铁路货车车体钢结构柔性组装装置设计分析
铁路货车端墙柔性化组焊夹具开发与应用
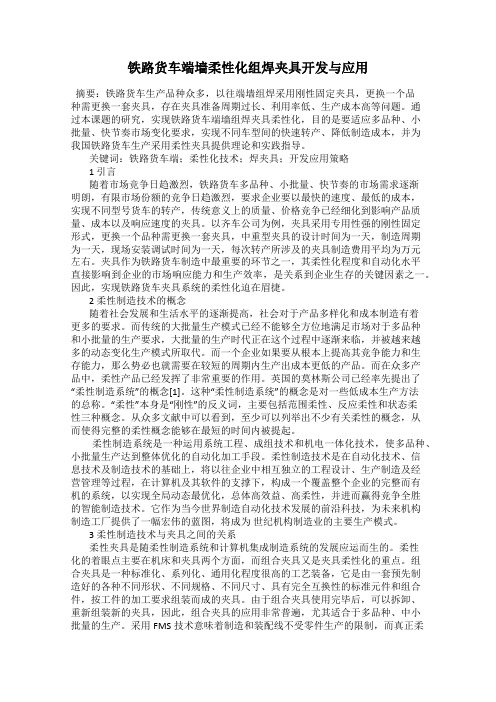
铁路货车端墙柔性化组焊夹具开发与应用摘要:铁路货车生产品种众多,以往端墙组焊采用刚性固定夹具,更换一个品种需更换一套夹具,存在夹具准备周期过长、利用率低、生产成本高等问题。
通过本课题的研究,实现铁路货车端墙组焊夹具柔性化,目的是要适应多品种、小批量、快节奏市场变化要求,实现不同车型间的快速转产、降低制造成本,并为我国铁路货车生产采用柔性夹具提供理论和实践指导。
关键词:铁路货车端;柔性化技术;焊夹具;开发应用策略1 引言随着市场竞争日趋激烈,铁路货车多品种、小批量、快节奏的市场需求逐渐明朗,有限市场份额的竞争日趋激烈,要求企业要以最快的速度、最低的成本,实现不同型号货车的转产,传统意义上的质量、价格竞争已经细化到影响产品质量、成本以及响应速度的夹具。
以齐车公司为例,夹具采用专用性强的刚性固定形式,更换一个品种需更换一套夹具,中重型夹具的设计时间为一天,制造周期为一天,现场安装调试时间为一天,每次转产所涉及的夹具制造费用平均为万元左右。
夹具作为铁路货车制造中最重要的环节之一,其柔性化程度和自动化水平直接影响到企业的市场响应能力和生产效率,是关系到企业生存的关键因素之一。
因此,实现铁路货车夹具系统的柔性化迫在眉捷。
2 柔性制造技术的概念随着社会发展和生活水平的逐渐提高,社会对于产品多样化和成本制造有着更多的要求。
而传统的大批量生产模式已经不能够全方位地满足市场对于多品种和小批量的生产要求,大批量的生产时代正在这个过程中逐渐来临,并被越来越多的动态变化生产模式所取代。
而一个企业如果要从根本上提高其竞争能力和生存能力,那么势必也就需要在较短的周期内生产出成本更低的产品。
而在众多产品中,柔性产品已经发挥了非常重要的作用。
英国的莫林斯公司已经率先提出了“柔性制造系统”的概念[1]。
这种“柔性制造系统”的概念是对一些低成本生产方法的总称。
“柔性”本身是“刚性”的反义词,主要包括范围柔性、反应柔性和状态柔性三种概念。
铁路车辆车体结构设计改进方法

铁路车辆车体结构设计的改进方法可以从以下几个方面入手:
1. 轻量化设计:采用新型材料和结构,如高强度钢、铝合金等,以减轻车体重量,提高运载能力和能效。
2. 模块化设计:将车体结构划分为若干模块,便于制造、组装和维护,同时提高了设计的灵活性和通用性。
3. 空气动力学优化:通过改进车体外形和减少空气阻力,降低列车运行时的能耗,提高运行速度和稳定性。
4. 结构强度优化:利用有限元分析等技术,对车体结构进行强度和刚度分析,优化结构设计,提高车体的安全性能。
5. 人性化设计:考虑乘客的舒适性和便利性,优化车内布局和设施设计,提高乘客的满意度。
6. 防火、隔音、隔热设计:采用防火材料、隔音材料和隔热材料,提高车体的防火、隔音、隔热性能,保障乘客的安全和舒适。
7. 耐腐蚀设计:选用耐腐蚀材料和表面处理技术,提高车体的耐腐蚀性能,延长车辆使用寿命。
8. 可持续性设计:在设计过程中考虑环保和可持续发展因素,如材料的回收利用、节能减排等。
通过以上改进方法,可以提高铁路车辆车体结构的设计水平,使其更加安全、高效、舒适和环保。
铁路货车制造中柔性工艺装备的研究与开发

铁路货车制造中柔性工艺装备的研究与开发摘要:柔性工艺装备结构模块化设计的不断探索将为工装设计与制造带来新的理念与方向。
科技要创新,思路要拓宽,我们要为今天的制造业发展走出新的路子。
关键词:铁路货车;柔性化;工艺装备柔性工艺装配在现在的机械制造行业有着举足轻重的地位,铁路货车柔性装配在各种铁路货车的研制中也是中心环节,把握好柔性装配技术,才能提高铁路货车装配的质量和效率,减短铁路货车研发的周期,降低成本,才能实现利益的最大化。
本文结合了铁路货车制造领域对于柔性装配的高要求进行分析,并且对柔性工装的发展状况进行了简要的概括,并提出了柔性工装控制系统的方案设计,为铁路货车柔性装配的进一步发展奠定了基础。
1柔性工装概述我们提到的柔性工装结构设计从实用角度看包含三方面内容:一是工装元件能够灵活重组,元件、组件、合件能够重复分解和有机拼装,实际应用中实现预定的功能,重组后实现特定结构的柔性化;二是柔性工装的结构设计,这里引进模块化设计理念,需要预先建立数据库包括标准建库、模块元件库、单元模块库,利用设计软件根据实际用途灵活快速组装设计,完成柔性工装的图纸预设计,可以在产品本工序未加工前实现工装按计划组装;三是工装在设备之间的换装,要实现柔性快速换装,这就要求在设备上增加快换接口,达到同一工装能够快速在不同设备之间换装,不同工装在同一设备上实现快换,以达到换装的柔性化,这就需要进一步研究被加工零件与工装之间快速定位夹紧与换装。
2柔性工装的结构设计研究2.1柔性工装结构设计的概念我们提到的柔性工装结构是由标准件、基础件、合件、功能组件、单元模块等按照特定功能拼装而成,能够满足工艺要求,并能快速拆分重组的工装结构。
要求元件具有很好的互换性和较高的精度及耐磨性,可以根据机床工作台的尺寸和不同零件的加工要求,选用所需要的元件、功能组件组装成各种工装结构,组装灵活方便,适应范围广。
2.2柔性工装结构设计方法近年来,高科技的普及和专业软件的开发,虚拟装配的应用,为柔性工装结构设计、数据管理提供优越的条件。
某型小汽车运输铁路专用车车体强度分析及结构优化

某型小汽车运输铁路专用车车体强度分析及结构优化某型小汽车运输铁路专用车车体强度分析及结构优化1.引言某型小汽车运输铁路专用车是一种用于将小汽车从一个地点运输到另一个地点的专用车辆。
为了确保车辆的安全和稳定运行,需要进行车体强度分析和结构优化。
本文将对该型号车辆车体进行强度分析,并提出结构优化方案。
2.车体强度分析2.1 模型建立首先,对该型车辆进行三维建模。
选择合适的软件,进行车辆车体的建模和网格划分,得到完整的有限元模型。
模型的划分应按照车身结构进行,包括车身底板、车身壳体、支撑结构等。
2.2载荷分析根据设计标准和实际使用情况,确定各种载荷条件。
主要包括静态荷载、动态荷载和温度荷载等。
静态荷载包括自重、车辆载荷和小汽车载荷等;动态荷载包括行车、刹车、转弯等时产生的加速度;温度荷载则是指因温度变化引起的应力。
2.3边界条件的设定根据实际情况,设定相应的边界条件。
例如,固定底板和支撑结构的连杆连接处,设定其固定约束。
同时,还需设置诸如悬挂、支撑连接处的约束。
2.4材料性能参数设置选择车辆的主要构件材料,并设置相应的材料性能参数。
包括杨氏模量、泊松比、抗拉强度、屈服强度等。
这些参数直接影响整个模型在载荷作用下的变形和应力情况。
2.5加载及分析根据前述模型的建立、载荷和边界条件的设定以及材料性能参数的设置,进行有限元分析。
根据模拟结果,获取车体在不同荷载工况下的应力、应变等信息。
3.结构优化根据车体的强度分析结果,进行结构优化。
主要通过调整结构的材料、厚度和减少不必要零件等方式,提高车身的强度。
优化的目标是在保证车辆运行稳定的前提下,尽量减少车身的重量。
3.1选用优质材料根据强度分析结果,选择优质材料以提高车体的强度。
合理选择材料可以有效减少车身的重量,并且提高车身的刚度和抗拉强度。
3.2优化车身结构通过优化车身结构,减少不必要的零件和连接件,降低车身的重量。
可以使用拓扑优化方法,分析不同结构形式下车体的强度。
铁路货车车体组装的柔性化模块设计
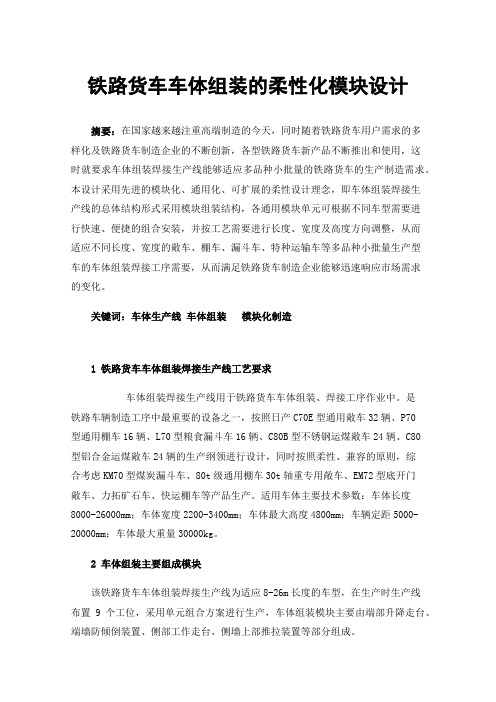
铁路货车车体组装的柔性化模块设计摘要:在国家越来越注重高端制造的今天,同时随着铁路货车用户需求的多样化及铁路货车制造企业的不断创新,各型铁路货车新产品不断推出和使用,这时就要求车体组装焊接生产线能够适应多品种小批量的铁路货车的生产制造需求。
本设计采用先进的模块化、通用化、可扩展的柔性设计理念,即车体组装焊接生产线的总体结构形式采用模块组装结构,各通用模块单元可根据不同车型需要进行快速、便捷的组合安装,并按工艺需要进行长度、宽度及高度方向调整,从而适应不同长度、宽度的敞车、棚车、漏斗车、特种运输车等多品种小批量生产型车的车体组装焊接工序需要,从而满足铁路货车制造企业能够迅速响应市场需求的变化。
关键词:车体生产线车体组装模块化制造1 铁路货车车体组装焊接生产线工艺要求车体组装焊接生产线用于铁路货车车体组装、焊接工序作业中。
是铁路车辆制造工序中最重要的设备之一,按照日产C70E型通用敞车32辆、P70型通用棚车16辆、L70型粮食漏斗车16辆、C80B型不锈钢运煤敞车24辆、C80型铝合金运煤敞车24辆的生产纲领进行设计,同时按照柔性、兼容的原则,综合考虑KM70型煤炭漏斗车、80t级通用棚车30t轴重专用敞车、EM72型底开门敞车、力拓矿石车、快运棚车等产品生产。
适用车体主要技术参数:车体长度8000-26000mm;车体宽度2200-3400mm;车体最大高度4800mm;车辆定距5000-20000mm;车体最大重量30000kg。
2 车体组装主要组成模块该铁路货车车体组装焊接生产线为适应8-26m长度的车型,在生产时生产线布置9个工位,采用单元组合方案进行生产,车体组装模块主要由端部升降走台、端墙防倾倒装置、侧部工作走台、侧墙上部推拉装置等部分组成。
2.1 端部升降走台,该部分为于各型车体的端部位置,采用模块化设计,可柔性移动,每个单元长度2米,宽度0.75米,工作时端部升降走台底部与基础固定,组装时根据车型尺寸进行模块单元柔性组合,间距可调。
浅谈卡车柔性自动化焊装生产线设计开发
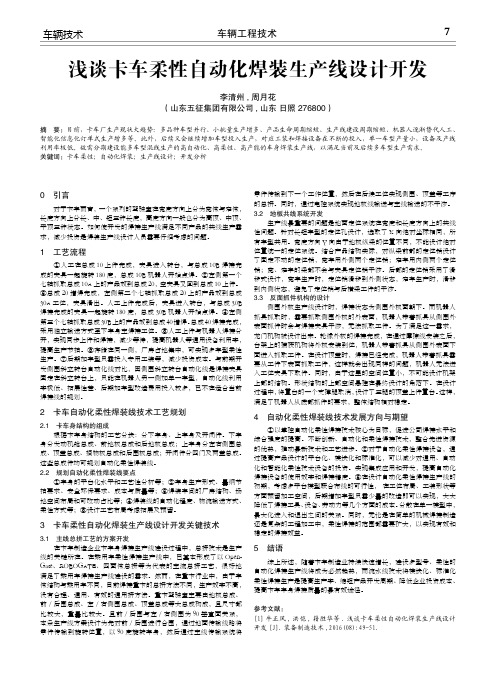
车辆工程技术7车辆技术0 引言 对于卡车而言,一个系列的驾驶室在宽度方向上分为宽体与窄体,长度方向上分长、中、短三种长度,高度方向一般也分为高顶、中顶、平顶三种状态。
如何使开发的焊接生产线满足不同产品的共线生产需求,减少投资是焊装生产线设计人员需要仔细考虑的问题。
1 工艺流程 ①人工在总成10上件完成,夹具进入转台,与总成10B焊接完成的夹具一起旋转180度,总成10B机器人开始点焊。
②左侧第一个七轴抓取总成10A上的产品放到总成20,空夹具又回到总成10上件。
③总成20增焊完成,左侧第二个七轴抓取总成20上的产品放到总成30A工位,夹具滑出。
人工上件完成后,夹具进入转台,与总成30B 焊接完成的夹具一起旋转180度,总成30B机器人开始点焊。
④左侧第三个七轴抓取总成30B上的产品放到总成40增焊。
总成40焊接完成,采用独立输送方式至下车身主焊接工位。
⑤人工上件与机器人焊接分开,实现同步上件和焊接,减少等待,提高机器人等通用设备利用率,提高生产节拍。
⑥存储在同一侧,厂房占地集中,可实现多车型柔性生产。
⑦后期加车型只需投入专用工装等,减少投资成本。
与前期开发侧围斜立转台自动化线对比,因侧围斜立转台自动化线是焊接夹具固定在斜立转台上,只能在机器人另一侧加单一车型,自动化线利用率极低、拓展性差、后期加车型改造费用投入较多,已不在适合当前焊接线的规划。
2 卡车自动化柔性焊装线技术工艺规划2.1 卡车身结构的组成 根据卡车身结构的工艺分块:分下车身、上车身及开闭件。
下车身分发动机舱总成、前地板总成和后地板总成;上车身分左右侧围总成、顶盖总成、搁物板总成和后围板总成;开闭件分四门及两盖总成。
这些总成件均可规划自动化柔性焊装线。
2.2 规划自动化柔性焊装线要点 ①车身的平台化水平和工艺性分析等;②车身生产形式、量纲节拍要求、安全环保要求、成本与质量等;③焊装车间的厂房结构、场地空间布局和可改动占比等;④焊装线的自动化程度、物流输送方式、柔性方式等;⑤设计工艺布局考虑拓展及预留。
铁道机车车辆车体分解

2020/7/1
14
二、集装箱车
集装箱车结构:在底架上不设地板和 墙板,由底架承受集中载荷,为了满足 承载结构和便于制造,底架采用全钢电 焊结构。
1一手制动机;2一端梁;3一斜撑;4一枕梁;5一侧梁;6一小顺梁; 7一门止挡;8一中梁;9一固定式锁闭装置;10一翻转式锁闭装置;11一横梁。
2020/7/1
二、P62型棚车(P62型棚车是在P61型基础上设计制造的 )
1一侧墙;2一侧门;3~通风口;4~车顶;5一扶梯;6一端墙;7~人力制动机。
特点:P61. P62型棚该车结构可靠,便于作业 和维修,但不适于运送人员、牲畜及军用物资。
2020/7/1
6
三、P64型棚车 P64型棚车载重58 t,自重25.4 t,容积116 m3 是在P62的 基础上设计的,其车体主要结构、外造型与P62型棚车基本相同
四、P65s型行 包快运棚车
1.P65s型 行包快运棚 车的组成
2.P65s型行包快运棚车的主要性能及特征
特点: P65s。型棚车在P65型棚车的基础上加装了押运间,减 少了一些载重和容积。车门上装有新型门锁,这种门锁安全可
靠20,20/7防/1 盗性能好,而且不易损坏。
7
五、活顶棚车
1.活顶棚车 组成
2020/7/1
4
图2-2货车车底架一般结构 1一端梁;2一枕梁;3一上旁承;4一上心盘;5一侧梁;6一中梁;
7一大横梁;8一地板托梁;9一从板座。
货车车底架由中梁、侧梁、枕梁、端梁、大横梁、小横 梁及地板托梁等组成。
2020/7/1
5
第二节 棚 车 一、P61型棚车 P61型棚车自重24 t,载重60 t,容积120 m3
关于铁路货车车体刚度评定标准的分析与思考
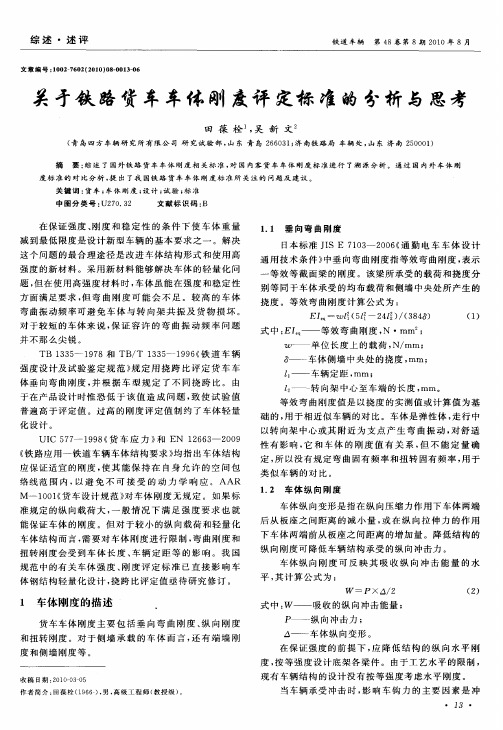
体钢 结构 轻量化 设计 , 跨 比评定 值亟 待研 究修 订 。 挠
1 车 体 刚 度 的 描 述
货车 车体 刚度 主要 包 括 垂 向弯 曲刚 度 、 向刚度 纵 和扭 转 刚度 。对 于侧墙 承载 的车 体 而 言 , 有 端墙 刚 还 度 和侧墙 刚度等 。
收 稿 日期 : 0 0 0 5 2 1 - 30
摘 要 : 述 了 国 外铁 路 货 车 车 体 刚 度 相 关 标 准 , 国 内客 货 车 车 体 刚 度 标 准 进 行 了溯 源分 析 。通 过 国 内 外 车 体 刚 综 对 度 标 准 的 对 比分 析 , 出 了我 国铁 路 货 车 车 体 刚 度 标 准 所 关 注 的 问题 及 建议 。 提
关 键 词 : 车 ; 体 刚 度 ; 计 ; 验 ; 准 货 车 设 试 标
中图分类号 : 7.2 U2 0 3
文 献 标 识 码 : B
在保证 强度 、 刚度 和稳 定性 的条 件 下 使 车 体 重量 减 到最低 限度是 设计 新 型车辆 的基 本要 求 之一 。解决
1 1 垂 向 弯 曲 刚 度 .
络 线 范 围 内 , 避 免 不 可 接 受 的 动 力 学 响 应 。 AAR 以
M一 1 0 《 O 1 货车 设计 规范 》 对车 体 刚度无 规 定 。如果 标
准 规 定 的 纵 向载 荷 大 , 般 情 况 下 满 足 强 度 要 求 也 就 一
车体 纵 向变形 是指 在纵 向压缩 力作 用下 车体 两端 后从 板 座之 间距离 的减 小量 , 或在 纵 向拉 伸力 的作 用 下 车体 两端前 从板 座之 间距 离的增 加量 。降低 结构 的 纵 向刚度 可 降低 车辆结 构承受 的纵 向冲击力 。 车体 纵 向 刚度 可 反 映 其 吸 收 纵 向 冲击 能 量 的 水 平, 其计 算公 式为 :
- 1、下载文档前请自行甄别文档内容的完整性,平台不提供额外的编辑、内容补充、找答案等附加服务。
- 2、"仅部分预览"的文档,不可在线预览部分如存在完整性等问题,可反馈申请退款(可完整预览的文档不适用该条件!)。
- 3、如文档侵犯您的权益,请联系客服反馈,我们会尽快为您处理(人工客服工作时间:9:00-18:30)。
[9] 贺振明.高速铣削在模具制作中的应用[J].机电一体化,1998
(4):42-与质
量,2005(2):25-28.
[11] 戴宏阁.刻痕模异形型面的加工方法[J].模具工业,1993(2):
54-56.
(编辑 昊 天)
作者简介:方军华(1984—),男,工学硕士,工程师,研究方向为易开 盖产品及模具研发。
后续,公司需要对 WF20 材料用于 SOT 刻线刀模的 加工工艺进行更深入的研究,以使其能够应用于该刀模 的制作,来提高刻线刀模的使用寿命,降低生产成本,提 高产品质量及效率。
[参考文献] [1] 何军.冲压模具失效形式分析及预防[J].湖北工业职业技术学
院学报,2014,27(4):103-106. [2] 吴华春,李名尧,董黎涛,等.冷作模具材料性能分析及其选用
收稿日期:2014- 09- 25
机械工程师 2015 年第 1 期 273
解决方案
SOLUTION 工艺 / 工装 / 模具 / 诊断 / 检测 / 维修 / 改造
型生产。 在底架制造过程中,以上心盘为基准进行定位,由于
车体组装采用流水作业,以心盘为基准进行车体定位组 装,定位装置影响工序传送,进行夹紧时容易造成底架倾 斜与扭曲,影响组装质量,因此为保证车体正常组装,将 该基准进行转换。根据底架组焊工艺,底架组焊后以心盘 为基准的三梁差应小于 3 mm。可以底架侧梁下平面为基 准,进行车体组装。即底架组装后,对三梁差尺寸进行确 定,在车体组装时,配置标准定位块与调整垫板,保证底 架水平尺寸,从而保证车体组装质量。因此底架定位主要 由底架的一位端端梁、两侧梁侧面及底架侧梁下平面定 位,对底架纵横方向以及水平面进行定位。 2.2.1 底架定位及夹持单元设计分析
[J]. 机械设计与制造,2011(1):250-252. [3] 廖晓明,王凌云.模具材料的表面改性和组织性能分析[J].热加
工工艺,2014,43(14):171-174. [4] 徐耀坤.模具材料及热处理技术对模具寿命影响的研究[J].锻
压技术,2002(4):62-64. [5] 程春炜.浅谈常用模具材料及其热处理工艺[J].科技论坛,2014
1)底架水平定位。在底架下侧梁下平面位于枕梁位 置,设计四定位支撑平台,安装时四支撑平台支承面的平 面度小于 1 mm,支撑台上配置顶升油缸与水平支撑定位 块,底架顶升后采用定位块将底架支撑水平。支撑平台固 定于地面 T 型槽上,可纵横调整,适应不同宽度、长度底 架组装定位。
根据产品设计基准为底架上心盘,以及车体结构特 点与技术参数规定,车体组装工艺以底架为基准,其余部 件组装以此为基准,保证各部件间组装尺寸与形位公差。 2.2 车体组装定位、夹紧单元结构设计分析
由于车体结构差异大,定位、夹紧装置应采用模块化 单元结构,模块单元安装在地面采用螺纹固定或安装于 地面轨道上,纵横以及高度方向可调整,满足不同类别车
块化设计方案,配置车体柔性组装装置,通过模块间组合,满足不同铁路货车车体钢结构组装生产,提高生产效率,降低
制造成本。
关键词:柔性;车体钢结构;装置
中图分类号:U 270.3
文献标志码:B
文章编号:1002-2333(2015)01-0273-03
0引言 铁路货车车体钢结构是装载货物的主体,根据用途
差异,类别迥然。随着铁路货运市场变化,对产品需求发 生根本变化,通用结构形式敞、棚车型市场逐步萎缩,专 用车型日渐成为市场主导,传统的大批量专一生产装备不 能适应市场多样化需求,多功能柔性生产装备成为现实。 1 铁路货车车体钢结构特点分析
铁路货车指的是敞、棚、平、漏、罐,以及特种车辆等 车型,车体钢结构大致由底架、端墙、侧墙、车顶等零部件 组焊而成;罐车钢结构主体由罐板筒体及底架钢结构组 焊成,其结构与敞、棚、平、漏等车型差异过大,其制造工 艺与敞、棚、平、漏等车型差异大,不能完全共线生产,本 柔性组装装备不考虑该类产品。同时平车为底架结构,也 不予分析考虑。组装装置以敞、棚、漏为主进行设计分析, 其主要技术参数如下:
解决方案
工艺 / 工装 / 模具 / 诊断 / 检测 / 维修 / 改造 SOLUTION
铁路货车车体钢结构柔性组装装置设计分析
邓兴伟, 金业全, 李勇, 郭唯 (中国南车眉山车辆有限公司,四川 眉山 620032)
摘 要:根据铁路货车车体钢结构产品图、技术条件的要求,以及车体钢结构特点,按照精益制造理念,采取通用化、模
度≤6 mm。 2 柔性组装装置结构分析设计
钢结构组装装置主要用于完成车体钢结构组成的整 个组装过程,即按技术要求和生产工艺将底架、2 个侧墙、 2 个端墙、车顶等部件组装焊接。为满足不同类别车型组 装要求,整体结构采用组合式、模块化柔性设计方案,以 适应车体长度 8.5~18 m,宽度 2.4~3.4 m,心盘距 5.7~15 m 的车体的组装要求。根据夹具设计原理,零部件组装主要 确定零部件相对位置,确保相对位置不变,即对零部件进 行定位、夹紧,保证零部件组装相对位置及工艺参数,因 此,根据车体钢结构的结构特点,组装装置主要对钢结构 底架、端墙、侧墙、车顶进行定位夹紧,即对该类零部件进 行定位夹紧机构设计。 2.1 工艺基准确定
1)车体外形尺寸:长 8.7~18 m,宽 2.4~3.4 m,高 2.4~ 4.8 m;2)角柱与地板面垂直度,全高内≤7 mm;3)角柱板 与侧梁之间隙≤0.5 mm;4)端墙对角线差≤5 mm;5)上侧 梁与上端缘各面错牙≤2 mm;6)中门孔对角线差≤5 mm; 7)敞车下侧门对角线差≤3 mm;8)侧墙对角线差≤12 mm; 9)上侧梁旁弯每米≤3 mm,全长≤12 mm;10)侧柱垂直
(8):200.
[6] 张清.模具材料及其合理选择[J].金属加工,2008(7):47-50.
[7] 鲁国清.高速切削技术在模具加工中的应用[J].漯河职业技术
学院学报,2014,13(2):51-53.
[8] 张雷.高速铣削表面粗糙度的研究[J].组合机床与自动化加工
技术,2012(12):21-24.