一氧化碳变换
一氧化碳变换题库
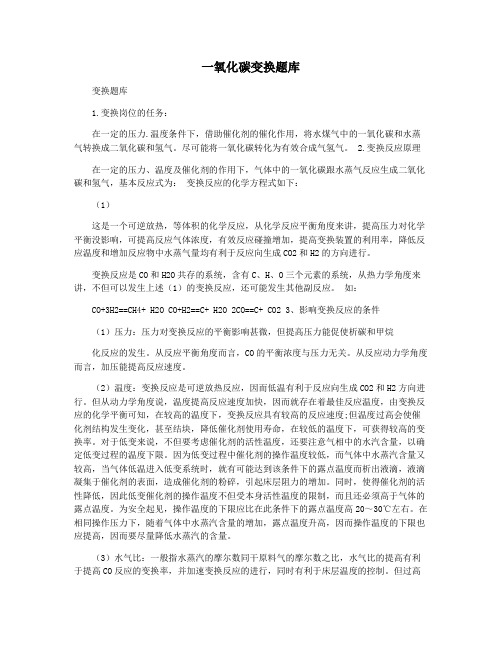
一氧化碳变换题库变换题库1.变换岗位的任务:在一定的压力.温度条件下,借助催化剂的催化作用,将水煤气中的一氧化碳和水蒸气转换成二氧化碳和氢气。
尽可能将一氧化碳转化为有效合成气氢气。
2.变换反应原理在一定的压力、温度及催化剂的作用下,气体中的一氧化碳跟水蒸气反应生成二氧化碳和氢气,基本反应式为:变换反应的化学方程式如下:(1)这是一个可逆放热,等体积的化学反应,从化学反应平衡角度来讲,提高压力对化学平衡没影响,可提高反应气体浓度,有效反应碰撞增加,提高变换装置的利用率,降低反应温度和增加反应物中水蒸气量均有利于反应向生成CO2和H2的方向进行。
变换反应是CO和H2O共存的系统,含有C、H、O三个元素的系统,从热力学角度来讲,不但可以发生上述(1)的变换反应,还可能发生其他副反应。
如:CO+3H2==CH4+ H2O CO+H2==C+ H2O 2CO==C+ CO2 3、影响变换反应的条件(1)压力:压力对变换反应的平衡影响甚微,但提高压力能促使析碳和甲烷化反应的发生。
从反应平衡角度而言,CO的平衡浓度与压力无关。
从反应动力学角度而言,加压能提高反应速度。
(2)温度:变换反应是可逆放热反应,因而低温有利于反应向生成CO2和H2方向进行。
但从动力学角度说,温度提高反应速度加快,因而就存在着最佳反应温度,由变换反应的化学平衡可知,在较高的温度下,变换反应具有较高的反应速度;但温度过高会使催化剂结构发生变化,甚至结块,降低催化剂使用寿命,在较低的温度下,可获得较高的变换率。
对于低变来说,不但要考虑催化剂的活性温度,还要注意气相中的水汽含量,以确定低变过程的温度下限。
因为低变过程中催化剂的操作温度较低,而气体中水蒸汽含量又较高,当气体低温进入低变系统时,就有可能达到该条件下的露点温度而析出液滴,液滴凝集于催化剂的表面,造成催化剂的粉碎,引起床层阻力的增加。
同时,使得催化剂的活性降低,因此低变催化剂的操作温度不但受本身活性温度的限制,而且还必须高于气体的露点温度。
一氧化碳低温变换

一氧化碳的低温变换CO变换的工艺流程主要由原料气组成来决定的,同时还与催化剂、变换反应器的结构,以及气体的净化要求有关。
目前低温变换主要是串接在中温变换催化剂后作为一氧化碳深度变换的。
而入口一氧化碳含量5%-8% , 最高使用温度不超过300℃。
中变串低变流程一般采用两种方法,一是中变炉外加低变炉, 另一种为变换炉中一二层用中变触媒, 三层使用低温触媒。
两种方法都使系统出口一氧化碳含量降至1%左右, 起到稳定生产、增产节能之效果。
1.中(高)变-底变串联流程采用此流程一般与甲烷化脱除少量碳氧化物相配合。
这类流程先通过中(高)温变换将大量CO变换达到3%左右后,再用低温变换使一氧化碳含量降低到0.3%-0.5%,。
为了进一步降低出口气中CO含量,也有在低变后面串联一个低变的流程。
当CO含量较高时,变换气一般选择在炉外串低变;而一氧化碳含量较低时,可选择在炉内串低变。
中串低流程中要主要两个问题,一是要提高低变催化剂的抗毒性,防止低变催化剂过早失活;二是要注意中变催化剂的过度还原,因为与单一的中变流程相比,中串低特别是中低低流程的反应汽气比下降,中变催化剂容易过度还原,引起催化剂失活、阻力增大及使用寿命缩短。
2.全低变流程中(高)变-低变串联流程操作繁琐,设备增加,特别是特殊材料阀门的选用给管理带来了许多不便。
使用全低变变换催化剂代替原Fe-Cr系中变催化剂,在低温下完成变换即可克服以上两种工艺的缺点,又能达到理想的目的。
全低变工艺采用宽温区的钴钼系耐硫变换催化剂,主要有下列优点。
(1)催化剂的起始活性温度低,变换炉入口温度及床层热点温度低于中变炉入口及热点温度100-200℃。
这样,就降低了床层阻力,缩小了气体体积约20%,从而提高了变换炉的生产能力。
(2)变换系统处于较低的温度范围内操作,在满足出口变换气中CO含量的前提下,可以降低入炉蒸汽量,使全低变流程的蒸汽消耗降低。
使用全低变变换催化剂代替原。
一氧化碳的变换技术62.
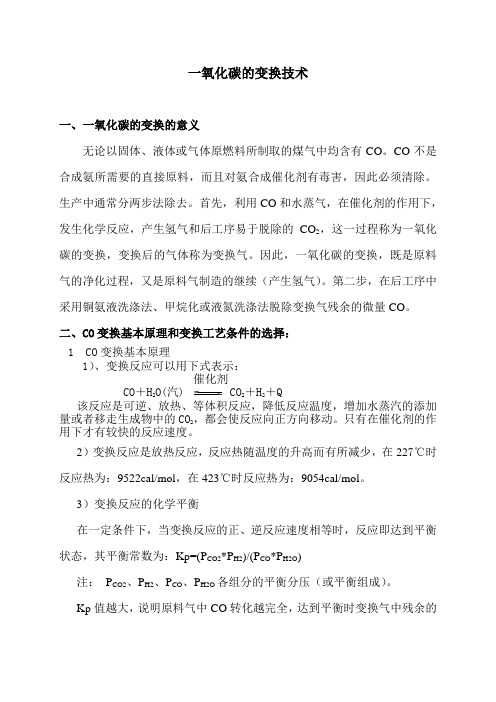
一氧化碳的变换技术一、一氧化碳的变换的意义无论以固体、液体或气体原燃料所制取的煤气中均含有CO 。
CO 不是合成氨所需要的直接原料,而且对氨合成催化剂有毒害,因此必须清除。
生产中通常分两步法除去。
首先,利用CO 和水蒸气,在催化剂的作用下,发生化学反应,产生氢气和后工序易于脱除的CO 2,这一过程称为一氧化碳的变换,变换后的气体称为变换气。
因此,一氧化碳的变换,既是原料气的净化过程,又是原料气制造的继续(产生氢气)。
第二步,在后工序中采用铜氨液洗涤法、甲烷化或液氮洗涤法脱除变换气残余的微量CO 。
二、CO 变换基本原理和变换工艺条件的选择:1 CO 变换基本原理1)、变换反应可以用下式表示:催化剂CO +H2O(汽2+H 2+Q该反应是可逆、放热、等体积反应,降低反应温度,增加水蒸汽的添加量或者移走生成物中的CO 2,都会使反应向正方向移动。
只有在催化剂的作用下才有较快的反应速度。
2)变换反应是放热反应,反应热随温度的升高而有所减少,在227℃时反应热为:9522cal/mol ,在423℃时反应热为:9054cal/mol 。
3)变换反应的化学平衡在一定条件下,当变换反应的正、逆反应速度相等时,反应即达到平衡状态,其平衡常数为:Kp=(P CO2*P H2)/(P CO *P H2O )注: P CO2、P H2、P CO 、P H2O 各组分的平衡分压(或平衡组成)。
Kp 值越大,说明原料气中CO 转化越完全,达到平衡时变换气中残余的CO含量越少。
由于变换反应是放热反应,降低温度有利于平衡向右移动,因此平衡常数随温度的降低而增大。
250℃时为86.51,450℃时为:7.311。
在工业生产中,受催化剂装填量、设备投资的经济效益等因素影响,反应不可能也没必要达到平衡,只能尽可能接近平衡。
实际的流程组合中,一般利用高温段之后再进行低温变换,就是为了提高反应平衡常数,从而提高变换率,降低变换气CO含量。
一氧化碳变换操作规程
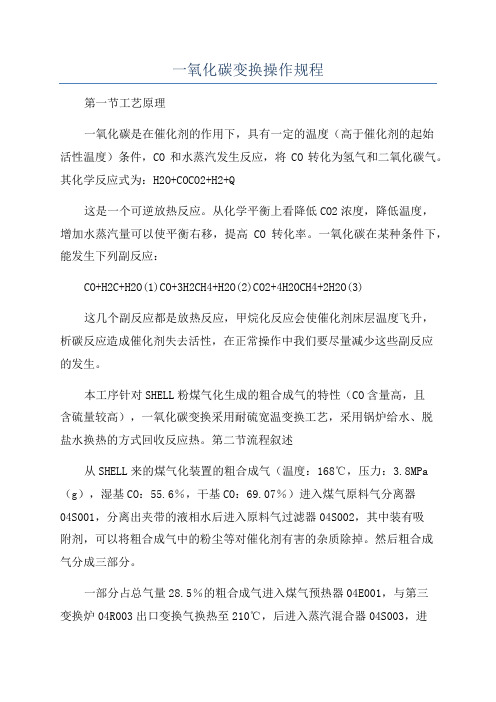
一氧化碳变换操作规程第一节工艺原理一氧化碳是在催化剂的作用下,具有一定的温度(高于催化剂的起始活性温度)条件,CO和水蒸汽发生反应,将CO转化为氢气和二氧化碳气。
其化学反应式为:H2O+COCO2+H2+Q这是一个可逆放热反应。
从化学平衡上看降低CO2浓度,降低温度,增加水蒸汽量可以使平衡右移,提高CO转化率。
一氧化碳在某种条件下,能发生下列副反应:CO+H2C+H2O(1)CO+3H2CH4+H2O(2)CO2+4H2OCH4+2H2O(3)这几个副反应都是放热反应,甲烷化反应会使催化剂床层温度飞升,析碳反应造成催化剂失去活性,在正常操作中我们要尽量减少这些副反应的发生。
本工序针对SHELL粉煤气化生成的粗合成气的特性(CO含量高,且含硫量较高),一氧化碳变换采用耐硫宽温变换工艺,采用锅炉给水、脱盐水换热的方式回收反应热。
第二节流程叙述从SHELL来的煤气化装置的粗合成气(温度:168℃,压力:3.8MPa (g),湿基CO:55.6%,干基CO:69.07%)进入煤气原料气分离器04S001,分离出夹带的液相水后进入原料气过滤器04S002,其中装有吸附剂,可以将粗合成气中的粉尘等对催化剂有害的杂质除掉。
然后粗合成气分成三部分。
一部分占总气量28.5%的粗合成气进入煤气预热器04E001,与第三变换炉04R003出口变换气换热至210℃,后进入蒸汽混合器04S003,进入该混合器前,来自蒸汽管网的过热蒸汽(4.4MPa,282℃)与粗合成气混合。
进蒸汽混合器的蒸汽量由调节阀FV-04005调节,该蒸汽量与28.5%的粗合成气量是比例控制,保证进入一变、汽、气比不低于1.09,原料气管线设有TV-04003调节阀旁路(测温点TE-04003在一变的入口。
混合后的粗合成气进入煤气换热器04E002管侧与来自第一变换炉04R001出口的变换气换热。
合成气温度由TV-04003控制在约255℃左右,进入第一变换炉04R001进行变换反应(一变入口湿基CO:33.1%)。
一氧化碳变换技术交流

℃
• 但实际上完全按最适宜温度曲线操作是不可能的,因 为在反应开始时,最适宜温度最高(以中温变换为例, 要达到620℃以上),大大超过催化剂的耐热温度, 而且热量的来源是个问题。随着反应的进行,要不断 地、准确地按照最适宜温度的需要移出反应热是极为 困难的,见二 段CO变换的T-x图。 图中: CD即为最适宜温度曲线,AB为平衡曲线,EF线为第 一段绝热反应线,FG线表示段间间接换热降温过程。 GH线表示第二段绝热反应线。。 • 变换过程的温度应综合各个方面因素来确定,主要原 则是: • 1)、反应开始温度应高于催化剂活性温度10~20℃ 左右。另外必须要高于气体露点温度20℃以上(防止 原料气析水,一是使催化剂粉碎结块,二是腐蚀设 备)。
CS2+4H2 2H2S+CH4+246 kJ∕mol MoO3+2H2S+H2 MoS2+3H2O+48.1 kJ∕mol CoO+H2S CoS+H2O+13.4 kJ∕mol • 升温硫化一般采用循环硫化法,升温硫化阶段所需要的热 量主要靠电加热器提供。 • 3)国内外Co-Mo系耐硫变换催化剂的发展历程 • ⑴1969年德国BASF公司开发成功的K8-11耐硫变换催化 剂(镁铝尖晶石复合材料为载体),1978年首次实现工业 化的应用,用于重油部分氧化法制合成气流程和加压煤气 化制合成氨流程的CO变换。它的主要特点是以镁铝尖晶 石为载体,硫化后活性高,耐高水蒸汽分压,可在高压下使用, 抗毒物能力强,能再生,平均寿命 3~5年。
• 由于变换反应是放热反应,降低温度有利于平衡 向右移动,因此平衡常数随温度的降低而增大。 例如:250℃时为86.51,450℃时为:7.311。 • 在工业生产中,受催化剂装填量、设备投资的经 济效益等因素影响,反应不可能也没必要达到平 衡,只能尽可能接近平衡。 • 实际生产的流程组合中,一般利用高温段之后再 进行低温变换,就是为了提高反应平衡常数,从 而提高变换率,降低变换气CO含量。
一氧化碳的变换

二、一氧化碳变换反应的化学平衡
(一)变换反应的热效应 变换反应的标准反应热△ H298 ,可以用有关气体的标准生成热数据进
行计算:
上一页 下一页 Байду номын сангаас回
其他副反应如下。
下一页 返回
项目三 一氧化碳的变换
(一)甲烷化反应 在一氧化碳与水蒸气共存的系统中,是含有C, H, O三个元素的系统。
从热力学角度,不但可能进行式(3一3一1)的变化反应,而且还可进行其 他反应,如:
上一页 下一页 返回
项目三 一氧化碳的变换
这一点与甲烷蒸气转化、煤气化等系统中所出现的反应式有相似之处。 但是,由于所用催化剂对反应式(3 -3-1)具有良好的选择性,从而抑制了 其他反应的发生。在计算反应系统平衡组成时,采用反应式(3-3-1)的平 衡关系,其结果基本符合实际情况。从以上反应式看,降低温度和增加 压力有利于生成甲烷的反应。但在实际生成中采用的工艺条件下,这一 副反应是不会发生的。降低床层的热点温度、增加水/气、提高空速都可 以抑制甲烷化副反应的影响。
还可进行其他反应:
由于所用的催化剂对变换反应有良好的选择性,可抑制其他反应的发生, 因此副反应发生的概率很小。
(二)变换反应的平衡常数 一氧化碳变换反应通常是在常压或压力不太高的条件下进行,故平衡常
数计算时各组分用分压表示已足够精确。因此平衡常数KD可用下式计算:
上一页 下一页 返回
项目三 一氧化碳的变换
平衡常数是温度的函数,可通过范特荷莆方程式计算:
不同温度下一氧化碳变换反应的平衡常数见表3-3 -2。
一氧化碳变换反应实验报告思考题目

一氧化碳变换反应实验报告思考题目【最新版】目录一、实验背景和目的二、实验过程和方法三、实验结果和分析四、实验结论和展望正文一、实验背景和目的一氧化碳变换反应是一种重要的化学反应,其目的是在工业上通过催化剂将一氧化碳转化为二氧化碳,以达到环保和资源利用的目的。
本次实验旨在通过实际操作,让学生深入理解一氧化碳变换反应的原理和过程,培养其实验操作能力。
二、实验过程和方法实验过程主要分为以下几个步骤:1.准备实验器材和试剂:包括实验管、酒精灯、试管夹、导气管等。
试剂主要包括一氧化碳、二氧化碳和氧化铁。
2.组装实验装置:将实验管固定在试管夹上,导气管一端连接实验管,另一端放入装有氧化铁的试管中。
3.进行实验:点燃酒精灯,加热实验管中的氧化铁,观察导气管中一氧化碳的流动情况。
4.收集和分析实验结果:实验过程中,观察一氧化碳的流量和二氧化碳的生成情况,记录实验数据,并进行分析。
三、实验结果和分析实验结果显示,随着氧化铁的加热,导气管中的一氧化碳逐渐减少,同时,试管中的二氧化碳含量逐渐增加。
这表明,在氧化铁的催化作用下,一氧化碳成功转化为二氧化碳。
通过对实验数据的分析,我们可以得出以下结论:1.氧化铁在一氧化碳变换反应中起到了重要的催化作用。
2.反应温度对反应速率有显著影响,随着温度的升高,反应速率也相应增加。
3.在一定范围内,反应时间与一氧化碳转化率呈正相关关系。
四、实验结论和展望通过本次实验,我们深入了解了一氧化碳变换反应的原理和过程,掌握了实验操作方法,并得出了一些有意义的结论。
然而,实验仍存在一些局限性,例如实验条件较为简单,可能无法完全模拟实际工业生产环境。
一氧化碳的变换.
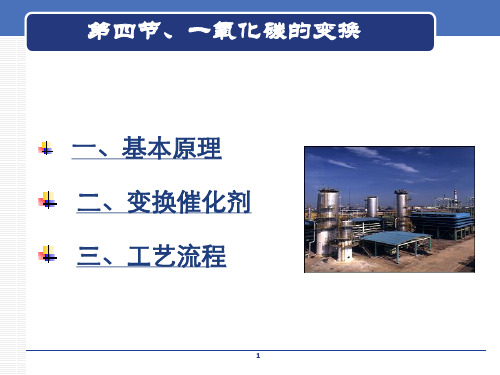
11
(二)、氧化锌法
❖氧化锌脱硫性能的好坏用硫容 量表示。所谓硫容就是每单位质 量氧化锌能脱除S的量。一些数 据如图所示。一些定性结论如下: 温度上升,硫容增加;空速增加, 硫容降低;汽气比上升,硫容下 降。
2、氧化锌脱硫剂:
100
ya,ya’ —分别为原料及变换气中一氧化碳的摩尔分率(干 基)
2
二、变换催化剂
❖ 1、中(高)变催化剂:
▪
以三氧化二铁为活性中心
▪ 铬、铜、锌、钴、钾等氧化物,可提高催化剂的活性
▪ 镁、铝等氧化物,可提高催化剂的耐热和耐毒性能。
❖ 目前常见的中(高)变换催化剂有:
▪ 铁铬系催化剂:以FeO3加Cr2O3为助催化剂。 ▪ 钴钼系催化剂:针对重油含S量高的耐高S变换催化剂。
K
0 p
pH2O
/
pH2S
10
❖ 一些条件下平衡S含量的计算值如下:
水蒸气含量/%
0.50 10 20
平衡硫含量/10-6 200℃ 0.000025 0.00055 0.005
300℃ 0.0008 0.018 0.16
400℃ 0.009 0.20 1.80
❖ 实际上天然气等原料中水蒸气含量很低,所以即使温度在400℃也可满足S含量 <0.1× 10-6的要求。 200℃含水20%时,S<0.005× 10-6,因此氧化锌也用在变 换工序作变换催化剂的保护剂。
提高其稳定性。 ❖ (2)低变催化剂的还原: ❖ CuO+H2=Cu+H2O △H0298=-86.7kJ/mol ❖ CuO+CO=Cu+CO2 △H0298=-127.7kJ/mol
- 1、下载文档前请自行甄别文档内容的完整性,平台不提供额外的编辑、内容补充、找答案等附加服务。
- 2、"仅部分预览"的文档,不可在线预览部分如存在完整性等问题,可反馈申请退款(可完整预览的文档不适用该条件!)。
- 3、如文档侵犯您的权益,请联系客服反馈,我们会尽快为您处理(人工客服工作时间:9:00-18:30)。
一氧化碳变换概述一氧化碳的变换是指煤气借助于催化剂的作用,在一定温度下,与水蒸气反应,一氧化碳生成二氧化碳和氢气的过程。
通过变换反应既除去了煤气中的一氧化碳,又得到了制取甲醇的有效气体氢气。
因此,变化工段既是转化工序,又是净化工序。
前工段来的煤气中,一氧化碳含量高,通过变换反应以后,要求达到工艺气体中的CO/H2约为2.05~2.1的关系,以满足甲醇合成的要求。
一氧化碳变换反应是在催化剂存在的条件下进行的,是一个典型的气固相催化反应。
60年代以前,变换催化剂普遍采用Fe-Gr催化剂,使用温度范围为350~550℃,60年代以后,开发了钴钼加氢转化催化剂和氧化锌脱硫剂,这种催化剂的操作温度为200~280℃,为了区别这两种操作温度不同的变换过程,习惯上将前者称为“中温变换”,后者称为“低温变换”。
按照回收热量的方法不同,变换又可分为激冷流程和废锅流程,冷激流程中,冷激后的粗原料气已被水蒸气饱和,在未经冷却和脱硫情况下直接进行变换,因此,两种流程按照工艺条件的不同选用不同的催化剂,激冷流程采用Co-Mo耐硫变换催化剂,废锅流程采用Fe-Cr变换催化剂。
第一节变换反应原理变换过程为含有C、H、O三种元素的CO和H2O共存的系统,在CO变换的催化反应过程中,除了主要反应CO+H2O=CO2+H2以外,在某种条件下会发生CO分解等其他副反应,分别如下:2CO=C+CO22CO+2H2=CH4+CO2CO+3H2=CH4+H2OCO2+4H2=CH4+2H2O这些副反应都消耗了原料气中的有效气体,生成有害的游离碳及无用的甲烷,避免副反应的最好方法就是使用选择性好的变换催化剂。
一、变换反应的热效应一氧化碳变换反应是一个放热反应,CO+H2O=CO2+H2+41kJ/gmol反应的热效应视H2O的状态而定,若为液态水,则是微吸热反应,若是水蒸气,则为放热反应。
变换反应的反应热随温度的升高而降低,具体反应热列表如下:表1 CO+H2O=CO2+H2的反应热温度℃25 200 250 300 350 400 450 500 550 △HkJ/gmol 41 39.8 39.5 39 38.5 38 37.6 37 36.6压力对变换反应的反应热影响较小,一般不做考虑。
二、变换反应的化学平衡1、变换反应的平衡常数变换反应的平衡常数随压力的增加而减小,而且与原料气组成有关,CO变换反应是可逆放热反应,平衡常数随着温度的升高而降低。
2、变换率和平衡变换率CO的变换程度通常用变换率来表示,它定义为反应后变换了的CO量与反应前气体中CO量之比。
CO变换率X%=(n co0-n co)/n co0×100式中n co0、n co分别表示变换反应前后的CO摩尔数。
反应达到平衡时的变换率叫做平衡变换率。
增加内容从以上的讨论可以得出:⑴降低反应温度,或增加蒸汽用量,可使反应向生成H2和CO2的方向进行,而降低变换气中CO的平衡浓度,若温度高,蒸汽用量少,可能使反应发生逆向,CO浓度反而比原料气中CO增加。
⑵在变换气中CO浓度一定的条件下,降低反应温度是降低蒸汽用量的必要手段。
⑶在不能降低反应温度的条件下,只求降低变换气中CO的浓度将会使蒸汽用量增加,因此,工艺上必须选择合适的变换气CO含量。
三、变换反应的动力学1、反应机理研究表明,变换反应进行时,水蒸气分子首先在催化剂表面形成吸附层,由于CO分子的碰撞而生成CO2,并离开催化剂表面。
2、扩散过程的影响一般认为,对于变换反应,内扩散的影响不容忽视。
内表面利用率不仅与催化剂的尺寸、结构及反应活性有关,而且与操作温度及压力等因素有关。
对于同一尺寸的催化剂,在相同压力下由于温度的升高,CO扩散速度有所增加,但在催化剂内表面反应的速度常数增加更为迅速,总的结果是温度升高,内表面利用率降低。
在相同的温度及压力下,小颗粒的催化剂具有较高的内表面利用率,这是因为催化剂尺寸越小,毛细孔的长度越短,内扩散阻力越小,故内表面利用率较高。
对于同一尺寸的催化剂,在相同温度下,随着压力的提高,反应速度增大,而CO有效扩散系数又显著变笑,故内表面利用率随压力的增加而迅速下降。
第二节中变催化剂早期的变换催化剂的研究工作在于提高活性,降低活行温度下限,抑制生成碳黑、甲烷的副反应,也就是提高催化剂的选择性。
后来在以Fe2O为主体的基础上,对添加Cr、Al、Cu、Zn、CO、Ni、Mn 和K的氧化物进行了大量研究工作,从而发现它们可以提高催化剂的活性、改善催化剂耐热及抗毒性能。
最后确定了以Fe2O3为主体,Cr2O3为主要添加剂的Fe-Cr系催化剂,一般含Fe2O380~90%,含Cr2O37~14%,并含有K2O、Al2O3等成分。
一、制备方法活性、选择性及使用寿命是催化剂的重要性能,这些性质与它的物理和化学结构有着密切的关系,而催化剂的物理和化学结构是由制备条件所控制的。
国内外Fe-Cr系催化剂制备方法有三种。
⑴机械混合法先将FeSO4溶解,在一定条件下加入(NH4)2CO3中和,制取的FeCO3经过热煮、水洗、过滤、干燥而得半成品,然后按规定的比例加入CrO3,有些还加入KOH、MgO等,混合后碾压,再造粒、干燥、打片、焙烧等制得成品。
此方法的优点是:方法简单,操作容易,处理量大。
但操作条件差,从微观角度来说,各组分混合可能不十分均匀。
⑵混沉法为了改善操作条件,将中和后的FeCO3经热煮后借助二价铁的还原性,加入CrO3将六价铬还原为三价铬。
其他操作同机械混合法。
由于改善了操作条件,减少了六价铬对人体的毒害,组分间的混合也比较均匀,提高了产品产量。
但各组分也可能仍不均匀。
上述两种方法,一般都采用(NH4)2CO3作为沉淀剂,在焙烧过程中,往往因碳酸盐分解而使催化剂强度降低,在使用过程中易粉化。
⑶共沉法该法是将催化剂各组分液相混合,并有碱为沉淀剂。
在一定的条件下,使之同时沉淀出来,因此各组分的均匀程度是比较好的。
所以产品质量稳定,活性高,强度好。
但是,沉淀的料浆是氢氧化物胶体结构,给洗涤带来了很大麻烦,并且硫酸根不易洗去,本体含硫高,但所得催化剂成品质量好,目前还是Fe-Cr系催化剂的最好制备方法。
为了解决催化剂本体含硫高的问题,现在已研究采用铁的硝酸盐代替F eSO4作为原料,以共沉法工艺生产高变催化剂。
二、中变催化剂的型号、组分、作用国内主要的中变催化剂:B107、B109、B112、B113、B114、B115、B116、B117、WB-2、WB-3、DGB、B118、B121等,其特性见下表:铁的氧化物是中变催化剂的活性组分,但纯Fe3O4的活性温度范围很窄,而且在低汽气比条件下有可能发生过度还原而变为FeO,甚至还原到铁,从而引起CO的甲烷化和歧化反应。
工业上用的中变催化剂都是添加Cr2O3的,它起稳定剂的作用,可以防止和延缓催化剂因高温烧结而使晶粒长大和表面积减小,当Fe2O3还原成Fe3O4时,Cr2O3可提高活性相Fe3O4的分散度,增大比表面积。
导致催化剂活性增加。
铬的氧化物还起另外一个作用,在一般条件下,从Cr3+转变为Cr是非常困难的,而Fe3+还原为Fe是比较容易的,因而在反应条件下Cr3+可以防止铁氧化物的过度还原。
在中变催化剂中,钾是有效的助催化剂,钾含量不同的催化剂其活性有很大差别。
加入少量的钾盐对于催化剂的活性、耐热性和强度都是有利的。
就容易使催化剂结皮、阻塞孔道,致使活性下降和床层阻力上涨。
催化剂一般含0.2~0.4%的K2O。
三、物理结构与活性和强度的关系中变催化剂中的Fe2O3需经还原成Fe3O4后才具有活性,但在还原过程中铁的氧化物或盐类都会发生变化,并对最终催化剂的活性和强度有很大的影响。
研究表明,催化剂活性随Cr2O3的量增至14%而达到最大值,一般在实际生产中,工业上中变催化剂的Cr2O3含量都小于14%。
另外Cr2O3进入了Fe3O4的晶格以后,形成了固溶体。
这种Fe3O4-Cr2O3与Fe3O4相比,具有较高的分散度和比表面积以防止Fe3O4的再结晶。
中变催化剂往往是由于压力降的上涨而不是因活性的丧失而停止使用的,即催化剂的强度对它的使用寿命起很重要的作用。
引起催化剂破碎的原因有:⑴搬运过程中磨损;⑵装填过程中互相冲击;⑶升温还原和生产过程中催化剂某些组分还原和氧化引起应力变化;⑷生产过程中的压力降、催化剂重量以及因床层和反应器的热胀冷缩而引起的外力。
前两种原因引起的破坏与催化剂的制作工艺有关,后两种原因引起的破坏与催化剂的还原情况和使用情况有关。
中变催化剂在开始投入使用后,其强度会下降,主要是由于催化剂在升温和还原前后结构上的变化引起的。
因此在升温还原过程中要严格控制升温速率,控制升温过程中水和二氧化碳的放出速度,如果还原速度太快以及水和二氧化碳放出的量过大,催化剂的孔结构会发生剧烈变化,强度会严重减弱。
另外在升温还原过程中,催化剂的晶体结构也发生变化,也引起其强度降低。
四、中变催化剂的主要特性中变催化剂具有相当高的选择性,在正常操作条件下不会发生甲烷化和析碳反应,中变催化剂的使用寿命,与它的活性、强度、和操作条件有关,它的耐热性和抗毒性也与活性和强度有关,而且大型化工企业的中变催化剂的本体含硫量也有很高的要求。
1、活性操作温度、催化剂颗粒大小和毒物等对中变催化剂的活性都有影响。
⑴操作温度:催化剂在生产过程中必须具有稳定的活性,即活性随时间的下降速度越慢越好。
温度对活性的下降速度影响很大。
随着时间的延长,活性逐渐衰退,可以采用提高操作温度的方法以弥补活性的衰退,但操作的温升范围是有限的,一般只有30~50℃。
必须慎重,分几年内逐步升温,否则将缩短催化剂的使用寿命。
⑵催化剂颗粒大小:中变催化剂的活性随颗粒的减小而增加。
当压力增大时,影响更为显著。
但是最适宜的颗粒大小还必须考虑变换炉的阻力降等因素。
⑶毒物:原料气中的某些杂质会使中变催化剂的活性显著下降。
最常见的毒物是H2S ,H2S与催化剂反应式如下:Fe3O4+H2S+H2=FS+H2O上述反应是可逆的,因此H2S不是永久性毒物。
一般认为,当气体中H2S的浓度低于200ppm时,活性不受影响。
一旦中毒了,当使用含H2S低的原料气时,催化剂的活性也可以较快地恢复。
但如果这一过程反复进行,实际上会加快催化剂活性下降速度,而且将引起催化剂的破碎。
2、强度催化剂的强度是评价催化剂性能优劣的重要指标,对于中变催化剂来说,甚至比活性更为关键。
因此必须保证还原态的中变催化剂具有很好的强度。
从目前的催化剂制造技术来说,已能生产密度较低且还原态强度高的催化剂了。
3、催化剂的本体含硫量本体含硫量高的催化剂耐毒性比较好,它们一般都能在H2S含量在20~200ppm的系统中使用,而活性不受影响。