工艺验证标准操作规程
检验方法验证标准操作规程(最新整理)
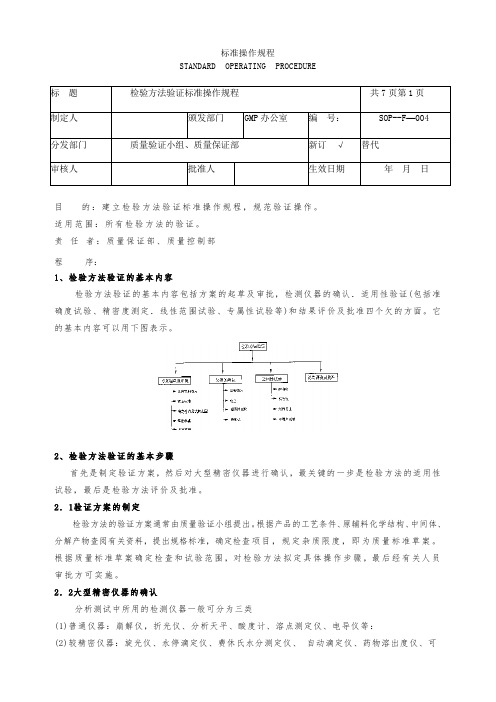
标准操作规程STANDARD OPERATING PROCEDURE标题检验方法验证标准操作规程共7页第1页制定人颁发部门GMP办公室编号: SOP--F—004分发部门质量验证小组、质量保证部新订√替代审核人批准人生效日期年月日目的:建立检验方法验证标准操作规程,规范验证操作。
适用范围:所有检验方法的验证。
责任者:质量保证部、质量控制部程序:1、检验方法验证的基本内容检验方法验证的基本内容包括方案的起草及审批,检测仪器的确认.适用性验证(包括准确度试验、精密度测定.线性范围试验、专属性试验等)和结果评价及批准四个欠的方面。
它的基本内容可以用下图表示。
2、检验方法验证的基本步骤首先是制定验证方案,然后对大型精密仪器进行确认,最关键的一步是检验方法的适用性试验,最后是检验方法评价及批准。
2.1验证方案的制定检验方法的验证方案通常由质量验证小组提出。
根据产品的工艺条件、原辅料化学结构、中间体、分解产物查阅有关资料,提出规格标准,确定检查项目,规定杂质限度,即为质量标准草案。
根据质量标准草案确定检查和试验范围,对检验方法拟定具体操作步骤,最后经有关人员审批方可实施。
2.2大型精密仪器的确认分析测试中所用的检测仪器一般可分为三类(1)普通仪器:崩解仪,折光仪、分析天平、酸度计、溶点测定仪、电导仪等:(2)较精密仪器:旋光仪、永停滴定仪、费休氏水分测定仪、自动滴定仪、药物溶出度仪、可共7页第2页见分光光度计、电泳仪等;(3)大型精密仪器:紫外分光光度计、红外分光光度计、气相色谱仪、高效液相色谱仪、薄层扫描仪等。
为了保证分析测试数据准确可靠,每台检测仪器在投入正式使用之前都应进行确认。
检测仪器的确认是检验方法验证的基础,应在其它验证试验开始之前首先完成。
检测仪器确认工作内容应根据仪器类型。
技术性能而定,通常包括:安装确认、校正、适用性预试验和再确认。
2.2.1安装确认同工艺验证中机械设备一样,仪器安装确认的土要内容包括如下各点:(1)要登记仪器名称.型号。
工艺检修安全操作规程范本

工艺检修安全操作规程范本一、检修前的准备工作1、检修前必须了解工艺检修设备的工作原理、结构、操作要领以及需要使用的工具和材料等。
2、检修前应对设备进行全面检查,确保设备没有异常情况存在。
3、检查并确认检修设备的电源已经切断,并采取相应的安全措施,如安装气缸等。
二、操作流程和注意事项1、确保胸前的工艺检修设备及周边区域没有杂物,保持整洁,防止跌倒和绊倒。
2、在进行操作前必须穿戴好相应的个人防护装备,如安全帽、安全鞋、手套等。
3、操作过程中严禁将手伸入设备运转的传动部位,避免发生夹伤或切割伤。
4、在操作过程中严禁随意更改设备的工作参数,以免引发事故。
5、操作过程中,对于设备发出的异常声音、异常振动等情况,应立即停止操作,并向相关责任人报告。
6、检修过程中严禁喧哗,并保持良好的工作秩序,避免发生其他事故。
三、应急处理措施1、发生意外事故时,首先要立即采取停机措施,并切断设备电源,确保人员和设备的安全。
2、如发生火灾等紧急情况,应立即拨打火警电话,并采取相应的灭火措施,确保火灾不扩散,保护周围人员的安全。
3、在伤员的处理中,应根据具体情况及时提供急救,并及时报告相关领导和医疗部门。
四、结束工作后的处理1、检修工作结束后,要在设备周围进行整理和清理,保持整洁。
2、及时报告检修工作的完成情况,并填写相应的工作记录和检修报告。
3、检修工作结束后,工艺检修设备应进行再次检查,确保设备可安全使用。
五、安全意识培养1、通过定期的安全培训、安全提示等方式,加强工艺检修操作人员的安全意识,提高其安全操作技能。
2、定期组织安全演练,加强人员的应急处理能力和危险情况下的反应能力。
3、对工艺检修操作过程中发生的安全事故进行分析和总结,提出改进措施,以防止类似事故再次发生。
六、安全责任1、设立专门的工艺检修安全管理人员,负责工艺检修操作的安全管理和督促,确保工艺检修操作规程的执行。
2、明确安全责任,对违反安全操作规程的操作人员进行相应的处理和纪律性处罚。
工艺验证标准操作规程
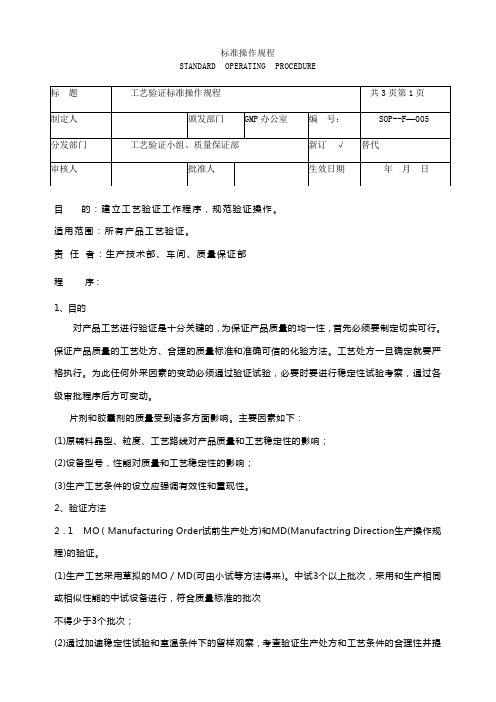
标准操作规程STANDARD OPERATING PROCEDURE目的:建立工艺验证工作程序,规范验证操作。
适用范围:所有产品工艺验证。
责任者:生产技术部、车间、质量保证部程序:1、目的对产品工艺进行验证是十分关键的,为保证产品质量的均一性,首先必须要制定切实可行。
保证产品质量的工艺处方、合理的质量标准和准确可信的化验方法。
工艺处方一旦确定就要严格执行。
为此任何外采因素的变动必须通过验证试验,必要时要进行稳定性试验考察,通过各级审批程序后方可变动。
片剂和胶囊剂的质量受到诸多方面影响。
主要因素如下:(1)原辅料晶型、粒度、工艺路线对产品质量和工艺稳定性的影响;(2)设备型号,性能对质量和工艺稳定性的影响;(3)生产工艺条件的设立应强调有效性和重现性。
2、验证方法2.1 MO(Manufacturing Order试前生产处方)和MD(Manufactring Direction生产操作规程)的验证。
(1)生产工艺采用草拟的MO/MD(可由小试等方法得来)。
中试3个以上批次,采用和生产相同或相似性能的中试设备进行,符合质量标准的批次不得少于3个批次;(2)通过加速稳定性试验和室温条件下的留样观察,考查验证生产处方和工艺条件的合理性并提出结论性报告;(3)根据中试批次的质量状况和稳定性试验小结,确定及草拟供试生产批次的MO/MD,并采用大生产设备进行试生产。
2.2通过试生产,制定现行MO/MD此为生产工艺的运行验证。
(1)使用大生产设备试生产2~3个批次,验证MO/MD的可行性和重现性;(2)根据试生产情况,必要时调整工艺条件和参数;(3)通过加速稳定性试验,考查验证生产处方和工艺条件对大生产的适应性并提出结论性报告;(4)制定切实可行的MO/MD并移交大生产。
2.3产品工艺验证这是针对某个产品分别进行的项目,依据产品不同和工艺方法不同制定不同的验证项目以及验证参数,为统一起见,在此按工艺流程分工序加以叙述,使用时可根据实际进行取舍。
工艺方法验证规程
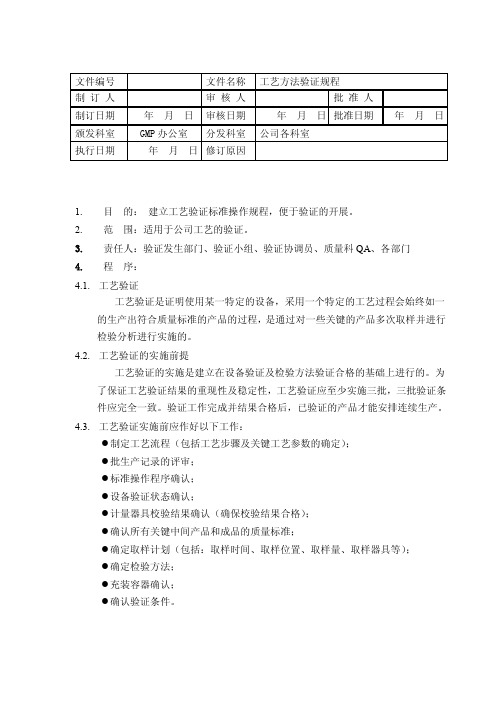
1.目的:建立工艺验证标准操作规程,便于验证的开展。
2.范围:适用于公司工艺的验证。
3.责任人:验证发生部门、验证小组、验证协调员、质量科QA、各部门4.程序:4.1.工艺验证工艺验证是证明使用某一特定的设备,采用一个特定的工艺过程会始终如一的生产出符合质量标准的产品的过程,是通过对一些关键的产品多次取样并进行检验分析进行实施的。
4.2.工艺验证的实施前提工艺验证的实施是建立在设备验证及检验方法验证合格的基础上进行的。
为了保证工艺验证结果的重现性及稳定性,工艺验证应至少实施三批,三批验证条件应完全一致。
验证工作完成并结果合格后,已验证的产品才能安排连续生产。
4.3.工艺验证实施前应作好以下工作:●制定工艺流程(包括工艺步骤及关键工艺参数的确定);●批生产记录的评审;●标准操作程序确认;●设备验证状态确认;●计量器具校验结果确认(确保校验结果合格);●确认所有关键中间产品和成品的质量标准;●确定取样计划(包括:取样时间、取样位置、取样量、取样器具等);●确定检验方法;●充装容器确认;●确认验证条件。
4.4.验证程序4.4.1.验证时间在以下情况下需实施工艺验证:●新产品开始进行批量生产;●关键工艺步骤发生变化;●重要材料改变(产地、规格等);●设备改变(与产品质量有关的设备);●通过产品年度回顾,对现行工艺过程产生疑问时。
4.4.2.验证方法4.4.2.1.工艺验证是基于大量的取样检测和对关键步骤的周密监测的基础上进行的。
4.4.2.2.正式工艺验证之前,如对所要验证的工艺流程(参数)无充分依据确定时,应先实施预验证。
通过预验证初步确定所要验证的工艺流程(参数),然后再实施正式工艺验证。
预验证的次数无明确规定,视工艺流程(参数)能否初步确定为准。
4.4.2.3.正式工艺验证至少应连续进行3批,以证明工艺验证过程的重现性。
3批验证的工艺流程及工艺参数应确保一致,不得随意更改。
如在验证过程中出现偏离验证可接受限度现象时,应及时查找原因,采取措施。
工艺验证标准操作规程
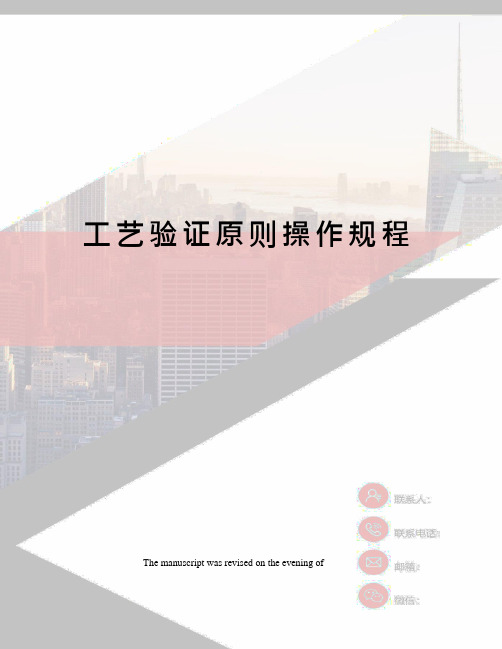
工艺验证原则操作规程The manuscript was revised on the evening ofXXXX有限公司现行文献1.目的:建立工艺验证的原则操作规程,并规范其操作。
2.范畴:合用于公司全部生产产品工艺的验证。
3.责任:生产部门负责验证方案与报告的编写;化验室负责验证过程中的检测工作;质量部负责验证方案与报告的同意与其中的偏差调查。
4.规程:验证的类型:工艺验证普通能够按照下列三种方式进行:前验证、同时验证、回想性验证。
4.1.1前验证:针对新的生产工艺或当工艺发生重大变化时所进行的工艺验证应采用前验证的方式,在验证成功结束之后才能够以放行产品。
工艺验证中所生产的产品批量应与最后上市的产品批量相似。
普通,工艺验证规定进行持续三个成功批次的生产。
4.1.2同时验证:在某些非常特殊的状况下也能够接受通过同时验证的方式进行工艺验证,即在常规生产过程中进行验证。
同时验证中生产的产品如果符合全部验证方案中规定的规定,能够在最后验证报告完毕之前放行。
进行同时验证的决定必须合理、有文献统计并且通过质量部门同意。
同时性验证办法合用于下列状况:4.1.2.1由于需求很小而不常生产的产品;4.1.2.2生产量很小的产品,如放射性药品;4.1.2.3从前未经验证的遗留工艺过程,没有重大变化的状况下;4.1.2.4已有的、已经验证的工艺过程发生较小的变化时;4.1.2.5已验证的工艺进行周期性再验证时。
4.1.3回想性验证:有些历史遗留的产品未进行工艺验证。
4.1.3.1这些工艺过程在满足下列条件能够通过对历史数据回想的方式进行回想性验证:4.1.3.始终按照市售产品批量规模进行生产,能够较好的理解生产中的工艺过程并都统计下来;4.1.3.有通过药典规定或通过验证明验办法进行检测所得到的充足可靠的验证数据;4.1.3.对核心程序参数和核心质量特性做了规定并进行了控制;4.1.3.建立了工艺过程的中间控制和可接受原则;4.1.3.没有由于操作失误和设备故障之外而引发的任何工艺过程或产品失败;4.1.3.在产品生产中应用的药品活性成分的杂质谱已经建立;4.1.3.同时还应含有:工艺过程没有重大的历史变化:全部核心工艺参数和核心质量特性都能够作为有代表性的历史数据;执行回想性验证的决定应得到质量部门同意。
工艺验证指南
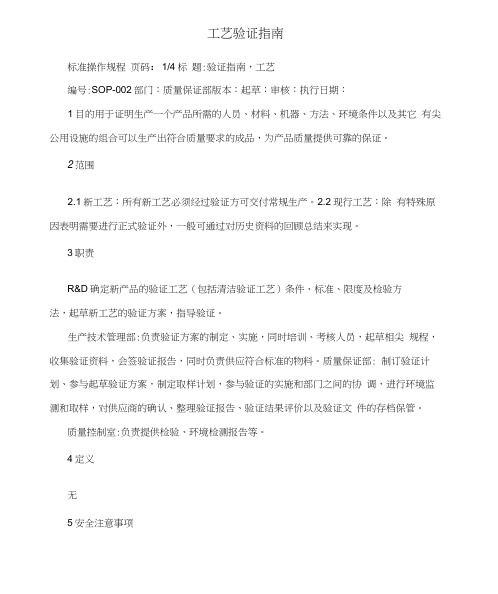
工艺验证指南标准操作规程页码:1/4标题:验证指南,工艺编号:SOP-002部门:质量保证部版本:起草:审核:执行日期:1目的用于证明生产一个产品所需的人员、材料、机器、方法、环境条件以及其它有尖公用设施的组合可以生产出符合质量要求的成品,为产品质量提供可靠的保证。
2范围2.1新工艺:所有新工艺必须经过验证方可交付常规生产。
2.2现行工艺:除有特殊原因表明需要进行正式验证外,一般可通过对历史资料的回顾总结来实现。
3职责R&D确定新产品的验证工艺(包括清洁验证工艺)条件、标准、限度及检验方法,起草新工艺的验证方案,指导验证。
生产技术管理部:负责验证方案的制定、实施,同时培训、考核人员,起草相尖规程,收集验证资料,会签验证报告,同时负责供应符合标准的物料。
质量保证部: 制订验证计划、参与起草验证方案,制定取样计划,参与验证的实施和部门之间的协调,进行环境监测和取样,对供应商的确认、整理验证报告、验证结果评价以及验证文件的存档保管。
质量控制室:负责提供检验、环境检测报告等。
4定义无5安全注意事项6规程6.1验证程序:6.1.2验证要求:6.1.2.1生产工艺验证应在完成厂房和设施、设备的验证和质量控制以及计量部门的验证后,对生产线所在的生产环境及装备的局部或整体功能、质量控制方法及工艺条件进行验证。
6.1.2.2 验证的工艺条件要模拟生产实际并考虑到可能遇到的条件,可以采用最差状况的条件或挑战性试验。
6.1.2.3 工艺验证至少应连续进行三次以证明其可靠性和重现性。
最差条件:指该工艺条件或状态其导致工艺及产品失败的可能性比正常的工艺条件更高的条件。
挑战性试验:指对某一工艺、设备或设施设定的苛刻条件的试验。
6.1.3验证方案内容:凡能对产品质量产生差异和影响的尖键生产工艺都应进行验证。
内容包括验证目的、范围、方法、最差状况和可接受标准,同时,应制订常规生产所需的全部标准操作程序(SOP),至少应有这些程序的草案。
工艺验证标准操作规程
工艺验证和中试放大标准操作规程工艺验证目的是证实某一工艺过程确实能稳定地生产出符合预定规格及质量标准的产品。
即通过验证,证明被验证的产品工艺处于“受控状态”产品质量保证目标:产品的设计和产生应符合优质、安全和有效的原则;产品质量应在药品生产全过程中形成;生产工艺中的每一个环节都能得到控制。
工艺验证是确保质量目标的关键要素。
工艺放大是工艺研究的重要内容,是实验室制备技术向工业化生产转移的必要阶段,是药品工业化生产的重要基础,同时也是制剂工艺进一步完善和优化过程。
由于实验室制剂设备、操作条件等与工业化生产的差别,实验室建立的制剂工艺在工业化生产中常常会遇到问题。
如胶囊剂工业化生产采用的高速填装设备与实验室设备不一致,实验室确定的处方颗粒的流动性可能并不完全适和生产的需要,可能导致重量差异变大;对于缓释、控释等新剂型,工艺放大研究更为重要。
研究重点主要有两方面,一是考察生产过程的主要环节,进一步优化工艺条件;二是确定适合工业化生产的设备和生产方法,保证工艺放大后产品的质量和重现性。
研究中需要注意对数据的详实记录和积累,发现前期研究建立的制备工艺与生产工艺之间的差别,包括生产设备方面(设计原理及操作原理)存在的差别。
如这些差别可能影响制剂的性能,则需要考虑进行进一步研究或改进。
一、工艺组经过多批小试,确定显著影响制剂质量的工艺参数。
确定工艺参数的合理范围和工艺验证方案。
由工艺验证组组长(新药部部门经理)确认工艺验证方案。
工艺验证方案中应包括:项目名称、方案编号、验证目的、验证方法、控制标准、验证步骤、验证周期、验证记录(空白样张)、验证报告(空白样张)、方案制定人、审核人、批准人及日期。
质量组负责制定取样和检验的操作规程。
二、工艺重现:工艺组组长组织工艺验证的全过程。
工艺根据确定的处方和工艺参数,组织人员严格按照拟定的方案执行。
1.验证前准备:验证小组对使用的设备和主辅料进行确认。
2.验证过程:为了显示试验结果的重现性,每个试验要重复3次。
工艺验证标准操作规程
XXXX有限公司现行文件1.目的:建立工艺验证的标准操作规程,并规范其操作。
2.范围:适用于公司所有生产产品工艺的验证。
3.责任:生产部门负责验证方案与报告的编写;化验室负责验证过程中的检测工作;质量部负责验证方案与报告的批准与其中的偏差调查。
4.规程:验证的类型:工艺验证通常可以按照以下三种方式进行:前验证、同步验证、回顾性验证。
4.1.1前验证:针对新的生产工艺或当工艺发生重大变化时所进行的工艺验证应采用前验证的方式,在验证成功结束之后才可以以放行产品。
工艺验证中所生产的产品批量应与最终上市的产品批量相同。
通常,工艺验证要求进行连续三个成功批次的生产。
4.1.2同步验证:在某些非常特殊的情况下也可以接受通过同步验证的方式进行工艺验证,即在常规生产过程中进行验证。
同步验证中生产的产品如果符合所有验证方案中规定的要求,可以在最终验证报告完成之前放行。
进行同步验证的决定必须合理、有文件记录并且经过质量部门批准。
同步性验证方法适用于以下情况:4.1.2.1由于需求很小而不常生产的产品;4.1.2.2生产量很小的产品,如放射性药品;4.1.2.3从前未经验证的遗留工艺过程,没有重大改变的情况下;4.1.2.4已有的、已经验证的工艺过程发生较小的改变时;4.1.2.5已验证的工艺进行周期性再验证时。
4.1.3回顾性验证:有些历史遗留的产品未进行工艺验证。
4.1.3.1这些工艺过程在满足以下条件可以通过对历史数据回顾的方式进行回顾性验证:4.1.3.一直按照市售产品批量规模进行生产,能够很好的理解生产中的工艺过程并都记录下来;4.1.3.有通过药典规定或经过验证实验方法进行检测所得到的充足可靠的验证数据;4.1.3.对关键程序参数和关键质量特性做了规定并进行了控制;4.1.3.建立了工艺过程的中间控制和可接受标准;4.1.3.没有由于操作失误和设备故障之外而引起的任何工艺过程或产品失败;4.1.3.在产品生产中应用的药物活性成分的杂质谱已经建立;4.1.3.同时还应具备:工艺过程没有重大的历史改变:所有关键工艺参数和关键质量特征都可以作为有代表性的历史数据;执行回顾性验证的决定应得到质量部门批准。
工艺验证指南
工艺验证指南标准操作规程页码:1/4 标题: 验证指南,工艺编号:soP-002部门:质量保证部版本:起草:审核:执行日期:1 目的用于证明生产一个产品所需的人员、材料、机器、方法、环境条件以及其它有关公用设施的组合可以生产出符合质量要求的成品,为产品质量提供可靠的保证。
2 范围2.1 新工艺:所有新工艺必须经过验证方可交付常规生产。
2.2 现行工艺:除有特殊原因表明需要进行正式验证外,一般可通过对历史资料的回顾总结来实现。
3 职责R&D确定新产品的验证工艺(包括清洁验证工艺)条件、标准、限度及检验方法,起草新工艺的验证方案,指导验证。
生产技术管理部:负责验证方案的制定、实施,同时培训、考核人员,起草相关规程,收集验证资料,会签验证报告,同时负责供应符合标准的物料。
质量保证部:制订验证计划、参与起草验证方案,制定取样计划,参与验证的实施和部门之间的协调,进行环境监测和取样,对供应商的确认、整理验证报告、验证结果评价以及验证文件的存档保管。
质量控制室:负责提供检验、环境检测报告等。
4 定义5 安全注意事项6 规程6.1 验证程序:6.1.2 验证要求:6.1.2.1 生产工艺验证应在完成厂房和设施、设备的验证和质量控制以及计量部门的验证后,对生产线所在的生产环境及装备的局部或整体功能、质量控制方法及工艺条件进行验证。
6.1.2.2 验证的工艺条件要模拟生产实际并考虑到可能遇到的条件,可以采用最差状况的条件或挑战性试验。
6.1.2.3 工艺验证至少应连续进行三次以证明其可靠性和重现性。
最差条件: 指该工艺条件或状态其导致工艺及产品失败的可能性比正常的工艺条件更高的条件。
挑战性试验: 指对某一工艺、设备或设施设定的苛刻条件的试验。
6.1.3 验证方案内容:凡能对产品质量产生差异和影响的关键生产工艺都应进行验证。
内容包括验证目的、范围、方法、最差状况和可接受标准,同时,应制订常规生产所需的全部标准操作程序(SOP),至少应有这些程序的草案。
验证标准操作规程
验证标准操作规程《验证标准操作规程》验证标准操作规程(SOP)是指一套经过验证和受控的操作程序,用于确保产品或服务达到特定标准和要求。
在各种行业中,SOP被广泛应用于生产、制造、服务和研发等领域,以确保过程的一致性、可靠性和符合性。
在实际操作中,验证标准操作规程通常涉及到一系列步骤和程序,包括但不限于:确定验证对象、编制验证计划、进行验证测试、记录验证结果、评估验证数据等。
通过这些程序,可以确保产品或服务在设计、生产、测试和使用过程中的一致性和稳定性。
验证标准操作规程的编制和执行对于组织来说至关重要。
首先,它可以帮助组织确保产品或服务的质量和可靠性,从而提升客户满意度和市场竞争力。
其次,它可以帮助组织确保生产过程的一致性和符合性,从而减少质量风险和提升生产效率。
再次,它可以帮助组织确保在监管要求和法律法规方面的合规性,避免潜在的法律风险和责任。
然而,验证标准操作规程的编制和执行也面临一些挑战。
例如,需要严格遵循相关标准和要求,确保验证过程的可靠性和有效性;需要合理安排验证时间和资源,确保验证过程的及时性和经济性;需要培训和指导相关人员,确保验证操作的规范性和合规性。
因此,对于组织来说,建立健全的验证标准操作规程体系是至关重要的。
这不仅需要组织高层的支持和重视,也需要相关部门的合作和配合。
只有这样,组织才能在竞争激烈的市场环境中保持持续的创新和发展。
总之,验证标准操作规程在现代组织中扮演着重要的角色,它不仅是确保产品或服务质量的保障,也是提升组织竞争力的重要手段。
因此,组织需要高度重视验证标准操作规程的编制和执行,不断完善和优化相关体系,以适应快速变化的市场环境和技术发展。
- 1、下载文档前请自行甄别文档内容的完整性,平台不提供额外的编辑、内容补充、找答案等附加服务。
- 2、"仅部分预览"的文档,不可在线预览部分如存在完整性等问题,可反馈申请退款(可完整预览的文档不适用该条件!)。
- 3、如文档侵犯您的权益,请联系客服反馈,我们会尽快为您处理(人工客服工作时间:9:00-18:30)。
标准操作规程
STANDARD OPERATING PROCEDURE
目的:建立工艺验证工作程序,规范验证操作。
适用范围:所有产品工艺验证。
责任者:生产技术部、车间、质量保证部
程序:
1、目的
对产品工艺进行验证是十分关键的,为保证产品质量的均一性,首先必须要制定切实可行。
保证产品质量的工艺处方、合理的质量标准和准确可信的化验方法。
工艺处方一旦确定就要严格执行。
为此任何外采因素的变动必须通过验证试验,必要时要进行稳定性试验考察,通过各级审批程序后方可变动。
片剂和胶囊剂的质量受到诸多方面影响。
主要因素如下:
(1)原辅料晶型、粒度、工艺路线对产品质量和工艺稳定性的影响;
(2)设备型号,性能对质量和工艺稳定性的影响;
(3)生产工艺条件的设立应强调有效性和重现性。
2、验证方法
2.1 MO(Manufacturing Order试前生产处方)和MD(Manufactring Direction生产操作规程)的验证。
(1)生产工艺采用草拟的MO/MD(可由小试等方法得来)。
中试3个以上批次,采用和生产相同或相似性能的中试设备进行,符合质量标准的批次
不得少于3个批次;
(2)通过加速稳定性试验和室温条件下的留样观察,考查验证生产处方和工艺条件的合理性并提出结论性报告;
(3)根据中试批次的质量状况和稳定性试验小结,确定及草拟供试生产批次的MO/MD,并采用大生产设备进行试生产。
2.2通过试生产,制定现行MO/MD
此为生产工艺的运行验证。
(1)使用大生产设备试生产2~3个批次,验证MO/MD的可行性和重现性;
(2)根据试生产情况,必要时调整工艺条件和参数;
(3)通过加速稳定性试验,考查验证生产处方和工艺条件对大生产的适应性并提出结论性报告;
(4)制定切实可行的MO/MD并移交大生产。
2.3产品工艺验证
这是针对某个产品分别进行的项目,依据产品不同和工艺方法不同制定不同的验证项目以及验证参数,为统一起见,在此按工艺流程分工序加以叙述,使用时可根据实际进行取舍。
(1)粉碎设计试验条件:速度、筛目大小、型号、刀的方向。
每次取3~5个样品。
评估项目:筛目分析,松密度、时间、休止角。
按MD规定条件粉碎,质量应符合要求。
(2)预混合设计试验条件:混合转速、混合时间。
每次取3~5个样品。
评估项目:水分、含量。
按MD规定条件混合,质量应符合要求。
(3)制粒设计试验条件:软材搅拌条件及时间,干燥温度及时间、粘合剂浓度及用量。
每次取3~5个样品。
评估项目:水分、筛目分析、松密度。
按MD规定参数制粒,质量应符合要求。
(4)总混合设计试验条件:如某产品规定混合时间10mim,验证时间可设定为5、10、15、20min,每次又设不同取样点。
评估项目:含量均匀度、水分(参考附表1)、粒度分布,松密度、颜色均匀度(指有不同颜色组分的产品)。
验证10min的规定是合理的。
(5)压片设计试验条件:转速、压力、压片时间、设定每15min取样1次直至300mim。
评估项目:外观、片重差异、厚度、溶出度(崩解时限)、含量(参考附表2)、脆碎度。
按MD参数压片,应适应包衣要求,并符合质量标准。
(6)包衣设计试验条件:锅速、进/排风温度、喷射速率、喷雾粒度、直径,包衣液用量、包衣液浓度、手工加料时的加料量、加料间隔,每次取3~6个样品,(参考附表3) 评估项目:片面、片重差异、溶出度(崩解时限)、色泽均匀性。
按MD规定参数包衣,质量符合要求。
(7)胶囊充填设计试验条件:转速、环境温湿度差、充填时间,设定每15min取样1次,直至300mim。
评估项目:外观、囊重差异、溶出度(或释放速率)、含量。
按MD规定条件操作,质量应符合要求。
(8)热合包装设计试验条件:运行速度、热封温度、热材压力(或热合轴间隙),设定每15mim 取样1次直至300min。
评估项目:外观、渗漏试验。
按包装操作规程(Packaging Direction PKD)操作,质量应符合要求。
3、工艺验证结论
工艺验证结束后,将所得到的验证数据及记录进行整理,写出验证报告。
再由验证小组成员综合工艺过程、设备参数、试验结果全面对验证内容和结果进行分析、评价,最后给出验证结论,呈报主管领导审核批准。
只有当生产工艺得到验证认可,该产品的生产工艺才能子以执行。
4、工艺验证文件
4.1验证方案内容
(1)封面格式统一(写明产品名称、规格、编码、验证编号、起草人签名,审批人批准签名及日期,这样便于管理及可追踪性)。
(2)目录
(3)概述(本方案制定原因及依据,实施计划,涉及到的程序)。
(4)工艺验证内容:
—验证目的;
—验证标准;
—验证产品和文件
—验证/检验方法及步骤;
—验证结果及批准。
4.2验证实施
记录,进行必须的分析检验。
4.3验证报告
(1)封面(与工艺验证方案首页格式类似)
(2)目录
(3)概述(本报告执行的验证方案、验证批次及有关情况概要)。
(4)验证结果小结(与方案一一对应)
—可接受标准;
—数据统计。
一数据统计。
5、验证结论
6、总体评价
验证报告由验证小组成员审批验证内容和结论。
附表1: 混合验证试验记录
批号: 日期: 年月日
化验员:
附表2: 压片验证试验记录
批号: 日期: 年月日
附表3: 包衣验证试验记录。