激光熔覆成形技术及其在汽车工业中的应用
激光熔覆技术的发展前景
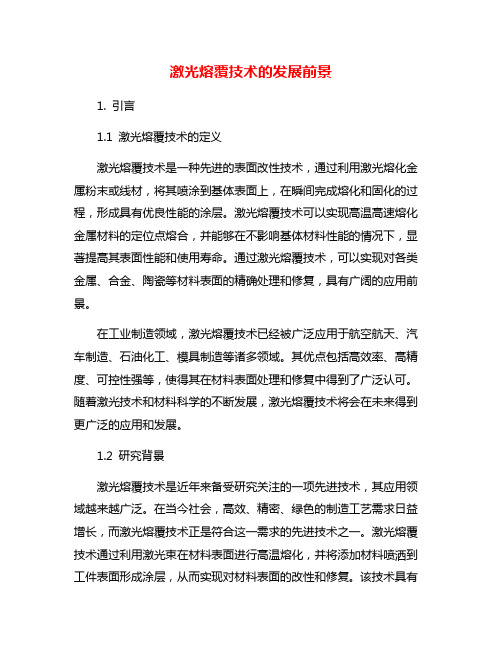
激光熔覆技术的发展前景1. 引言1.1 激光熔覆技术的定义激光熔覆技术是一种先进的表面改性技术,通过利用激光熔化金属粉末或线材,将其喷涂到基体表面上,在瞬间完成熔化和固化的过程,形成具有优良性能的涂层。
激光熔覆技术可以实现高温高速熔化金属材料的定位点熔合,并能够在不影响基体材料性能的情况下,显著提高其表面性能和使用寿命。
通过激光熔覆技术,可以实现对各类金属、合金、陶瓷等材料表面的精确处理和修复,具有广阔的应用前景。
在工业制造领域,激光熔覆技术已经被广泛应用于航空航天、汽车制造、石油化工、模具制造等诸多领域。
其优点包括高效率、高精度、可控性强等,使得其在材料表面处理和修复中得到了广泛认可。
随着激光技术和材料科学的不断发展,激光熔覆技术将会在未来得到更广泛的应用和发展。
1.2 研究背景激光熔覆技术是近年来备受研究关注的一项先进技术,其应用领域越来越广泛。
在当今社会,高效、精密、绿色的制造工艺需求日益增长,而激光熔覆技术正是符合这一需求的先进技术之一。
激光熔覆技术通过利用激光束在材料表面进行高温熔化,并将添加材料喷洒到工件表面形成涂层,从而实现对材料表面的改性和修复。
该技术具有精度高、热影响区小、成形自由度大等优点,为材料加工和制造业带来了革命性的变革。
在当前科技进步和工业发展的大背景下,激光熔覆技术得到了广泛的研究和应用。
随着人们对材料表面性能要求的不断提高,激光熔覆技术已成为一种不可或缺的表面处理和修复工艺。
在制造业领域,激光熔覆技术开启了全新的制造范式,使得传统的加工方法逐渐被取代。
深入研究激光熔覆技术的原理与特点,探索其在材料表面处理和制造业中的应用,对于推动我国制造业的发展具有重要的意义。
2. 正文2.1 激光熔覆技术的原理与特点激光熔覆技术是一种利用激光束对材料表面进行加热,然后与添加剂进行熔化混合,最终形成具有特定性能的涂层的技术。
其原理主要是利用激光束的高能量密度,使加热区域迅速升温,达到熔化温度并与添加剂反应。
激光熔覆技术的发展现状

激光熔覆技术的发展现状引言
1.1 什么是激光熔覆技术
1.2 激光熔覆技术的应用领域
激光熔覆技术的原理
2.1 激光熔覆的基本过程
2.2 激光熔覆的物理原理
2.3 激光熔覆设备及系统
激光熔覆技术的发展历程
3.1 初期发展阶段
3.2 技术改进与应用拓展
3.3 现代激光熔覆技术的进展
激光熔覆技术的优势与局限性
4.1 优势
4.2 局限性
激光熔覆技术的应用案例
5.1 汽车制造业中的应用
5.1.1 引擎缸体熔覆修复
5.1.2 汽车零部件的功能修复
5.2 能源行业中的应用
5.2.1 火力发电设备的熔覆保护
5.2.2 涡轮机叶片的修复与再生利用
5.3 航空航天领域中的应用
5.3.1 航空发动机叶片的修复
5.3.2 航天器表面覆盖材料的制备
激光熔覆技术的挑战与展望
6.1 材料选择的挑战
6.2 激光熔覆技术在大规模应用中面临的问题
6.3 未来发展方向与展望
结论
激光熔覆技术作为一种高效、精密的表面修复和涂层制备方法,已经在多个领域得到了广泛应用。
随着科技的进步和技术的不断创新,激光熔覆技术在材料修复、零部件制备等方面的应用前景更加广阔。
然而,该技术在材料选择、大规模应用等方面仍然面临一些挑战和问题,需要进一步研究和改进。
展望未来,随着技术的成熟和应用的推广,激光熔覆技术有望在更多领域发挥其重要作用。
激光熔覆技术研究现状及其发展

激光熔覆技术研究现状及其发展一、本文概述激光熔覆技术,作为一种先进的表面处理技术,近年来在材料科学、机械制造、航空航天等领域引起了广泛关注。
本文旨在全面综述激光熔覆技术的研究现状及其发展趋势,以期为相关领域的研究人员和技术人员提供有价值的参考。
文章首先将对激光熔覆技术的基本原理、特点及其应用领域进行简要介绍,然后重点分析当前激光熔覆技术的研究热点和难点,包括材料选择、工艺优化、性能评估等方面。
在此基础上,文章将探讨激光熔覆技术的发展趋势和未来展望,包括新材料、新工艺、新技术的应用以及环境友好型、智能化、高效化的发展趋势。
通过本文的综述,读者可以对激光熔覆技术的最新研究成果和发展动态有一个全面而深入的了解,为相关领域的研究和实践提供有益的借鉴和指导。
二、激光熔覆技术的研究现状激光熔覆技术自问世以来,就凭借其独特的优势在材料科学与工程领域引起了广泛的关注和研究。
该技术以其高精度、高能量密度和快速加热冷却过程等特点,使得在材料表面实现高质量、高性能的熔覆层成为可能。
随着科技的不断发展,激光熔覆技术的研究现状呈现出以下几个主要特点。
在材料选择方面,激光熔覆技术已经不仅仅局限于金属材料的熔覆。
近年来,陶瓷、高分子材料甚至复合材料的激光熔覆也开始得到研究,这极大地扩展了激光熔覆技术的应用范围。
同时,对于金属材料的熔覆,也逐步实现了多元化,涵盖了铁基、镍基、钴基等多种合金材料。
在熔覆过程控制方面,研究者们通过引入数值模拟、智能控制等技术手段,实现了对激光熔覆过程更为精准的控制。
这包括对激光功率、扫描速度、送粉速度等关键参数的优化,以及对熔池温度、形貌的实时监控和调控。
这些技术的发展,使得激光熔覆的质量稳定性和重复性得到了显著提升。
再次,在熔覆层性能提升方面,研究者们通过设计合理的熔覆层结构和成分,实现了对熔覆层硬度、耐磨性、耐腐蚀性等多种性能的提升。
同时,还通过引入纳米颗粒、增强相等手段,进一步优化了熔覆层的显微组织和性能。
激光熔覆技术的原理和应用
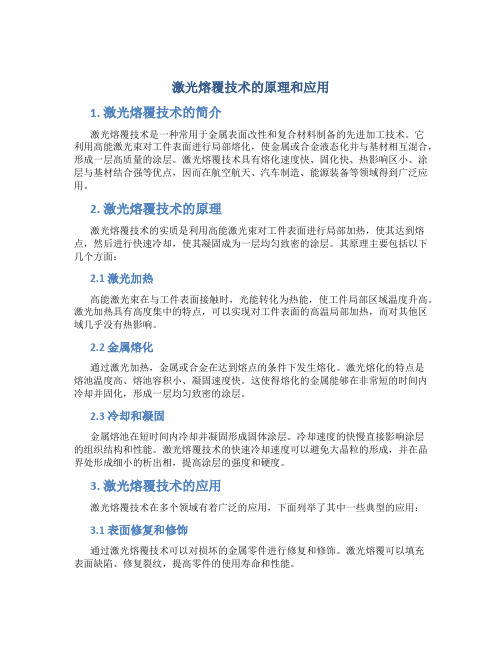
激光熔覆技术的原理和应用1. 激光熔覆技术的简介激光熔覆技术是一种常用于金属表面改性和复合材料制备的先进加工技术。
它利用高能激光束对工件表面进行局部熔化,使金属或合金液态化并与基材相互混合,形成一层高质量的涂层。
激光熔覆技术具有熔化速度快、固化快、热影响区小、涂层与基材结合强等优点,因而在航空航天、汽车制造、能源装备等领域得到广泛应用。
2. 激光熔覆技术的原理激光熔覆技术的实质是利用高能激光束对工件表面进行局部加热,使其达到熔点,然后进行快速冷却,使其凝固成为一层均匀致密的涂层。
其原理主要包括以下几个方面:2.1 激光加热高能激光束在与工件表面接触时,光能转化为热能,使工件局部区域温度升高。
激光加热具有高度集中的特点,可以实现对工件表面的高温局部加热,而对其他区域几乎没有热影响。
2.2 金属熔化通过激光加热,金属或合金在达到熔点的条件下发生熔化。
激光熔化的特点是熔池温度高、熔池容积小、凝固速度快。
这使得熔化的金属能够在非常短的时间内冷却并固化,形成一层均匀致密的涂层。
2.3 冷却和凝固金属熔池在短时间内冷却并凝固形成固体涂层。
冷却速度的快慢直接影响涂层的组织结构和性能。
激光熔覆技术的快速冷却速度可以避免大晶粒的形成,并在晶界处形成细小的析出相,提高涂层的强度和硬度。
3. 激光熔覆技术的应用激光熔覆技术在多个领域有着广泛的应用,下面列举了其中一些典型的应用:3.1 表面修复和修饰通过激光熔覆技术可以对损坏的金属零件进行修复和修饰。
激光熔覆可以填充表面缺陷、修复裂纹,提高零件的使用寿命和性能。
3.2 硬质合金涂层制备激光熔覆技术可以在金属基材表面涂覆硬质合金材料,提高金属零件的耐磨性、耐腐蚀性和抗疲劳性。
硬质合金涂层广泛应用于机械零件、切削工具等领域。
3.3 功能性涂层制备通过激光熔覆技术可以在金属基材表面制备各种功能性涂层,如热障涂层、阻尼涂层、导电涂层等。
这些涂层可以为金属零件赋予新的性能和功能,拓展其应用范围。
激光熔覆的应用及前景

激光熔覆的应用及前景激光熔覆是一种通过激光束将金属、塑料等材料熔化后与基体表面融合的表面处理技术。
它具有高精度、高效率、低热影响区等优点,被广泛应用于航空航天、汽车制造、电子设备、工具刀具、冶金等行业。
激光熔覆技术未来的前景十分广阔,以下是详细分析。
首先,激光熔覆在航空航天领域具有重要应用前景。
航空航天工业对材料的性能要求极高,激光熔覆技术可通过在零件表面形成高硬度、高粘附力的涂层,提高零件的耐磨、耐腐蚀、抗高温等性能,从而延长零件使用寿命,提高飞行器的可靠性和安全性。
其次,激光熔覆在汽车制造行业有广泛应用前景。
随着汽车工业的快速发展,对零部件的耐磨、耐腐蚀性能要求也越来越高。
激光熔覆技术可以在发动机缸套、活塞环、气门座圈等部位形成高硬度、低摩擦系数的涂层,大幅提高汽车的使用寿命和性能。
此外,激光熔覆还可以应用于汽车车身和零部件的表面美化处理,如通过激光熔覆技术在汽车外壳上形成金属漆等不锈钢涂层,提高汽车的外观质量。
再次,激光熔覆在电子设备制造行业有重要的应用前景。
随着电子设备的迅猛发展,对导电、散热性能的要求越来越高。
激光熔覆技术可以在电子器件的金属基板上形成导电层,提高电路板的导电性能;同时,激光熔覆还可以在电子散热器上形成高散热系数的涂层,有效提高散热效果。
此外,激光熔覆还可用于电子产品的表面装饰,如手机外壳、电脑键盘等。
此外,激光熔覆在工具刀具制造领域有广泛的应用前景。
工具刀具是生产加工的重要工具,对耐磨性、切削性能要求极高。
激光熔覆技术可以在刀具表面形成高硬度、高温硬度的涂层,提高刀具的耐磨性、切削性能以及抗热疲劳性能,从而提高刀具的使用寿命和可靠性。
最后,激光熔覆还可应用于冶金领域。
冶金材料的性能直接影响到汽车、航空航天等重要行业的发展。
激光熔覆技术可以在金属材料的表面形成覆盖层,改善材料的性能。
特别是在高温、高压、高腐蚀等恶劣环境下,通过激光熔覆技术形成的保护层可以提高材料的耐蚀性、耐高温性能和机械性能,从而提高材料的应用范围和效率。
激光熔覆技术
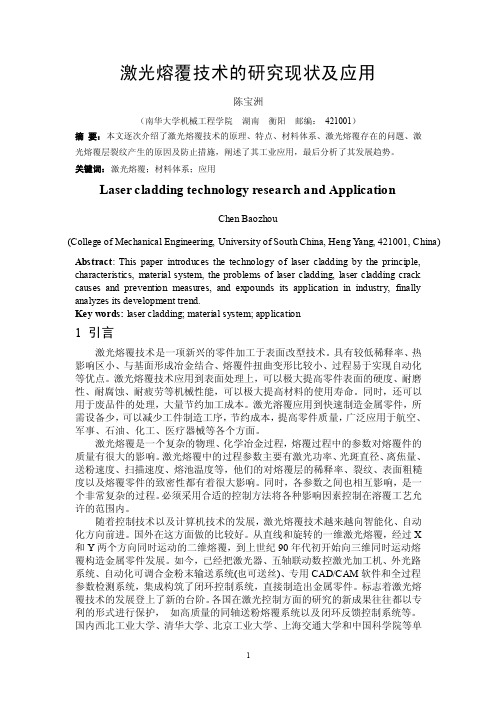
激光熔覆技术的研究现状及应用陈宝洲(南华大学机械工程学院湖南衡阳邮编:421001)摘要:本文逐次介绍了激光熔覆技术的原理、特点、材料体系、激光熔覆存在的问题、激光熔覆层裂纹产生的原因及防止措施,阐述了其工业应用,最后分析了其发展趋势。
关键词:激光熔覆;材料体系;应用Laser cladding technology research and ApplicationChen Baozhou(College of Mechanical Engineering, University of South China, Heng Y ang, 421001, China) Abstract: This paper introduces the technology of laser cladding by the principle, characteristics, material system, the problems of laser cladding, laser cladding crack causes and prevention measures, and expounds its application in industry, finally analyzes its development trend.Key words: laser cladding; material system; application1 引言激光熔覆技术是一项新兴的零件加工于表面改型技术。
具有较低稀释率、热影响区小、与基面形成冶金结合、熔覆件扭曲变形比较小、过程易于实现自动化等优点。
激光熔覆技术应用到表面处理上,可以极大提高零件表面的硬度、耐磨性、耐腐蚀、耐疲劳等机械性能,可以极大提高材料的使用寿命。
同时,还可以用于废品件的处理,大量节约加工成本。
激光溶覆应用到快速制造金属零件,所需设备少,可以减少工件制造工序,节约成本,提高零件质量,广泛应用于航空、军事、石油、化工、医疗器械等各个方面。
激光深熔焊的应用场景
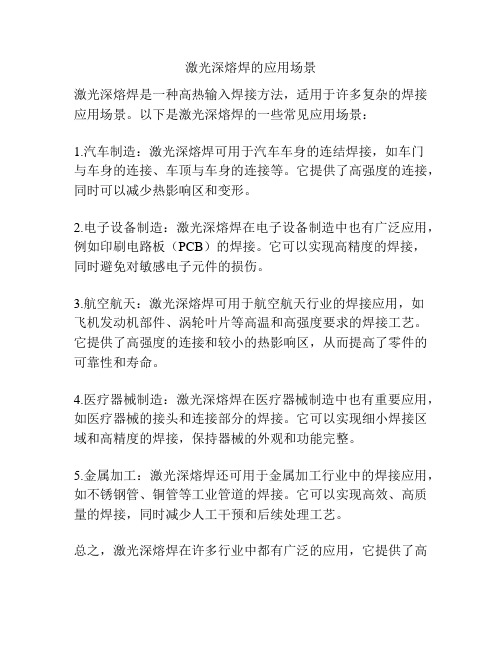
激光深熔焊的应用场景
激光深熔焊是一种高热输入焊接方法,适用于许多复杂的焊接应用场景。
以下是激光深熔焊的一些常见应用场景:
1.汽车制造:激光深熔焊可用于汽车车身的连结焊接,如车门
与车身的连接、车顶与车身的连接等。
它提供了高强度的连接,同时可以减少热影响区和变形。
2.电子设备制造:激光深熔焊在电子设备制造中也有广泛应用,例如印刷电路板(PCB)的焊接。
它可以实现高精度的焊接,同时避免对敏感电子元件的损伤。
3.航空航天:激光深熔焊可用于航空航天行业的焊接应用,如
飞机发动机部件、涡轮叶片等高温和高强度要求的焊接工艺。
它提供了高强度的连接和较小的热影响区,从而提高了零件的可靠性和寿命。
4.医疗器械制造:激光深熔焊在医疗器械制造中也有重要应用,如医疗器械的接头和连接部分的焊接。
它可以实现细小焊接区域和高精度的焊接,保持器械的外观和功能完整。
5.金属加工:激光深熔焊还可用于金属加工行业中的焊接应用,如不锈钢管、铜管等工业管道的焊接。
它可以实现高效、高质量的焊接,同时减少人工干预和后续处理工艺。
总之,激光深熔焊在许多行业中都有广泛的应用,它提供了高
精度、高强度和低热影响区的焊接解决方案,可以应对各种复杂的焊接需求。
激光熔覆应用场景

激光熔覆应用场景激光熔覆技术是一种非常有前景的表面工程技术,它通过激光束将喷粉材料和基础材料熔化,形成一层均匀的涂层,可以改善零件的表面性能,增加零件的使用寿命,提高零件的耐磨性、耐腐蚀性和抗疲劳能力。
下面我们来看看激光熔覆技术的应用场景。
1、航空航天领域航空航天领域需要使用高强度、高耐久性、高温抗蚀等特性的零部件,因此激光熔覆技术在航空航天领域的应用非常广泛。
例如,在飞机发动机领域使用激光熔覆技术,可以熔覆高温合金、抗疲劳合金等材料,提高发动机的性能和寿命,从而提高整个飞机的安全性和可靠性。
2、汽车工业汽车工业也是激光熔覆技术的重要应用领域之一。
激光熔覆技术可以应用于汽车发动机、传动装置、底盘等零部件表面的涂层加工。
例如,在气门、缸体、曲轴等部件上可以使用激光熔覆技术覆盖耐热合金、耐磨合金、耐腐蚀合金等材料,从而提高零件的耐用性和性能。
3、船舶制造船舶制造涉及复杂的工艺过程和高性能零部件的生产,激光熔覆技术可以应用于船舶零部件表面的涂层加工,提高零件的耐用性和性能。
例如,在船用发动机、尾轮、推进器等部件上采用激光熔覆涂层可以有效提高其耐磨性、抗腐蚀性和耐高温性能,从而降低维护成本,延长设备的使用寿命。
4、石油化工石油化工行业是激光熔覆技术的重要应用领域之一。
熔覆涂层可以应用于管道、容器、阀门等石油化工设备的内、外表面,提高设备的抗腐蚀能力,降低维护成本,延长设备的使用寿命。
5、医疗器械医疗器械需要耐磨、防腐、耐高温等特性的零部件,在医疗器械的制造中也可以应用激光熔覆技术。
激光熔覆可用于医疗器械表面的涂层加工,如人工髋关节、支架、植入物等,可以显著提高器械的耐用性和性能,同时也可减少手术次数和治疗周期。
综上所述,激光熔覆技术在航空航天、汽车工业、船舶制造、石油化工、医疗器械等领域都具有广泛的应用前景,在未来的发展中还有很大的空间和潜力。
- 1、下载文档前请自行甄别文档内容的完整性,平台不提供额外的编辑、内容补充、找答案等附加服务。
- 2、"仅部分预览"的文档,不可在线预览部分如存在完整性等问题,可反馈申请退款(可完整预览的文档不适用该条件!)。
- 3、如文档侵犯您的权益,请联系客服反馈,我们会尽快为您处理(人工客服工作时间:9:00-18:30)。
激光熔覆成形技术的研究进展1基本概念激光熔覆成形(Laser cladding forming, LCF)技术集激光技术、计算机技术、数控技术、传感器技术及材料加工技术于一体,是一门多学科交叉的边缘学科和新兴的先进制造技术。
该技术把快速原型制造技术和激光熔覆表面强化技术相结合,利用高能激光束在金属基体上形成熔池,将通过送粉装置和粉末喷嘴输送到熔池的金属粉末或事先预置于基体上的涂层熔化,快速凝固后与基体形成冶金结合,根据零件的计算机辅助设计模型,逐线、逐层堆积材料,直接生成三维近终形金属零件。
激光熔覆成形系统主要由计算机、粉末输送系统、激光器和数控工作台四部分组成,其原理如图1 所示。
由于该技术可以直接制造全密度金属零件,从20 世纪90 年代中期开始,就成为快速成形领域的研究热点和发展方向,具有广阔的应用前景。
激光熔覆成形技术在产生后的短短几年内获得了飞速发展,并被冠以不同的名称:如送粉方式的激光工程化近成形(Laser Engineered Net Shaping, LENSTM)、直接光制造技术(Directed light fabrication, DLF)、直接金属沉积(Direct metal deposition, DMD)、堆积成形制造(Shape deposition manufacturing, SDM),激光固结(Laser consolidation, LC),激光增材制造(Laser additive manufacturing, LAMSM),以及粉末预置方式的选择性激光熔化(Selective laser melting, SLM)和金属直接激光烧结(Direct laser sintering of metals ,DSM)等,这些技术的原理和加工方法基本相同,将它们统称为激光熔覆成形技术。
图1 激光熔覆成形原理示意图2激光熔覆成形的特点和研究进展和传统的材料成形方法相比,激光熔覆成形技术具有成形零件复杂、结构优化、性能优良、加工材料范围广泛,柔性化程度高,可实现梯度功能材料的制造、制造周期短、可实现无模近终成形等独特优点,在材料利用率、研制周期和总的制造成本方面均优于铸造和锻造技术,是一种优质、节材、低成本、无污染的先进制造技术。
此外,激光熔覆成形技术还具有成形零件结构复杂,可加工材料范围广泛,加工时热影响区和基体的变形小等独特的优点,是一种优质、低成本和无污染的先进制造技术,可以广泛应用于复杂零件的直接制造和修复。
激光熔覆成形技术可以在无需支撑的条件下成形具有悬臂特征和复杂内腔的零件,使用这种方法成形模具时,可以在制造过程中优化布置模具内部的冷却管道,实现模具特定区域快速冷却以减小零件的变形,提高模具制造精度。
在使用激光熔覆成形技术加工零件时,零件的生产周期可以缩短约20% ,降低零件成本,提高制造精度。
此外,激光熔覆成形技术还可以用来加工难熔金属、高温合金和金属间化合物等难加工材料。
采用锻造和机加工生产带翼肋的整体性补强飞机结构件时,制造周期长,材料利用率低;若采用激光熔覆成形技术加工,不仅制造周期缩短75% ,成本降低20% -30% ,而且零件性能可以达到甚至超过铸造和锻造材料的标准。
激光熔覆成形技术使用高功率激光进行加工,能量密度高度集中,可以进行难加工材料的成形,加工完成后熔覆材料和基体形成冶金结合,为航空发动机叶片、汽轮机叶片、叶轮,石化行业转子、定子和核阅零件等关键零部件的修复提供了一条崭新的途径。
该技术还可以用来修复定向凝固单晶超合金叶片,在降低修复成本的同时而不会降低母材的性能,零件的表面耐磨、耐腐蚀、耐高温等性能甚至有所提高。
2.1激光熔覆成形技术的发展在激光熔覆成形技术的研究方面,从20 世纪70 年代开始,随着激光熔覆及相关技术的发展,激光熔覆成形技术逐渐成为激光加工领域的研究热点,获得迅猛发展。
在这一时期,国内外的众多研究机构进入该领域,并取得了一系列研究成果,美国的Los Alamos 国家实验室、Sandia 国家实验室、密执安(Michigan)大学和Aero Met 公司等等所取得的研究成果较有代表性。
20 世纪90 年代中期,美国Sandia 国家实验室与United Technologies Pratt & Whitney 公司展开合作,利用激光近形制造技术,对多种材料的激光熔覆成形工艺进行研究,制造出锦基超合金、铁合金、不锈钢和H13 工具钢等零件,成形零件的性能相对于锻造件在强度和塑性方面均有显著的提高,加工精度在z 、y 方向达到0.0 5 mm,z方向达到0.38mm,通过改变粉末的成分使零件的不同部位具有不同的成分和性能,实现了零件的梯度功能制造。
Sandia 还与3M、Honeywell、NASA 以及Ford 等合作,将激光成形制造技术集成于零件的制造过程中,缩短零件的制造周期,降低零件成本,提高零件的性能。
Los Alamos 国家实验室开发了采用2 kW Nd:YAG 激光器和五轴数控工作台的DLF 系统,在充满氧气的不锈钢手套箱中进行加工,系统中带有粉末回收装置,可以将未熔化的粉末回收,而且还可以输送4 种不同成分的粉末实现功能梯度材料的制造,零件的表面粗糙度可以达到10μm ,精度达土0. 12mm。
Aero Met 公司采用激光熔覆成形工艺进行航空铁合金零件的成形制造和修复,该系统内装有自动反馈控制传感器,工作台定位精度为±0.00762 cm(3/1 000 in),可加工长度243.84cm(8ft)、质量为272.154 kg(600 b)的飞机原型。
该公司的制造速率较高,其单层沉积厚度达到4 mm,单道沉积宽度达到13 mm,可进行较大体积零件的制造,产品达到近终形,且成分和性能己经达到ASTM标准。
图5 为Aero Met 公司的Lasform 工艺系统和采用该技术制造的大型零件,零件最大尺寸已达到2 400 mm×225 mm×100 mm。
Aero Met 公司在2000 年3 月为波音飞机公司(Boeing Company)制造了F/A-18 E/F 机翼零件。
其生产的Ti-6Al-4V 零件Lockheed-Martin F-22 支架、波音F/A-18 E/F 机翼连接板和降落连杆零件已达到航空零件的性能要求。
这些激光熔覆成形技术加工的钛合金零件不仅疲劳寿命大大超出传统工艺制造的零件,同时该技术节约材料及切削加工费用,零件成本降低20%~40%,生产周期也缩短80%。
国内在激光熔覆成形技术方面的研究起步较晚,始于20 世纪90 年代末,到2000 年以后才陆续有文献报道。
西北工业大学凝固技术国家重点实验室、中国有色金属研究总院、清华大学、北京航空航天大学和上海交通大学等单位相继开展这方面的研究,并在快速成形理论、工艺、设备和材料等各方面取得阶段性成果。
如西北工业大学、中国有色金属研究院和北京航空航天大学已采用不同的合金制成了具有一定形状的激光熔覆成形件,清华大学开发出了应用于激光熔覆成形的同轴送粉系统,并研究了加工过程的闭环控制。
西北工业大学在快速成形工艺、快速成形组织的定向凝固及力学性能等方面作了大量的研究工作。
近几年来,激光熔覆成形技术在国内发展较快,更多的企业、高校和研究机构购置了大功率激光加工设备,并在激光熔覆成形技术的工艺和应用方面开展了研究工作。
具有代表性的激光熔覆装备制造或系统集成的公司主要有深圳大族激光、北京陆合飞虹激光、武汉团结激光、南京煜宸激光和江苏中科四象等。
从事激光熔覆技术应用的公司主要有沈阳大陆激光、武钢华工、山东能源、鞍山正发股份、沈阳金研激光、泰安金宸激光、江苏永年激光及大族金石凯等。
2.2激光熔覆成形技术的研究进展随着激光技术的进步和测控技术等学科的发展,激光熔覆成形技术在硬件系统和理论研究等方面获得了迅猛发展,促进了其应用范围的不断扩大和成形质量的日益提高。
世界各国研究机构开发的各具特色的熔覆成形系统不断完善,激光熔覆成形组织性能研究、熔覆成形送粉器、粉末喷嘴和检测控制系统、激光、粉末和基体的相互作用及成形组织的外延生长以及柱状晶、等轴晶的转变理论等取得了一定的进展。
温度场建模与仿真、熔池温度和形状的检测与控制等方面的工作成为该领域的研究热点。
2.2.1 成形组织与性能研究成形零件的性能由其组织决定,而组织取决于熔覆成形材料、工艺参数、熔池的传热、传质和固液界面的冷却速度等,研究激光熔覆成形组织形成机理与特征对于成形零件性能的控制具有重要意义。
对激光熔覆成形组织的研究主要以试验研究为主。
GRIFFITH 等[1-2]采用LENS 工艺对316SS、SS304L 不锈钢以及IN625 和IN690 镍基超合金和H13 工具钢等多种材料进行了沉积,研究了工艺参数对性能的影响。
试验发现,当激光功率低时,组织较为细小;激光功率高时,由于晶粒长大,获得的组织比较粗大。
当激光功率低、扫描速度快时,屈服强度和抗拉强度高。
因此,可以通过工艺参数的匹配获得所需的性能。
LENS 制造的316SS 不锈钢屈服强度达到锻造材料的2 倍,断后伸长率接近50%。
凝固沿着热流方向,从而导致晶粒的生长方向不一。
初始的沉积组织发生重熔和粗化,树枝晶的特征不能完整保留下来。
BROOKS 等对H13 钢进行了激光熔覆成形,建立了简单的描述H13 钢硬度与热历史关系的动力学模型,并结合LENS 的热数据来估计熔覆层的硬度,单道熔覆层的硬度预测与测量结果吻合较好。
DINDA 等研究了Inconel625 合金激光熔覆成形组织在800~1 200 ◦C 的热稳定性。
研究发现:柱状晶组织在1 000 ◦C 以下较为稳定,而在1 200 ◦C 左右,可见完全再结晶的等轴晶组织。
李延民等研究了侧向送粉激光快速成形工艺参数对成形特征的影响,得出了熔覆层厚度和宽度与激光功率、扫描速度以及能量密度之间的关系,并采用神经网络技术对工艺参数进行了优化。
席明哲等[25]研究了激光功率对激光快速成形316L薄壁墙组织和性能的影响,得出了零件抗拉强度和伸长率随激光功率的变化趋势,获得了与常规方法制成的零件性能相当的薄壁墙。
HUNT 研究了稳态下等轴晶和柱状晶的生长,建立了柱状晶向等轴晶转化(Columnar-to-equiaxed transition, CET)的理论模型,同时考虑了形核和长大的影响,得出当等轴晶体积分数φ<0.66%时,凝固组织为柱状晶,而φ>49%时为等轴晶,两者之间为柱状晶和等轴晶的混合生长区。
GÄUMANN 等对CMSX-4激光成形凝固显微组织进行了系统的研究,对单晶基体上外延生长定向凝固组织的形成进行了解释。