SMT工艺制程详细流程图
SMT车间生产工艺流程图
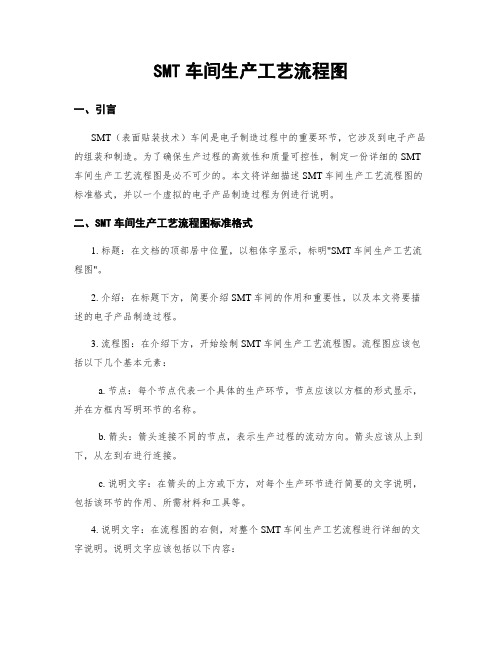
SMT车间生产工艺流程图一、引言SMT(表面贴装技术)车间是电子制造过程中的重要环节,它涉及到电子产品的组装和制造。
为了确保生产过程的高效性和质量可控性,制定一份详细的SMT 车间生产工艺流程图是必不可少的。
本文将详细描述SMT车间生产工艺流程图的标准格式,并以一个虚拟的电子产品制造过程为例进行说明。
二、SMT车间生产工艺流程图标准格式1. 标题:在文档的顶部居中位置,以粗体字显示,标明"SMT车间生产工艺流程图"。
2. 介绍:在标题下方,简要介绍SMT车间的作用和重要性,以及本文将要描述的电子产品制造过程。
3. 流程图:在介绍下方,开始绘制SMT车间生产工艺流程图。
流程图应该包括以下几个基本元素:a. 节点:每个节点代表一个具体的生产环节,节点应该以方框的形式显示,并在方框内写明环节的名称。
b. 箭头:箭头连接不同的节点,表示生产过程的流动方向。
箭头应该从上到下,从左到右进行连接。
c. 说明文字:在箭头的上方或下方,对每个生产环节进行简要的文字说明,包括该环节的作用、所需材料和工具等。
4. 说明文字:在流程图的右侧,对整个SMT车间生产工艺流程进行详细的文字说明。
说明文字应该包括以下内容:a. 车间布局:描述SMT车间的布局和设备摆放情况,包括生产线的位置和工作台的布置等。
b. 生产环节:逐个描述每个生产环节的具体操作步骤和注意事项,包括材料准备、设备调试和操作流程等。
c. 质量控制:说明每个生产环节中的质量控制点和检测方法,以确保产品质量的可控性。
d. 人员分工:描述每个生产环节中各个岗位的职责和工作内容,以及人员之间的协作关系。
e. 安全措施:列举在SMT车间生产过程中需要注意的安全事项和防护措施,以确保员工的人身安全。
三、示例:虚拟电子产品制造过程以下是一个虚拟的电子产品制造过程的SMT车间生产工艺流程图的标准格式示例:[图]说明文字:1. 车间布局:SMT车间由三条生产线组成,每条生产线包括设备摆放区、材料准备区和成品检测区。
SMT工艺制程详细流程图(更新版)

目 录
• SMT工艺简介 • SMT工艺流程 • SMT工艺材料 • SMT工艺设备 • SMT工艺质量与可靠性 • SMT工艺发展趋势与挑战
01 SMT工艺简介
SMT工艺定义
01
SMT工艺是一种表面组装技术,通 过将电子元件直接贴装在印刷电路 板(PCB)表面,实现电子产品的 组装和集成。
在选择贴片元件时,需要考虑 其电气性能、机械性能、可靠 性、成本等因素。
钢板
01
钢板在SMT工艺中起到支撑和定位电子元件的作用,是重要的 辅助材料之一。
02
钢板通常采用不锈钢或镀锌钢板制成,具有高强度、耐腐蚀、
不易变形等特点。
在选择钢板时,需要考虑其尺寸、精度、平整度、强度等因素,
03
以确保良好的支撑和定位效果。
图像处理系统用于处理和识别拍摄到的图像。
检测设备的精度和可靠性对于产品质量和生产效率有着至关重要的影响。
05 SMT工艺质量与可靠性
质量检测方法
视觉检测
通过高分辨率相机和图像处理技术, 对SMT制程中的元件放置、焊接质量 等进行实时检测。
自动光学检测(AOI)
利用光学原理对焊接后的PCB进行检 测,识别焊接缺陷、元件错位等问题。
02
SMT工艺涉及的设备包括贴片机 、印刷机、回流焊炉等,通过自 动化生产线完成电子元件的快速 、高密度组装。
SMT工艺特点
01
02
03
高密度组装
SMT工艺可以实现高密度、 小型化的电子元件组装, 提高电子产品的性能和可 靠性。
自动化程度高
SMT工艺采用自动化生产 线,提高了生产效率和产 品质量。
环保节能
SMT工艺使用的材料多为 无铅环保材料,有利于环 保和节能减排。
smt流程图

smt流程图SMT流程图。
SMT(Surface Mount Technology)是一种表面贴装技术,它是一种在电子元器件表面直接焊接到印刷电路板上的技术。
SMT流程图是用来描述SMT工艺流程的图表,下面将详细介绍SMT流程图的相关内容。
首先,SMT流程图的第一步是原材料准备。
在SMT生产过程中,需要准备各种原材料,包括电子元器件、PCB板、焊膏、清洁剂等。
这些原材料的质量和准备工作直接影响到整个SMT生产过程的质量和效率。
接下来,SMT流程图的第二步是PCB板的制作。
PCB板是SMT生产的基础,它需要经过设计、制版、印刷、固化等一系列工艺流程。
在这个阶段,需要严格控制PCB板的质量,确保其符合设计要求。
第三步是贴片。
在SMT流程图中,贴片是一个非常关键的环节。
在这个阶段,需要使用贴片机将各种电子元器件精准地贴片到PCB板上。
贴片的精准度和质量直接影响到整个产品的性能和可靠性。
紧接着是焊接。
焊接是SMT流程图中的另一个关键环节。
在这个阶段,需要使用回流炉将焊膏熔化,将电子元器件牢固地焊接到PCB板上。
焊接工艺的稳定性和可靠性对产品的质量和性能有着重要影响。
最后是清洗和检测。
在SMT生产过程中,清洗和检测是非常重要的环节。
清洗可以去除焊接过程中产生的残留物,确保产品的外观和性能;而检测则可以发现潜在的质量问题,保证产品的可靠性和稳定性。
总的来说,SMT流程图是SMT生产过程中的重要参考,它可以帮助生产人员清晰地了解整个生产过程,确保每个环节都能够得到严格控制和管理。
只有在严格按照SMT流程图的要求进行生产,才能生产出高质量、高可靠性的SMT产品。
SMT车间作业流程图及工艺

SMT车间作业流程图及工艺
SMT生产工艺Check List
验证内容:SMT 其它
拟制:审核:批准:
一、过程关键工序控制:
①合格率=合格数÷投入总数以该工序实际生产的数量填写,无该工序时不填写。
二、IPQC检验合格率
①合格率=合格数÷检查数
三、可生产性及改善建议
四、生产结论
□生产正常,不需作任何更改。
□不可以正常生产,必须重新改进后再生产。
拟制:审核:批准:
精品文档精心整理
附3 废水、噪声、粉尘、固体废弃物处理工艺流程图1、废水处理
2、噪声处理
3、粉尘处理
4固体废弃物处理
精品文档可编辑的精品文档。
(完整版)LEDsmt生产工艺流程图

1.物料领用(按换 线通知单提前4小 时领好备用物料, 每盘物料上标示站 位,每次只领当天 所需数量,并对所 领用物料做好标 示); 2.根据物料规格正 确选用Feeder:装 料时注意注意不要 拉出太多物料,完 整填写上料记录 3.IPQC核对物按照 站位表进行核对, 2人同时进行确认, 节省核对时间。注 意四统一:料盘与 料盘、料盘与实物、 料盘与站位表、站 位表与站位 4.生产1枚首件板 予IPQC进行首件确 认(IPQC使用LCR 对电阻、电容进行 测量,对照机种晶 片图纸核对元件规 格、方向等);
1.后检针对回流焊 后PCB’A进行检查 确认(对照机种作 业指导书,对PCB 每个元件逐个确认 其规格、方向、贴 装精度等,并做好 记录及检查后不良 与良品的标示,盛 放在不良品架上, 严格区分良品与不 良品; 2.;对检查出不良 点连续出现时须及 时反馈到中检及操 机人员技术员做改 善并记录; 3、落实不良项目 的记录,班\组长 对不良记录每2H做 签名确认一次并反 馈到前段改善;
号、尺寸。
2.填写产品外箱标 签时注意标签所填
规格、色温等要于
内部实物相符,对
确认OK品进行封口
并盖PASS章; 3.必须保持工作台 面的清洁与整齐, 严格按照5S规定放 入成品区,托运过 程中按规定路线行 走,装车不能超过 规定1.5米高度
1.中检人员对贴装 后PCB’A进行检查 确认无偏移、漏打、 反向等不良后方可 投入下一工序 2.取拿PCB’A时应 拿取板边无元件位 置,以免抹到元件。 同一位置发生3个 以上不良时,须立 即反馈工程调整机 器 3.对连续出现的不 良须及时反馈到操 作人员及印刷人员 做调试 4.对缺件的完成品 统一由修理对照 BOM修理,并由品 管人员确认;
SMT生产流程与制程简介

Solder Paste Inspection
Pick& Place
Reflow Soldering
AOI Inspection
X-Ray Inspection
ICT Test
DEK Infinity API
➢Screen Print Solder Paste ➢Maximum Size 510 x 508 mm /(610 x 508mm*) ➢Minimum Size 40 x 50 mm ➢Thickness range 0.2 – 6 mm ➢Underside component clearance 3- 42 mm ➢Alignment: Stencil to Board Repeatability 1.6 Cpk @+/- 25μm ➢Product Changeover: 2 minutes ➢New Product Setup: < 10 minutes ➢Support 2D(Coverage) Inspection
➢In Circuit tester;ICT ➢Short、Open and Power Test ➢Low MDA Entry Price ➢Conduct function test with Advanced PXI Module Architecture ➢Optional Digital Components Test ➢Optional On Board programming and Boundary Scan Test ➢Two Stage Fixtures Available
4
Bare Board
Solder Printing
2nd Side SMT
Pick & place
SMT印刷工序作业流程图
SMT印刷工序作业流程图流程图作业内容1、熟悉工艺指导书及生产注意事项参照《锡膏印刷作业指导书》,里面有一些产品的特殊要求。
2、准备PCB、辅料、工具2.1、工具准备:搅拌刀、酒精瓶、擦拭纸、顶针、印刷治具、气枪、放大镜(针对一些特殊产品)2.2、锡膏、红胶准备根据产品要求选择无铅锡膏、有铅锡膏、红胶。
千住锡膏(M705-GRN360-K2)在室温下进行回温2小时。
车间温度:18~26℃,车间湿度40-70%。
已回温未开封的焊膏不得放置超过24小时,超过24小时应重新放回冰箱,下次先领用;同一瓶焊膏的回温次数≤2次。
乐泰锡膏(CR37)在室温下进行回温4小时。
车间温度:18~26℃,车间湿度40-70%。
已回温未开封的焊膏不得放置超过24小时,超过24小时应重新放回冰箱,下次先领用;同一瓶焊膏的回温次数≤2次。
贴片胶使用前,应先从冷藏柜中取出,放置在阴凉处(不要放在冰柜顶部)回温,ESGS.W880、富士NE3000S回温时间3-4小时。
回温时不应打开封口,贴片胶只允许回温一次. 锡膏搅拌时间3分钟。
2.3、准备PCB板2.3.1、确认PCB型号/周期/数量/版本号/包装状态(OSP必须是真空袋包装)。
2.3.2、确认领取时是否有不同版本的PCB,如果有必须确认清楚。
2.4、刮刀准备2. 4.1、每次生产前必须先检查刮刀的平整度、变形、磨损情况,若不良现象存在于印刷区域中,致使无法印刷出品品质合格的图形,该刮刀必须报废处理;若不影响印刷效果或不良情况未在印刷区域中,则需请技术部确认后方可使用。
2. 4.2、上述情况必须完全记录在《SMT制程记录表》上。
2.5、准备钢网2.5.1、检查钢网版本/状态/是否与PCB相符。
2.5.2、每次使用前必须先检查钢网的平整度、变形、磨损、钢网绷网、张力,若不良现象存在于需印刷的图形之上致使无法印刷出合格的图形,该钢网必须报废处理;2.5.3、若不影响印刷效果或不良情况未在印刷图形之上,则需请技术部确认后,才能使用;针对绷网胶水开裂致使钢网松弛现象,则需请技术部进行绷网处理之后,测试张力大于30N/cm,方可使用。
标准SMT工艺流程图
13
Paste Handling BEFORE Printing/丝印之前的锡浆处理 丝印之前的锡浆处理
15 April 2012
Allow approximately 4 hours for paste to reach room temperature (~25 deg C) 可以用将近4小时令锡浆温度达到室温(~25摄氏度) Avoid rapid warming 避免迅速升温 DO NOT apply heat to expedite thawing 不要用加热的方法来加速熔化。 Label jar with open date and time 在广口瓶上用标签标上开封日期和时间。
Powder Size
TYPE/+325 -325/+500 -400/+635 -500/+635 -635
Printing Parameters Pitch Aperture width (Avg.) # small inches microns inches microns spheres 0.050 1270 0.023 584.2 7.8 0.025 635 0.0125 317.5 7.1 0.020 508 0.0095 241.3 9.7 0.016 406.4 0.0075 190.5 9.5 0.012 304.8 0.0055 139.7 7.0 0.008 203.2 0.004 101.6 ?
Powder Diameter microns 75 150 45 75 25 45 20 38 20 25 fines 20
11
Which Powder Mesh Should Be Used?/应该使用哪一种粉末的网孔? 应该使用哪一种粉末的网孔? 应该使用哪一种粉末的网孔
SMT车间生产工艺流程图
SMT车间生产工艺流程图一、引言SMT(表面贴装技术)是一种电子元器件贴装技术,广泛应用于电子制造行业。
本文将详细介绍SMT车间的生产工艺流程图,包括各个环节的具体步骤和所需设备。
二、SMT车间生产工艺流程图以下是SMT车间生产工艺流程图的详细步骤:1. 元器件采购首先,SMT车间需要进行元器件的采购。
这包括与供应商的沟通、选择合适的元器件、进行价格谈判等环节。
采购部门需要根据生产计划和需求,及时采购所需的元器件,并确保元器件的质量和供货时间。
2. 元器件存储和管理采购到的元器件需要进行存储和管理。
SMT车间应设立专门的仓库,对元器件进行分类、编号和标记,以便于后续的使用和管理。
同时,需要定期进行库存盘点,确保元器件的数量和质量。
3. PCB制板SMT车间需要进行PCB(印刷电路板)的制板工作。
这包括设计电路图、制作PCB板、进行电路板的化学处理等步骤。
制板部门需要根据产品的要求和设计图纸,进行精确的制板工作。
4. 贴片接下来是SMT车间的核心工艺环节——贴片。
贴片机是SMT车间的主要设备之一,用于将元器件精确地贴装到PCB板上。
在贴片过程中,需要根据元器件的封装类型、规格和位置,设置贴片机的参数,并确保贴装的准确性和稳定性。
5. 焊接贴片完成后,需要进行焊接工艺。
SMT车间通常采用热风炉或回流焊炉进行焊接。
焊接工艺需要控制温度、焊接时间和焊接剂的使用,以确保焊接质量和可靠性。
6. 检测和测试焊接完成后,需要对贴装完成的产品进行检测和测试。
这包括外观检查、功能测试、性能测试等环节。
SMT车间需要配备相应的检测设备和测试仪器,对产品进行全面的检测和测试,确保产品的质量和性能符合要求。
7. 清洁和包装最后,SMT车间需要对产品进行清洁和包装。
清洁工艺包括去除焊接剂残留、清洗PCB板等步骤。
包装工艺包括产品的包装设计、包装材料的选择和包装方式的确定。
清洁和包装环节需要注意产品的防静电处理和防潮措施,以保证产品的完整性和质量。
SMT详细流程图(更新版)
03
返修工具具有操作简便、灵活多变等特点,能够大大提高 返修效率和修复质量。
04 SMT材料
焊锡膏
焊锡膏是一种由焊剂和焊料组 成的混合物,用于将电子元件
焊接到PCB板上。
焊锡膏的成分和特性决定了 焊接的质量和可靠性,因此 选择合适的焊锡膏非常重要。
焊锡膏的粘度、触变性和润湿 性等特性需根据不同的工艺要
振动测试
模拟产品在实际使用过程 中可能受到的振动,以检 测产品的机械可靠性和稳 定性。
温度循环测试
模拟产品在不同温度环境 下工作,以检测产品的热 性能和耐温性能。
质量保证体系
ISO 9001质量管理体系
国际标准化组织制定的质量管理体系标准, 用于企业质量管理和持续改进。
QS9000质量管理体系
汽车行业质量管理体系标准,要求对产品从开发、 采购、生产到售后服务的全过程进行质量控制。
AOI检测设备
AOI检测设备是SMT生产流程中 的质量检测设备之一,主要负责 对印刷好锡膏或贴片胶的PCB板 进行自动光学检测,以发现和纠 正锡膏印刷、电子元件贴装和焊 接等工序中可能存在的缺陷和问 题。
AOI检测设备通常由传送系统、 检测系统和控制系统等组成,其 中检测系统的作用是通过高分辨 率相机和专用软件对PCB板进行 全方位扫描和图像处理,以发现 并定位缺陷和问题。
03 SMT设备与工具
印刷机
01
印刷机是SMT生产流程中的第一道工序设备,主要负责将预先印有电路的模板 (也称为钢网)上的锡膏或贴片胶均匀地涂抹在PCB板焊盘上,为后续的贴片 和焊接工序做好准备。
02
印刷机的性能和精度直接影响到锡膏的涂抹质量和后续工序的顺利进行。
03
印刷机通常由印刷板、刮刀、传动系统和控制系统等组成,其中刮刀的作用是 将锡膏或贴片胶从模板上刮平并均匀涂抹在PCB板上。
- 1、下载文档前请自行甄别文档内容的完整性,平台不提供额外的编辑、内容补充、找答案等附加服务。
- 2、"仅部分预览"的文档,不可在线预览部分如存在完整性等问题,可反馈申请退款(可完整预览的文档不适用该条件!)。
- 3、如文档侵犯您的权益,请联系客服反馈,我们会尽快为您处理(人工客服工作时间:9:00-18:30)。
按要求焊接物料并清洗
过回流炉固化
过回流炉固化
清洗焊接后的残留物
IPQC检验(品质部)
13
SMT换料流程
SMT部
巡查机器用料情况 提前准备需要更换的物料 机器出现缺料预警信号 操作员根据机器显示缺料状况进行备料 机器停止后,操作员取出缺料Feeder
N
品质部
对原物料、备装物料、上料卡进行三方核对
IPQC核对物料(料 号/规格/厂商/周期) 并测量记录实测 值
列。 在采用波峰焊接时,应尽力保证使片状元件的两端焊点同时接触焊料波峰。
后面电极焊 接可能不良
正确
不正确
波峰焊时PCB运行方向
25
PCB在SMT设计中工艺通常原则
4.2、元器件的布局 对尺寸相差较大的片状元件相邻排列,且间隔很小时,较小元件应排列在线板过波峰 /回流时流向的前面; 当元件交错排列时,它们之间的应留出一定的间隔; 对拼板PCB元件靠近切割槽侧的元件在分离时易损伤。
部门领导审核物料试用跟踪单
机芯及试用跟踪单发放并交接
18
SMT清机流程
提前清点线板数 N
物料清点 Y 配套下机
物料申请/领料
已发出机芯清点
不良品清点
坏机返修
N
丝印位、操作员、炉后QC核对生产数 Y 手贴机器抛料,空贴机芯标识、区分
QC开欠料单补料
QC对料,操作 员拆料、转机
19
SMT在生产上对PCB的要求
将程序导入软盘
导入生产线
在线调试程序
5
SMT转机工作准备流程
按PMC计划或接上级转机通知
熟悉工艺指导卡及生产注意事项
生产资料、物料、辅料、工具准备
资料准备
钢网准 备 检查钢 网版本/ 状态/是 否与PCB 相符
刮刀准 备
PCB板
领物料
锡膏、红胶 准备
料架准 备
转机工 具准备
程序/排列表 /BOM/位置图 检查是否正 确、有效
将实测值记录至首件测量记录表
检查元件实物或通知技术员调整
判断测量值是否符合规格要求 Y
更换物料或调试后再次确认 N
将已测量元件贴回原焊盘位置 重复测量所有可测元件 N
将首件测量记录表交QC组长审核 Y
将机芯标识并归还生产线
10
SMT炉温设定及测试流程
SMT部
根据工艺进行炉温参数设置
工程部
炉温实际值测量 N N N
品质部 IPQC在线工艺监督、物料/首件确认 IQC来料异常跟踪处理
SMT部
PCB外观检查 Y PCB安装检查 网印效果检查 N N 校正/调试 清洗PCB N 退仓或做废处理
OQC外观、 功能抽检 Y 贴PASS贴或签名 N
Y 炉前贴片效果检查 设置正确回流参数并测试
填写返工通知单 炉后QC外观检查 Y X-Ray对BGA检查(暂无) 分板、后焊、外观检查
确认PCB 型号/周 期/数量
物料分 机/站位
解冻
搅拌
清机前点数
清机前对料
转机开始
6
SMT转机流程
接到转机通知 熟悉工艺指导卡及注意事项
领钢网
领PCB
领物料及分区
领辅助材料
准备料架
准备工具
更换资料
传程序
炉前清机
网印调试
调轨道
拆料
上料
更换吸嘴
对料
元件调试
炉温调整
炉温测试
对样机
首件确认
正常生产
7
SMT转机物料核对流程
23
PCB在SMT设计中工艺通常原则
3、导通孔及导线的处置 为防止大面积铜导体的热效应而影响焊接质量,表面安装焊盘与导线的连接部宽度不 宜大于0.3mm
不好
较好
24
PCB在SMT设计中工艺通常原则
4.1、元器件的布局 在SMT中,元器件在SMB上的排向应使同类元器件尽可能按相同的方向排
炉前检查作业指导书
外观检查作业指导书
印锡作业指导书
上料作业指导书
点胶作业指导书
贴片作业指导书
补件作业指导书
后焊作业指导书
测试作业指导书
包装作业指导书
Y
备份保存 审核者签名
按已审核上料卡备料、上料
熟悉各作业指导书要求
熟悉各作业指导书要求
严格按作业指导书实施执行
监督生产线按作业指导书执行
3
SMT品质控制流程
B=50~330mm
A=50~250mm E>5mm
D<8mm
G< 0.5mm E>5mm
F<1.2mm
C>5mm
20
SMT生产上对PCB的要求
2.识别点(Mark)的要求: A. Mark的形状:标准圆形、正方形、三角形; B. Mark的大小;0.8~1.5mm; C. Mark的材质:镀金、镀锡、铜铂; D. Mark的表面要求:表面平整、光滑、无氧化、无污物; E. Mark的周围要求:周围1mm内不能有绿油或其它障碍物,与Mark颜色有明显差异; F. Mark的位置:距离板边5mm以上,周围5mm内不能有类似Mark的过孔、测试点等; G.为避免生产时进板方向错误,PCB左右两边Mark与板缘的位置差别应在10mm以上。
17
SMT物料试用流程
PMC/品质部/工程部
提供试用物料通知
SMT部
明确物料试用机型
下达试用物料跟踪单 发放试用物料
领试用物料及物料试用跟踪单
试用物料及试用单发放至生产线
生产线区分并试用物料 Y 技术员跟踪试用料贴装情况 N N 停止试用
IPQC跟踪试用料品质情况 Y 填写物料试用跟踪单
通知相关部门
21
PCB在SMT设计中工艺通常原则
1、特殊焊盘的设计规则 MELF柱状元器件:为防止回流焊接时元器滚动,焊盘上须开一个缺口
D E A C hSOP、QFP K=1.2
B hPLCC
主焊面
22
PCB在SMT设计中工艺通常原则
2、导通孔及导线的处置 为避免焊锡的流走,导通孔应距表面安装焊盘0.65以上。在片状元件下面不应设置导 通孔。
N N 外观、功能修理
SMT出货
SMT返工
N 功能测试 机芯包装
4
SMT生产程序制作流程
研发/工程/PMC部
提供PCB文件 提供PCB
SMT部
导出丝印图、坐标,打印BOM
品质部
制作或更改程序
N
IPQC审核程 序与BOM一 致性
提供BOM NC 程序 排列 程序 基板 程序
Y
打印相关程序文件
审核者签名
炉温测试初步判定 Y 技术员审核签名 Y 产品过炉固化 Y 跟踪固化效果 Y N PE确认炉温并签 名 Y 正常生产
11
SMT炉前质量控制流程
元件贴装完毕 N 确认PCB型号/版本 Y N 检查锡膏/胶水量及精准度
N 检查极性元件方向 N 检查元件偏移程度 通知技术员确认 N 对照样机检查有无少件、多件、错件竖 件、反件、侧立等不良 Y 记录检查报表
Y
换料登记(换料时间/料号/规格/数量/生产数 /实物保存),签名(操作员/生产QC/IPQC)
对缺料站位进行装料
检查料架是否装置合格
各项检查合格后进行正常生产
跟踪实物贴装效果并对样板
14
SMT换料核对流程
品质部 SMT部
操作员根据上料卡换料 Y IPQC核对物料并 测量实际值
生产线QC核对物料正确性
1.PCB大小及变形量: A. PCB宽度(含板边) :50~250mm; B. PCB长度(含板边) :50~330mm; C. 板边宽度:>5mm; D. 拼板间距:<8mm; E. PAD与板缘距离:>5mm; F. 向上弯曲程度:<1.2mm; G. 向下弯曲程度:<0.5mm; H. PCB扭曲度:最大变形高度÷对角长度<0.25
>2.5mm 可能被遮蔽
26
SMT部
生产线转机前按上料卡分机台、站位
品质部
转机时按已审核排列表上料
Y
产线QC与操作员 核对物料正确性
N 查证是否有代用料 N
N IPQC复核生产线上料正确性 物料确认或更换正确物料 Y
产线QC与操作员确认签名
IPQC签名确认
开始首件生产
8
SMT首件样机确认流程
工程部 品质部 SMT部
提供工程样机 N PE确认 Y
生产调试合格首部机芯
核对工程样机 Y 元件贴装效果确认 N IPQC元件实物 测量 Y N 通知技术员调试
OQC对焊接质量进行复检
Y
N 回流焊接或固化并确认质量
填写样机卡并签名
对照样机进行生产、检查调试已贴元件合格机芯 N 通知技术员调整 检查所有极性元件方向 Y 参照丝印图从机芯上取下元件 将仪表调至合适档位进行测量
N
焊接效果检查 Y 后焊(红胶工艺先进行波 峰焊接) 后焊效果检查 Y
N
向上级反馈改善
交修理维修
N
向上级反馈改善
N 功能测试 Y 成品机芯包装送检 交修理员进行修理
2
SMT工艺控制流程
SMT部 品质部 工程部
按工艺要求制作《作业指导书》
N
对照生产制令,按研发部门 提供的BOM、PCB文件制作或 更改生产程序、上料卡 对BOM、生 产程序、上 料卡进行三 方审核
N
详细填写换料记录
通知生产线立即暂停生产
追踪所有错料机芯并隔离、标识
记录实测值并签名
生产线重新换上合格物料
继续生产
对错料机芯进行更换
标识、跟踪
15
SMT机芯测试流程
工程部