谈一氧化碳变换工艺条件选择
一氧化碳低温变换

一氧化碳的低温变换CO变换的工艺流程主要由原料气组成来决定的,同时还与催化剂、变换反应器的结构,以及气体的净化要求有关。
目前低温变换主要是串接在中温变换催化剂后作为一氧化碳深度变换的。
而入口一氧化碳含量5%-8% , 最高使用温度不超过300℃。
中变串低变流程一般采用两种方法,一是中变炉外加低变炉, 另一种为变换炉中一二层用中变触媒, 三层使用低温触媒。
两种方法都使系统出口一氧化碳含量降至1%左右, 起到稳定生产、增产节能之效果。
1.中(高)变-底变串联流程采用此流程一般与甲烷化脱除少量碳氧化物相配合。
这类流程先通过中(高)温变换将大量CO变换达到3%左右后,再用低温变换使一氧化碳含量降低到0.3%-0.5%,。
为了进一步降低出口气中CO含量,也有在低变后面串联一个低变的流程。
当CO含量较高时,变换气一般选择在炉外串低变;而一氧化碳含量较低时,可选择在炉内串低变。
中串低流程中要主要两个问题,一是要提高低变催化剂的抗毒性,防止低变催化剂过早失活;二是要注意中变催化剂的过度还原,因为与单一的中变流程相比,中串低特别是中低低流程的反应汽气比下降,中变催化剂容易过度还原,引起催化剂失活、阻力增大及使用寿命缩短。
2.全低变流程中(高)变-低变串联流程操作繁琐,设备增加,特别是特殊材料阀门的选用给管理带来了许多不便。
使用全低变变换催化剂代替原Fe-Cr系中变催化剂,在低温下完成变换即可克服以上两种工艺的缺点,又能达到理想的目的。
全低变工艺采用宽温区的钴钼系耐硫变换催化剂,主要有下列优点。
(1)催化剂的起始活性温度低,变换炉入口温度及床层热点温度低于中变炉入口及热点温度100-200℃。
这样,就降低了床层阻力,缩小了气体体积约20%,从而提高了变换炉的生产能力。
(2)变换系统处于较低的温度范围内操作,在满足出口变换气中CO含量的前提下,可以降低入炉蒸汽量,使全低变流程的蒸汽消耗降低。
使用全低变变换催化剂代替原。
一氧化碳变换综述

的氧化铬、氧化铝、氧化锰、氧化钡等, 它们的存在,可增加催化剂抗烧结的作用, 延长催化剂使用寿命,增长催化剂的成型 性能和机械强度。 目前,中小型氮肥厂的低变催化剂均采用 Co-Mo系催化剂。Co-Mo系变换催化剂是 以Co, Mo为有效组份,以Al2O3为骨架, 碱金属或稀土金属的氧化物为辅助催化剂。 Co-Mo系变换催化剂使用前必须先进行硫 化,生成CoS, MoS2才能获得高的活性。 1.3.2 低变催化剂的主要成分
全低变的工艺流程
半水煤气 油 分 离 器 活 性 炭 滤 油 器
变 换 气 换 热 器
煤 气 换 热 器
第 一 变 换 炉
变换气 工段
变 换 气 冷 却 器
淬 冷 过 滤 器
淬 冷 过 滤 器
第 二 变 换 炉
Ⅰ
Ⅱ
半水煤气首先进入油水分离器,脱除部分固体和液体杂质后 进入活性炭滤油器,进一步脱除杂质。经净化的半水煤气 进入变换气换热器与从第二变换炉出来的变换气进行逆向 热交换,使其温度上升到180 ℃左右,变换气温度下降到 160 ℃左右。出变换气换热器的半水煤气再进入煤气换热 器与从第一变换炉出来的变换气进行逆向热交换,变换气 自身的温度下降到300 ℃左右,半水煤气升温到200 ℃左 右。出煤气换热器的半水煤气与来自管网的中压水蒸气混 合,一方面使半水煤气温度上升到变换反应温度,另一方 面使半水煤气增湿,并达到设计要求所需要的汽气比进入 第一变换炉发生变换反应,在第一变换炉内CO的变换率 可达到60%左右。经第一变换炉变换后出来的变换气进入 煤气换热器与半水煤气逆向换热后进入淬冷过滤器I,逆 向与喷淋下来的冷却水换热并使冷却水汽化,此时变换气 的温度下降到230 ℃左右,冷却水和变换气换热后汽化, 从而使蒸汽含量达到设计要求,湿变换气进入第二变换炉 第一段催化剂床层进行变换反应。经第二变换炉第一段催 化剂床层变换反应后CO的变换率可达到85%左右,温度
一氧化碳变换操作规程
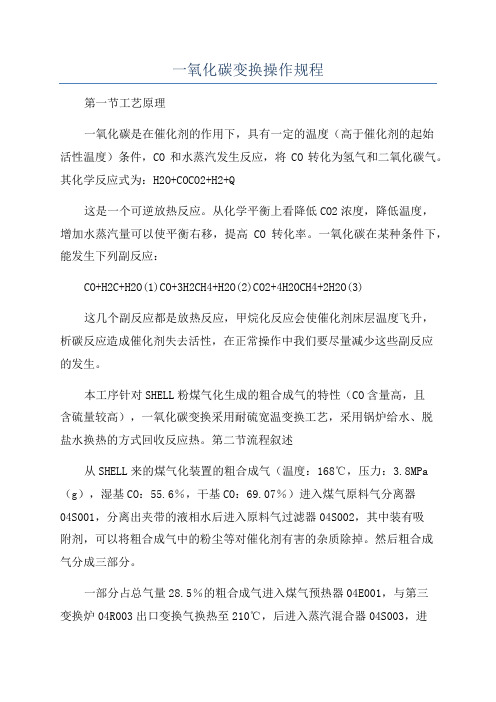
一氧化碳变换操作规程第一节工艺原理一氧化碳是在催化剂的作用下,具有一定的温度(高于催化剂的起始活性温度)条件,CO和水蒸汽发生反应,将CO转化为氢气和二氧化碳气。
其化学反应式为:H2O+COCO2+H2+Q这是一个可逆放热反应。
从化学平衡上看降低CO2浓度,降低温度,增加水蒸汽量可以使平衡右移,提高CO转化率。
一氧化碳在某种条件下,能发生下列副反应:CO+H2C+H2O(1)CO+3H2CH4+H2O(2)CO2+4H2OCH4+2H2O(3)这几个副反应都是放热反应,甲烷化反应会使催化剂床层温度飞升,析碳反应造成催化剂失去活性,在正常操作中我们要尽量减少这些副反应的发生。
本工序针对SHELL粉煤气化生成的粗合成气的特性(CO含量高,且含硫量较高),一氧化碳变换采用耐硫宽温变换工艺,采用锅炉给水、脱盐水换热的方式回收反应热。
第二节流程叙述从SHELL来的煤气化装置的粗合成气(温度:168℃,压力:3.8MPa (g),湿基CO:55.6%,干基CO:69.07%)进入煤气原料气分离器04S001,分离出夹带的液相水后进入原料气过滤器04S002,其中装有吸附剂,可以将粗合成气中的粉尘等对催化剂有害的杂质除掉。
然后粗合成气分成三部分。
一部分占总气量28.5%的粗合成气进入煤气预热器04E001,与第三变换炉04R003出口变换气换热至210℃,后进入蒸汽混合器04S003,进入该混合器前,来自蒸汽管网的过热蒸汽(4.4MPa,282℃)与粗合成气混合。
进蒸汽混合器的蒸汽量由调节阀FV-04005调节,该蒸汽量与28.5%的粗合成气量是比例控制,保证进入一变、汽、气比不低于1.09,原料气管线设有TV-04003调节阀旁路(测温点TE-04003在一变的入口。
混合后的粗合成气进入煤气换热器04E002管侧与来自第一变换炉04R001出口的变换气换热。
合成气温度由TV-04003控制在约255℃左右,进入第一变换炉04R001进行变换反应(一变入口湿基CO:33.1%)。
一氧化碳低温变换工艺及应用
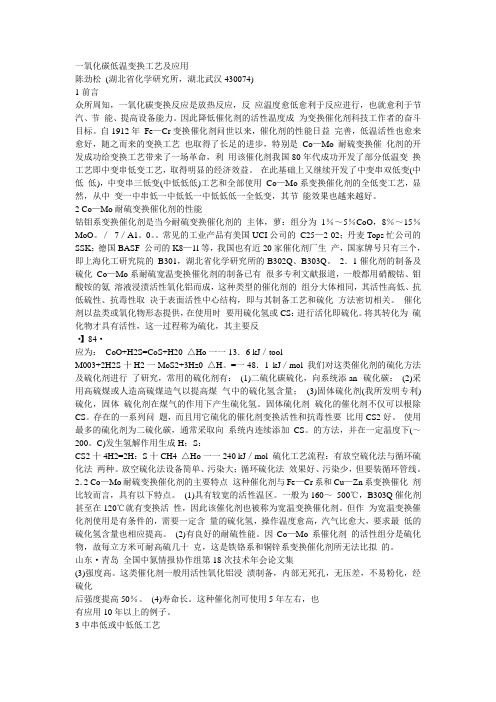
一氧化碳低温变换工艺及应用陈劲松(湖北省化学研究所,湖北武汉430074)1前言众所周知,一氧化碳变换反应是放热反应,反应温度愈低愈利于反应进行,也就愈利于节汽、节能、提高设备能力。
因此降低催化剂的活性温度成为变换催化剂科技工作者的奋斗目标。
自1912年Fe—Cr变换催化剂问世以来,催化剂的性能日益完善,低温活性也愈来愈好,随之而来的变换工艺也取得了长足的进步,特别是Co—Mo耐硫变换催化剂的开发成功给变换工艺带来了一场革命,利用该催化剂我国80年代成功开发了部分低温变换工艺即中变串低变工艺,取得明显的经济效益。
在此基础上又继续开发了中变串双低变(中低低),中变串三低变(中低低低)工艺和全部使用Co—Mo系变换催化剂的全低变工艺,显然,从中变一中串低一中低低一中低低低一全低变,其节能效果也越来越好。
2 Co—Mo耐硫变换催化剂的性能钴钼系变换催化剂是当今耐硫变换催化剂的主体,萝:组分为1%~5%CoO,8%~15%MoO。
/7/A1。
0。
常见的工业产品有美国UCI公司的C25—2-02;丹麦Tops忙公司的SSK;德国BASF 公司的K8—1l等,我国也有近20家催化剂厂生产,国家牌号只有三个,即上海化工研究院的B301,湖北省化学研究所的B302Q、B303Q。
2.1催化剂的制备及硫化Co—Mo系耐硫宽温变换催化剂的制备已有很多专利文献报道,一般都用硝酸钴、钼酸铵的氨溶液浸渍活性氧化铝而成,这种类型的催化剂的组分大体相同,其活性高低、抗低硫性、抗毒性取决于表面活性中心结构,即与其制备工艺和硫化方法密切相关。
催化剂以盐类或氧化物形态提供,在使用时要用硫化氢或CS:进行活化即硫化。
将其转化为硫化物才具有活性,这一过程称为硫化,其主要反·】84·应为:CoO+H2S=CoS+H20 △Ho一一13.6 kJ/toolM003+2H2S十H2一MoS2+3Hz0 △H。
=一48.1 kJ/mol 我们对这类催化剂的硫化方法及硫化剂进行了研究,常用的硫化剂有:(1)二硫化碳硫化,向系统添an--硫化碳;(2)采用高硫煤或人造高硫煤造气以提高煤气中的硫化氢含量;(3)固体硫化剂(我所发明专利)硫化,固体硫化剂在煤气的作用下产生硫化氢。
一氧化碳变换技术交流

℃
• 但实际上完全按最适宜温度曲线操作是不可能的,因 为在反应开始时,最适宜温度最高(以中温变换为例, 要达到620℃以上),大大超过催化剂的耐热温度, 而且热量的来源是个问题。随着反应的进行,要不断 地、准确地按照最适宜温度的需要移出反应热是极为 困难的,见二 段CO变换的T-x图。 图中: CD即为最适宜温度曲线,AB为平衡曲线,EF线为第 一段绝热反应线,FG线表示段间间接换热降温过程。 GH线表示第二段绝热反应线。。 • 变换过程的温度应综合各个方面因素来确定,主要原 则是: • 1)、反应开始温度应高于催化剂活性温度10~20℃ 左右。另外必须要高于气体露点温度20℃以上(防止 原料气析水,一是使催化剂粉碎结块,二是腐蚀设 备)。
CS2+4H2 2H2S+CH4+246 kJ∕mol MoO3+2H2S+H2 MoS2+3H2O+48.1 kJ∕mol CoO+H2S CoS+H2O+13.4 kJ∕mol • 升温硫化一般采用循环硫化法,升温硫化阶段所需要的热 量主要靠电加热器提供。 • 3)国内外Co-Mo系耐硫变换催化剂的发展历程 • ⑴1969年德国BASF公司开发成功的K8-11耐硫变换催化 剂(镁铝尖晶石复合材料为载体),1978年首次实现工业 化的应用,用于重油部分氧化法制合成气流程和加压煤气 化制合成氨流程的CO变换。它的主要特点是以镁铝尖晶 石为载体,硫化后活性高,耐高水蒸汽分压,可在高压下使用, 抗毒物能力强,能再生,平均寿命 3~5年。
• 由于变换反应是放热反应,降低温度有利于平衡 向右移动,因此平衡常数随温度的降低而增大。 例如:250℃时为86.51,450℃时为:7.311。 • 在工业生产中,受催化剂装填量、设备投资的经 济效益等因素影响,反应不可能也没必要达到平 衡,只能尽可能接近平衡。 • 实际生产的流程组合中,一般利用高温段之后再 进行低温变换,就是为了提高反应平衡常数,从 而提高变换率,降低变换气CO含量。
甲醇原料气中一氧化碳的变换—变换工艺条件的选择
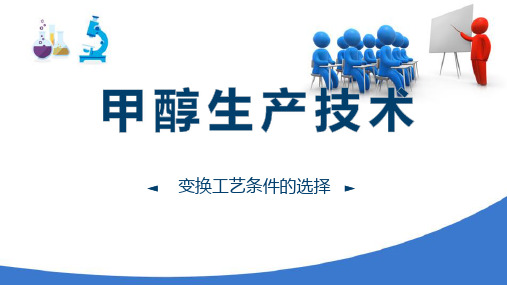
二、压力
压力对变换反应的平衡几乎没有影响,但加压可 提高反应速度和催化剂的生产能力,可采用较大的空 间速度,使设备紧凑,有利于过热蒸汽回收。由于干 原料气的物质的量小于干变换气物质的量,所以,先 压缩原料气进行加压变换的能耗,比常压变换后再压 缩变换气的能耗低15~30%,但加压变换需用压力较 高蒸汽,对设备材质要求高,所以一般小型合成氨厂 操作压力为0.8~1.2 MPa,中型厂为1.2~1.8MPa、 大型厂为3.0~8.0 MPa 。
✓ 如果进入中低变系统原料气中氧含量高,会引起催化剂活性组分与氧反 应,导致催化剂层的剧烈温升。同时,活性组分不同程度硫酸盐化造成 催化剂活性下降,所以各种变换催化剂入口气体中氧含量应小于0.5%。
三、汽气比
增加水蒸汽量,有利于提高CO的平衡变换率,降低CO残余含量, 加快反应速率,为此生产上均采用过量水蒸气。
• 过量水蒸汽的存在,抑制了析碳及甲烷化的副反应发生,保证了催化 剂活性组分Fe3O4的稳定而不被过渡还原,同时还起到载热体的作用, 使催化剂床层温升减小。所以,改变水蒸汽用量是调节床层温度的有 效手段。
五、出口气体中CO含量
✓ 小型氨厂中低变串联工艺指标是中变三段出口6%~8%,低变炉出口约 1.5%,以减轻原料气精制负荷;全低变工艺流程工艺指标是 一变炉出 口4%~7%,二变炉出口0.7%~1.5%,系统温度降低,出口一氧化碳 含量降低。总之,出口气体中一氧化碳含量应与后工序联合考虑。
六、入口气体中氧含量
变换工艺条件的选择
一、温度
变换反应存在最适宜温度
• 如果整个反应过程按最适宜温度曲线进行,则反应速率最大,在相同 的生产能力下所需催化剂用量最小,但实际生产完全按最适宜温度曲 线操作是不现实的。首先,反应开始时,最适宜温度很高,已超过了 中温变换催化剂允许使用的温度范围。其次,随着反应进行,要不断 移出反应热,使最适宜温度逐渐降低是极困难的。因此,变换过程的 操作温度应综合各方面因素来确定。
一氧化碳低温变换工艺及应用综述

国内外高职院校招生制度对比研究2014年9月国务院发布《关于深化考试招生制度改革的实施意见》,其中指出,到2020年,基本建立中国特色的现代教育考试招生制度,形成分类考试、综合评价、多元录取的考试招生模式。
这一意见的提出,将招生考试改革又一次推到了大众面前,引发了广泛的讨论。
与此同时,美国、德国、加拿大等发达国家的招生制度也在不断地发展和完善,我们在思考自身的同时,也可以比较各国的招生制度,通过分析研究促进我国教育招生制度的改革。
标签:高职院校;招生制度改革;国内外对比高校招生制度改革一直是一个热门话题,高校招生制度的优劣直接影响了整个教育体系,高职院校作为高校的一部分,在招生制度的改革中也起着举足轻重的作用。
近年来,高职院校的招生制度随着我国高考制度的改革也一直在调整着,无论从招生方式、考试内容还是管理办法方面,都进行了很大的改革。
一、我国高职院校招生制度的改革及现行招生制度1.我国招生制度的历史沿革我国古代选拔人才的方式可以追溯到秦朝以前的“世卿世禄”制度,直到隋唐年间,随着改革的深入,形成了比较完善的科举制,科举制又经过历次改革,一直沿用到清朝灭亡,但是这些制度主要都是古代为统治者选拔人才服务的,古代的学校数量稀少,学生大都是家境宽裕以及有一定文化程度的,这也体现了当时考试制度的缺失。
直到新中国成立后,我国才逐步建立起了全国统一的招生制度,虽然有一定的弊端,但是当时国家亟须人才,统一的招生考试的确在一定时间内为国家解决了一部分困难。
后来由于“文化大革命”影响,高考制度暂停了一段时间,直到1976年才正式恢复,恢复后的高校仍然主要是通过高考的形式选拔学生,但是高考的内容一直有小的变动,比如英语课程的加入等。
到了21世纪,随着学校数量的增多,考生生源的扩大,不同省份学校、生源的差异越来越明显,部分省份对高考试卷采用自主命题的方式,其他省份还是沿用全国高考卷。
2003年,教育部开始推行自主招生,结束了此前高校只能在每年同一时间通过高考选拔学生的历史,这次改革可以说是比较大的改变,也有很深远的影响。
一氧化碳变换
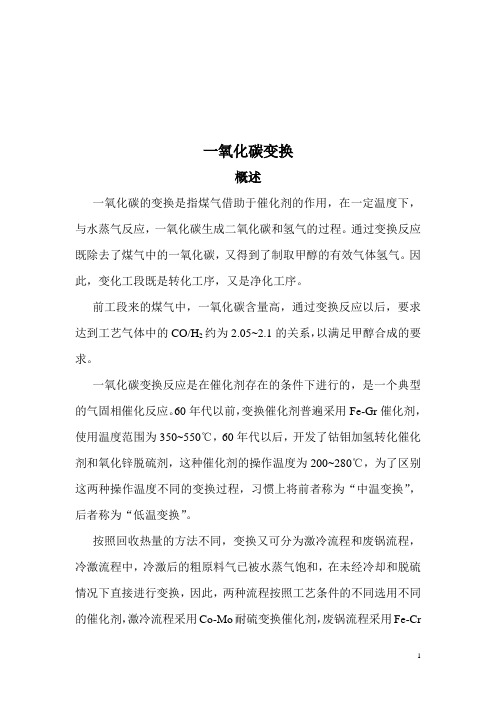
一氧化碳变换概述一氧化碳的变换是指煤气借助于催化剂的作用,在一定温度下,与水蒸气反应,一氧化碳生成二氧化碳和氢气的过程。
通过变换反应既除去了煤气中的一氧化碳,又得到了制取甲醇的有效气体氢气。
因此,变化工段既是转化工序,又是净化工序。
前工段来的煤气中,一氧化碳含量高,通过变换反应以后,要求达到工艺气体中的CO/H2约为2.05~2.1的关系,以满足甲醇合成的要求。
一氧化碳变换反应是在催化剂存在的条件下进行的,是一个典型的气固相催化反应。
60年代以前,变换催化剂普遍采用Fe-Gr催化剂,使用温度范围为350~550℃,60年代以后,开发了钴钼加氢转化催化剂和氧化锌脱硫剂,这种催化剂的操作温度为200~280℃,为了区别这两种操作温度不同的变换过程,习惯上将前者称为“中温变换”,后者称为“低温变换”。
按照回收热量的方法不同,变换又可分为激冷流程和废锅流程,冷激流程中,冷激后的粗原料气已被水蒸气饱和,在未经冷却和脱硫情况下直接进行变换,因此,两种流程按照工艺条件的不同选用不同的催化剂,激冷流程采用Co-Mo耐硫变换催化剂,废锅流程采用Fe-Cr变换催化剂。
第一节变换反应原理变换过程为含有C、H、O三种元素的CO和H2O共存的系统,在CO变换的催化反应过程中,除了主要反应CO+H2O=CO2+H2以外,在某种条件下会发生CO分解等其他副反应,分别如下:2CO=C+CO22CO+2H2=CH4+CO2CO+3H2=CH4+H2OCO2+4H2=CH4+2H2O这些副反应都消耗了原料气中的有效气体,生成有害的游离碳及无用的甲烷,避免副反应的最好方法就是使用选择性好的变换催化剂。
一、变换反应的热效应一氧化碳变换反应是一个放热反应,CO+H2O=CO2+H2+41kJ/gmol反应的热效应视H2O的状态而定,若为液态水,则是微吸热反应,若是水蒸气,则为放热反应。
变换反应的反应热随温度的升高而降低,具体反应热列表如下:表1 CO+H2O=CO2+H2的反应热温度℃25 200 250 300 350 400 450 500 550 △HkJ/gmol 41 39.8 39.5 39 38.5 38 37.6 37 36.6压力对变换反应的反应热影响较小,一般不做考虑。
- 1、下载文档前请自行甄别文档内容的完整性,平台不提供额外的编辑、内容补充、找答案等附加服务。
- 2、"仅部分预览"的文档,不可在线预览部分如存在完整性等问题,可反馈申请退款(可完整预览的文档不适用该条件!)。
- 3、如文档侵犯您的权益,请联系客服反馈,我们会尽快为您处理(人工客服工作时间:9:00-18:30)。
谈一氧化碳变换工艺条件的选择
摘要:本文根据作者多年工作经验,从中温变换工艺条件、低温变换工艺条件和耐硫低温变换工艺条件三个方面探讨了一氧化碳
变换工艺条件的选择,希望能够对同仁提供帮助。
关键词:化工;一氧化碳变换;工艺条件;选择
1 中温变换工艺条件
1.1 温度
变换反应存在最适宜温度,如果变换反应在最适宜的温度条件下进行,那么它的反应速率将会是最大的,所需要催化剂的用量也会相应的最小,但是在实际的生产过程中完全按照最适温度进行时不现实的。
变换过程的操作温度应综合各方面因素来确定。
其主要原则如下。
(1)在活性温度范围内操作,变换反应发生时的温度一定要满足催化剂活性温度的要求。
开始反应时的温度要比催化剂起始活性的温度高20℃,不同的催化剂开始反应的温度为32℃~38℃,热点温度为45℃~50℃。
(2)尽可能接近最适宜温度曲线进行反应,根据原料气中co的含量,将催化剂分为一段、二段或多段,段间进行冷却。
主要是采用中间间接换热式(用原料气或蒸汽间接换热)或中间直接冷激式(即在段间加入冷激水、水蒸气、冷煤气降温)的冷却方式来降低反应系统的温度,使变换过程操作线接近最适宜温度曲线。
几种冷却方式混合使用,尽可能不用煤气冷激和蒸汽冷激,是用喷水冷激,以利于降低蒸汽的消耗。
一些较新的设计中,
喷水冷却方式已被废热锅炉所取代,这样可以获得高压或低压蒸汽供氨厂其他用途。
1.2 压力
变换反应的平衡中压力的影响微乎其微,但是压力大可以加快反应速度。
让设备变得更加紧凑,这样方便于过热蒸汽的回收利用。
因为干变换气物质的量大于干原料气的物质的量,所以,常压变换后压缩变换气的能耗比压缩原料气进行加压变换的能耗高15%~30%,但是加压变换时我们需用压力比较高的蒸汽,相应的对设备的材质要求更高。
所以,小型合成氨厂的操作压力一般为0.8~1.2mpa,中型厂为1.2~1.8mpa、大型厂为 3.0~8.0mpa。
1.3 汽压比
水蒸气的量增加了,就会有助于提高co的平衡变换率,并且能够降低co残余的含量,使反应的速率增大,所以在实际生产中所采用的水蒸气都是过量的。
水蒸气过量还能抑制析炭和甲烷化等其它反应的发生,能够维护催化剂活性的稳定,还能够起到载热体的作用,减小催化剂床的层温。
水蒸气用量的多少可以对床层温度进行很好的调节。
在变换过程中最主要的消耗就是水蒸气的用量,为了降低能耗,在工业的生产过程中应当在满足变换工艺要求的前提下,尽可能的减少水蒸气的消耗。
中温变换操作适宜的汽压比为h2o/co=1.5~3,经中温变换后气体中h2o/co可达15以上,不必再加蒸汽即可直接进行低温变换。
2 低温变换工艺条件
2.1 温度
低温变换操作温度必须较该条件下的露点温度高30摄氏度,一般控制在180~260摄氏度。
2.2 压力和空间速率
低温变换操作压力一般是随中温变换而定,一般为1~3mpa,空间速率则随压力升高而增大,当压力为2mpa左右时,空间速率为1000~1500h-1,压力在3mpa左右时,空间速率则增大到2500h-1左右。
2.3 入口气体中co含量
低温变换催化剂虽然活性高,但操作温度范围窄,对热敏感,价格高。
低温变换入口气体中co含量一般为3%~6%。
3 耐硫低温变换工艺条件
3.1 温度
耐硫低温变换是在低温的情况下,根据催化剂在低温情况下的活性,把变换气体中co的含量降到1%以下。
为了保证低变出口co的变换率,催化剂须分段。
耐硫低温度变换操作一般入口温度为180~220℃,热点温度为330~400摄氏度,并且随着催化剂使用时间延长,催化剂活性降低,操作温度应适当提高。
3.2 压力和空间速率
一般情况下,应当根据进入低变系统的原料气压力来决定耐硫低温变换的压力,一般为0.8~3mpa。
空间速率与催化剂的型号和压力相关,不同型号的催化剂确定不同的空速,且空速随压力上升而
增大。
低变催化剂空速一般控制在1000~2000h-1,b303q低变催化剂用于全低变流程,其空速可控制在2500h-1。
3.3 入口气体中氧含量
如果进入低变系统原料气中氧含量高,会引起耐硫低变催化剂床层温度上涨,活性组分不同程度硫酸盐化造成催化剂活性下降,所以耐硫低温变换入口气体中氧含量应小于0.5%。
3.4 半水煤气中硫化氢含量
在co变换过程中,如果半水煤气中h2s含量高,耐硫低温催化剂中的钴和钼以硫化物形式存在,催化剂维持高活性。
当反应温度高,汽压比大而气体中h2s含量不足时,易使低变催化剂出现反硫化现象,造成催化剂失活。
所以半水煤气中应维持一定的h2s含量,为避免h2s含量过高使变换系统腐蚀加剧和增加后工段二次脱硫的压力,全低变流程一般控制h2s含量150mg/m3(标)左右,而中低低流程由于中变催化剂不耐硫,半水煤气中的h2s含量为100mg/m3(标)左右,中串低流程的hzs含量为50mg/m3(标)左右。
4 结语
一氧化碳变换工艺条件的选择应根据不同生产环境和流程进行
合理选择,在操作过程中注意能耗的降低和产品质量把关。
参考文献
[1] 李练昆.合成氨装置一氧化碳变换单元技术改进分析[j].大氮肥. 2011(02)。