粉末冶金:钢压模具设计
粉末冶金模具设计算
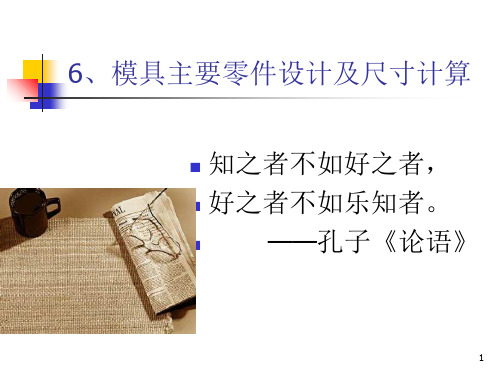
38
(一)金属粉末的松装密度
金属粉末的松装密度直接影响模腔的高度。此参 数选择不当,自动装粉时则会造成粉料装不下, 或粉料装得太多的现象。 实际生产中,松装密度在一定范围内有波动,为 此,在结构设计中一般考虑了调节装粉高度的装 置,但调节范围不宜过大。
29
Hf—阴模高度 H1—压坯台阶高度 H10—压坯台阶1的装粉高度
H2—压坯总高度 H20—压坯台阶2的装粉高度
30
(二)模具高度的计算
(1)阴模
阴模高度 Hf一般由三部分高度组成, 即
Hf=H0+H1+H2
式中
Hf——阴模高度(mm); H0——装粉高度(mm) ; H1——下模冲定位高度。一般为10~50mm ; H2——手动模装粉锥高度(mm)。不需要时H2=031
6、模具主要零件设计及尺寸计算
知之者不如好之者,
好之者不如乐知者。
——孔子《论语》
1
6.1模具主要零件设计
2
模具主要零件包括: 阴模、芯棒、模冲
3
6.1.1对模具主要零件的一般要求:
(一)成形模具 1.阴模要求 1)高度; 2)保证压坯的几何形状和尺寸精度 3)粗糙度要低; 4)硬度高、耐磨性好 5)足够的强度和刚性; 6)合适的阴模材料 7)便于制造,使用安全,便于操作 8)容易脱模;
39
1.松装密度的影响因素
1)粉料的成分、 2)颗粒形状、 3)粒度组成 4)流动性等。
40
2.调节松装密度措施有:
1)将成分相同而松装密度不同的各批粉末按比例 混合,以获得所需要的松装密度。
例如,可合批或将还原铁粉与雾化铁粉混合等。 2)改变粉末的粒度组成。 一般粗中细粉末按适当比例相配,可增大松装密度。 3)改变混料工艺。 如延长混料时间,可提高松装密度。 4)增加润滑剂。 如硬脂酸锌或少层整体阴模
粉末冶金模具设计
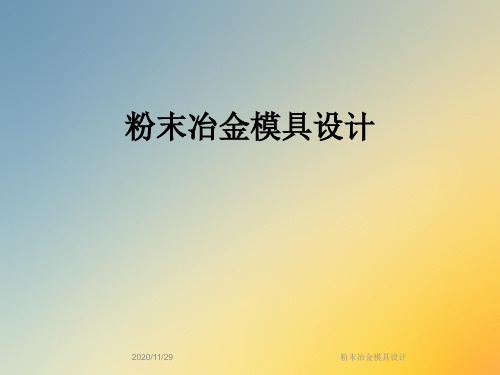
2020/11/29
粉末冶金模具设计
•带斜面的第五类压坯
当压坯斜面与垂直方向的夹角超过25°~30°,或 者具有多个斜面和平面时,一般按照斜面和平面的 分界线设计组合下模冲。斜面的装粉高度等于斜面 的压坯平均高度乘以粉末填装系数。
x=(d2-d1)h/d1
或者 y=x/l=100(d2-d1)/d1(k-1)
其中:d2为要求的压坯平均密度;d1为单向压 制的平均密度;h为压坯高度;k为压缩比;l 为装粉高度与压坯高度之差。
2020/11/29
粉末冶金模具设计
非同时双向压制原理为压模结构设计提供了 压坯密度均匀分布的理论基础;也为粉末压 机的设计提供了重要基础,使得多凸轮和凸 轮曲柄粉末压机更好地满足粉末压坯密度均 匀分布的要求。
2020/11/29
粉末冶金模具设计
摩擦压制
在压制过程中,让阴模或芯杆与样品侧面产 生同向相对移动,即运动得更快,借助粉末 与模壁之间的摩擦,带动与阴模或芯杆接触 的粉末层移动,从而可改善沿压坯高度方向 的密度分布均匀性。
2020/11/29
粉末冶金模具设计
2020/11/29
粉末冶金模具设计
2020/11/29
距离,用先压缩高区粉末再同时压缩高低区粉末的
方法,使压坯各横截面上的粉末受到相同的压缩程
度。
2020/11/29
粉末冶金模具设计
2020/11/29
粉末冶金模具设计
如果压坯中间带内、外台阶,除不同横截面需要 设计组合下模冲外,还有根据粉末移动成形法的 要求设计组合上模冲。
粉末冶金模具及设计介绍
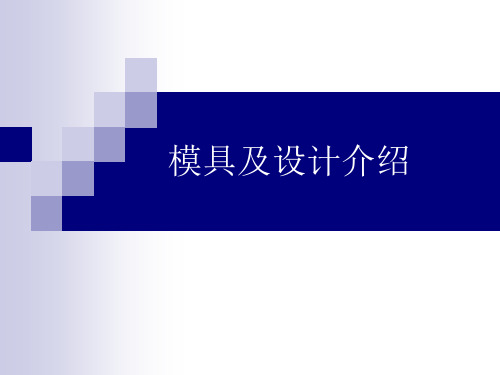
45°
30°
模具耐用设计
1.内外有效段不一样长,有效提高模 具强度; 2.尽可能的内有效段小于外有效段, 节省成本; 3.逃气孔尽可能向上开到根部,提高 强度避免粉末喷出,上二零件不开逃 气孔,在上二冲底部磨小缺口跑气; 4.尽可能大的R弧或斜角过渡,且光 洁度尽可能高,避免应力集中; 5.尽可能小的底座,防止垫片受力时 挠曲导致底座受力后折断; 6.底座倒5°角,防止垫片挠曲,模 冲受力面外移引起模具断裂
模具设计
1.根据产品外形和尺寸、强度要求,制定产品的工艺 流程。 2.计算和设计所需的成形和整形的机台和成形结构。 3.根据产品材质要求,选择成形原料。 4.根据原料变化率和整形、切削余量,设计模具结构 与尺寸。 5.依照成形方式,画出装配图。 6.画出模具各零件图。 7.设计各测量和装模治具。
3V
ห้องสมุดไป่ตู้淬火
HRC61~63 550
9V MH85 ASP23 ASP60 WC
淬火 淬火 淬火
HRC57-59
600
HRC58~60 800 HRC61~63 650 HRC66~69 700
一胜百晶粒特细PM高速工具钢, 成形上下冲,芯棒, 热处理稳定性好,高耐磨损高 适用温压 韧性 一胜百ASP23改进型,替代易崩 适用斜齿轮或台阶中 角的WC,高耐磨损高韧性 模(用40Cr包套)
上下冲特别是长零件温压零件的上下3v淬火hrc6163550美国cpm粉末钢超级的尺寸稳定性可磨削性和韧性替代高合金钢可解决崩角问题成形上下冲特别是9v淬火hrc5759600美国cpm粉末钢超级的尺寸稳定性可磨削性韧性比3v更高可解决崩角问题mh85淬火hrc5860800大同高速钢高耐磨损高韧性齿形下一冲强制用料温压不可用asp23淬火hrc6163650一胜百晶粒特细pm高速工具钢热处理稳定性好高耐磨损高韧性成形上下冲芯棒适用温压asp60淬火hrc6669700一胜百asp23改进型替代易崩角的wc高耐磨损高韧性适用斜齿轮或台阶中模用40cr包套wchra91yg6hra89yg8hra87yg15国600进口1000g代表钴含量越高韧性越好耐磨性也较差一般采用超微粒春宝国产稍差常用模具材料热处理工艺牌号使用硬度热处理温度保温时回火时间温度冷却方式sldhrc5759hrc60611030125分钟3小时220160风v4hrc5657hrc60611130125分钟3小时220160风skh9hrc5759hrc6061119035分钟3小时605580风cr12hrc4550960100分钟3小时530风40crhrc4550860100分钟3小时450风1
粉末冶金模具的设计与制造

粉末冶金模具的设计与制造1. 引言粉末冶金是一种重要的金属制造工艺,广泛应用于汽车、航空航天、电子、能源等领域。
在粉末冶金工艺中,模具的设计与制造是关键环节,直接影响产品的质量和性能。
本文将介绍粉末冶金模具的设计与制造过程,包括模具材料的选择、模具的结构设计、加工工艺等内容,以帮助读者全面了解粉末冶金模具的制造方法和技术要点。
2. 模具材料的选择模具材料的选择是粉末冶金模具设计的第一步。
模具材料需要具备一定的硬度、耐磨性和耐各种腐蚀介质的能力。
常用的模具材料有以下几种:•工具钢:具有较高的硬度和韧性,适用于大部分粉末冶金模具的制造。
•高速钢:具有更高的硬度和耐磨性,适用于对模具耐磨性要求较高的情况。
•硬质合金:具有较高的硬度和耐磨性,适用于对模具耐磨性要求极高的情况。
在选择模具材料时,需要根据具体应用场景和成本考虑,综合各种性能指标做出合理选择。
3. 模具的结构设计模具的结构设计是粉末冶金模具制造中的核心环节。
良好的模具结构设计可以提高产品的制造效率和质量,降低生产成本。
以下是模具结构设计的几个要点:•模具的整体结构应该合理,易于安装和拆卸。
模具的结构应简洁、牢固,能够承受制造过程中的力和压力。
•模具的导向和定位系统要设计到位,以确保模具在制造过程中的稳定性和精度。
•模具的开合系统要灵活可靠,能够实现快速开合和调节。
对于大型模具,可以考虑采用液压或气动开合系统。
•模具的冷却系统要充分考虑,以保证模具在制造过程中能够及时散热,提高产品质量和生产效率。
4. 模具的制造过程粉末冶金模具的制造过程主要包括以下几个步骤:4.1 模具设计在模具设计阶段,根据产品的形状和尺寸要求,通过CAD软件进行三维建模。
在设计过程中,要充分考虑模具的可行性和制造工艺,以确保模具的质量和可生产性。
4.2 模具加工模具加工是模具制造的关键环节。
常用的模具加工方法包括数控加工、线切割、铣削等。
在加工过程中,需要根据模具材料和结构要求选择合适的加工工艺,精确控制加工尺寸和表面质量。
粉末冶金原理及模具计算要求
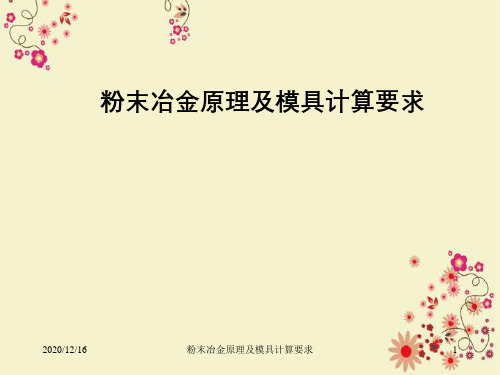
3.4 组合模具的设计原理
形状完整,具有一定强度
3.5 压制过程的图示
2020/12/16
粉末冶金原理及模具计算要求
2
•压制压力的计算
模压过程的总压制力等于净压力与外摩擦力 之和
单位压制压力与压坯密度定量关系的研究, 是近60年来粉末成形理论研究的主要内容
•脱模力的计算
压制压力去掉后,侧压力因为高度方向的弹 性后效,侧压力会下降35~77%
单向压制
S侧max/S=[1-(ρ下/ρ上)m]/μξ=K
当柱状压坯S侧/S<K或者圆柱体压坯高径比
H/D<K/4时,采用单向压制可以满足压坯密度
分布均匀性的要求
2020/12/16
粉末冶金原理及模
粉末冶金原理及模具计算要求
17
双向压制
S侧max/S=[1-(ρ中/ρ上)m]/μξ=2K
压力相等时双向压制与非同时双向压制的效 果相同
非同时双向压制中第二次压制的模冲移动距 离:
x=(d2-d1)h/d1
或者 y=x/l=100(d2-d1)/d1(k-1)
其中:d2为要求的压坯平均密度;d1为单向压 制的平均密度;h为压坯高度;k为压缩比;l 为装粉高度与压坯高度之差。
2020/12/16
•压制时粉体产生柱式流动,几乎不产生明显
的横向流动 2020/12/16
粉末冶金原理及模具计算要求
8
压坯中中立层的位置可以表示压坯密度分布
的均匀程度。通过压制方式和压模结构合理
选择使中立层2边受相同压缩,提高密度分布
均匀性 2020/12/16
粉末冶金原理及模具计算要求
9
2020/12/16
d粉—粉末松装密度; d1—第一次压制后压坯平均密度; 第一次压制后:d粉H粉=d1h1 x=h1-h d粉H粉=d1(h+x) ∴x=(d粉H粉-d1h)/d1 第二次压制后:d粉H粉=dh d粉=d ·h/H粉 x=(d-d1)h/d1; k=H粉/h=(l+h)/h 粉末冶金原理及∴模x具=计(算d要-d求1)l/d1(k-1); y=x/l ·11000%
粉末冶金及模具设计 完整版
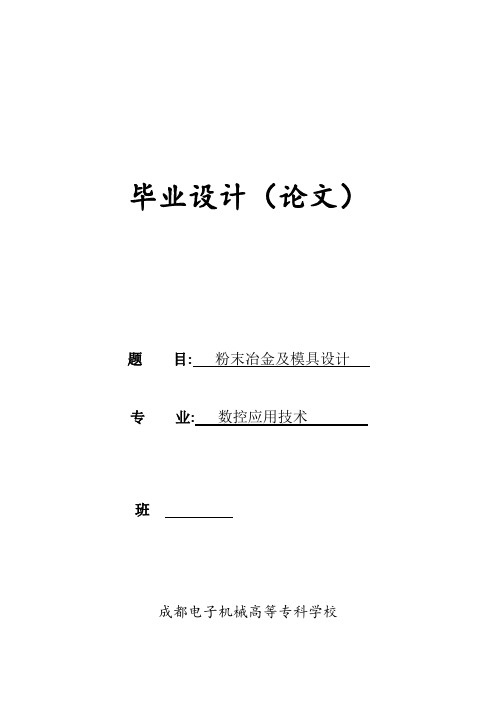
毕业设计(论文)题目:粉末冶金及模具设计专业:数控应用技术班成都电子机械高等专科学校二〇〇七年六月摘要本文主要围绕粉末冶金及模具设计开展了以下几方面的研究1、在粉末冶金技术的特点及其在新材料中的作用进行研究,重点介绍了粉末冶金在工业中的重要性及其压制步骤。
2、在粉末冶金工艺中,根据产品的要求选择金属粉末或非金属粉末为原材料来压制。
3、在粉末冶金模具设计原理方面,本文重点围绕精整模具设计进行研究,归纳、总结并提出了精整模具三个关键零部件(芯棒、模冲、阴模)。
关键词:粉末冶金粉末冶金模具精整AbstractThis text was main circumambience powder metallurgy and molding tool design to open an exhibition the following several aspect of research1,carry on research in the new function within material in the characteristics of technique of the powder metallurgy and it,point introduction the powder metallurgy is in the industry of importance andit inhibit a step。
2,in the powder metallurgy the craft,according to the metals powder of the request choice or nonmetal powder of product for original material to inhibit。
3,at the molding tool design of the powder metallurgy principle,this text point around Jing's whole molding tool design carry on research and induce,summary and put forward Jing the whole key with three molding tool zero partses(Xin stick,mold blunt,Yin mold)new of classification method。
粉末冶金模具设计课件
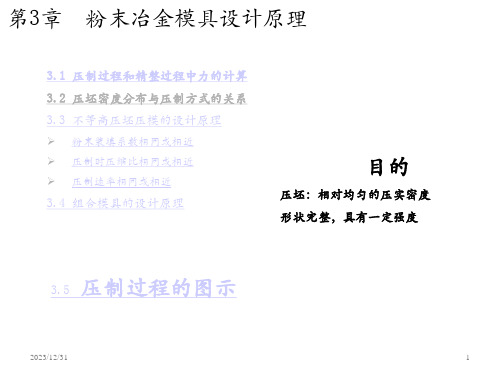
2023/12/31
12
2023/12/31
13
2023/12/31
14
•压制方式的选择依据
压制方式和方法不同,上、下模冲、芯杆和阴 模相对于粉末压坯的相对运动方向及速度也不 同,从而使外摩擦对压坯密度的均匀分布产生 有害或者有利的影响。
单向压制
S侧max/S=[1-(ρ下/ρ上)m]/μξ=K
2023/12/31
19
选择原则
•(S侧阴+S侧芯)/S<K或者圆筒形压坯h/T<K/2时, 可采用单向压制;
•(S侧阴+S侧芯)/S>K时,如果(S侧阴+S侧芯)/2< (S侧阴-S侧 芯),或者圆筒形压坯D内<T,可采用双向压制;
•(S侧阴+S侧芯)/S>K时,如果(S侧阴+S侧芯)/2> (S侧阴-S侧 芯),或者圆筒形压坯D内>T,可采用摩擦芯杆压 制
当柱状压坯S侧/S<K或者圆柱体压坯高径比 H/D<K/4时,采用单向压制可以满足压坯密 度分布均匀性的要求
2023/12/31
15
2023/12/31
16
双向压制
S侧max/S=[1-(ρ中/ρ上)m]/μξ=2K
当柱状压坯K<S侧/S<2K,或者圆柱体 K/4<H/D<K/2时,采用双向压制、非同时双 向压制、浮动阴模双向压制或者下拉式压制 可以满足压坯密度分布均匀性要求
b>(a-b)时,采用带斜面的整体下模冲压制;
b<(a-b)时,需要采用组合下模冲来压制。
2023/12/31
38
2023/12/31
39
2023/12/31
粉末冶金模具设计说明书样板
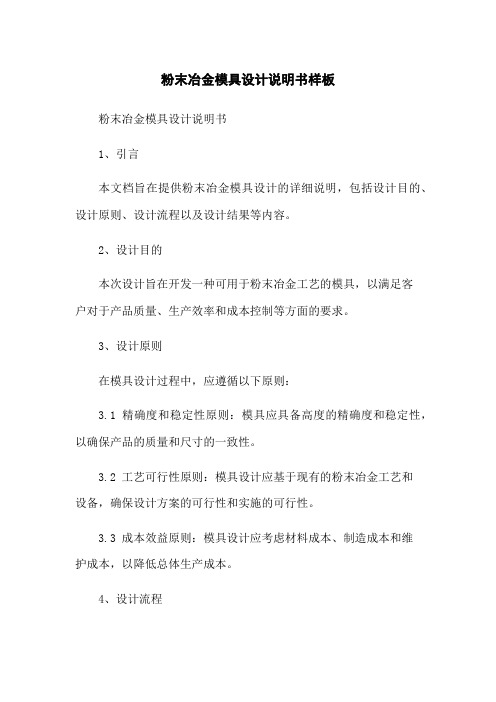
粉末冶金模具设计说明书样板粉末冶金模具设计说明书1、引言本文档旨在提供粉末冶金模具设计的详细说明,包括设计目的、设计原则、设计流程以及设计结果等内容。
2、设计目的本次设计旨在开发一种可用于粉末冶金工艺的模具,以满足客户对于产品质量、生产效率和成本控制等方面的要求。
3、设计原则在模具设计过程中,应遵循以下原则:3.1 精确度和稳定性原则:模具应具备高度的精确度和稳定性,以确保产品的质量和尺寸的一致性。
3.2 工艺可行性原则:模具设计应基于现有的粉末冶金工艺和设备,确保设计方案的可行性和实施的可行性。
3.3 成本效益原则:模具设计应考虑材料成本、制造成本和维护成本,以降低总体生产成本。
4、设计流程4.1 产品需求分析:了解客户对于产品性能、尺寸和表面质量等方面的要求,获得设计的基础数据。
4.2 材料选择:根据产品需求和工艺要求,选择适合的材料,包括模具材料和涂层材料等。
4.3 模具结构设计:设计模具的整体结构和零部件结构,考虑模具的可装卸性、易维护性和生产效率等。
4.4 模具零部件设计:设计模具的各个零部件,包括模具芯和模具腔等,确保其几何形状和尺寸的准确性。
4.5 涂层选择和设计:根据模具的使用环境和工艺要求,选择合适的涂层材料,并设计涂层的厚度和结构等。
4.6 模具制造和调试:根据设计图纸和规范,制造和组装模具,并进行调试和试产,以确保模具的正常使用。
4.7 模具维护和管理:建立模具维护和管理体系,包括清洗、保养和修复等工作,延长模具的使用寿命。
5、设计结果基于以上设计流程和原则,我们提供了粉末冶金模具的设计方案。
设计方案包括模具结构图纸、材料选择和涂层设计等内容,请参阅附件1:附件:1、粉末冶金模具设计图纸本文涉及的法律名词及注释:1、粉末冶金:一种通过将金属粉末压制成形并经过烧结过程得到制品的金属加工工艺。
2、模具:用于塑料、金属等物质加工中的一种工具,用于赋予材料所需的形状和尺寸。
- 1、下载文档前请自行甄别文档内容的完整性,平台不提供额外的编辑、内容补充、找答案等附加服务。
- 2、"仅部分预览"的文档,不可在线预览部分如存在完整性等问题,可反馈申请退款(可完整预览的文档不适用该条件!)。
- 3、如文档侵犯您的权益,请联系客服反馈,我们会尽快为您处理(人工客服工作时间:9:00-18:30)。
好的材料 ➢ 高密度、高精度件用耐磨性好的材料 ➢ 整形模用耐磨性好的材料
绘制模具装配图和零件图
➢ 绘制模具装配图和零件图 ➢ 标注尺寸偏差和形位公差 ➢ 标注其他加工要求
绘制模具装配图和零件图
模具示例
模具示例
设计模具结构
根据制品图纸设计坯件,选择压机和压制方式,设计 模具结构草图 ➢ 从生产工艺、压制成形和经济成本方面分析制品图纸 及技术要求,看是否适于用粉末冶金方法生产 ➢ 根据制品图纸及技术要求和粉末冶金生产工艺的特点, 设计坯件的几何形状、精度和密度 ➢ 为了使制品适于压制成形,或为了简化模具结构,常 对制品形状进行修改,设计出适合于压制的压坯 ➢ 在设计坯件形状的同时要确定压制方向,然后根据压 坯的形状、高径比、生产批量和压机来选择压制方式、 压模结构类型
粉末成形模具分类
➢ 压模、精整模、复压模、锻模、挤压模、 热压模、等静压模、粉浆浇注模、松装 烧结模
➢ 钢模、硬质合金模、石墨模、塑料橡皮 模和石膏模
钢压模具结构
钢压模具一般由 阴模、模冲、芯棒 组成
钢压模具结构
1—模柄 2,9—法兰圈 3—上模冲 4—模套 5—阴模 6—模座 7—弹簧 8—下模冲 10—下模冲座 11—压垫 12—下模板 13—顶杆 14—顶板
➢ 制品生产工艺流程及工艺参数:粉末混合料成分、杜 装密度、流动性、压制性、单位压制压力、压坯密度、 压缩比、弹性后效、烧结收缩率、精整余量、机加工 余量、复压装模间隙和压下率等
➢ 压机类型及主要技术参数:公称压力、脱模压力、压 机行程、每分钟压制次数、工作台面积、压机自动化 程度和安全保险装置等
➢ 模具加工设备及能力 ➢ 典型模具图册及模具使用过程中曾出现的问题
选择模具材料
➢ 高强度、高硬度和高耐磨性 ➢ 高的刚度和小的热膨胀系数 ➢ 优良的热处理性能和一定的韧性 ➢ 较好的机加工性能
选择模具材料
➢ 阴模工作条件最苛刻,一般选用硬质合金、高速钢、 高合金工具钢、低合金工具钢和碳素工具钢来制造
➢ 芯杆和阴模具有大致相同的工作要求,常用与阴模相 同的材料来制造,但要求有较好的抗弯强度和一定的 韧性;芯杆的热处理硬度稍低于阴模,特别是细长芯 杆,要求比粗短芯杆具有较好的韧性
钢压模具结构
钢压模具结构
通用标准模架
模具设计不合理造成的问题
➢ 坯件开裂、分层、掉边、掉角 ➢ 坯件精度、粗糙度不合要求 ➢ 密度分布不均匀 ➢ 坯件脱模困难 ➢ 模具难于加工,容易损坏和炸裂 ➢ 操作繁杂,劳动强度大 ➢ 模具费用过高
设计原则
➢ 充分发挥粉末冶金少、无切削的工艺特点,保 证坯体达到几何形状、尺寸精度和表面粗糙度、 坯体密度及其分布等三项基本要求
➢ 模冲的工作条件与阴模不同,要求有良好的韧性,同 时也要求耐磨、抗疲劳和抗振动,硬度可以降低些, 一般选用低合金工具钢、船用工具钢和青铜等
➢ 模套、压垫、模座、顶杆、控制杆、导柱、模板等辅 助零件,常选用碳素钢(如:45号、50号钢)和低合金 钢(如:40Cr、GCrl5)来制造
选择模具材料
➢ 大批量生产用耐磨性好的材料,小大批量生产 用廉价材料
计算模具零件尺寸
模具零件尺寸计算的关键在于正确地选择设计 参数 ➢ 压缩比K ➢ 弹性后效t ➢ 烧结收缩率s ➢ 精整余量△Z ➢ 机加工余量△ J ➢ 复压装模间隙△ b ➢ 复压压下率f
计算模具零件尺寸
要求不高产品 ➢ 压缩比K ➢ 弹性后效t ➢ 烧结收缩率s
高要求产品 ➢精整余量△Z ➢机加工余量△ J ➢复压装模间隙△ b ➢复压压下率f
模具示例
模具示例
模具示例
模具示例
➢ 浮动式模具 ➢ 拉下式模具
1-上内冲压垫 2-上内冲 3-上外冲压垫 4-上外冲 5-模腔 6-下一冲 7-下一冲压垫 8-下二冲 9-下二冲压垫 10-芯棒 11-芯棒接杆
1—轭形板;2—提升杆;3—装 粉调整螺母;4—第二下模冲支座; 5—导体;6—第二下模冲托板; 7—第二下模冲;8—第一下模冲 支座;9—第一下模冲托板;1 0—第一下模冲压板;11—第一 下模冲;12—阴模板;13—阴 模;14—阴模压板;15—芯棒; 16—上模冲;17—上模冲底板; 18—上模冲板;19—导柱;2 0—上模冲压板;21—阴模座; 22—拔出调整螺栓;23—楔形 块;24—第二下模冲压板;2 5—滑块;26—滚轮;27—滚 轮销;28—耐磨板;29—底板; 30—导柱;31—芯棒压板;3 2—芯棒底板
时阴模、芯杆和上模冲能相对于下模冲移动的压 模结构
设计模具结构草图
等高制品成形模设计
根据高径比确定压制方式
不等高制品成形模设计
➢ቤተ መጻሕፍቲ ባይዱ粉末装填系数相同或相近 ➢ 压缩比相同或相近 ➢ 压制速率相同
计算模具零件尺寸
满足以下基本要求 ➢ 产品对压坯形状、尺寸、密度和强度的
要求 ➢ 压制过程(装粉、压制、脱模)的要求 ➢ 模具强度和刚度的要求
➢ 合理设计模具结构和选择模具材料,使模具零 件具有足够高的强度、刚度和硬度,具有高耐 磨性和使用寿命;便于操作、调节,保证安全 可靠/尽可能实现模具自动化和机械手操作
➢ 注意模具结构的可加工性和模具制造成本问题
掌握有关设计资料
➢ 制品图纸及技术要求:制品性能、形状、尺寸、精度 和表面粗糙度等制品生产批量
钢压模具设计
➢粉末成形模具分类 ➢钢压模具结构 ➢模具设计原则 ➢模具结构设计 ➢模具零件尺寸计算 ➢模具材料选择 ➢装配图和零件图绘制
粉末成形模具的作用
➢ 模具是粉末成形的主要工艺装备之一,对产品 质量、成本、安全、生产率、自动化产生重要 影响,模具技术发展水平反映一个国家的工艺 水平
➢ 掌握粉末冶金模具设计方法,设计高质量自动 化模具,是粉末冶金工业发展的需要
设计模具结构
一般可按制品的高径比(H/D)或高度与壁厚之比(H/δ) 来选择压制方式和压模结构类型
➢ H/D<1或H/δ≤3时,采用单向压制和单向压模 ➢ H/D>l或H/δ>3时,采用双向压制和双向压模 ➢ H/D>4时,采用压制时芯杆和阴模能相对移动的
压模结构 ➢ H/D>6—10时,采用摩擦芯杆压模,或采用压制