中间轴式变速器设计
CA10TA190M双中间轴变速器的设计-开题报告

毕业设计(论文)开题报告(或9档)倍档组合式机械变速器。
增加倍档组合式变速器最大输入扭矩和最低档传动比的技术难点是副变速器低档齿轮的强度容量不足,超出齿轮轮齿的承载能力。
解决的办法是将由一个轮齿承受的载荷分流给几个轮齿来承担。
这样一来,输入齿轮扭矩不变,每个轮齿的负荷将等于同时接触齿数的平均数值。
倍档组合式变速器的副变速器功率分流方法有两种:一种是采用行星齿轮系的传动方法,这种结构非常紧凑,体积小而扭矩容量大,直到现在仍广泛应用;另一种功率分流的方法是采用双中间轴传动结构。
双中间轴传动最大工艺难点是保证主传动齿轮能和所啮合的双中间轴齿轮的轮齿同时接触问题,解决的办法是用浮动主传动齿轮的方法来消除齿轴对位的制造误差,确保轮齿同时接触,达到功率分流的目的。
与此相适应的换档同步器也有一定的浮动量。
图1 双中间轴倍档组合式变速器双中间轴倍档组合式变速器具有如下优点:1)由于一轴和二轴上各档齿轮同时与两根中间轴上对应的齿轮相啮合,功率分流,从理论上讲,每对齿轮上传递的扭矩为1/2,这就使每对齿轮传递的扭矩减少50%,使变速器的中心距、齿轮模数和宽度可以减小,从而减小变速器的质量和尺寸,特别是长度尺寸。
2)由于二轴从动齿轮在轴上处于径向浮动状态,两根中间轴的轴心线均匀分布在以二轴理论轴心为圆心、以中心距为半径的圆柱面上,所以二轴上各档齿轮及一轴齿轮在与两根中间轴上的对应齿轮相啮合产生的径向力达到平衡,即互相抵消。
二轴不承受径向力,只传递扭矩,这样二轴可以设计得细一些,结构可以简单一些,其后轴承可以选择较小的规格,这也有助于减小变速器的质量和尺寸。
3)由于二轴齿轮的径向浮动和二轴的铰接式浮动的结果,使得齿轮在啮合时能自动抵消一部分制造和装配误差,啮合质量优于单中间轴。
啮合区容易达到设计要求,实际使用情况也证实了这点。
这就有利于降低啮合噪声和提高耐用度。
4)由于双中间轴倍档组合式变速器可以明显地减小变速器的质量和轴向尺寸,利用这种优点,可提高变速器的最大传递功率和扭矩,扩大使用范围。
中间轴变速器工作原理
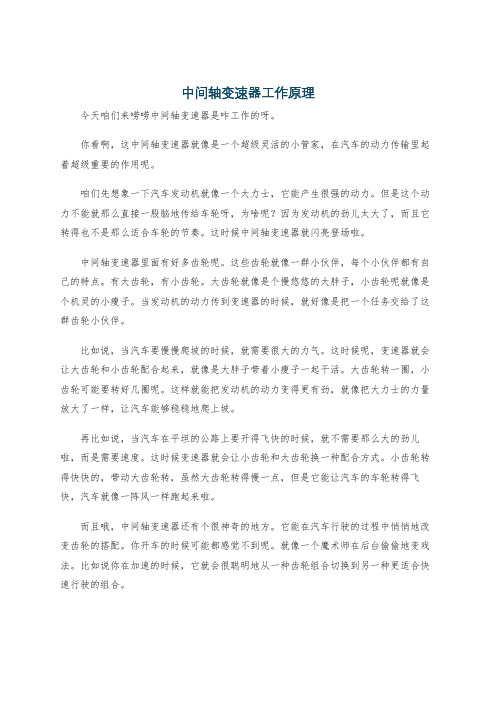
中间轴变速器工作原理今天咱们来唠唠中间轴变速器是咋工作的呀。
你看啊,这中间轴变速器就像是一个超级灵活的小管家,在汽车的动力传输里起着超级重要的作用呢。
咱们先想象一下汽车发动机就像一个大力士,它能产生很强的动力。
但是这个动力不能就那么直接一股脑地传给车轮呀,为啥呢?因为发动机的劲儿太大了,而且它转得也不是那么适合车轮的节奏。
这时候中间轴变速器就闪亮登场啦。
中间轴变速器里面有好多齿轮呢。
这些齿轮就像一群小伙伴,每个小伙伴都有自己的特点。
有大齿轮,有小齿轮。
大齿轮就像是个慢悠悠的大胖子,小齿轮呢就像是个机灵的小瘦子。
当发动机的动力传到变速器的时候,就好像是把一个任务交给了这群齿轮小伙伴。
比如说,当汽车要慢慢爬坡的时候,就需要很大的力气。
这时候呢,变速器就会让大齿轮和小齿轮配合起来,就像是大胖子带着小瘦子一起干活。
大齿轮转一圈,小齿轮可能要转好几圈呢。
这样就能把发动机的动力变得更有劲,就像把大力士的力量放大了一样,让汽车能够稳稳地爬上坡。
再比如说,当汽车在平坦的公路上要开得飞快的时候,就不需要那么大的劲儿啦,而是需要速度。
这时候变速器就会让小齿轮和大齿轮换一种配合方式。
小齿轮转得快快的,带动大齿轮转,虽然大齿轮转得慢一点,但是它能让汽车的车轮转得飞快,汽车就像一阵风一样跑起来啦。
而且哦,中间轴变速器还有个很神奇的地方。
它能在汽车行驶的过程中悄悄地改变齿轮的搭配。
你开车的时候可能都感觉不到呢。
就像一个魔术师在后台偷偷地变戏法。
比如说你在加速的时候,它就会很聪明地从一种齿轮组合切换到另一种更适合快速行驶的组合。
这中间轴变速器里面的齿轮之间的配合可精密啦。
它们之间的距离、大小比例都是经过精心设计的。
就像一个精心编排的舞蹈,每个动作都要恰到好处。
如果哪个齿轮有点小毛病,就像舞蹈演员跳错了一步,整个变速器的工作就会受到影响呢。
有时候啊,当你听到汽车换挡的时候有奇怪的声音,就可能是这个中间轴变速器里面的齿轮小伙伴闹别扭啦。
车辆工程毕业设计101九档双中间轴变速器
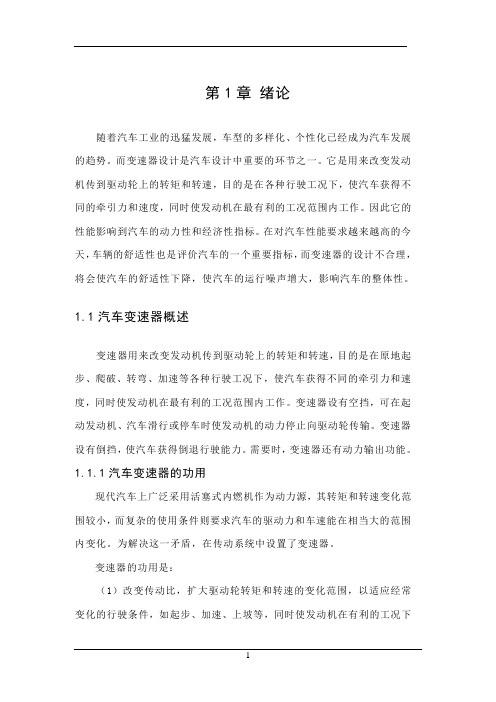
第1章绪论随着汽车工业的迅猛发展,车型的多样化、个性化已经成为汽车发展的趋势。
而变速器设计是汽车设计中重要的环节之一。
它是用来改变发动机传到驱动轮上的转矩和转速,目的是在各种行驶工况下,使汽车获得不同的牵引力和速度,同时使发动机在最有利的工况范围内工作。
因此它的性能影响到汽车的动力性和经济性指标。
在对汽车性能要求越来越高的今天,车辆的舒适性也是评价汽车的一个重要指标,而变速器的设计不合理,将会使汽车的舒适性下降,使汽车的运行噪声增大,影响汽车的整体性。
1.1汽车变速器概述变速器用来改变发动机传到驱动轮上的转矩和转速,目的是在原地起步、爬破、转弯、加速等各种行驶工况下,使汽车获得不同的牵引力和速度,同时使发动机在最有利的工况范围内工作。
变速器设有空挡,可在起动发动机、汽车滑行或停车时使发动机的动力停止向驱动轮传输。
变速器设有倒挡,使汽车获得倒退行驶能力。
需要时,变速器还有动力输出功能。
1.1.1汽车变速器的功用现代汽车上广泛采用活塞式内燃机作为动力源,其转矩和转速变化范围较小,而复杂的使用条件则要求汽车的驱动力和车速能在相当大的范围内变化。
为解决这一矛盾,在传动系统中设置了变速器。
变速器的功用是:(1)改变传动比,扩大驱动轮转矩和转速的变化范围,以适应经常变化的行驶条件,如起步、加速、上坡等,同时使发动机在有利的工况下工作;(2)在发动机旋转方向不变的前提下,使汽车能倒退行驶;(3)利用空挡,中断动力传递,以使发动机能够起动、怠速,并便于变速器换挡或进行动力输出。
1.1.2汽车变速器的分类汽车变速器按传动比变化方式不同,可分为有级式、无级式和综合式三种。
(1)有级式变速器应用最为广泛,它采用齿轮传动,具有若干个定值传动比。
按所用轮系形式不同,有级式变速器又可分为有轴线固定式变速器和轴线旋转式变速器两种。
目前,轿车和轻、中型货车变速器的传动比通常有3-5个前进挡和一个倒挡;在重型货车用的组合式变速器中,则有更多挡位。
变速箱中间轴课程设计说明书
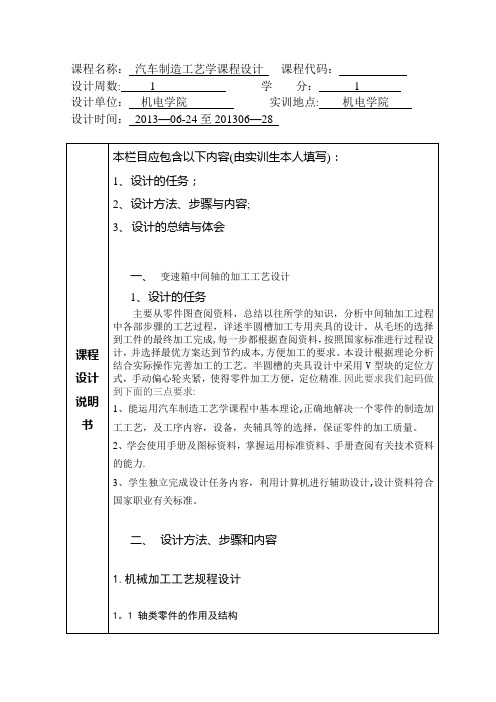
140 滚夹左端Φ30k6外圆顶右端中心孔
150 去毛刺去滚齿毛刺
160 铣 铣b=10 t=10 四槽
170 铣 铣平面
180 去毛 去齿轮左端毛刺
190 倒角 到齿轮园脚
200 去毛去倒角毛刺
210 剃 剃齿m=4.25 z=13 a=20°
220 铣 铣M30X1.5—6g螺纹
本夹具可选用偏心夹紧机构,符合工件的加工要求。
三、设计的总结与体会
经过一个星期的学习和查阅资料,我终于完成了汽车变速器中间轴承的设计。从开始接触课程题目到设计方案的确定,再到课程设计任务书的完成,每走一步对于我来说都是新的尝试和挑战。这也是我在大学期间独立完成的较大的项目。在这段时间里,我学到了很多知识也有也有很多感受。
通过这次设计我开始独立的学习和探索,查看相关资料和书籍,让自己头脑从模糊到逐渐清晰,使自己的设计逐步完善起来,每一次改进都使我受益颇丰。虽然我的设计有很多的不足,但是付出了自己的努力,这是我引以为傲的地方,我相信只有经历过的人才会明白其中的酸甜苦辣。在此感谢老师的指导和同学的热心帮助,让我解决了许多难题。希望这次经历能让我在以后的学习工作中激励。
加工的第二阶段是毛坯最初进入机械加工的阶段。各轴段粗加工半精加工,基准表面的精加工切齿加工。由于下一阶段进行半圆槽加工需要使用端面基准,所以需要使得端面的精度达到规定的技术要求。
加工的第三阶段是半圆槽的加工。采用V型块定位,端面为基准。
加工的第四阶段是剃齿加工。这个阶段的目的,在于修正齿轮经过淬火后所引起的齿形变形,进一步提高齿形精度和降低表面粗糙度,使之达到最终的精度要求.在这个阶段中首先应对定位基准面(孔和端面)进行修整,因淬火以后齿轮的内孔和端面均会产生变形,如果在淬火后直接采用这样的孔和端面作为基准进行齿形精加工,是很难达到齿轮精度的要求的.以修整过的基准面定位进行齿形精加工,可以使定位准确可靠,余量分布也比较均匀,以便达到精加工的目的。
汽车设计--3变速器设计
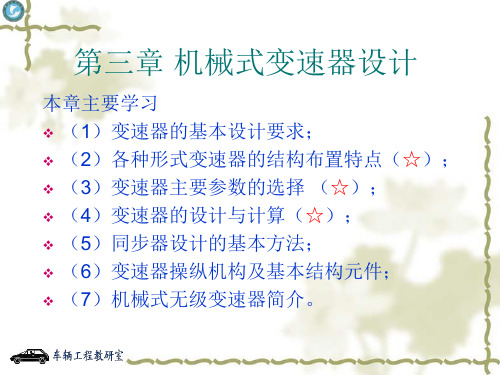
直齿:b=Kcm, Kc为齿宽系数,取为4.5~8.0 斜齿:b= Kcmn,Kc取6.0~8.5
5、变位系数的选择原则
◎采用变位的原因:
1)避免齿轮产生根切 2)配凑中心距 3)通过变位影响齿轮的强度,使用平稳性,耐磨性、抗胶
合能力及齿轮的啮合噪声。 ◎变位齿轮的种类:高度变位和角度变位。 1)高度变位:齿轮副的一对啮合齿轮的变位系数的和为零。
1、变速器的传动比范围: 指变速器最低挡传动比与最高挡传动比的比值。 2、最高挡传动比的选取: 直接挡1.0,超速挡0.7~0.8。
3、最低挡传动比选取:
影响因素:
发动机的最大转矩、最低稳定转速;
驱动轮与路面间的附着力; 主减速比与驱动轮的滚动半径;
Ft max Ff Fi max
汽车的最低稳定车速。
1、中间轴式变速器
❖ 多用于FR,RR布置的 乘用车和商用车上
❖ 能设置直接挡,直接挡 效率高
❖ 一挡传动比能设计较大
❖ 一轴与输出轴转向相同 (挂前进档时)
❖ 零件多,尺寸、质量大
2、两轴式变速器
❖ 结构简单、紧凑、轮廓 尺寸小
❖ 中间挡位传动效率高、 噪音低(少了中间轴、 中间传动齿轮)
❖ 不能设置直接挡,高挡 位时噪音高(轴承齿轮 均承载),且效率略比 三轴式低
第三章 机械式变速器设计
本章主要学习 ❖ (1)变速器的基本设计要求; ❖ (2)各种形式变速器的结构布置特点(☆); ❖ (3)变速器主要参数的选择 (☆); ❖ (4)变速器的设计与计算(☆); ❖ (5)同步器设计的基本方法; ❖ (6)变速器操纵机构及基本结构元件; ❖ (7)机械式无级变速器简介。
发动机功率48KW 中间轴 五档变速器课程设计讲解
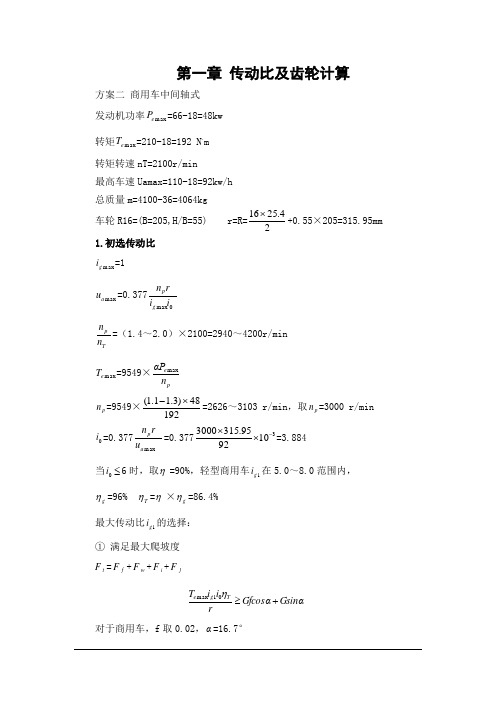
第一章 传动比及齿轮计算方案二 商用车中间轴式 发动机功率max e P =66-18=48kw 转矩max e T =210-18=192 N .m 转矩转速nT=2100r/min 最高车速Uamax=110-18=92kw/h 总质量m=4100-36=4064kg 车轮R16=(B=205,H/B=55) r=R=24.2516 ⨯+0.55×205=315.95mm 1.初选传动比m ax g i =1max a u =0.377max i i r n g pTp n n =(1.4~2.0)×2100=2940~4200r/minmax e T =9549×pe n αP maxp n =9549×19248)3.11.1( ⨯-=2626~3103 r/min ,取p n =3000 r/min0i =0.377maxa p u rn =0.3773109295.3153000-⨯⨯=3.884当0i ≤6时,取η=90%,轻型商用车1g i 在5.0~8.0范围内,g η=96% T η=η×g η=86.4% 最大传动比1g i 的选择: ① 满足最大爬坡度 t F =f F +w F +i F +j FGsin αGfcos αri i T Tg e +≥η01max对于商用车,f 取0.02,α=16.7°∴()T e g i T sin αfcos αGr i η0max 1+≥=()%4.86884.31927.1671602.031595.08.94064⨯⨯︒+︒⨯⨯⨯⨯sin .cos =5.44② 满足附着条件t F =f F +i F201max z Tg e f ri i T ≤ηφ,即T e z g i T r f i η0max 21≤φ=%4.86884.319231595.08.08.94064⨯⨯⨯⨯⨯=15.62在沥青混凝土干路面,φ=0.7~0.8,取φ=0.8 由以上两式得,5.44≤1g i ≤15.62 ∵轻型商用车1g i =5.0~8.0 ∴取1g i =7 各档传动比的确定 五档5g i =1,为直接挡按等比级数原则,一般汽车各挡传动比大致符合如下关系:q i i i i i i i i g g g g g g g g ====54433221式中:q —常数,也就是各挡之间的公比;因此,各挡的传动比为41q i g =,32q i g =,23q i g =,q i g =441g i q ==1.627所以各挡传动比与Ι挡传动比的关系为2g i =4.307,3g i =2.647,4g i =1.6272.初选中心距A初选中心距时,可根据下述经验公式31max g e A i T K A η=式中:A —变速器中心距(mm );A K —中心距系数,商用车:A K =8.6~9.6; max e T —发动机最大转矩(N .m );1i —变速器一挡传动比;g η—变速器传动效率,取96%。
九档双中间轴变速器毕业设计
摘要汽车传动系是汽车的核心组成部分。
其任务是调节变换发动机的性能,将动力有效而经济地传至驱动车轮,以满足汽车的使用要求。
变速器是完成传动系任务的重要部件,也是决定整车性能的主要部件之一。
变速器的设计水平对汽车的动力性、燃料经济性、换挡操纵的可靠性与轻便性、传动平稳性与效率等都有直接的影响。
随着汽车工业的发展,轿车变速器的设计趋势为增大变速器传递功率与重量之比,并要求变速器具有较小的尺寸和良好性能。
双中间轴变速器具有广泛的适用性,良好的整车匹配性。
广泛匹配载重车、自卸车、牵引车及各种专用车辆和特种车辆,为重型汽车的升级换代提供较好优化配置。
本文主要是对9档双中间轴变速器进行传动方案的设计,对主要零件轴、齿轮进行结构设计,对其他零件进行结构和选型设计。
进行齿轮的设计:包括材料选择、参数计算、强度计算及校核;轴的设计:包括结构设计并作出轴的计算简图、强度校核;轴承的选用及其他零件的结构设计。
关键词:9档双中间轴变速器;变速器;双中间轴ABSTRACTDrivetrain is the core components of automobile. Its task is transforming and regulateing the performance of engine. Transmission can effectively and economically conveyed the power to the wheel which can meet the requirement of vehicles. Transmission is the important part of drivetrain components to complete the tasks. as well as one of the main factor to decide the whole performance of vehicle. The standards of Transmission designing can directly impact the vehicle dynamics, fuel economy, the reliability and portability of shifting, the smoothness and efficiency of Transmiting. Along with the development of the automobile industry, the trend of car transmission designing is to increase its transmission power and decrese its weight ,and hope have smaller size and excellent performance.This paper mainly describes the design of nine block manual transmission, the transmission principle of work elaborated, Transmission of the gear shaft and do a detailed design, and the intensity of a school. For some standard parts for the selection. Transmission Trans mission program design. A brief description of the trans mission of all components of the material choice.Keywords: Nine block manual transmission;Transmission;Twin countershaft transmission目录摘要................................................................................................... .I Abstract (II)目录 (3)第1章绪论 (1)1.1汽车变速器概述 (1)1.1.1汽车变速器的功用 (1)1.1.2汽车变速器的分类 (2)1.2双中间轴变速器概述 (2)1.2.1双中间轴变速器的原理 (3)1.2.2双中间轴变速器的特点 (3)1.2.3汽车变速器国内外发展状况 (4)1.3课题设计意义 (6)1.4课题设计内容和方案 (7)1.4.1变速器设计应满足的基本要求 (7)1.4.2课题设计内容 (8)1.4.3课题设计方案 (9)第2章九档变速器总体方案设计 (10)2.1车型及基本参数的选择 (10)2.2减速器的基本要求及型号设定 (12)2.2.1变速器的基本要求 (12)2.2.2变速器的型号设定 (12)2.3 变速器传动机构布置方案 (13)2.3.1 变速器传动方案分析与选择 (13)2.3.2 倒档布置方案 (15)2.3.3零部件结构方案分析 (16)2.4变速器操纵机构布置方案 (18)2.4.1变速器操纵机构概述 (18)2.4.2典型的操纵机构及其锁定装置 (19)2.5换挡机构形式 (21)第3章变速器主要参数的选取和计算 (23)3.1档数的选择 (23)3.2传动比的计算 (23)3.2.1传动比范围 (23)3.2.2变速器各档传动比的选取 (29)3.2.3变速器各档传动比的计算校核 (25)3.2.4中心距的计算 (29)3.2.5变速器的外形尺寸 (34)3.2.6齿轮参数的选择 (35)3.2.7各档齿轮齿数的分配及传动比的计算 (37)第4章变速器的设计与校核 (37)4.1 齿轮的校核 (37)4.1.1 齿轮材料的选择原则 (37)4.1.2变速器齿轮弯曲强度校核 (38)4.1.3变速器齿轮轮齿接触应力校核 (43)4.1.4变速器轮齿轮齿强度校核 (51)4.2 轴的结构与尺寸设计 (54)4.2.1 初选轴的直径 (54)4.3 轴的验算 (54)4.3.1 轴的刚度计算 (55)4.3.2轴的强度计算 (57)4.4 轴承选择与寿命计算 (60)4.4.1轴承的选择与寿命计算 (60)第5章同步器与操纵机构设计 (62)5.1 同步器设计 (62)5.1.1同步器的功用及分类 (62)5.1.2 惯性式同步器 (62)5.1.3 锁环式同步器主要尺寸的确定 (63)5.1.4同步器主要参数的确定 (64)结论 (65)致谢 (66)参考文献 (67)第1章绪论随着汽车工业的迅猛发展,车型的多样化、个性化已经成为汽车发展的趋势。
中间轴式变速器课程设计
第一章变速器传动机构布置方案1.1变速器传动方案的选择与分析机械式变速器具有结构简单、传动效率高、制造成本底和工作可靠等优点,故在不同形式的汽车上得到广泛应用。
变速器传动方案分析与选择机械式变速器传动机构布置方案主要有两种:两轴式变速器和中间轴式变速器。
1.2倒档方案的确定倒档布置选择方案适用于全部齿轮均为常啮合的齿轮,换挡轻便。
如下图1.3换挡操纵装置方案的确定倒档设置在变速器左侧或右侧,在结构上均能实现,不同之处是挂到当时驾驶员移动变速杆的方向改变了,为防止无挂倒档,一般在挂倒档时设有一个挂到当时克服弹簧所产生的力,来提醒驾驶员本次设计选的变速器档杆换挡位置与顺序如下图:1.4变速器总传动方案的确定由以上的内容可以基本设计出档位布置,如下图:1-一轴常啮合齿轮2-中间轴常啮合齿轮3-二轴四挡齿轮4-中间轴四挡齿轮5-二轴三挡齿轮6-中间轴三挡齿轮7-二周二挡齿轮8-中间轴二挡齿轮9-二轴一挡齿轮10-中间轴一挡齿轮11-二轴倒挡齿轮12-中间轴倒挡齿轮13-倒挡中间齿轮。
第二章变速器的设计与计算2.1汽车基本参数的确定商用车(中间轴式)低档传动比选取的因素有:发动机的最大转矩和最低稳定转速所要求的汽车最大爬坡能力、驱动轮与路面间的附着力、主减速比和驱动轮的滚动半径以及所要求达到的最低稳定行驶车速等。
目前乘用车的传动比范围在3.0~4.5之间,总质量轻些的商用车在5.0~8.0之间,其它商用车则更大。
?本设计最高档传动比为1。
2.2.3.变速器各档传动比的确定1)确定主减速器传动比的发动机转速与汽车行驶速度之间的关系式为[12]:377.0i i rnu g a =(3.1) 式中:a u ——汽车行驶速度(km/h ); n ——发动机转速(r/min );max e T ——发动机最大扭矩(N ·m); 0i ——主减速器传动比; g i ——变速器传动比;t η——为传动效率(96%);R ——车轮滚动半径;m ax α——最大爬坡度(商用车要求能爬上30%的坡,大约 7.16) 由公式(3.2)得:te g i T rG G i ηααμ0max max max 1)sin cos (+≥(3.3)已知:m=4000kg ;015.0=f ; 7.16max =α;r=0.42m ;196max =e T N ·m ;58.50=i ;g=9.8m/s 2;88.0=t η,把以上数据代入(3.3)式:式中:A ——变速器中心距(mm );A K ——中心距系数,商用车A K =8.6~9.6; max e T ——发动机最大输出转距为196(N·m );1i ——变速器一档传动比为6;g η——变速器传动效率,取96%。
(毕业设计)中型专用汽车变速器设计说明书
摘要变速器用来改变发动机传到驱动轮上的转矩和转速,目的是在原地起步、爬坡、转弯、加速等各种行驶工况下,使汽车获得不同的牵引力和速度,同时使发动机在最有利的工况范围内工作。
所以变速器的结构设计的合理性直接影响到汽车动力性和经济性。
设计要求达到换挡迅速、省力、方便、有较高的工作效率、工作噪声低。
因此变速器在汽车中得到广泛应用。
本次设计的是五个前进档加一个倒档的中型专用车的变速器。
为了使该变速器应用范围更加的广泛,应用到不同工程上,使得本变速器带有取力器。
变速器采用中间轴式,换档形式采用的是同步器和滑移齿轮换档,使的换档方便,可靠。
操纵机构设有自锁和互锁装置。
先利用已知参数确定各挡传动比,再后确定齿轮的模数、压力角、齿宽等参数。
由中心矩确定箱体的长度、高度和中间轴及二轴的轴径,然后对中间轴和各挡齿轮进行校核。
在设计过程中,利用CAXA绘图,运用MATALAB软件编程。
最后绘制装配图及零件图。
通过本次设计,使所设计的变速器工作可靠,传动效率更高。
关键词:变速器,同步器,齿轮,取力器AbstractTo change the engine used to spread transmission of torque and wheel speed, the aim of starting in place, climb, turn and accelerate a variety of driving conditions, different vehicle traction and speed, while the engine in the most favorable range conditions.Therefore, the reasonability of the structure design of a transmission gearbox directly affects the vehicle's dynamic performance. It is usually required shifting gears rapidly and conveniently, saving force, and having a higher working efficiency and low working noises.The design of the five forward file plus a reverse of the transmission medium-sized special vehicle. In order to make the transmission more broad range of applications, application to a different project, make a check of the power transmission device. Transmission use of the middle axis, shifting the form of using the synchronizer gear shift and sliding to make the shift easy and reliable. Manipulation of institutions with self-locking and interlocking devices.Using the given basic parameters, it was firstly determined the transmission ratio of each shift, the shaft center distances, the gear modulus, the gear pressing angles and widths, and so on. And then the general dimension of the gearbox, including its length, width and height , and then on the intermediate shaft and the block to check gear. During the design process, using CAXA mapping, the use of software programming MATALAB. The final assembly drawing and components drawing Fig.Through this design, so that the design of the transmission of reliable, efficient transmission.Key words:Transmission,,Synchronizer,Gear,Take out of power目录第一章前言 (1)第二章变速器结构概述 (2)第三章变速器各主要参数的设计计算 (3)3.1变速器传动比的确定 (3)3.2中心距的初步确定 (4)3.3轴的直径的初步确定 (4)3.4齿轮模数的确定 (5)3.5齿轮压力角的选择 (5)3.6各档齿轮齿数的分配 (5)3.7变位系数的选择 (7)3.8齿轮齿宽的设计计算 (7)3.9变速器同步器的设计计算 (8)第四章变速器中间轴的校核 (11)4.1中间轴常啮合齿轮处进行校核 (11)4.2对中间轴四挡齿轮处进行校核 (12)4.3对中间轴三挡齿轮进行校核 (13)4.4对中间轴二挡齿轮处进行校核 (13)4.5对中间轴一档挡齿轮处进行校核 (14)第五章变速器各档齿轮强度的校核 (16)5.1齿轮弯曲应力计算 (16)5.1.1二轴一挡直齿轮校核 (16)5.1.2倒挡直齿轮校核 (16)5.1.3二轴二挡斜齿轮校核 (17)5.1.4二轴三挡斜齿轮校核 (17)5.1.5二轴四挡斜齿轮校核 (17)5.1.6二轴常啮合斜齿轮校核 (18)5.1.7中间轴一档齿轮校核 (18)5.1.8中间轴二档齿轮校核 (18)5.1.9中间轴三档齿轮校核 (18)5.1.1.0中间轴四档齿轮校核 (19)5.1.1.1中间轴常啮合齿轮校核 (19)5.2齿轮接触应力计算 (19)5.2.1 二轴一挡直齿轮校核 (20)5.2.2二轴二挡斜齿轮校核 (20)校核 (21)5.2.3 二轴三挡斜齿轮Z7校核 (21)5.2.4二轴四挡斜齿轮Z5校核 (22)5.2.5二轴常啮合斜齿轮Z35.2.6中间轴一档齿轮校核 (22)5.2.7中间轴二档齿轮校核 (23)5.2.8中间轴三档齿轮校核 (23)5.2.9中间轴四档齿轮校核 (23)5.2.1.0中间轴常啮合齿轮校核 (24)5.2.1.1倒档齿轮校核 (24)第六章变速器操纵机构的设计 (25)第七章变速器轴承的选择 (26)第八章取力器的设计与计算 (27)8.1取力器的布置 (27)8.2取力器齿轮、轴和轴承的参数选择和强度计算 (28)第九章结论 (31)参考文献 (32)致谢 (33)附录一 (34)外文翻译 (34)附录二 (43)第一章前言变速器是传动系的重要部件,它的任务就是充分发挥发动机的性能,使发动机发出的动力有效而经济地传到驱动轮,以满足汽车行驶上的各项要求。
中间轴式变速器设计
目录1.概述 (2)2 中间轴式变速器设计 (3)2.1传动方案和零部件方案的确定 (3)2.1.1传动方案初步确定 (4)2.1.2零部件结构方案 (4)2.2 主要参数的选择和计算 (5)2.2.1 先确定最小传动比 (5)2.2.2 确定最大传动比 (6)2.2.3 挡位数确定 (7)2.2.4 中心距A (8)2.2.5 外形尺寸设计 (8)2.2.6 齿轮参数 (9)3 变速器的设计计算 (14)3.1轮齿设计计算 (14)3.1.1 齿轮弯曲强度计算 (14)3.1.2 轮齿接触应力 (17)3.2 轴设计计算 (19)3.2.1 轴的结构 (19)3.2.2 确定轴的尺寸 (19)3.2.3 轴的校核 (20)图1:中间轴式变速器2 中间轴式变速器设计2.1传动方案和零部件方案的确定作为一辆前置后轮驱动的货车,毫无疑问该选用中间轴式多挡机械式变速器。
中间轴式变速器传动方案的共同特点如下。
(1)设有直接挡;(2)1挡有较大传动比;(3)档位搞的齿轮采用常啮合传动,档位低的齿轮(1挡)可以采用或不采用常啮合齿轮川东南;(4)除1挡外,其他档位采用同步器或啮合套换挡;(5)除直接挡外,其他档位工作时的传动效率略低。
2.1.1传动方案初步确定(1)变速器第一轴后端与常啮合主动齿轮做成一体,第2轴前端经滚针轴承支撑在第1轴后端的孔内,且保持两轴轴线在同一条直线上,经啮合套将它们连接后可得到直接挡。
档位搞的齿轮采用常啮合齿轮传动,1挡采用滑动直齿轮传动。
(2)倒档利用率不高,而且都是在停车后在挂入倒档,因此可以采用支持滑动齿轮作为换挡方式。
倒挡齿轮采用联体齿轮,避免中间齿轮在最不利的正负交替对称变化的弯曲应力状态下工作,提高寿命,并使倒挡传动比有所增加,装在靠近支承出的中间轴1挡齿轮处。
2.1.2零部件结构方案2.1.2.1齿轮形式齿轮形式有直齿圆柱齿轮、斜齿圆柱齿轮。
两者相比较,斜齿圆柱齿轮有使用寿命长、工作时噪声低的优点;缺点是制造工艺复杂,工作时有轴向力。
- 1、下载文档前请自行甄别文档内容的完整性,平台不提供额外的编辑、内容补充、找答案等附加服务。
- 2、"仅部分预览"的文档,不可在线预览部分如存在完整性等问题,可反馈申请退款(可完整预览的文档不适用该条件!)。
- 3、如文档侵犯您的权益,请联系客服反馈,我们会尽快为您处理(人工客服工作时间:9:00-18:30)。
汽车设计课程设计——变速器设计学院机械与汽车工程学院组别指导教师学生姓名 Sanity Shaw 学号提交日期 2011年 7 月 8 日目录1.概述 (3)2 中间轴式变速器设计 (4)2.1传动方案和零部件方案的确定 (4)2.1.1传动方案初步确定 (4)2.1.2零部件结构方案 (5)2.2 主要参数的选择和计算 (6)2.2.1 先确定最小传动比 (6)2.2.2 确定最大传动比 (7)2.2.3 挡位数确定 (8)2.2.4 中心距A (9)2.2.5 外形尺寸设计 (9)2.2.6 齿轮参数 (10)3 变速器的设计计算 (15)3.1轮齿设计计算 (15)3.1.1 齿轮弯曲强度计算 (15)3.1.2 轮齿接触应力 (18)3.2 轴设计计算 (20)3.2.1 轴的结构 (20)3.2.2 确定轴的尺寸 (20)3.2.3 轴的校核 (21)1.概述变速器的功用是根据汽车在不同的行驶条件下提出的要求,改变发动机的扭矩和转速,使汽车具有适合的牵引力和速度,并同时保持发动机在最有利的工况范围内工作。
为保证汽车倒车以及使发动机和传动系能够分离,变速器具有倒档和空档。
在有动力输出需要时,还应有功率输出装置。
对变速器的主要要求是:(1).应保证汽车具有高的动力性和经济性指标。
在汽车整体设计时,根据汽车载重量、发动机参数及汽车使用要求,选择合理的变速器档数及传动比,来满足这一要求。
(2).工作可靠,操纵轻便。
汽车在行驶过程中,变速器内不应有自动跳档、乱档、换档冲击等现象的发生。
为减轻驾驶员的疲劳强度,提高行驶安全性,操纵轻便的要求日益显得重要,这可通过采用同步器和预选气动换档或自动、半自动换档来实现。
(3).重量轻、体积小。
影响这一指标的主要参数是变速器的中心距。
选用优质钢材,采用合理的热处理,设计合适的齿形,提高齿轮精度以及选用圆锥滚柱轴承可以减小中心距。
(4).传动效率高。
为减小齿轮的啮合损失,应有直接档。
提高零件的制造精度和安装质量,采用适当的润滑油都可以提高传动效率。
(5).噪声小。
采用斜齿轮传动及选择合理的变位系数,提高制造精度和安装刚性可减小齿轮的噪声。
图1:中间轴式变速器2 中间轴式变速器设计2.1传动方案和零部件方案的确定作为一辆前置后轮驱动的货车,毫无疑问该选用中间轴式多挡机械式变速器。
中间轴式变速器传动方案的共同特点如下。
(1)设有直接挡;(2) 1挡有较大传动比;(3)档位搞的齿轮采用常啮合传动,档位低的齿轮(1挡)可以采用或不采用常啮合齿轮川东南;(4)除1挡外,其他档位采用同步器或啮合套换挡;(5)除直接挡外,其他档位工作时的传动效率略低。
2.1.1传动方案初步确定(1)变速器第一轴后端与常啮合主动齿轮做成一体,第2轴前端经滚针轴承支撑在第1轴后端的孔内,且保持两轴轴线在同一条直线上,经啮合套将它们连接后可得到直接挡。
档位搞的齿轮采用常啮合齿轮传动,1挡采用滑动直齿轮传动。
(2)倒档利用率不高,而且都是在停车后在挂入倒档,因此可以采用支持滑动齿轮作为换挡方式。
倒挡齿轮采用联体齿轮,避免中间齿轮在最不利的正负交替对称变化的弯曲应力状态下工作,提高寿命,并使倒挡传动比有所增加,装在靠近支承出的中间轴1挡齿轮处。
2.1.2零部件结构方案2.1.2.1齿轮形式齿轮形式有直齿圆柱齿轮、斜齿圆柱齿轮。
两者相比较,斜齿圆柱齿轮有使用寿命长、工作时噪声低的优点;缺点是制造工艺复杂,工作时有轴向力。
变速器中的常啮合齿轮均采用斜齿圆柱齿轮。
直齿圆柱齿轮仅用于抵挡和倒挡。
2.1.2.2换挡机构形式此变速器换挡机构有直齿滑动齿轮、移动啮合套换挡和同步器换挡三种形式。
采用轴向滑动直齿齿轮换挡,会在轮齿端面产生冲击,齿轮端部磨损加剧并过早损坏,并伴有噪声,不宜用于高档位。
为简化机构,降低成本,此变速器1挡、倒挡采用此种方式。
常啮合齿轮可用移动啮合套换挡。
因承受换挡冲击载荷的接合齿齿数多,啮合套不会过早被损坏,但不能消除换挡冲击。
目前这种换挡方法只在某些要求不高的挡位及重型货车变速器上应用。
因此不适合用于本设计中的变速器,不采用啮合套换挡。
使用同步器能保证换挡迅速、无冲击、无噪声,得到广泛应用。
虽然结构复杂、制造精度要求高、轴向尺寸大,但为了降低驾驶员工作强度,降低操作难度,2挡以上都采用同步器换挡。
2.1.2.3变速器轴承变速器轴承常采用圆柱滚子轴承、球轴承、滚针轴承、圆锥滚子轴承、滑动轴套等。
变速器第1轴、第2轴的后部轴承以及中间轴前、后轴承,按直径系列一般选用中系列球轴承或圆柱滚子轴承。
中间轴上齿轮工作时产生的轴向力,原则上由前或后轴承来承受都可以;但当在壳体前端面布置轴承盖有困难的时候,必须由后端轴承承受轴向力,前端采用圆柱滚子轴承承受径向力。
滚针轴承、滑动轴套用于齿轮与轴不固定连接,有相对转动的地方,比如高档区域同步器换挡的第2轴齿轮和第2轴的连接,由于滚针轴承滚动摩擦损失小,传动效率高,径向配合间隙小,定位及运转精度高,有利于齿轮啮合,在不影响齿轮结构的情况下,应尽量使用滚针轴承。
2.2 主要参数的选择和计算目前,货车变速器采用4~5个挡或多挡,多挡变速器多用于重型货车和越野汽车。
因此挡位数大致在4~5个,需要通过计算传动比范围后最后确定。
2.2.1 先确定最小传动比传动系最小传动比可由变速器最小传动比i g和主减速器传动比i0的乘积来表示i tmin=i gmin i0 3-1通常变速器最小传动比i gmin取决于传动系最小传动比i t0和主减速器传动比i0,而根据汽车理论,汽车最高车速时变速器传动比最小,则根据公式u a=0.377rni gmin i03-2式中:u a为汽车行驶速度,km/h; n为发动机转速,r/min; r为车轮半径,m; i gmin 特指为最高档传动比。
可得i tmin=0.377rnu amax3-3轻型车轮胎尺寸根据GB/T2977-1997《载重汽车轮胎系列》可选用7.50R20,即轮胎名义宽度7.5in,轮辋名义直径16in,轮胎扁平率为90~100,在此取90,则轮胎直径可以算为r=(7.5x2x0.95+20)2x25.41000≈0.435(m)汽车给定的最大车速为100km/h,发动机转速为2566.3r/min,代入③式得i tmin=4. 23另外,为了满足足够的动力行呢,还需要校核最高档动力因数D0max。
一般汽车直接挡或最高档动力因数取值范围如下表所示本设计汽车总质量为7000t,为中型货车,可选取D0max=0.06,最小传动比与最高档动力因数D0max有如下关系D0max=T tqmax i tminηtrG −C D Au at221.15G3-4式中:u at为直接挡或最高档时,发动机发出最大扭矩时的最大车速,km/h,此时可近似取u at=u amax。
其它参数见下表。
tmin小传动比为i tmin=4.11。
若按变速器直接挡i gmin=1,则i0=4.11,该车采用单级主减速器,主减速器传动比i0≤7,满足要求。
2.2.2 确定最大传动比确定传动系最大传动比,要考虑三方面问题,最大爬坡度或1挡最大动力因数D1max、附着力和汽车最低稳定车速。
传动系的最大传动比通常是变速器1挡传动比i g1与主减速器传动比i0的乘积,即i tmax=i g1i0 3-5当汽车爬坡时车速很低,可以忽略空气阻力,汽车的最大驱动力应为F tmax=F f+F imax 3-6各表达式展开为T tqmax i tminηtr=Gf cosαmax+G sinαmax 3-7 则i g1≥G(f cosαmax+sinαmax)rT tqmax i0ηt3-8 各参数见下表计算参数表一般货车最大爬坡度为30%,即αmax≈16.7°。
代入3-8式计算可得i g1≥4.50。
1挡传动比还应满足附着条件F tmax =T tqmax i g1i 0ηt r ≤F φ 3-9对于后轮驱动汽车,最大附着力有如下公式F φ=F Z2φ=G 2φ=m 2gφ 3-10式中:m 2为后轴质量,查表得满载时取值范围为m 2=(65%-70%)m a ,选取65.3%m a ,即满载时后轴质量为4571kg将式3-9代入式3-10求得i g1≤m 2gφrT tqmax i 0ηt 取φ=0.7,计算可得i g1≤6.71。
结合上面已经计算数值i g1≥4.23。
故c 初步取i g1=4.5,即变速器传动比范围是1~4.5,传动系最大传动比i tmax =18.495。
2.2.3 挡位数确定增加变速器挡位数能够改善汽车的动力性和经济性。
挡位数越多,变速器的结构越复杂,使轮廓尺寸和质量加大,而且在使用时换挡频率也增高。
在最低挡传动比不变的条件下,增加变速器的挡位数会使变速器相邻的低挡与高挡之间的传动比比值减小,换挡容易进行。
在确定汽车最大和最小传动比之后,应该确定中间各挡的传动比。
实上上,汽车传动系各挡传动比大体上是按照等比级数分配的。
因此,各挡传动比的大致关系为q i i iig g g g ==3221式中:q 为各挡之间的公比。
当挡位数为n 时,有 11-=n g i q对于本变速器,挡位数暂定为4,则11-=n g i q =35.4=1.65<1.8一般挡数选择要求如下。
1)为了减小换挡难度,相邻档位之间的传动比比值在1.8以下。
2)高挡区相邻档位之间的传动比比值要比抵挡相邻挡位之间的比值小。
即本例满足要求,确定挡位数为4,则i g1=4.5,i g2=q2=2.72,i g3=q=1.65,i g4=1.2.2.4 中心距A对于中间轴式变速器,中间轴与第2轴之间的距离称为变速器中心距A。
变速器中心距是一个基本参数,对变速器的外形尺寸、体积和质量大小、齿轮的接触强度都有影响。
中心距越小,齿轮的接触应力越大,齿轮的寿命越短。
因此,最小允许中心距应当由保证轮齿有必要的接触强度来确定。
初选中心距A时,可根据下面的经验公式计算33-11A=K A√T emax i g1ηg式中:K A为中心距系数,货车为8.6~9.6;T emax为发动机最大转矩,N.m;i g1为变速器1挡传动比;η为变速器传动效率,取96%。
g货车的变速器中心距在80~170mm范围内变化。
对于本中型货车,可取K A=9.0,其余取值按照已有参数计算3-11式可得A≈120.07mm。
2.2.5 外形尺寸设计货车变速器壳体的轴向尺寸与挡数有关,4挡为(2.2~2.7)A。
当变速器选用的常啮合齿轮对数和同步器多时,应取给出范围的上限。
本中型货车,4挡变速器壳体的轴向尺寸取2.7A,即324.20mm,取整得L=325mm。