变压器制作工艺标准
变压器制造标准规范最新版
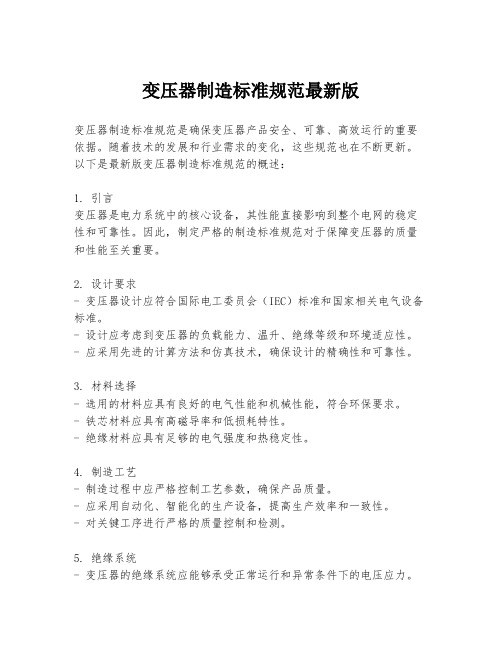
变压器制造标准规范最新版变压器制造标准规范是确保变压器产品安全、可靠、高效运行的重要依据。
随着技术的发展和行业需求的变化,这些规范也在不断更新。
以下是最新版变压器制造标准规范的概述:1. 引言变压器是电力系统中的核心设备,其性能直接影响到整个电网的稳定性和可靠性。
因此,制定严格的制造标准规范对于保障变压器的质量和性能至关重要。
2. 设计要求- 变压器设计应符合国际电工委员会(IEC)标准和国家相关电气设备标准。
- 设计应考虑到变压器的负载能力、温升、绝缘等级和环境适应性。
- 应采用先进的计算方法和仿真技术,确保设计的精确性和可靠性。
3. 材料选择- 选用的材料应具有良好的电气性能和机械性能,符合环保要求。
- 铁芯材料应具有高磁导率和低损耗特性。
- 绝缘材料应具有足够的电气强度和热稳定性。
4. 制造工艺- 制造过程中应严格控制工艺参数,确保产品质量。
- 应采用自动化、智能化的生产设备,提高生产效率和一致性。
- 对关键工序进行严格的质量控制和检测。
5. 绝缘系统- 变压器的绝缘系统应能够承受正常运行和异常条件下的电压应力。
- 应采用多层绝缘结构,提高绝缘性能和可靠性。
6. 冷却系统- 变压器应配备有效的冷却系统,以保持设备在安全的工作温度下运行。
- 冷却方式可以是自然冷却、风冷或油冷,具体取决于变压器的容量和使用环境。
7. 测试与验收- 变压器在出厂前应经过严格的测试,包括绝缘电阻测试、短路阻抗测试和温升试验等。
- 测试结果应符合设计要求和相关标准规范。
8. 安装与运行- 提供详细的安装指南和操作手册,确保变压器的正确安装和运行。
- 运行过程中应定期进行维护和检查,以延长变压器的使用寿命。
9. 环境与安全- 变压器的设计和制造应考虑到环境保护和人员安全。
- 应采取措施减少噪音和电磁干扰,确保对环境的影响降到最低。
10. 结语变压器制造标准规范的最新版旨在通过严格的设计、材料选择、制造工艺、测试与验收等环节,确保变压器产品的高性能和高可靠性。
变压器制造工艺流程

变压器制造工艺流程变压器是一种将电能按照不同电压传递的电气设备,广泛应用于电力系统中。
变压器的制造工艺流程包括变压器设计、材料采购、铁心加工、线圈制作、组装和测试等多个环节。
首先是变压器的设计阶段。
根据用户需求、电力系统要求以及变压器的额定功率和电压等参数,设计师将制定出适合的变压器结构、尺寸和性能要求。
接下来是材料采购阶段。
变压器的主要材料包括铁芯、导线、绕组绝缘和介质等。
制造商将根据设计要求和产品质量要求选择合适的材料,并与供应商进行合作采购。
然后是铁心加工阶段。
铁芯是变压器的核心部件,主要用于传导磁通。
铁芯通常由硅钢片组成,制造商将根据设计要求和减小磁通损耗的需要,对硅钢片进行切割、堆叠和焊接,形成具有特定结构和尺寸的铁芯。
接着是线圈制作阶段。
线圈是变压器的导线组成部分,通过绕制和连接实现电能的传递。
制造商将根据设计要求选择合适的导线规格和绕制方法,并进行绕制、固定和打包等工艺操作,最终形成具有特定匝数和绝缘性能的线圈。
然后是组装阶段。
制造商将根据设计要求和变压器的结构尺寸,将铁芯和线圈进行组合,通过绝缘垫片和支撑结构等辅助部件固定和分隔,形成变压器的基本结构。
同时,制造商还会安装绝缘和绝缘油循环系统等重要设备,确保变压器的安全和可靠运行。
最后是测试阶段。
变压器在制造完成后,需要进行一系列的测试来验证其性能和质量。
这些测试包括绝缘电阻测试、绕组相序检查、冷却系统测试以及负载性能测试等。
只有通过这些测试并符合设计和标准要求,变压器才能出厂。
总之,变压器的制造工艺流程包括设计、材料采购、铁心加工、线圈制作、组装和测试等多个环节。
通过科学的设计和精细的制造过程,才能生产出高质量、高性能的变压器,为电力系统的稳定运行提供可靠的保障。
变压器制作工艺标准及要求
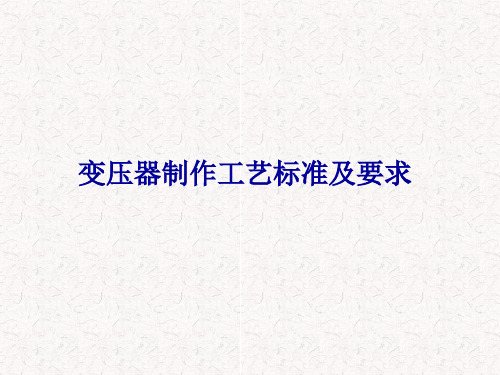
三:包胶带
▪ 包胶带的方式 ▪ 注意事项
1.包胶带的方式一般有以下几种
A.同組不同層的絕緣方法. B.不同層的絕緣方法. C.最外層的絕緣方法.
5~10mm
5mm 以 上
D.壓線膠帶的貼法
出線處的絕緣
2、注意事项
▪ 胶带须拉紧包平,不可翻起刺破,不可露铜 线.最外层胶带不宜包得太紧,以免影响产品 美观.
4、引线要领
▪ 4.1.1引线长度 按工程程图要 求控制,如须 绞线,长度须 多预留10%.
套管
飛線長度
多芯線時須絞線
10~15mm 吃錫
3mm CREEPAGE(安全間隔) min
▪ 4.1.2套管须深 入挡墙3mm以 上.(如图6.5)
套管 套管
飛線長度
多芯線時須絞線
10~15mm 吃錫
3mmimn CREEPAGE(安全間隔)
定之,且可在磁芯接合处点EPOXY胶固定,点胶后须阴干半 小时再置于120℃烤箱中烘烤一小时。包磁芯之固定胶带须 使用与线包颜色相同之胶带(图纸特殊要求除外), 厂家需符 合UL规格。 ▪ NOTE: 磁芯胶带起绕处与结束处;立式起绕于PIN端中央, 结束于中央;卧式起绕 于PIN1,结束于PIN 1。有加 COPPER则起绕于焊接点,结束于焊接点。
▪ 2.1铜箔绕法除焊点处必须压平外铜箔之起 绕边应避免压在BOBBIN转角处,须自 BOBBIN的中央处起绕,以防止第二层铜箔 与第一层间因挤压刺破胶布而形成短路。
錯誤
正確
BOBBIN COPPER
BOBBIN COPPER
▪ 2.2内铜片于层间作SHIELDING绕组时,其宽度应尽 可能涵盖该层之绕线区域面积, 厚度0.025mm(1mil) 以下时两端可免倒圆角,但厚度在0.05mm(2mils)(含) 以上之铜箔时两端则需以倒圆角方式处理。
变压器工艺标准
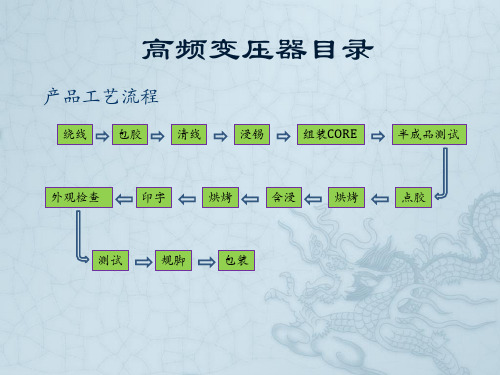
5.组装CORE
1.CORE与CORE表面不能有氧化的现象 和异物 2.两铁芯之间错位标准
CORE >15 0.5mm MAX CORE ≦15 0.3mm MAX 3.包磁芯胶带漏磁芯0.5mm MAX 4.上下层胶纸偏差标准
CORE ≧28 0.5mm MAX CORE <28 0.3mm MAX 5.点胶产品则按WI要求作业
高频变压器目录
产品工艺流程
绕线 包胶
清线
浸锡
组装CORE
半成品测试
外观检查
印字
烘烤
含浸
烘烤
点胶
测试
规脚
包装
1.材料确认 1.1BOBBIN规格确认 1.2BOBBIN分辨PIN1脚后,按要求正确插 入治具 1.3线包按照工程图纸绕制
2.绕线标准 2.1密绕允收标准
1.排线均匀紧密; 2.排线无打结,无交叉, 无重叠, 上一层无陷入下一层 现象.
2.绕线标准 2.2密绕不良现象
1.排线不均匀紧密; 2.排线出现线没有 紧密的靠在一起 3.有交叉重叠,及 有铜线陷入下一层 现象
2.绕线标准 2.3均绕
1.绕线均匀疏开
2.绕线标准 2.4均绕拒收现象
1.疏線不均勻,沒疏繞開.
2.5定位绕线
定位绕线一般分以上五种方式作业
2.6并绕方式
6.含浸凡立水
1.调好凡立水浓度:0.91±0.05。 2.含浸时间为先浸泡3分钟,在 含浸抽3分钟,再干抽3分钟, 最后摆盘烘烤 3.个别机种按WI实际要求作业 4.烘烤时间及温度按照WI实际 要求作业 5.含浸时凡立水不可以碰到PIN 脚上 6.除需要二次洗脚产品外
7.印字要求
1.在30cm以内字体可清晰易变,不会产生误判及歧意 2.不可有断字,於字,中空等现象 3.图2为不良字体 4.印字要按WI/PTS要求作业,要对齐要对应的脚位 5.标签须贴正贴平,贴完后须用手按一下,使之与产品完全接触, 歪斜最大角度CORE小于15的不可超10度,大于15的不可超10度。 6.标签不可贴错、贴反、贴歪或漏贴
变压器的工艺
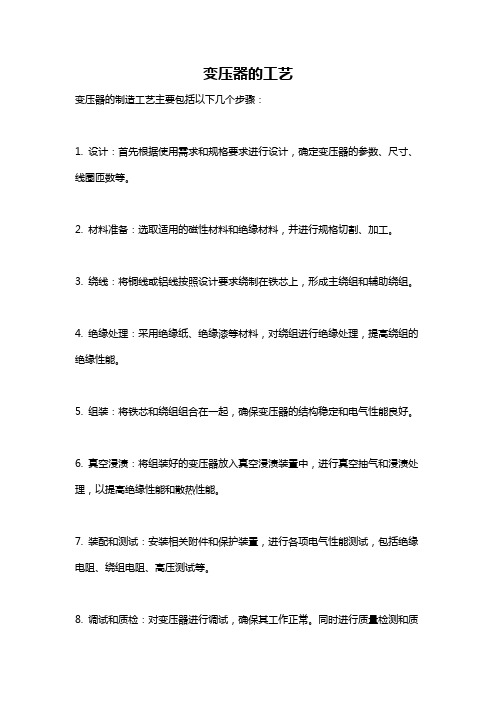
变压器的工艺
变压器的制造工艺主要包括以下几个步骤:
1. 设计:首先根据使用需求和规格要求进行设计,确定变压器的参数、尺寸、线圈匝数等。
2. 材料准备:选取适用的磁性材料和绝缘材料,并进行规格切割、加工。
3. 绕线:将铜线或铝线按照设计要求绕制在铁芯上,形成主绕组和辅助绕组。
4. 绝缘处理:采用绝缘纸、绝缘漆等材料,对绕组进行绝缘处理,提高绕组的绝缘性能。
5. 组装:将铁芯和绕组组合在一起,确保变压器的结构稳定和电气性能良好。
6. 真空浸渍:将组装好的变压器放入真空浸渍装置中,进行真空抽气和浸渍处理,以提高绝缘性能和散热性能。
7. 装配和测试:安装相关附件和保护装置,进行各项电气性能测试,包括绝缘电阻、绕组电阻、高压测试等。
8. 调试和质检:对变压器进行调试,确保其工作正常。
同时进行质量检测和质
量控制,确保产品符合标准和要求。
9. 包装和出厂:对调试合格的变压器进行包装,标明产品型号、规格和性能参数等,并按照订单要求发货出厂。
以上是一般变压器的制造工艺,不同类型的变压器可能会有一些细微的差异。
工艺的精细化和自动化程度也会随着制造技术的不断发展而不断提高。
变压器生产品质工艺标准
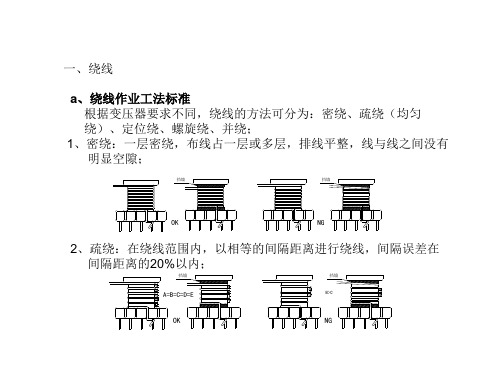
A=B=C=D=E
B>C
OK
NG
3、定位绕:布线指定在固定的位置,常用绕线方法;
4、螺旋绕:起始线紧靠TOP端打直角入槽,贴胶布盖住起始线,绕 线从TOP端向PIN端绕;
5、并绕:两根(或以上)的线同时绕线,各自平行,不可交叉;同组 或不同组多根线并绕。
6、绕线不良两次以上,此段线作废处理。绕线不良或需回线时,线要 落在工作台面以下,不可落在工作台面上,防止造成线伤; NG
c、若要求贴危险标签时,应要求贴于所规定的位置,标示 “DANGER”“HIGH VOITAGE”及其闪电符号应贴附于变压器上方中央位置,其粘贴方向朝变 压 器初级绕组为作业要求;
d、标签须贴正、贴平,不可贴错、贴歪及漏贴,贴完后用手将标签按平、按紧, 使之与产品完全接触;
八、剪脚、整脚: a、按SPEC要求,选择、剪除对应之PIN(中间抽头之PIN,一般位于初级侧), 剪切位置高于或平齐锡峰,但低于挡板(柱)或线包位置;
e、不同材质磁芯不可组装于同一产品,加材质垫GAP之材质须耐温130℃,磁 芯组合面须绝对保持清洁,否则在含浸后易导致“L”值下降。
六、含浸、烘烤: a、将凡立水加稀释剂按3:1比例调均匀(以比重或粘度为准); b、PIN脚朝上整齐摆放产品于含浸盘后,放入含浸槽内; c、启动真空含浸机,视产品无气泡溢出;
b、PIN长依SPEC为标准,一般BOBBIN在采购时即以SPEC之要求PIN长为采 购标准,即符合生产要求, 但部分代用BOBBIN的PIN会过长,须先剪脚后 进行焊锡作业,以保持PIN焊锡后留有锡尖;
c、用针咀或平咀钳将PIN脚校正、校直,再将产品PIN脚对正整脚板针孔套入,以 自由、轻松套入模板为标准;(整脚板以完全参照PCB板之PIN或远BOBBIN之 PIN位制作,且呈喇叭口形状)
高频变压器制作标准

高频变压器制作标准高频变压器是一种能够将输入的电压转换为不同电压输出的电器元件。
在现代电子设备中,高频变压器被广泛应用于各种电源和通信设备中。
为了确保高频变压器的性能稳定和安全可靠,制作过程中需要遵循一定的标准和规范。
本文将介绍高频变压器制作的一般标准,以供参考。
首先,高频变压器的制作需要选择合适的材料。
在选材时,需要考虑材料的介电常数、磁导率、损耗等因素,以确保高频变压器具有良好的电磁性能。
常见的高频变压器材料包括硅钢片、铜线、绝缘材料等。
这些材料的选择对于高频变压器的性能有着重要的影响。
其次,高频变压器的制作需要严格控制工艺流程。
在制作过程中,需要确保绕线的匝数、绝缘层的厚度、铁芯的包覆等工艺参数符合设计要求。
特别是在绕线过程中,需要保证匝间绝缘良好,绕线均匀紧密,以减小电磁损耗和焦耳热。
此外,还需要注意绕线的接线方式和焊接工艺,确保接触良好、可靠。
另外,高频变压器的制作还需要进行严格的测试和检验。
在制作完成后,需要进行绝缘电阻测试、匝间电阻测试、耐压测试等,以确保高频变压器在使用过程中不会出现绝缘击穿、匝间短路等故障。
同时,还需要进行磁通泄漏测试、温升测试等,以验证高频变压器的磁性能和热特性。
最后,高频变压器的制作需要符合相关的标准和规范。
在国内,高频变压器的制作需要符合《高频变压器制作通用技术条件》(GB/T 15288-94)等国家标准。
而在国际上,高频变压器的制作需要符合IEC等国际电工委员会的标准。
综上所述,高频变压器的制作需要选择合适的材料,严格控制工艺流程,进行严格的测试和检验,并符合相关的标准和规范。
只有在严格遵循这些标准和规范的前提下,才能制作出性能稳定、安全可靠的高频变压器,满足现代电子设备对于电源和通信的需求。
希望本文能为高频变压器制作提供一些参考和帮助。
变压器制造过程和工艺
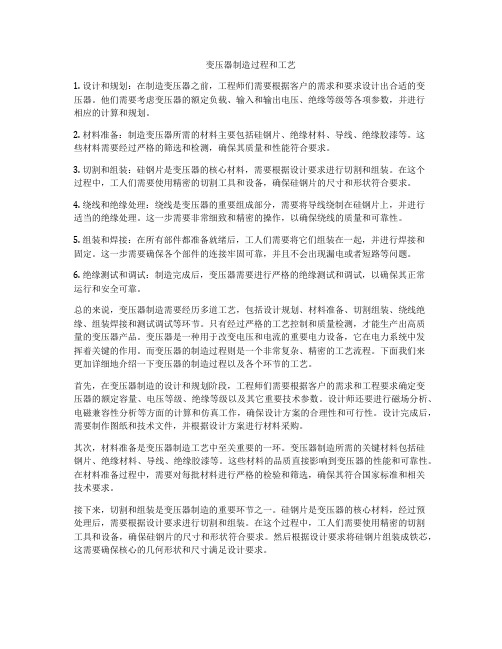
变压器制造过程和工艺1. 设计和规划:在制造变压器之前,工程师们需要根据客户的需求和要求设计出合适的变压器。
他们需要考虑变压器的额定负载、输入和输出电压、绝缘等级等各项参数,并进行相应的计算和规划。
2. 材料准备:制造变压器所需的材料主要包括硅钢片、绝缘材料、导线、绝缘胶漆等。
这些材料需要经过严格的筛选和检测,确保其质量和性能符合要求。
3. 切割和组装:硅钢片是变压器的核心材料,需要根据设计要求进行切割和组装。
在这个过程中,工人们需要使用精密的切割工具和设备,确保硅钢片的尺寸和形状符合要求。
4. 绕线和绝缘处理:绕线是变压器的重要组成部分,需要将导线绕制在硅钢片上,并进行适当的绝缘处理。
这一步需要非常细致和精密的操作,以确保绕线的质量和可靠性。
5. 组装和焊接:在所有部件都准备就绪后,工人们需要将它们组装在一起,并进行焊接和固定。
这一步需要确保各个部件的连接牢固可靠,并且不会出现漏电或者短路等问题。
6. 绝缘测试和调试:制造完成后,变压器需要进行严格的绝缘测试和调试,以确保其正常运行和安全可靠。
总的来说,变压器制造需要经历多道工艺,包括设计规划、材料准备、切割组装、绕线绝缘、组装焊接和测试调试等环节。
只有经过严格的工艺控制和质量检测,才能生产出高质量的变压器产品。
变压器是一种用于改变电压和电流的重要电力设备,它在电力系统中发挥着关键的作用。
而变压器的制造过程则是一个非常复杂、精密的工艺流程。
下面我们来更加详细地介绍一下变压器的制造过程以及各个环节的工艺。
首先,在变压器制造的设计和规划阶段,工程师们需要根据客户的需求和工程要求确定变压器的额定容量、电压等级、绝缘等级以及其它重要技术参数。
设计师还要进行磁场分析、电磁兼容性分析等方面的计算和仿真工作,确保设计方案的合理性和可行性。
设计完成后,需要制作图纸和技术文件,并根据设计方案进行材料采购。
其次,材料准备是变压器制造工艺中至关重要的一环。
变压器制造所需的关键材料包括硅钢片、绝缘材料、导线、绝缘胶漆等。
- 1、下载文档前请自行甄别文档内容的完整性,平台不提供额外的编辑、内容补充、找答案等附加服务。
- 2、"仅部分预览"的文档,不可在线预览部分如存在完整性等问题,可反馈申请退款(可完整预览的文档不适用该条件!)。
- 3、如文档侵犯您的权益,请联系客服反馈,我们会尽快为您处理(人工客服工作时间:9:00-18:30)。
(一)配电变压器技术及工艺特点
1.工艺保证:
同绕工艺绕制高压线圈是使用高速绕线机绕制的,该绕线机对导线采用机械张紧且张紧力恒定。
伺服系统是实现无极规自动控制排线,排线紧密紧凑,自动计数准确;由于高压线圈绕制过程中对导线施以拉紧和紧靠,所以高压线圈的导线是靠实的,与端绝缘之间是刚性紧挨接无压缩余量,同理,低压线圈也是如此。
所以,同绕后的相绕组的轴向高度即可保证设计尺寸(从而保证了阻抗电压的准确性)。
2.铁芯叠装:
铁芯是在气动翻转起立的叠装台上装配的,利用特制的位置定位工装,采用不叠上铁轭工艺叠码铁,铁芯夹码后夹紧下夹件,柱铁用槽钢和上夹件临时夹紧,并用C型卡具在空间辅夹柱铁;起立移动存放区涂刷固定剂,干燥固化后卸下临时卡具,转入器身装配工序。
铁芯片间结合牢固,损耗低和噪音小。
3.器身装配:
由于铁芯不带上铁轭,绕组式相单元,铁轭垫块采用模注成型的环氧树脂垫快,高压引线及分接引线的绝缘采用增强的PVC管穿套等特殊配套组合,在滚动平台流水线上进行器身绝缘和引线装配,装配速度快,质量好且清洁卫生。
4.波纹油箱
波纹油箱是利用波纹生产线中的“波纹片折叠机”,自动将规格的冷轧钢板卷料折叠成设计图纸要求的片型,包括波纹片的波纹高,节距,波纹片,直边长度及总长度和宽度。
折叠质量好速度快;波纹片折叠后进入焊接,完成折叠端缝和加强铁焊接,此焊接采用氩弧焊,焊接电弧稳定,焊缝熔深大,成型好无缺陷。
波纹油箱有箱底,箱沿,中间是波纹片组对焊接而成的长方形邮箱。
波纹片是由薄板折叠加工而成,变压器工作时除具有良好的散热性能外,波纹片的波翅还具有膨胀可缓解内部压力上升的功能。
5.技术特点:
10KV,35KV级S9,S10.S11系列配电变压器,容量范围30-3150KVA;铁芯为三相三柱式,多级阶梯圆柱型;线圈采用同绕技术,同心度好,抗短路能力强,主要技术指标达到同类产品国内先进水平。
(二)电力变压器技术及工艺特点
1.产品设计:
利用计算机对电场,磁场,温度场及冲击场进行精确的分析与计算,确定其相应的结构与设计参数,使场强和冲击梯度合理分布,漏磁通密度和梯度分布在合理范围之内,保证变压器运行安全可靠,快捷的得到质量可靠经济技术指标优良的最佳设计方案。
采用CAD计算机辅助绘图系统,使绘图准确,快捷。
易存储和高效率。
2.抗突发短路能力:
在设计上,按相应电网的短路容量,对变压器各绕组及线圈的各个部位在运行时产生的力和发生最严重突发短路时的各种轴向和辅助电磁力进行计算,确定合理结构。
在工艺制造上,采用带压紧和紧靠装置的绕线设备,既能保证线圈径向绕紧实,又能避免轴向压缩而引起径向松动,实现不留装配裕度;采用换位导线,组合导线,高电压产品的线圈采用内屏蔽代替传统的纠接式,减少故障点提高了工效。
采取绝缘件预干燥;线圈,相装配和器身装配后分别进行施加带恒压的预压力,并进行干燥。
保证线圈高度一致安匝平衡,保证线圈的抗拉,抗弯曲,抗剪切强度;同时线圈采用硬纸筒,撑条垫块加密处理,保证线圈支撑的稳定性。
能保证变压器承受各种标准规定的短路冲击而不损伤。
3.相装配:
运用特殊设备,预先进行相装配,调整每项各个线圈的电抗高度完全符合设计要求,最大限度的减少端部漏磁,降低杂散损耗和机械力。
4.干燥:
采用自动控制的干燥设备干燥线圈和机身,能够较好的实现脱水效果。
5.铁芯:
铁芯采用优质冷轧晶粒取向高导磁硅钢片,45°全斜接缝结构,运用平衡起立的叠铁工作台,采用不叠铁轭的工艺叠铁,借助C型夹具和液压千斤顶卡紧柱铁盒铁轭,进行绑扎和卡紧,芯柱采用玻璃
丝带绑扎,铁芯各级侧表面涂刷固化和防锈双重作用的聚氨酯粘合剂。
6.油箱:
桶式油箱和钟罩式油箱两种,配以片式散热器,风扇底吹式,低噪音,下料成型采用大型剪板机,滚板机,液压折弯机,自动焊机,富氩混合气体等设备,确保油箱质量。
电力变压器产品的油箱等结构件采用磷化除锈,选用优质的环氧树脂和丙烯酸树脂的涂料,采用自控热风循环干燥,多层多次涂漆,漆膜厚度大于150um,漆膜附着力好,防腐效果好,漆膜耐候和抗老化性好,漆膜饱满美观。
7.运行:
变压器的抗震,运输受力均经过严密计算,并采取了相应可靠和细致的密封处理,保证变压器在现场可免吊芯,可免维护运行。
8.降低局放:
变压器绝缘件全部进行倒圆角去毛边处理,并采用优质绝缘材料,保证纸板及其制品无异物无缺陷。
引线包扎采用加屏蔽办法,保证电极光滑。
引线连接采用焊后去尖角毛刺,油箱接地电极均进行倒圆角钝化处理。
9.防止变压器渗漏油:
所有油箱法兰均精心加工,法兰带限位槽保证密封垫的压缩量和防止滚动,密封垫采用进口胶料制作,提高胶垫的耐油,耐温及老化性能,所有组部件在厂内进行演装,并进行打压试实验,保证变压器运行不发生渗漏油。
10.降低变压器噪音:
优先推荐使用风冷和自冷的冷却方式,本产品具有自冷和风冷自动转换功能,噪音水品可低于60dB,油箱箱底加减振垫,箱壁可加装隔音板,磁通密度低于1.6特斯拉。
S9与S7:空载损耗平均下降10.25%,年运行成本平均下降18.91%。
S11与S9:空载损耗平均下降30%,年运行成本平均下降11.68%
10KV S11-M.R系列卷铁芯变压器说明:
卷铁芯全密封型配电变压器,是近几年研制的新一代低噪声、低损耗型变压器,其铁芯无接缝,较大的减少了空载损耗及空载电流,使空载电流降低60%~80%,高低压线圈在芯柱上连续绕制,绕组紧实,同心度好,更加增强了产品的防盗性能。
噪声下降10分贝以上。
温升低16-20K。
由于铁芯(横截面为纯圆形)连续卷绕,充分利用了硅钢片的取向性,使空载损耗降低了20%~30%,是新一代的高科技节能环保产品。