空调用多翼离心风机参数优化设计
控制速度分布的多翼离心风机优化设计

控制速度分布的多翼离心风机优化设计王瑞;王灿星【摘要】对于多翼离心风机,叶轮叶道中的边界层分离、回流等都是影响风机气动性能的主要因素。
为抑制流动分离,本文运用控制平均速度分布规律的方法,通过编制FORTRAN程序对叶轮叶片进行优化设计,并进行了数值模拟计算分析。
结果表明:基于控制平均速度分布设计的多翼离心风机整体性能明显提高,工况点附近效率提高约4%。
通过分析叶轮流道内的速度场分布,可以看到风机叶轮叶道内靠近中间位置附近的边界层分离现象得到有效抑制。
% For multi-blade centrifugal fan, boundary layer separation and inverse flow are the main factors affecting aerodynamic performance. The method of controlled velocity is applied to restrain separation flow, and the impeller blade is optimized by programming FORTRAN and the numerical simulation calculation and analysis is also carried out as well. The results show that the performance of multi-blade centrifugal fan is improved and the efficiency near the operating point is increased about 4%based on the controlled mean velocity law design. Through analyzing the velocity distribution within the impeller flow field, the boundary layer separation phenomenon near intermediate position of impeller is effectively suppressed.【期刊名称】《风机技术》【年(卷),期】2013(000)003【总页数】6页(P47-52)【关键词】多翼离心风机;速度控制;边界层分离【作者】王瑞;王灿星【作者单位】浙江大学流体工程研究所;浙江大学流体工程研究所【正文语种】中文【中图分类】TH4320 引言多翼离心风机具有结构紧凑、压力系数高、流量系数大和噪声低等优点,被广泛应用于许多换气装置、电子设备和空调系统等场合。
离心风机流道设计及优化研究

离心风机流道设计及优化研究离心风机是目前常见的一种用于通风、排风、送风等工程领域的设备,其核心部件——流道设计和优化,对于风机的性能和效率具有重要影响。
在本文中,将探讨离心风机流道设计及优化的相关内容,并介绍一些常见的优化方法和技术。
一、离心风机流道设计的重要性在离心风机中,流道是将进入的气体引导并加速到风机出口的关键部分,其设计直接影响到风机的性能和效率。
合理的流道设计能够改善气体的流动情况,提高风机的压力能力和送风量,从而达到更高的效率和能耗降低。
而不合理的流道设计可能会导致流动不均匀、能量损失过多等问题,降低风机的性能。
二、离心风机流道设计的要点1. 流道截面设计:离心风机的流道截面形状对于气体流动的扩张和压力变化起着重要作用。
合理的截面设计应考虑流体的流动特性和气体性质,使得气体能够顺利地通过截面,避免过度扩张和收缩,从而减少气流的阻力和能量损失。
2. 纵向流道设计:纵向流道的设计主要考虑气流的加速和扩张,在保持流态稳定的前提下,提高风机的压力能力。
通过合理的纵向流道设计,可以使气流在流道内部能够顺利加速,并尽量减少阻力和湍流的产生,从而最大程度地提高离心风机的效率。
3. 流道表面光滑度:流道表面的光滑度对气流的流动阻力和损耗有着重要影响。
光滑的表面能够减少摩擦阻力,提高流道的效率。
因此,在流道设计中,应注意流道表面的加工工艺和涂层材料的选用,以保证流道表面的光滑度和微粗糙度控制在合理范围内。
三、离心风机流道优化的方法和技术1. 数值模拟与仿真:利用计算流体力学(CFD)方法,对离心风机的流场进行数值模拟和仿真分析,可以得到流道内气流的速度、压力等分布情况,进而评估不同设计方案的性能。
这种方法不仅能够快速进行流道设计的优化,还能够为流道的改进提供有效的思路和参考。
2. 正交试验设计:利用正交试验设计方法,对流道的关键参数进行多因素、多水平的试验,以寻找最佳的参数组合,优化流道设计。
通过实验数据的统计分析,可以确定不同参数对流场的影响程度和相互关系,为进一步的优化提供依据。
空调用多翼离心风机参数的优化设计

空调用多翼离心风机参数的优化设计摘要:通过对空调用多翼离心风机的结构和性能参数进行相应的优化,提高了离心风机的效率,并降低离心风机的噪音,以风机的效率和噪音为优化设计的寻优目标。
风机的全压效率及噪音是叶轮入口平均直径、叶片进口安装角、叶片出口安装角、蜗壳宽度、蜗壳出口长度、叶片数及流量等几何参数的函数。
因此,可以借助于数学优化的手段,通过有限次迭代,就可以求出当综合目标函数达到最大值时有关参数的具体数值。
关键词:多翼离心风机;优化设计;ANSYS多翼离心风机[]因其体积小、噪声低、压力系数高及流量系数大的优点,被广泛使用在抽油烟机、空调等领域。
由于风机的性能直接影响空调系统的品质,于是对空调系统中风机性能优化的要求也越来越高。
在中央空调系统中人们总希望在满足低噪声的同时,空调风机能送出更大的风量。
因此,从节约能源、降低噪音污染的角度考虑,设计出高效率低噪声的风机有十分重要的意义。
用传统设计理论设计多翼离心风机时,风机叶轮进、出口角、叶片数等一些影响风机性能的结构参数在选择时有很大的不确定性[1][2],因此设计出的产品方案不一定是最优方案,造成工程产品常常出现风量、压力达不到性能要求的情况,为此人们对多翼离心风机的结构参数进行了一些试验优化研究。
目前,风机的数学优化方面的工作仅仅局限于一些单目标优化,如加大叶片宽度,减小蜗壳相对宽度,及减小出口安装角来提高离心风机的效率。
且优化同时所选择的设计变量也是有限的几个,这对于风机这一复杂的系统来说是远远不够的。
在本文的优化设计中,主要是通过对离心式通风机结构、性能参数的优化来降低离心风机的噪音和提高离心风机的效率。
风机的效率和噪音可表示成风机的叶轮直径、叶轮入口平均直径、叶片进口安装角、叶片出口安装角、蜗壳宽度B、蜗壳出口长度C、叶片数Z及流量Q的函数[2][3],在离心风机优化设计中选取以上八个参数作为离心风机优化设计的设计变量。
1、空调用多翼离心风机的数学优化方法在进行优化设计时,用公式描述一个实际系统的模型即确定数学模型是整个优化设计中最具有决策性的一步,因为它关系到所要求的解是否具有物理意义且现实可行。
多翼离心风机叶片参数优化设计对壁挂式空调新风部件的气动性能研究

多翼离心风机叶片参数优化设计对壁挂式空调新风部件的气动
性能研究
林健辉;曹雷;张宏闯;周拨;马列;党南南
【期刊名称】《家电科技》
【年(卷),期】2024()1
【摘要】随着城市化的发展,舒适健康以及审美需求逐年提升,新风空调的销量越来越大,新风量、新风噪声都越来越受到用户关注,新风带来的困扰越来越凸显。
为改
善多翼离心风机的气动性能和噪声值,基于CFD数值摸拟与实验测试相结合的方式对单圆弧叶轮进行全参数优化设计。
通过响应面设计方法对叶片进口安装角
βb_(1)、出口安装角βb_(2)、叶片内径D_(2)、叶片数Z几个参数进行参数化设计。
经过多组方案计算,获得叶片参数与风量和功率的关系。
研究发现通过调整叶轮参数,改善叶片流道内的流场分布,能够有效提高叶片的做功能力并且降低风机噪声性能。
与原型相比,实测同风量噪声降低0.8dB(A),功率降低11.8%。
【总页数】6页(P16-20)
【作者】林健辉;曹雷;张宏闯;周拨;马列;党南南
【作者单位】广东美的制冷设备有限公司
【正文语种】中文
【中图分类】TH432
【相关文献】
1.采用仿鸮翼叶片降低空调用离心风机气动噪声的研究
2.采用吸力面仿鱼形叶片的多翼离心风机气动性能研究
3.多翼离心风机双圆弧叶片的参数优化设计及气动性能分析
4.多翼离心风机分组优化设计对风机盘管整机气动性能的响应度研究
5.采用仿鲤科鱼C型启动构型叶片的多翼离心风机气动性能研究
因版权原因,仅展示原文概要,查看原文内容请购买。
多翼离心风机数值计算及改进设计研究

从表 1 中可以看出,采用的 3 种 k-ε 湍流模型所 得到的结果极为接近,并且与试验结果也比较吻合, 这说明了数值计算的结果是合理的,计算方法是可靠 的,同时也说明了采用这 3 种 k-ε 模型计算风机内部 流场均是可行的。从表 1 可以看出,数值计算结果比 试验测量结果偏大,产生该误差的主要原因如下:
( 1) 建模阶段对风机的部分区域进行了简化处 理,从而使得数值计算中的摩擦损失、轮阻损失和泄 漏损失与试验测量结果相比偏小。
( 2) 建模时忽略的一些次要结构,会带来一定 的误差。
( 3) 由于模型的复杂性以及计算条件的限制, 选用的网格类型是非结构网格,精度有限,从而引起 一定的误差。 1. 4 流场分析
对以上 4 个流体区域的连接面,有两种处理方 法: 一种方法是将连接面定义为内边界 ( interior) , 此时就要在几何建模阶段使这个面相邻的两个区域 共用该面; 另一种方法是将连接面定义为交界面 ( interface) ,此时在几何建模阶段,对这个面相邻的 两个区域分别定义一个面,而这两个面的几何位置 和形状是相同的,但拥有不同的名称和标记,并可采 用不同的网格类型。采用第一种方法,在计算中不 需要进行任何处理; 若采用第二种方法,则在计算中 需要通过 Fluent 中的 Define / Grid interface 来实现这 两个面的数据交换[2]。
2 结构参数对风机性能的影响 影响多翼离心风机性能的结构参数很多,如叶片
进口安装角、叶片出口安装角、叶轮宽度比、叶轮内外 径比、叶轮外径、叶片型线、叶片数、蜗壳型线、蜗舌间 距等等。笔者只在转速、叶轮内外径、叶轮宽度不变 的情况下,对叶片进口安装角、叶片出口安装角、叶片 数、叶片型线、蜗壳型线和蜗舌间距这些影响多翼离 心风机性能的结构参数进行数值模拟计算。 2. 1 叶片进口安装角的影响
离心鼓风机的优化设计与性能提升
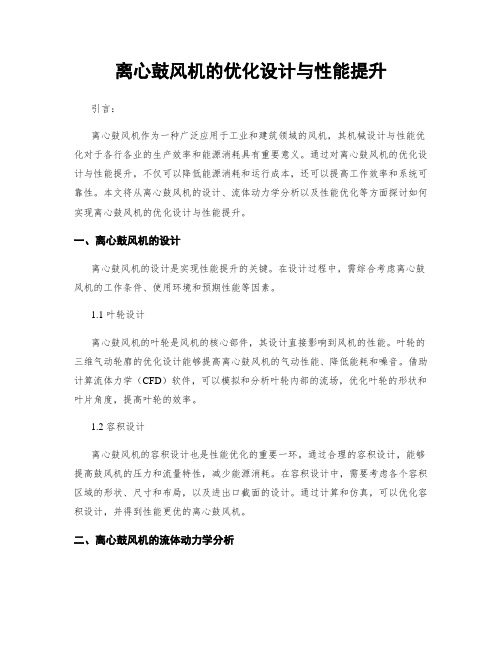
离心鼓风机的优化设计与性能提升引言:离心鼓风机作为一种广泛应用于工业和建筑领域的风机,其机械设计与性能优化对于各行各业的生产效率和能源消耗具有重要意义。
通过对离心鼓风机的优化设计与性能提升,不仅可以降低能源消耗和运行成本,还可以提高工作效率和系统可靠性。
本文将从离心鼓风机的设计、流体动力学分析以及性能优化等方面探讨如何实现离心鼓风机的优化设计与性能提升。
一、离心鼓风机的设计离心鼓风机的设计是实现性能提升的关键。
在设计过程中,需综合考虑离心鼓风机的工作条件、使用环境和预期性能等因素。
1.1 叶轮设计离心鼓风机的叶轮是风机的核心部件,其设计直接影响到风机的性能。
叶轮的三维气动轮廓的优化设计能够提高离心鼓风机的气动性能、降低能耗和噪音。
借助计算流体力学(CFD)软件,可以模拟和分析叶轮内部的流场,优化叶轮的形状和叶片角度,提高叶轮的效率。
1.2 容积设计离心鼓风机的容积设计也是性能优化的重要一环。
通过合理的容积设计,能够提高鼓风机的压力和流量特性,减少能源消耗。
在容积设计中,需要考虑各个容积区域的形状、尺寸和布局,以及进出口截面的设计。
通过计算和仿真,可以优化容积设计,并得到性能更优的离心鼓风机。
二、离心鼓风机的流体动力学分析离心鼓风机的流体动力学分析是对其内部流场进行定量研究的过程,通过这一分析,可以更好地理解离心鼓风机的工作原理,找到性能瓶颈,为性能提升提供依据。
2.1 流动特性分析通过CFD建模和仿真分析,可以详细地了解离心鼓风机内部的流动特性。
在分析过程中,需要考虑各个区域的速度、压力分布等参数,并结合叶轮的转速和叶轮的气动特性,分析离心鼓风机的工作点、流量特性和压力特性。
2.2 损失分析离心鼓风机中存在着各种损失,如动量损失、径向压力损失和方向损失等。
通过流体动力学分析,可以定量计算各种损失,并找到导致性能下降的关键因素。
在优化设计过程中,针对损失因素进行改进和调整,能够有效地提升离心鼓风机的性能。
多翼离心风机蜗壳气动性能与出风均匀性优化设计

多翼离心风机蜗壳气动性能与出风均匀性优化设计
刘江;沈春根;林传生
【期刊名称】《排灌机械工程学报》
【年(卷),期】2024(42)6
【摘要】以某型号风暖浴霸吹风系统的多翼离心风机为研究对象,利用ANSYS Fluent 2020 R2对原型风机的出口风量与均匀度进行仿真分析,结果显示仿真与实测误差在5%以内,验证了用CFD数值模拟方法来优化浴霸多翼离心风机的可靠性.将蜗壳型线参数化,通过正交试验设计,针对蜗舌放置角α、蜗舌半径R、等角螺线常数A(蜗壳周向面积)与风轮移动距离L(蜗舌与叶轮间隙)4个因素,制定了16组参数组合方案并进行了CFD数值模拟,得到各方案的出口风量与均匀度,并由均值与极差分析确定了最优参数组合.通过数值计算结果可知,优化后的风机在蜗舌附近区域湍流强度减小,内部流动改善.测试结果显示,优化后的风机出口风量提升7.3%,均匀度提升4.5%,全压效率提升5.9%.显著提升了风暖浴霸离心风机的出风性能和出口风速分布均匀性,对提高风暖浴霸取暖效率和增强人体舒适性有重要意义.
【总页数】8页(P591-597)
【作者】刘江;沈春根;林传生
【作者单位】江苏大学机械工程学院
【正文语种】中文
【中图分类】TH432
【相关文献】
1.离心风机蜗壳基于响应面法的气动优化设计
2.多翼离心风机风叶和蜗壳径向间隙对风管机风量噪声的影响研究
3.多翼离心风机模化设计中叶轮-蜗壳的匹配性研究
4.教育研究中情感转向的出场与实现
5.分流孔结构对蜗壳式风环出风均匀性的影响
因版权原因,仅展示原文概要,查看原文内容请购买。
汽车空调前向多翼离心通风机气动声学特性分析与优化
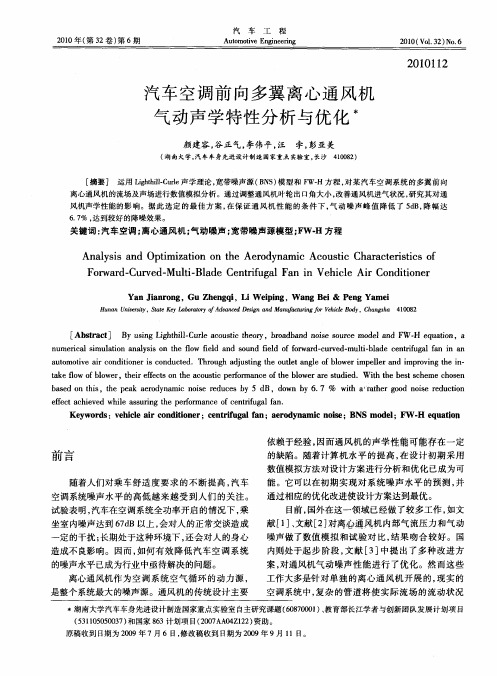
随着人们对乘 车舒适度要求的不断提高 , 汽车
空调 系统 噪声 水 平 的 高低 越 来 越 受 到人 们 的关 注 。 试 验表 明 , 车在 空调系统 全功 率开 启 的情 况 下 , 汽 乘
坐室内噪声达到 6 d 7 B以上 , 会对人的正常交谈造成
[ bta t B s gLg ti—u eao scter , rab n os orem dl n W— q a o , A s c ] yui ihhlC r cut oy bod a dn i suc o e a dF H e ut n a r n l i i h e i
H n nU iri ,Sae e aoaoyo da cdD s nadMa u c r gfrVhc o y C agh 40 8 u a n esy ttK yL brtr fA vne ei n v t g nf t i o eieB a , hn sa 10 2 aun l
a t oi ic n io e od c d ho g dut gteot t n l o l e e e n r igte n u m t ea o dt nr s n u t .T ruhajsn ul ge f o rmpl r di o n — o v r i ic e i h ea b w i l a mp v hi
tk lw fb o r h i fe t n te a o si e fr n e o e b o rae su id.W i h e ts h mec o e a e fo o lwe ,t erefc so h c u tc p roma c ft lwe y t d e h t t e b s c e h s n h b s d o h s h e k a rdy a c n ie r d c s b B,d wn b . % wih w r t e o d n ie r d c in a e n t i ,t e p a e o n mi os e u e y 5 d o y6 7 t ah rg o o s e u t o
- 1、下载文档前请自行甄别文档内容的完整性,平台不提供额外的编辑、内容补充、找答案等附加服务。
- 2、"仅部分预览"的文档,不可在线预览部分如存在完整性等问题,可反馈申请退款(可完整预览的文档不适用该条件!)。
- 3、如文档侵犯您的权益,请联系客服反馈,我们会尽快为您处理(人工客服工作时间:9:00-18:30)。
空调用多翼离心风机参数的优化设计摘要:通过对空调用多翼离心风机的结构和性能参数进行相应的优化,提高了离心风机的效率,并降低离心风机的噪音,以风机的效率和噪音为优化设计的寻优目标。
风机的全压效率及噪音是叶轮入口平均直径、叶片进口安装角、叶片出口安装角、蜗壳宽度、蜗壳出口长度、叶片数及流量等几何参数的函数。
因此,可以借助于数学优化的手段,通过有限次迭代,就可以求出当综合目标函数达到最大值时有关参数的具体数值。
关键词:多翼离心风机;优化设计;ansys
多翼离心风机[]因其体积小、噪声低、压力系数高及流量系数大的优点,被广泛使用在抽油烟机、空调等领域。
由于风机的性能直接影响空调系统的品质,于是对空调系统中风机性能优化的要求也越来越高。
在中央空调系统中人们总希望在满足低噪声的同时,空调风机能送出更大的风量。
因此,从节约能源、降低噪音污染的角度考虑,设计出高效率低噪声的风机有十分重要的意义。
用传统设计理论设计多翼离心风机时,风机叶轮进、出口角、叶片数等一些影响风机性能的结构参数在选择时有很大的不确定
性[1][2],因此设计出的产品方案不一定是最优方案,造成工程产品常常出现风量、压力达不到性能要求的情况,为此人们对多翼离心风机的结构参数进行了一些试验优化研究。
目前,风机的数学优化方面的工作仅仅局限于一些单目标优化,如加大叶片宽度,减小蜗壳相对宽度,及减小出口安装角来提高离心风机的效率。
且优化
同时所选择的设计变量也是有限的几个,这对于风机这一复杂的系统来说是远远不够的。
在本文的优化设计中,主要是通过对离心式通风机结构、性能参数的优化来降低离心风机的噪音和提高离心风机的效率。
风机的效率和噪音可表示成风机的叶轮直径、叶轮入口平均直径、叶片进口安装角、叶片出口安装角、蜗壳宽度b、蜗壳出口长度c、叶片数z及流量q的函数[2][3],在离心风机优化设计中选取以上八个参数作为离心风机优化设计的设计变量。
1、空调用多翼离心风机的数学优化方法
在进行优化设计时,用公式描述一个实际系统的模型即确定数学模型是整个优化设计中最具有决策性的一步,因为它关系到所要求的解是否具有物理意义且现实可行。
对问题建立好的公式描述是优化研究成功的关键[7]。
一般情况下,风机的设计指标关键在于效率,故首先以风机效率为优化设计的寻优目标。
离心风机的效率响应模型的建立
通常情况下,通风机的损失主要包括轮盘损失、流动损失、容积损失和外部机械损失四部分。
流动损失引起通风机压力的降低;容积损失引起流量减小轮盘摩擦损失;外部机械损失则引起外加的功率消耗。
轮盘摩擦损失
轮盘损失的计算可借助于封闭在机壳内的圆盘试验结果计算[2]。
计算公式常写成下列形式:
(瓦)(1)
式中:—圆盘摩擦损失功率,瓦;—气体密度,千克/米3;d2—叶轮外径,米;u2—叶轮外径处圆周速度,米/秒;—轮阻损失计算系数。
1.1.2容积损失
在离心式通风机叶轮入口与进风口间有一定间隙,由于蜗壳内的气流压力超过一个大气压,蜗壳内的气体会从主轴与蜗壳之间的间隙泄露一部分到大气中去。
并且在机壳与通风机轴或轴套之间,也将引起气体泄露。
泄露损失的计算式如下:
(米3/秒)(2)
式中:—泄露量,米3/秒;—叶轮入口直径,米;—进风口与叶轮间隙,米;—锐边孔的流量系数。
1.1.3流动损失
流动损失相对于前两种损失比较复杂,其产生的原因在于气体的粘性。
在整个流动过程中一方面存在沿程摩擦损失,另一方面还因为边界层分离,产生涡流损失。
流动损失可表示如下[4]:
(3)
式中:—风机进气口的流动损失,帕;—叶轮进口转弯处流动损失,帕;—叶道中的损失,帕;—气流从叶轮出口流入蜗壳时的突然扩大损失,帕;—蜗壳中转弯撞击和摩擦损失,帕;—蜗壳尾部的扩压损失,帕。
1.1.4机械损失
通风机由于轴承、联轴器及皮带轮等的机械摩擦所消耗的功率,叫做机械损失。
由风机的基本理论可知,通风机转子传给气体的功率等于有效功率和流动损失功率及轮盘摩擦损失功率之和。
各计算公式分别为:
其中:,为理论全压;,为叶轮外径处圆周速度;为叶轮外径;,为叶片出口速度切向分量;,为环流系数;为叶片出口速度子午方向分量,米/秒;为叶轮入口平均直径;为泄露量;为叶轮入口直径,一般与近似相等;,为进风口与叶轮间隙;可取0.15~0.7,为锐边孔的流量系数;,为圆盘摩擦损失功率;为轮阻损失计算系数,根据斯脱多拉意见=0.81~0.88。
由以上可以看出,风机的全压效率是几何参数、、、、、、……以及气动参数、等的函数。
因此,可以借助于数学优化的手段,通过有限次迭代,就可以求出当全压效率达到最大值时有关参数的具体数值。
离心风机的噪音响应模型的建立
风机在一定工况下运转时,产生的噪声主要包括空气动力噪声、机械噪声及气体和固体弹性系统相互作用产生的气固藕合噪声。
在风机的这些噪声中,空气动力噪声约占45%,机械噪声约占30%,气固藕合噪声约占25%。
[8]
假设通风机损耗中有一部分转化为声功率,其比例为,则可表
示为:
(w) (9)
其中:—比例因子;—风机全压(kgf/m2);—风机风量(m3/s);—风机气动效率。
设离心通风机在额定工况时k≈0.0047[9]。
离心风机的声功率级的表达式为:
(db)(10)
因此,离心风机的声功率级也可以表达成几何参数、、、、、、……以及气动参数、等的函数。
设计变量的选取
由上面的效率响应模型和噪音响应模型可以得到:
在上两式中,、、、及等参数是在设计时预先给定的参数,称为给定参数。
、及可由其它参数决定,称为相关变量。
剩下的、、、、、z及c可初步选定为要优选的参数,即设计变量[5]。
初步选定设计变量以后,还要进行进一步的筛选。
本优化共有8个设计变量,即本数学优化是一个8维非线性数学规划问题。
通过这一系列的工作不仅可以考虑到某一因素的影响,还可以兼顾到诸因素交互作用的影响。
这对于风机这一复杂的系统是很难能可贵的。
综合目标函数的建立
确定目标函数是整个优化设计中最重要的一步,它代表优化的
总方向和总目标,目标函数大都是根据工程实际的需要而定。
由上面的讨论可以得出本优化的目标函数。
实际上,对于风机的数学优化问题,应该是一个既考虑效率又考虑噪音的多目标优化问题。
由于不管在理论上还是实践上,我们总希望效率越大越好,噪音越小越好【6】,因此本论文的目标函数为:
(11)
式中和分别为单纯考虑声功率级和效率时的声功率级和效率的最优值。
和可以表示成八个设计变量的函数,则也可以表示成这八个设计变量的函数形式。
本文需要进行优化的数学模型不能直接表示成约束变量的函数,即所用数学模型是各设计变量的隐函数。
因此对本文中数学模型的求导应该算是极其复杂的。
首先采用ansys-apdl语言对风机参数进行编程,建立数学模型,进行优化迭代,选出最优参数,对参数进行分析,并将优化前后的参数进行对比。
其次以优化完的风机参数在ansys软件中建立优化风机的有限元模型,划分网格,施加位移和载荷约束,将处理好的风机的有限元模型再进行模态分析和静力分析计算,并进行结果分析。
最后在ansys workbench里面进行流场模拟,并对设计结果进行分析。
2、结论
1、建立了离心风机的效率和噪声综合目标函数,不仅可以考虑
到某一因素的影响,还可以兼顾到诸因素交互作用的影响。
2、通过对风机叶轮的模拟,可以了解到叶轮对效率的影响。
3、用声振分析的方法,进行结构周围的声场分析;探索解决离心通风机噪声数值模拟的方法,具有很强的实用价值,它可以解决实际工程中的一类问题。
参考文献:
[1]李庆宜.通风机[m].北京:机械工业出版社,1981.09.
[2]商景泰.通风机手册[m].北京:机械工业出版社,1994.08.
[3]b.埃克.通风机.沈阳鼓风机研究所等译,机械工业出版社,1983.2.
[4]黄哀武,区颖达,张吕超.多翼离心通风机叶轮主要特征参数的试验分析.风机技术,
2001(6): 9-11.
[5]刘秋洪,祁大同,曹淑珍.风机降噪研究的现状与分析[j].风机技术,2001.(02).
[6]胡如夫,芦亚萍,林艳华.离心式通风机的降噪试验研究.风机技术2001,no.2,11-12.
[7]胡如夫,俞大川.离心式通风机设计与改造中的降噪方法.流体机械, 2000,vol.28,
no.10,32-34.
[8]赵复荣,郭志新,姚承范.提高多翼离心风机性能的试验研究[j].流体机械.1997,
25(2):9-11.
[9]智乃刚,萧滨诗.风机噪声控制技术[m].北京:机械工业出版社,1985
注:文章内所有公式及图表请以pdf形式查看。