铝挤压工序
铝型材挤压工艺流程

铝型材挤压工艺流程铝型材挤压工艺流程铝型材挤压是一种常见的金属加工方法,通过将铝材放入挤压机中,经过一系列加工步骤,使其挤压成所需形状的型材。
下面介绍一下铝型材挤压的工艺流程。
首先,准备工作。
在进行铝型材挤压前,需要进行一系列准备工作。
首先,选择合适的铝材料。
铝材料应具有一定的韧性和延展性,以便于挤压成型。
其次,对铝材进行预处理,包括去油、除尘和表面清洁等。
这是为了保证铝材的质量和表面光洁度。
最后,根据产品的要求,设计和制作挤压模具,即模具上的挤压形状和孔型。
第二步,挤压加工。
挤压加工是铝型材挤压的核心步骤。
首先,将铝块预热至一定温度。
铝块预热的目的是提高其延展性和可塑性,便于挤压成型。
然后,将预热的铝块放入挤压机的料斗中。
挤压机内部有一个柱塞,通过向铝块施加压力,使其被挤压出来。
铝块经过挤压孔,在挤压模具的作用下,被挤压成型,形成所需的铝型材。
挤压过程中,需要控制挤压机的压力、速度和温度等参数,以确保铝型材的质量。
第三步,冷却处理。
铝型材挤压完成后,需要进行冷却处理。
冷却处理是为了加快铝材的固化和增强结构的稳定性。
一般采用水冷或空冷的方式进行冷却。
冷却时间根据铝材的尺寸和形状等参数而定。
第四步,切割和整理。
经过冷却处理后,挤压好的铝型材需要进行切割和整理。
首先,根据产品要求,将铝型材切割成所需的长度。
然后,用刷子清除铝型材表面的铝屑和杂质,以保持其光洁度和美观度。
第五步,表面处理。
最后,对铝型材进行表面处理。
根据产品的要求,可以进行阳极氧化、喷涂、电泳涂装等。
这些表面处理方法可以增加铝型材的耐腐蚀性、耐磨性和美观度。
以上就是铝型材挤压的工艺流程。
铝型材挤压工艺简单高效,可以生产出形状各异的铝型材,广泛应用于建筑、家具、电子、汽车等行业。
铝型材挤压工艺流程

铝型材挤压工艺流程铝型材挤压工艺流程铝型材挤压是一种常见的铝合金加工方法,常用于生产各种规格的铝型材。
以下是一般的铝型材挤压工艺流程。
首先,选择适当的铝合金材料。
铝合金具有优良的力学性能和耐腐蚀性能,适合用于挤压成型。
根据产品要求,选择合适的铝合金材料,并根据其化学成分和性能进行配料。
其次,将铝合金材料加热至挤压温度。
铝合金材料需要加热至一定温度才能进行挤压。
加热温度一般根据铝合金的组成和性能来确定,一般在480℃到520℃之间。
加热过程需要控制加热速度和温度均匀性,以保证挤压后产品的质量。
然后,将熔化的铝合金从加热炉中取出,注入挤压机中。
挤压机是铝型材挤压的核心设备,通过压力将铝合金压入型腔中,使其形成所需形状的型材。
挤压机中含有模具,通过模具的形状来决定最终的产品形状。
在注入挤压机前,需要对挤压机进行检查和调整,确保其正常运行。
接下来,进行铝型材的挤压。
在挤压机的作用下,铝合金在模具中受到压力的挤压,从而形成所需的型材。
挤压过程中需要控制挤压速度和压力,以及模具温度,以保证产品的质量和精度。
挤压过程中一般需要多次挤压,通过不同的模具和挤压头形成不同截面形状的型材。
最后,进行型材的冷却和固化。
挤压完成后,将型材从挤压机中取出,进行冷却和固化。
冷却过程中,型材会逐渐冷却并固化,使其具有良好的力学性能和表面质量。
冷却过程中需要控制冷却速度和温度,以避免产生内应力和尺寸偏差。
以上是一般的铝型材挤压工艺流程。
铝型材挤压工艺具有高效、节能和环保的特点,广泛应用于建筑、交通运输、电子、机械等领域。
随着科技的进步和工艺的改进,铝型材挤压技术将不断发展和创新,为各个行业提供更好的产品和解决方案。
铝合金挤压成型工艺

铝合金挤压成型工艺铝合金挤压成型工艺是一种常见的金属加工方法,通过将铝合金材料加热至一定温度,然后通过挤压机将其挤压成所需形状的工件。
该工艺具有高效、精准、重复性好等优点,在许多工业领域得到广泛应用。
本文将对铝合金挤压成型工艺进行详细介绍。
一、工艺流程铝合金挤压成型工艺的一般流程包括材料准备、加热、模具设计、挤压加工、冷却和后续处理等环节。
1.材料准备铝合金挤压成型的首要工作是选取合适的铝合金材料。
通常选择具有良好塑性和可挤压性的铝合金,如6063、6061等。
在选取材料时,还需要考虑工件的用途、强度要求和耐腐蚀性等因素。
2.加热选取好的铝合金材料后,需要将其加热至一定温度。
加热的目的是使铝合金材料变软和可塑性增加,便于进行挤压加工。
加热温度一般控制在材料的连续搬运温区。
3.模具设计模具设计是铝合金挤压成型工艺中非常关键的一环。
模具的设计需要考虑工件的形状、尺寸、挤压比和冷却方式等因素。
合理的模具设计可以确保工件的质量和尺寸精度。
4.挤压加工在加热和模具设计完成后,将铝合金材料放入挤压机中进行挤压加工。
挤压机通过给定的冲程和行程将铝合金材料挤压入模具中,并形成所需形状的工件。
挤压过程需要控制好挤压速度和压力,以保证工件的质量和形状。
5.冷却挤压完成后,将工件进行冷却以增加其强度和硬度。
冷却可以通过自然冷却或水冷方式进行。
6.后续处理部分工件需要进行后续处理,如修整、打磨、抛光等工序,以进一步提高工件的表面质量和光洁度。
二、工艺参数及影响因素铝合金挤压成型工艺中的一些关键参数包括挤压温度、挤压速度、挤压比和模具温度等。
1.挤压温度挤压温度是指将铝合金材料加热至一定温度后进行挤压加工的温度。
挤压温度的选择需要考虑材料的可塑性和粘度,一般在材料的连续搬运温区进行挤压。
2.挤压速度挤压速度是指铝合金材料在挤压机中的运动速度。
挤压速度的选择需要平衡生产效率和工件质量的要求,过快的挤压速度可能导致工件表面粗糙,过慢的挤压速度可能影响生产效率。
铝合金型材挤压加工全过程
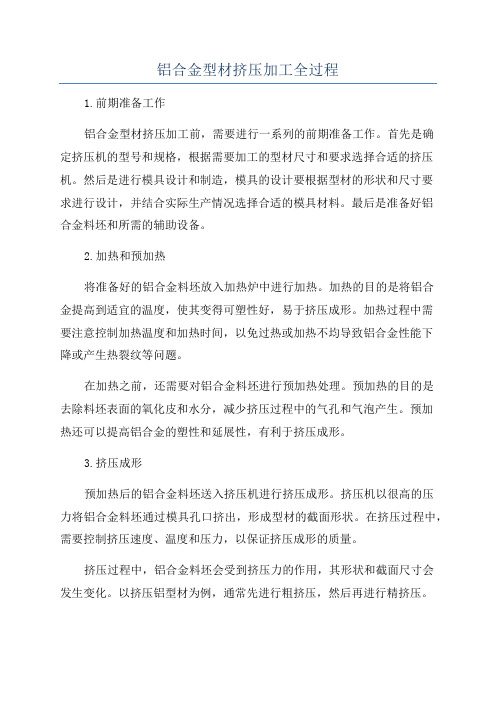
铝合金型材挤压加工全过程1.前期准备工作铝合金型材挤压加工前,需要进行一系列的前期准备工作。
首先是确定挤压机的型号和规格,根据需要加工的型材尺寸和要求选择合适的挤压机。
然后是进行模具设计和制造,模具的设计要根据型材的形状和尺寸要求进行设计,并结合实际生产情况选择合适的模具材料。
最后是准备好铝合金料坯和所需的辅助设备。
2.加热和预加热将准备好的铝合金料坯放入加热炉中进行加热。
加热的目的是将铝合金提高到适宜的温度,使其变得可塑性好,易于挤压成形。
加热过程中需要注意控制加热温度和加热时间,以免过热或加热不均导致铝合金性能下降或产生热裂纹等问题。
在加热之前,还需要对铝合金料坯进行预加热处理。
预加热的目的是去除料坯表面的氧化皮和水分,减少挤压过程中的气孔和气泡产生。
预加热还可以提高铝合金的塑性和延展性,有利于挤压成形。
3.挤压成形预加热后的铝合金料坯送入挤压机进行挤压成形。
挤压机以很高的压力将铝合金料坯通过模具孔口挤出,形成型材的截面形状。
在挤压过程中,需要控制挤压速度、温度和压力,以保证挤压成形的质量。
挤压过程中,铝合金料坯会受到挤压力的作用,其形状和截面尺寸会发生变化。
以挤压铝型材为例,通常先进行粗挤压,然后再进行精挤压。
粗挤压时,将料坯通过挤压机挤出,并形成初步的截面形状。
精挤压时,将初步挤出的型材再次送入挤压机进行挤压,形成最终的型材截面形状。
4.后期处理挤压成形后的型材需要进行一些后期处理,以提高其性能和表面质量。
常见的后期处理方法包括:-退火处理:通过加热和保温的方式对挤压成形后的型材进行退火,以消除内应力,提高材料的机械性能。
-拉伸加工:将挤压成形后的型材进行拉伸,以提高其强度和硬度。
-切割和修整:将挤压成形后的型材按照所需的长度进行切割,并进行修整,以获得所需的尺寸和形状。
-表面处理:对型材进行表面处理,如喷漆、阳极氧化、电泳涂装等,以提高其防腐蚀性和美观度。
以上就是铝合金型材挤压加工的全过程。
铝挤压加工生产工艺流程
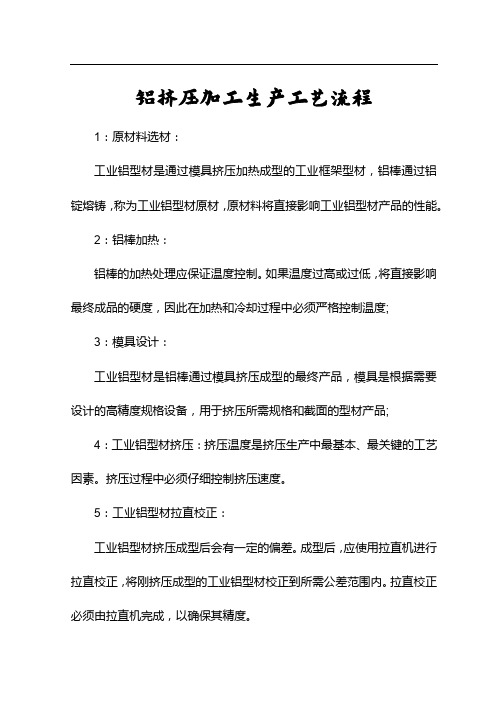
铝挤压加工生产工艺流程
1:原材料选材:
工业铝型材是通过模具挤压加热成型的工业框架型材,铝棒通过铝锭熔铸,称为工业铝型材原材,原材料将直接影响工业铝型材产品的性能。
2:铝棒加热:
铝棒的加热处理应保证温度控制。
如果温度过高或过低,将直接影响最终成品的硬度,因此在加热和冷却过程中必须严格控制温度;
3:模具设计:
工业铝型材是铝棒通过模具挤压成型的最终产品,模具是根据需要设计的高精度规格设备,用于挤压所需规格和截面的型材产品;
4:工业铝型材挤压:挤压温度是挤压生产中最基本、最关键的工艺因素。
挤压过程中必须仔细控制挤压速度。
5:工业铝型材拉直校正:
工业铝型材挤压成型后会有一定的偏差。
成型后,应使用拉直机进行拉直校正,将刚挤压成型的工业铝型材校正到所需公差范围内。
拉直校正必须由拉直机完成,以确保其精度。
6:人工时效:
挤压生产的铝型材在时效前硬度低,不能作为成品使用。
因此,一般来说,强度必须通过时效来提高。
7:喷砂+氧化:
挤压成型后,工业铝型材表面会有明显的拉伸线,表面微孔较大,相对粗糙,必须经过喷砂处理
8:包装:
由于工业铝型材产品质量要求很高,整体外观美观非常精致,所以后期包装要求非常严格。
铝挤压型材工艺

铝挤压型材工艺一、原材料准备铝挤压型材的原材料主要是铝锭,需要经过熔炼、铸造、切割等工序,制成适合挤压的铝棒。
在准备过程中,需要确保铝棒的成分、尺寸、表面质量等符合要求,以保证挤压过程的顺利进行。
二、模具设计模具是铝挤压型材成型的关键设备,需要根据产品规格、形状、尺寸等要求进行设计。
模具设计需要考虑挤压比、模具强度、润滑等要素,以保证挤压过程的稳定性和产品的质量。
三、挤压成型挤压成型是铝挤压型材生产的核心环节,通过将铝棒放入模具中,在高温高压下进行挤压,使铝棒变形成为所需形状和尺寸的型材。
在挤压过程中,需要控制挤压速度、温度、压力等参数,以保证型材的质量和稳定性。
四、热处理热处理是铝挤压型材生产的重要环节,通过加热和冷却处理,可以改变型材的内部结构,提高其强度和硬度。
热处理工艺需要根据型材的成分、规格和性能要求进行制定,以保证型材的性能和稳定性。
五、表面处理表面处理是提高铝挤压型材表面质量和防腐性能的重要环节,包括清洗、喷涂、氧化等工艺。
表面处理可以增加型材的美观性和使用寿命,提高产品的附加值。
六、尺寸调整在挤压过程中,由于模具、设备等因素的影响,可能会导致型材的尺寸发生变化。
因此,需要对型材进行尺寸调整,以确保其符合规格要求。
七、检验与测试在生产过程中和产品出厂前,需要对铝挤压型材进行检验和测试,包括尺寸、形状、成分、性能等方面的检测。
通过检验和测试,可以确保产品的质量和稳定性,提高客户满意度。
八、包装与运输为了保护铝挤压型材在运输和存储过程中的质量和安全,需要进行包装和运输。
包装材料应具有防潮、防震、防腐等功能,以确保产品在运输和存储过程中的完好无损。
同时,在运输过程中应采取防震、防水等措施,以防止产品损坏和变形。
铝合金热挤压的基本工艺

铝合金热挤压的基本工艺
铝合金热挤压是一种常见的金属加工工艺,用于生产各种铝合金型材,如铝合金门窗、铝合金管材、铝合金棒材等。
其基本工艺包括以下几个步骤:
1. 原料准备:选择适宜的铝合金材料,并对其进行预处理,如切割、去毛刺等。
2. 加热:将铝合金材料加热至合适的温度,通常为材料的再结晶温度或略高于该温度。
3. 模具准备:准备好挤压模具,根据产品的形状和尺寸要求进行设计和制造。
4. 挤压:将加热后的铝合金材料放入挤压机的料斗中,通过压力将材料挤压进模具中。
在挤压过程中,铝合金材料会发生塑性变形,使得其截面形状和尺寸得到改变。
5. 切割:将挤压出的铝合金型材按照需要的长度进行切割。
6. 退火处理:对挤压出的铝合金型材进行退火处理,以消除残余应力和改善材料的机械性能。
7. 表面处理:对铝合金型材进行表面处理,如阳极氧化、喷涂、喷砂等,以提高其耐腐蚀性和美观度。
通过以上基本工艺步骤,可以生产出各种形状和尺寸的铝合金型材,满足不同行业的需求。
铝型材挤压流程
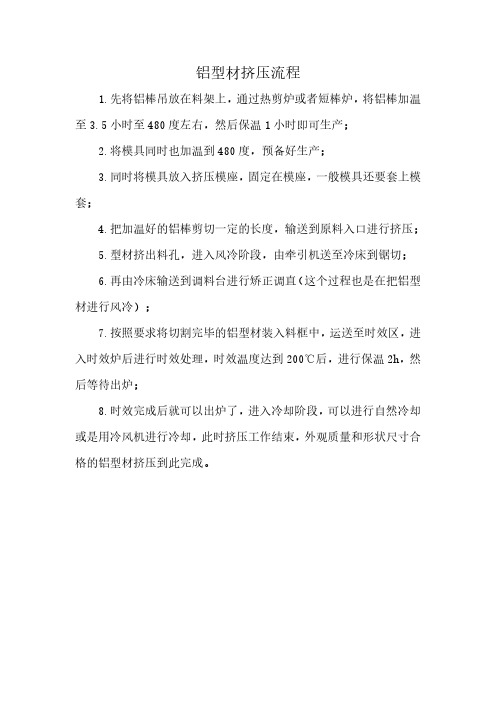
铝型材挤压流程
1.先将铝棒吊放在料架上,通过热剪炉或者短棒炉,将铝棒加温至3.5小时至480度左右,然后保温1小时即可生产;
2.将模具同时也加温到480度,预备好生产;
3.同时将模具放入挤压模座,固定在模座,一般模具还要套上模套;
4.把加温好的铝棒剪切一定的长度,输送到原料入口进行挤压;
5.型材挤出料孔,进入风冷阶段,由牵引机送至冷床到锯切;
6.再由冷床输送到调料台进行矫正调直(这个过程也是在把铝型材进行风冷);
7.按照要求将切割完毕的铝型材装入料框中,运送至时效区,进入时效炉后进行时效处理,时效温度达到200℃后,进行保温2h,然后等待出炉;
8.时效完成后就可以出炉了,进入冷却阶段,可以进行自然冷却或是用冷风机进行冷却,此时挤压工作结束,外观质量和形状尺寸合格的铝型材挤压到此完成。
- 1、下载文档前请自行甄别文档内容的完整性,平台不提供额外的编辑、内容补充、找答案等附加服务。
- 2、"仅部分预览"的文档,不可在线预览部分如存在完整性等问题,可反馈申请退款(可完整预览的文档不适用该条件!)。
- 3、如文档侵犯您的权益,请联系客服反馈,我们会尽快为您处理(人工客服工作时间:9:00-18:30)。
铝挤压工序
2006-2-15
热量分析
铝棒温度
出口温度
最佳挤压温度
牵引机速度
挤压杆速度
模具温度
盛料筒温度
淬火温度(温差)
合金型态
时效
最佳金属物理性能的达成
成品率
生产效率
热量分析
铝绦和铝棒在挤压前需预先加热,达到接近溶线温度(Solvus temperature),以便在铝棒内的及镁能熔化,并在铝料中均匀地流动。
当铝棒被放进挤压机内时,温度没有太大的变化,在图表中以一水平线表示。
而当挤压机开动时,挤压杆的巨大推挤力量把软化了的铝料由模具孔挤出,产生很大的摸察力,这摸擦力转化为温度,使挤出的型材温度超过熔线温度,此时及镁熔化,向四处流动,极不稳定。
温度的提高决不能高出固熔相线(Solidus temperature),不然铝也会熔化,而型材就无法成型。
铝棒温度
铝棒温度应保持在400-540°C之间(以6xxx系铝合金为例),最好是420-440°C。
太高会引起撕裂现象,太低会减低挤压速度(因铝料必须软化)挤压的摩擦力大部分会转化为热量,导致温度上升. 温度的上升与挤压速度及挤压压力成正比。
出口温度
出口温度应保持在550 to 575 °C 之间,起码也要在 500 to 530°C之上. 不然铝合金内的镁和就不能熔化而影向金属性能。
但决不能高过固熔相线,太高的出口温度会导致撕裂现象,并且影向型材的表面品资.
最佳挤压温度
铝棒温度要结合挤压速度来调节,使挤压温差不低於溶线温度(Solvus temperature),也不高於固相线温度 (Solidus temperature),即620°C。
不同的合金有不同的溶线温度,比如6063合金的溶线温度是498°C,而6005合金的溶线温度则是510°C。
牵引机速度
牵引机速度是生产效率的一个重要指标。
但不同的型材、型状、合金、尺寸等都有可能影向牵引机速度。
固不能一概而论。
现代西方的挤压型材厂都能做到每分锺80米的牵引机速度。
挤压杆速率
挤压杆速率是生产率的另一重要指标。
它是以毫米/分锺或 /分锺为量度单位的。
在研究生产效率时,挤压杆速率往往比牵引机速度更可靠,因不同的型材、型状、合金、尺寸等都有可能影向牵引机速度。
模具温度
Die Oven
模具温度对挤压型材的品质致为重要. 模具温度在挤压前须保持在426°C左右。
不然会容易产生堵塞甚至损毁模具的现象。
盛料筒温度
盛料筒温度须保持在426°C左右。
淬火温度(温差)
淬火(冷却)的目的在於"冷冻"合金元素,即镁和 ,把不稳定的镁和(矽)原子稳定下来,不让其沉淀。
以保持型材的强度。
三种主要的淬火方式包括:
风冷
水雾冷却
水槽冷却
用哪种淬火方式取决於挤压速度、型材厚度及所需的物理性能,特别是对强度的要求。
合金型态
合金型态是合金的硬度和弹性能的综合标示
美国铝业协会对铝合型态已有详细规定: 基础状态代号
铝、镁及其合金的基础状态代号为:
F
自由加工状态,适用於在成型过程中对温度或材料的加工硬化程度无特殊控制的产品(对加工产品无力学性能要求);
O
退火状态,适用於经退火获得最低强度的加工产品及经退火提高延展性和尺稳定性的铸造产品,O後可缀有除零以外的一位阿拉伯数字;
H
加工硬化状态,适用於通过加工硬化提高强度的产品(这种产品可通过热处理降低一些强度),H 後总是缀有两位以上的阿拉伯数字;
W
固溶热处理状态(一种不稳定状态),仅适用於固溶热处理後在室温自然时效的合金,并只有具体指出自然时效的时间才使用这种特殊代号,如W1/2小时;
T
热处理後产生的稳定状态(不同於F、O和H状态),适用於经热处理产生稳定状态的产品(这种产品也可进行加工硬化),T字母总是缀有一位以上的阿拉伯数字;
时效
大部分型材在淬火之後,需要在时效炉内进行热处理,时效的作用主要是对合金元素(镁和)进行重新配置,使其能均匀地分布在型材的所部位,以提高型材的强度。
温度和时间是两个人工时效需要严格控制的指标. 在人工时效炉内,每个部位的温度都必须一样。
低温时效虽然能提高型材的强度,但所需的时间也需相应地拉长。
最佳金属物理性能的达成
要达到最佳金属物理性能必须: 选取适当的铝合金及其最佳的型态
选择适当的淬火(冷却)方式
应用合适的时效温度及控制时效时间
成品率
成品率是生产效率的另一重要指标.100%的成品率,理论上是不可能实现的,因为挤压切头(Butts)和因牵引机及拉伸机夹痕而切掉的料材是无可避免的。
加上挤压时出现的废品、碰伤、产前试料、换模试机等,一般成品率都只能达到85%左右. 中国国内的挤压厂一般都只能达到70% - 75%的成品率.
生产效率
型材挤压的主要生产效率指标包括:
挤压机利用率: 挤压机的实际产出舆设计产能的比率
挤压机成品率
单位时间内的人均产量
内部废品率
退货率
停机次数及时间。