汽车制动系统的概况及作用8正文
汽车制动系统简介
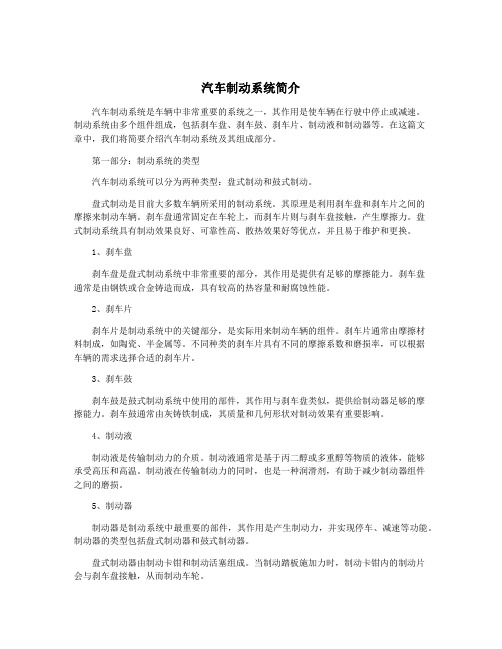
汽车制动系统简介汽车制动系统是车辆中非常重要的系统之一,其作用是使车辆在行驶中停止或减速。
制动系统由多个组件组成,包括刹车盘、刹车鼓、刹车片、制动液和制动器等。
在这篇文章中,我们将简要介绍汽车制动系统及其组成部分。
第一部分:制动系统的类型汽车制动系统可以分为两种类型:盘式制动和鼓式制动。
盘式制动是目前大多数车辆所采用的制动系统。
其原理是利用刹车盘和刹车片之间的摩擦来制动车辆。
刹车盘通常固定在车轮上,而刹车片则与刹车盘接触,产生摩擦力。
盘式制动系统具有制动效果良好、可靠性高、散热效果好等优点,并且易于维护和更换。
1、刹车盘刹车盘是盘式制动系统中非常重要的部分,其作用是提供有足够的摩擦能力。
刹车盘通常是由钢铁或合金铸造而成,具有较高的热容量和耐腐蚀性能。
2、刹车片刹车片是制动系统中的关键部分,是实际用来制动车辆的组件。
刹车片通常由摩擦材料制成,如陶瓷、半金属等。
不同种类的刹车片具有不同的摩擦系数和磨损率,可以根据车辆的需求选择合适的刹车片。
3、刹车鼓刹车鼓是鼓式制动系统中使用的部件,其作用与刹车盘类似,提供给制动器足够的摩擦能力。
刹车鼓通常由灰铸铁制成,其质量和几何形状对制动效果有重要影响。
4、制动液制动液是传输制动力的介质。
制动液通常是基于丙二醇或多重醇等物质的液体,能够承受高压和高温。
制动液在传输制动力的同时,也是一种润滑剂,有助于减少制动器组件之间的磨损。
5、制动器制动器是制动系统中最重要的部件,其作用是产生制动力,并实现停车、减速等功能。
制动器的类型包括盘式制动器和鼓式制动器。
盘式制动器由制动卡钳和制动活塞组成。
当制动踏板施加力时,制动卡钳内的制动片会与刹车盘接触,从而制动车轮。
制动系统的工作原理是将制动力传递给车轮,从而实现减速和停车的功能。
当司机踩下制动踏板时,制动器组件会产生摩擦力,将车轮减速或停止转动。
制动系统的工作过程可以分为三个阶段:制动前段、制动中段和制动后段。
在制动前段,制动器和车轮之间开始接触,并逐渐产生摩擦力;在制动中段,制动器和车轮之间的摩擦力达到最大;在制动后段,制动器逐渐减小制动力,车轮恢复正常运转。
汽车制动系统ppt课件完整版
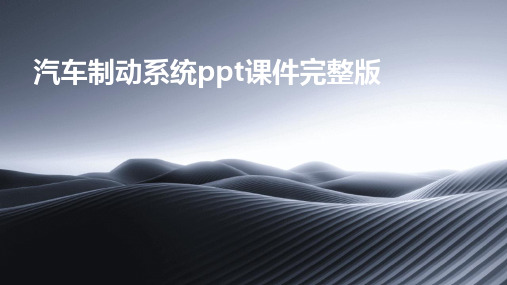
制动距离
指从驾驶员开始制动到车辆完全停 止所行驶的距离。它是评价汽车制
动性能的重要指标之一。
A
B
C
D
制动时方向稳定性
指车辆在制动过程中保持直线行驶或按预 定轨迹行驶的能力。它是评价汽车制动安 全性的重要指标之一。
制动力分配
指前后轴制动力分配的比例。合理的制动 力分配可以提高制动稳定性和制动效率。
产生压缩空气。
制动阀
控制压缩空气进入 制动气室的开关。
制动管路
连接各部件,传递 压缩空气。
气压制动系统优缺点分析
01
优点
02
结构简单,维护方便。
制动效能稳定,受环境影响小。
03
气压制动系统优缺点分析
• 适用于大型车辆和重载车辆。
气压制动系统优要空气压缩机和储气罐,占用空间较大 。
拆卸检查
对疑似故障部件进行拆卸检查 ,观察其磨损、变形等情况。
路试检测
在安全条件下进行路试,检测 制动系统的实际表现,进一步
确认故障。
故障排除措施和维修建议
制动失效排除
制动跑偏排除
制动拖滞排除
驻车制动失效排除
检查制动液泄漏情况并修复, 清洗或更换堵塞的管路,更换 磨损严重的制动蹄片等。
调整两侧车轮制动力至均衡, 调整轮胎气压至一致,检查并 修复悬挂系统故障等。
03
制动响应速度相对较慢。
04
在严寒地区,压缩空气可能结冰,影响制 动效果。
04
伺服制动系统与电子控制制动系 统
伺服制动系统组成及工作原理
组成
伺服制动系统主要由制动踏板、真空助力器、制动主缸、制动轮缸、制动器等组成。
工作原理
当驾驶员踩下制动踏板时,真空助力器提供助力,推动制动主缸内的活塞移动,使制动液压力升高。制动液通过 制动管路传递到各个制动轮缸,推动轮缸内的活塞移动,使制动器产生制动力矩,从而实现车辆减速停车。
简述汽车制动系统的作用
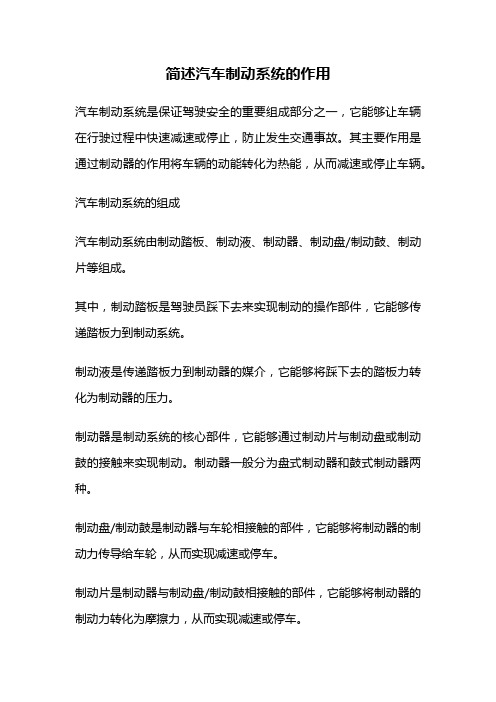
简述汽车制动系统的作用汽车制动系统是保证驾驶安全的重要组成部分之一,它能够让车辆在行驶过程中快速减速或停止,防止发生交通事故。
其主要作用是通过制动器的作用将车辆的动能转化为热能,从而减速或停止车辆。
汽车制动系统的组成汽车制动系统由制动踏板、制动液、制动器、制动盘/制动鼓、制动片等组成。
其中,制动踏板是驾驶员踩下去来实现制动的操作部件,它能够传递踏板力到制动系统。
制动液是传递踏板力到制动器的媒介,它能够将踩下去的踏板力转化为制动器的压力。
制动器是制动系统的核心部件,它能够通过制动片与制动盘或制动鼓的接触来实现制动。
制动器一般分为盘式制动器和鼓式制动器两种。
制动盘/制动鼓是制动器与车轮相接触的部件,它能够将制动器的制动力传导给车轮,从而实现减速或停车。
制动片是制动器与制动盘/制动鼓相接触的部件,它能够将制动器的制动力转化为摩擦力,从而实现减速或停车。
汽车制动系统的工作原理汽车制动系统的工作原理是利用制动器对车轮的制动力,将车轮的动能转化为热能,并通过摩擦的方式,使车辆减速或停止。
当驾驶员踩下制动踏板时,制动液会传递踏板力到制动器,制动器通过制动片与制动盘/制动鼓的接触来实现制动。
制动片与制动盘/制动鼓的摩擦力会将车轮的动能转换为热能,从而使车辆减速或停止。
盘式制动器与鼓式制动器的区别盘式制动器与鼓式制动器是两种常见的制动器类型,它们的工作原理有所不同。
盘式制动器是将制动片与制动盘相接触,制动片与制动盘的接触面积大,散热快,制动效果好,适用于高速行驶时的制动。
鼓式制动器是将制动片与制动鼓相接触,制动片与制动鼓的接触面积小,散热慢,制动效果相对较差,但适用于低速行驶时的制动。
汽车制动系统的维护保养汽车制动系统的维护保养十分重要,它能够保证制动系统的正常工作,从而保证驾驶安全。
常见的制动系统维护保养包括制动片更换、制动盘/制动鼓磨损检查、制动液更换、制动系统清洗、制动器调整等。
驾驶员在日常使用中应该注意制动系统的工作状态,及时检查维护保养,确保制动系统的正常工作。
汽车制动系统的概况及作用正文

绪论汽车行驶时能在短距离内停车且维持行驶方向稳定性和在下长坡时能维持一定车速的能力称为汽车的制动性。
人们在汽车上装设专门装置,以便驾驶员根据道路和交通等情况借以使外界(主要是路面)在汽车的某些部分(主要是车轮)施加一定的力,对汽车进行一定程度的强制制动,使驾驶员和乘客免受车祸的灾害。
这一系列专门装置即称为制动系。
1.汽车制动系统的概况及作用1.1汽车制动系统的发展概况从汽车诞生时起,车辆制动系统在车辆的安全方面就扮演着至关重要的角色。
近年来,随着车辆技术的进步和汽车行驶速度的提高,这种重要性表现得越来越明显。
汽车制动系统种类很多,形式多样。
传统的制动系统结构型式主要有机械式、气动式、液压式、气—液混合式。
它们的工作原理基本都一样,都是利用制动装置,用工作时产生的摩擦热来逐渐消耗车辆所具有的动能,以达到车辆制动减速,或直至停车的目的。
伴随着节能和清洁能源汽车的研究开发,汽车动力系统发生了很大的改变,出现了很多新的结构型式和功能形式。
新型动力系统的出现也要求制动系统结构型式和功能形式发生相应的改变。
例如电动汽车没有内燃机,无法为真空助力器提供真空源,一种解决方案是利用电动真空泵为真空助力器提供真空。
汽车制动系统的发展是和汽车性能的提高及汽车结构型式的变化密切相关的,制动系统的每个组成部分都发生了很大变化。
1.2汽车制动系统作用使行驶中的汽车按照驾驶员的要求进行强制减速甚至停车;使已停驶的汽车在各种道路条件下(包括在坡道上)稳定驻车;使下坡行驶的汽车速度保持稳定。
2.制动器(brake staff)简介制动器就是刹车。
是使机械中的运动件停止或减速的机械零件。
俗称刹车、闸。
制动器主要由制动架、制动件和操纵装置等组成。
有些制动器还装有制动件间隙的自动调整装置。
为了减小制动力矩和结构尺寸,制动器通常装在设备的高速轴上,但对安全性要求较高的大型设备(如矿井提升机、电梯等)则应装在靠近设备工作部分的低速轴上。
有些制动器已标准化和系列化,并由专业工厂制造以供选用。
汽车制动系统的组成及功用
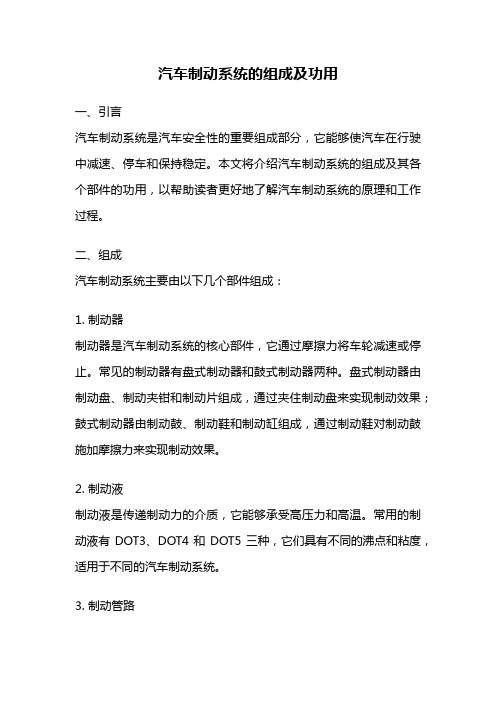
汽车制动系统的组成及功用一、引言汽车制动系统是汽车安全性的重要组成部分,它能够使汽车在行驶中减速、停车和保持稳定。
本文将介绍汽车制动系统的组成及其各个部件的功用,以帮助读者更好地了解汽车制动系统的原理和工作过程。
二、组成汽车制动系统主要由以下几个部件组成:1. 制动器制动器是汽车制动系统的核心部件,它通过摩擦力将车轮减速或停止。
常见的制动器有盘式制动器和鼓式制动器两种。
盘式制动器由制动盘、制动夹钳和制动片组成,通过夹住制动盘来实现制动效果;鼓式制动器由制动鼓、制动鞋和制动缸组成,通过制动鞋对制动鼓施加摩擦力来实现制动效果。
2. 制动液制动液是传递制动力的介质,它能够承受高压力和高温。
常用的制动液有DOT3、DOT4和DOT5三种,它们具有不同的沸点和粘度,适用于不同的汽车制动系统。
3. 制动管路制动管路是连接制动器和制动液储存器的管道系统,它能够传递制动力和控制制动压力。
制动管路需要具有足够的强度和密封性,以确保制动系统正常工作。
4. 制动助力装置制动助力装置是帮助驾驶员施加制动力的装置,它能够减轻驾驶员的踩踏力度。
常见的制动助力装置有真空助力器和液压助力器两种,它们通过利用真空或液压原理来增加制动力的传递效果。
5. 制动控制系统制动控制系统是驾驶员控制汽车制动的装置,它包括制动踏板、制动灯和制动开关等。
驾驶员通过踩下制动踏板来控制制动器的工作,并通过制动灯和制动开关向后方车辆发出制动信号,提醒后车注意行车安全。
三、功用汽车制动系统的主要功用有以下几点:1. 减速和停车汽车行驶过程中,制动系统能够通过减速车轮的转动来降低车速,使汽车能够准确停在目标位置。
制动器通过施加摩擦力,将车轮减速甚至停止,提供可靠的制动效果。
2. 保持稳定汽车制动系统能够保持车辆的稳定性,防止在制动过程中车辆产生侧滑或失控。
制动系统通过对车轮的制动力分配,使车辆保持平稳的行驶状态,提高行车安全性。
3. 刹车灵敏汽车制动系统的制动灵敏度对驾驶员的操控能力起着重要的影响。
车辆制动系统简介
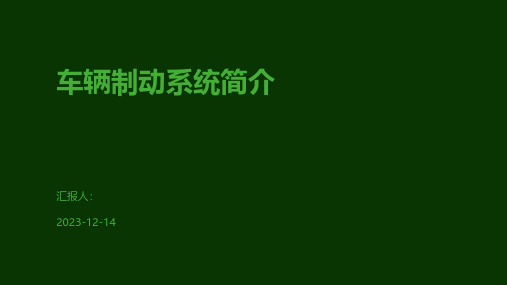
车辆制动系统简介汇报人:2023-12-14•制动系统概述•制动系统组成与工作原理•不同类型车辆制动系统对比目录•安全性与舒适性考量因素•维护保养与故障排除方法论述•未来发展趋势预测与展望01制动系统概述车辆制动系统是用于使行驶中的汽车减速或停车的一套专门装置。
定义通过摩擦将车辆的动能转化为热能,从而降低车速或使车辆停止。
作用定义与作用从最初的机械制动系统,到液压制动系统,再到现在的电子控制制动系统,制动技术不断发展,性能不断提高。
未来制动系统将更加智能化、电子化,如线控制动系统、再生制动系统等,以提高制动性能和安全性。
发展历程及趋势趋势发展历程制动系统是汽车安全性的重要组成部分,消费者对制动性能的要求越来越高。
安全性需求舒适性需求环保性需求制动系统的舒适性也是消费者关注的重点,如制动噪音、制动踏板感觉等。
随着环保意识的提高,消费者对制动系统的环保性也提出了更高的要求,如制动能量的回收利用等。
030201市场需求分析02制动系统组成与工作原理主要部件介绍用于驾驶员操作,将脚力转化为液压或气压信号,传递给制动器。
接受制动踏板的信号,将液压或气压放大并传递给制动器。
包括盘式制动器和鼓式制动器,用于将车轮减速或停止。
用于增加制动踏板的力量,减轻驾驶员的踏板力。
制动踏板制动主缸制动器制动助力器当驾驶员踩下制动踏板时,制动主缸将液压或气压信号传递给制动器。
制动器通过摩擦将车轮减速或停止。
制动助力器可以增加制动踏板的力量,从而减轻驾驶员的踏板力。
工作原理简述评价制动系统减速或停车的能力,包括制动距离、制动减速度等。
制动效能评价制动系统在高速行驶或紧急制动时的稳定性,包括制动跑偏、制动侧滑等。
制动稳定性评价制动系统在正常行驶或低速行驶时的舒适性,包括制动踏板力、噪声、振动等。
制动舒适性性能指标评价方法03不同类型车辆制动系统对比传统燃油汽车制动系统制动器类型主要包括盘式制动器和鼓式制动器,其中盘式制动器具有散热性好、制动平稳等优点,广泛应用于现代汽车中。
车辆制动系统解析
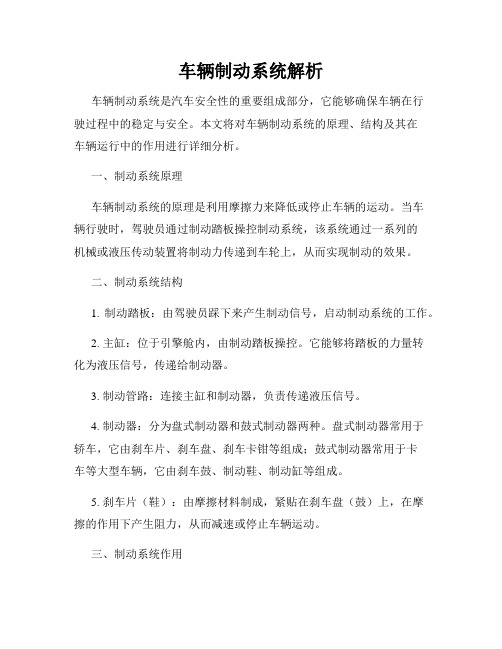
车辆制动系统解析车辆制动系统是汽车安全性的重要组成部分,它能够确保车辆在行驶过程中的稳定与安全。
本文将对车辆制动系统的原理、结构及其在车辆运行中的作用进行详细分析。
一、制动系统原理车辆制动系统的原理是利用摩擦力来降低或停止车辆的运动。
当车辆行驶时,驾驶员通过制动踏板操控制动系统,该系统通过一系列的机械或液压传动装置将制动力传递到车轮上,从而实现制动的效果。
二、制动系统结构1. 制动踏板:由驾驶员踩下来产生制动信号,启动制动系统的工作。
2. 主缸:位于引擎舱内,由制动踏板操控。
它能够将踏板的力量转化为液压信号,传递给制动器。
3. 制动管路:连接主缸和制动器,负责传递液压信号。
4. 制动器:分为盘式制动器和鼓式制动器两种。
盘式制动器常用于轿车,它由刹车片、刹车盘、刹车卡钳等组成;鼓式制动器常用于卡车等大型车辆,它由刹车鼓、制动鞋、制动缸等组成。
5. 刹车片(鞋):由摩擦材料制成,紧贴在刹车盘(鼓)上,在摩擦的作用下产生阻力,从而减速或停止车辆运动。
三、制动系统作用1. 制动力传递:制动系统能够将驾驶员的制动指令迅速传递给车轮,通过制动器产生摩擦力,从而减速或停止车辆的运动。
2. 稳定行驶:制动系统能够使车辆在制动过程中保持稳定,避免发生侧滑或失控等危险情况。
3. 加强控制:通过制动踏板的力度控制,驾驶员可以根据需要调整制动器施加的力量,从而对车速进行精确控制。
4. 能量回收:一些现代车辆的制动系统还可以通过回收制动能量,将部分能量转化为电能储存起来,以提高燃油利用率。
四、常见问题与解决方法1. 刹车失灵:如果在驾驶过程中发现刹车失灵,应该立即采取应急措施,如使用手刹或变挡减速,并尽快找到安全地点停车检查。
2. 刹车异响:刹车系统发出噪音可能是由于刹车片磨损、刹车盘或刹车鼓的变形等原因造成,应及时检修或更换相关零部件。
3. 刹车偏软或过紧:刹车过软可能是由于制动液泄漏,刹车过紧可能是系统有堵塞或制动盘有温度过高等原因,应及时检查并处理。
简述汽车制动系统的作用
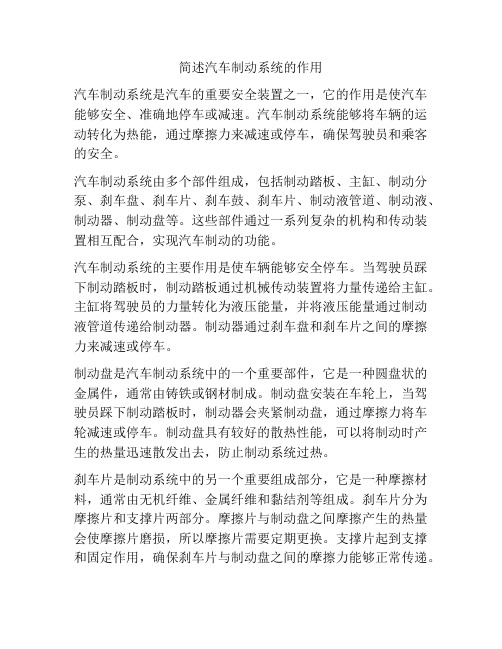
简述汽车制动系统的作用汽车制动系统是汽车的重要安全装置之一,它的作用是使汽车能够安全、准确地停车或减速。
汽车制动系统能够将车辆的运动转化为热能,通过摩擦力来减速或停车,确保驾驶员和乘客的安全。
汽车制动系统由多个部件组成,包括制动踏板、主缸、制动分泵、刹车盘、刹车片、刹车鼓、刹车片、制动液管道、制动液、制动器、制动盘等。
这些部件通过一系列复杂的机构和传动装置相互配合,实现汽车制动的功能。
汽车制动系统的主要作用是使车辆能够安全停车。
当驾驶员踩下制动踏板时,制动踏板通过机械传动装置将力量传递给主缸。
主缸将驾驶员的力量转化为液压能量,并将液压能量通过制动液管道传递给制动器。
制动器通过刹车盘和刹车片之间的摩擦力来减速或停车。
制动盘是汽车制动系统中的一个重要部件,它是一种圆盘状的金属件,通常由铸铁或钢材制成。
制动盘安装在车轮上,当驾驶员踩下制动踏板时,制动器会夹紧制动盘,通过摩擦力将车轮减速或停车。
制动盘具有较好的散热性能,可以将制动时产生的热量迅速散发出去,防止制动系统过热。
刹车片是制动系统中的另一个重要组成部分,它是一种摩擦材料,通常由无机纤维、金属纤维和黏结剂等组成。
刹车片分为摩擦片和支撑片两部分。
摩擦片与制动盘之间摩擦产生的热量会使摩擦片磨损,所以摩擦片需要定期更换。
支撑片起到支撑和固定作用,确保刹车片与制动盘之间的摩擦力能够正常传递。
制动液是汽车制动系统的传动介质,它是一种黏稠的液体,具有较高的沸点和较低的冰点。
制动液的主要成分是乙二醇和水,它能够在制动过程中产生很高的压力,并能够保持一定的粘度。
制动液通过制动液管道将驾驶员踩下制动踏板产生的力量传递给制动器,从而实现汽车的制动功能。
汽车制动系统的作用不仅仅是停车,它还能够帮助驾驶员在行驶中减速。
当驾驶员需要减速时,只需轻踩制动踏板即可实现减速。
制动系统通过调整刹车片与制动盘的接触面积来控制摩擦力的大小,从而实现减速的目的。
这样,驾驶员可以根据道路情况和交通状况自由地选择减速的程度。
- 1、下载文档前请自行甄别文档内容的完整性,平台不提供额外的编辑、内容补充、找答案等附加服务。
- 2、"仅部分预览"的文档,不可在线预览部分如存在完整性等问题,可反馈申请退款(可完整预览的文档不适用该条件!)。
- 3、如文档侵犯您的权益,请联系客服反馈,我们会尽快为您处理(人工客服工作时间:9:00-18:30)。
绪论汽车行驶时能在短距离内停车且维持行驶方向稳定性和在下长坡时能维持一定车速的能力称为汽车的制动性。
人们在汽车上装设专门装置,以便驾驶员根据道路和交通等情况借以使外界(主要是路面)在汽车的某些部分(主要是车轮)施加一定的力,对汽车进行一定程度的强制制动,使驾驶员和乘客免受车祸的灾害。
这一系列专门装置即称为制动系。
1.汽车制动系统的概况及作用1.1汽车制动系统的发展概况从汽车诞生时起,车辆制动系统在车辆的安全方面就扮演着至关重要的角色。
近年来,随着车辆技术的进步和汽车行驶速度的提高,这种重要性表现得越来越明显。
汽车制动系统种类很多,形式多样。
传统的制动系统结构型式主要有机械式、气动式、液压式、气—液混合式。
它们的工作原理基本都一样,都是利用制动装置,用工作时产生的摩擦热来逐渐消耗车辆所具有的动能,以达到车辆制动减速,或直至停车的目的。
伴随着节能和清洁能源汽车的研究开发,汽车动力系统发生了很大的改变,出现了很多新的结构型式和功能形式。
新型动力系统的出现也要求制动系统结构型式和功能形式发生相应的改变。
例如电动汽车没有内燃机,无法为真空助力器提供真空源,一种解决方案是利用电动真空泵为真空助力器提供真空。
汽车制动系统的发展是和汽车性能的提高及汽车结构型式的变化密切相关的,制动系统的每个组成部分都发生了很大变化。
1.2汽车制动系统作用使行驶中的汽车按照驾驶员的要求进行强制减速甚至停车;使已停驶的汽车在各种道路条件下(包括在坡道上)稳定驻车;使下坡行驶的汽车速度保持稳定。
2.制动器(brake staff)简介制动器就是刹车。
是使机械中的运动件停止或减速的机械零件。
俗称刹车、闸。
制动器主要由制动架、制动件和操纵装置等组成。
有些制动器还装有制动件间隙的自动调整装置。
为了减小制动力矩和结构尺寸,制动器通常装在设备的高速轴上,但对安全性要求较高的大型设备(如矿井提升机、电梯等)则应装在靠近设备工作部分的低速轴上。
有些制动器已标准化和系列化,并由专业工厂制造以供选用。
制动器分为行车制动器(脚刹),驻车制动器(手刹)。
在行车过程中,一般都采用行车制动(脚刹),便于在先进的过程中减速停车,不单是使汽车保持不动。
若行车制动失灵时才采用驻车制动。
当车停稳后,就要使用驻车制动(手刹),防止车辆前滑和后溜。
停车后一般除使用驻车制动外,上坡要将档位挂在一档(防止后溜),下坡要将档位挂在倒档(防止前滑)。
使机械运转部件停止或减速所必须施加的阻力矩称为制动力矩。
制动力矩是设计、选用制动器的依据,其大小由机械的型式和工作要求决定。
制动器上所用摩擦材料(制动件)的性能直接影响制动过程,而影响其性能的主要因素为工作温度和温升速度。
摩擦材料应具备高而稳定的摩擦系数和良好的耐磨性。
摩擦材料分金属和非金属两类。
前者常用的有铸铁、钢、青铜和粉末冶金摩擦材料等,后者有皮革、橡胶、木材和石棉等。
3.捷达汽车制动器结构分类制动器按制动目的可分为行车制动器、驻车制动器、应急制动器和辅助制动器。
制动器按耗散能量的方式可分为摩擦式、液力式、电磁式和电涡流式,目前广泛使用的是摩擦式制动器。
摩擦式制动器按其摩擦副的几何形状可分为鼓式、盘式和带式,以鼓式、盘式制动器应用最广泛。
大众捷达鼓式、盘式制动器的分类如图3-1所示。
图3-1制动器分类示意图4.鼓式制动器结构与工作原理及检修4.1捷达汽车领从蹄式制动器结构及制动性能4.1.1领从蹄式制动器结构图4-1 领从蹄式制动器示意图1-领蹄;2-从蹄;3、4-支点;5-制动鼓;6-制动轮缸。
4.1.2领从蹄式制动器的制动性能汽车前进时制动鼓旋转方向(制动鼓正向旋转)如图4-1中箭头所示,沿箭头方向看去,制动蹄1的支点3在前端,制动轮缸6所施加的促动力作用于其后端,因而该制动蹄张开时的旋转方向与制动鼓的旋转方向相同。
具有这种属性的制动蹄称为领蹄。
与此相反,制动蹄2的支点4在后端,促动力加于其前端,其张开时的旋转方向与制动鼓的旋转方向相反。
具有这种属性的制动蹄称为从蹄。
当汽车倒向行驶,即制动鼓反向旋转时,蹄1变成从蹄,而蹄2变成领蹄。
这种在制动鼓正向旋转和反向旋转时,都有一个领蹄和一个从蹄的制动器即称为从蹄式制动器。
领从蹄制动器发展较早,其效能及效能稳定性均居于中游,且有结构较简单。
前进、倒退行使的制动效果不变;结构简单成本低;便于附装驻车制动驱动机构;易于调整蹄片与制动鼓之间的间隙。
热稳定性和制动稳定性均一般。
北京BJ2020N型汽车的后轮制动器和上海桑塔纳轿车、一汽捷达轿车和一汽奥迪100型轿车(四缸机)的后轮制动器都为领从蹄式制动器结构。
4.2上海大众捷达轿车的后轮制动器的结构和原理图4-2 大众捷达轿车后轮制动器1-制动底板;2-销轴;3、4、11、12-弹簧;5-压杆;6-制动杆;7-带杠杆装置的制动蹄总成;8-支架;9-止档板;10-铆钉;13-检测孔;14-压簧;15-夹紧销;16-弹簧座;17-带斜契装置的制动总成;18-摩擦称片;19-斜契支撑;20-契形块;21-制动轮缸。
制动轮缸是双活塞内张型液压轮缸。
制动底板1用螺栓固定在后桥轴端支承座上,制动轮缸21用螺钉固定在制动底板1上方,支架8、止挡板9用铆钉10紧固在底板下方,以上构成了制动底板总成。
夹紧销15、弹簧座16和压簧14将制动蹄17和7紧压在制动底板带储油孔的支承平面上,防止制动蹄轴向窜动。
制动蹄17上固定有斜楔支承19,它用于支撑调节间隙用的楔形块20,称为带斜楔装置的制动蹄总成。
制动蹄7上铆有可以绕销轴2自由转动的制动杆6.制动杆6下端做成构型,与驻车制动钢索相连。
制动蹄7称为带杠杆装置的制动蹄总成。
摩擦衬片18用空心铆钉与制动蹄铆接在一起,铆钉头端部埋入摩擦片中,深度约为新摩擦片的三分之二。
制动蹄的两端做成圆弧形。
复位弹簧3、4、11分别将两个制动蹄上端贴考在轮缸左右活塞端面上,下端贴靠在止挡板两端面上。
制动时,轮缸活塞在制动液压力的作用下推动制动蹄绕制动蹄与止挡板的接触点向外旋转,使摩擦片紧压在制动鼓上,产生制动力矩使汽车制动。
解除制动时,制动液压力消失,在复位弹簧3、4、11的作用下制动蹄复位。
捷达轿车后轮制动器兼作驻车制动器,因此在制动器中装有驻车制动器的机械促动装置(图4-2)。
制动杆6插在压杆5右端槽中,它们的接触点就成为中间支点。
制动蹄7、17的腹板卡在制动压杆两端的槽中。
弹簧4的左端钩在制动压杆的孔中,右端与带杠杆装置的制动蹄腹板相连。
弹簧3的右端卡在制动压杆右端的钩槽内,左端与斜楔支承19的制动蹄腹板相连。
驻车制动时,将车厢内的驻车制动杆连到制动位置,制动钢索拉动制动杆,使之绕销轴2转动;制动杆在转动过程中,压迫制动压杆向左移动,将带斜楔支承的制动蹄压向制动鼓后,制动压杆停止移动,而制动杆绕与压杆接触的点即中间支点转动,把带杠杆的制动蹄总成压向制动鼓,钢索拉得越紧,摩擦片对制动鼓的压力越大,制动鼓与摩擦片之间产生的摩擦力矩也越大。
接触驻车制动时,松开驻车制动杆,制动杆6在复位弹簧作用下回位,同时在复位弹簧3、4、11作用下将两制动蹄拉离制动鼓,回复原位。
4.3捷达汽车鼓式制动器工作原理鼓式制动器一般工作原理是,利用与车身(或车架)相连的非旋转元件和与车轮(或传动轴)相连的旋转元件之间的相互摩擦来阻止车轮的转动或转动的趋势可用一种简单的液压制动系统示意图来说明制动系统的工作原理。
一个以内圆面为工作表面的金属制动鼓固定在车轮轮毂上,随车轮一同旋转。
在固定不动的制动底板上,有两个支承销,支承着两个弧形制动蹄的下端。
制动蹄的外圆面上装有摩擦片。
制动底板上还装有液压制动轮缸,用油管5与装在车架上的液压制动主缸相连通。
主缸中的活塞3可由驾驶员通过制动踏板机构来操纵。
当驾驶员踏下制动踏板,使活塞压缩制动液时,轮缸活塞在液压的作用下将制动蹄片压向制动鼓,使制动鼓减小转动速度,或保持不动。
如下图捷达鼓式制动器示意图。
图4-31-制动踏板;2-推杆;3-主缸活塞;4-制动主缸;5-制动油管;6-制动轮缸;7-轮岗活塞;8-制动鼓;9-摩擦片;10-制动蹄;11-制动底板;12-支撑销;13-制动蹄回位弹簧制动时,驾驶员踩下制动踏板1、推杆2、便推动制动主缸3,迫使制动油液经油管5进入轮缸6,推动轮缸活塞7克服复位弹簧13的拉力,使制动蹄10绕支撑轴12转动而张开,消除制动蹄与制动鼓之间的间隙后压紧在制动鼓上。
这样,不旋转的制动蹄摩擦片9对旋转的制动鼓8就产生一个摩擦力矩,其方向与车轮旋转方向相反,其大小取决于轮缸的张开力、制动鼓和制动蹄的尺寸及摩擦系数。
制动鼓将力矩传至车轮后,由于车轮与路面的附着作用,车轮即对路面作用一个向前的周缘力。
同时,路面也给车轮一个向后的反作用力,这个力就是车轮受到的制动力。
各车轮制动力之和就是汽车受到总制动力。
在制动力作用下使汽车减速,直至停车。
放松制动踏板,在复位弹簧13的作用下,制动蹄与制动鼓的间隙又得到恢复,从而解除制动。
4.4大众捷达鼓式制动器零件的检测4.4.1制动蹄摩擦衬层与制动鼓的检测如图4-4所示,摩擦衬层的厚度不能小于1.0mm,能有不均匀磨损现象,否则,应予以更换。
如果不得不更换任何一个制动蹄片,则需要换左右两轮全部蹄片。
图4-4制动蹄摩擦衬层的检查制动鼓内表面即摩擦面如有划痕或磨损起槽,可用车床将其打磨,一次打磨深度为0.50mm。
打磨后内径比标准内径的扩大不能超过2mm(有些标有MAX,那就是极限尺寸)。
4.4.2检查制动蹄与制动鼓之间的贴合情况①如图4-5所示,在制动鼓摩擦面上均匀涂抹一层白粉笔,将制动蹄在制动鼓内贴合转l 周。
②检查制动蹄表面与制动鼓的接触面积(制动蹄表面的白色部分),应占整个摩擦面的90%以上。
否则,应打磨制动蹄摩擦表面,用砂纸或锯片打磨白色部分,再进行贴合试验,重复进行,直至符合要求。
③将制动蹄中间部分约10mm 宽的地方横向打磨,进行贴合试验,该位置应不白(即未与制动鼓接触),这样有利于在使用中提高制动蹄与制动鼓的接触面积。
图4-5 制动鼓的检查4.4.3鼓式车轮制动器的安装(1)在制动分泵活塞、皮碗上涂一层锂—皂基乙二醇黄油,组装制动分泵,如图4-6所示。
(2)将制动分泵安装在底板上并连接好制动油管。
(3)在底板与制动蹄片的接触面上以及调紧装置螺栓的螺纹和尾端涂抹高温黄油。
(4)将调整装置装至后制动蹄片上,装上后制动蹄片(同时装好驻车制动装置),然后装上前制动蹄片,装好支承弹簧。
(5)如图4-7所示,将后制动蹄的手制动器操纵杆前后拉动,检验调整装置应能回转(即回位),否则应检验后制动蹄的安装是否正确;然后将调整装置的长度尽可能调至最短,装上制动鼓。
(6)制动蹄片与制动鼓间隙的调整。
用螺丝刀从调节孔调节调整螺栓,使制动鼓用手不能转动,再用螺丝刀慢慢放松至制动鼓可用手转动,但有点阻力为宜。