多变量耦合系统中文
第四章多变量控制系统-PPT全文编辑修改

u1 D21(s)
G11(s)
y1
G21(s)
r2
Gc2(s)
uc2
D12(s) u2
G12(s)
G22(s)
y2
前馈解耦原理:使y1与uc2无关联;使y2与uc1无关联
4、5 MIMO系统得解耦设计
• 前馈补偿法
uD1 21uD112uu22uuc1c2
u1 u2
1
1 D21D12
1 D21
4、5 MIMO系统得解耦设计
解耦控制得目得
解耦系统得目得就是寻求适当得控制律,使输入输出相互 关联得多变量系统实现每一个输出仅受相应得一个输入 所控制,每一个输入也仅能控制相应得一个输出,以此构 成独立得单回路控制系统,获得满意得控制性能。
解耦控制得先行工作
• 控制变量与被控参数得配对 • 部分解耦:即有选择性得解耦,在选择时可根据被控参
4、4 耦合测度与配对规则
u1(s)
y1(s)
u2(s) .
MIMO
y2(s) .
..
过程
..
un(s)
yn(s)
有无规则? 如何评价?
u1(s)
y1(s)
u2(s)
y2(s)
...
...
un(s)
yn(s)
配对规则 耦合测度
4、4 耦合测度与配对规则
以TITO系统为例:
u1(s) u2(s)
y1(s) y2(s)
4、2 MIMO系统得稳定性分析
MIMO传递函数模型为
其中
Y s GsU s Gd sds
g11s g12 s g1m s
d11s d12 s d1k s
G
灾害多变量耦合技术_解释说明以及概述
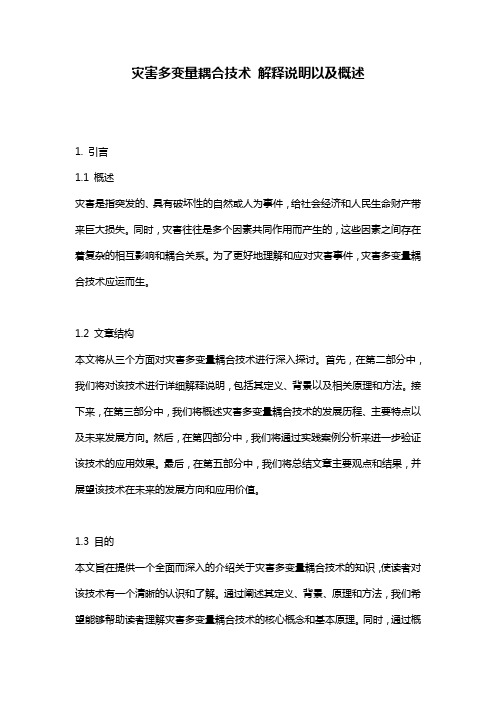
灾害多变量耦合技术解释说明以及概述1. 引言1.1 概述灾害是指突发的、具有破坏性的自然或人为事件,给社会经济和人民生命财产带来巨大损失。
同时,灾害往往是多个因素共同作用而产生的,这些因素之间存在着复杂的相互影响和耦合关系。
为了更好地理解和应对灾害事件,灾害多变量耦合技术应运而生。
1.2 文章结构本文将从三个方面对灾害多变量耦合技术进行深入探讨。
首先,在第二部分中,我们将对该技术进行详细解释说明,包括其定义、背景以及相关原理和方法。
接下来,在第三部分中,我们将概述灾害多变量耦合技术的发展历程、主要特点以及未来发展方向。
然后,在第四部分中,我们将通过实践案例分析来进一步验证该技术的应用效果。
最后,在第五部分中,我们将总结文章主要观点和结果,并展望该技术在未来的发展方向和应用价值。
1.3 目的本文旨在提供一个全面而深入的介绍关于灾害多变量耦合技术的知识,使读者对该技术有一个清晰的认识和了解。
通过阐述其定义、背景、原理和方法,我们希望能够帮助读者理解灾害多变量耦合技术的核心概念和基本原理。
同时,通过概述其发展历程、特点和未来发展方向,我们将揭示该技术在应对灾害事件中的重要作用和前景。
最后,通过实践案例分析,我们将进一步验证该技术的实际应用效果,并为读者提供更加具体和实用的参考。
2. 灾害多变量耦合技术解释说明:2.1 定义和背景:灾害多变量耦合技术是一种综合利用多个指标参数进行灾害评估和预测的方法。
传统的灾害评估方法通常只考虑单一因素对灾害形成和发展的影响,无法全面准确地预测灾情。
而灾害多变量耦合技术则通过对多个相关因素之间的关联性和相互作用进行分析,实现了对复杂自然灾害事件及其潜在风险的全面评估。
2.2 原理和方法:在灾害多变量耦合技术中,针对不同的自然灾害类型,可以选择适应性强、信息获取便捷且具有代表性的指标参数进行分析。
这些指标参数可以包括气象数据、地质地貌数据、水文数据等。
通过数学统计、模型推演等方法,对这些指标参数之间的相互关系进行建模分析,得出各个因素对于某一特定自然灾害事件发生概率或程度的影响。
锅炉解耦

(1)经典解耦控制方法; (2)自适应解耦控制方法; (3)模糊解耦控制方法; (4)反馈线性化解耦控制方法。
经典解耦控制方法 对角矩 串联解耦 三角矩 前状态补偿 前馈解耦 反馈补偿
解耦实例------锅炉温度的解耦控制 锅炉温度的解耦控ቤተ መጻሕፍቲ ባይዱ 解耦实例
(1)微型锅炉、纯滞后系统、热 微型锅炉、纯滞后系统、 微型锅炉 电耦 (2)电动调节阀 电动调节阀 (3)变频器 变频器
模拟锅炉温度的解耦控制
解耦: 解耦
变量之间相互干涉的现象称为耦合。 消除这种耦合称为解耦。
多变量系统( 系统) 多变量系统(MIMO系统) 系统
切断相互关 系
MIMO系统的特殊性在于: 系统的特殊性在于: 系统的特殊性在于
(1)输入输出之间彼此响应产生交连; (2)难以得到精确的数学模型; (3)控制部件失效的可能性增大。
以上问题的存在使得采用单变量系统的设计方 无法满足要求, 法已无法满足要求 法已无法满足要求,但单变量控制在工业上的应用 已经发展得相当成熟,因此, 已经发展得相当成熟,因此,将多变量系统解耦为 单变量系统再进行控制无疑是能够利用已有成果的 单变量系统再进行控制无疑是能够利用已有成果的 最好选择。 最好选择。
解耦前系统
解耦后系统
解耦
…
…
…
…
相互影响
…
一一对应, 一一对应,互不影响
…
单变量控制技术很成熟
独立控制
独立控制
独立控制
独立控制
解决了复杂的耦合控制问题, 解决了复杂的耦合控制问题,简单化控制
解耦作用是显而易见的 关键是如何解耦? 关键是如何解耦?
多变量系统的解耦控制可分为四大类: 多变量系统的解耦控制可分为四大类:
多变量耦合系统的辨识方法

多变量耦合系统的辨识方法深入探讨多变量耦合系统的辨识方法在现代科学与工程领域,多变量耦合系统的研究和辨识已经成为了一个重要的研究方向。
这些系统通常涉及到多个相互影响的变量,其复杂性和动态特性使得辨识过程充满了挑战。
本文将深入探讨多变量耦合系统的辨识方法,旨在揭示其内在的工作原理和应用策略。
首先,我们需要理解什么是多变量耦合系统。
这种系统由两个或更多的变量组成,它们之间存在直接或间接的影响,形成了复杂的交互网络。
例如,电力系统、生物系统、经济系统等都是典型的多变量耦合系统。
辨识这样的系统,就是要找出这些变量之间的关系,构建能够准确预测系统行为的数学模型。
传统的辨识方法主要包括最小二乘法、灰色系统理论、神经网络等。
最小二乘法是最常用的辨识方法之一,它通过最小化误差平方和来确定模型参数。
然而,对于非线性或者多变量耦合的系统,这种方法可能会失效。
此时,灰色系统理论和神经网络等非线性模型辨识方法就显得尤为重要。
灰色系统理论通过构建灰色关联模型,能够处理数据信息不完全的情况。
而神经网络则利用其强大的非线性拟合能力,对多变量耦合系统进行建模。
近年来,随着机器学习和深度学习的发展,新的辨识方法也在不断涌现。
例如,递归神经网络(RNN)和长短期记忆网络(LSTM)在处理时间序列数据,尤其是具有长期依赖性的多变量系统中表现出色。
另外,卷积神经网络(CNN)在处理图像或信号数据的系统辨识问题上也有独到之处。
这些方法通过大量的训练数据,自动学习和提取特征,从而构建出复杂的系统模型。
然而,多变量耦合系统的辨识并非易事。
首先,数据的获取和处理是一项巨大的挑战。
系统中的变量可能受到各种因素的影响,需要大量的实验或观测数据来揭示其内在规律。
其次,模型的复杂性也是一个问题。
过度复杂的模型可能导致过拟合,而过于简单的模型则可能无法捕捉系统的复杂动态。
因此,如何选择合适的模型复杂度,以及如何有效地处理非线性、非平稳和噪声等问题,是辨识过程中需要解决的关键问题。
自动控制原理多变量系统知识点总结

自动控制原理多变量系统知识点总结自动控制原理涉及的知识点繁多而深奥,其中,多变量系统是其中的一个重要分支。
多变量系统指的是具有多个输入和多个输出的控制系统,它常常用来描述和控制复杂的工业过程。
在这篇文章中,将对多变量系统的基本概念、建模方法和常见的控制策略进行总结,希望对读者们对多变量系统有一个清晰的了解。
一、多变量系统的基本概念多变量系统是指具有多个输入和多个输出的控制系统。
一个多变量系统可以用矩阵形式表示,其中输入矩阵表示控制器对系统的输入,输出矩阵表示系统对输入的响应。
多变量系统的状态可以通过状态方程来描述,状态方程是一组描述系统演变的微分方程。
多变量系统的稳定性可以通过判据和观测函数来进行判断。
二、多变量系统的建模方法多变量系统的建模是指根据实际问题,将系统的输入、输出和状态之间的关系建立数学模型。
常用的多变量系统建模方法包括物理建模、数据建模和经验建模。
物理建模根据系统的物理特性建立数学模型,数据建模通过收集实际数据来建立模型,经验建模则是根据经验知识和专家经验来建立模型。
三、多变量系统的控制策略多变量系统的控制策略旨在实现对系统的稳定性、性能和鲁棒性的控制。
常用的多变量控制策略包括PID控制、模型预测控制和最优控制。
PID控制是一种经典的控制策略,通过调节比例、积分和微分参数来实现对系统的稳定性和性能的控制。
模型预测控制是一种基于系统数学模型进行预测和优化的控制策略,最优控制则是通过优化目标函数来寻找系统最优控制输入。
四、多变量系统的应用领域多变量系统广泛应用于各个领域,包括化工、电力、航空等工业过程。
在化工领域,多变量系统常用于控制化工反应过程,保持反应物浓度和温度等参数在一定范围内。
在电力领域,多变量系统可用于控制电网的稳定性和供电质量。
在航空领域,多变量系统可用于控制飞行器的姿态和航迹。
五、总结多变量系统是自动控制原理中的一个重要分支,它涉及的知识点繁多而复杂。
本文对多变量系统的基本概念、建模方法和常见的控制策略进行了总结。
频域解耦控制与多变量系统的优化控制器设计

频域解耦控制与多变量系统的优化控制器设计频域解耦控制(Frequency Domain Decoupling Control)是一种通过对多变量系统进行频域分析和控制的方法。
多变量系统指的是具有多个输入和输出的系统,这些输入和输出之间可能存在耦合关系。
优化控制器设计是指根据系统的特性和性能要求,设计出最优的控制器来实现系统的稳定和性能优化。
频域解耦控制的基本思想是通过设计合适的频域控制器,将多变量系统分解为多个单变量回路,从而实现对系统的解耦。
解耦后的子系统可以通过独立的单变量控制器进行控制,简化了系统的控制问题。
频域解耦控制的关键是通过适当的频域设计方法将多变量系统转化为多个单变量系统,并采用合适的控制策略将其稳定和优化。
频域解耦控制的具体实现过程包括以下几个步骤:1. 确定系统的输入输出关系:首先需要建立系统的输入与输出之间的数学模型,可以采用传递函数或状态空间模型表示。
通过确定系统的参数和互关系,得到多变量系统的传递函数矩阵或状态空间矩阵。
2. 进行频域分析:利用频域分析方法,对多变量系统的传递函数矩阵或状态空间矩阵进行分析,得到系统的频域响应特性。
包括振荡频率、衰减系数、相位等参数。
3. 进行解耦设计:根据系统的输入输出关系和频域分析结果,设计相应的频域解耦器。
解耦器用于分解多变量系统成为多个单变量回路,并通过合适的耦合矩阵来减弱或消除不同回路之间的耦合影响。
4. 设计单变量控制器:根据解耦后的子系统,针对单个回路设计相应的单变量控制器。
可以采用PID控制器、模糊控制器、自适应控制器等不同的控制策略。
5. 完整系统的控制:将设计好的解耦器和单变量控制器结合起来,形成完整的频域解耦控制系统。
通过对每个单变量回路的控制,实现对整个多变量系统的控制和优化。
多变量系统的优化控制器设计是在频域解耦控制的基础上进行的。
优化控制器的设计目标是在系统稳定的前提下,通过合适的控制策略来优化系统的性能指标。
多变量解耦控制方法研究

多变量解耦控制方法研究多变量解耦控制是现代控制理论中的重要分支,也是工业过程控制的关键技术之一、在实际工程应用中,往往需要同时控制多个输入输出变量,而这些变量之间往往存在相互影响和耦合关系。
多变量解耦控制方法旨在消除这种耦合,实现多变量系统的分离控制和单变量控制。
多变量解耦控制方法主要应用于工业过程控制、化工过程控制、电力系统控制等领域。
其核心思想是通过对系统进行建模和分析,利用现代控制理论中的方法和技术,将多变量系统转化为多个单变量的子系统,从而实现系统的解耦控制。
多变量解耦控制方法通常包括模型预测控制(MPC)、广义预测控制(GPC)、自适应控制等。
模型预测控制(MPC)是一种基于优化理论和动态系统模型的先进控制方法,广泛应用于工业过程控制领域。
MPC通过建立系统的数学模型,根据系统状态的变化进行预测,并在每个控制周期内进行优化求解,以实现对系统变量的控制。
在多变量系统中,MPC通过对多个子系统进行分析和建模,将多变量控制问题转化为多个单变量的优化控制问题,然后采用协调控制策略来实现解耦控制。
广义预测控制(GPC)是一种通过在线参数估计和模型预测来实现多变量控制的方法。
GPC通过对系统建立动态模型,利用过去时刻的控制输入和输出数据,通过在线参数估计来更新模型的参数,实现对系统的预测和控制。
与MPC相比,GPC更加适用于动态环境下的多变量系统控制,具有良好的鲁棒性和自适应性。
自适应控制是一种利用自适应算法和参数估计方法来实现多变量解耦控制的方法。
自适应控制能够根据系统的变化和模型的误差,自动调整控制器的参数,以实现对系统的自适应控制。
在多变量系统中,自适应控制方法可以通过在线参数估计和优化算法,实现对多个子系统的解耦控制和优化控制。
总之,多变量解耦控制方法是实现多变量系统控制的重要技术,对于提高系统的性能和稳定性具有重要意义。
未来,随着控制理论的不断发展和应用领域的扩大,多变量解耦控制方法将得到进一步的研究和应用,并在各个领域中发挥更大的作用。
840D 、系统变量表 中文

15.2.59 安全集成………………………………………………………………
15-621
15-509
15 09.01
15 表格
15.1 指令表
15.1 指令表
说明 1 程序开始时的缺省设定(以提供之控制系统交货状态,没有编程其它设定) 2 群组编号与/PG/,编程指南,基础篇,部份 12.3 的表格”G 功能/准备菜单”一致。 3 绝对终点:模态的;增量的终点:非模态的;模态/非模态端视 G 功能语句而定 4 IPO 参数增量地如弧心作用。它们可以在绝对模式中以 AC 被编程。当它们有其它的意义(如冲孔)时,略去 地址修改。 5 词汇不适用于 SINUMERIK FM-NC/810D 6 词汇不适用于 SINUMERIK FM-NC/810D/NCU571 7 词汇不适用于 SINUMERIK 810D 8 OEM 用户可以合并两个额外的插补类型和修改它们的名称 9 仅用于 SINUMERIK FM-NC 的词汇 10 不能就这些功能使用扩展之地址程序段格式。
B25
刀具方向:方向向量组件
Real
s
B35
程序段开始用的刀具方向
Real
s
B45
程序段结束用的刀具方向; Real
s
一般向量组件
B55
通过后面的 3 个点定义第一个 Real
s
样条区(开始
BAUTO 通过随后的 3 个点定义第一个样条段(开始非
m 19
一个结节)
BLSYNC 中断程序的处理仅以下一个区域改变启动
成字符串(get axis as string) AXIS
SW6 版起
SW6 版(含)以上,主轴编号转 从 SW6 版起
成字符串(get string)
- 1、下载文档前请自行甄别文档内容的完整性,平台不提供额外的编辑、内容补充、找答案等附加服务。
- 2、"仅部分预览"的文档,不可在线预览部分如存在完整性等问题,可反馈申请退款(可完整预览的文档不适用该条件!)。
- 3、如文档侵犯您的权益,请联系客服反馈,我们会尽快为您处理(人工客服工作时间:9:00-18:30)。
多变量耦合系统在工业中的应用摘要:在机组功率调节、供热抽汽压力调节、工业抽汽压力调节时各受控对象相互影响,因此该系统为多变量耦合系统,一般的控制方法难以得到满意的控制效果;针对系统的上述特性,并根据实际情况,把它们看成一个统一的整体来考虑,并将多变量串级解耦技术应用到控制系统当中,使该系统的控制品质有了较大的提高;在自动投入后,电厂发电、热网供热、工业抽汽系统能够经济、稳定地运行,为电厂取得良好的社会效益和经济效益奠定了基础。
关键词:功率调节工业抽汽供热抽汽多变量解耦
引言
供热抽汽采用两机的低压缸前抽汽为汽源,由两个由油动机驱动的蝶阀控
制抽汽压力,供热抽汽的额定压力为0.196MPa;工业抽汽承担供气的重任,它
采用两机的一级调整抽汽为汽源、由四个油动机驱动的调节阀门(中调门)控制
工业抽汽压力,工业抽汽的额定压力为4.122Mpa,满负荷为160T/H。
当机组
功率、供热抽汽压力、工业抽汽压力中任一变量发生扰动时,其它两个变量都会
受到影响,而它们的变化反过来又会影响这个变量,因此,在考虑控制策略时,不应把系统分开对待,应将各系统看作一个多变量整体。
这种电、热、汽联调的
机组在内蒙尚属首次,这也增加了控制策略选取和自动投入的难度。
为保证系统的稳定性和经济性,调试时采用多变量解耦控制策略,尽可能减
少变量间的相互影响。
考虑到实际应用时,控制策略受DCS系统运算速度和对
象数学模型不确定性等因素影响,我们将一些控制方法做了一定的简化,使其更适合实际运用。
1 理论依据
1.1控制对象介绍
系统在实际应用时,有以下三种情况
(1)工业抽汽压力自动投入,供热抽汽压力自动未投(电汽联调)
(2)工业抽汽压力自动未投,供热抽汽压力自动投入(电热联调)
(3)供热抽汽压力自动投入,工业抽汽压力自动投入(电热汽联调)
前两种方式为双输入、双输出的多变量控制系统;在第三种情况下,系统控制对象为三输入、三输出的多变量对象:三个输入调节量为高调门指令u1,中调门指令u2,低压缸出口碟阀指令u3;三个输出控制量为机组实发功率P,工业抽汽压力P1,供热抽汽压力P2。
三种情况的传递函数分别如式(1)、式(2)、式(3)
(1)
(2)
(3)
1.2解耦控制方法
解耦的本质在于设置一个逻辑网络,减少或解除耦合,以保证各个单回路控制对象能独立的工作。
常用的解耦控制方法共有:串级解耦控制、反馈解耦控制、前补偿法三种,本系统选用串级解耦控制方法中的对角矩阵法,下面以双输入、双输出的多变量对象为例,介绍一下对角矩阵解耦方法。
图(一)中,G c1(s)、G c2(s)为控制器,D11、D21(s)、D12(s)、D22(s)为解耦器,G11(s)、G21(s)、G12(s)、G22(s)为控制对象的传递函数。
Y1、Y2为输出。
如图(一)所示,,被控量与控制量之间的关系矩阵为:
(4 )
D
控制量与调节器输出之间的关系矩阵为
11
(5)
由(4)式和(5)式得到系统传递函数为
(6)对角矩阵解耦方法是将传递函数矩阵转化为对角阵的形式,相当于以下形式
(7)由(6)式和(7)式可得到解耦器的数学模型为
(8)如果解耦器设计成与式(8)相同或与式(8)相近的形式,则系统可化为式(7)的形式,框图如图(二)所示,可见两组控制对象相互之间不再影响,达到了解耦的目的。
对于式(3)的三输入、三输出系统,通过上述办法也可以的求得解耦器的数学模型,但变量越多,解耦器越复杂,必须对其进行近似简化。
工业抽汽自动投入时,考虑到对抽汽压力和供热压力的精度要求不是很高,故抽汽压力和供热压力的控制器选取比例调节器,且调节死区放得稍大。
电厂供热和抽汽控制根据实际应用可分为三种情况,其中电热联调和电汽联调为两输入、两输出系统,而电热汽联调为三输入、三输出系统,其解耦控制原理图如图(三)所示,在实际调试时必须分别对三种情况进行参数整定。
2.1解耦控制器的求取
为简化控制系统,并减少因计算量大而带来的控制偏差,将所有解耦器都近似为比例系数,电热联调和电汽联调各有四个解耦系数,电热器联调为九个解耦系数,也就是说需整定三种情况共十七个解耦系数。
另外,在实际工业中难以得到控制对象精确的数学模型,因而在整定时采用先按前面用到的公式计算近似值,然后在实际调试时用试凑的办法得到最佳的控制参数。
2.2动态响应
(1)图(四)为解耦控制未投入,工业抽汽压力加扰动时发电机功率(红色)、工业蒸汽压力(绿色)、供热蒸汽压力(蓝色)的响应曲线。
(2) 图(五)为解耦控制投入,工业抽汽压力加扰动时发电机功率(红色)、工业蒸汽压力(绿色)、供热蒸汽压力(蓝色)的响应曲线。
图(四)
图(五)
3 结语
系统采用中调门和低压缸出口蝶阀调节工业抽汽压力和供热抽汽压力,并承担供汽和给城市供热的任务,自动调节品质的好坏、控制系统的稳定性具有较重要的现实意义。
由图(四)和图(五)的响应曲线可见,采用多变量解耦控制技术之后,三个变量之间互扰明显减小,对象的调节品质有了很大的提高,调节效果比未投解耦控制时有明显改善。