一氧化碳低温变换
铜基一氧化碳低温变换催化剂的研究进展

为在 c .n l uZ. 系低变催 化剂 中添加 不同 的助 剂 A
可以提高催化剂某一方面 的性能 , I I 公司在其产 c 品中添加锰 以获得催化剂最佳活性及热稳定性 。 用 B0 促进 A23 23 l 载体 , 0 以及单独用 c 促 进载 o 体, 以提高 C O转化率。壳牌公 司及英 国 D S N YO 耐火材料公 司在低变 中引入 ( 或 co 来改 ) 3 e2 善低变催化剂耐氯性能 , 但未见在工业上应用 的
H KA 型 催 化 剂 其 组 成 为 CO 5 .% 、 n T- u 54 ZO
1.% 、r 31.% 、 1 3 32 。 四金 属 氧 化 16 C2 4 8 A2 .% o 02
物组成的低变催化剂物化性能与三金属氧化物组
成的低变催化剂相 比, 具有较好 的耐硫性能 , 由 但
维普资讯
20 年 2 06 月 第 2 卷第 1 9 期
S ae Ni o e o s F r l e c l t g n u e ti r r iz
土 磊 他
Vn. 9 N . J o1 2
F2 e0 b6 . 0
铜 基 一 氧化 碳低 温 变换 催 化 剂 的研 究进 展
铜的晶粒度和分散度决定 , 分 中的 A23 组 l)为催 (
化剂提供了高的机械强度和热稳 定性 , ZO的 而 n
加入是为了提高催化 剂的抗硫 、 氯和抗硅等毒 抗 低温变换催化剂是 由金属氧化物组成, 根据 其发展过程可分为双金属氧化物 、 三金属氧化物 以及四金属 氧化物…。16 93年美 国 U I 司研 C公 制成功了 C 81 1. 型双金属低温变换催化剂 , 组成 为 C O3 %、n 7 u 3 ZO6 %。美国盖法勒化学公 司生 产的组成为 C O ZO=l l 06B型低温变换 u :n :的 6
一氧化碳的变换技术62.
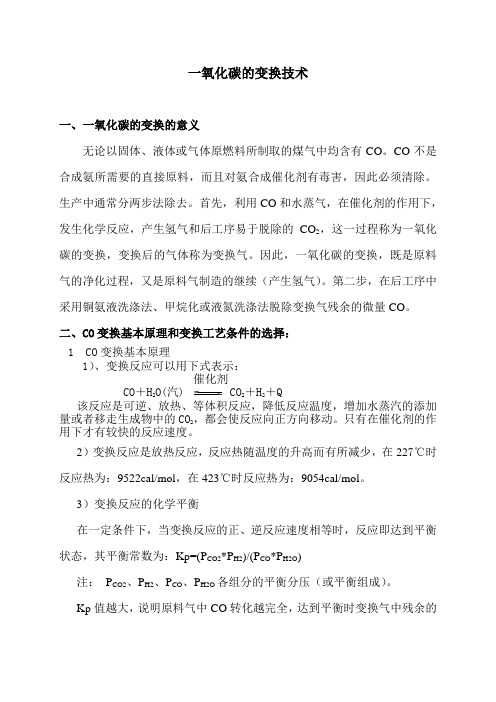
一氧化碳的变换技术一、一氧化碳的变换的意义无论以固体、液体或气体原燃料所制取的煤气中均含有CO 。
CO 不是合成氨所需要的直接原料,而且对氨合成催化剂有毒害,因此必须清除。
生产中通常分两步法除去。
首先,利用CO 和水蒸气,在催化剂的作用下,发生化学反应,产生氢气和后工序易于脱除的CO 2,这一过程称为一氧化碳的变换,变换后的气体称为变换气。
因此,一氧化碳的变换,既是原料气的净化过程,又是原料气制造的继续(产生氢气)。
第二步,在后工序中采用铜氨液洗涤法、甲烷化或液氮洗涤法脱除变换气残余的微量CO 。
二、CO 变换基本原理和变换工艺条件的选择:1 CO 变换基本原理1)、变换反应可以用下式表示:催化剂CO +H2O(汽2+H 2+Q该反应是可逆、放热、等体积反应,降低反应温度,增加水蒸汽的添加量或者移走生成物中的CO 2,都会使反应向正方向移动。
只有在催化剂的作用下才有较快的反应速度。
2)变换反应是放热反应,反应热随温度的升高而有所减少,在227℃时反应热为:9522cal/mol ,在423℃时反应热为:9054cal/mol 。
3)变换反应的化学平衡在一定条件下,当变换反应的正、逆反应速度相等时,反应即达到平衡状态,其平衡常数为:Kp=(P CO2*P H2)/(P CO *P H2O )注: P CO2、P H2、P CO 、P H2O 各组分的平衡分压(或平衡组成)。
Kp 值越大,说明原料气中CO 转化越完全,达到平衡时变换气中残余的CO含量越少。
由于变换反应是放热反应,降低温度有利于平衡向右移动,因此平衡常数随温度的降低而增大。
250℃时为86.51,450℃时为:7.311。
在工业生产中,受催化剂装填量、设备投资的经济效益等因素影响,反应不可能也没必要达到平衡,只能尽可能接近平衡。
实际的流程组合中,一般利用高温段之后再进行低温变换,就是为了提高反应平衡常数,从而提高变换率,降低变换气CO含量。
一氧化碳变换操作规程
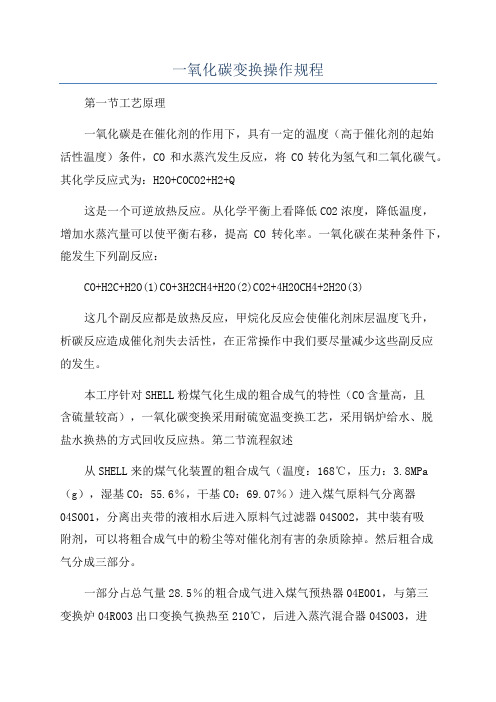
一氧化碳变换操作规程第一节工艺原理一氧化碳是在催化剂的作用下,具有一定的温度(高于催化剂的起始活性温度)条件,CO和水蒸汽发生反应,将CO转化为氢气和二氧化碳气。
其化学反应式为:H2O+COCO2+H2+Q这是一个可逆放热反应。
从化学平衡上看降低CO2浓度,降低温度,增加水蒸汽量可以使平衡右移,提高CO转化率。
一氧化碳在某种条件下,能发生下列副反应:CO+H2C+H2O(1)CO+3H2CH4+H2O(2)CO2+4H2OCH4+2H2O(3)这几个副反应都是放热反应,甲烷化反应会使催化剂床层温度飞升,析碳反应造成催化剂失去活性,在正常操作中我们要尽量减少这些副反应的发生。
本工序针对SHELL粉煤气化生成的粗合成气的特性(CO含量高,且含硫量较高),一氧化碳变换采用耐硫宽温变换工艺,采用锅炉给水、脱盐水换热的方式回收反应热。
第二节流程叙述从SHELL来的煤气化装置的粗合成气(温度:168℃,压力:3.8MPa (g),湿基CO:55.6%,干基CO:69.07%)进入煤气原料气分离器04S001,分离出夹带的液相水后进入原料气过滤器04S002,其中装有吸附剂,可以将粗合成气中的粉尘等对催化剂有害的杂质除掉。
然后粗合成气分成三部分。
一部分占总气量28.5%的粗合成气进入煤气预热器04E001,与第三变换炉04R003出口变换气换热至210℃,后进入蒸汽混合器04S003,进入该混合器前,来自蒸汽管网的过热蒸汽(4.4MPa,282℃)与粗合成气混合。
进蒸汽混合器的蒸汽量由调节阀FV-04005调节,该蒸汽量与28.5%的粗合成气量是比例控制,保证进入一变、汽、气比不低于1.09,原料气管线设有TV-04003调节阀旁路(测温点TE-04003在一变的入口。
混合后的粗合成气进入煤气换热器04E002管侧与来自第一变换炉04R001出口的变换气换热。
合成气温度由TV-04003控制在约255℃左右,进入第一变换炉04R001进行变换反应(一变入口湿基CO:33.1%)。
CO变换过程

反应条件对变换反应速率的影响 1.反应温度 T↑ ,开始k1占主导地位( k1 ↑ ),r ↑; 当T ↑继续升高到一定,k2占主导地位(k2 ↑, K ↓) ,r ↓。 当T达到Top温度下, r达到最大值。 Te:对应转化率x的平衡温度
化学工艺学
化学工艺学
TOP与气体原始组成、转化率及催化剂有关.
化学工艺学
5.5 一氧化碳变换过程
CO变换 步骤、功能和发展 5.5.1 热力学 5.5.2 催化剂 5.5.3 动力学 5.5.4 反应器 5.5.5 工艺流程
化学工艺学
1. 热效应
CO+ H2O ↔ CO2 + H2 热力学分析
H 298 (H 298 H ) ( H H ,CO2 298, H 2 298,CO 298, H 2O )
化学工艺学
5.8 CO2的脱除
CO变换反应后,CO2含量约28-30%,必须脱除。
因为:
(1)CO2是合成氨催化剂毒物
(2)太高CO2影响甲醇收率
(3)CO2可以再利用合成尿素、纯碱、NH4HCO3等
化学工艺学
采用溶液吸收法
根据吸附剂性能不同,分为物理吸收法和化学吸收法 物理吸收法:利用CO2溶解于水或有机溶剂的性质完 成。如加压水洗法、低温甲醇洗涤法、碳酸丙烯酯 (Flour法),聚乙醇二甲醚(Selexd法)、N-甲 基吡啶烷酮(Purisol法)。
气体原始组成、催化剂一定: 反应初期转化率低,最适宜温度较高; 反应后期,转化率高,最适宜温度较低。 随反应进行,转化率增加,为使反应速 度快,需降低反应温度。 反应放热,分段冷却降温。
化学工艺学
化学工艺学
一氧化碳变换工艺发展过程及趋势

一氧化碳变换工艺发展过程及趋势摘要 文章对CO 变换工艺过程进行综述,主要包括:CO 变换工艺技术的应用领域及历史演变;CO 变换催化剂的研究进展。
最后对CO 变换工艺的趋势进行预测。
关键词 CO 变换 催化剂 发展过程Abstract The development process and trend of carbon monoxide conversion process This paper summarizes the CO transform process, mainly including: the evolution of application of CO transform technology and history; research progress of CO catalyst. Finally CO transformation process trend forecast.Key words CO transform Catalyst The development process自1913年以来,一氧化碳变换工艺伴随合成氨工业走过了一百余年的历程。
在变换工艺的发展过程中,广大的科研工作者及工程技术人员不断探索高效率、低成木,推动整个一个氧化碳变换工艺发生翻天覆地的变化。
一氧化碳变换就是在催化剂作用下,煤气中的碳类氧化物与水反应,生成二氧化碳的过程,主要发生的反应有:SH CO O H COS H CO O H CO 222222+→++→+ 此反应为放热反应,高温下,反应速率快,但是转化率低;低温下转化率高,但是反应速率慢。
木文针对一氧化碳变换技术的发展过程,催化剂工艺操作技术等方而进行综述。
一 CO 变换工艺技术的应用领域及历史演变CO 与水蒸气在催化剂作用下反应生成2H 和2CO 的过程,即变换过程,此过程在1913年就用于合成氨工业,然后又用于制氢。
在合成甲醇和合成汽油生产中,也用此反应来调节CO 与氢的比例,以满足工艺要求。
甲醇原料气中一氧化碳的变换—变换工艺条件的选择
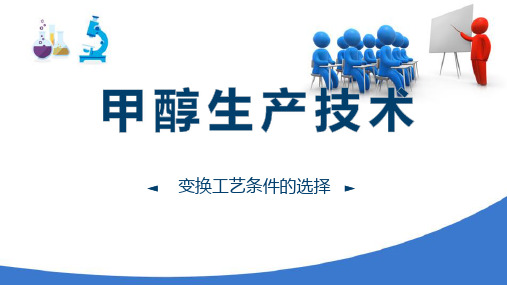
二、压力
压力对变换反应的平衡几乎没有影响,但加压可 提高反应速度和催化剂的生产能力,可采用较大的空 间速度,使设备紧凑,有利于过热蒸汽回收。由于干 原料气的物质的量小于干变换气物质的量,所以,先 压缩原料气进行加压变换的能耗,比常压变换后再压 缩变换气的能耗低15~30%,但加压变换需用压力较 高蒸汽,对设备材质要求高,所以一般小型合成氨厂 操作压力为0.8~1.2 MPa,中型厂为1.2~1.8MPa、 大型厂为3.0~8.0 MPa 。
✓ 如果进入中低变系统原料气中氧含量高,会引起催化剂活性组分与氧反 应,导致催化剂层的剧烈温升。同时,活性组分不同程度硫酸盐化造成 催化剂活性下降,所以各种变换催化剂入口气体中氧含量应小于0.5%。
三、汽气比
增加水蒸汽量,有利于提高CO的平衡变换率,降低CO残余含量, 加快反应速率,为此生产上均采用过量水蒸气。
• 过量水蒸汽的存在,抑制了析碳及甲烷化的副反应发生,保证了催化 剂活性组分Fe3O4的稳定而不被过渡还原,同时还起到载热体的作用, 使催化剂床层温升减小。所以,改变水蒸汽用量是调节床层温度的有 效手段。
五、出口气体中CO含量
✓ 小型氨厂中低变串联工艺指标是中变三段出口6%~8%,低变炉出口约 1.5%,以减轻原料气精制负荷;全低变工艺流程工艺指标是 一变炉出 口4%~7%,二变炉出口0.7%~1.5%,系统温度降低,出口一氧化碳 含量降低。总之,出口气体中一氧化碳含量应与后工序联合考虑。
六、入口气体中氧含量
变换工艺条件的选择
一、温度
变换反应存在最适宜温度
• 如果整个反应过程按最适宜温度曲线进行,则反应速率最大,在相同 的生产能力下所需催化剂用量最小,但实际生产完全按最适宜温度曲 线操作是不现实的。首先,反应开始时,最适宜温度很高,已超过了 中温变换催化剂允许使用的温度范围。其次,随着反应进行,要不断 移出反应热,使最适宜温度逐渐降低是极困难的。因此,变换过程的 操作温度应综合各方面因素来确定。
一氧化碳变换反应工艺流程
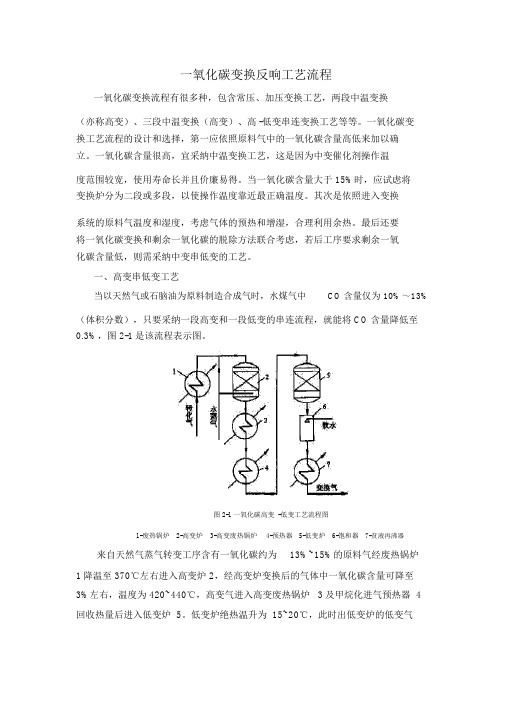
一氧化碳变换反响工艺流程一氧化碳变换流程有很多种,包含常压、加压变换工艺,两段中温变换(亦称高变)、三段中温变换(高变)、高 -低变串连变换工艺等等。
一氧化碳变换工艺流程的设计和选择,第一应依照原料气中的一氧化碳含量高低来加以确立。
一氧化碳含量很高,宜采纳中温变换工艺,这是因为中变催化剂操作温度范围较宽,使用寿命长并且价廉易得。
当一氧化碳含量大于 15%时,应试虑将变换炉分为二段或多段,以使操作温度靠近最正确温度。
其次是依照进入变换系统的原料气温度和湿度,考虑气体的预热和增湿,合理利用余热。
最后还要将一氧化碳变换和剩余一氧化碳的脱除方法联合考虑,若后工序要求剩余一氧化碳含量低,则需采纳中变串低变的工艺。
一、高变串低变工艺当以天然气或石脑油为原料制造合成气时,水煤气中CO含量仅为 10%~13%(体积分数),只要采纳一段高变和一段低变的串连流程,就能将 CO含量降低至0.3%,图 2-1是该流程表示图。
图 2-1一氧化碳高变 -低变工艺流程图1-废热锅炉2-高变炉3-高变废热锅炉4-预热器5-低变炉6-饱和器7-贫液再沸器来自天然气蒸气转变工序含有一氧化碳约为13%~15%的原料气经废热锅炉1降温至 370℃左右进入高变炉 2,经高变炉变换后的气体中一氧化碳含量可降至3%左右,温度为 420~440℃,高变气进入高变废热锅炉3及甲烷化进气预热器 4 回收热量后进入低变炉 5。
低变炉绝热温升为 15~20℃,此时出低变炉的低变气中一氧化碳含量在 0.3%~0.5%。
为了提升传热成效,在饱和器6中喷入少许软水,使低变气达到饱和状态,提升在贫液再沸器7中的传热系数。
二、多段中变工艺以煤为原料的中小型合成氨厂制得的半水煤气中含有许多的一氧化碳气体,需采纳多段中变流程。
并且因为来自脱硫系统的半水煤气温度较低,水蒸气含量较少。
气体在进入中变炉以前设有原料气预热及增湿装置。
此外,因为中温变换的反响放热多,应充足考虑反响热的转移和余热回收利用等问题。
一氧化碳变换

中温变换工艺设计方案目录前言 (2)1、背景 (2)2、分类 (2)3、工艺方法的选择 (2)反应原理 (3)中温变换催化剂 (4)工艺流程 (6)工艺条件 (7)设计体会与收获 (8)参考文献 (9)前言氨是一种重要的化工产品,主要用于化学肥料的生产。
合成氨生产经过多年的发展,现已发展成为一种成熟的化工生产工艺。
合成氨的生产主要分为:原料气的制取;原料气的净化与合成。
粗原料气中常含有大量的C,由于CO是合成氨催化剂的毒物,所以必须进行净化处理,通常,先经过CO变换反应,使其转化为易于清除的CO2和氨合成所需要的H2。
因此,CO变换既是原料气的净化过程,又是原料气造气的继续。
最后,少量的CO用液氨洗涤法,或是低温变换串联甲烷化法加以脱除。
1、背景变换是合成氨生产中的重要工序,同时也是一个耗能重点工序,而外加蒸汽量的大小,是衡量变换工段能耗的主要标志。
因此,尽量减少其用量对其过程的节能降耗具有重要意义。
从70年代以来,我国在变换工艺的节能降耗方面,进行了大量的科研开发和技改工作,先后开发了中变、中变串低变、全低变等变换工艺,使蒸汽消耗量从传统的中变消耗1 t/tNH 以上,降低到200 kg/tNH,从而形成一种能耗低、稳定可靠、周期长的变换工艺。
2、分类一氧化碳变换的工艺流程包括中变-低变串联流程、多段中变流程、全低变流程、中低低流程等。
3、工艺方法的选择变换工艺流程的设计,首先应依据原料气中的一氧化碳含量高低来加以确定。
以煤为原料气的中小型氨厂制得的半水煤气中含有较高的一氧化碳,所以需采用多段中变流程。
中变催化剂操作温度范围较宽,而且价廉易得,使用寿命长。
因此,在一氧化碳转换工艺设计中,我组选用中温变换工艺。
反应原理变换反应可用下式表示:此外,一氧化碳与氢之间还可发生下列反应(1-2) O H C H CO 22+⇔+(1-3)但是,由于变换所用催化剂对反应式(1-1)具有良好的选择性,从而抑制了其他副反应的发生。
- 1、下载文档前请自行甄别文档内容的完整性,平台不提供额外的编辑、内容补充、找答案等附加服务。
- 2、"仅部分预览"的文档,不可在线预览部分如存在完整性等问题,可反馈申请退款(可完整预览的文档不适用该条件!)。
- 3、如文档侵犯您的权益,请联系客服反馈,我们会尽快为您处理(人工客服工作时间:9:00-18:30)。
一氧化碳的低温变换
CO变换的工艺流程主要由原料气组成来决定的,同时还与催化剂、变换反应器的结构,以及气体的净化要求有关。
目前低温变换主要是串接在中温变换催化剂后作为一氧化碳深度变换的。
而入口一氧化碳含量5%-8% , 最高使用温度不超过300℃。
中变串低变流程一般采用两种方法,一是中变炉外加低变炉, 另一种为变换炉中一二层用中变触媒, 三层使用低温触媒。
两种方法都使系统出口一氧化碳含量降至1%左右, 起到稳定生产、增产节能之效果。
1.中(高)变-底变串联流程
采用此流程一般与甲烷化脱除少量碳氧化物相配合。
这类流程先通过中(高)温变换将大量CO变换达到3%左右后,再用低温变换使一氧化碳含量降低到0.3%-0.5%,。
为了进一步降低出口气中CO含量,也有在低变后面串联一个低变的流程。
当CO含量较高时,变换气一般选择在炉外串低变;而一氧化碳含量较低时,可选择在炉内串低变。
中串低流程中要主要两个问题,一是要提高低变催化剂的抗毒性,防止低变催化剂过早失活;二是要注意中变催化剂的过度还原,因为与单一的中变流程相比,中串低特别是中低低流程的反应汽气比下降,中变催化剂容易过度还原,引起催化剂失活、阻力增大及使用寿命缩短。
2.全低变流程
中(高)变-低变串联流程操作繁琐,设备增加,特别是特殊材料阀门的选用给管理带来了许多不便。
使用全低变变换催化剂代替原Fe-Cr系中变催化剂,在低温下完成变换即可克服以上两种工艺的缺点,又能达到理想的目的。
全低变工艺采用宽温区的钴钼系耐硫变换催化剂,主要有下列优点。
(1)催化剂的起始活性温度低,变换炉入口温度及床层热点温度低于中变炉入口及热点温度100-200℃。
这样,就降低了床层阻力,缩小了气体体积约20%,从而提高了变换炉的生产能力。
(2)变换系统处于较低的温度范围内操作,在满足出口变换气中CO含量的前提下,可以降低入炉蒸汽量,使全低变流程的蒸汽消耗降低。
使用全低变变换催化剂代替原。
一系中变催化剂, 在低温下完成变换即可克服以上两种工艺的缺点, 又能达到理想的目的。
近年来推广使用钻一铂系列低温变换催化剂, 低温活性好, 耐高硫, 一般活性温度
左右, 这样就可节约大量的热能。
钻一钥系列催化剂投产前将催化剂中的铂的氢化物转化为硫化物, 催化剂才有高活性。
氢化钻在硫化过程中转化成硫化钻可以显著提高催化剂活性。
由于使用钻一钥系催化剂, 使用过程中煤气含硫化氢皿, 不影响低变催化剂正常使用, 现在国内合成氨流程中, 先脱硫后变换再碳化的流程不能满足上述硫含量要求, 如不经脱硫会产生碳化过程中硫含量过高, 而导致碳钱结晶细小, 且一旦碳化原料气中硫含量跑高, 就会引起铜洗硫化铜的大量沉淀。