粉末冶金模具设计教学内容
第六章+粉末冶金模设计
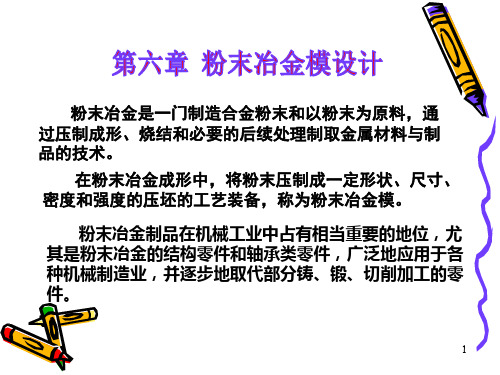
30
<压铸模、锻模及其他模具>
1.压坯尺寸变化影响因素
造成压坯尺寸变化的主要影响因素来自成形、烧结和精整。
31
<压铸模、锻模及其他模具>
2.工艺参数对压模尺寸的影响
(1)金属粉末的松装密度ρ粉 金属粉末的松装密度直接影响模镗的高度。
(2)压缩比K 压缩比是指粉末被压缩前的体积与压缩后压坯的体积比。
29
<压铸模、锻模及其他模具>
二.粉末冶金模主要零件尺寸计算
粉末冶金制品的生产过程一般为混料-成形-烧结-精 整(或复压)。
成型模具尺寸的计算步骤为:
(1)选定精整方式及精整模具尺寸,根据精整余量确定 烧结制品尺寸; (2)根据所选的烧结材料和制造工艺的烧结收缩量(或 膨胀量),确定压坯尺寸; (3)根据压坯尺寸确定成形模具尺寸。 粉末冶金模的主要零件有凹模、芯棒和模冲。
24
<压铸模、锻模及其他模具>
2.压机分类:
按传统机构可分为:液压式压机和机械式压机两类。 按模具操作方式可分为:下模冲固定式压机、凹模固定式压机和上 模冲固定式压机三大类。 按模冲动作方式可分为:上模冲单向压制压机、下模冲单向压制压 机、双向压制压机、多模冲压制压机和模冲回转压制压机等五大类。
在选用时,要考虑的因素主要有压制压力、脱模压力、 工作台面尺寸和行程等因素。 二.压机参数的确定
(4)保证压模刚度和强度
21
<压铸模、锻模及其他模具>
3.压模精度设计
(1)压模的尺寸精度
压模径向尺寸主要受模具尺寸精度的影响;轴向尺寸主要 受压机动作、压机本身精度、装粉精度的影响。大致可分为粗、 中、精三级。
(2)压坯的位置精度
粉末冶金模具设计资料PPT课件

形状完整,具有一定强度
3.5 压制过程的图示
03.11.2020
2
•压制压力的计算
模压过程的总压制力等于净压力与外摩擦力 之和
单位压制压力与压坯密度定量关系的研究, 是近60年来粉末成形理论研究的主要内容
•脱模力的计算
压制压力去掉后,侧压力因为高度方向的弹 性后效,侧压力会下降35~77%
03.11.2020
整形区的单位精整压力为
Pc=σ/[1+(S+μQ)/2S2]
在此: σ为单向压缩条件下材料塑性变形的抗 力
通常内胀外精整方式的精整压力几乎只有外箍 内精整方式的十分之一
材料塑性变形抗力与材质、组织和孔隙率密切
关连03.11.2020
7
•压坯密度分布与压制方式的关系
压坯密度分布不均匀的地方,常常是压坯截 面积发生变化的分界处;脱模时这种部位也 容易产生裂纹,烧结时易引起变形。
d粉—粉末松装密度; d1—第一次压制后压坯平均密度; 第一次压制后:d粉H粉=d1h1 x=h1-h
d粉H粉=d1(h+x) ∴x=(d粉H粉-d1h)/d1 第二次压制后:d粉H粉=dh
d粉=d ·h/H粉 x=(d-d1)h/d1; k=H粉/h=(l+h)/h ∴x=(d-d1)l/d1(k-1); y=x/l ·11000%
03.11.2020
21
03.11.2020
22
03.11.2020
23
不等高压坯压模的设计原理
影响压制过程中粉末流动方式的因素: 粉末的流动性 装粉方法 外摩擦力 上下模冲设计 压坯横截面形状
在压制的不同阶段,粉末流动方式也不同
03.11.2020
粉末冶金模具设计
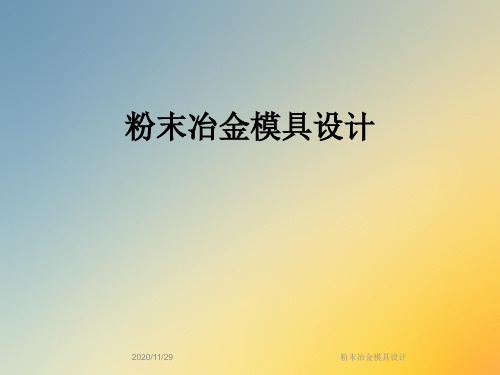
2020/11/29
粉末冶金模具设计
•带斜面的第五类压坯
当压坯斜面与垂直方向的夹角超过25°~30°,或 者具有多个斜面和平面时,一般按照斜面和平面的 分界线设计组合下模冲。斜面的装粉高度等于斜面 的压坯平均高度乘以粉末填装系数。
x=(d2-d1)h/d1
或者 y=x/l=100(d2-d1)/d1(k-1)
其中:d2为要求的压坯平均密度;d1为单向压 制的平均密度;h为压坯高度;k为压缩比;l 为装粉高度与压坯高度之差。
2020/11/29
粉末冶金模具设计
非同时双向压制原理为压模结构设计提供了 压坯密度均匀分布的理论基础;也为粉末压 机的设计提供了重要基础,使得多凸轮和凸 轮曲柄粉末压机更好地满足粉末压坯密度均 匀分布的要求。
2020/11/29
粉末冶金模具设计
摩擦压制
在压制过程中,让阴模或芯杆与样品侧面产 生同向相对移动,即运动得更快,借助粉末 与模壁之间的摩擦,带动与阴模或芯杆接触 的粉末层移动,从而可改善沿压坯高度方向 的密度分布均匀性。
2020/11/29
粉末冶金模具设计
2020/11/29
粉末冶金模具设计
2020/11/29
距离,用先压缩高区粉末再同时压缩高低区粉末的
方法,使压坯各横截面上的粉末受到相同的压缩程
度。
2020/11/29
粉末冶金模具设计
2020/11/29
粉末冶金模具设计
如果压坯中间带内、外台阶,除不同横截面需要 设计组合下模冲外,还有根据粉末移动成形法的 要求设计组合上模冲。
粉末冶金材料模具设计
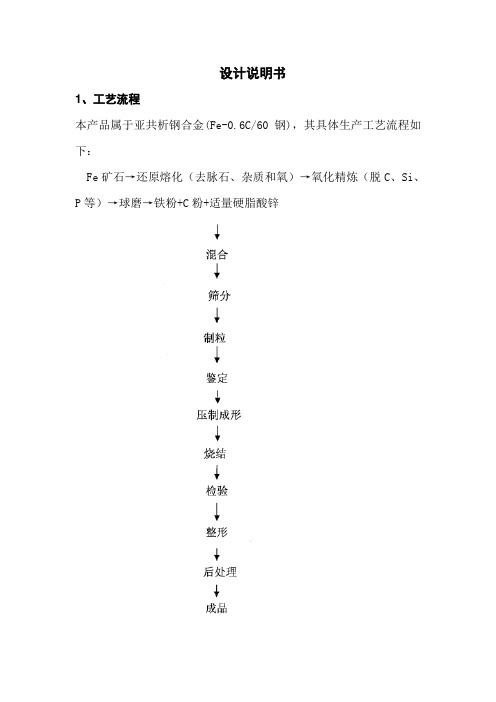
设计说明书1、工艺流程本产品属于亚共析钢合金(Fe-0.6C/60钢),其具体生产工艺流程如下:Fe矿石→还原熔化(去脉石、杂质和氧)→氧化精炼(脱C、Si、P等)→球磨→铁粉+C粉+适量硬脂酸锌2、压坯设计2.1产品零件分析该产品采用Fe-0.6C(60钢),属于铁基制品,其制品密度依靠较高的压坯密度来达到,因此,在压制成形时需要采用较高的单位压力(一般在400-500MPa)。
由于该产品零件形状比较简单,带一个外台阶,采用简单的单上双下模冲即可成形,并使其密度分布均匀。
有配合、定位、相对运动要求的零部件,产品尺寸精度和形位精度及表面粗糙度要求较高,因此,该产品的的尺寸精度定义为IT8、形位精度如图所示为7级,表面粗糙度精度要求为7级。
2.2压坯精度设计由模具设计任务书的零件成品图可得知该产品压坯同轴度需控制在0.08mm,相当于IT10级;压坯垂直度控制为0.1mm,相当于IT11级;压坯侧面平行度为0.15mm,相当于IT12级。
2.3压坯密度和单重的确定由于已知压坯密度ρ=6.6g/cm3,因此压坯单重W=ρ×V ,由成品图给数据计算其压坯体V=h×S,算的V=166.8cm3 ,所以求的压坯单重W=6.6×166.8=1100.8g。
3、压机与压制方式选择3.1压机压力选择铁基制品一般采用固相烧结,其制品密度除了依靠烧结温度、保温时间之外,在一定程度上还依靠较高的压坯密度来达到,因此该产品采用500MPa的单位压力。
根据任务书要求,截面积S=74.0cm2 ,所以F=P×S=5×74=370t脱模压力,根据实际生产经验,铁基压坯的脱模压力P脱模≈0.13P=0.13×500MPa=65MPa3.2压制类型的选择年生产量为50万件,假设每年的工作时间为300天,每天工作时间为8小时,则p=500000/300/8/60=3.47=4件/min,所以选择自动压制。
粉末冶金模具设计-PPT精品文档

4
其中:
∑R :卸压后阴模半径上剩余的变形量; j: 剩余侧压强与侧压强之比,决定于模具的刚度;
剩
m:阴模外径与内径之比;
ρ:压坯的相对密度
当相对密度为:0.80~0.85时,m=2~4,可粗略 估算: 对于铁基:P侧剩=0.18~0.20P
对于铜基: P侧剩=0.20~0.22P
2019/3/18 5
•(S +S )/S>K时,如果(S +S )/2> (S -S ), 或者圆筒形压坯D >T,可采用摩擦芯杆压制
侧阴 侧芯 侧阴 侧芯 侧阴 侧芯 内
2019/3/18
21
2019/3/18
22
3.4 组合模具的设计原理
3.5
压制过程的图示
2
2019/3/18
•压制压力的计算
模压过程的总压制力等于净压力与外摩擦力 之和 单位压制压力与压坯密度定量关系的研究, 是近60年来粉末成形理论研究的主要内容 •脱模力的计算 压制压力去掉后,侧压力因为高度方向的弹 性后效,侧压力会下降35~77%
2019/3/18 3
当柱状压坯S /S<K或者圆柱体压坯高径比 H/D<K/4时,采用单向压制可以满足压坯密度 分布均匀性的要求
2019/3/18 16
2019/3/18
17
双向压制
S
侧max
/S=[1-(ρ /ρ )m]/μξ=2K
中 上 侧
当柱状压坯K<S /S<2K,或者圆柱体 K/4<H/D<K/2时,采用双向压制、非同时双 向压制、浮动阴模双向压制或者下拉式压制 可以满足压坯密度分布均匀性要求
压力相等时双向压制与非同时双向压制的效 果相同
粉末冶金模具设计 教学大纲
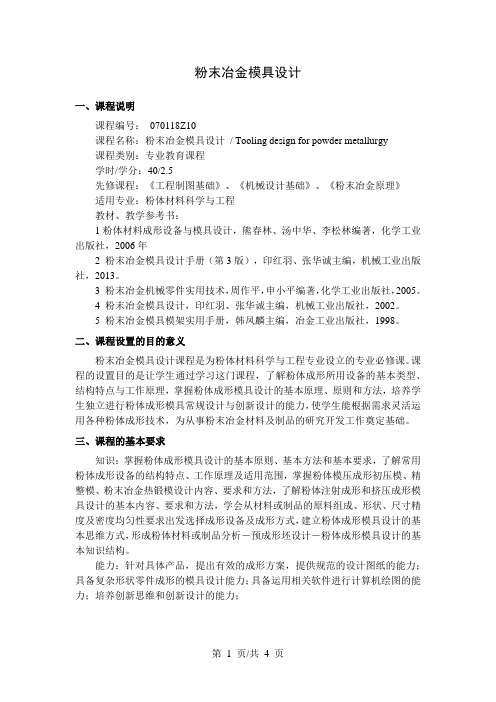
粉末冶金模具设计一、课程说明课程编号:070118Z10课程名称:粉末冶金模具设计/ Tooling design for powder metallurgy课程类别:专业教育课程学时/学分:40/2.5先修课程:《工程制图基础》、《机械设计基础》、《粉末冶金原理》适用专业:粉体材料科学与工程教材、教学参考书:1粉体材料成形设备与模具设计,熊春林、汤中华、李松林编著,化学工业出版社,2006年2 粉末冶金模具设计手册(第3版),印红羽、张华诚主编,机械工业出版社,2013。
3 粉末冶金机械零件实用技术,周作平,申小平编著,化学工业出版社,2005。
4 粉末冶金模具设计,印红羽、张华诚主编,机械工业出版社,2002。
5 粉末冶金模具模架实用手册,韩凤麟主编,冶金工业出版社,1998。
二、课程设置的目的意义粉末冶金模具设计课程是为粉体材料科学与工程专业设立的专业必修课。
课程的设置目的是让学生通过学习这门课程,了解粉体成形所用设备的基本类型、结构特点与工作原理,掌握粉体成形模具设计的基本原理、原则和方法,培养学生独立进行粉体成形模具常规设计与创新设计的能力,使学生能根据需求灵活运用各种粉体成形技术,为从事粉末冶金材料及制品的研究开发工作奠定基础。
三、课程的基本要求知识:掌握粉体成形模具设计的基本原则、基本方法和基本要求,了解常用粉体成形设备的结构特点、工作原理及适用范围,掌握粉体模压成形初压模、精整模、粉末冶金热锻模设计内容、要求和方法,了解粉体注射成形和挤压成形模具设计的基本内容、要求和方法,学会从材料或制品的原料组成、形状、尺寸精度及密度均匀性要求出发选择成形设备及成形方式,建立粉体成形模具设计的基本思维方式,形成粉体材料或制品分析-预成形坯设计-粉体成形模具设计的基本知识结构。
能力:针对具体产品,提出有效的成形方案,提供规范的设计图纸的能力;具备复杂形状零件成形的模具设计能力;具备运用相关软件进行计算机绘图的能力;培养创新思维和创新设计的能力;素质:建立科学设计,用户至上的观念,通过课程中的分析、讨论和辩论培养良好的沟通交流素质;通过课外导学的模式,提升自主学习、在实践中学习和终身学习的意识,形成不断学习和适应发展的素质。
第8教学单元粉末冶金模具尺寸设计原则.doc
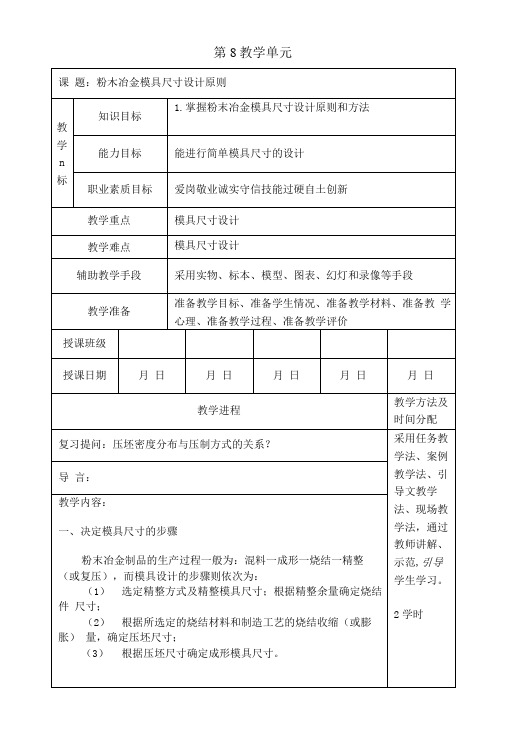
第8教学单元课 题:粉木冶金模具尺寸设计原则教 学 n 标知识目标 1.掌握粉末冶金模具尺寸设计原则和方法能力目标 能进行简单模具尺寸的设计 职业素质目标 爱岗敬业诚实守信技能过硬自土创新 教学重点 模具尺寸设计 教学难点 模具尺寸设计辅助教学手段 采用实物、标本、模型、图表、幻灯和录像等手段 教学准备准备教学目标、准备学生情况、准备教学材料、准备教 学心理、准备教学过程、准备教学评价授课班级授课日期月 日月 日 月 日月 日月 日 教学进程教学方法及 时间分配 复习提问:压坯密度分布与压制方式的关系? 采用任务教 学法、案例 教学法、引 导文教学 法、现场教 学法,通过 教师讲解、 示范,引导 学生学习。
2学时导 言: 教学内容:一、决定模具尺寸的步骤粉末冶金制品的生产过程一般为:混料一成形一烧结一精整 (或复压),而模具设计的步骤则依次为:(1) 选定精整方式及精整模具尺寸;根据精整余量确定烧结件 尺寸;(2) 根据所选定的烧结材料和制造工艺的烧结收缩(或膨胀) 量,确定压坯尺寸;(3) 根据压坯尺寸确定成形模具尺寸。
这主要是由于造成压坯尺寸变化的因素来自成形、烧结和精整。
下面逐一加以说明。
先假设粉末冶金制品的形状如图所示,当粉末在模具中成形时,加压(300-800MPa)后,将会使阴模与第一下模冲产生径向应变。
待压坯由模具中脱出之际,内应力得以释放,这时在径向产生胀大,表现为压制回弹。
为减小压制回弹,提高阴模刚性,一般采用将阴模红装以保护套,以及使用杨氏模量高于合金工具钢与高速钢的硬质合金制作阴模。
成形后的压坯的C部分比 B部分的同弹要大,主要是由于在阴模与第一下模冲之间留有适当间隙,成形时,被撑大的第一下模冲便变为挤住阴模的状态。
模冲因受形状的制约,无法用提高阴模刚性的办法来提高模冲的刚性。
下模冲与阴模的间隙一般为径向尺寸的0. 03%-0. 1%,间隙过大则易造成模冲破损。
压坯经过烧结后,一般会产生尺寸变化,或收缩或膨胀,统称为烧结收缩量,用百分数来表示。
粉末冶金模具设计(1)
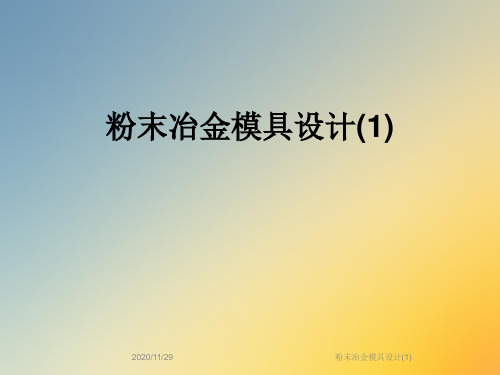
当压坯斜面与垂直方向的夹角超过25°~30°,且 斜面很长时,应该设计组合模冲来成形斜面部分。
2020/11/29
粉末冶金模具设计(1)
•带曲面的第五类压坯
要根据曲面变化分界线设计组合下模冲;装粉高度 等于这部分曲面的压坯平均密度与粉末填装系数之 积。
2020/11/29
粉末冶金模具设计(1)
•精整压力的计算
外箍内的精整: 精整压力Fc=F1+F2+F3
其中:F1为实现轴套纯变形所需要的力;
F2为克服整形区外摩擦所需的力;
F3克服内摩擦所需的力。
精整压力计算公式Fc=Pc (S+μQ)+0.58σαS2
其中:Pc 为精整区的平均单位压力;Q为阴模精 整区的工作面积;σ为精整件的塑性变形抗力
d粉H粉=d1(h+x) ∴x=(d粉H粉-d1h)/d1 第二次压制后:d粉H粉=dh
d粉=d ·h/H粉 x=(d-d1)h/d1; k=H粉/h=(l+h)/h ∴x=(d-d1)l/d1(k-1); y=x/l ·100%
粉末冶金模具设计(1)
压力相等时双向压制与非同时双向压制的效 果相同
2020/11/29
粉末冶金模具设计(1)
•压制方式的选择依据
压制方式和方法不同,上、下模冲、芯杆和阴 模相对于粉末压坯的相对运动方向及速度也不 同,从而使外摩擦对压坯密度的均匀分布产生 有害或者有利的影响。
单向压制
S侧max/S=[1-(ρ下/ρ上)m]/μξ=K
当柱状压坯S侧/S<K或者圆柱体压坯高径比 H/D<K/4时,采用单向压制可以满足压坯密度 分布均匀性的要求
- 1、下载文档前请自行甄别文档内容的完整性,平台不提供额外的编辑、内容补充、找答案等附加服务。
- 2、"仅部分预览"的文档,不可在线预览部分如存在完整性等问题,可反馈申请退款(可完整预览的文档不适用该条件!)。
- 3、如文档侵犯您的权益,请联系客服反馈,我们会尽快为您处理(人工客服工作时间:9:00-18:30)。
其中:Pc 为精整区的平均单位压力;Q为阴模精
整区的工作面积;σ为精整件的塑性变形抗力
(三向压力);α为阴模入口端的角度;S2为精整
区轴套的横截面积
2020/7/2
5
内胀外精整
精整压力计算与外箍内时相同;
整形区的单位精整压力为
Pc=σ/[1+(S+μQ)/2S2]
在此: σ为单向压缩条件下材料塑性变形的抗 力
对于铁基:P侧剩=0.18~0.20P 对于铜基: P侧剩=0.20~0.22P
2020/7/2
4
•精整压力的计算
外箍内的精整: 精整压力Fc=F1+F2+F3
其中:F1为实现轴套纯变形所需要的力;
F2为克服整形区外摩擦所需的力;
F3克服内摩擦所需的力。
精整压力计算公式Fc=Pc (S+μQ)+0.58σαS2
•模具表面质量
•摩擦力
•压制时粉体产生柱式流动,几乎不产生明显
的横向流动 2020/7/2
7
压坯中中立层的位置可以表示压坯密度分布
的均匀程度。通过压制方式和压模结构合理
选择使中立层2边受相同压缩,提高密度分布
均匀性 2020/7/2
8
2020/7/2
d粉—粉末松装密度; d1—第一次压制后压坯平均密度; 第一次压制后:d粉H粉=d1h1 x=h1-h
2020/7/2
19
选择原则
•(S侧阴+S侧芯)/S<K或者圆筒形压坯h/T<K/2时,可 采用单向压制;
•(S侧阴+S侧芯)/S>K时,如果(S侧阴+S侧芯)/2< (S侧阴-S侧芯), 或者圆筒形压坯D内<T,可采用双向压制;
•(S侧阴+S侧芯)/S>K时,如果(S侧阴+S侧芯)/2> (S侧阴-S侧芯), 或者圆筒形压坯D内>T,可采用摩擦芯杆压制
单向压制
S侧max/S=[1-(ρ下/ρ上)m]/μξ=K
当柱状压坯S侧/S<K或者圆柱体压坯高径比 H/D<K/4时,采用单向压制可以满足压坯密度 分布均匀性的要求
2020/7/2
15
2020/7/2
16
双向压制
S侧max/S=[1-(ρ中/ρ上)m]/μξ=2K
当柱状压坯K<S侧/S<2K,或者圆柱体 K/4<H/D<K/2时,采用双向压制、非同时双 向压制、浮动阴模双向压制或者下拉式压制 可以满足压坯密度分布均匀性要求
x=(d2-d1)h/d1
或者 y=x/l=100(d2-d1)/d1(k-1)
其中:d2为要求的压坯平均密度;d1为单向压 制的平均密度;h为压坯高度;k为压缩比;l 为装粉高度与压坯高度之差。
2020/7/2
10
非同时双向压制原理为压模结构设计提供了 压坯密度均匀分布的理论基础;也为粉末压 机的设计提供了重要基础,使得多凸轮和凸 轮曲柄粉末压机更好地满足粉末压坯密度均 匀分布的要求。
采用添加润滑剂、振动装粉、过量装粉和吸入装 粉方法可以消除拱桥现象。
压制开始阶段
拱桥现象被破坏;当压坯各横截面上的粉末受到 相同程度的压缩时,只发生柱状流动;如果压坯 各横截面上的粉末受到不同程度的压缩,先受压 缩或者受压缩程度大的截面上的粉末会向其他处 发生横向流动。
是否发生横向流动取决于各截面的受压缩程度和
2020/7/2
17
2020/7/218摩擦芯杆压制上模冲强迫芯杆一起向下移动,且芯杆下 移的速度大于粉末下移的速度,因而靠芯 杆与粉末之间的摩擦力带动粉末向下移动。
[(S侧阴-S侧芯)/S]max=[1-(ρ下/ρ上)m]/μξ=K 对于圆筒形压坯的高与壁厚之比:
h/T=K(1+D内/T)/2 摩擦芯杆压制特别适合于大孔薄壁压坯
模202冲0/7/2形状
24
压制最后阶段
粉末冶金模具设计
•压制压力的计算
模压过程的总压制力等于净压力与外摩擦力 之和
单位压制压力与压坯密度定量关系的研究, 是近60年来粉末成形理论研究的主要内容
•脱模力的计算
压制压力去掉后,侧压力因为高度方向的弹 性后效,侧压力会下降35~77%
2020/7/2
2
在低速高单位压制压力条件下,塑性金属粉 末易发生“模瘤”;模具表面质量差、润滑 不良和模温过高,加重模瘤现象。
严重时脱模压力超过压制压力,使得模具拉 伤。
无润滑塑性金属粉末应当避免高压压制
F脱=μ静P侧剩S侧 P侧剩=E∑R剩(m2-1)/2R
P侧剩=jξ0ρP
2020/7/2
3
其中:
∑R剩:卸压后阴模半径上剩余的变形量; j: 剩余侧压强与侧压强之比,决定于模具的刚度;
m:阴模外径与内径之比; ρ:压坯的相对密度 当相对密度为:0.80~0.85时,m=2~4,可粗略 估算:
d粉H粉=d1(h+x) ∴x=(d粉H粉-d1h)/d1 第二次压制后:d粉H粉=dh
d粉=d ·h/H粉 x=(d-d1)h/d1; k=H粉/h=(l+h)/h ∴x=(d-d1)l/d1(k-1); y=x/l ·1090%
压力相等时双向压制与非同时双向压制的效 果相同
非同时双向压制中第二次压制的模冲移动距 离:
通常内胀外精整方式的精整压力几乎只有外箍 内精整方式的十分之一
材料塑性变形抗力与材质、组织和孔隙率密切
关连2020/7/2
6
•压坯密度分布与压制方式的关系
压坯密度分布不均匀的地方,常常是压坯截 面积发生变化的分界处;脱模时这种部位也 容易产生裂纹,烧结时易引起变形。
影响压坯密度分布均匀性的因素:
•粉末成分和性能
2020/7/2
20
2020/7/2
21
2020/7/2
22
不等高压坯压模的设计原理
影响压制过程中粉末流动方式的因素: 粉末的流动性 装粉方法 外摩擦力 上下模冲设计 压坯横截面形状
在压制的不同阶段,粉末流动方式也不同
2020/7/2
23
装粉阶段
粉末以散状流动的方式充填模腔,由于摩擦力的 影响容易产生“拱桥”现象。
2020/7/2
11
摩擦压制
在压制过程中,让阴模或芯杆与样品侧面产 生同向相对移动,即运动得更快,借助粉末 与模壁之间的摩擦,带动与阴模或芯杆接触 的粉末层移动,从而可改善沿压坯高度方向 的密度分布均匀性。
2020/7/2
12
2020/7/2
13
2020/7/2
14
•压制方式的选择依据
压制方式和方法不同,上、下模冲、芯杆和阴 模相对于粉末压坯的相对运动方向及速度也不 同,从而使外摩擦对压坯密度的均匀分布产生 有害或者有利的影响。