变压器制造工艺守则
变压器制造标准规范最新版
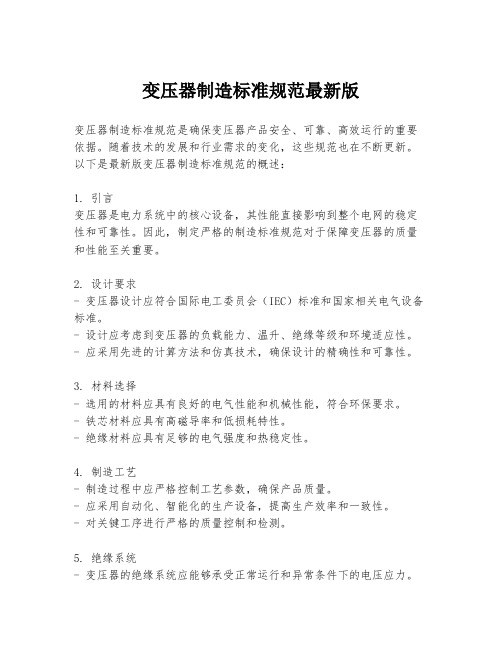
变压器制造标准规范最新版变压器制造标准规范是确保变压器产品安全、可靠、高效运行的重要依据。
随着技术的发展和行业需求的变化,这些规范也在不断更新。
以下是最新版变压器制造标准规范的概述:1. 引言变压器是电力系统中的核心设备,其性能直接影响到整个电网的稳定性和可靠性。
因此,制定严格的制造标准规范对于保障变压器的质量和性能至关重要。
2. 设计要求- 变压器设计应符合国际电工委员会(IEC)标准和国家相关电气设备标准。
- 设计应考虑到变压器的负载能力、温升、绝缘等级和环境适应性。
- 应采用先进的计算方法和仿真技术,确保设计的精确性和可靠性。
3. 材料选择- 选用的材料应具有良好的电气性能和机械性能,符合环保要求。
- 铁芯材料应具有高磁导率和低损耗特性。
- 绝缘材料应具有足够的电气强度和热稳定性。
4. 制造工艺- 制造过程中应严格控制工艺参数,确保产品质量。
- 应采用自动化、智能化的生产设备,提高生产效率和一致性。
- 对关键工序进行严格的质量控制和检测。
5. 绝缘系统- 变压器的绝缘系统应能够承受正常运行和异常条件下的电压应力。
- 应采用多层绝缘结构,提高绝缘性能和可靠性。
6. 冷却系统- 变压器应配备有效的冷却系统,以保持设备在安全的工作温度下运行。
- 冷却方式可以是自然冷却、风冷或油冷,具体取决于变压器的容量和使用环境。
7. 测试与验收- 变压器在出厂前应经过严格的测试,包括绝缘电阻测试、短路阻抗测试和温升试验等。
- 测试结果应符合设计要求和相关标准规范。
8. 安装与运行- 提供详细的安装指南和操作手册,确保变压器的正确安装和运行。
- 运行过程中应定期进行维护和检查,以延长变压器的使用寿命。
9. 环境与安全- 变压器的设计和制造应考虑到环境保护和人员安全。
- 应采取措施减少噪音和电磁干扰,确保对环境的影响降到最低。
10. 结语变压器制造标准规范的最新版旨在通过严格的设计、材料选择、制造工艺、测试与验收等环节,确保变压器产品的高性能和高可靠性。
干式变压器工艺守则箔绕线圈绕制工艺
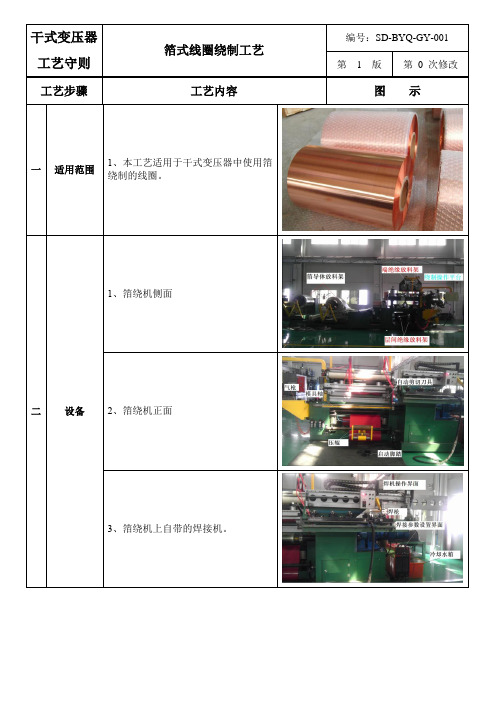
工艺步骤
箔式线圈绕制工艺 工艺内容
编号:SD-BYQ-GY-001 第 1 版 第 0 次修改
图示
一
适用范围
1、本工艺适用于干式变压器中使用箔 绕制的线圈。
1、箔绕机侧面
二 设备 2、箔绕机正面
3、箔绕机上自带的焊接机。
2、普通工具:大力钳、铁锤、胶锤、 木锤、打板、通用工具、锉刀、砂布, 扳手、绑带、铜排定位板。
7、设备和绕制场地必须经常清扫,保持清洁,减少灰尘,以保证质量。
8、注意安全操作,人离开时切断电、水、气。
1、产品尺寸符合图纸及偏差要求 七 质量要求 2、绕制紧凑无松动。
3、线圈清洁,无油污、垃圾及灰尘。标源自 处数 更改文件号 签 字日期
提出部门
编制
校对
标准化 审定 批准
30、将低压线圈平放推入固化炉内,并 随时监视固化炉内的工作情况。从常温 升温 40 分钟到 130℃,在 130℃下保温 6 小时,完全开门冷却 1 小时拉出烘炉 拆模,完全冷却后打磨,控制高度。 1、铜箔与引出排的焊接必须牢固,挫平砂光,以免变压器运行时发生局部过热。 2、铜箔两边如有菱角毛刺,必须用砂纸磨去菱角或使用压毛刺装置压平菱角。 六 注意事项 3、在整个绕制过程中防止碰坏线圈或出工伤事故。 5、线圈绕毕后应该带模横放在清洁的地方,不能竖直。 6、线圈吊运过程中一定要平稳、轻放,以免线圈变形。
24、剪断层绝缘,用粘胶带粘牢。
25、用 50mm 宽的 DMD 预浸布带半叠 包匝线圈外部。
26、DMD 预浸布带包扎效果如右图, 包扎完后用粘胶带粘牢。
27、用车架将连同模具的线圈从箔绕机 上取出。
28、用端绝缘剪下 50~100mm 不等长 的 DMD 纸带塞于端绝缘尽头缝隙处。
干式变压器工艺守则-

干式变压器工艺守则-19中山长征电气有限公司干式变压器工艺守则编号版次页次CZB-01-2022A/0共19页低压箔绕线圈绕制工艺1.适用范围本工艺使用于电压等级10kV容量200-2500kVA三相干式配电变压器及630-6300kVA三相式干式变压器低压箔式绕圈的绕制。
2.主要设备箔绕机、氩弧焊机、空压机、吊车。
2.2工装、工具线圈专用起吊工具、绕线模、工业用氩气、大力钳、小铁锤、锉刀、钢丝刷子、直角尺、橡胶锤、扳手、外卡钳、卷尺、布剪子、油性记号笔。
3.材料铜(铝)箔、铜铝排、砂布、、层绝缘、端绝缘、0.05聚酯薄膜。
4.准备工作4.1熟悉线圈图图样,明确其技术条件要求,对线圈结构的工艺难点要考虑好其操作要领。
4.2按图样备好所需材料及所用工具,检查所用设备是否正常,无误后,方可进行绕线。
4.3准备好绕线模,将低压绕线模固定在绕线轴上。
5.工艺过程5.1..在绕线模上刷一层脱模剂。
5.2.在绕线模上围上一圈0.05的聚酯薄膜。
5.3用氩弧焊焊低压内引出线铜(铝)排。
5.4拉回铜(铝)箔,将低压内引出线铜(铝)线放到绕线模槽中固定好开始绕线圈,绕制时,层间绝缘放在铜箔的下面,端绝缘放在铜箔左右两端,分别与铜(铝)箔一起同步绕制,边绕边不断地用木槌敲打端部绝缘,使端部绝缘与铜(铝)箔紧靠在一起,每绕几匝,都应随时检查线圈端面是否整齐,如有不齐,可以将绕线轴倒转进行纠正。
5.5继续按图样同步绕制铜(铝)箔、层绝缘及端绝缘,当绕制到图样要求的尺寸后,应按图样要求的位置放置气道撑板,但铜(铝)排处不放。
5.6气道撑板放好后,继续同步绕制铜(铝)箔、层绝缘及端绝缘,绕制时要求缠绕整齐、密贴、紧实。
若绕制过程中发现铜箔两边毛刺超差或有缺口,应挫掉毛刺并砂光(注意:不要使铜(铝)屑落入线圈上)。
当绕到图样规定的匝数时,在铜(铝)箔剪切的位置处用钢板尺逼着用划线刀划出剪切线,然后让开卷机反转,使划线处正对剪刀口的位置,用压辊压住线圈,按下剪切按钮将铜(铝)箔剪断。
变压器制作工艺标准及要求
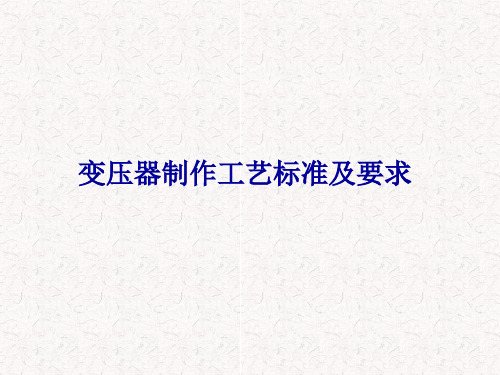
三:包胶带
▪ 包胶带的方式 ▪ 注意事项
1.包胶带的方式一般有以下几种
A.同組不同層的絕緣方法. B.不同層的絕緣方法. C.最外層的絕緣方法.
5~10mm
5mm 以 上
D.壓線膠帶的貼法
出線處的絕緣
2、注意事项
▪ 胶带须拉紧包平,不可翻起刺破,不可露铜 线.最外层胶带不宜包得太紧,以免影响产品 美观.
4、引线要领
▪ 4.1.1引线长度 按工程程图要 求控制,如须 绞线,长度须 多预留10%.
套管
飛線長度
多芯線時須絞線
10~15mm 吃錫
3mm CREEPAGE(安全間隔) min
▪ 4.1.2套管须深 入挡墙3mm以 上.(如图6.5)
套管 套管
飛線長度
多芯線時須絞線
10~15mm 吃錫
3mmimn CREEPAGE(安全間隔)
定之,且可在磁芯接合处点EPOXY胶固定,点胶后须阴干半 小时再置于120℃烤箱中烘烤一小时。包磁芯之固定胶带须 使用与线包颜色相同之胶带(图纸特殊要求除外), 厂家需符 合UL规格。 ▪ NOTE: 磁芯胶带起绕处与结束处;立式起绕于PIN端中央, 结束于中央;卧式起绕 于PIN1,结束于PIN 1。有加 COPPER则起绕于焊接点,结束于焊接点。
▪ 2.1铜箔绕法除焊点处必须压平外铜箔之起 绕边应避免压在BOBBIN转角处,须自 BOBBIN的中央处起绕,以防止第二层铜箔 与第一层间因挤压刺破胶布而形成短路。
錯誤
正確
BOBBIN COPPER
BOBBIN COPPER
▪ 2.2内铜片于层间作SHIELDING绕组时,其宽度应尽 可能涵盖该层之绕线区域面积, 厚度0.025mm(1mil) 以下时两端可免倒圆角,但厚度在0.05mm(2mils)(含) 以上之铜箔时两端则需以倒圆角方式处理。
变压器生产工艺标准

河南泰隆电力设备股份有限公司河南泰隆电力设备有限公司、▲芝文件皆导书)编制: 日期: 校准:日期: 审核:日期:2017-01-01 颁布2017-01-01 实施干式变压器生产工艺流程简图-3 -铁芯叠装工艺低压箔绕线圈绕制工艺高压分段圆筒式线圈绕制工艺-11 - 高压连续式线圈绕制工艺-16 - 环氧树脂浇注工艺-21 - 线圈真空压力浸漆工艺-24 - 环氧树脂浇注线圈工艺-27 - 干式变压器套装配工艺-34 - 电力变压器油箱制造工艺规范-42 - 电力变压器油箱试漏工艺规范-47 - 非晶变压器制造工艺规范-51 -式变压器生产工艺流程简图铁芯叠装工艺1.适用范围本工艺使用于电压等级10kV容量30 —2500KVA三相干式配电变压强及630—6300kVA三相干式电力变压器的铁芯叠装,凡结构相同的产品均可参照执行。
2.主要设备及工具 2.1主要设备铁芯叠装平台(有条件的生产厂家可选用铁芯叠装台)、吸尘器、吊车。
2.2工具槽钢、心柱支撑件、夹紧工具、料架、扳子、橡胶木槌、打平垫块、水平尺、卡尺、卷尺、钢板尺、卡钳、摇表。
3.准备工具 3.1认真仔细的查看图样,熟悉和了解铁芯结构及特点,明确图样的技术要求及操作要点。
3.2按图样备好铁芯叠装时所用的所有零部件、材料及工、量、卡具。
3.3按铁芯的重量和外型尺寸选择相应的槽钢及心柱支撑件(有条件的生产厂家可选用相应的铁芯叠装台)。
3.4布置好铁芯叠装工作台面及四周的放料位置,按铁芯叠积图吊放(或工人搬运)好铁芯片。
3.5用干净的抹布清洁上下夹件及拉板待用。
4.工艺过程 4.1铺台面 4.1.1按图样中铁心尺寸要求,在铁心叠装平台上布置好槽钢及心柱支撑件保证它们都在一个水平面上。
4.1.2铺放低压侧上下夹件及低压侧拉板,调整心柱支撑件的高度,用水平尺分别沿铁心长度方向和铁轭长度方向测量上下夹件表面的水平度,使上下夹件的表面处在同一个水平面上, 同时应保证上下夹件平行,端部对齐,对角线尺寸一致。
变压器制作工艺
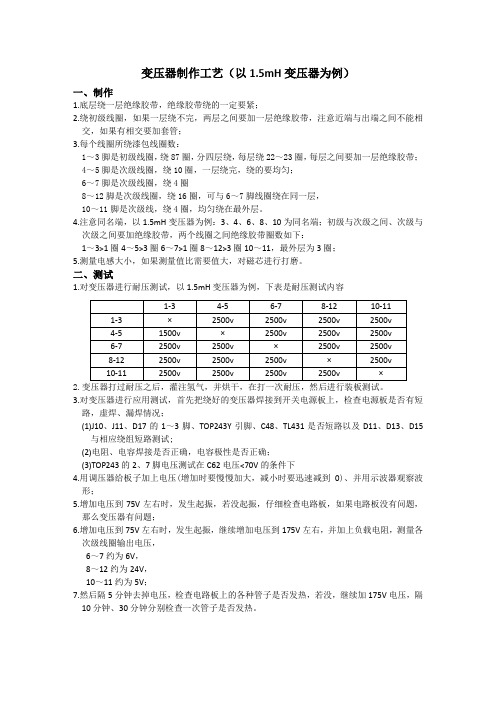
变压器制作工艺(以1.5mH变压器为例)一、制作1.底层绕一层绝缘胶带,绝缘胶带绕的一定要紧;2.绕初级线圈,如果一层绕不完,两层之间要加一层绝缘胶带,注意近端与出端之间不能相交,如果有相交要加套管;3.每个线圈所绕漆包线圈数:1~3脚是初级线圈,绕87圈,分四层绕,每层绕22~23圈,每层之间要加一层绝缘胶带;4~5脚是次级线圈,绕10圈,一层绕完,绕的要均匀;6~7脚是次级线圈,绕4圈8~12脚是次级线圈,绕16圈,可与6~7脚线圈绕在同一层,10~11脚是次级线,绕4圈,均匀绕在最外层。
4.注意同名端,以1.5mH变压器为例:3、4、6、8、10为同名端;初级与次级之间、次级与次级之间要加绝缘胶带,两个线圈之间绝缘胶带圈数如下:1~3>1圈4~5>3圈6~7>1圈8~12>3圈10~11,最外层为3圈;5.测量电感大小,如果测量值比需要值大,对磁芯进行打磨。
二、测试1.对变压器进行耐压测试,以1.5mH变压器为例,下表是耐压测试内容2.变压器打过耐压之后,灌注氢气,并烘干,在打一次耐压,然后进行装板测试。
3.对变压器进行应用测试,首先把绕好的变压器焊接到开关电源板上,检查电源板是否有短路,虚焊、漏焊情况;(1)J10、J11、D17的1~3脚、TOP243Y引脚、C48、TL431是否短路以及D11、D13、D15与相应绕组短路测试;(2)电阻、电容焊接是否正确,电容极性是否正确;(3)TOP243的2、7脚电压测试在C62电压<70V的条件下4.用调压器给板子加上电压(增加时要慢慢加大,减小时要迅速减到0)、并用示波器观察波形;5.增加电压到75V左右时,发生起振,若没起振,仔细检查电路板,如果电路板没有问题,那么变压器有问题;6.增加电压到75V左右时,发生起振,继续增加电压到175V左右,并加上负载电阻,测量各次级线圈输出电压,6~7约为6V,8~12约为24V,10~11约为5V;7.然后隔5分钟去掉电压,检查电路板上的各种管子是否发热,若没,继续加175V电压,隔10分钟、30分钟分别检查一次管子是否发热。
变压器制造工艺守则
变压器制造工艺守则Virtue carries wealth. On the morning of November 2, 2022绕组制造工艺守则①圆筒式绕组的绕制1、弯折导线始端及包扎绝缘,按图样规定的绕向和始端长度,用折弯工具将导线弯成90°;左绕向的绕组始端向右弯折,右绕向绕组始端向左弯折;折弯损坏的导线绝缘必须剥去重新包扎,用与匝绝缘相同等级的绝缘材料半叠包一层;端绝缘根部的相邻线匝应包扎100mm长的绝缘;2、800kVA以上绕组的第一匝、第二匝和最后二匝用NH纸半叠包一层;3、将端绝缘用拉紧带将其绑扎在第一匝导线上,绑扎成“S”字形;所有线匝应拉紧靠实,以保证绕组在轴向上是紧实的;4、在绕第一层线匝时,要随绕随用木锤将线匝靠紧;在绕制过程中要使导线保持一定的涨紧力,保证绕组的紧实平整;随时检查导线质量,对损坏的绝缘应及时包扎;5、两根以上导线并绕进行换位而产生的匝间空隙用匝间垫条填平,匝间垫条用绝缘带绑扎在相邻的线匝上,换位处的S弯用NOMEX绝缘纸半叠包一层,包扎长度略大于S弯长度;6、绕第一层最后一匝时,与起始端相同的办法把端绝缘均匀绑在线匝上,然后将拉紧带端头用胶粘接在撑条上并压在线匝下面,切勿脱落;当层间为气道撑条时,拉紧带必须放在气道撑条上面;7、当层间有气道撑条时,按图样规定的数量和位置沿圆周均匀放置,各撑条之间应放置临时撑条,其厚度要小于气道撑条~1mm;放置气道撑条时,要注意撑条与引出线始、尾端之间的位置;导线的升层处以撑条为中心,用0.05mm厚的NOMEX绝缘纸半叠包一层,包长50~100mm;8、无气道的多层绕组,层与层之间加垫层间绝缘纸,绝缘纸的两端应错位搭接,搭接长度为20~40mm,宽度与绕组轴向相同;9、绕线至最后,引出端按图样要求留出一定长度,剪断导线,定准引出线位置,用折弯工具将导线弯成90°,包扎引出端绝缘;10、对高压绕组的分接线引出线,弯折处均补包绝缘,包至弯折处向内10~20mm;绑牢后在分接线两侧用收紧带拉紧;11、将绕制好的绕组连同绕线模具从绕线机上卸下,吊运到绕组起立架上,将绕组竖起后移到脱模台上,侧档座朝下,要严防碰伤绕组,然后拆下档座螺栓,收缩可调绕线模,使绕组与绕线模脱离,垂直抽出绕线模即可;②连续式绕组的绕制1、将绝缘筒、绝缘端圈套在绕线模上,调节绕线模直径至绝缘筒涨紧;2、将T 型撑条均匀地绑在绝缘筒上并穿上相应的燕尾垫块;3、线匝为单根、整数匝,绕线引出端在外侧,左绕正接时的连续式绕组的绕制;a 第一段为反段;首先将导线的始端固定在绕线模上;调整导线涨力,起动绕线机;根据设计要求和匝数绕成一个临时线段,折换位S弯,在S弯处要半叠包一层与导线相同等级的绝缘,其长度每端长出S弯10~15mm;将临时线段的最后一匝移置到撑条上,将其成正式反段的最内一匝;然后依次将其余的线匝移置到第一匝的上面;最后将线段移到并靠近线模的挡板旁,用力反向拉紧打实,用绝缘带将引出线与线段绑牢;b 放置第一段与第二段之间的气道燕尾垫片,垫好临时撑条,开始绕制正段;其涨力略小于反段涨力,边绕边用手锤打板将线段靠紧打实;绕好最后一匝时,按图样规定弯折导线S换位弯;c 放置段间气道燕尾垫块;反段绕制必须将导线从前一正段上面用临时楔形垫将导线引渡下来,放置在撑条上绕一个临时线段;为防止导线从正段上拉下散落,应在绕好正段的换位S弯处用布带扎牢或用∩形夹固定;绕好最后一匝弯折导线内部换位S弯;内部换位S 弯的包扎与外部换位S弯相同;d 将临时线段的最后一匝移置到撑条上,使内部换位的位置处在图样规定的撑条间隔内,但应稍落后一些,以便于移置后面的各匝;导线要边移边拉紧;移完最后一匝,将整个线段移动靠紧前一段;在推动反段时,要用∩形夹或布带将线段卡紧扎实,防止线段松散;用力逆向旋转线段,将线段拉紧,然后用力拉一下导线,以涨紧内部换位的导线;用手锤打板将线段间靠紧打实;4、两根及以上导线并绕的连续式绕组连续式绕组的线匝由两根以上导线并绕时,从一个线段到另一个线段的过渡方式与单根导线的绕制相同,但在进行多根导线过渡时,要交换导线的位置,将最上面的一根导线放到最下面去,最下面的一根导线换到上面的位置上;如此类推;多根导线并绕的连续式绕组与单根导线绕制的不同处:a 线段的起点,即计算匝数的起始点不同;两根导线并绕时,以任意一根导线的内部换位位置计算匝数的起始点;三根并绕导线并绕以中间一根导线内部换位位置为计算匝数的起始点;四根以中间两根为起始点,其余类推;b 弯折内部换位S弯时,必须先弯下边一根导线,再依次弯折其余导线;弯折外部换位S弯时,必须先弯折最上面的一根导线,再依次弯折其余导线;c 从第二个反段开始,所有临时线段绕制时,都必须利用楔形垫将导线由正段上引渡到撑条上;不论反段或正段绕制第一匝时,都必须垫与撑条相同厚度的临时垫条,临时段绕好后弯折换位S弯,包扎换位导线绝缘,并在已绕好的相邻的正段上做出反段换位位置标记;d 因换位松动的匝间间隙不能超过1mm,并用~1 mm垫条塞紧;e 分接头在线段外侧沿径向引出时,必须与换位处隔一根撑条,分接头及尾端的绑扎与绝缘包扎方法与始端相同;5、绕制完毕,套上下端的绝缘端圈并固定;6、将绕制好的绕组连同绕线模具从绕线机上卸下,吊运到绕组起立架上,将绕组竖起移到脱模台上,侧档座朝下,然后拆下档座螺栓,收缩可调绕线模,使绕组与绕线模脱离,垂直抽出绕线模即可;③箔式绕组的绕制1、始端引线的焊接1将焊接台运行到合适位置;2用固定钳将铜箔带与铜排压在焊接台上,铜排与铜箔带垂直;接缝要严密;具体焊接工艺过程按钨极亚弧焊机操作说明书进行;3引线焊好后将焊机退回原位;清除焊点焊瘤;2、绕首匝1先绕二层层间绝缘,不放端绝缘;2将铜箔带端头固定在绕线模上,并整好两端端绝缘;3、绕第二匝之前,在铜排引线上盖三张层间绝缘纸,其长度为绕组的高度,宽度为铜排宽度的2倍,中心线与引线中心线重合;同时按要求绕上端绝缘及层间绝缘,端头用胶带粘紧;4、同步绕制铜箔、层间绝缘及端绝缘到气道;5、将撑条插入铜箔下面,慢速转动卷绕机,使气道边缘与端绝缘平行,如有多层气道,上撑条应与下撑条对齐;气道撑条的垫放应平等均匀;6、继续同步绕制直至最后一匝;7、绕制完后,在需切割的箔带位置上划上记号,驱动开卷机使铜箔带退到剪切位置;8、将卷绕机压紧辊压在绕组上,切断铜箔,按图样焊好末端引线;9、在引线下面垫三张层间绝缘纸,其长度为绕组的高度,宽度为铜排宽度的2倍,中心线与引线中心线重合;10、在绕组外部绕三层层间绝缘纸,然后切断,用胶带粘紧,并用60mm宽的层间绝缘纸半叠包扎一层,包时应用力拉紧;11、绕组绕好后,用专用卸料车将绕组连绕线模从绕线机上取下绕组浸漆、干燥工艺守则1、绕组的整理①夹具夹紧绕组,撑条必须垂直,不可有松动现象,绕组不可倾斜;②将修整压装后的绕组清理浮尘,垂直放入烘箱内,绕组与加热器要保持足够的距离,一般不小于300mm,防止因局部过热而损坏绕组绝缘;2、预烘检查风道、组间距离等各部分正常后,关闭烘箱进行干燥处理;烘箱逐渐升温至130℃;130±5℃干燥4~5小时,待干燥过程结束后,烘箱停止加热,当绕组降至90℃以下,绕组出烘箱;3、浸漆①取出干燥后的绕组,重新检查整理撑条、垫块及绕组轴向高度,调整夹紧螺母,使其符合图样要求;②将绕组上端引出线向上竖起,尽量减小引出端的浸漆长度;③待绕组冷却到<50℃时,将绕组吊入浸漆罐中,浸渍时间不少于30min;4、滴漆把绕组从漆罐中吊起进行滴漆,滴漆时间不少于30min;滴漆后的绕组如有漆瘤,应用刮板将其轻轻刮掉,以保证漆膜光滑平整;滴漆过程中注意防尘;5、浸漆后干燥①绕组入烘箱时,烘箱温度必须在165±5℃, 干燥3~4小时;②绕组出炉时,以漆膜完全干燥为合格;否则要延长干燥时间,直至烘干;6、然后再重复过程3、4、5一遍,即绕组浸漆、烘干两遍;器身装配工艺守则1、铁芯烘干;将铁芯送入烘箱,逐渐升温至130℃;130℃±5℃恒温4小时后出炉,拆除固定用夹件,铁芯温度降到50℃以下,开始刷铁芯漆,上铁轭暂时不刷,待装配完后再刷;2、绕组套装;①拆除待装铁芯的上铁轭,并分级摆放在铁心架上;②按图样要求放置端部隔板、绝缘垫块、绝缘板;③按绕组相序编号,选择心柱的套装位置;④按引出线方向调整绕组的位置;绕组应与铁轭垂直,与心柱同心;⑤靠绕组边垫绝缘板,插入气道撑条;撑条应自然插入绕组高度的1/2,其余部分用木锤打入;3、插上铁轭按铁芯级别顺序插上铁轭;有穿芯螺孔的要边插边校对孔的中心;4、铁心夹紧①按图纸要求放置上部绝缘垫块、接地片;②上夹紧装置,紧固夹紧螺栓;③按图样要求放置相间隔板;5、焊接高低压引线将器身非焊部分的绝缘用湿布包好,按图样焊接高压电缆引线、低压铜排或电缆引线;焊后立即用干净水浇焊点,使焊点快速冷却;去湿布,用风动砂轮打掉高点和毛刺;用聚酰亚胺薄膜带将焊接处包扎,最后将包扎处涂一遍无溶剂绝缘漆;6、安装高低压引线夹、分接板、绝缘子等其它固定件;旋紧各导电杆螺母;7、干燥:清洁器身表面,送入烘箱进行干燥处理,烘箱温度控制在130℃±5℃、4小时;出炉后待器身冷却到50℃以下,将上铁轭刷上黑涂料;。
变压器制作工艺标准
变压器制作工艺标准(一)配电变压器技术及工艺特点1.工艺保证:同绕工艺绕制高压线圈是使用高速绕线机绕制的,该绕线机对导线采用机械张紧且张紧力恒定。
伺服系统是实现无极规自动控制排线,排线紧密紧凑,自动计数准确;由于高压线圈绕制过程中对导线施以拉紧和紧靠,所以高压线圈的导线是靠实的,与端绝缘之间是刚性紧挨接无压缩余量,同理,低压线圈也是如此。
所以,同绕后的相绕组的轴向高度即可保证设计尺寸(从而保证了阻抗电压的准确性)。
2.铁芯叠装:铁芯是在气动翻转起立的叠装台上装配的,利用特制的位置定位工装,采用不叠上铁轭工艺叠码铁,铁芯夹码后夹紧下夹件,柱铁用槽钢和上夹件临时夹紧,并用C型卡具在空间辅夹柱铁;起立移动存放区涂刷固定剂,干燥固化后卸下临时卡具,转入器身装配工序。
铁芯片间结合牢固,损耗低和噪音小。
3.器身装配:由于铁芯不带上铁轭,绕组式相单元,铁轭垫块采用模注成型的环氧树脂垫快,高压引线及分接引线的绝缘采用增强的PVC管穿套等特殊配套组合,在滚动平台流水线上进行器身绝缘和引线装配,装配速度快,质量好且清洁卫生。
4.波纹油箱波纹油箱是利用波纹生产线中的“波纹片折叠机”,自动将规格的冷轧钢板卷料折叠成设计图纸要求的片型,包括波纹片的波纹高,节距,波纹片,直边长度及总长度和宽度。
折叠质量好速度快;波纹片折叠后进入焊接,完成折叠端缝和加强铁焊接,此焊接采用氩弧焊,焊接电弧稳定,焊缝熔深大,成型好无缺陷。
波纹油箱有箱底,箱沿,中间是波纹片组对焊接而成的长方形邮箱。
波纹片是由薄板折叠加工而成,变压器工作时除具有良好的散热性能外,波纹片的波翅还具有膨胀可缓解内部压力上升的功能。
5.技术特点:10KV,35KV级S9,S10.S11系列配电变压器,容量范围30-3150KVA;铁芯为三相三柱式,多级阶梯圆柱型;线圈采用同绕技术,同心度好,抗短路能力强,主要技术指标达到同类产品国内先进水平。
(二)电力变压器技术及工艺特点1.产品设计:利用计算机对电场,磁场,温度场及冲击场进行精确的分析与计算,确定其相应的结构与设计参数,使场强和冲击梯度合理分布,漏磁通密度和梯度分布在合理范围之内,保证变压器运行安全可靠,快捷的得到质量可靠经济技术指标优良的最佳设计方案。
变压器工艺流程及要求
变压器工艺流程及要求一、变压器的工艺流程变压器是一种将电能从一个电路传递到另一个电路时改变电压的设备。
它主要由铁芯、线圈和绝缘材料等组成。
变压器的制造过程一般可分为以下几个工艺流程。
1.材料准备:根据设计要求,选用合适的铁芯材料和线圈材料。
铁芯材料一般选择硅钢片,线圈材料一般为漆包线。
绝缘材料可以选择纸板、胶带等。
2.铁芯制造:将铁芯材料切割成合适的尺寸,进行压扁、角度切割等加工工艺,以保证铁芯的形状和尺寸符合设计要求。
3.绕线:将漆包线缠绕在铁芯上,分别制作出高压绕组和低压绕组。
绕制时要注意线圈的匝数、层数等参数,以保证后续电性能的要求。
4.绝缘:将绝缘材料覆盖在绕组上,以增加线圈的绝缘强度和耐电压能力。
绝缘材料要选择合适的厚度和质量,并采用适当的固定和粘合工艺。
5.组合装配:将高压绕组和低压绕组依次放置在合适的位置上,通过螺栓和螺母进行固定连接。
同时,对绕组和铁芯进行定位调整,以确保变压器的结构和尺寸符合设计要求。
6.绕组连接:根据设计要求,将绕组上的引线通过连接板连接到端子上,形成输入输出电路。
在连接的过程中,要注意引线的长度和间距,以确保电压和电流的稳定输出。
7.清洁和包装:对变压器进行清洁和外观除尘处理,以保证产品的外观质量。
然后进行包装和标识,方便运输和使用。
二、变压器的工艺要求为了保证变压器产品的质量和性能,工艺上需要满足一些要求。
1.材料要求:各种材料的选择要符合标准要求,如铁芯材料要选用低磁导率的硅钢片,线圈材料要选用电阻低、绝缘性能好的漆包线。
2.尺寸要求:变压器的尺寸要与设计要求一致,以保证其结构的稳定性和安装的便捷性。
3.绕制要求:线圈的绕制要按照设计要求进行,匝数、层数等参数要精确控制,以免影响变压器的电性能。
4.绝缘要求:绝缘材料要具有足够的厚度和质量,以保证变压器的绝缘强度和耐电压能力,防止电击和泄漏。
5.连接要求:绕组的引线连接要牢固可靠,接触电阻低,并注意引线的长度和间距,以免产生过大的电阻和电压降。
变压器工艺流程及要求
节能环保型变压器的研究与应用
总结词
随着对节能和环保的重视,节能环保 型变压器成为研究的热点,旨在降低 运行过程中的能耗和减少对环境的影 响。
详细描述
节能环保型变压器通常采用更高效的 冷却方式和材料,以减少散热损失和 环境温度的影响。同时,采用环保材 料和工艺,以降低对环境的影响。
智能化变压器的探索与推广
振动测试和冲击测试用于检测变压器在运输和使用过程中承受振动和冲击的能力 ,而短路测试则用于检测变压器在短路故障发生时的承受能力。这些测试的结果 能够反映出变压器的机械稳定性和可靠性。
环境适应性测试
总结词
环境适应性测试是评估变压器在不同环境条件下的性能表现的重要环节,包括温升试验、湿度试验、盐雾试验等 。
详细描述
温升试验用于检测变压器在正常工作条件下的最高温升,以验证其散热性能;湿度试验用于检测变压器在高湿度 环境下的性能表现;盐雾试验则用于检测变压器在沿海地区等盐雾环境下的耐腐蚀性能。这些测试能够确保变压 器在不同环境条件下能够稳定可靠地运行。
05 变压器维护与保养
CHAPTER
日常维护
每日检查
详细描述
电气性能测试主要包括绝缘电阻测试、耐压测试、空载电流和空载损耗测试、 负载电流和负载损耗测试等。这些测试能够检测出变压器在正常工作条件下的 性能表现,以及在异常情况下的安全性能。
机械性能测试
总结词
机械性能测试是评估变压器承受机械应力的能力的重要手段,包括振动测试、冲 击测试和短路测试等。
详细描述
电力变压器
用于电力系统中的电压升降和 系统隔离。
音频变压器
用于音频信号的传输和阻抗匹 配。
测量变压器
用于高电压、大电流的测量 和 校验。
- 1、下载文档前请自行甄别文档内容的完整性,平台不提供额外的编辑、内容补充、找答案等附加服务。
- 2、"仅部分预览"的文档,不可在线预览部分如存在完整性等问题,可反馈申请退款(可完整预览的文档不适用该条件!)。
- 3、如文档侵犯您的权益,请联系客服反馈,我们会尽快为您处理(人工客服工作时间:9:00-18:30)。
绕组制造工艺守则①圆筒式绕组的绕制1、弯折导线始端及包扎绝缘,按图样规定的绕向和始端长度,用折弯工具将导线弯成90°。
左绕向的绕组始端向右弯折,右绕向绕组始端向左弯折。
折弯损坏的导线绝缘必须剥去重新包扎,用与匝绝缘相同等级的绝缘材料半叠包一层。
端绝缘根部的相邻线匝应包扎100mm长的绝缘。
2、800kV A以上绕组的第一匝、第二匝和最后二匝用NH纸半叠包一层。
3、将端绝缘用拉紧带将其绑扎在第一匝导线上,绑扎成“S”字形。
所有线匝应拉紧靠实,以保证绕组在轴向上是紧实的。
4、在绕第一层线匝时,要随绕随用木锤将线匝靠紧。
在绕制过程中要使导线保持一定的涨紧力,保证绕组的紧实平整。
随时检查导线质量,对损坏的绝缘应及时包扎。
5、两根以上导线并绕进行换位而产生的匝间空隙用匝间垫条填平,匝间垫条用绝缘带绑扎在相邻的线匝上,换位处的S弯用NOMEX 绝缘纸半叠包一层,包扎长度略大于S弯长度。
6、绕第一层最后一匝时,与起始端相同的办法把端绝缘均匀绑在线匝上,然后将拉紧带端头用胶粘接在撑条上并压在线匝下面,切勿脱落。
当层间为气道撑条时,拉紧带必须放在气道撑条上面。
7、当层间有气道撑条时,按图样规定的数量和位置沿圆周均匀放置,各撑条之间应放置临时撑条,其厚度要小于气道撑条~1mm。
放置气道撑条时,要注意撑条与引出线始、尾端之间的位置。
导线的升层处以撑条为中心,用0.05mm厚的NOMEX绝缘纸半叠包一层,包长50~100mm。
8、无气道的多层绕组,层与层之间加垫层间绝缘纸,绝缘纸的两端应错位搭接,搭接长度为20~40mm,宽度与绕组轴向相同。
9、绕线至最后,引出端按图样要求留出一定长度,剪断导线,定准引出线位置,用折弯工具将导线弯成90°,包扎引出端绝缘。
10、对高压绕组的分接线引出线,弯折处均补包绝缘,包至弯折处向内10~20mm。
绑牢后在分接线两侧用收紧带拉紧。
11、将绕制好的绕组连同绕线模具从绕线机上卸下,吊运到绕组起立架上,将绕组竖起后移到脱模台上,侧档座朝下,要严防碰伤绕组,然后拆下档座螺栓,收缩可调绕线模,使绕组与绕线模脱离,垂直抽出绕线模即可。
②连续式绕组的绕制1、将绝缘筒、绝缘端圈套在绕线模上,调节绕线模直径至绝缘筒涨紧。
2、将T 型撑条均匀地绑在绝缘筒上并穿上相应的燕尾垫块。
3、线匝为单根、整数匝,绕线引出端在外侧,左绕正接时的连续式绕组的绕制。
a) 第一段为反段。
首先将导线的始端固定在绕线模上。
调整导线涨力,起动绕线机。
根据设计要求和匝数绕成一个临时线段,折换位S 弯,在S弯处要半叠包一层与导线相同等级的绝缘,其长度每端长出S 弯10~15mm。
将临时线段的最后一匝移置到撑条上,将其成正式反段的最内一匝。
然后依次将其余的线匝移置到第一匝的上面。
最后将线段移到并靠近线模的挡板旁,用力反向拉紧打实,用绝缘带将引出线与线段绑牢。
b) 放置第一段与第二段之间的气道(燕尾)垫片,垫好临时撑条,开始绕制正段。
其涨力略小于反段涨力,边绕边用手锤打板将线段靠紧打实。
绕好最后一匝时,按图样规定弯折导线S换位弯。
c) 放置段间气道燕尾垫块。
反段绕制必须将导线从前一正段上面用临时楔形垫将导线引渡下来,放置在撑条上绕一个临时线段。
为防止导线从正段上拉下散落,应在绕好正段的换位S弯处用布带扎牢或用∩形夹固定。
绕好最后一匝弯折导线内部换位S弯。
内部换位S弯的包扎与外部换位S弯相同。
d) 将临时线段的最后一匝移置到撑条上,使内部换位的位置处在图样规定的撑条间隔内,但应稍落后一些,以便于移置后面的各匝。
导线要边移边拉紧。
移完最后一匝,将整个线段移动靠紧前一段。
在推动反段时,要用∩形夹或布带将线段卡紧扎实,防止线段松散。
用力逆向旋转线段,将线段拉紧,然后用力拉一下导线,以涨紧内部换位的导线。
用手锤打板将线段间靠紧打实。
4、两根及以上导线并绕的连续式绕组连续式绕组的线匝由两根以上导线并绕时,从一个线段到另一个线段的过渡方式与单根导线的绕制相同,但在进行多根导线过渡时,要交换导线的位置,将最上面的一根导线放到最下面去,最下面的一根导线换到上面的位置上。
如此类推。
多根导线并绕的连续式绕组与单根导线绕制的不同处:a) 线段的起点,即计算匝数的起始点不同。
两根导线并绕时,以任意一根导线的内部换位位置计算匝数的起始点;三根并绕导线并绕以中间一根导线内部换位位置为计算匝数的起始点;四根以中间两根为起始点,其余类推。
b) 弯折内部换位S弯时,必须先弯下边一根导线,再依次弯折其余导线。
弯折外部换位S弯时,必须先弯折最上面的一根导线,再依次弯折其余导线。
c) 从第二个反段开始,所有临时线段绕制时,都必须利用楔形垫将导线由正段上引渡到撑条上。
不论反段或正段绕制第一匝时,都必须垫与撑条相同厚度的临时垫条,临时段绕好后弯折换位S弯,包扎换位导线绝缘,并在已绕好的相邻的正段上做出反段换位位置标记。
d) 因换位松动的匝间间隙不能超过1mm,并用~1 mm垫条塞紧。
e) 分接头在线段外侧沿径向引出时,必须与换位处隔一根撑条,分接头及尾端的绑扎与绝缘包扎方法与始端相同。
5、绕制完毕,套上下端的绝缘端圈并固定。
6、将绕制好的绕组连同绕线模具从绕线机上卸下,吊运到绕组起立架上,将绕组竖起移到脱模台上,侧档座朝下,然后拆下档座螺栓,收缩可调绕线模,使绕组与绕线模脱离,垂直抽出绕线模即可。
③箔式绕组的绕制1、始端引线的焊接1)将焊接台运行到合适位置。
2)用固定钳将铜箔带与铜排压在焊接台上,铜排与铜箔带垂直。
接缝要严密。
具体焊接工艺过程按《钨极亚弧焊机操作说明书》进行。
3)引线焊好后将焊机退回原位。
清除焊点焊瘤。
2、绕首匝1)先绕二层层间绝缘,不放端绝缘。
2)将铜箔带端头固定在绕线模上,并整好两端端绝缘。
3、绕第二匝之前,在铜排引线上盖三张层间绝缘纸,其长度为绕组的高度,宽度为铜排宽度的2倍,中心线与引线中心线重合。
同时按要求绕上端绝缘及层间绝缘,端头用胶带粘紧。
4、同步绕制铜箔、层间绝缘及端绝缘到气道。
5、将撑条插入铜箔下面,慢速转动卷绕机,使气道边缘与端绝缘平行,如有多层气道,上撑条应与下撑条对齐。
气道撑条的垫放应平等均匀。
6、继续同步绕制直至最后一匝。
7、绕制完后,在需切割的箔带位置上划上记号,驱动开卷机使铜箔带退到剪切位置。
8、将卷绕机压紧辊压在绕组上,切断铜箔,按图样焊好末端引线。
9、在引线下面垫三张层间绝缘纸,其长度为绕组的高度,宽度为铜排宽度的2倍,中心线与引线中心线重合。
10、在绕组外部绕三层层间绝缘纸,然后切断,用胶带粘紧,并用60mm宽的层间绝缘纸半叠包扎一层,包时应用力拉紧。
11、绕组绕好后,用专用卸料车将绕组连绕线模从绕线机上取下绕组浸漆、干燥工艺守则1、绕组的整理①夹具夹紧绕组,撑条必须垂直,不可有松动现象,绕组不可倾斜。
②将修整压装后的绕组清理浮尘,垂直放入烘箱内,绕组与加热器要保持足够的距离,一般不小于300mm,防止因局部过热而损坏绕组绝缘。
2、预烘检查风道、组间距离等各部分正常后,关闭烘箱进行干燥处理。
烘箱逐渐升温至130℃。
130±5℃干燥4~5小时,待干燥过程结束后,烘箱停止加热,当绕组降至90℃以下,绕组出烘箱。
3、浸漆①取出干燥后的绕组,重新检查整理撑条、垫块及绕组轴向高度,调整夹紧螺母,使其符合图样要求。
②将绕组上端引出线向上竖起,尽量减小引出端的浸漆长度。
③待绕组冷却到<50℃时,将绕组吊入浸漆罐中,浸渍时间不少于30min。
4、滴漆把绕组从漆罐中吊起进行滴漆,滴漆时间不少于30min。
滴漆后的绕组如有漆瘤,应用刮板将其轻轻刮掉,以保证漆膜光滑平整。
滴漆过程中注意防尘。
5、浸漆后干燥①绕组入烘箱时,烘箱温度必须在165±5℃,干燥3~4小时。
②绕组出炉时,以漆膜完全干燥为合格。
否则要延长干燥时间,直至烘干。
6、然后再重复过程3、4、5一遍,即绕组浸漆、烘干两遍。
器身装配工艺守则1、铁芯烘干。
将铁芯送入烘箱,逐渐升温至130℃。
130℃±5℃恒温4小时后出炉,拆除固定用夹件,铁芯温度降到50℃以下,开始刷铁芯漆,上铁轭暂时不刷,待装配完后再刷。
2、绕组套装。
①拆除待装铁芯的上铁轭,并分级摆放在铁心架上。
②按图样要求放置端部隔板、绝缘垫块、绝缘板。
③按绕组相序编号,选择心柱的套装位置。
④按引出线方向调整绕组的位置。
绕组应与铁轭垂直,与心柱同心。
⑤靠绕组边垫绝缘板,插入气道撑条。
撑条应自然插入绕组高度的1/2,其余部分用木锤打入。
3、插上铁轭按铁芯级别顺序插上铁轭。
有穿芯螺孔的要边插边校对孔的中心。
4、铁心夹紧①按图纸要求放置上部绝缘垫块、接地片。
②上夹紧装置,紧固夹紧螺栓。
③按图样要求放置相间隔板。
5、焊接高低压引线将器身非焊部分的绝缘用湿布包好,按图样焊接高压电缆引线、低压铜排(或电缆引线)。
焊后立即用干净水浇焊点,使焊点快速冷却。
去湿布,用风动砂轮打掉高点和毛刺。
用聚酰亚胺薄膜带将焊接处包扎,最后将包扎处涂一遍无溶剂绝缘漆。
6、安装高低压引线夹、分接板、绝缘子等其它固定件。
旋紧各导电杆螺母。
7、干燥:清洁器身表面,送入烘箱进行干燥处理,烘箱温度控制在130℃±5℃、4小时。
出炉后待器身冷却到50℃以下,将上铁轭刷上黑涂料。