收和传递余热的设备,其设计应考虑以下几个方面的因素:(1)结构形式:换热器可以采用板式换热器、管式换热器等不同结构形式,根据实际工况和换热要求进行选择。
(2)换热面积:根据需要回收的余热量和介质的流量,合理确定换热器的换热面积,以确保换热效果。
(3)材料选取:换热器的材料应具有良好的导热性和耐腐蚀性,能够适应高温高压环境。
3. 热交换介质选择在焦化热管余热回收系统中,热交换介质起到了传递热能的作用,通常可选择水蒸汽、热水或者其他工业生产过程中需要加热的介质作为热交换介质。
在选择介质时需要考虑介质的流动性、热容量、热传导性等因素,以确保系统的稳定运行和换热效果。
三、系统运行控制为了保证焦化热管余热回收系统的安全、稳定、高效运行,需要对系统进行合理的运行控制。
在系统运行中,可以采取以下措施:1. 温度控制:通过温度传感器对余热管、换热器等关键部件进行实时监测,根据监测结果调整介质的流动速度和温度,以确保系统的稳定运行。
2. 压力控制:对系统中的压力进行实时监测,合理设计和选取压力表、安全阀等安全装置,确保介质在安全的压力范围内运行。
空压机余热回收工程背景原理以及设计方案
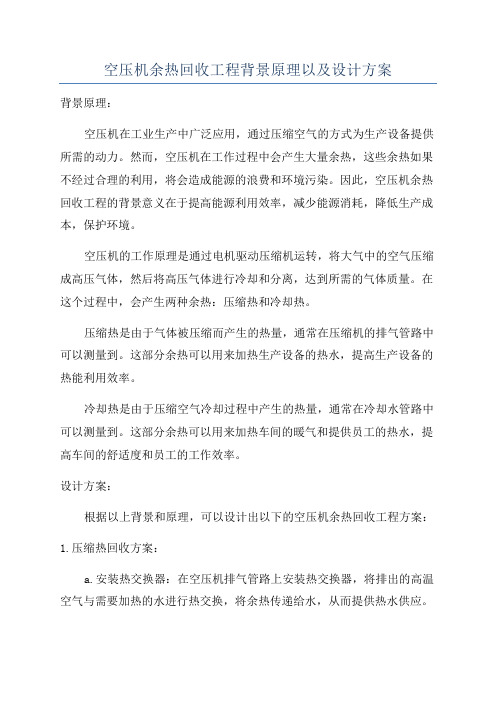
空压机余热回收工程背景原理以及设计方案背景原理:空压机在工业生产中广泛应用,通过压缩空气的方式为生产设备提供所需的动力。
然而,空压机在工作过程中会产生大量余热,这些余热如果不经过合理的利用,将会造成能源的浪费和环境污染。
因此,空压机余热回收工程的背景意义在于提高能源利用效率,减少能源消耗,降低生产成本,保护环境。
空压机的工作原理是通过电机驱动压缩机运转,将大气中的空气压缩成高压气体,然后将高压气体进行冷却和分离,达到所需的气体质量。
在这个过程中,会产生两种余热:压缩热和冷却热。
压缩热是由于气体被压缩而产生的热量,通常在压缩机的排气管路中可以测量到。
这部分余热可以用来加热生产设备的热水,提高生产设备的热能利用效率。
冷却热是由于压缩空气冷却过程中产生的热量,通常在冷却水管路中可以测量到。
这部分余热可以用来加热车间的暖气和提供员工的热水,提高车间的舒适度和员工的工作效率。
设计方案:根据以上背景和原理,可以设计出以下的空压机余热回收工程方案:1.压缩热回收方案:a.安装热交换器:在空压机排气管路上安装热交换器,将排出的高温空气与需要加热的水进行热交换,将余热传递给水,从而提供热水供应。
b.温度控制系统:根据生产设备对热水温度的要求,安装温度控制系统来控制热交换器的工作,在达到所需温度后停止工作,以避免能源浪费。
2.冷却热回收方案:a.安装冷却系统:在冷却水管路上安装热交换器,将冷却水与需要加热的水进行热交换,将冷却水的余热传递给需要热水的系统,提供暖气和热水供应。
b.温度控制系统:根据车间的温度要求,安装温度控制系统来控制热交换器的工作,在达到所需温度后停止工作,以避免能源浪费。
3.综合管理系统:a.监测系统:安装温度、压力和流量传感器来监测热交换器的工作状态和能源利用效率,实时监控能源消耗和节能效果。
b.控制系统:根据监测系统的反馈信息,采用自动控制或人工干预的方式调整热交换器的工作状态,以达到最佳的能源利用效果。
镀锌厂镀锌锅余热回收系统方案设计
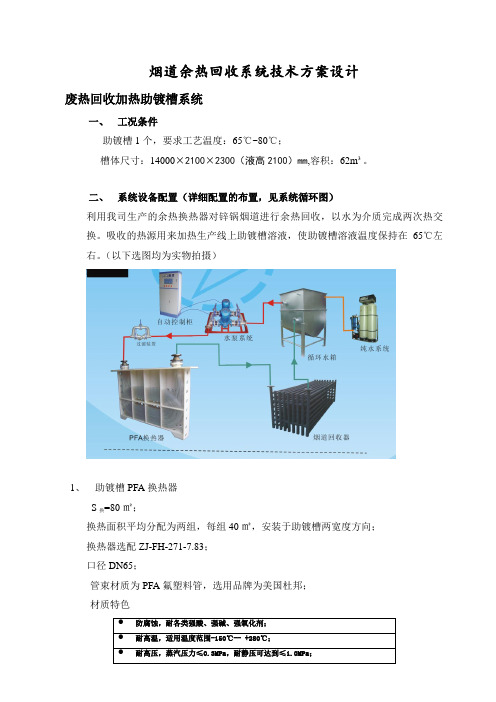
烟道余热回收系统技术方案设计废热回收加热助镀槽系统一、工况条件助镀槽1个,要求工艺温度:65℃~80℃;槽体尺寸:14000×2100×2300(液高2100)mm,容积:62m³。
二、系统设备配置(详细配置的布置,见系统循环图)利用我司生产的余热换热器对锌锅烟道进行余热回收,以水为介质完成两次热交换。
吸收的热源用来加热生产线上助镀槽溶液,使助镀槽溶液温度保持在65℃左右。
(以下选图均为实物拍摄)1、助镀槽PFA换热器S换=80㎡;换热面积平均分配为两组,每组40㎡,安装于助镀槽两宽度方向;换热器选配ZJ-FH-271-7.83;口径DN65;管束材质为PFA氟塑料管,选用品牌为美国杜邦;材质特色●防腐蚀,耐各类强酸、强碱、强氧化剂;●耐高温,适用温度范围-150℃-- +280℃;●耐高压,蒸汽压力≤0.3MPa,耐静压可达到≤1.0MPa;管道与法兰焊接方法为热熔;保护框架为20mmPP板(大板),支撑框架为15mmPP板(大板)。
备选方案:将PFA管束换成FEP材质,换热器换热面积增加至96㎡,口径DN65;选型:ZJ-FH-271-9.4;耐温:-150℃~200℃;同等工况下,PFA的柔性为FEP的10倍以上。
2.烟道余热回收换热器管材:20#无缝钢管上加红外新型纳米高温节能防腐涂料,吸热能为普通余热换热器所吸热量的140%;余热换热器选配:S余换=56㎡;烟道尺寸:待确定;烟道余热回收器尺寸:3300 x 1100 x1300,12排10根,具体尺寸可根据烟道尺寸调节。
3.水泵系统水泵系统包括热水泵2台,变频水泵1台,阀门6个,压力表6个;靠近烟道处热水泵2台为一个系统,采用一备一用方式运转,型号:IRG-65-160。
水泵为自动控制,当一台水泵运行4-5小时后,另一台水泵开始运行。
如一台水泵遇故障,另一台水泵将自动运行,并进行故障报警。
控制柜内装有24小时微电脑调节器,可进行手动设定。
焦化热管余热回收系统的结构设计

焦化热管余热回收系统的结构设计一、系统概述焦化热管余热回收系统是利用焦化产生的高温废热,通过热管进行传热,将废热再利用的一种节能环保技术。
该系统主要包括热源、传热管路、热交换器、热储罐、回收利用设备等部分。
通过该系统的构建和优化设计,可以实现对焦化废热的高效回收和再利用,提高能源利用效率,减少环境污染。
二、结构设计1. 热源部分热源部分主要包括焦炉的废热产生装置,包括热炉炉排、热风炉、燃气炉等。
这些设备产生的高温烟气和热风是焦化过程中的主要废热来源,也是余热回收系统的主要热源。
在设计时需要考虑热源的热功率、热风流量、烟气温度等参数,以便确定后续传热和回收利用设备的规格和容量。
2. 传热管路传热管路是焦化热管余热回收系统的重要组成部分,通过传热管路将热源产生的高温废热传递到热交换器和热储罐等设备中。
传热管路的设计需要考虑管道材质、管道直径、管道长度、传热介质等参数,以确保高效传热,并尽量减少热损失。
3. 热交换器热交换器是实现焦化废热回收的核心设备之一,主要通过传热管路将热量传递给回收利用设备。
在设计时需要考虑热交换器的传热面积、传热效率、结构材质、耐高温性能等参数,以确保其能够承受高温高压环境下的工作条件,并实现高效传热。
4. 热储罐热储罐是用于存储焦化废热的设备,通过储存高温热能来保证系统的稳定运行,并在需要时释放热能供回收利用设备使用。
在设计时需要考虑热储罐的容量、保温性能、耐高温性能等参数,以确保其能够稳定存储高温热能。
5. 回收利用设备回收利用设备是焦化废热回收系统中的最终载体,主要包括汽轮发电机组、热能锅炉、供热设备等。
这些设备通过接收回收的高温热能,并将其转化为电能或热能供工业生产或生活使用。
在设计时需要考虑回收利用设备的匹配性、效率和安全性等参数,以确保其能够稳定运行,并实现对焦化废热的充分利用。
三、总结焦化热管余热回收系统的结构设计是一个综合考虑热源、传热、存储和利用的过程,需要充分考虑系统的整体性和协调性,以确保系统能够稳定、高效地实现对废热的回收和再利用。
《2024年北京某燃气热电厂余热回收系统设计》范文

《北京某燃气热电厂余热回收系统设计》篇一一、引言随着能源需求的不断增长和环境保护意识的日益加强,余热回收技术已成为提高能源利用效率、减少环境污染的重要手段。
北京某燃气热电厂作为城市能源供应的重要组成部分,其余热回收系统的设计对于提高能源利用效率、降低环境污染具有重要意义。
本文将详细介绍北京某燃气热电厂余热回收系统的设计思路、方法及实施措施。
二、项目背景与目标北京某燃气热电厂位于城市核心区域,承担着城市供暖及供电的重要任务。
为了提高能源利用效率,减少环境污染,本设计旨在将燃气热电厂排放的余热进行有效回收,实现能源的再利用。
项目目标包括:提高能源利用效率,降低环境污染,实现经济效益与社会效益的双赢。
三、余热回收系统设计原则1. 高效性:系统设计应充分考虑余热的回收效率,确保回收的热量能够满足供暖、供电等需求。
2. 安全性:系统设计应保证设备运行的安全可靠性,降低事故风险。
3. 环保性:系统设计应符合国家环保要求,减少对环境的影响。
4. 经济性:系统设计应在保证性能的前提下,尽可能降低投资成本和运行成本。
四、余热回收系统设计方案1. 系统组成余热回收系统主要由余热收集装置、余热回收装置、换热器、储热装置等组成。
其中,余热收集装置用于收集燃气热电厂排放的余热;余热回收装置通过换热器将余热转化为可利用的热量;储热装置用于储存回收的热量,以满足供暖、供电等需求。
2. 工作原理余热收集装置将燃气热电厂排放的余热引入余热回收装置,通过换热器将余热传递给工作介质,使工作介质温度升高。
然后,工作介质将热量传递给储热装置中的储热介质,实现热量的储存和利用。
在需要供暖或供电时,储热装置中的储热介质将热量释放出来,满足需求。
3. 技术参数(1)余热收集装置:收集效率≥90%,耐高温、耐腐蚀。
(2)余热回收装置:换热效率≥95%,运行稳定可靠。
(3)换热器:传热效率高,结构紧凑,易于维护。
(4)储热装置:储热量大,储存时间长,安全可靠。
瓦斯发电机组余热回收系统方案

富维江森自控汽车饰件系统有限公司搪塑炉烟气余热回收项目方For personal use only in study and research; not for commercial use案报价书提案单位:成都凯峰环保科技有限公司联系人:苏超峰联系方式:传真:日期:2015年11月18日一、概述节能与环保是当代全球关注的重要课题,我国是最大的发展中国家,按人口平均计算也是能源最匮乏的国家,节约能源并为后代保护资源,是我们每一个人的责任。
余热回收利用对企业来说最直接的收益就是节省燃料费用,提高经济效益,增强企业竞争力。
对社会来说减少有害气体的排放,保护环境。
可谓节能环保一举两得。
余热是指能利用而未被利用的热能。
由于我国工业装备落后,能源利用率低。
如化工、石油、建材、轻纺、冶金、动力、食品、造纸、电子电器等行业,生产中大量的可利用热能直接排空,既浪费能源又污染环境。
将浪费的热能回收利用,提高能源利用率,降低生产成本,减少二氧化碳以及各种有害气体的排放,具有经济和社会双重效益。
二、设计方案1、热源基本情况炉型:瓦斯发电机组烟气温度:500℃-550℃烟气流量:5000Nm3/h2、余热回收效率计算a、烟气平均密度:0.85kg/m³,比热:0.24kcal/kgb、总热负荷=流量×密度×比热×温差=5000×0.85×0.24 ×(500-170)=336600kcal/h =390KW综上所诉贵企瓦斯发电机组可回收热热值336600 kcal/h,回收热量能充分满足办公大楼供暖所需热量。
3、工艺流程由于瓦斯发电机组所排放的烟气热量足够大,在瓦斯发电机组原排烟管处布置一台内外翅片管式余热回收机,将瓦斯发电机组所排放的≥500℃烟气温度降至170-200 ℃左右进行排放,利用瓦斯发电机组(内燃机组)烟气的热量加热纯水将其升温至80-90 ℃。
余热回收系统设计方案
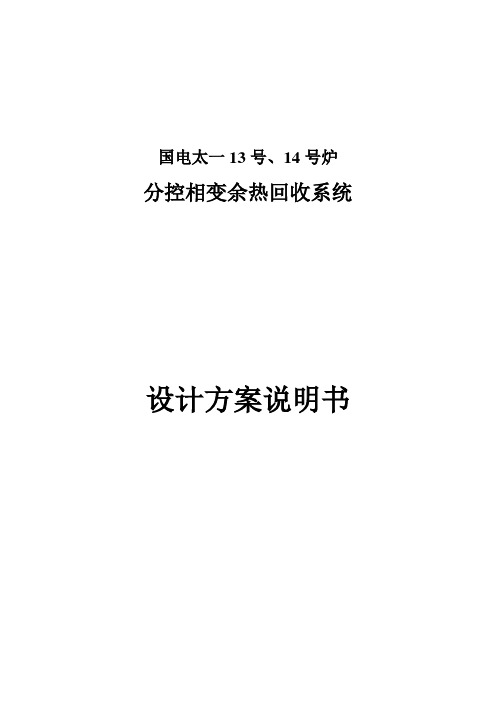
国电太一13号、14号炉分控相变余热回收系统设计方案说明书太一13、14号炉余热回收系统设计方案热力系统设计方案本设计严格遵照投标文件的技术方案和技术要求,相关内容见投标文件。
本说明仅为细化图纸的说明,作为投标文件的补充。
本系统图是在投标文件的基础上进行了细化,增加了详细的管道、设备布置和规格。
烟道热源换热器分为4组布置在除尘器前的水平烟道上,重心在风机房最靠近除尘器的支撑横梁上,设安装平台,并进行横梁加固(由脱硝装置改造单位配套完成)。
膨胀节设在靠近除尘器一侧,换热器采用滑动支撑。
二次风道冷源换热器布置在送风机出口的水平风道,一次风道冷源换热器布置在一次风机出口的弯道前倾斜布置。
气流调节分为两个单元,即左侧的两个烟道换热器的出口蒸汽母管汇合后由一个调节阀控制,相应右侧两个烟道换热器的出口蒸汽母管汇合后由另一个调节阀控制,部分母管制简化了系统,也增加了系统的稳定。
水位的调节由四个水位计分别控制四个供水调节阀,左侧的两个水位计分别指示左侧两个烟道换热器的上部单元和下部单元,右侧的两个水位计分别指示右侧两个烟道换热器的上部单元和下部单元。
每个换热单元都独立设有隔离阀。
为防止冬季设备停运时管路冻裂,每个换热单元都独立设有放水阀。
烟道换热器进出口的阀门分左右侧,集中布置在风机房顶,汇总到母管后由风机房顶进入风机房二次风道换热器侧。
水箱和汽液换热器等设备布置在零米风道换热器之间,水泵布置在水箱附近-1.0米的泵坑。
为了夏季进一步降低排烟温度,本设计补充了凝结水加热器作为备用设备,凝结水加热器的耗汽量为余热回收系统最大负荷的35%。
本设计的排空管路由三个电磁阀控制,便于手动和自动操作。
本设计的补充氮气系统是为了在冷源换热器负压较大时,在不改变相变分压的前提下,增加系统全压,避免空气漏入系统内。
另外,本次工程还将原风道内的暖风器拆除,以减小系统的阻力,降低风机的电耗。
本余热回收系统可替代原暖风器系统,但供汽和回水仍用原系统管路。
余热回收设计方案

恒昌焦化焦炉烟气余热回收项目设计方案唐山德业环保设备有限公司二〇一二年三月一、焦化工艺概述:备煤车间送来的配合煤装入煤塔,装煤车按作业计划从煤塔取煤,经计量后装入炭化室内。
煤料在炭化室内经过一个结焦周期的高温干馏制成焦炭并产生荒煤气。
炭化室内的焦炭成熟后,用推焦车推出,经拦焦车导入熄焦车内,并由电机车牵引熄焦车到熄焦塔内进行喷水熄焦。
熄焦后的焦炭卸至凉焦台上,冷却一定时间后送往筛焦工段,经筛分按级别贮存待运。
煤在炭化室干馏过程中产生的荒煤气汇集到炭化室顶部空间,经过上升管、桥管进入集气管。
约800℃左右的荒煤气在桥管内被氨水喷洒冷却至84℃左右。
荒煤气中的焦油等同时被冷凝下来。
煤气和冷凝下来的焦油等同氨水一起经过吸煤气管送入煤气净化车间。
焦炉加热用的焦炉煤气,由外部管道架空引入。
焦炉煤气经预热后送到焦炉地下室,通过下喷管把煤气送入燃烧室立火道底部与由废气交换开闭器进入的空气汇合燃烧。
燃烧后的废气经过立火道顶部跨越孔进入下降气流的立火道,再经蓄热室,又格子赚把废气的部分显热回收后,经过小烟道、废气交换开闭器、分烟道、总烟道、烟囱排入大气。
对于其中经总烟道进入烟囱热烟气的仍有较大的余热回收价值。
二、余热回收工艺流程图技术方案如下:该系统由热管蒸气发生器、软水预热器、汽包、上升管、下降管、外连管路和控制仪表等组成,并且互相独立。
主要技术特点:1、地下烟道开孔技术:如何实现地下主烟道在焦炉正常行产情况下在线开孔,是本项目成功实施的第一关键。
我公司根据多次地下烟道的开孔经验,成功总结出一套行之有效施工方案。
地下烟道路截面尺寸如上图所示。
开孔及布筋图支模示意图支撑系统图2、防止地下烟道、余热回收设备、引风机间环流形成的技术。
由于地下烟道翻板阀与地下烟道周围的150-200的环隙,在风机工作的过程中,风机出口压头大于风机进口压头,且进口压头低于烟囱吸力,因此在设备烟气进口处与风机出口处间地下烟道有环流存在。
经验告诉我们在这种情况下,增大风机功率是没有作用的,因为随风机功率的增加,其环量也在增加,其结局是或影响焦炉总烟道负压度从而影响焦炉的正常生产,或影响余热回收的正常产汽量,这也是一般设备制造厂家在焦炉余热回收上失败的原因之一。
- 1、下载文档前请自行甄别文档内容的完整性,平台不提供额外的编辑、内容补充、找答案等附加服务。
- 2、"仅部分预览"的文档,不可在线预览部分如存在完整性等问题,可反馈申请退款(可完整预览的文档不适用该条件!)。
- 3、如文档侵犯您的权益,请联系客服反馈,我们会尽快为您处理(人工客服工作时间:9:00-18:30)。
国电太一13 号、14号炉分控相变余热回收系统
设计方案说明书
太一13、14 号炉余热回收系统设计方案热力系统设计方案本设计严格遵照投标文件的技术方案和技术要求,相关内容见投标文件。
本说明仅为细化图纸的说明,作为投标文件的补充。
本系统图是在投标文件的基础上进行了细化,增加了详细的管道、设备布置和规格。
烟道热源换热器分为4 组布置在除尘器前的水平烟道上,重心在风机房最靠近除尘器的支撑横梁上,设安装平台,并进行横梁加固(由脱硝装置改造单位配套完成)。
膨胀节设在靠近除尘器一侧,换热器采用滑动支撑。
二次风道冷源换热器布置在送风机出口的水平风道,一次风道冷源换热器布置在一次风机出口的弯道前倾斜布置。
气流调节分为两个单元,即左侧的两个烟道换热器的出口蒸汽母管汇合后由一个调节阀控制,相应右侧两个烟道换热器的出口蒸汽母管汇合后由另一个调节阀控制,部分母管制简化了系统,也增加了系统的稳定。
水位的调节由四个水位计分别控制四个供水调节阀,左侧的两个水位计分别指示左侧两个烟道换热器的上部单元和下部单元,右侧的两个水位计分别指示右侧两个烟道换热器的上部单元和下部单元。
每个换热单元都独立设有隔离阀。
为防止冬季设备停运时管路冻裂,每个换热单元都独立设有放水阀。
烟道换热器进出口的阀门分左右侧,集中布置在风机房顶,汇总到母管后由风机房顶进入风机房二次风道换热器侧。
水箱和汽液换热器等设备布置在零米风道换热器之间,水泵布置在水箱附近-1.0 米的泵坑。
为了夏季进一步降低排烟温度,本设计补充了凝结水加热器作为备用设备,凝结水加热器的耗汽量为余热回收系统最大负荷的35%。
本设计的排空管路由三个电磁阀控制,便于手动和自动操作。
本设计的补充氮气系统是为了在冷源换热器负压较大时,在不改变相变分压的前提下,增加系统全压,避免空气漏入系统内。
另外,本次工程还将原风道内的暖风器拆除,以减小系统的阻力,降低风机的电耗。
本余热回收系统可替代原暖风器系统,但供汽和回水仍用原系统管路。
锅炉烟气余热回收系统图
控制系统设计方案
1、汽流及相关控制
在气流调节阀控制器中设定压力设定值,通过压力传感器测量该吸热装置内的蒸汽压力(初始设定值为表压0.053MPa);由该气流调节阀控制器将由压力传感器测量的蒸汽压力与压力设定值进行比较,并且利用气流调节阀控制器对气流调节阀的开度调节。
在气流调节阀控制器中设定温度设定值(初始设定值为112℃),通过温度传感器测量该吸热装置内的蒸发液和饱和蒸汽温度;利用气流调节阀控制器将
气流调节阀的开度调节为吸热装置内的蒸汽温度与气流调节阀控制器中的温度
设定值一致时的开度,以修正压力调节误差。
热源换热器壁温(初始设定值为115℃)(壁温测点去掉高、低极值各1~2 个后的平均值。
测量值与平均值比较的偏差大于正负5~10%时即为极值)也可作为控制对象,可切换投入。
压力设定值和温度设定值根据煤种不同而不同,最终确保烟气换热器的壁温高于烟气酸露点。
通过比较电厂脱硫塔前烟气SO2 含量与设定值,其偏差用于修正烟气酸露点,从而修正壁温的设定值。
蒸发液和饱和蒸汽温度的设定值大于烟气酸露点3~5℃。
(可采用蒸汽压力、温度和换热器壁温分别作为控制对象,切换投入。
同时以温度修正压力的控制方案作为备用)
2、液流及相关控制在液流调节阀控制器中设定液位设定值(初始设定值为2000mm),通过液位传感器测量吸热装置内的液位;由液流调节阀控制器将由液位传感器测量的液位与液位设定值进行比较,并利用液流调节阀控制器将液流调节阀的开度调节为吸热装置内的液位与液流调节阀控制器中的液位设定值
一致时的开度。
在液流调节阀控制器中设定低一值的壁温设定值(初始设定值为113℃)或蒸发液温度值,并且该壁温设定值是液流调节阀开启的限制阀值;当温度传感器所测得的壁温值(下壁温测点去掉高低极值后平均值)低于该温度设定值时,发出报警信号;当测得的温度值进一步降低到低二值时(初始设定值为
110℃),
降低变频器输出为额定值的50%,解除水泵联锁启动,同时系统的放液阀打开,将热源换热器内存水回收排入系统的储水箱(储水箱水位高时,存水将直接排出系统,进入凝汽器)。
放液阀可根据情况手动打开。
两台循环水泵互为备用,根据母管压力传感器控制备用泵的启停,当母管测量的压力低于设定值0.04MPa 时备用泵启动。
循环水泵正常运行采用变频控制,根据母管压力的设定值调节变频器的输出,母管压力的设定值为
0.28~0.45MPa (初设值为表压0.28MPa)。
当储水箱的水位低于设定值(液位高度150mm),则循环水泵被自动禁止运行。
当水泵出口压力低于设定值0.02MPa时发出报警信号。
循环水泵电机和变频器除有远程自动和手动控制外,还设有就地控制柜,包括水泵手动启停按钮和运行状态指示。
就地控制柜有远程和就地切换开关。
3、储水箱的水位控制储水箱的水位由暖风器回水控制阀来控制,回水控制阀设有手动旁路阀以备用。
暖风器回水控制阀为连续调节阀,其开度根据储水箱的水位设定值(初始设定值为400mm)控制。
当储水箱水位高于最高值(初始设定值为450mm)和低于最低值(初始设定值为200mm)时,均发出报警信号。
4、外接汽流的控制汽液换热器的外接汽源控温调节阀由相应调节阀控制器控制开度,该调节阀控制器根据汽液换热器出液温度传感器测量信号实施控制;
当汽液换热器出液温度传感器测量的温度与该调节阀控制器的设定值(初始设定值为108℃)发生偏差,则该调节阀控制器根据该偏差进行运算,计算出相应可纠正该运行偏差的调节阀开度值,作为控制值输出,调节该调节阀的开度,使测量值与设定值保持一致。
向汽液换热器后蒸汽总管供汽的外接汽源供汽调节阀由相应外接汽源供汽阀控制器控制开度,该外接汽源供汽阀控制器根据手动给定值和汽液换热器后蒸汽总管压力(冷源端蒸汽压力)给定值实施控制;当汽液换热器后蒸汽总管压力传感器测量信号值大于给定值(初设值为表压0.06MPa)时,该阀门关小,直至关闭。
当汽液换热器后蒸汽总管表压压力高于0.08MPa时发出报警信号。
调压阀是为了控制阀后表压压力不超过0.1MPa,调压阀预紧力设置需在系统投运
时调试。
5、凝结水换热器的凝结水控制
根据凝结水换热器出口的凝结水水温与设定值(初始设定值为95℃)的偏
差控制凝结水入口调节阀的开度。
当换热器的进汽量减小时,凝结水入口调节阀的开度也会随之关小,这样可始终控制返回7 号低加的凝结水温达到设计值,保持余热回收系统处于最佳经济运行状态。
换热器进汽量根据排烟温度的变化手动控制,在夏季为降低排烟温度,进汽阀一般处于全开位置。
冬季可将凝结水侧出入口手动门关闭,以使得蒸汽全部用于加热锅炉送风,提高余热回收的经济性。
凝结水管路需设流量计以便于热平衡计算。
6、排气控制和氮气补充控制
系统的排气由3 个排气电磁阀控制。
当汽流调节阀后的系统处于正压运行并达到排气压力时,可手动打开排气电磁阀将系统内不凝气体排除。
当储水箱正压超过限值时(初始设定值为表压0.08MPa),排气电磁阀将自动打开以泄压。
系统还设有自动水封装置,当系统内压力超过水封高度时,自动将系统内不凝气体排除以降压。
在汽流调节阀后的系统长时间处于负压状态运行时,也可通过开启辅助的外接汽源以增加系统的压力来排气。
排气后若系统处于负压运行可手动开启自动补气装置,将氮气等惰性气体充入系统,以维持系统处于微负压或微正压,避免系统由渗漏点吸入空气。
系统停电状态下,汽流和液流调节阀等阀门处于打开状态,以便于疏水和排气。
7、测点清单控制系统采用就地控制柜程控,全部测量信号都接入控制
柜。
接入控制柜的显示监督信号包括:
通过控制柜接入电厂DCS系统的监测数据包括:热源换热器前后烟温、冷源换热器前后空气温度、热源换热器壁温,以及前述的报警信号。
水泵运行状态信号,烟道换热器和水箱的液位指示信号。
接入电厂DCS系统的最基本监测数据清单
设定值与控制、报警清单
单独设置报警清单画面,便于及时查看
设备清单。