一氧化碳低温变换工艺
一氧化碳的变换
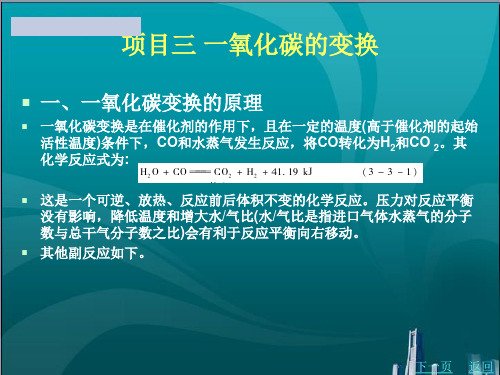
项目三 一氧化碳的变换
③催化剂要有一定的抗毒能力,也就是能耐气体中含有的少量有毒气体。 ④催化剂的机械性能要好,以免在使用中破碎或粉碎,增加变换阻力。 ⑤催化剂有一定的热稳定性,在一定温度范围内,不致因反应后温度升
高而损坏催化剂。 ⑥催化剂要防止发生副反应,主要是一氧化碳分解析碳和生成甲烷的反
综上所述,影响变换反应的因素有以下几种。 1.压力 如前所述,压力对变换反应的平衡几乎无影响,但加压变换有以下优点。 ①可加快反应速度和提高催化剂的生产能力,从而可采用较大空速提高
生产强度。
上一页 下一页 返回
项目三 一氧化碳的变换
②设备体积小,布置紧凑,投资较少。 ③湿变换气中水蒸气冷凝温度高,有利于热能的回收利用。 但提高压力会使系统冷凝液酸度增大,使析炭和生成甲烷等副反应易于
上一页 下一页 返回
项目三 一氧化碳的变换
反应温度按最佳温度进行可使催化剂用量最少,但要控制反应温度严格 按照最佳温度曲线进行在目前是不现实和难于达到的。目前在工业上是 通过特催化剂床层分段来达到使反应温度靠近最佳温度进行。但对于低 温变换过程,由于温升很小,催化剂不必分段。
3.汽气比 CO变换的汽气比一般是指H2O/CO比值或水蒸气/干原料气的比值(摩尔
一、一氧化碳Leabharlann 换的原理一氧化碳变换是在催化剂的作用下,且在一定的温度(高于催化剂的起始 活性温度)条件下,CO和水蒸气发生反应,将CO转化为H2和CO 2。其 化学反应式为:
这是一个可逆、放热、反应前后体积不变的化学反应。压力对反应平衡 没有影响,降低温度和增大水/气比(水/气比是指进口气体水蒸气的分子 数与总干气分子数之比)会有利于反应平衡向右移动。
其他副反应如下。
一氧化碳低温变换

一氧化碳的低温变换CO变换的工艺流程主要由原料气组成来决定的,同时还与催化剂、变换反应器的结构,以及气体的净化要求有关。
目前低温变换主要是串接在中温变换催化剂后作为一氧化碳深度变换的。
而入口一氧化碳含量5%-8% , 最高使用温度不超过300℃。
中变串低变流程一般采用两种方法,一是中变炉外加低变炉, 另一种为变换炉中一二层用中变触媒, 三层使用低温触媒。
两种方法都使系统出口一氧化碳含量降至1%左右, 起到稳定生产、增产节能之效果。
1.中(高)变-底变串联流程采用此流程一般与甲烷化脱除少量碳氧化物相配合。
这类流程先通过中(高)温变换将大量CO变换达到3%左右后,再用低温变换使一氧化碳含量降低到0.3%-0.5%,。
为了进一步降低出口气中CO含量,也有在低变后面串联一个低变的流程。
当CO含量较高时,变换气一般选择在炉外串低变;而一氧化碳含量较低时,可选择在炉内串低变。
中串低流程中要主要两个问题,一是要提高低变催化剂的抗毒性,防止低变催化剂过早失活;二是要注意中变催化剂的过度还原,因为与单一的中变流程相比,中串低特别是中低低流程的反应汽气比下降,中变催化剂容易过度还原,引起催化剂失活、阻力增大及使用寿命缩短。
2.全低变流程中(高)变-低变串联流程操作繁琐,设备增加,特别是特殊材料阀门的选用给管理带来了许多不便。
使用全低变变换催化剂代替原Fe-Cr系中变催化剂,在低温下完成变换即可克服以上两种工艺的缺点,又能达到理想的目的。
全低变工艺采用宽温区的钴钼系耐硫变换催化剂,主要有下列优点。
(1)催化剂的起始活性温度低,变换炉入口温度及床层热点温度低于中变炉入口及热点温度100-200℃。
这样,就降低了床层阻力,缩小了气体体积约20%,从而提高了变换炉的生产能力。
(2)变换系统处于较低的温度范围内操作,在满足出口变换气中CO含量的前提下,可以降低入炉蒸汽量,使全低变流程的蒸汽消耗降低。
使用全低变变换催化剂代替原。
一氧化碳的变换技术62.
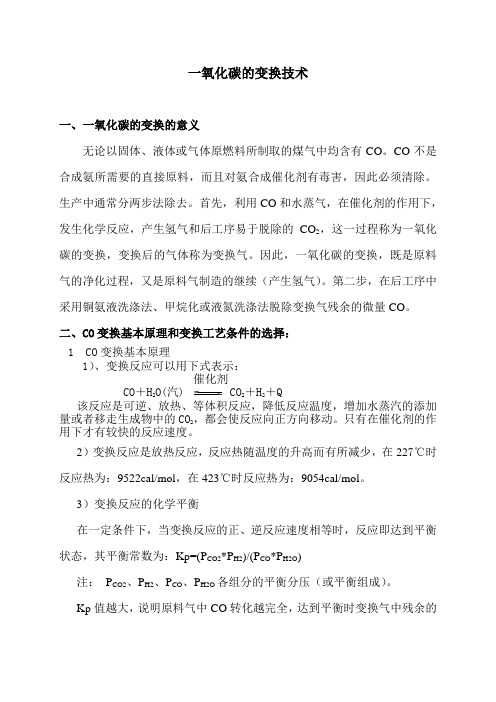
一氧化碳的变换技术一、一氧化碳的变换的意义无论以固体、液体或气体原燃料所制取的煤气中均含有CO 。
CO 不是合成氨所需要的直接原料,而且对氨合成催化剂有毒害,因此必须清除。
生产中通常分两步法除去。
首先,利用CO 和水蒸气,在催化剂的作用下,发生化学反应,产生氢气和后工序易于脱除的CO 2,这一过程称为一氧化碳的变换,变换后的气体称为变换气。
因此,一氧化碳的变换,既是原料气的净化过程,又是原料气制造的继续(产生氢气)。
第二步,在后工序中采用铜氨液洗涤法、甲烷化或液氮洗涤法脱除变换气残余的微量CO 。
二、CO 变换基本原理和变换工艺条件的选择:1 CO 变换基本原理1)、变换反应可以用下式表示:催化剂CO +H2O(汽2+H 2+Q该反应是可逆、放热、等体积反应,降低反应温度,增加水蒸汽的添加量或者移走生成物中的CO 2,都会使反应向正方向移动。
只有在催化剂的作用下才有较快的反应速度。
2)变换反应是放热反应,反应热随温度的升高而有所减少,在227℃时反应热为:9522cal/mol ,在423℃时反应热为:9054cal/mol 。
3)变换反应的化学平衡在一定条件下,当变换反应的正、逆反应速度相等时,反应即达到平衡状态,其平衡常数为:Kp=(P CO2*P H2)/(P CO *P H2O )注: P CO2、P H2、P CO 、P H2O 各组分的平衡分压(或平衡组成)。
Kp 值越大,说明原料气中CO 转化越完全,达到平衡时变换气中残余的CO含量越少。
由于变换反应是放热反应,降低温度有利于平衡向右移动,因此平衡常数随温度的降低而增大。
250℃时为86.51,450℃时为:7.311。
在工业生产中,受催化剂装填量、设备投资的经济效益等因素影响,反应不可能也没必要达到平衡,只能尽可能接近平衡。
实际的流程组合中,一般利用高温段之后再进行低温变换,就是为了提高反应平衡常数,从而提高变换率,降低变换气CO含量。
CO变换过程

反应条件对变换反应速率的影响 1.反应温度 T↑ ,开始k1占主导地位( k1 ↑ ),r ↑; 当T ↑继续升高到一定,k2占主导地位(k2 ↑, K ↓) ,r ↓。 当T达到Top温度下, r达到最大值。 Te:对应转化率x的平衡温度
化学工艺学
化学工艺学
TOP与气体原始组成、转化率及催化剂有关.
化学工艺学
5.5 一氧化碳变换过程
CO变换 步骤、功能和发展 5.5.1 热力学 5.5.2 催化剂 5.5.3 动力学 5.5.4 反应器 5.5.5 工艺流程
化学工艺学
1. 热效应
CO+ H2O ↔ CO2 + H2 热力学分析
H 298 (H 298 H ) ( H H ,CO2 298, H 2 298,CO 298, H 2O )
化学工艺学
5.8 CO2的脱除
CO变换反应后,CO2含量约28-30%,必须脱除。
因为:
(1)CO2是合成氨催化剂毒物
(2)太高CO2影响甲醇收率
(3)CO2可以再利用合成尿素、纯碱、NH4HCO3等
化学工艺学
采用溶液吸收法
根据吸附剂性能不同,分为物理吸收法和化学吸收法 物理吸收法:利用CO2溶解于水或有机溶剂的性质完 成。如加压水洗法、低温甲醇洗涤法、碳酸丙烯酯 (Flour法),聚乙醇二甲醚(Selexd法)、N-甲 基吡啶烷酮(Purisol法)。
气体原始组成、催化剂一定: 反应初期转化率低,最适宜温度较高; 反应后期,转化率高,最适宜温度较低。 随反应进行,转化率增加,为使反应速 度快,需降低反应温度。 反应放热,分段冷却降温。
化学工艺学
化学工艺学
一氧化碳变换工艺发展过程及趋势

一氧化碳变换工艺发展过程及趋势摘要 文章对CO 变换工艺过程进行综述,主要包括:CO 变换工艺技术的应用领域及历史演变;CO 变换催化剂的研究进展。
最后对CO 变换工艺的趋势进行预测。
关键词 CO 变换 催化剂 发展过程Abstract The development process and trend of carbon monoxide conversion process This paper summarizes the CO transform process, mainly including: the evolution of application of CO transform technology and history; research progress of CO catalyst. Finally CO transformation process trend forecast.Key words CO transform Catalyst The development process自1913年以来,一氧化碳变换工艺伴随合成氨工业走过了一百余年的历程。
在变换工艺的发展过程中,广大的科研工作者及工程技术人员不断探索高效率、低成木,推动整个一个氧化碳变换工艺发生翻天覆地的变化。
一氧化碳变换就是在催化剂作用下,煤气中的碳类氧化物与水反应,生成二氧化碳的过程,主要发生的反应有:SH CO O H COS H CO O H CO 222222+→++→+ 此反应为放热反应,高温下,反应速率快,但是转化率低;低温下转化率高,但是反应速率慢。
木文针对一氧化碳变换技术的发展过程,催化剂工艺操作技术等方而进行综述。
一 CO 变换工艺技术的应用领域及历史演变CO 与水蒸气在催化剂作用下反应生成2H 和2CO 的过程,即变换过程,此过程在1913年就用于合成氨工业,然后又用于制氢。
在合成甲醇和合成汽油生产中,也用此反应来调节CO 与氢的比例,以满足工艺要求。
CO变换工艺发展过程及趋势
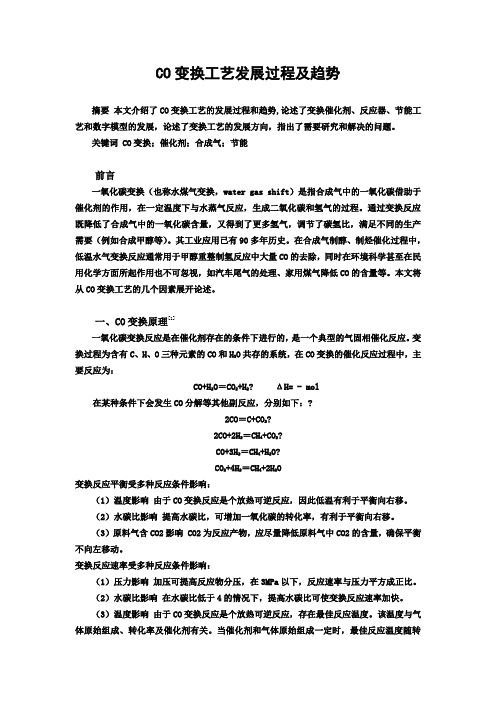
CO变换工艺发展过程及趋势摘要本文介绍了CO变换工艺的发展过程和趋势,论述了变换催化剂、反应器、节能工艺和数字模型的发展,论述了变换工艺的发展方向,指出了需要研究和解决的问题。
关键词 CO变换;催化剂;合成气;节能前言一氧化碳变换(也称水煤气变换,water gas shift)是指合成气中的一氧化碳借助于催化剂的作用,在一定温度下与水蒸气反应,生成二氧化碳和氢气的过程。
通过变换反应既降低了合成气中的一氧化碳含量,又得到了更多氢气,调节了碳氢比,满足不同的生产需要(例如合成甲醇等)。
其工业应用已有90多年历史。
在合成气制醇、制烃催化过程中,低温水气变换反应通常用于甲醇重整制氢反应中大量CO的去除,同时在环境科学甚至在民用化学方面所起作用也不可忽视,如汽车尾气的处理、家用煤气降低CO的含量等。
本文将从CO变换工艺的几个因素展开论述。
一、CO变换原理[1]一氧化碳变换反应是在催化剂存在的条件下进行的,是一个典型的气固相催化反应。
变换过程为含有C、H、O三种元素的CO和H2O共存的系统,在CO变换的催化反应过程中,主要反应为:CO+H2O=CO2+H2? ΔH= - mol在某种条件下会发生CO分解等其他副反应,分别如下:?2CO=C+CO2?2CO+2H2=CH4+CO2?CO+3H2=CH4+H2O?CO2+4H2=CH4+2H2O变换反应平衡受多种反应条件影响:(1)温度影响由于CO变换反应是个放热可逆反应,因此低温有利于平衡向右移。
(2)水碳比影响提高水碳比,可增加一氧化碳的转化率,有利于平衡向右移。
(3)原料气含CO2影响 CO2为反应产物,应尽量降低原料气中CO2的含量,确保平衡不向左移动。
变换反应速率受多种反应条件影响:(1)压力影响加压可提高反应物分压,在3MPa以下,反应速率与压力平方成正比。
(2)水碳比影响在水碳比低于4的情况下,提高水碳比可使变换反应速率加快。
(3)温度影响由于CO变换反应是个放热可逆反应,存在最佳反应温度。
一氧化碳低温变换工艺及应用
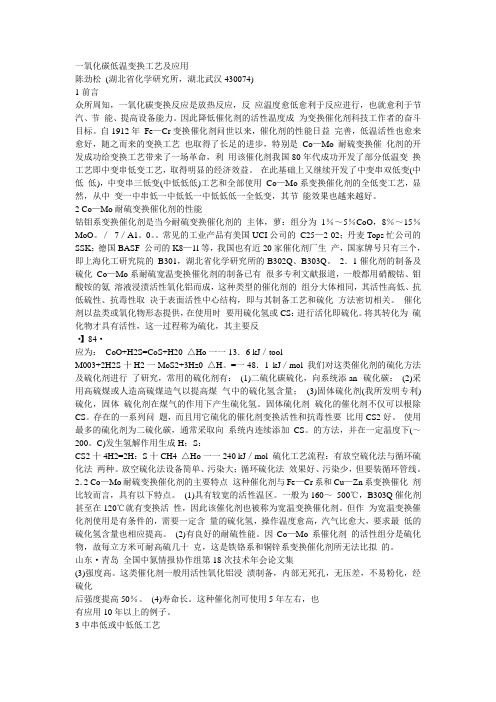
一氧化碳低温变换工艺及应用陈劲松(湖北省化学研究所,湖北武汉430074)1前言众所周知,一氧化碳变换反应是放热反应,反应温度愈低愈利于反应进行,也就愈利于节汽、节能、提高设备能力。
因此降低催化剂的活性温度成为变换催化剂科技工作者的奋斗目标。
自1912年Fe—Cr变换催化剂问世以来,催化剂的性能日益完善,低温活性也愈来愈好,随之而来的变换工艺也取得了长足的进步,特别是Co—Mo耐硫变换催化剂的开发成功给变换工艺带来了一场革命,利用该催化剂我国80年代成功开发了部分低温变换工艺即中变串低变工艺,取得明显的经济效益。
在此基础上又继续开发了中变串双低变(中低低),中变串三低变(中低低低)工艺和全部使用Co—Mo系变换催化剂的全低变工艺,显然,从中变一中串低一中低低一中低低低一全低变,其节能效果也越来越好。
2 Co—Mo耐硫变换催化剂的性能钴钼系变换催化剂是当今耐硫变换催化剂的主体,萝:组分为1%~5%CoO,8%~15%MoO。
/7/A1。
0。
常见的工业产品有美国UCI公司的C25—2-02;丹麦Tops忙公司的SSK;德国BASF 公司的K8—1l等,我国也有近20家催化剂厂生产,国家牌号只有三个,即上海化工研究院的B301,湖北省化学研究所的B302Q、B303Q。
2.1催化剂的制备及硫化Co—Mo系耐硫宽温变换催化剂的制备已有很多专利文献报道,一般都用硝酸钴、钼酸铵的氨溶液浸渍活性氧化铝而成,这种类型的催化剂的组分大体相同,其活性高低、抗低硫性、抗毒性取决于表面活性中心结构,即与其制备工艺和硫化方法密切相关。
催化剂以盐类或氧化物形态提供,在使用时要用硫化氢或CS:进行活化即硫化。
将其转化为硫化物才具有活性,这一过程称为硫化,其主要反·】84·应为:CoO+H2S=CoS+H20 △Ho一一13.6 kJ/toolM003+2H2S十H2一MoS2+3Hz0 △H。
=一48.1 kJ/mol 我们对这类催化剂的硫化方法及硫化剂进行了研究,常用的硫化剂有:(1)二硫化碳硫化,向系统添an--硫化碳;(2)采用高硫煤或人造高硫煤造气以提高煤气中的硫化氢含量;(3)固体硫化剂(我所发明专利)硫化,固体硫化剂在煤气的作用下产生硫化氢。
一氧化碳中温—低温串联变换反应实验
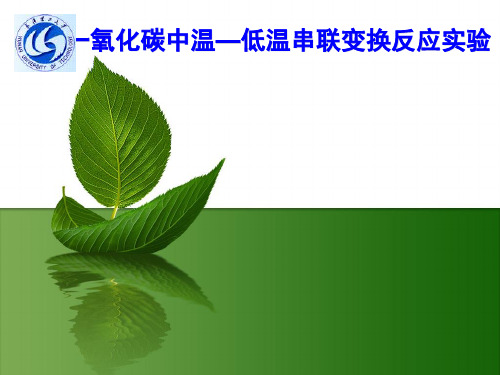
一氧化碳中温—低温串联变换反应实验
实验步骤如下: (1)开车步骤 ① 检查系统是否处于正常状态; ② 开启氮气钢瓶,置换系统约5 min; ③ 接通电源,缓慢升反应器温度,同时把脱氧槽缓慢升温至200 ℃, 恒定; ④ 中、低变床层温度升至100 ℃时,开启管道保温控制仪,开启水饱 和器,同时打开冷却水,管道保温,水饱和器温度恒定在实验温度下; ⑤ 调节中、低变反应器温度到实验条件后,切换成原料气,稳定20 min左右,随后进行分析,记录实验条件和分析数据。
一氧化碳中温—低温串联变换反应实验
(2)停车步骤 ① 关闭原料气钢瓶,切换成氮气,关闭反应器控温仪; ② 稍后关闭水饱和器加热电源,置换水浴热水; ③ 关闭管道保温,待反应床温低于200 ℃以下,关闭脱氧槽加热电 源,关闭冷却水,关闭氮气钢瓶,关闭各仪表电源及总电源。
一氧化碳中温—低温串联变换反应实验
R0 p H 2O p a p g p H 2O
式中:水汽饱和蒸汽压
p H 2O
用安托因公式计算:
一氧化碳中温—低温串联变换反应实验
式中:A、B、C——安托因系数,可查表4-5-2;t——饱和温度, ℃ 。
一氧化碳中温—低温串联变换反应实验
(3)清理计算思路列出主要公式,计算一点数据得到结果。 (4)计算不同温度下的反应速率常数。 (5)根据实验结果,浅谈中—低变串联反应器工艺条件。 (6)分析本实验结果,讨论本实验方法。
(6)试分析实验操作过程中应注意哪些事项? ①注意实验条件的控制,保证实验的准确性。 ②注意规范操作,确保实验的安全性。
一氧化碳中温—低温串联变换反应实验
8、思考题及参考答案
(1)实验系统中的气体如何净化?净化的作用有那些? 实验通过U型管中的净化剂 使气体得到净化。由于变换催化剂对硫、氧、酸雾等易 于中毒,净化可防止催化剂中毒,增加实验的准确性。 (2)如何判断内、外扩散的消除? 当所选择的催化剂粒径(足够小)不影响实验结果时刻判断为消除了内扩散的影响, 当实验所选气体空速(足够大,20000~30000 mol/g.h)不影响实验结果时刻判断为 消除了外扩散的影响。 (3)如何确证床层的等温条件? 采用惰性物料石英砂稀释催化剂,装填较少量的催化剂,使反应热不至于过分集中。 选用适当的反应管内径与颗粒的直径之比,选用较小的反应管径,减小壁效应。将 反应管置于恒温铜块中,铜块置于管式电阻炉内,用DWK—702控制炉温,用电热 偶和数字显示仪测量和读取反应温度。实验人员应精心操作,防止温度大幅度波动 或超温。
- 1、下载文档前请自行甄别文档内容的完整性,平台不提供额外的编辑、内容补充、找答案等附加服务。
- 2、"仅部分预览"的文档,不可在线预览部分如存在完整性等问题,可反馈申请退款(可完整预览的文档不适用该条件!)。
- 3、如文档侵犯您的权益,请联系客服反馈,我们会尽快为您处理(人工客服工作时间:9:00-18:30)。
一氧化碳低温变换工艺
作者:陈劲松
作者单位:湖北省化学研究所、国家CO变换催化剂工业基地,湖北武汉,430074
1.会议论文陈劲松一氧化碳低温变换工艺及应用2001
本文对一氧化碳低温变换工艺及应用进行了阐述。
众所周知,一氧化碳变换反应是放热反应,反应温度愈低愈利于反应进行,也就愈利于节汽、节能、提高设备能力。
因此降低催化剂的活性温度成为变换催化剂科技工作者的奋斗目标。
自1912年Fe-Cr变换催化剂问世以来,催化剂的性能日益完善
,低温活性也愈来愈好,随之而来的变换工艺也取得了长足的进步,特别是Co—Mo耐硫变换催化剂的开发成功给变换工艺带来了一场革命,利用该催化剂我国80年代成功开发了部分低温变换工艺即中变串低变工艺,取得明显的经济效益。
在此基础上又继续开发了中变串双低变(中低低),中变串三低变(中低低低)工艺和全部使用Co-Mo系变换催化剂的全低变工艺,显然,从中变→中串低→中低低→中低低低→全低变,其节能效果也越来越好。
2.会议论文陈劲松.曾建桥CO低温变换工艺2000
一氧化碳变换反应是放热反应,反应温度愈低愈利于反应进行,也就愈利于节能、提高设备能力。
因此降低催化剂的活性温度成为变换催化剂科技工作者的奋斗目标。
Co-Mo耐硫变换催化剂的开发成功给变换工艺带来了一场革命,利用该催化剂我国八十年代成功开发了部分低温变换工艺即高变串低变工艺,取得明显的经济效益。
本文就CO低温变换工艺作一介绍。
3.学位论文杨松甲醇生产中变换工艺的设计与探讨2009
一氧化碳变换反应,在合成甲醇的生产中占有非常重要的地位。
它既是原料气的净化过程,又是原料气的制造过程。
在变换反应过程中要消耗大量蒸汽,其蒸汽消耗量,占合成甲醇生产总蒸汽消耗量的30%以上。
本文对不同的变换工艺进行分析对比,为甲醇生产确定一条工艺流程简单、投资费用低、节能降耗的工艺路线。
采用全气量部分低温耐硫变换,可以提高反应速率和生产能力,降低蒸汽消耗,节约能量,减小投资,节约催化剂用量,有利于低温变换催化剂的应用。
本文以山东红日阿康化肥有限公司10万吨/年甲醇装置加压变换工艺为对象,分析不同的变换工艺、变换催化剂和反应器,确立了全低温变换工艺。
论文对系统进行了物料衡算,求出变换气组成、脱硫气体组成以及CO总转化率;分析了不同类型的变换催化剂,研究了气体中H2S含量、不同温度及汽气比对催化剂的影响。
从热量的补充和热量的回收利用方面,阐述了变换反应中的能量消耗问题。
分析了低温变换系统中应注意的问题。
4.学位论文杨余芳一氧化碳加压变换系统的探讨与设计2002
一氧化碳变换反应在合成氨的生产中占有非常重要的地位,它既是原料气的净化过程,又是原料气的制造过程.在变换反应过程中要消耗大量蒸汽,其蒸汽消耗量占合成氨生产总蒸汽消耗量的30%以上.采用加压变换反应,可以提高反应速度和生产能力,降低蒸汽消耗,节约能量,减小投资,节约催化剂用量,有利于低温变换催化剂的应用.该文对加压变换反应中的三种不同工艺的优点和存在的问题作了分析和归纳总结,认为不使用饱和热水塔的全低温变换工艺为最佳变换工艺.变换炉是变换反应的关键设备,该文根据湘江氮肥厂的实际生产情况,对加压中温变换炉进行了物料和热量衡算.求出了变换炉的各段进出口组成和平衡变换率,以及各平衡变换率所对应的最适宜温度,求出了变换炉的每一段应该加入的蒸汽量,以及各段所损失或补充的热量,确定了各段的操作线方程,并且绘出了平衡曲线和最适宜温度曲线.同时,为了优化变换工段的操作,对变换炉的操作编制了程序,进行了模拟计算,找出了三种情况下合适的反应温度,获得了较大的转化率.此外,分析了温度对变换反应的影响;从热量的补充和热量的回收利用方面阐述了变换反应中的能量消耗问题;分析和概括了加压变换系统中存在的问题和不足之处.
本文链接:/Conference_6314932.aspx
授权使用:重庆大学(cqdx),授权号:a28271ab-3538-4071-b6df-9e41014c1817
下载时间:2010年12月3日。