球墨铸铁退火工艺规范(精)
球墨铸铁正火工艺规范(精)

球墨铸铁正火工艺规范
规范金相组织备注
织均匀性,改善可加工性,提高强度、硬度、耐磨性或口及游离渗碳体珠光体+少量铁素体(牛眼状)
复杂铸件
珠光体+少量铁素体(牛眼状)复杂铸件正火后需要回火
高的综合力学性能,特别是塑性和韧性珠光体+(碎块状或条块状)铁素体+球状石墨
复杂铸件
珠光体+(碎块状或条块状)铁
素体+球状石墨
复杂铸件正火后需要回火
珠光体+(碎块状或条块状)铁素体+球状石墨
铸态如存过量自由渗碳体时,在正火前需经高温石墨化退火 复杂铸件正火后需要回火。
铸造厂退火炉操作规程
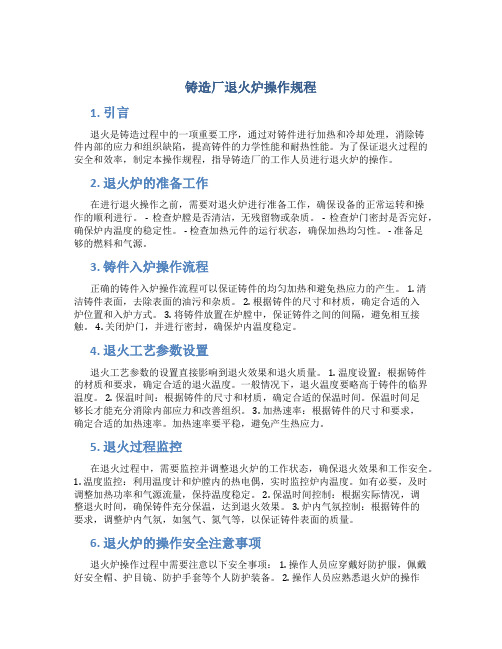
铸造厂退火炉操作规程1. 引言退火是铸造过程中的一项重要工序,通过对铸件进行加热和冷却处理,消除铸件内部的应力和组织缺陷,提高铸件的力学性能和耐热性能。
为了保证退火过程的安全和效率,制定本操作规程,指导铸造厂的工作人员进行退火炉的操作。
2. 退火炉的准备工作在进行退火操作之前,需要对退火炉进行准备工作,确保设备的正常运转和操作的顺利进行。
- 检查炉膛是否清洁,无残留物或杂质。
- 检查炉门密封是否完好,确保炉内温度的稳定性。
- 检查加热元件的运行状态,确保加热均匀性。
- 准备足够的燃料和气源。
3. 铸件入炉操作流程正确的铸件入炉操作流程可以保证铸件的均匀加热和避免热应力的产生。
1. 清洁铸件表面,去除表面的油污和杂质。
2. 根据铸件的尺寸和材质,确定合适的入炉位置和入炉方式。
3. 将铸件放置在炉膛中,保证铸件之间的间隔,避免相互接触。
4. 关闭炉门,并进行密封,确保炉内温度稳定。
4. 退火工艺参数设置退火工艺参数的设置直接影响到退火效果和退火质量。
1. 温度设置:根据铸件的材质和要求,确定合适的退火温度。
一般情况下,退火温度要略高于铸件的临界温度。
2. 保温时间:根据铸件的尺寸和材质,确定合适的保温时间。
保温时间足够长才能充分消除内部应力和改善组织。
3. 加热速率:根据铸件的尺寸和要求,确定合适的加热速率。
加热速率要平稳,避免产生热应力。
5. 退火过程监控在退火过程中,需要监控并调整退火炉的工作状态,确保退火效果和工作安全。
1. 温度监控:利用温度计和炉膛内的热电偶,实时监控炉内温度。
如有必要,及时调整加热功率和气源流量,保持温度稳定。
2. 保温时间控制:根据实际情况,调整退火时间,确保铸件充分保温,达到退火效果。
3. 炉内气氛控制:根据铸件的要求,调整炉内气氛,如氢气、氮气等,以保证铸件表面的质量。
6. 退火炉的操作安全注意事项退火炉操作过程中需要注意以下安全事项: 1. 操作人员应穿戴好防护服,佩戴好安全帽、护目镜、防护手套等个人防护装备。
灰铁、球铁热处理工艺指导书

铸件热处理工艺指导书1.灰铸铁的退火、正火热处理工艺1.1消除内应力退火(人工时效)工艺灰铸铁消除内应力退火(人工时效)热处理工艺适用范围1.较薄、故冷却速度较快的灰铁件;2.形状复杂、截面变化较大的铸件;3。
需进行机加工的大型铸件;4。
经过少量焊修,因而局部积累些许焊应力的铸件.*加热温度越高,应力消除越快。
但温度过高,则易发生石墨化与珠光体球化而使性能降低,尤其是含Si 量较高时;*保温时间一般按炉内铸件平均壁厚的5min/mm计算。
形状复杂的铸件,要以75~100℃/h的速率缓慢加热;*保温时间终了,以30~50℃/h的速率在炉内缓冷,冷却至150~200℃出炉冷却(空冷).1.2软化退火和正火工艺灰铸铁软化退火和正火热处理工艺适用范围*保温时间一般按炉内铸件平均壁厚的5min/mm计算。
形状复杂的铸件,要以75~100℃/h的速率缓慢加热.2.球墨铸铁的退火、正火(+回火)和调质热处理工艺2.1 高温退火当铸态组织为铁素体+珠光体+渗碳体+石墨时,必须采用高温退火工艺:适用范围1。
获得铁素体球墨铸铁;2.分解渗碳体和珠光体,提高机械性能;3.改善加工性能,使工件容易加工且不易变形。
*退火温度越高,渗碳体组织分解速度越快,白口现象越易消除.但温度过高将使铸件机械性能反而变坏,发生变形和表面氧化失碳,故须严格控制温度上限。
* 保温时间也可按炉内铸件每15mm的有效厚度、需要保温1~2h计算,铸件白口深度大、渗碳体组织成分多时,应适当增加保温时间。
*形状复杂的铸件,要以75~100℃/h的速率缓慢加热。
保温终了,以60~80℃/h的速率在炉内缓冷,至600℃后出炉空冷。
2.2 低温退火当铸态组织为铁素体+珠光体+石墨(没有渗碳体)时,只需采用低温退火工艺:球墨铸铁低温退火热处理工艺适用范围1。
获得铁素体球墨铸铁;2。
分解渗碳体和珠光体,提高机性能;3。
改善加工性能。
* 保温时间也可按炉内铸件每15mm的有效厚度、需要保温1~2h计算;*形状复杂的铸件,要以75~100℃/h的速率缓慢加热。
退火热处理规范
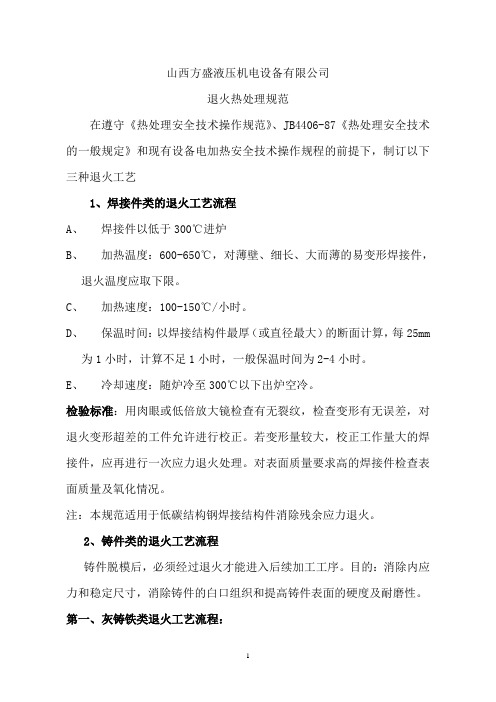
山西方盛液压机电设备有限公司退火热处理规范在遵守《热处理安全技术操作规范》、JB4406-87《热处理安全技术的一般规定》和现有设备电加热安全技术操作规程的前提下,制订以下三种退火工艺1、焊接件类的退火工艺流程A、焊接件以低于300℃进炉B、加热温度:600-650℃,对薄壁、细长、大而薄的易变形焊接件,退火温度应取下限。
C、加热速度:100-150℃/小时。
D、保温时间:以焊接结构件最厚(或直径最大)的断面计算,每25mm为1小时,计算不足1小时,一般保温时间为2-4小时。
E、冷却速度:随炉冷至300℃以下出炉空冷。
检验标准:用肉眼或低倍放大镜检查有无裂纹,检查变形有无误差,对退火变形超差的工件允许进行校正。
若变形量较大,校正工作量大的焊接件,应再进行一次应力退火处理。
对表面质量要求高的焊接件检查表面质量及氧化情况。
注:本规范适用于低碳结构钢焊接结构件消除残余应力退火。
2、铸件类的退火工艺流程铸件脱模后,必须经过退火才能进入后续加工工序。
目的:消除内应力和稳定尺寸,消除铸件的白口组织和提高铸件表面的硬度及耐磨性。
第一、灰铸铁类退火工艺流程:A、去应力退火:将铸件缓慢加热到500-560℃,保温2小时左右,然后以极缓慢的速度随炉冷至150-200℃后出炉。
注意:退火温度过高或保温时间过长,会引起石墨化,降低铸件强度和硬度,这是不适宜的。
B、消除白口、改善切削加工性的退火工艺:将铸件加热到800-900℃,保温2-5小时,使共晶渗碳体发生分解,然后又在随炉缓慢冷却过程中,使二次渗碳体及共析渗碳体发生分解,待随炉缓冷到500-400℃时,再出炉空冷,这样可以改善切削加工性。
若保温后采用较快的冷却速度,可以增加铸件强度和耐磨性。
第二、球墨铸铁类退火工艺流程:A、去应力退火:球墨铸铁的弹性模量以及凝固时收缩率比灰铸铁高,故铸造内应力比灰铸铁约大2倍。
对于不再进行其他热处理的球墨铸铁铸件,都应进行去应力退火。
离心球墨铸铁管的组织及退火工艺研究

离心球墨铸铁管的组织及退火工艺研究王玉峰1,刘宗昌1,朱文方2,陈龙2(1.包头钢铁学院材料系,包头014010;2.抚顺特殊钢有限责任公司,抚顺113001)摘要:从大型离心球墨铸铁管上取样,用光学金相、电子金相法研究了铸造和不同退火状态下的离心球墨铸铁的组织,实行了低温退火新工艺。
研究表明,采用低温退火,使片状珠光体转变为粒状珠光体,并且控制粒状珠光体量为15%!25%,其余为铁素体+石墨,具有良好的综合力学性能。
关键词:球墨铸铁;离心铸管;珠光体;石墨中图分类号:TG143.5文献标识码:A文章编号:0254-6051(2002)10-0038-04M icrostruct ure and M echanical pro p erties of l ar g e d ia m eterC entrif u g al C asti n g ductile iron p i p e and its Anneali n g processW ANG Y u-f en g1,L I U Zon g-chan g1,ZHU W en-f an g2,CHENG L on g2(1.D e p art m ent o f M aterial s cience and En g i neeri n g,B ao tou U n ivers it y o f Iron and s tee l t echno lo gy,B ao tou N e i m en gg u014010,Ch i na;2.Fushun s p ecial s tee l C o.,L td.,Fushun L iaon i n g113001,Ch i na)分,那些没有逸出的游离的氢就会以原子态和分子态的形式残留在渗碳层内而对钢产生有害影响。
对于渗层浅的小工件,渗碳时间短,渗碳层内总的氢含量较少,再加上渗碳装炉时工件紧密排放使得出炉后降温速度缓慢,渗层内游离氢会在降温过程中较完全地扩散出工件表面。
球墨铸铁的淬火退火回火正火热处理分析
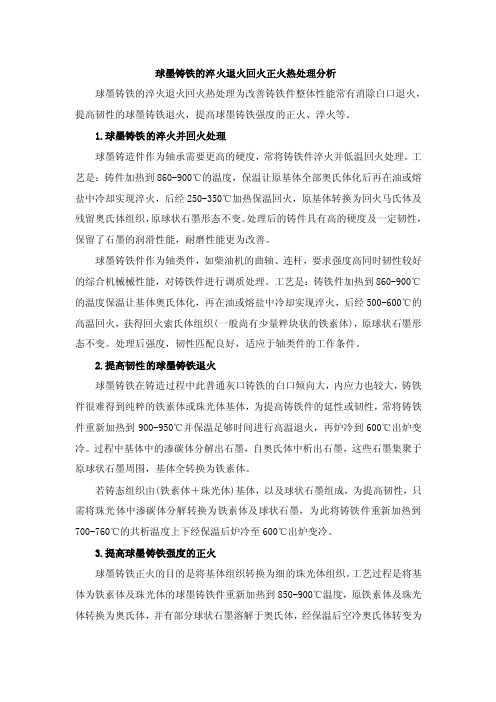
球墨铸铁的淬火退火回火正火热处理分析球墨铸铁的淬火退火回火热处理为改善铸铁件整体性能常有消除白口退火,提高韧性的球墨铸铁退火,提高球墨铸铁强度的正火、淬火等。
1.球墨铸铁的淬火并回火处理球墨铸造件作为轴承需要更高的硬度,常将铸铁件淬火并低温回火处理。
工艺是:铸件加热到860-900℃的温度,保温让原基体全部奥氏体化后再在油或熔盐中冷却实现淬火,后经250-350℃加热保温回火,原基体转换为回火马氏体及残留奥氏体组织,原球状石墨形态不变。
处理后的铸件具有高的硬度及一定韧性,保留了石墨的润滑性能,耐磨性能更为改善。
球墨铸铁件作为轴类件,如柴油机的曲轴、连杆,要求强度高同时韧性较好的综合机械械性能,对铸铁件进行调质处理。
工艺是:铸铁件加热到860-900℃的温度保温让基体奥氏体化,再在油或熔盐中冷却实现淬火,后经500-600℃的高温回火,获得回火索氏体组织(一般尚有少量粹块状的铁素体),原球状石墨形态不变。
处理后强度,韧性匹配良好,适应于轴类件的工作条件。
2.提高韧性的球墨铸铁退火球墨铸铁在铸造过程中此普通灰口铸铁的白口倾向大,内应力也较大,铸铁件很难得到纯粹的铁素体或珠光体基体,为提高铸铁件的延性或韧性,常将铸铁件重新加热到900-950℃并保温足够时间进行高温退火,再炉冷到600℃出炉变冷。
过程中基体中的渗碳体分解出石墨,自奥氏体中析出石墨,这些石墨集聚于原球状石墨周围,基体全转换为铁素体。
若铸态组织由(铁素体+珠光体)基体,以及球状石墨组成,为提高韧性,只需将珠光体中渗碳体分解转换为铁素体及球状石墨,为此将铸铁件重新加热到700-760℃的共析温度上下经保温后炉冷至600℃出炉变冷。
3.提高球墨铸铁强度的正火球墨铸铁正火的目的是将基体组织转换为细的珠光体组织。
工艺过程是将基体为铁素体及珠光体的球墨铸铁件重新加热到850-900℃温度,原铁素体及珠光体转换为奥氏体,并有部分球状石墨溶解于奥氏体,经保温后空冷奥氏体转变为细珠光体,因此球墨铸件的强度提高。
球墨铸铁淬火工艺规范(精)
球墨铸铁淬火工艺规范
热处理规范金相组织备注
回火索氏体+少量铁素体及球状石墨淬火
以前最好先经正火当铸件中存在过量
自由渗碳体时,在淬火前必须进行高温
石墨化退火,以免析出二次网状渗碳
体,这种方式叫“二阶段淬火”。
考虑
到回火脆性,应尽量避免250~300℃范围
内淬火
石墨
石墨
表面层为细针状马氏体+少量残留奥氏体及球状石墨,过渡层为小岛状马氏体+细小铁素体,内部与原始组织相同对铁素体基体的球铁,必须先进行正火,使珠光体量≥70%,有时为了消除淬火应力而在380~410℃温度范围内回火处理
提高强度、硬度和耐磨性,减少淬火变形及裂纹。
它是发挥球铁材料最大潜力的热处理方法下贝氏体+少量马氏体+少量残留奥氏体+
球状石墨
铸态组织需无游离渗碳
石墨化退火。
等温淬火
获得良好的强度和韧性下贝氏体+碎片状铁素体铸态组织需无游离渗碳石墨化退火。
等温淬火。
铸铁件去应力退火工艺规范
铸铁件去应力退火工艺规范
1 目的
为规范铸铁件去应力退火工艺,特制定本规范。
2 适用范围
本规范适用于普通灰铸铁、合金铸铁和球墨铸铁件去应力(包括铸造应力、焊后应力和粗加工应力)退火。
3 基本要求
3.1 铸铁件去应力退火升温速度、冷却速度要慢,保温时间要长,出炉温度要低。
3.2 铸铁件去应力退火工序应由经考试合格取得上岗证的热处理工担任。
4 去应力退火工艺规程
铸铁件去应力退火工艺规程见表1。
表1铸铁件去应力退火工艺规程
5
5.1 铸铁件的升温速度应根据铸件结构的复杂性来决定,形状简单的铸件采用80~100℃/h的升温速度,形状复杂的(易裂的)铸件采用小于60~80℃/h 的升温速度。
5.2 保温时间应根据同炉铸件中的最大壁厚值来决定。
最大壁厚小于25mm 时,保温时间要求不小于4h。
壁厚每增厚25mm,保温时间则在4h基础上增加1h。
装炉量多时,可适当延长保温时间。
5.3 铸铁件去应力退火均采用炉冷,形状复杂的铸件采用小于30~40℃/h冷。
球墨铸铁的退火热处理工艺
球墨铸铁的退火热处理工艺球墨铸铁退火热处理工艺包括消除内应力退火、高温退火和低温退火三种。
球墨铸铁消除内应力退火一般是以75~100℃/h的速度加热到500~600℃,根据铸件壁厚可按每25mm保温1h来计算,而后空冷。
这种方法消除铸件90%~95%的应力,可提高铸件的塑性及韧性,但组织并没有发生明显改变。
高温退火是将铸件加热到900~950℃,保温1~4h,进行第一阶段石墨化,然后炉冷至720~780℃,保温2~8h,进行第二阶段石墨化。
如果在900~950℃保温后炉冷至600℃空冷,则由于第二阶段石墨化没有进行,将得到珠光体球墨铸铁。
由于用Mg处理的球墨铸铁形成白口的倾向较大,铸态组织中常出现莱氏体和自由渗碳体,因此使铸件脆性增大,硬度升高,切削性能恶化。
特别是当铸件厚薄不均匀时,薄壁处极易出现白口,使其变脆,不便加工。
为消除白口,获得高韧性的铁素体球墨铸铁,需进行高温石墨化退火,具体工艺如图a 所示,此时只完成了石墨化的第一阶段,得到的是珠光体为基体的。
球墨铸铁消除白口的高温退火工艺a)珠光体球墨铸铁退火工艺 b)铁素体球墨铸铁退火工艺若按如图b所示的工艺进行热处理,也就是在石墨化第一阶段完成后,进行第二阶段石墨化,根据此阶段保温时间长短可以得到不同的铁索体及珠光体的比例。
如果进行完全,可得到以铁素体为基体的球墨铸铁,这种铸铁具有高的韧性,伸长率可达到5%~25%,这种高韧性球墨铸铁多用于代替可锻铸铁和低碳钢制作零件。
低温退火是将铸件加热到720~760℃,保温3~6h,然后随炉缓冷至60℃出炉空冷,使珠光体中渗碳体发生石墨化分解。
当铸态球墨铸铁组织中只有铁素体、珠光体及球状石墨而无自由渗碳体时,为了获得高韧性的铁素体球墨铸铁,可采用低温退火。
延伸阅读可锻铸铁的组织介绍可锻铸铁是由白口铸铁经热处理得到的一种高强度铸铁,其石墨呈团絮状,削弱了石墨对基体的割裂作用和应力集中效应,因此可锻铸铁具有较高的强度,而且具有一定的塑性和韧性。
铸件退火安全操作规程
铸件退火安全操作规程铸件退火是指对铸件进行高温加热并冷却处理的工艺,目的是提高铸件的力学性能和物理性能。
在进行铸件退火处理时,操作人员必须遵守一系列安全操作规程,确保人身安全和工作环境的安全性。
以下是铸件退火的安全操作规程:1. 熟悉铸件:在进行铸件退火处理之前,操作人员必须熟悉铸件的材质、形状和尺寸以及退火的要求。
只有清楚了解铸件的特点,才能制定正确的操作方案。
2. 使用合适的工具和设备:在进行铸件退火处理时,操作人员必须使用合适的工具和设备。
这包括熔炉、温度控制设备、燃料等。
工具和设备必须经过检查和维护,确保其正常工作。
3. 穿戴个人防护装备:在进行铸件退火处理时,操作人员必须穿戴个人防护装备,包括热防护服、手套、护目镜等。
这些个人防护装备能有效保护操作人员免受高温和火焰的伤害。
4. 严格控制温度:在进行铸件退火处理时,操作人员必须严格控制退火的温度。
应按照工艺要求设定温度,并使用温度控制设备进行监控和调整。
同时,必须避免温度过高,以免引起事故。
5. 遵循操作规程:在进行铸件退火处理时,操作人员必须严格遵循退火的操作规程。
这包括放置铸件的位置、燃料的选择、加热时间和冷却过程等。
任何违反操作规程的行为都可能导致事故发生。
6. 防火防爆措施:在进行铸件退火处理时,必须采取防火防爆措施。
需要确保操作区域没有易燃易爆物品,并保持清洁整齐的工作环境。
同时,必须备有灭火器材,以防火灾事故的发生。
7. 定期检查设备:为了保障铸件退火处理的安全性,操作人员需要定期检查和维护设备和仪器。
如有发现问题,应及时进行修理或更换,确保设备和仪器的正常工作。
8. 加热过程中的安全措施:在进行铸件退火处理的加热过程中,操作人员必须时刻保持警惕。
应随时注意加热设备和工件的状态,确保火焰的稳定和温度的准确控制。
同时,必须避免烟雾和有害气体的产生,以免对操作人员造成伤害。
9. 冷却过程中的安全措施:在进行铸件退火处理的冷却过程中,操作人员必须遵循工艺要求进行操作。
- 1、下载文档前请自行甄别文档内容的完整性,平台不提供额外的编辑、内容补充、找答案等附加服务。
- 2、"仅部分预览"的文档,不可在线预览部分如存在完整性等问题,可反馈申请退款(可完整预览的文档不适用该条件!)。
- 3、如文档侵犯您的权益,请联系客服反馈,我们会尽快为您处理(人工客服工作时间:9:00-18:30)。
球墨铸铁退火工艺规范
热处理类型热处理目的热处理规范金相组织
备注
去应力低温退火消除或降低
残留应力,
并使其稳定
化
同铸铁原始
组织
球铁根据对工件的组织和性能的要
求,一般均经其它较复杂的热处理,
故不一定要进行此项去应力退火
高温石墨化退火消除自由渗
碳体并降低
硬度,改善
可加工性,
提高塑性和
韧性
1、2-铁素体
+石墨或铁
素体+珠光
体+石墨
3-珠光体+
石墨
1、2-铁素体基体规范3-珠光体基体
规范
低温石墨化退火使共析渗铁
体石墨化与
粒化,从而
降低硬度,
改善可加工
性并提高塑
性和韧性
1-铁素体+
珠光体+石
墨2、3-
铁素体+石
墨
1-铁素体-珠光体基体规范2、3-铁素
体基体规范。