数控铣削加工实例
华中系统数控铣削加工实例

华中系统数控铣削加工实例教学要求:1.掌握数控铣床常用指令。
2.掌握固定循环的应用。
3.掌握数控铣床的操作。
4.运用数控编程的知识,进行零件加工工艺分析,完成典型零件的加工程序编制。
教学内容:⌝HNC-21M的编程指令体系⌝常用指令的综合运用⌝华中(HNC-21/22M)系统的操作第一节HNC-21M的编程指令体系一、辅助功能M代码华中世纪星HNC-21M数控装置M指令功能二、CNC内定的辅助功能1.程序暂停M002.程序结束M023.程序结束并返回到零件程序头M30 4.子程序调用M98及从子程序返回M99三、有关单位的设定1.尺寸单位选择G20、G21、G22四、进给控制指令1.快速定位G002.单方向定位G603.线性进给G014.圆弧进给G02/G03五、回参考点控制指令1.自动返回参考点G282.自动从参考点返回G29六、刀具补偿功能指令1.刀具半径补偿G40、G41、G422.刀具长度补偿G43、G44、G49七、其他功能指令八、简化编程指令1.镜像功能G24、G25格式:G24X__Y__Z__M98P_G25X__Y__Z__说明:G24为建立镜像,G25为取消镜像,XYZ为镜像位置。
2.缩放功能G50、G51格式:G51X_Y_Z_P_M98P_G503.旋转变换G68G69格式:G17G68X__Y__P__G18G68X__Z__P__G19G68Y__Z__P__M98P_G69九、固定循环1.孔加工固定循环指令G73~G892.常用固定循环(1)高速深孔加工循环G73格式:G98/G99G73X_Y_Z_R_Q_P_K_F_L_(2)反攻螺纹循环G74格式:G98/G99G74X_Y_Z_R_P_F_L_(3)精镗循环G76格式:G98/G99G76X_Y_Z_R_P_I_J_F_L_(4)钻孔循环(中心钻)G81格式:G98/G99G81X_Y_Z_R_F_L_(5)带停顿的钻孔循环G82格式:G98/G99G82X_Y_Z_R_P_F_L_(6)深孔加工循环G83格式:G98/G99G83X_Y_Z_R_Q_P_K_F_L_(7)攻螺纹循环G84格式:G98/G99G84X_Y_Z_R_P_F_L_(8)镗孔循环G85G85指令与G84指令相同,但在孔底时主轴不反转。
数控铣削加工工艺与编程实例
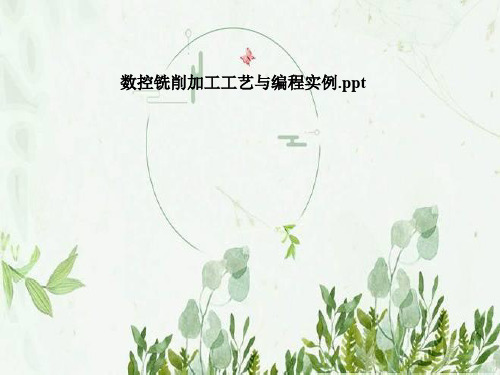
(3)工、量、刃具选择
(4)合理选择切削用量
2.编制参考程序 1)认真阅读零件图,确定工件坐标系。根据工件坐标系 建立原则,X、Y向加工原点选在φ60H7mm孔的中心, Z向加工原点选在B面(不是毛坯表面)。工件加工原点 与设计基准重合,有利于编程计算的方便,且易保证零 件的加工精度。Z向对刀基准面选择底面A,与工件的定 位基准重合,X、Y向对刀基准面可选择φ60H7mm毛坯 孔表面或四个侧面。 2)计算各基点(节点)坐标值。如图3-112所示各圆的 圆心坐标值见表3-32。
子程序:
3.6.4 加工中心零件的编程与操作
图3-105所示为端盖零件,其材料为45钢,毛坯尺寸为 160mm×160mm×19mm。试编写该端盖零件的加工 程序并在XH714加工中心上加工出来。
(1)加工方法 由图3-105可知,该盖板材料为铸铁,故毛坯为铸件,四 个侧面为不加工表面,上下面、四个孔、四个螺纹孔、 直径为φ60mm的孔为加工面,且加工内容都集中在A、 B面上。从定位、工序集中和便于加工考虑,选择A面为 定位基准,并在前道工序中加工好,选择B面及位于B面 上的全部孔在加工中心上一次装夹完成加工。 该盖板零件形状较简单,尺寸较小,四个侧面较光滑, 加工面与非加工面之间的位置精度要求不高,故可选机 用平口钳,以盖板底面A和两个侧面定位,用机用平口 钳的钳口从侧面夹紧。
3)参考程序:数控加工程序单见表3-33。
加工φ160mm中心线上孔的子程序的数控加工程序单见 表3-33。
加工φ100mm中心线上孔的子程序的数控加工程序单见 表3-33。
3.操作步骤及内容 1)机床上电。合上空气开关,按“NC启动”。 2)回参考点。选择“机械回零”方式,按下“循环启动”按钮,完成 回参考点操作。返回零点后,X、Y、Z三轴向负向移动适当距离。 3)刀具安装。按要求将所有刀具安装到刀库,注意刀具号是否正 确。 4)清洁工作台,安装夹具和工件。检查坯料的尺寸,确定工件的 装夹方式(用机用虎钳夹紧)。将机用虎钳清理干净装在干净的工 作台上,通过百分表找正、找平机用虎钳并夹紧,再将工件装正在 机用虎钳上,工件伸出钳口8mm左右。
数控铣床编程实例(铣内外圆并钻孔) 8
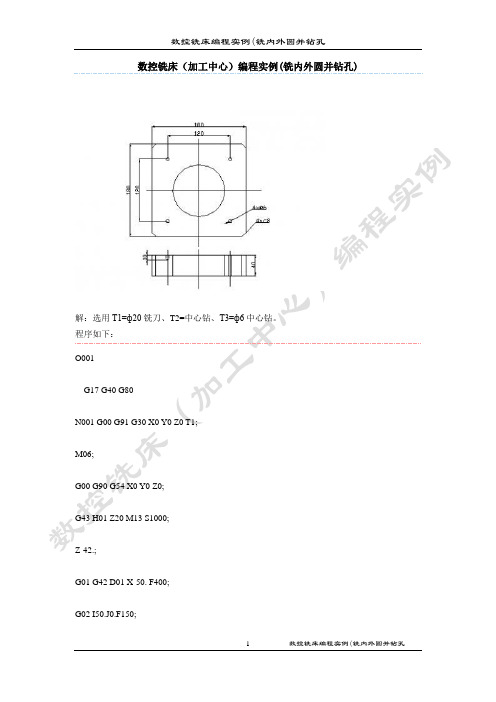
数控铣床(加工中心)编程实例(铣内外圆并钻孔)解:选用T1=ф20铣刀、T2=中心钻、T3=ф6中心钻。
程序如下:O001G17 G40 G80N001 G00 G91 G30 X0 Y0 Z0 T1;M06;G00 G90 G54 X0 Y0 Z0;G43 H01 Z20 M13 S1000;Z-42.;G01 G42 D01 X-50. F400;G02 I50.J0.F150;数控加工工艺分析主要包括的内容数控加工工艺分析的主要内容实践证明,数控加工工艺分析主要包括以下几方面:1)选择适合在数控机床上加工的零件,确定工序内容。
2)分析被加工零件图样,明确加工内容及技术要求,在此基础上确定零件的加工方案,制定数控加工工艺路线,如工序的划分、加工顺序的安排、与传统加工工序的衔接等。
3)设计数控加工工序。
如工步的划分、零件的定位与夹具的选择、刀具的选择、切削用量的确定等。
4)调整数控加工工序的程序。
如对刀点、换刀点的选择、加工路线的确定、刀具的补偿。
5)分配数控加工中的容差。
6)处理数控机床上部分工艺指令。
总之,数控加工工艺内容较多,有些与普通机床加工相似。
数控铣床加工的特点数控铣削加工除了具有普通铣床加工的特点外,还有如下特点:1、零件加工的适应性强、灵活性好,能加工轮廓形状特别复杂或难以控制尺寸的零件,如模具类零件、壳体类零件等。
2、能加工普通机床无法加工或很难加工的零件,如用数学模型描述的复杂曲线零件以及三维空间曲面类零件。
3、能加工一次装夹定位后,需进行多道工序加工的零件。
4、加工精度高、加工质量稳定可靠。
5、生产自动化程序高,可以减轻操作者的劳动强度。
有利于生产管理自动化。
6、生产效率高。
一7、从切削原理上讲,无论是端铣或是周铣都属于断续切削方式,而不像车削那样连续切削,因此对刀具的要求较高,具有良好的抗冲击性、韧性和耐磨性。
在干式切削状况下,还要求有良好的红硬性。
数控系统的组成计算机数控系统由程序、输入/输出设备、计算机数字控制装置、可编程控制器(PLC)、主轴驱动装置和进给驱动装置等组成。
UG数控铣削入门实例教程

UG数控铣削入门实例教程建好要加工的零件模型后,进入UG的“制造”(Manufacturing)功能模块。
初次进入会弹出初始化用户环境对话框,选铣削环境。
以一典型平面铣为例进行介绍。
以下为具体操作步骤:1.创建刀具:点击图标,弹出对话框选择铣刀,弹出对话框设置好刀具直径、长度参数,记住刀具号;2.创建几何体:点击图标,弹出对话框命名父组、名称,记住该名称,点击图标,弹出对话框(1)点击其上图标再点击“选择”按钮,弹出选择零件几何对话框在视图区选择零件模型如图所示单击确认按钮,自动返回上一级对话框。
(2)单击其上图标再点击“选择”按钮,弹出选择毛坯对话框通常毛坯创建方式有多种,可几何体毛坯、特征毛坯、根据表面偏移量定义毛坯等,这里选择“自动毛坯(Auto Block)”,再ZM+栏中输入10,表示平面上有10mm的余量。
然后点击确认按钮,返回上一级对话框,再点击确认结束几何体定义。
3.创建程序:单击工具栏上图标,弹出对话框确认并记住所命名的父组、名称。
4.创建操作:单击工具栏上图标,弹出对话框对话框中选择铣削类型,程序、所用几何、刀具、方法等要和以上所使用的名称一致,然后确认,弹出对话库(1)在其上点击图标,再点击“选择(select)”,弹出对话框,在视图区选择零件相关表面先选择上表面,再选择中间岛屿上表面,然后选择底面,单击确认。
(2)在其上点击图标,再点击“选择(select)”,弹出侧壁几何对话框先选择型腔侧壁,再选择岛屿侧壁,然后单击确认返回上一级对话框。
(3)在其上单击图标,弹出显示参数设置对话框点击确认,一直点击确认,知道生成刀轨为止。
(4)在其上单击刀轨确认验证图标,弹出对话框,选择3D 动态,可进行刀轨模拟。
(5)在其上单击刀轨确认验证图标,可列出所生成刀轨的详细信息。
在上面对话框中选择“文件”,点击“另存为”,将刀轨保存到所需路径下。
5.刀轨文件后处理先如下图所示,在软件最右侧的导航栏中,点选操作导航(Operation Navagator)图标,选择生成刀轨所属操作名称,然后找到工具栏,点击其中“后置处理(Post process)”图标,弹出对话框在其中选择三轴铣床项目,再定义欲输出的G代码文件合法路径,点击确认,弹出后处理好的G代码文件如下图所示,然后另存为所需文件名称,共数控机床加工时使用。
课题6:数控铣削综合加工实例(1)
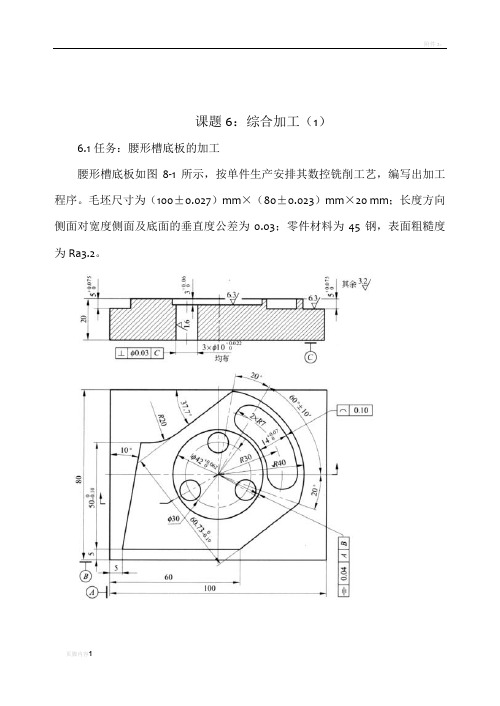
附件2:课题6:数控铣削综合加工实例(1)理论:1.掌握铣削加工的工艺知识;2.掌握综合件的编程思路。
技能:1.能编制综合件的加工程序;2.能熟练使用数控铣床仿真软件;3.能完成综合件仿真加工。
编制综合件的加工程序综合件仿真加工专业课(理实一体)讲授法、引导文教学法、案例教学法、示范法、练习法多媒体、网络或投影仪4/4 0杨丰回顾:铣削单项加工项目1.任务:加工要求、零件图2.相关知识:(1)工艺知识(2)编程知识3.项目实施4.小结课题6:综合加工(1)6.1任务:腰形槽底板的加工腰形槽底板如图8-1所示,按单件生产安排其数控铣削工艺,编写出加工程序。
毛坯尺寸为(100±0.027)mm×(80±0.023)mm×20 mm;长度方向侧面对宽度侧面及底面的垂直度公差为0.03;零件材料为45钢,表面粗糙度为Ra3.2。
6.2 任务决策和实施6.2.1 工艺(1)工艺分析工艺分析该零件包含了外形轮廓、圆形槽、腰形槽和孔的加工,有较高的尺寸精度和垂直度、对称度等形位精度要求。
编程前必须详细分析图纸中各部分的加工方法及走刀路线,选择合理的装夹方案和加工刀具,保证零件的加工精度要求。
外形轮廓中的50和60.73两尺寸的上偏差都为零,可不必将其转变为对称公差,直接通过调整刀补来达到公差要求;3×φ10孔尺寸精度和表面质量要求较高,并对C面有较高的垂直度要求,需要铰削加工,并注意以C面为定位基准;φ42圆形槽有较高的对称度要求,对刀时X、Y方向应采用寻边器碰双边,准确找到工件中心。
加工过程如下:①外轮廓的粗、精铣削,批量生产时,粗精加工刀具要分开,本例采用同一把刀具进行。
粗加工单边留0.2mm余量。
②加工3×φ10孔和垂直进刀工艺孔。
③圆形槽粗、精铣削,采用同一把刀具进行。
④腰形槽粗、精铣削,采用同一把刀具进行。
(2)刀具与工艺参数选择见表8-1、表8-2。
数控铣削编程实例

工 件 坐 标 系 选 择 (G54~G59)
说明
• 1、G54~G59是系统预置的六个坐标系,可根据 需要选用。
• 2、该指令执行后,所有坐标值指定的坐标尺寸 都是选定的工件加工坐标系中的位置。1~6号工 件加工坐标系是通过CRT/MDI方式设置的。
• 3、G54~G59预置建立的工件坐标原点在机床坐 标系中的坐标值可用MDI方式输入,系统自动记 忆。
• 或 G18 G02(G03) X... Z... R... Y... F...
•
G19 G02(G03) Y... Z... R... X... F...
即在原G02、G03指令格式程序段后部再增加一个与加工平 面相垂直的第三轴移动指令,这样在进行圆弧进给的同时 还进行第三轴方向的进给,其合成轨迹就是一空间螺旋线。
❖当圆弧圆心角小于180°时,R为正值,当 圆弧圆心角大于180°时,R为负值。
❖整圆编程时不可以使用R,只能用I、J、K
。
起点
❖F为编程的两个轴的合成进给速度。
2020/3/23
• (3)编程算法
Y r2
(X b,Yb )
B
O2 (Xc,Yc) C
(X2 ,Y2 )
2020/3/23
(X 1,Y 1)
2020/3/23
二、坐标平面选定
坐标平面选择 G17,G18,G19
• 格式: G17
G18
Y
G19
G17
X G19
G18
Z
2020/3/23
Y
➢ G17—— XY平面,
•
G18—— ZX平面,
G17
•
G19—— YZ平面。 G19
X
第7章数控铣削编程与加工应用实例

这种情况下,若用同一把刀进行挖槽加工,则要求刀具在轮 廓边界1上连续切削时,使用一次刀具半径补偿;当刀具在轮廓边界2 上连续切削时,要撤消前次刀具半径补偿,重新建立新的刀具半径补 偿值,粗加工后,根据实测及各自公差的要求对刀补值作不同的修改, 调整后再进行精加工。
上一页 下一页 返回
7.2 挖槽加工实例
4)铣削图7-4(c)所示的凸台轮廓时,亦可看作挖槽加工的特例。 但此时不能用图纸所示的外轮廓作为加工边界,因为将这轮廓作为边 界时,角上的部分材料可能铣不掉,见图7-9(a)所示,1、2、3、4分别 为4个角残留的材料。此时可改为以边界2作为挖槽加工边界,4个角上 就不会留下残余材料。见图7-9(b)所示。
铣削工件外轮廓,通常采用高速钢或硬质合金的立铣刀,下刀点 选择在工件实体外,并使切入点位置和方向尽可能沿工件轮廓切向延 长线方向。刀具切入和切出时要注意避让夹具,并要避免碰到工件上 不该切削的部位。切出工件时仍要尽可能沿工件轮廓切向延长线方向 切出工件,以利于刀具受力平稳同时尽可能保证工件轮廓过度处无明 显接痕。
2)选择加工机床:用立式三坐标数控铣床较为合适 3)加工工序与工步的划分及走刀路线的确定 根据图样分析,凸台加工时材料的切削量不大,而且材料的切削 性能较好,选择φ20的圆柱形直柄立铣刀,材料为高速钢(HSS),沿 轮廓铣削一周即可去处余量,考虑实习用机床主轴刚性不够,深度 6mm,采用分层加工每次切深3mm。
(1)图7-3中基点A的坐标计算
在Rt△O1CD中,
典型零件数控加工工艺分析实例

说明:表格中刀尖半径和备注栏可以不要;25×25 指车刀刀柄的截面尺寸。
(5)切削用量选择
一般情况下,粗车:恒转速 n=800r/min 恒线速 v=100m/min
进给量 f=0.2mm/r 以下
vf=120m/min
背吃刀量 ap=2mm 以下
精车:恒转速 n=1100r/min 恒线速 v=150m/min
以零件右端面和中心轴作为 坐标原点建立工件坐标系。
根据零件尺寸精度及技术要 求,零件从右向左加工,将粗、 精加工分开来考虑。
加工工艺顺序为:车削右端面→复合型车削固定循环粗、精加工右端需要加工的所有轮 廓(粗车Φ44、Φ40.5、Φ34.5、Φ28.5、Φ22.5、Φ16.5 外圆柱面→粗车圆弧面 R14.25→ 精车外圆柱面Φ40.5→粗车外圆锥面→粗车外圆弧面 R4.75→精车圆弧面 R14→精车外圆锥 面→精车外圆柱面Φ40→精车外圆弧面 R5)。 (4)选择刀具
所选定刀具参数如表 1-2 所示。 说明:铣削内、外轮廓时,铣刀直径受槽宽限制,可选择φ6 的立铣刀;精铰的量通常 小于 0.2mm;刀刃和长度通常要比切削的深度大。 5.切削用量选择 一般情况下,粗铣:恒转速 n=600r/min
进给量 f=180mm/min 以下 背吃刀量 ap=5mm 以下 精车:恒转速 n=800r/min 进给量 f=120mm/min 以下
零件的底面和外部轮廓已经加工,本工序是在铣床上加工槽与孔。 1.零件图分析
凸轮内外轮廓由直线和圆弧组成。凸轮槽侧面和
20
0.021 0
、
12
0.018 0
两个内孔尺寸精
度要求较高,表面粗糙度要求也较高,Ra1.6;内孔
20
- 1、下载文档前请自行甄别文档内容的完整性,平台不提供额外的编辑、内容补充、找答案等附加服务。
- 2、"仅部分预览"的文档,不可在线预览部分如存在完整性等问题,可反馈申请退款(可完整预览的文档不适用该条件!)。
- 3、如文档侵犯您的权益,请联系客服反馈,我们会尽快为您处理(人工客服工作时间:9:00-18:30)。
N21 G01 X42 Y0;
N22 G01 X48 Y0; N23 G01 X48 Y50; N24 G0 Z5 M09; N25 M30;
铣端面
G17 G21 G28 G40 G49 G80 G90 G91 G94
Xy平面选择 公制单位输入选择 参考点返回 取消刀具半径补偿 取消刀具长度补偿 取消固定循环 绝对坐标编程 增量坐标编程 每分钟进给量
Y50;
X6; Y0; X12; Y50; X18; Y0;
X24;
Y50; X30; Y0; X36; Y50; X42;
Y0;
X48; Y50; G0 Z5 M09;
O4321 G0 G40 G49 G80 G90 G17 G21 G97 G94; G91 G28 Z0; G28 X0 Y0; G0 G90 G54 X-25 Y-25 S300 M03; Z3; G01 Z-7 F120; X-10 Y5; X40 M08; G03 R5 X45 Y10; G01 Y45; X10; G03 R5 X5 Y40; G01 Y-5; G0 Z5 M09; M30;
铣轮廓
实例二
已知主轴转速为:400r/min,进给量为:200mm/min.
O2323 G0 G40 G49 G80 G90 G17 G21 G97 G94; G0 G90 G54 X-35 Y-70 S400 M03; Z50; G01 Z-25.0 F1000 M08; X-60 F200; G03 X-110 Y-20 R50; G01 Y-40; G02 X-140 Y-70 R-30; G01 X-160; G03 X-110 Y-120 R50; G01 Y-140; X-80; 当圆弧圆心角α≤180°,R取正值, G02 X-40 Y-100 R40; G01 Y-65; 当α > 180°,R取负值。 G0 Z50; M30;
数 控 加 工
工程训练中心
数控铣加工编程实例
编程应该注意的几个问题:
数控装置初始状体的设定 工件坐标系的设置
安全高度的确定
进、退刀方式的确定
数控铣加工编程实例
O1234 N01 G0 G40 G49 G80 G90 G17 G21 G97 G94; N03 G91 G28 Z0; N03 G28 X0 Y0; N04 G0 G90 G54 X0 Y-25 S300 M03; N05 G0 X0 Y-25 Z3; N06 G01 X0 Y-25 Z-2 F120 M08;
铣轮廓
为了保证程序运行安全,在程序开始应该有程序初始状态设定程序段。
数控铣加工编程实例
O1234 G0 G40 G49 G80 G90 G17 G21 G97 G94; G91 G28 Z0; G28 X0 Y0; G0 G90 G54 X0 Y-25 S300 M03; Z3; G01 Z-2 F120 M08;
N07 G01 X0 Y50 ;
N08 G01 X6 Y50; N09 G01 X6 Y0; N10 G01 X12 Y0; N11 G01 X12 Y50; N12 G01 X18 Y50; N13 G01 X18 Y0;
N14 G01 X24 Y0 ;
N15 G01 X24 Y50; N16 G01 X30 Y50; N17 G01 X30 Y0; N18 G01 X36 Y0; N19 G01 X36 Y50; N20 G01 X42 Y50;