超声加工技术在陶瓷加工中的应用
超声波加工技术论文

超声波加工技术论文超声波加工是利用工具断面的超声振动,通过磨料悬浮液加工脆硬材料的一种成型方法。
这是店铺为大家整理的超声波加工技术论文,仅供参考!超声波加工技术论文篇一超声加工的应用及发展摘要:陶瓷、光学玻璃、功能晶体、金刚石、宝石和先进复合材料等具有优越的物理、化学和机械性能,在航空、航天、军工、电子、汽车和生物工程等领域正得到越来越广泛的应用,并且其应用还在不断向新的领域扩展。
与此同时,人们开始探索特种加工方式来加工这些难加工材料。
超声加工技术就是在此背景下发展起来的,实践证明,它是加工上述难加工硬脆材料的高效和经济有效的方法之一。
超声技术在工业中的应用开始于20世纪10~20年代,它是以经典声学理论为基础,同时结合电子技术、计量技术、机械振动和材料学等学科领域的成就发展起来的一门综合技术。
超声技术的应用可划分为功率超声和检测超声两大领域。
其中,功率超声是利用超声振动形成的能量使物质的一些物理、化学和生物特性或状态发生改变,或者使这种状态改变加快的一门技术。
功率超声在机械加工方面的应用,按其加工工艺特征大致分为2类,一类是带磨料的超声磨料加工(包括游离磨料和固结磨料),另一类是采用切削刀具与其他加工方法相结合形成的超声复合加工。
关键词:超生加工发展特点及优势应用潜能一、超声加工技术的发展1927年,美国物理学家伍德和卢米斯最早作了超声加工试验,利用超声振动对玻璃板进行雕刻和快速钻孔。
但当时超声加工并未应用到工业上,直到大约1940年在文献上第一次出现超声加工(USM-Ultrasonic Machining)工艺技术描述以后,超声加工才吸引了大家的注意,并且逐渐融入到其他的工业领域。
1951年,科恩研制了第一台实用的超声加工机,为超声加工技术的发展奠定了基础。
USM提供了比常规机械加工技术更多的优点。
例如,导电和非导电材料它都可以加工,并且加工复杂的三维轮廓也可以像简单形状那样快速。
此外,超声加工过程不会产生有害的热区域,同时也不会在工件表面带来化学/ 电气变化,而且加工时在工件表面上所产生的有压缩力的残余应力可以增加被加工零件的高周期性疲劳强度。
超声加工技术的应用及发展趋势
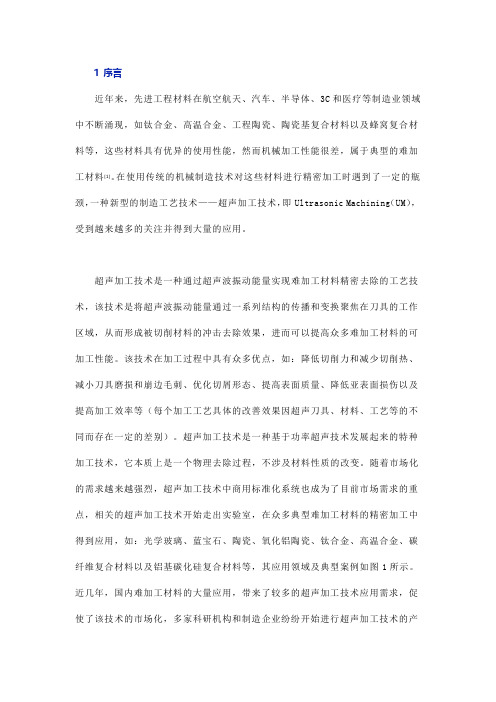
1 序言近年来,先进工程材料在航空航天、汽车、半导体、3C和医疗等制造业领域中不断涌现,如钛合金、高温合金、工程陶瓷、陶瓷基复合材料以及蜂窝复合材料等,这些材料具有优异的使用性能,然而机械加工性能很差,属于典型的难加工材料[1]。
在使用传统的机械制造技术对这些材料进行精密加工时遇到了一定的瓶颈,一种新型的制造工艺技术——超声加工技术,即Ultrasonic Machining(UM),受到越来越多的关注并得到大量的应用。
超声加工技术是一种通过超声波振动能量实现难加工材料精密去除的工艺技术,该技术是将超声波振动能量通过一系列结构的传播和变换聚焦在刀具的工作区域,从而形成被切削材料的冲击去除效果,进而可以提高众多难加工材料的可加工性能。
该技术在加工过程中具有众多优点,如:降低切削力和减少切削热、减小刀具磨损和崩边毛刺、优化切屑形态、提高表面质量、降低亚表面损伤以及提高加工效率等(每个加工工艺具体的改善效果因超声刀具、材料、工艺等的不同而存在一定的差别)。
超声加工技术是一种基于功率超声技术发展起来的特种加工技术,它本质上是一个物理去除过程,不涉及材料性质的改变。
随着市场化的需求越来越强烈,超声加工技术中商用标准化系统也成为了目前市场需求的重点,相关的超声加工技术开始走出实验室,在众多典型难加工材料的精密加工中得到应用,如:光学玻璃、蓝宝石、陶瓷、氧化铝陶瓷、钛合金、高温合金、碳纤维复合材料以及铝基碳化硅复合材料等,其应用领域及典型案例如图1所示。
近几年,国内难加工材料的大量应用,带来了较多的超声加工技术应用需求,促使了该技术的市场化,多家科研机构和制造企业纷纷开始进行超声加工技术的产业化应用。
图1超声加工应用领域及典型案例2 超声加工技术发展现状“工欲善其事,必先利其器”,超声加工技术是针对难加工材料精密加工的利器。
在大多数切削加工领域,超声加工更确切的名称应该为“超声辅助精密加工”,即在传统切削加工技术上辅助超声振动,从而实现特殊的材料去除效果。
超声加工技术及其在陶瓷加工中的应用_梁晶晶
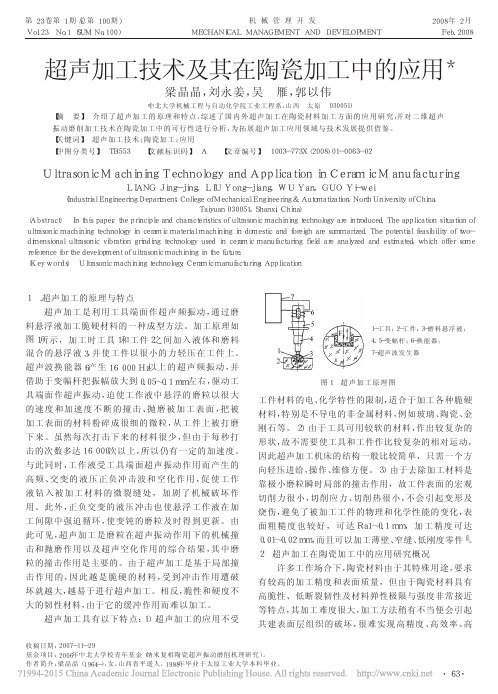
1.超声加工的原理与特点超声加工是利用工具端面作超声频振动,通过磨料悬浮液加工脆硬材料的一种成型方法。
加工原理如图1所示,加工时工具1和工件2之间加入液体和磨料混合的悬浮液3,并使工件以很小的力轻压在工件上。
超声波换能器6产生16000Hz以上的超声频振动,并借助于变幅杆把振幅放大到0.05~0.1mm左右,驱动工具端面作超声振动,迫使工作液中悬浮的磨粒以很大的速度和加速度不断的撞击、抛磨被加工表面,把被加工表面的材料粉碎成很细的微粒,从工件上被打磨下来。
虽然每次打击下来的材料很少,但由于每秒打击的次数多达16000次以上,所以仍有一定的加速度。
与此同时,工作液受工具端面超声振动作用而产生的高频、交变的液压正负冲击波和空化作用,促使工作液钻入被加工材料的微裂缝处,加剧了机械破坏作用。
此外,正负交变的液压冲击也使悬浮工作液在加工间隙中强迫循环,使变钝的磨粒及时得到更新。
由此可见,超声加工是磨粒在超声振动作用下的机械撞击和抛磨作用以及超声空化作用的综合结果,其中磨粒的撞击作用是主要的。
由于超声加工是基于局部撞击作用的,因此越是脆硬的材料,受到冲击作用遭破坏就越大,越易于进行超声加工。
相反,脆性和硬度不大的韧性材料,由于它的缓冲作用而难以加工。
超声加工具有以下特点:1)超声加工的应用不受工件材料的电、化学特性的限制,适合于加工各种脆硬材料,特别是不导电的非金属材料,例如玻璃、陶瓷、金刚石等。
2)由于工具可用较软的材料,作出较复杂的形状,故不需要使工具和工件作比较复杂的相对运动,因此超声加工机床的结构一般比较简单,只需一个方向轻压进给,操作、维修方便。
3)由于去除加工材料是靠极小磨粒瞬时局部的撞击作用,故工件表面的宏观切削力很小,切削应力、切削热很小,不会引起变形及烧伤,避免了被加工工件的物理和化学性能的变化,表面粗糙度也较好,可达Ra1~0.1mm,加工精度可达0.01~0.02mm,而且可以加工薄壁、窄缝、低刚度零件[1]。
超声波在精密加工中的应用研究

超声波在精密加工中的应用研究超声波技术是一种在材料加工过程中非常重要的工艺技术,它可以增强处理效果,优化工件质量,缩短加工周期,降低能源消耗。
近年来,随着科学技术的进步和工业化生产的不断发展,超声波技术在精密加工领域发挥的作用越来越大。
本文将探讨超声波在精密加工中的应用研究。
一、超声波在金属加工中的应用1. 拉伸加工中的应用超声波在拉伸加工中的应用较为普遍,它可以使金属材料在最小的变形条件下达到极限变形程度。
超声波是基于共振原理,在振幅足够大时,其作用力可以远远超过传统的拉伸加工。
目前,超声波拉伸加工已广泛应用于锻造、压铸、拉伸等金属加工领域。
2. 表面处理中的应用超声波在金属表面处理中的应用主要包括超声波磨料、超声波打磨、超声波除锈等。
这些处理方式可以使金属表面更加平滑,减少金属表面的缺陷,提高金属表面的质量和稳定性。
3. 金属切削加工中的应用超声波在金属切削加工中的应用与其他技术相比具有独特的优势,它可以提高加工质量,缩短加工周期,降低加工成本等。
目前,超声波在金属切削领域已得到广泛应用,如超声波加工中心、超声波切割机、超声波皮带磨削机等。
二、超声波在非金属加工中的应用除了在金属加工中广泛应用之外,超声波技术在非金属加工领域中也发挥了不同的作用。
1. 塑料加工中的应用超声波技术在塑料加工领域中具有广泛的应用前景,主要包括超声波焊接、超声波水处理和超声波清洗等。
这些应用可以提高产品的品质和稳定性,同时缩短生产周期。
2. 陶瓷加工中的应用超声波在陶瓷加工中的应用主要包括超声波破碎、超声波磨料和超声波鼓磨等。
这些应用可以提高陶瓷工件的质量和精度,同时降低加工难度和成本。
三、超声波在医疗领域中的应用除了在工业领域中应用之外,超声波技术在医疗领域中也具有广泛的应用。
超声波在医疗领域中的优点在于非侵入性、无放射性、低成本和可重复使用等方面。
目前,超声波医疗设备已非常普及,主要包括超声波诊断仪、超声波手术机和超声波治疗仪等。
超声波加工技术在制造业中的应用及发展
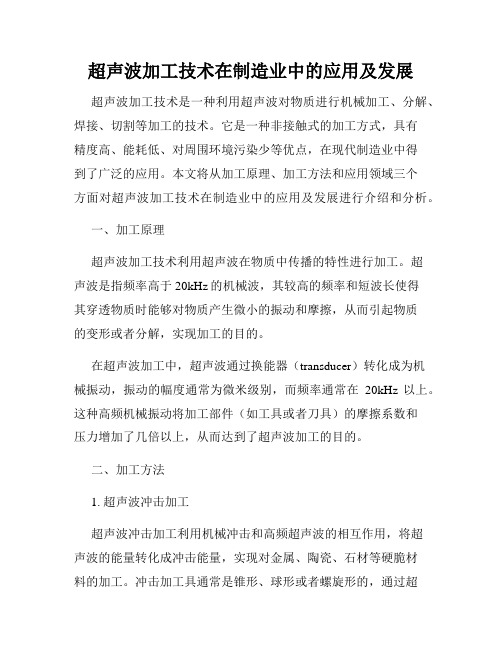
超声波加工技术在制造业中的应用及发展超声波加工技术是一种利用超声波对物质进行机械加工、分解、焊接、切割等加工的技术。
它是一种非接触式的加工方式,具有精度高、能耗低、对周围环境污染少等优点,在现代制造业中得到了广泛的应用。
本文将从加工原理、加工方法和应用领域三个方面对超声波加工技术在制造业中的应用及发展进行介绍和分析。
一、加工原理超声波加工技术利用超声波在物质中传播的特性进行加工。
超声波是指频率高于20kHz的机械波,其较高的频率和短波长使得其穿透物质时能够对物质产生微小的振动和摩擦,从而引起物质的变形或者分解,实现加工的目的。
在超声波加工中,超声波通过换能器(transducer)转化成为机械振动,振动的幅度通常为微米级别,而频率通常在20kHz以上。
这种高频机械振动将加工部件(如工具或者刀具)的摩擦系数和压力增加了几倍以上,从而达到了超声波加工的目的。
二、加工方法1. 超声波冲击加工超声波冲击加工利用机械冲击和高频超声波的相互作用,将超声波的能量转化成冲击能量,实现对金属、陶瓷、石材等硬脆材料的加工。
冲击加工具通常是锥形、球形或者螺旋形的,通过超声波的震动驱动,加工部分会发生爆炸性的形变和裂纹,从而实现加工的目的。
超声波冲击加工的优点是能够进行精细加工,但加工速度较慢,只适用于小加工量的生产。
2. 超声波切割加工超声波切割加工是利用超声波在物质中产生的高频振动,通过对切割工具施加高频振动,实现对材料的切割。
切割工具通常是金属薄板、金属丝、钻头和锯片等。
切割时,超声波的能量通过切割工具传递到材料中,使其发生振动和变形,从而实现切割的目的。
超声波切割加工的优点是能够进行高速切割,不会产生粉尘和机床磨损,但是对材料有一定的厚度限制。
3. 超声波焊接超声波焊接是利用超声波在物质中产生的高频振动,通过对金属表面施加振动,从而实现金属的焊接。
焊接时,将金属部分挤压在一起,在部件接触面上施加高频振动,使金属表面微观颗粒之间不断摩擦和碰撞,达到焊接的目的。
超声波加工机床在精密机械加工中的应用研究

超声波加工机床在精密机械加工中的应用研究超声波加工机床是一种利用高频振动将声波能量转化为机械能的专用设备。
它在精密机械加工领域具有广泛的应用,可以用于加工各种材料,如金属、陶瓷、塑料等。
本文将对超声波加工机床在精密机械加工中的应用进行深入研究,并探讨其优势和发展前景。
一、超声波加工机床的基本原理超声波加工机床利用高频振动的原理进行加工,其基本原理可以概括为以下几点:1.1 超声波传导:超声波在材料中的传导速度较高,使得能量传递到工件表面时能够迅速产生切削效果。
1.2 液体介质:超声波加工通常是在液体介质中进行的,液体可有效传导声波,减少工件表面的摩擦和磨损。
1.3 脉冲能量:超声波加工机床通常以脉冲形式输出能量,利用脉冲能量的瞬时冲击力来实现加工效果。
二、超声波加工机床在精密机械加工中的应用领域2.1 集成电路加工:超声波加工机床可以用于集成电路的微细加工,例如微孔加工、蚀刻、刻蚀等。
2.2 珠宝首饰加工:超声波加工机床在珠宝首饰加工中具有较大的优势,可以用于切割、打磨、雕刻等工艺。
2.3 高硬度材料加工:超声波加工机床可以用于高硬度材料的切削和表面处理,如金刚石、硬质合金等。
2.4 医疗器械加工:超声波加工机床可以用于医疗器械的加工和组装,保证产品的精度和质量。
三、超声波加工机床的优势超声波加工机床相比传统机床在精密机械加工中具有以下几个优势:3.1 高精度:超声波加工机床可以实现精细加工和高精度加工,提高产品质量和精度。
3.2 低热影响区:超声波加工机床所产生的热影响区较小,不会对工件产生过多的热变形和残余应力。
3.3 切削力小:超声波加工机床采用脉冲形式输出能量,切削力小,不易造成刀具磨损和工件表面损伤。
3.4 特殊材料加工:超声波加工机床可以用于加工各种特殊材料,如玻璃、陶瓷等,具有广泛的适应性。
四、超声波加工机床的发展前景超声波加工机床作为一种高效、高精度的加工设备,在精密机械加工领域有着广阔的应用前景。
简述超声波加工的特点和应用范围

简述超声波加工的特点和应用范围
超声波加工是一种利用超声波来进行物体加工和处理的技术。
这种技
术具有许多独特的特点和应用范围,下面将对其进行简要介绍。
一、特点
1. 高精度:超声波可以精确地控制物体表面的处理程度,从而实现高
精度的加工效果。
2. 高效率:超声波加工速度快、效率高,可以大大提高生产效率。
3. 低损耗:超声波可以在不损坏物体表面的情况下进行处理,因此不
会造成物体的损耗,保持物体完整性。
4. 处理范围广泛:超声波可以用于处理各种材料,如金属、陶瓷、塑料、纸张等。
5. 节能环保:超声波加工不需要使用化学物质或其他有害物质,可以
减少环境污染,因此具有良好的节能环保效果。
二、应用范围
1. 加工生产:超声波加工可用于制造各种零部件及产品的加工,如飞机、汽车、电器等产品。
2. 精密加工:超声波加工可用于精密的加工领域,例如制造电子元件、医疗器械、钟表等精密产品。
3. 清洗处理:超声波还可用于清洗处理,例如清洗机器零件、玻璃器
皿、金属零件等。
4. 软物料处理:超声波可用于软物料的加工处理,如医用棉、食品、生物学样品等。
5. 医疗领域:超声波在医疗领域的应用范围也很广泛,如超声波胶囊内镜、超声治疗、透析等。
总之,超声波加工成为现代工业生产中不可或缺的一种技术。
其应用范围广泛,能够提高生产效率、降低成本,同时还有良好的节能环保效果。
随着技术的不断发展,相信超声波加工在未来还会发挥更加重要的作用。
简述超声加工工艺特点及应用
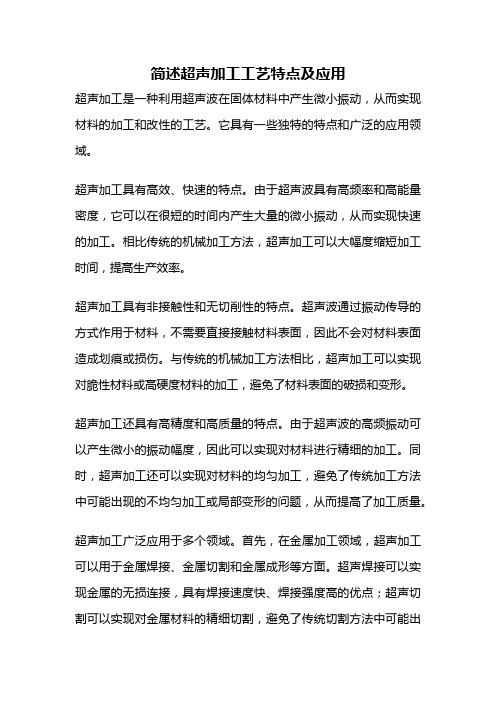
简述超声加工工艺特点及应用超声加工是一种利用超声波在固体材料中产生微小振动,从而实现材料的加工和改性的工艺。
它具有一些独特的特点和广泛的应用领域。
超声加工具有高效、快速的特点。
由于超声波具有高频率和高能量密度,它可以在很短的时间内产生大量的微小振动,从而实现快速的加工。
相比传统的机械加工方法,超声加工可以大幅度缩短加工时间,提高生产效率。
超声加工具有非接触性和无切削性的特点。
超声波通过振动传导的方式作用于材料,不需要直接接触材料表面,因此不会对材料表面造成划痕或损伤。
与传统的机械加工方法相比,超声加工可以实现对脆性材料或高硬度材料的加工,避免了材料表面的破损和变形。
超声加工还具有高精度和高质量的特点。
由于超声波的高频振动可以产生微小的振动幅度,因此可以实现对材料进行精细的加工。
同时,超声加工还可以实现对材料的均匀加工,避免了传统加工方法中可能出现的不均匀加工或局部变形的问题,从而提高了加工质量。
超声加工广泛应用于多个领域。
首先,在金属加工领域,超声加工可以用于金属焊接、金属切割和金属成形等方面。
超声焊接可以实现金属的无损连接,具有焊接速度快、焊接强度高的优点;超声切割可以实现对金属材料的精细切割,避免了传统切割方法中可能出现的毛刺和变形问题;超声成形可以实现对金属材料的精确成型,提高了零件的加工精度。
在陶瓷加工领域,超声加工可以用于陶瓷的切割、打孔和表面处理等方面。
由于陶瓷材料具有脆性和高硬度的特点,传统的加工方法往往难以实现对陶瓷材料的加工。
而超声加工可以通过振动作用将能量集中在局部区域,实现对陶瓷材料的切割和打孔,同时还可以通过超声波的热效应对陶瓷材料进行表面处理,提高陶瓷材料的表面质量。
在生物医学领域,超声加工也得到广泛的应用。
超声加工可以用于生物医学器械的制造和生物医学材料的改性。
超声焊接可以实现生物医学器械的无损连接,避免了传统焊接方法中可能出现的材料变形和焊接强度低的问题;超声改性可以改善生物医学材料的表面性能,使其更适合用于人体内部的应用。
- 1、下载文档前请自行甄别文档内容的完整性,平台不提供额外的编辑、内容补充、找答案等附加服务。
- 2、"仅部分预览"的文档,不可在线预览部分如存在完整性等问题,可反馈申请退款(可完整预览的文档不适用该条件!)。
- 3、如文档侵犯您的权益,请联系客服反馈,我们会尽快为您处理(人工客服工作时间:9:00-18:30)。
论超声加工技术在陶瓷加工中的应用摘要:本文结合超声加工技术原理,对超声加工技术在陶瓷加工中的应用进行分析,着重介绍二维超声加工技术的运用,以更好地
保障工程陶瓷加工质量水平。
关键词:超声加工陶瓷加工二维超声技术应用
中图分类号:tg74 文献标识码:a 文章编
号:1672-3791(2012)09(c)-0094-01
超声加工技术的应用,主要利用超声振动工具,在具备磨料的干磨料、液体介质中形成冲击力、液压力、抛磨力等,产生气蚀之后可去除材料;或者将工具、工件等按照一定方向实行超声频振动,形成振动加工;或者通过超声振动作用,促进工件的相互结合。
近年来,超声加工技术已经广泛发展起来,并且在磨削加工、超声振动切削领域广泛应用,尤其在工程陶瓷加工中,已经取得一定进展,解决了诸多关键性技术问题,效果良好。
1 超声加工技术原理
将磨料悬浮液加入到工件与工具之间,利用超声发生器形成超
声振动波;经过换能器的转换之后,形成超声机械振动,这样悬浮液中产生的磨粒就会对加工表面造成撞击,被加工材料的局部就会经过撞击而掉落。
在工件的表面,具有瞬间交替作用的正压冲击波与负压空化作用,以此强化加工过程。
在超声加工技术中,涉及到机床、超声振动系统、电源、轴向力反馈保护系统等,且超声振动系统是关键、核心环节[1],主要包括以下几部分。
1.1 超声波换能器
通过应用超声波转换器,可以将高频电振动转化为机械振动,并通过以下两种形式实现:(1)磁致伸缩法。
在处于变化状态的磁场中,砦铁磁体或者铁氧化体的长度也会发生变化,即磁致伸缩效应。
在磁致伸缩换能器中,q值(即能量峰值锐度)相对较低,因此可以传递较宽的频率,以此增加设计变幅杆的灵活性,而刀具与其相连接之后,即使发生加工过程的磨损现象,也可进行重磨[2];(2)压电效应法。
通过应用压电晶片,在外电场中随着电场的方向变化而产生形变,利用压电换能器将高频的电振动转化为机械振动。
压电换能器的电声转换频率较高,不会产生热量损失,也不需要采取冷却方法,可支持旋转性操作,便于操作。
1.2 变幅杆
通过应用变幅杆,可以进一步扩大换能器中发出的超声振幅,支持超声波加工过程。
这主要由于在任意截面中的振动能量保持不变,而截面越小的地方,能量密度则越大,而振动幅度也随之加大。
在加工大功率超声过程中,可以将变幅杆与工具设计为一个整体,可考
虑采用cad技术、cam技术、有限元分析技术等[3]。
1.3 工具
可以将工具看作是变幅杆的负载,因此工具尺寸大小、质量好坏等,将与变幅杆的连接密切相关,同时也对超声振动频率、超声波加工性能等产生影响。
通过应用螺钉或者焊接形式,将工具固定到变幅杆中。
如果采取可拆卸的方式,虽然便于工具的更换速度,但是可
能造成超声能量损失、工具松懈或者过于疲劳等缺陷。
2 超声加工技术在陶瓷加工中的应用
陶瓷材料可以广泛应用于诸多工作场合,由于其用途的特殊性,因此对加工精度、表面质量等提出诸多要求;但是考虑到陶瓷材料的低断裂韧性、高脆性等特征,和材料的弹性较为接近,因此加工过程存在一定难度,如果加工方法不当,可能破坏表面层组织,对加工质量造成影响。
因此,加工技术的选择,将对陶瓷材料应用范围产生重要作用。
当前,国内外诸多学者已经开展超声加工技术在陶瓷加工中的应用研究。
2.1 精密超声加工技术的应用
精密超声加工技术主要针对a12o3陶瓷材料中的微去除量应用,主要对陶瓷材料中超声加工的特征进行模拟,分析材料的去除原理。
经大量的实践研究来看,在低冲击力的作用下。
陶瓷材料的结构会发生变化,同时出现晶粒错位问题,而过高的冲击力,又会发生凹痕或者裂纹[4]。
2.2 超声振动脉冲放电加工技术的应用
超声振动脉冲放电加工技术主要应用于工程陶瓷小孔中,工具电极中的超声振动,形成脉冲放电,进而取替传统的电火花加工形式,发挥专用脉冲发生器的重要作用。
另外,通过应用工具电极中超声振动,还可以对缝隙进行清洗。
该技术可以对a12o3基陶瓷刀具的材料表面方孔进行定位和加工;通过对其工作机理、加工参数等研究,可获得不同陶瓷材料加工的效率、表面粗糙性等,总结发生影
响的规律[5]。
通过实验结果来看,采取该种复合加工技术,结合超声加工与放电加工的双重优势,提高陶瓷材料的性能与质量,更好
地投入使用。
2.3 超声振动磨削技术
该技术主要针对陶瓷深孔加工,具有高效性、精密性等特征,通过对超声振动磨削技术及传统的磨削陶瓷深孔技术进行对比。
从实验结果来看,采取超声振动磨削技术,可有效保障陶瓷加工的效率,并可避免在加工过程中发生的裂纹、凹坑等缺陷和问题,因此在陶瓷加工中具有良好的应用空间,将成为今后发展趋势。
3 二维超声技术在陶瓷加工中的应用
当前,超声振动磨削机理的研究较为深入,尤其是细晶氧化锆陶瓷试件中,进行二维超声振动磨削试验,对其性能、应用等进行确定。
该实验中,主要针对磨削的深度,对磨削力、材料去除率、表面粗糙度等因素进行探讨。
通过实验结果,获得如下体会。
(1)通过研究普通的磨削技术,与二维超声振动磨削技术进行对比,充分体现了磨削深度的变化对增加材料去除率的影响;在同样
的磨削深度状态下,二维超声振动磨削的去除率强于普通磨削技术;而超声振动磨削材料的去除率可以达到普通技术的2倍左右[6]。
(2)无论是普通磨削技术还是超声振动磨削技术,都将随着磨削深度的增加而有所提高,如果达到了临界值,那么磨削力就会产生
波动,进而超过了该临界的深度值,磨削力进一步下降。
经实验来看,采用超声振动磨削力技术,与普通磨削力相比将减少20%~35%左
右。
(3)在同样的切深状态下,二维超声振动的磨削表面粗超度较低,与普通的磨削技术相比,表面粗糙度可降低20%~50%,而二维振动
磨削可有效保障磨削的性能与表面质量。
(4)超声加工技术的应用,可有效改善传统加工技术的弊端,尤
其在脆硬材料加工中的应用,推动材料加工技术的优化发展。
由上可见,通过超声加工技术在陶瓷加工中的应用,可有效控制成本,提高加工效率,确保工件的良好性能与质量水平。
因此,经大量实验来看,超声加工技术是一种有效的工程陶瓷加工方法。
随着我国在陶瓷材料加工方面的不断探索与研究,研发了越来越多先进的加工设备、掌握了复合加工方法,推动工程陶瓷加工技术的成熟发展,进而为今后工程陶瓷材料的应用拓展空间。
参考文献
[1]张磊.硬脆材料异形面超声微精加工工艺研究[d].扬州大学,2010.
[2]冯平法,郑书友,张京京.功率超声加工关键技术的研究进展[j].制造技术与机床,2009(5).
[3]赵文凤,郭钟宁,唐勇军.新型超声振动结构的研究进展[j].机床与液压,2010(15).
[4]贾宝贤,王冬生,赵万生,等.微细超声加工技术的发展现状
与评析[j].电加工与模具,2006(4).
[5]魏星.面向先进性材料的超声加工技术[a].中国电子学会
2008年电子机械、微波结构工艺学术会议,2008.
[6]郑建新,徐家文,吕正兵.陶瓷材料延性域磨削机理[j].硅酸盐学报,2006(1).。