moldflow分析报告
moldflow分析报告
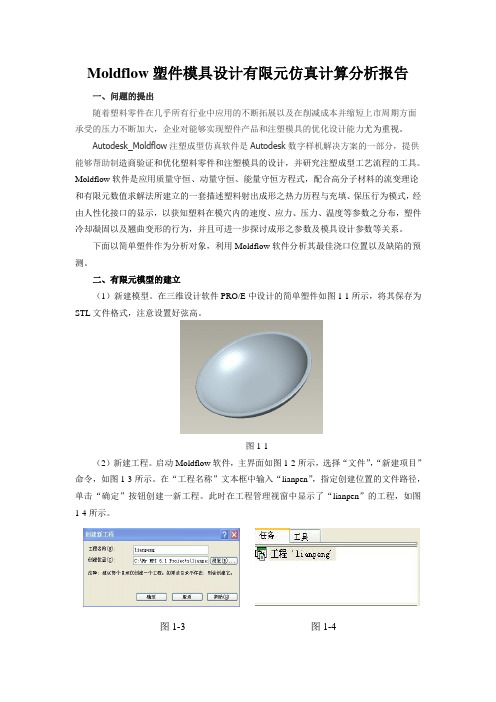
Moldflow塑件模具设计有限元仿真计算分析报告一、问题的提出随着塑料零件在几乎所有行业中应用的不断拓展以及在削减成本并缩短上市周期方面承受的压力不断加大,企业对能够实现塑件产品和注塑模具的优化设计能力尤为重视。
Autodesk_Moldflow注塑成型仿真软件是Autodesk数字样机解决方案的一部分,提供能够帮助制造商验证和优化塑料零件和注塑模具的设计,并研究注塑成型工艺流程的工具。
Moldflow软件是应用质量守恒、动量守恒、能量守恒方程式,配合高分子材料的流变理论和有限元数值求解法所建立的一套描述塑料射出成形之热力历程与充填、保压行为模式,经由人性化接口的显示,以获知塑料在模穴内的速度、应力、压力、温度等参数之分布,塑件冷却凝固以及翘曲变形的行为,并且可进一步探讨成形之参数及模具设计参数等关系。
下面以简单塑件作为分析对象,利用Moldflow软件分析其最佳浇口位置以及缺陷的预测。
二、有限元模型的建立(1)新建模型。
在三维设计软件PRO/E中设计的简单塑件如图1-1所示,将其保存为STL文件格式,注意设置好弦高。
图1-1(2)新建工程。
启动Moldflow软件,主界面如图1-2所示,选择“文件”,“新建项目”命令,如图1-3所示。
在“工程名称”文本框中输入“lianpen”,指定创建位置的文件路径,单击“确定”按钮创建一新工程。
此时在工程管理视窗中显示了“lianpen”的工程,如图1-4所示。
图1-3 图1-4图1-2(3)导入模型。
选择“文件”,“输入”命令,或者单击工具栏上的“输入模型”图标,进入模型导入对话框。
选择STL文件进行导入。
选择文件“lianpen.stl”。
单击“打开”按钮,系统弹出如图1-5所示的“导入”对话框,此时要求用户预先旋转网格划分类型(Fusion)即表面模型,尺寸单位默认为毫米。
图1-5单击“确定”按钮,脸盆模型被导入,如图1-6所示,工程管理视图出现“lp1_study”工程,如图1-7所示,方案任务视窗中列出了默认的分析任务和初始位置,如图1-8所示。
Moldflow分析报告
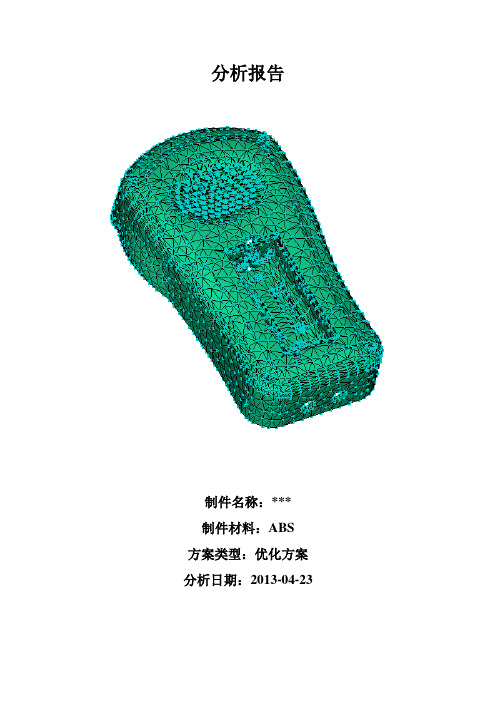
分析报告制件名称:***制件材料:ABS方案类型:优化方案分析日期:2013-04-23目录1.产品信息2.材料信息3.网格模型4.最佳浇口位置5.初始方案的设计1)浇口位置的选择2)浇注系统的设计3)冷却系统的设计4)原始方案分析结果6.优化方案的设计1)优化后浇口位置的确定2)优化后浇注系统的设计3)优化后冷却系统的设计4)优化方案分析结果7.结论与建议1.产品信息制件材料:ABS材料收缩率:0.6%制件外形尺寸:180mmx130mmx45mm180mmx130mmx40mm制件壁厚:该制件为非均匀壁厚,最大壁厚为2.2mm,最小壁厚为0.4mm。
2.材料信息本分析所用材料为Generic Default制造商,其具体数据如下:粘度曲线图PVT曲线图机器属性3.网格模型实体计数:三角形: 12780已连接的节点: 6216连通区域 1面积:表面面积: 220.056 cm^2体积:三角形:15.6014 cm^3纵横比:最大平均最小224.6 4.67 1.16边细节:自由边0共用边19170多重边0取向细节:配向不正确的单元0交叉点细节:相交单元0完全重叠单元0匹配百分比:匹配百分比77.5%相互百分比67.9%4.最佳浇口位置说明:最佳浇口位置位于蓝色区域内。
5.初始方案的设计1)浇口位置的选择说明:因考虑到浇注系统的加工工艺成型条件、结构工艺性,以及模具的制造成本,优先选用侧浇口。
2)浇注系统的设计3)冷却系统的设计4)原始方案分析结果1、流动分析结果说明:充填时间为0.96S,充填平衡,无滞留现象,满足分析要求。
充填过程如下:时发生短射。
说明:顶出时产品收缩率为11.3%,收缩率较大,需要改进。
适当加大填充的压力。
的可做镶件处理,满足分析要求。
2、冷却分析结果说明:回路冷却液温度在允许范围内,满足分析要求。
说明:回路雷洛数为10000,满足分析要求。
要说明:零件冻结层因子在材料允许范围内,满足分析要求。
(完整版)MOLDFLOW分析报告

引言概述:MOLDFLOW分析是一种重要的工具,广泛应用于塑料制品设计和生产过程中。
它可以提供关于模具充填、冷却和固化的详细信息,帮助设计师优化模具设计,提高产品质量和生产效率。
本文将通过分析报告的方式,详细介绍MOLDFLOW分析的应用和意义。
正文内容:一、模具充填分析1. 熔体流动模拟:对熔体在模具中的流动进行模拟,可以分析熔体的充填情况、充填时间和充填压力等参数,以及可能出现的缺陷,如短充、气泡等。
2. 塑料充填模拟:通过模拟塑料在模具中的充填过程,可以评估模具的设计是否合理,以及可能存在的充填不良、厚薄不均等问题。
3. 充填时间分析:根据模具充填模拟的结果,可以计算出塑料充填的时间,从而优化生产周期和工艺参数。
二、冷却系统分析1. 冷却效果模拟:通过模拟冷却系统的布局和工艺参数,在模具充填结束后,对模具进行冷却效果的分析。
可以评估冷却系统的设计是否合理,以及可能存在的冷却不均、温度过高等问题。
2. 温度分布模拟:根据冷却系统分析结果,可以计算出模具内部的温度分布,帮助优化冷却系统的设计和工艺参数。
3. 冷却时间分析:根据冷却系统模拟的结果,可以计算出模具冷却的时间,从而优化生产周期和工艺参数。
三、固化模拟分析1. 熔体固化分析:通过模拟塑料在模具中的固化过程,可以评估模具冷却效果和固化时间,避免可能出现的缺陷,如收缩、变形等。
2. 温度变化分析:根据固化模拟分析结果,可以计算出模具内部的温度变化曲线,帮助优化冷却系统和固化参数的设计。
3. 固化时间分析:根据固化模拟分析的结果,可以计算出模具固化的时间,从而优化生产周期和工艺参数。
四、缺陷分析1. 模具缺陷预测:通过模拟模具充填、冷却和固化的过程,可以预测可能出现的缺陷,如短充、气泡、收缩等,并给出相应的解决方案。
2. 缺陷修复优化:根据缺陷分析结果,可以优化模具设计和工艺参数,减少缺陷的发生,并提高产品质量和生产效率。
五、效果验证与总结1. 效果验证:通过对MOLDFLOW分析结果与实际生产产品进行对比,验证分析的准确性和可靠性,并修正和改进分析模型。
moldflow的分析报告
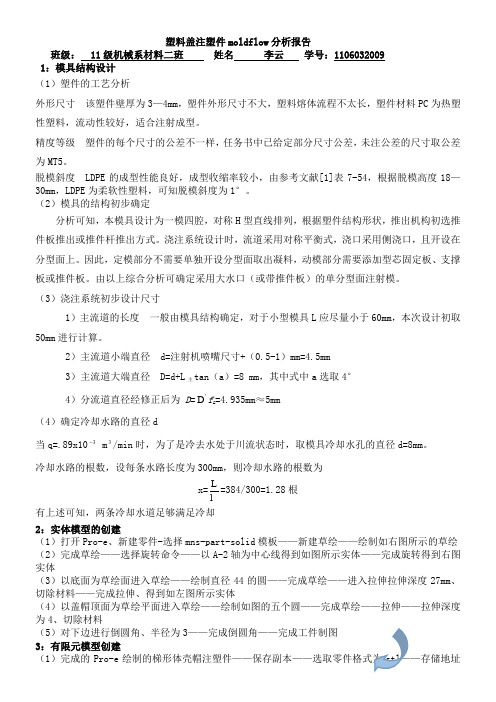
塑料盖注塑件moldflow 分析报告班级: 11级机械系材料二班 姓名 李云 学号:11060320091:模具结构设计(1)塑件的工艺分析外形尺寸 该塑件壁厚为3—4mm ,塑件外形尺寸不大,塑料熔体流程不太长,塑件材料PC 为热塑性塑料,流动性较好,适合注射成型。
精度等级 塑件的每个尺寸的公差不一样,任务书中已给定部分尺寸公差,未注公差的尺寸取公差为MT5。
脱模斜度 LDPE 的成型性能良好,成型收缩率较小,由参考文献[1]表7-54,根据脱模高度18—30mm ,LDPE 为柔软性塑料,可知脱模斜度为1°。
(2)模具的结构初步确定分析可知,本模具设计为一模四腔,对称H 型直线排列,根据塑件结构形状,推出机构初选推件板推出或推件杆推出方式。
浇注系统设计时,流道采用对称平衡式,浇口采用侧浇口,且开设在分型面上。
因此,定模部分不需要单独开设分型面取出凝料,动模部分需要添加型芯固定板、支撑板或推件板。
由以上综合分析可确定采用大水口(或带推件板)的单分型面注射模。
(3)浇注系统初步设计尺寸1)主流道的长度 一般由模具结构确定,对于小型模具L 应尽量小于60mm ,本次设计初取50mm 进行计算。
2)主流道小端直径 d=注射机喷嘴尺寸+(0.5-1)mm=4.5mm3)主流道大端直径 D=d+L 主tan (a )=8 mm ,其中式中a 选取4°4)分流道直径经修正后为 D ='D f L =4.935mm ≈5mm(4)确定冷却水路的直径d当q=.89x103 m 3/min 时,为了是冷去水处于川流状态时,取模具冷却水孔的直径d=8mm 。
冷却水路的根数,设每条水路长度为300mm ,则冷却水路的根数为 x=lL =384/300=1.28根 有上述可知,两条冷却水道足够满足冷却2:实体模型的创建(1)打开Pro-e 、新建零件-选择mns-part-solid 模板——新建草绘——绘制如右图所示的草绘(2)完成草绘——选择旋转命令——以A-2轴为中心线得到如图所示实体——完成旋转得到右图实体(3)以底面为草绘面进入草绘——绘制直径44的圆——完成草绘——进入拉伸拉伸深度27mm 、切除材料——完成拉伸、得到如左图所示实体(4)以盖帽顶面为草绘平面进入草绘——绘制如图的五个圆——完成草绘——拉伸——拉伸深度为4、切除材料(5)对下边进行倒圆角、半径为3——完成倒圆角——完成工件制图3:有限元模型创建(1)完成的Pro-e为桌面——命名为:gaimao.stl(2)打开moldflow——新建工程:梯形体壳帽——导入保存在桌面的:gaimao.stl——网格类型选取:双层面、单位为:mm——确定(3)网格——生成网格——网格长度修改为注塑件最小薄壁3mm的两倍:6mm——立即划分网格——关闭,得到如右图所示(4)网格——网格统计、检查网格问题(5)由网格统计得最大纵横比为:15.5、自由边为0、多重边为0、匹配不正确的单元为0、相交单元为0、完全重叠单元为0、匹配百分比在82.9%;因此以上项目中需要修复的有纵横比和匹配百分比(6)纵横比的修复1)网格——网格诊断——在右边参数填入:最小10——纵横比诊断得此时纵横比为15.5比较大,需要修复2)网格——网格工具——节点工具——移动、对齐、合并、消除等操作来降低纵横比3)遵循先修大纵横比后修小纵横比原则进行修复最后使纵横比低于10以下(7)厚度诊断及其修复1)网格——网格诊断——厚度诊断选取红色三角形——右击菜单——属性——指定厚度:3.5——确定4:浇注系统及冷却系统创建(1)本盖帽设计是一模四腔所以需要先型腔重复1)建模——型腔重复向导——根据注塑模设计填写数据2)曲线法画浇注系统——建模——创建直线画出如左图所示直线,其数据完全依照注塑模具设计图纸尺寸来3)选中直线右击菜单—属性—赋予各自的属性——选中一条直线——网格生成网格——网格长度:5——关闭、由此得到浇注系统(2)冷却回路创建1)建模——冷却回路向导——填写相关数据:水道直径8mm、与工件距离20mm、零件外长度70mm、管道中心间距离30mm2)通过平移、复制等操作完成最后冷却水道设计5:盖帽注塑件的流动分析(1)材料的选取:如右图(2)工艺设置如下图(3)流动分析1)充填时间充填时间为动态结果,它可以显示从进料开始到充填完成整个注塑过程中,任一时刻流动前锋的位置。
Moldflow模流分析报告

体积收缩示意图
从上图可以看出此产品的收缩趋势明显,并且收缩的一致性较差. 因此推荐采用较大的保压压力及较长的保压时间
气孔
可能出现的气孔位置如上图所示的紫色区域
熔接线
图上可能看出熔接线的位置,但深度不足以影响产品的机械性能
翘曲变形, 所有的方向
可能发生的翘曲变形如 右图所示 X方向的变形 此变形结果包括了收缩 变形 可以根据图上数值进行 判断
Back ground
1. 2. 3. 4. 5. 6. 7. 使用软件: Moldflow plastics insight 6.1. 网格类型: fusion(表面网格). 塑胶材料: Zytel EMX 505A (PA66+20%GF, DuPont Engineering Polymers (Moldflow Verified)). 分析序列: 冷却->填充->-饱和->变形. 分析目的: a). 预测成型缺陷 b)预测变形趋势.
由上表可以看出,此材料较容易充填,并且对温度的变化不敏感..
有限元模型分析
Entity counts-------------------------------Surface triangles 28290 Nodes Connectivity regions 7 Mesh volume 19.8781 cm^3 Mesh area 1549.36 cm^2
注塑参数设置(参考)
Temperature Settings -----------------------------------------------------------------------------Melt temperature: 280.0000 C Mold cavity_side temperature: 75.0000 C Mold core-side temperature: 75.0000 C -----------------------------------------------------------------------------Injection Settings -----------------------------------------------------------------------------Injection control method: Injection Time Injection Time: 1.5000 s Nominal Flow rate: 285.2910 cm^3/s Packing pressure profile Duration Pressure (s) (MPa) 0.0000 80.0000 5.0000 80.0000 1.9094 0.0000 Cooling time: 33.4732 s -----------------------------------------------------------------------------Results from Flow Analysis -----------------------------------------------------------------------------Total volume of the part and cold runners: 427.9370 cm^3 Switch-over Pressure: 53.0071 MPa Maximum clamp force required: 164.9420 tonne
Moldflow模流分析报告范例

14
Shear Stress at Wall 最大剪切应力
流道系统上最大剪切应力: 2.8MPa 产品上最大剪切应力:0.4MPa
一般产品上的最大剪切应力,不要超过成型材料所允许的数值(如第8页所示, 该材料允许最大剪切应力为0.5MPa )。剪切应力太大,产品易开裂。
通过加大最大剪切应处壁厚,降低注塑速度,采用低粘度的材料,提高料温,可 减小剪切速率。
一般,脱模时相邻区域的体积收缩值相差>2%,产品表面易出现缩水。
可通过优化产品壁厚、浇口放置在壁厚区域、加大保压等措施,来降低 体积收缩。
DESIGN SOLUTIONS
18
Frozen Layer Fraction 凝固层因子
6.3s 12.2s 30.9s
Frozen Layer Fraction反映的是产品的凝固顺序。该产品在6.3秒时,红色区 域已凝固,导致安装孔位保压不足,故体积收缩较大,易出现表面缩水。 当产品100%凝固,冷流道系统凝固50%以上。产品可脱模。从而确定该产 品成型周期31s(不包括开合模时间)。 可通过优化冷却水路排布、降低局部壁厚区域的厚度、优化冷流道尺寸,来 缩短成型周期。
DESIGN SOLUTIONS
19
Sink Mark Estimate 凹痕深度
一般,凹痕数值>0.03mm,表面缩水较明显。 可通过加大基本壁厚、减小加强筋和螺栓柱等壁厚、加大保压等方式,来降 低凹痕深度。
DESIGN SOLUTIONS
20
Sink Mark Shaded 凹痕阴影显示
阴影显示凹痕的分析结果。圈示区域,肉眼看起来较明显。
22
Temperature, Part 冷却结束时产品表面温度
moldflow_分析报告
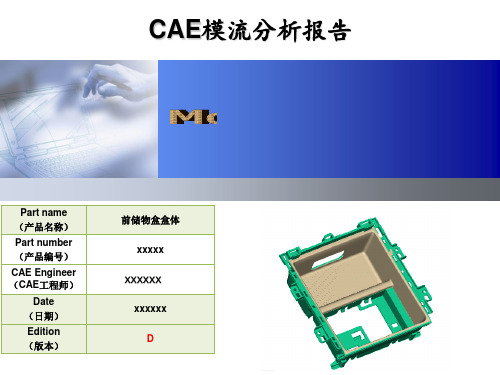
2022/1/12
Pressure at injection location:XY plot
第一射
第二射
Page - 16
injection pressure are acceptable. 注塑压力是可以接受的.
2022/1/12
Clamp force:XY plot(锁模力曲线)
Page - 17
2022/1/12 1/12/2022
Material Data(材料信息) 第二射
TPV Elastron V Grade V250.A64.B:Generic Default
01. 熔融密度
0.82366
g/cm^3
02. 固体密度
0.95654
g/cm^3
03. 建议模温 04. 建议料温
35
Press Shift+F5 to play the fill time animation,Flow behavior are umbalance, has short shot occur. (按shift+F5可播放动画,产品流动不平衡,没有短射发生)
2022/1/12
Fill time(充填时间)
50
℃
10. 最小料溫
210
℃
11. 最大料溫
05. 裂解温度
290
℃
12. 最大剪切力
06. 顶出温度
119
℃
13. 最大剪切率
07.粘度指数
VI(209)0089
14.熔体流动速率
PVT曲线图
40 60 190 230 0.25 100000
11.4
粘度曲线图
Page - 3
Moldflow模流分析报告

Page 9
Moldflow Analysis Report
Original1
原始方案分析結果
以下解析的包括冷卻、充填、保壓、翹曲分析的較爲重要的結果。
Page 10
Moldflow Analysis Report
冷卻水溫變化
Original1
由圖中可知,水溫升高較小 (進出口水溫差在兩度以 内),冷卻水路的長度設計 是可以達成冷卻要求的。成 型時不要爲了省事而將水路 串聯起來,否則會導致水路 過長水溫持續升高而降低冷 卻效果。
Original1
從圖中可知,公母模側 表面溫差較大,會使產 品公母模側收縮不均一 而導致翹曲變形問題。
Page 13
Moldflow Analysis Report
產品凝固需要的時間
Original1
上面兩圖表示的是從循環周期開始到產品完全凝固所需要的時 間。開模時圈示的幾個區域仍未凝固(如右圖,大部分區域在 16s内就可以凝固),而最長凝固時間竟達80s左右(也正是產 品上最厚的區域),故必將有嚴重縮水發生。
Page 14
Moldflow Analysis Report
充填時間(點擊Filபைடு நூலகம் time圖面即可播放動畫)
Original1
充填時間約為2.2秒,充填流動不太平衡。箭頭指示處為最後充填區域。圈示處的薄肋發 生嚴重滯流現象,導致產品短射。歸因於此肋太薄(僅0.9mm左右),而澆口又距離此肋 太近,塑膠流動到該處時受到極大阻力而停滯不前並迅速凝固了。實際試模中用GE PPE +PS+40%GF的塑膠可能勉強填滿,但成型窗口很窄,仍可能短射,對此應高度重視。
Original1
原始方案冷卻系統設計
- 1、下载文档前请自行甄别文档内容的完整性,平台不提供额外的编辑、内容补充、找答案等附加服务。
- 2、"仅部分预览"的文档,不可在线预览部分如存在完整性等问题,可反馈申请退款(可完整预览的文档不适用该条件!)。
- 3、如文档侵犯您的权益,请联系客服反馈,我们会尽快为您处理(人工客服工作时间:9:00-18:30)。
基于moldflow电池后盖注塑模型过程分析
大连工业大学
班级:材控101
摘要:moldflow作为注塑产品分析的软件,通过对它的使用是技术上的一大进步,通过对产品进行分析,以及设计方案的
优化,还有掌握基本流程分析,浇口位置设计,冷却系统和浇注系统的操作,工艺参数的设置,并在此基础上,优化方案,
达到工程参考的要求,为实际的生产指导提供帮助。
关键词:网格划分,流道设计,冷却系统,翘曲分析
前言
在塑料产品的设计和制造领域,随着塑料制品在汽车,电子,机械,船舶,航空等领域的广泛使用,以及对塑料制品的精度要求越来越高,传统的设计和成型方法已无法适应产品的更新换代和提高质量的要求。
与传统的工艺相比,moldflow技术无论在提高生产率,保证产品质量,还是在降低成本,减轻劳动强度等方面,都具有很大优越性。
所有moldflow产品围绕的都是moldflow的战略,——进行广泛的注塑分析。
通过“广泛的注塑分析”将moldflow积累的丰富的注塑经验带进制品和模具设计,并将注塑分析与实际注塑机控制相联系,自动监控和调整注塑机参数,从而优化模具设计、优化注塑机参数设置、提高制件产品质量,使制件具有更好的工艺性。
下面是分析的过程及结果:
1流动分析
(1)充填时间
通过对充填情况的观察,可以知道是否充填完全,充填时间,有无缺料,迟滞现象。
如图1可以知道充填时间为 1.83s。
图1 充填时间
(2)流动前沿温度
流动前沿温度如果过高,熔体流动将更为顺畅,熔接痕形成是熔体温度高,则熔接
痕的强度就较强。
本次分析采用的料温是
230度,而熔体的流动前沿温度是
230-230.6度,说明流动前沿的温度与料温
接近,充填效果较好,熔接痕的强度也很高。
当制件的流动前沿温度过低时,造成该结果的可能是制件的壁厚较薄或流程过长
等。
可以通过增加制件的壁厚,增加浇口的
数目,以及改变浇口的位置进行改善。
如图2和图3所示
图
2
图3
(3) 注塑位置的压力图
通过压力图可以看到压力的变化情况,看图可知当压力最大等于24.27Ma 是达到的时间是1.81s ,熔体的充填的过程中,压力先增加后降低,然后达到平衡。
比较注塑机的最大注塑压力,看出,满足要求。
如图4和图5 所示。
(4) 锁模力XY 图
计算锁模力时把XY 平面作为分型面,锁模力根据每个单元在XY 平面的投影面积和单元内的压力进行计算。
当使用的是表面模型时,考虑的是相互匹配的单元组,因此锁模力没有重复计算。
如果制件的几何结构,在XY 平面上的投影有重叠时,预测值将会偏大,这是可以通过设置,排出重叠单元。
如图6所示。
图
5
图6 (5) 气穴
气穴是在成型制品内部所形成的空隙,产生的原
因可能是由于排气不良造成熔体中的水分或挥发成分被封闭在成型材料中所形成的气泡,也可能是由于熔体冷却固化时体积收缩而产生在制品厚壁或加强筋、凸台等壁厚不均匀处的气泡。
可以通过调节料温不要太高,改变模具结构,减少狭长的流道,改善排气情况。
如图
7
图7
(6)推荐的螺杆速度XY图
推荐的螺杆速度是以流动前沿温度的速度更
加均匀为原则而建立起来的,它将有助于消除压力
的尖峰,同时改善制件表面的光洁度。
还可作为注
塑机参数的研究依据。
图8所示。
图8
(7)顶出时的体积收缩率
体积收缩率显示了制件在保压和冷却过程中的
收缩率的变化,整个型腔的收缩率应该均匀,通常
可以通过调整工艺参数和设置合理的保压控制曲
线进行改善。
通常在制件壁厚较大处和远离浇口的
位置体积率较大。
由分析结果可以看出,体积收缩
率较大的位置出现在远离浇口最后充填的位置,可
以通过延长保压时间,增加保压压力和更改该处的
制品壁厚等方式进行改善。
图9
(7)缩痕指数
缩痕指数显示出制件上产生缩痕的相对性,缩
痕指数值越大的区域,表明出现缩痕或缩孔的可能
性越大。
由结果可知,缩痕指数最大的位置出现在
流动的最末端,针对这种情况,可以延长保压是时
间,增加保压压力等方式来改善缩痕指数的情况。
如图10所示
图10
(2)冷却分析
(1)回路冷却介质温度
该结果显示了冷却水流经冷却水路是的温度
变化,一般情况下,冷却液随温度升高应在3度以
内,如图11,最高温度与最低温度之差为0.22度,
整个冷却系统模拟的效果比较理想。
(2)模具温度
通过结果可以看出模具的最高温度为40.28度,最低温度基本上集中在塑件的边缘。
(3)翘曲分析
翘曲变形指的是注塑制品形状偏离了
型腔形状,从而影响了制品的尺寸精度和形状精度的现象。
翘曲分析的目的是预测制品成型后的翘曲程度、分析翘曲产生的原因。
产生翘曲的原因主要有: ● 流动取向导致的收缩差异
● 型腔压力差导致沿流动方向的收缩差异 ● 不均匀冷却导致收缩差异
翘曲的分类:总体变形、冷却因素导致的变形、收
缩因素导致的变形、分子去想导致的
变形。
(1) 所有因素
从结果可以看出所有因素影响的变形总量为0.09,如图
12
图12
结果查看发现:冷却并不是引起翘曲的主要原因, (2) 收缩因素
由于收缩时引起的翘曲变形的主要因素,如图13,
(3)取向因素
在注塑成型时,由于注塑压力和保压压力对制品的收缩有很大的影响,通常较高的注塑压力和保压压力会是制品的收缩较小,模腔中的压力分布在浇口处最大,而在填充的末端处最小,沿流动方向上存在明显的压力降,特别是对于流程较长或壁厚较薄的制品,一般在远离浇口处的型腔末端收缩比较大。
熔体在高温高压下沿一定的路径被注塑到模具型腔中,高分子链收到拉伸而产生取向,进而形成各向异性的收缩行为,如果制品的刚性不足时,会产生翘曲。
为了避免出现翘曲,可以采用增加压力和保压
时间的方式来减少收缩,也可以通过提高模温,降低收缩。
影响制品翘曲变形的因素:
●材料的因素
●制品的结构设计因素包括壁厚的设计、加强
筋的设计、
●模具设计的因素包括浇口位置影响、浇口数
目影响、冷却系统设计的影响、顶出系统
●注塑加工工艺条件
结论
通过使用moldflow来修改方案和设计思路,更好的为我们指导生产。
参考文献
1 王刚,单岩 Moldflow模具分析应用实例北京:
清华大学出版社,2005,
2宋满仓,乔飞,王振注塑制品厚度对收缩率变化影响的研究模具制造,2006,(6):47-49. 3郭志英,梁书云,张宜生,高密度聚乙烯平板翘曲变形实验研究塑料工业,2001,29(2):
37-40
4丁玉兴,温守东影响塑料注塑制品内应力的因素探讨承德名族师专学报 2003,23(2):86,96 5杨杨,刘春太,成型温度对纤维增强注塑熔接线拉伸性能的影响郑州大学学报:(工学报),
2004,25(3):102-106。