一氧化碳变换的主要设备及操作控制
小型氨厂一氧化碳多段变换流程叙述
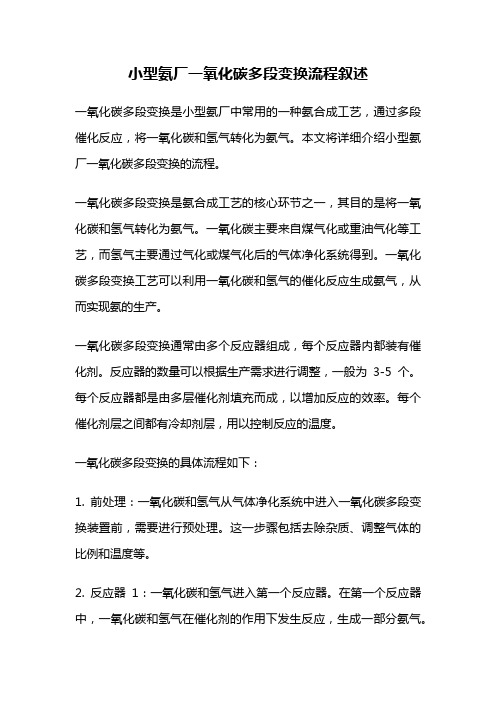
小型氨厂一氧化碳多段变换流程叙述一氧化碳多段变换是小型氨厂中常用的一种氨合成工艺,通过多段催化反应,将一氧化碳和氢气转化为氨气。
本文将详细介绍小型氨厂一氧化碳多段变换的流程。
一氧化碳多段变换是氨合成工艺的核心环节之一,其目的是将一氧化碳和氢气转化为氨气。
一氧化碳主要来自煤气化或重油气化等工艺,而氢气主要通过气化或煤气化后的气体净化系统得到。
一氧化碳多段变换工艺可以利用一氧化碳和氢气的催化反应生成氨气,从而实现氨的生产。
一氧化碳多段变换通常由多个反应器组成,每个反应器内都装有催化剂。
反应器的数量可以根据生产需求进行调整,一般为3-5个。
每个反应器都是由多层催化剂填充而成,以增加反应的效率。
每个催化剂层之间都有冷却剂层,用以控制反应的温度。
一氧化碳多段变换的具体流程如下:1. 前处理:一氧化碳和氢气从气体净化系统中进入一氧化碳多段变换装置前,需要进行预处理。
这一步骤包括去除杂质、调整气体的比例和温度等。
2. 反应器1:一氧化碳和氢气进入第一个反应器。
在第一个反应器中,一氧化碳和氢气在催化剂的作用下发生反应,生成一部分氨气。
3. 中间处理:从第一个反应器出来的气体需要经过中间处理,主要是降低温度和去除反应产生的副产物。
4. 反应器2:经过中间处理的气体进入第二个反应器。
在第二个反应器中,剩余的一氧化碳和氢气继续反应,生成更多的氨气。
5. 中间处理:从第二个反应器出来的气体同样需要经过中间处理,以进一步降低温度和去除副产物。
6. 反应器3:经过中间处理的气体进入第三个反应器。
在第三个反应器中,剩余的一氧化碳和氢气再次反应,生成更多的氨气。
7. 末端处理:从第三个反应器出来的气体需要经过末端处理,主要是降低温度、去除副产物和分离氨气。
通过以上的多段反应和中间处理,一氧化碳和氢气可以充分反应,生成大量的氨气。
整个一氧化碳多段变换的流程需要严格控制反应温度、催化剂的选择和催化剂层之间的冷却剂流动,以确保反应的高效进行。
一氧化碳的变换

一氧化碳变换时半水煤气借助于催化剂的作用,在一定温度下,水蒸气反应,生成二氧化碳和氢的工艺过程。
通过变换即除去了一氧化碳,又得到了合成氨的原料气氢和氨加工的原料气二氧化碳。
近年来,变换工段由于采用了低温高活性的催化剂和高串低,高-低-低(俗称“中串低”、“中-低-低”),全低变等多种新工艺流程,加强了热量回收利用,工段面貌发生了很大变化。
1、一氧化碳变换反应的基本原理时什么?其反应的特点时怎么样的?一氧化碳变换反应是在一定条件下,半水煤气中的一氧化碳和水蒸气反应生成氢气和二氧化塔的工艺过程。
CO + H2O <==> CO2 +H2+41kj/mol这是一个可逆放热反应,从化学平衡来看,降低反应温度,增加水蒸气用量,有利于上述可逆反应向二氧化碳和氢气的方向移动,提高平衡变换率。
但是水蒸气增加到一定值后,变换率增加幅度会变小。
温度对变化反应的速度影响较大,而且对正逆反应速度的影响不一样。
温度升高,放热反应即上述变换反应速度增加的慢,逆反应(吸热反应)速度增加得快。
因此,当变换反应开始时,反应物浓度大,提高温度,可加快变换反应,在反应的后一段,二氧化碳和氢的浓度增加,逆反应速度加快,因此,需降低反应温度,使逆反应速度减慢,这样可得到较高的变换率。
提高变化压力,分子间的有效碰撞次数,可以加快变换反应速度,提高催化剂的生产能力。
2“高串低”工艺与传统的高温变换工艺主要有什么不同?有何优点?传统的高温变换工艺,变换炉入口温度一般控制在320~340℃。
在流程设置上一般是一个变换炉,炉内装填铁-铬系催化剂,分两段或三段,半水煤气从上到下一次通过各段催化此后即完成变换过程。
“高串低”工艺与创痛的高温变换工艺主要不同之处是在原高变炉之后,又串联了一个装有钴-钼系列耐硫宽温催化剂的低变炉,形成高变串低变的工艺流程。
耐硫宽温变换催化剂在“高串低”工艺中被利用做低变催化剂。
低变炉入口气体温度一般可控制在210~230℃。
一氧化碳的变换
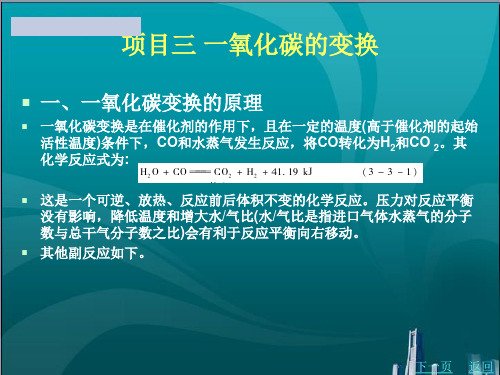
项目三 一氧化碳的变换
③催化剂要有一定的抗毒能力,也就是能耐气体中含有的少量有毒气体。 ④催化剂的机械性能要好,以免在使用中破碎或粉碎,增加变换阻力。 ⑤催化剂有一定的热稳定性,在一定温度范围内,不致因反应后温度升
高而损坏催化剂。 ⑥催化剂要防止发生副反应,主要是一氧化碳分解析碳和生成甲烷的反
综上所述,影响变换反应的因素有以下几种。 1.压力 如前所述,压力对变换反应的平衡几乎无影响,但加压变换有以下优点。 ①可加快反应速度和提高催化剂的生产能力,从而可采用较大空速提高
生产强度。
上一页 下一页 返回
项目三 一氧化碳的变换
②设备体积小,布置紧凑,投资较少。 ③湿变换气中水蒸气冷凝温度高,有利于热能的回收利用。 但提高压力会使系统冷凝液酸度增大,使析炭和生成甲烷等副反应易于
上一页 下一页 返回
项目三 一氧化碳的变换
反应温度按最佳温度进行可使催化剂用量最少,但要控制反应温度严格 按照最佳温度曲线进行在目前是不现实和难于达到的。目前在工业上是 通过特催化剂床层分段来达到使反应温度靠近最佳温度进行。但对于低 温变换过程,由于温升很小,催化剂不必分段。
3.汽气比 CO变换的汽气比一般是指H2O/CO比值或水蒸气/干原料气的比值(摩尔
一、一氧化碳Leabharlann 换的原理一氧化碳变换是在催化剂的作用下,且在一定的温度(高于催化剂的起始 活性温度)条件下,CO和水蒸气发生反应,将CO转化为H2和CO 2。其 化学反应式为:
这是一个可逆、放热、反应前后体积不变的化学反应。压力对反应平衡 没有影响,降低温度和增大水/气比(水/气比是指进口气体水蒸气的分子 数与总干气分子数之比)会有利于反应平衡向右移动。
其他副反应如下。
一氧化碳变换反应实验报告思考题目
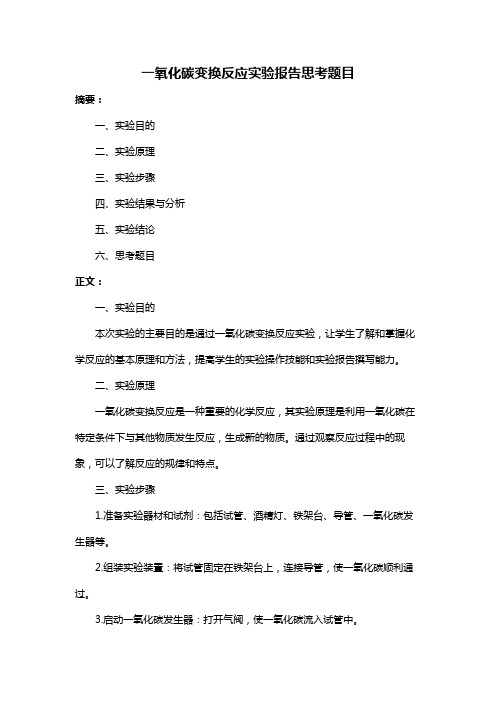
一氧化碳变换反应实验报告思考题目摘要:一、实验目的二、实验原理三、实验步骤四、实验结果与分析五、实验结论六、思考题目正文:一、实验目的本次实验的主要目的是通过一氧化碳变换反应实验,让学生了解和掌握化学反应的基本原理和方法,提高学生的实验操作技能和实验报告撰写能力。
二、实验原理一氧化碳变换反应是一种重要的化学反应,其实验原理是利用一氧化碳在特定条件下与其他物质发生反应,生成新的物质。
通过观察反应过程中的现象,可以了解反应的规律和特点。
三、实验步骤1.准备实验器材和试剂:包括试管、酒精灯、铁架台、导管、一氧化碳发生器等。
2.组装实验装置:将试管固定在铁架台上,连接导管,使一氧化碳顺利通过。
3.启动一氧化碳发生器:打开气阀,使一氧化碳流入试管中。
4.观察实验现象:在一氧化碳的作用下,试剂发生反应,观察反应过程中的现象。
5.记录实验数据:记录实验过程中各个阶段的现象和数据。
6.实验结束:关闭气阀,整理实验器材。
四、实验结果与分析实验结果显示,在特定条件下,一氧化碳与其他物质发生反应,生成了新的物质。
通过对实验数据的分析,可以得出反应的规律和特点。
五、实验结论通过本次实验,学生可以了解一氧化碳变换反应的原理和方法,掌握实验操作技能,提高实验报告撰写能力。
同时,本次实验也有助于培养学生的观察力、思维能力和实验能力。
六、思考题目在实验过程中,学生可以思考以下问题:1.一氧化碳变换反应的原理是什么?2.实验中观察到了哪些现象?这些现象说明了什么?3.如何根据实验数据分析反应的规律和特点?4.如何撰写一份完整的实验报告?。
一氧化碳的变换技术62.
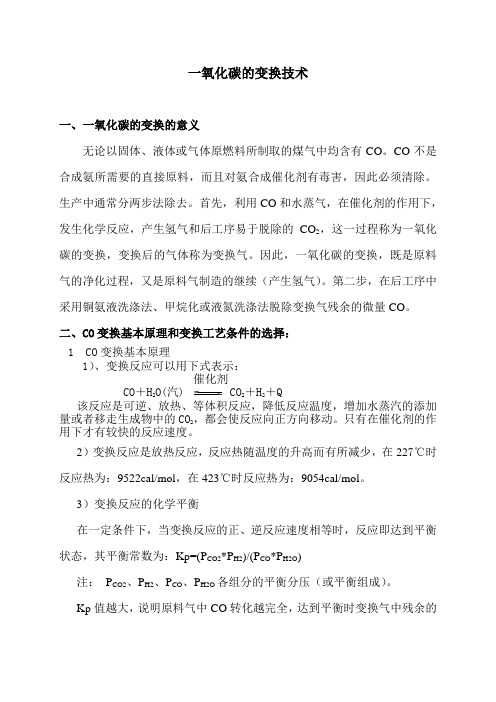
一氧化碳的变换技术一、一氧化碳的变换的意义无论以固体、液体或气体原燃料所制取的煤气中均含有CO 。
CO 不是合成氨所需要的直接原料,而且对氨合成催化剂有毒害,因此必须清除。
生产中通常分两步法除去。
首先,利用CO 和水蒸气,在催化剂的作用下,发生化学反应,产生氢气和后工序易于脱除的CO 2,这一过程称为一氧化碳的变换,变换后的气体称为变换气。
因此,一氧化碳的变换,既是原料气的净化过程,又是原料气制造的继续(产生氢气)。
第二步,在后工序中采用铜氨液洗涤法、甲烷化或液氮洗涤法脱除变换气残余的微量CO 。
二、CO 变换基本原理和变换工艺条件的选择:1 CO 变换基本原理1)、变换反应可以用下式表示:催化剂CO +H2O(汽2+H 2+Q该反应是可逆、放热、等体积反应,降低反应温度,增加水蒸汽的添加量或者移走生成物中的CO 2,都会使反应向正方向移动。
只有在催化剂的作用下才有较快的反应速度。
2)变换反应是放热反应,反应热随温度的升高而有所减少,在227℃时反应热为:9522cal/mol ,在423℃时反应热为:9054cal/mol 。
3)变换反应的化学平衡在一定条件下,当变换反应的正、逆反应速度相等时,反应即达到平衡状态,其平衡常数为:Kp=(P CO2*P H2)/(P CO *P H2O )注: P CO2、P H2、P CO 、P H2O 各组分的平衡分压(或平衡组成)。
Kp 值越大,说明原料气中CO 转化越完全,达到平衡时变换气中残余的CO含量越少。
由于变换反应是放热反应,降低温度有利于平衡向右移动,因此平衡常数随温度的降低而增大。
250℃时为86.51,450℃时为:7.311。
在工业生产中,受催化剂装填量、设备投资的经济效益等因素影响,反应不可能也没必要达到平衡,只能尽可能接近平衡。
实际的流程组合中,一般利用高温段之后再进行低温变换,就是为了提高反应平衡常数,从而提高变换率,降低变换气CO含量。
一氧化碳变换操作规程
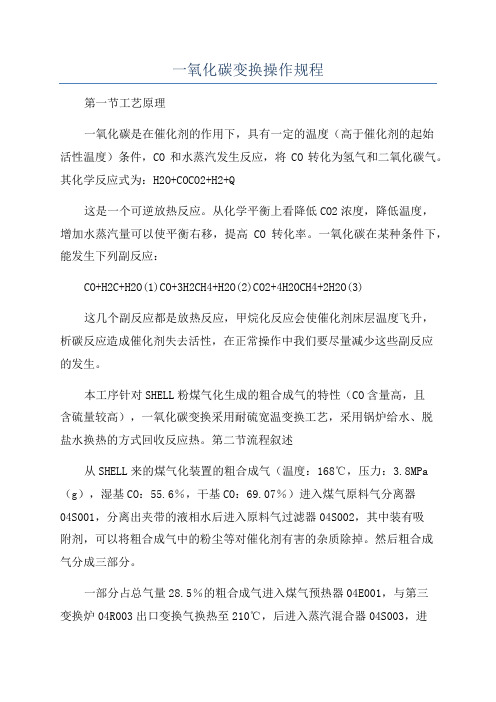
一氧化碳变换操作规程第一节工艺原理一氧化碳是在催化剂的作用下,具有一定的温度(高于催化剂的起始活性温度)条件,CO和水蒸汽发生反应,将CO转化为氢气和二氧化碳气。
其化学反应式为:H2O+COCO2+H2+Q这是一个可逆放热反应。
从化学平衡上看降低CO2浓度,降低温度,增加水蒸汽量可以使平衡右移,提高CO转化率。
一氧化碳在某种条件下,能发生下列副反应:CO+H2C+H2O(1)CO+3H2CH4+H2O(2)CO2+4H2OCH4+2H2O(3)这几个副反应都是放热反应,甲烷化反应会使催化剂床层温度飞升,析碳反应造成催化剂失去活性,在正常操作中我们要尽量减少这些副反应的发生。
本工序针对SHELL粉煤气化生成的粗合成气的特性(CO含量高,且含硫量较高),一氧化碳变换采用耐硫宽温变换工艺,采用锅炉给水、脱盐水换热的方式回收反应热。
第二节流程叙述从SHELL来的煤气化装置的粗合成气(温度:168℃,压力:3.8MPa (g),湿基CO:55.6%,干基CO:69.07%)进入煤气原料气分离器04S001,分离出夹带的液相水后进入原料气过滤器04S002,其中装有吸附剂,可以将粗合成气中的粉尘等对催化剂有害的杂质除掉。
然后粗合成气分成三部分。
一部分占总气量28.5%的粗合成气进入煤气预热器04E001,与第三变换炉04R003出口变换气换热至210℃,后进入蒸汽混合器04S003,进入该混合器前,来自蒸汽管网的过热蒸汽(4.4MPa,282℃)与粗合成气混合。
进蒸汽混合器的蒸汽量由调节阀FV-04005调节,该蒸汽量与28.5%的粗合成气量是比例控制,保证进入一变、汽、气比不低于1.09,原料气管线设有TV-04003调节阀旁路(测温点TE-04003在一变的入口。
混合后的粗合成气进入煤气换热器04E002管侧与来自第一变换炉04R001出口的变换气换热。
合成气温度由TV-04003控制在约255℃左右,进入第一变换炉04R001进行变换反应(一变入口湿基CO:33.1%)。
变换工段操作规程

变换工段操作规程一、工艺概述经过脱硫、除尘后的水煤气中,除含有双氧水生产时所需要的氢气外,还含有26~30%的一氧化碳及其它气体。
直接分离一氧化碳是比较困难的,但在一定的温度条件下,借助低变催化剂的催化作用,可使水煤气中一氧化碳与水蒸汽发生反应,生成二氧化碳和氢气。
二、化学反应原理变换的主要反应是在一定的温度条件下,气体中的一氧化碳与水蒸汽反应生成氢气和二氧化碳,反应方程式如下:CO+H 2O (g 2+H 2+41KJ/mol这个反应的特点是:(1)反应前后体积没有变化;(2)反应前后是放热的;(3)是完全可逆的反应,当正反两个方面进行的速度相等时,反应达到平衡。
1、影响化学平衡的因素(1)温度的影响,变换反应是放热反应,温度降低、平衡向生成氢气和二氧化碳的方面移动。
(2)反应物浓度的影响,增加反应物浓度或减少生成物浓度,反应向有利于生成二氧化碳和氢气的方向进行,可采用增加蒸汽量来实现。
2、影响反应速度的因素,变换反应在有催化剂存在时,才能大大加快反应 速度,另外提高温度和增加蒸汽用量对加快变换反应的速度也有很大作用。
三、工艺流程1、水煤气气体流程:压缩机 → 冷却器 → 除油器 → 热交换器 → 电加热器 → 变换炉一 、二段 → 变换炉三段 → 热交换器 →冷却器 →气水分离器 → 精脱硫塔(A ) →精脱硫塔(B ) → PSA 提氢装置。
2、软化水流程:由电厂送的软化水 →加压水泵 →变换炉二、三段。
3、蒸汽流程:由电厂送的蒸汽 →汽水分离器 → 电加热器 →变换炉一段。
4、循环水流程:凉水泵→冷却器→热水池→热水泵→冷却塔→凉水池→凉水泵。
四、主要设备及性能1、水煤气压缩机:L—40/0.2—8型往复式压缩机,Q:40m3/min,N:280KW,压缩机的任务是把水煤气输送到后工段,并提供过程进行所必要的压力条件。
2、变换炉φ1600×7000,变换一段上层装填抗氧剂和抗毒剂,变换二、三段上层均装填耐火球,下部装填低变催化剂,是完成一氧化碳和水蒸汽反应生成二氧化碳和氢气的主要设备。
一氧化碳变换工艺流程及设备
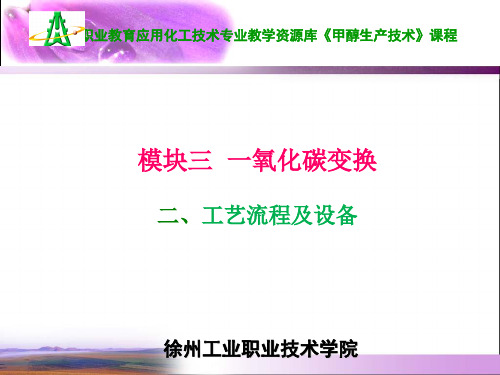
脱硫剂
ZnO+H2S = ZnS+H2O
主要活性物质:ZnO 载体:Al2O3 促进剂:铜、钼、锰的氧化物生
不可再生,送往锌冶炼厂回收
职业教育应用化工技术专业教学资源库《甲醇生产技术》课程
模块三 一氧化碳变换
二、工艺流程及设备
徐州工业职业技术学院
第二节 一氧化碳变换工艺流程及设备
一、一氧化碳变换工艺流程
二、一氧化碳变换主要设备
1.变换炉
2.热交换器
3.变换气水冷器
4.余热回收器
三、氧化锌法
原理
转化吸收式脱硫——有机硫化物在氧化锌催化作用下与氢 发生转化反应,转化为硫化氢,然后被氧化锌吸收
- 1、下载文档前请自行甄别文档内容的完整性,平台不提供额外的编辑、内容补充、找答案等附加服务。
- 2、"仅部分预览"的文档,不可在线预览部分如存在完整性等问题,可反馈申请退款(可完整预览的文档不适用该条件!)。
- 3、如文档侵犯您的权益,请联系客服反馈,我们会尽快为您处理(人工客服工作时间:9:00-18:30)。
一氧化碳变换的主要设备及操作控制
摘要:本文根据作者自己的工作经验,结合实际,对一氧化碳变换的知识进行阐述,并探讨了一氧化碳变换的主要设备和变换过程中的操作要点。
关键词:化工;一氧化碳变换;设备;操作要点
1.一氧化碳变换的主要设备
1.1变换炉
变换炉随工艺流程不同而异,但都应满足以下要求:变换炉的处理气量尽可能大;气流阻力小;气流在炉内分布均匀;热损失小,温度易控制;结构简单,便于制造和维修,并能实现最适宜温度的分布。
变换炉主要有绝热型和冷管型,最广泛的是绝热型。
现介绍生产中常用的两种不同结构的绝热型变换炉。
(1)中间间接冷却式变换炉
中间间接冷却式变换炉结构的外壳是由钢板制成的圆筒体,内壁砌有耐混凝土衬里,再砌一层硅薄土砖和一层轻质黏土砖,以降低炉壁温度和防止热损失。
内用钢板隔成上、下两段,每层催化剂靠支架支撑,支架上铺篦子板,钢丝网及耐火球,上部再装一层耐火球。
为了测量炉内各处温度,炉壁多处装有热电偶,炉体上还配置了入孔与装卸催化剂口。
(2)轴径向变换炉
半水煤气和蒸汽由进气口进入,经过分布器后,70%的气体从壳体外集气器进入,径向通过催化剂,30%气体从底部轴向进入催化剂层,两股气体反应后一起进入中心内集气器而出反应器,底部用Al2 O3球并用钢丝网固定。
外集气器上开孔面积为0.5%,气流速率为6. 7m/s,中心内集气器开孔面积为1.5%,气流速率为22m/ s,大大高于传统轴向线速0. 5m/s。
因此,要求使用强度较高的小颗粒催化剂。
轴径向变换炉的优点是催化剂床层阻力小,催化剂不易烧结失活,是目前广泛推广的一项新技术。
1.2饱和热水塔
饱和塔的作用是提高原料气的温度,增加其水蒸气含量,以节省补充蒸汽量。
热水塔的作用主要是回收变换气中的蒸汽和湿热,提高热水温度,以供饱和塔使用。
工业上将饱和塔和热水塔组成一套装置的目的是使上塔底部的热水可自动流入下塔,省去一台热水泵。
目前饱和塔用新型垂直筛板塔,可提高传质效率20%左右,气体处理量可提高50%以上,具有低压降,抗结垢抗堵塞能力强的特点。
2.操作控制要点
2.1变换炉的操作
(1)催化剂的填装、升温与还原
催化剂装填的好与坏,对于降低床层阻力、提高变换率、延长催化剂使用寿命有直接影响。
装填前,应先把催化剂过筛,除去运输中产生的粉尘碎粒,使颗粒均匀,以减少生产时的阻力,并在炉内标记出催化剂要装填的高度,在炉篦上铺好钢丝网和耐火球,然后自上而下分层进行装填。
装填人员进炉时,严禁踩踏催化剂,可站在临时木板上操作,装好后,用木板将表面刮平,再覆盖上一层铁丝网和耐火球,然后封上入孔和变换炉顶盖。
(2)正常操作
①中温变换的正常操作。
中温变换的正常操作主要是将催化剂床层温度控制在适宜的范围内,以便充分发挥催化剂的活性,提高设备的生产能力和一氧化碳的变换率,同时尽量降低水蒸气消耗。
在控制炉温时,必须细心观察催化剂床层温度变化,正确分析原因,精心调节,注意参照“灵敏点”预见炉温的变化趋势,及时采取调节措施,使床层温度波动控制在指标范围内。
②低温变换的正常操作。
低温变换的正常操作主要是将温度控制在适宜的范围内,防止催化剂中毒和出现冷凝液。
低温变换催化剂的正常使用温度是180 ~260℃。
使用初期,在满足工艺指标的前提下,应尽量降低操作温度,但不得低于露点温度。
使用后期可适当提高操作温度,幅度以每次5℃为宜。
催化剂床层温度主要靠入口气体温度来调节,应根据床层温度及时调节原料气温度。
由于低温变换催化剂对温度很敏感,应避免发生超温和温度剧烈波动的情况。
原料气中一氧化碳含量一般控制在3%~6%,当其增加时,反应热增加,温度上升,这时应及时调节蒸汽添加量,以保证床层温度稳定和出口一氧化碳含量符合要求。
2.2饱和塔和热水塔的操作
(1)填瓷环
饱和塔和热水塔的瓷环分别进行安装,先将瓷环洗净。
在篦子板上铺一层铁丝网,在网上整齐排列十层较大的瓷环,然后向塔内加水。
加水前在热水塔气体进口上插盲板,并关闭相关阀门,以免将水灌入变换炉内。
当水加至入孔处时,用斜槽把瓷环滑入塔内。
装瓷环时要轻拿轻放,以防瓷环破碎,装填到规定高度时,要将塔内水面上漂浮的杂物捞出,把水放净,将瓷环扒平,抽掉盲板,封好入空。
(2)饱和塔和热水塔的操作
饱和塔和热水塔的操作主要是控制适宜热水循环量,提高饱和塔出口气体温度,稳定两个塔的正常液位。
①饱和塔出口气体温度控制。
变换工序的主要消耗定额是蒸汽消耗量,它指的是从系统外补加的蒸汽,蒸汽消耗量等于变换炉入口湿半水煤气中的蒸汽量与饱和塔出口气体中蒸汽量之差。
饱和塔出口气体中回收蒸汽量的多少主要取决于气体温度。
饱和塔出口气体温度越高,气体中所含的水蒸气越多,消耗的外供蒸汽量就越少,所以,在生产中总是尽量提高饱和塔出口半水煤气的温度。
循环热水量是决定饱和塔出口气体温度的主要因素。
因此需控制适宜的循环热水量,以提高气体出口温度。
一般热水循环量控制在每吨氨气10~20m3水,并根据不同的变换流程选择不同的循环水量。
②饱和塔和热水塔液位控制。
饱和塔和热水塔液位过高,塔阻力增大,使气体带液。
过低,两塔容易发生串气现象,半水煤气不经过变换炉直接串入变换气中被带到后系统,还会使热水泵抽空,所以,饱和热水塔液位一般控制在液位计高度的1/2~2/3。
③水质的控制。
热水在循环使用中,各种无机盐等固体含量逐渐增加,将随半水煤气带入变换炉内,沉积在催化剂颗粒表面,降低催化剂活性。
同时,由于酸性气体溶于水,pH值下降会对设备产生腐蚀。
因此要经常从热水塔底排放一部分污水,并补充新鲜软水或脱盐水。
3.结语
一氧化碳的变换过程中,需要考虑的因素有很多,不仅仅要选择合理的设备,还要有非常好的操作技巧。
较好的考虑变换过程中的温度、湿度和各种内部条件能够提高变换的效率和设备的使用寿命。
参考文献:
[1]程桂华.合成氨.北京:化学工业出版社.1998
[2]陈劲松.一氧化碳低温变换工艺及应用.会议论文.2001。