连铸方坯中心裂纹成因分析及控制方法
第六讲 连 铸 坯 裂 纹 控 制

连 铸 坯 质 量 控 制
北 京 科 技 大 学 冶 金 学 院
3 连铸坯表面裂纹形成及防止
3.1铸坯表面裂纹类型
◆ 纵裂纹 ◆ 横裂纹 ◆ 星形裂纹 ◆ 皮下气孔
图3-1 铸坯表面裂纹示意图
连 铸 坯 质 量 控 制
北 京 科 技 大 学 冶 金 学 院
3.2表面纵裂纹
3.2.1定义 沿拉坯方向,板坯表面中心位置或距边部10~15mm处产 生的裂纹。裂纹长10~1500mm,宽0.1~3.5mm,深<5mm。 3.2.2产生原因 在结晶器弯月面区(钢液面下170mm左右),钢凝固在 固相线以下发生δ→γ转变,导致凝固厚度生长的不均匀性, 由于热收缩使坯壳产生应力梯度,在薄弱处产生应力集中, 坯壳表面形成纵向凹陷,从而形成纵向裂纹。 可以说,结晶器弯月面区凝固壳厚度不均匀性是产生表 面纵裂纹的根本原因,在二冷区铸坯裂纹进一步扩展。
连 铸 坯 质 量 控 制
北 京 科 技 大 学 冶 金 学 院
2.2 产生内裂纹的判据
内裂纹的产生主要决定于凝固面前沿所能承受的应力应 变。当凝固前沿承受的应变ε 超过临界应变ε 临值,则 产生裂纹。 不同作者实际测定ε临值如下:
C,% 0.15 0.17~0.28 0.16~0.23 0.13~0.15 0.13 0.18~0.24 0.42 ε(应变) 0.2~0.5 3.2~3.6 0.5~1.0 3.2~3.3 0.45~0.56 0.32~0.62 1.0~1.5
液面波动<±5mm,纵裂纹最少(图3-8); 液面控制方式对纵裂影响如图3-9。
图3-8 结晶器液面波动对纵裂的影响
图3-9 液面控制方式对纵裂的影响
连 铸 坯 质 量 控 制
方坯铸坯缺陷产生原因及预防措施

方坯铸坯缺陷产生原因及预防措施1.前言由于连铸坯质量问题多发于连铸,因此对连铸质量缺陷进行了分析,总结出发生原因,以减少连铸坯质量问题的发生。
2.铸坯主要有以下几种缺陷:2.1卷渣2.1.1表面卷渣(见图1)2.1.2内部卷渣(见图2)图1 图22.2裂纹2.2.1表面裂纹:头部表面裂纹(图3 )、尾部表面裂纹(见4)。
图3 图42.2.2内部裂纹(见图5)图52.3气泡缺陷(见图6、见图7)图6 图73、缺陷产生原因及预防措施3.1卷渣产生原因及预防措施3.1.1表面卷渣产生原因及预防措施产生原因:(1)结晶器内形成渣条,当结晶器内钢液面波动量大于熔渣层厚度时、或挑渣条未挑净时、或在挑渣条过程中将渣条带入结晶器坯壳上时形成卷渣。
(2)在换包或等包降速过程中,由于操作不当造成中包液位较浅,导致中包内钢液形成涡流将中包渣卷进结晶器内,在上浮过程中被坯壳捕作形成卷渣。
(3)调整渣线高度超过液渣层厚度、或有渣条未挑净、等原因时造成颗粒渣被卷到坯壳上而形成卷渣。
(4)在开浇升速前液渣厚度未达到标准,造成颗粒渣或予熔层的保护渣直接与钢液接触,升速过程中在结晶器内造成钢液面发生波动,导致保护渣被卷入到坯壳上,形成卷渣。
(5)中包掉料或有杂物,开浇过程中被钢水冲到结晶器内,从而形成卷渣。
(6)中包内钢液面剧烈波动时,造成中包内覆盖剂被卷入中包钢液中,此时被卷入的覆盖剂受两个力作用:向上的钢水的浮力和向下的钢流股吸力作用,当向下的钢流股吸力大于向上钢水的上浮力时,卷入的覆盖剂就被卷入到结晶器内,在钢流流股的作用下,如被坯壳捕作而形成皮下卷渣,如被向下流股带入液相穴深处而形成内部卷渣。
(7)挑渣条用8#钢线(或细铁线),在钢线上结钢瘤或渣块,有钢瘤的8#线熔断到结晶器钢液内部,如被坯壳捕作到而形成皮下卷渣,如进入液相穴深处而形成内部卷渣。
(8)拉速波动,特别是在升速或降速过程,由于拉矫机电机转速发生变化,从而造成结晶器液面波动,从而形成渣条,形成的渣条被卷入结晶器坯壳上形成卷渣。
连铸坯表面裂纹形成及防止(理化中心)

-
15
横裂纹产生原因
(1) 横裂纹产生于结晶器初始坯壳形成振痕的波谷处,振痕越深, 则横裂纹越严重,在波谷处,由于:一是奥氏体晶界析出沉淀物 (AlN,Nb(CN)),产生晶间断裂(如下图); 二是沿振痕波谷 S、P元素呈正偏析,降低了钢高温强度。这样,振痕波谷处,奥 氏体晶界脆性增大,为裂纹产生提供了条件。
不均匀性强,振痕深,表面易产 生凹陷或横裂纹;生产实践表明, C避开这个区间时,振痕浅了, 铸坯边部横裂减少; (2)降低钢中[N],防止氮化物沉 淀; 2. 结晶器振动特点 (1)振痕深度增加,横裂纹增加 (如图所示);
图: 振痕深度与横裂纹产生几率的关系
-
18
(2)振动频率f增加,振痕变浅,横裂纹减少(如图所示); (3)负滑脱时间增加,振痕深度增加(如图所示),方圆坯 tN=0.12~0.15s,板坯tN=0.20s。
图 铸坯表面的网状裂纹
-
23
铸坯表面星形裂纹产生原因
铸坯表面星形裂纹沿一次晶界分布,裂纹边界有脱C现象,说明是 在结晶器内高温下(1400℃)坯壳奥氏体转变之前形成的。
图 振动频率与振痕深度的关系
-
图 负滑脱与振痕深度的关系
19
Байду номын сангаас
3. 合适二冷强度
调整二冷水分布,在矫 直前铸坯温度>850℃,避 开脆性区(如图所示);
合适二冷水量并降低铸 坯横向中心与边部温度差, 避免回热温度过高。
图 矫直温度与横裂纹关系
-
20
防止横裂纹措施
(1) 采用高频率,小振幅结晶器振动负滑脱时间tN与拉速v成正比, 与频率和振幅f成反比。为防止横裂纹,就要减浅振痕,则必须降 低,要降低,则必须采用高频率(100~400min-1),小振幅 (±5mm)的结晶器振动机构。
板坯中心裂纹的成因与对策
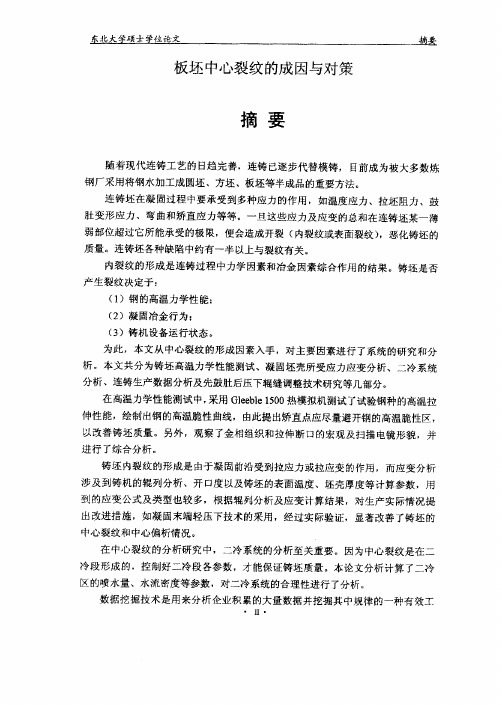
在中心裂纹的分析研究中,二冷系统的分析至关重要。因为中心裂纹是在二 冷段形成的,控制好二冷段各参数,才能保证铸坯质量。本论文分析计算了二冷 区的喷水量、水流密度等参数,对二冷系统的合理性进行了分析。 数据挖掘技术是用来分析企业积累的大量数据并挖掘其中规律的一种有效工
I ・ I
I . V
t pru ad lh kesA crn tt rls l iad cli ru s e e t e s l ns co i o oe aa s n cl ao e l m a r n h tc . d g h lr n y s a u t n t e i e s o se , r i m as pt a ad i t b p cc. r m l sf f s ip v g n a uf wr n vla d r te o ea p , t sm on e r r e o d ad e y i F x e o r a t r utn nl y be aot tip v t st o cuao ad t n e co t ho g hs n p d m r e tu f si n sli d i e o a e d e o o h a s a tn o o c e u
() a o f d i i ; i o sl ict n 2 B hv r oi f ao e
( R ni stoeu m n g e qi et 3 un t f p . ) n a T e fr i t s ie as o o ao i o bn t nl e cn r , h atl cue f m t n cm i d aa z te t hr oe n rc , e i f i s r e o y h e e
ic ssii a tn a pro sb c cs lap rs qato sb t ua n ea w k t l s r k w u pe , ul f s a tn cri e a f , n a a o d a o i y l a
连铸坯表面裂纹形成及防止(蔡开科)
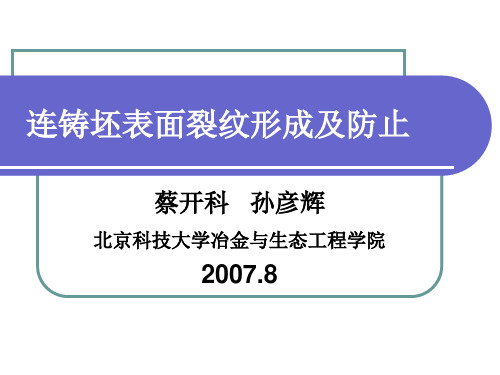
图2-17 结晶器锥度和钢成分对皮下内裂的影响 (断面尺寸240x240mm,拉速0.7m/min)
2 铸坯表面纵裂纹
(7) 结晶器振动
振痕浅,无角部纵裂纹; 振痕深,角部纵裂纹增加; 负滑脱时间值增大,板坯表面纵裂升高;=0.2~0.3s,纵裂降低。 (8) 结晶器钢液流动 水口对中,防止产生偏流;水口材质浸蚀,出口流股不对称,造 成偏流。 水口插入深度合适
图2-8 结晶器液面波动对纵裂纹的影响
图2-9 液面控制方式对纵裂纹的影响
2 铸坯表面纵裂纹
(5) 结晶器热流和冷却
如图2-10所示,90×1000mm 板坯结晶器弯月面以下45mm热流 与纵裂纹指数关系。 ◆低碳钢(0.05%C),结晶器热 流>60Cal/cm2· s(2.1MW/ M2), 纵裂纹增加; ◆中碳钢(0.11%C),结晶器热 流>41Cal/cm2· s(1.7MW/M2),纵裂 纹增加。
3 铸坯(1) 钢成分 C=0.10~0.15%,坯壳厚度不均 匀性强,振痕深,表面易产生凹陷 或横裂纹;生产实践表明,C= 0.15~0.18%或0.15~0.20%时, 振痕浅了,铸坯边部横裂减少; 降低钢中[N],防止氮化物沉淀; (2) 结晶器振动特点 振痕深度增加,横裂纹增加(图 3-4); 振动频率f增加,振痕变浅,横裂纹 减少(图3-5); 负滑脱时间增加,振痕深度增加 (图3-6),方坯tN=0.12~0.15s, 板坯tN=0.20s。
2 铸坯表面纵裂纹
(2) 结晶器钢水流动的合理性
液面波动±3~±5mm
浸入式水口对中,防止偏流 合理的浸入式水口设计(合适的出口直径,倾角) 合适的水口插入深度
(3) 结晶器振动
连铸坯在凝固过程中形成裂纹的原因

连铸坯在凝固过程中形成裂纹的原因随着市场竞争的日趋激烈,产品的质量已经成为占有市场的主要砝码,连铸坯作为炼钢厂的终端产品,其质量直接影响着轧材单位的产量和轧材质量,据统计炼钢厂连铸坯质量缺陷中约70%为连铸坯裂纹,连铸坯裂纹成为影响连铸坯产量和质量的重要缺陷之一,下面将对铸坯在凝固过程中裂纹的形成做简要分析:一、铸坯凝固过程的形成铸坯在连铸机内的凝固可看成是一个液相穴很长的钢锭,而凝固是沿液相穴的固液界面在液固相温度区间把液体转变为固体把潜热释放出来的过程。
在固液界面间刚凝固的晶体强度和塑性都非常小,当作用于凝固壳的热应力、鼓肚力、矫直力、摩擦力、机械力等外力超过所允许的外力值时,在固液界面就产生裂纹,这就形成了铸坯内部裂纹。
而已凝固的坯壳在二冷区接受强制冷却,由于铸坯线收缩,温度的不均匀性,坯壳鼓肚、导向段对弧形不准,固相变引起质点如(AlN)在晶界的沉淀等,容易使外壳受到外力和热负荷间歇式的突变,从而产生裂纹就是表面裂纹。
二、连铸坯裂纹形态和影响因素连铸坯裂纹形态分为表面裂纹和内部裂纹,表面裂纹有纵向、横向角部裂纹、表面横裂和纵裂、网状裂纹和凹陷等,内部裂纹有中间、中心和矫直裂纹等。
连铸坯裂纹的影响因素:连铸坯表面裂纹主要决定于钢水在结晶器的凝固过程,它是受结晶器传热、振动、润滑、钢水流动和液面稳定性所制约的,铸坯内部裂纹主要决定于二冷区凝固冷却过程和铸坯支撑系统(导向段)的对弧准确性。
铸坯凝固过程坯壳形成裂纹,从工艺设备和钢凝固特性来考虑影响裂纹形成的因素可分为:1、连铸机设备状态方面有:1)结晶器冷却不均匀2)结晶器角部形状不当。
3)结晶器锥度不合适。
4)结晶器振动不良。
5)二冷水分布不均匀(如喷淋管变形、喷咀堵塞等)。
6)支承辊对弧不准和变形。
2、工艺参数控制方面有:1)化学成份控制不良(如C、Mn/S)。
2)钢水过热度高。
3)结晶器液面波动太大。
4)保护渣性能不良。
5)水口扩径。
6)二次冷却水分配不良,铸坯表面温度回升过大。
211172579_连铸方坯的常见表面缺陷及控制

管理及其他M anagement and other连铸方坯的常见表面缺陷及控制康旭辉摘要:连铸方坯表面的质量直接影响材料轧制后成品的质量,而近年来,我国部分企业在连铸方坯生产的过程中,存在诸多的表面缺陷问题,不能确保生产的质量和效果。
基于此,本文分析连铸方坯常见表面缺陷问题,提出几点表面缺陷控制的建议和措施,旨在为增强连铸方坯的表面质量提供帮助。
关键词:连铸方坯;常见表面缺陷;控制全面掌握方坯缺陷的类型、形成机理和消除途径是方坯质量控制的关键。
目前,国内外钢铁企业在钢坯质量控制方面取得了可喜的成绩,并获得了大量的生产数据和实际操作经验。
全面提高方坯质量,对提高连铸方坯成品率、改善钢材质量、节能降耗、降低成本具有重要意义。
连铸钢属于直接浇注钢水的工艺。
它的出现从根本上改变了主导了一个世纪的钢锭开坯过程。
液态金属连铸钢的概念早在19世纪中叶就被提出。
1840年,美国的销售商获得了连铸铅管的专利。
1846年,转炉的发明者贝塞默使用水冷旋转双辊连铸机生产锡箔、铅板和玻璃板。
1872年,David提出了移动式结晶器连铸的概念。
1886年~1889年,提出了立式连铸机的设计方案。
1921年,皮尔逊提出了结晶器振动的概念,即结晶器振动使板坯和结晶器之间连续的相对运动。
1933年,连铸的先驱德国准噶斯人建造了第一台1700t/月振动结晶器立式连铸机。
20世纪30年代,第一个成功铸造铜铝合金的有色金属连铸应用于生产。
目前,部分企业在连铸方坯生产的过程中,方坯表面的质量波动幅度很高,存在脱方缺陷、凹陷,缺陷和渣沟缺陷等,不能确保整体结构表面质量符合标准要求,对特钢产品生产质量造成一定的危害,因此,在连铸方坯实际生产的过程中需结合具体表面缺陷问题的发生原因与实际情况,采用有效的措施进行控制,确保连铸方坯表面质量符合标准规范,为特钢产品高质量生产夯实基础。
1 连铸方坯的常见表面缺陷和发生原因1.1 渣沟缺陷与原因从实际情况而言,连铸方坯表面出现渣沟缺陷问题,轧制以后线材表面出现裂纹缺陷问题的发生存在直接联系,从表面观察可以发现坯件有纵向贯通性的沟状缺陷问题,具体是在连铸方坯的内弧部分分布,很小一部分会在侧弧的位置,采用跟踪性轧制12.5mm绞丝钢实验的方式,可以发现线材的表面存在裂纹问题。
连铸坯发纹裂纹产生的原因

连铸坯发纹裂纹产生的原因连铸坯发纹裂纹是指在连铸过程中,坯料表面产生裂纹的现象。
这种现象在连铸过程中非常常见,如果没有正确的处理,会影响连铸坯的质量和后续加工工艺,甚至可能导致产量的降低。
连铸坯发纹裂纹的产生原因非常多样化,主要包括以下几个因素。
首先,连铸坯发纹裂纹的产生与坯料的化学成分有关。
在连铸过程中,如果坯料中含有不溶于钢液的硬质夹杂物,这些夹杂物会被硬质粒子剪切或滚动而产生裂纹。
此外,坯料中如果含有超过允许值的硫、磷等元素,会导致钢液的黏度增加,使连铸过程中液面波动较大,从而增加坯料表面的应力,进一步促进裂纹的发生。
其次,连铸坯发纹裂纹的产生与连铸工艺参数有关。
连铸过程中的拉速度、浇注速度、结晶器冷却剂的喷射速度等参数的过大或过小都会导致连铸坯表面产生应力,从而引发裂纹的产生。
此外,连铸过程中,如果坯料温度过低或结晶器冷却不均匀,也会导致坯料表面产生裂纹。
再次,连铸坯发纹裂纹的产生与结晶器的表面状况有关。
结晶器的表面状况会直接影响连铸坯表面的光滑度和均匀度。
如果结晶器表面存在磨损、凹凸不平等缺陷,会导致连铸坯表面产生过多的应力,从而引发裂纹的产生。
此外,连铸坯发纹裂纹的产生还与连铸辊的形状和磨损程度有关。
连铸辊的形状不合理或磨损过度会导致钢坯的厚度不均匀,在拉伸过程中产生裂纹。
在连铸工艺中,如果连铸辊的温度过高或过低,也会导致连铸坯的拉伸和表面温度不均匀,从而引发裂纹的产生。
最后,连铸坯发纹裂纹的产生还与工艺操作和设备维护有关。
操作不当会导致坯料表面的应力增加,设备维护不到位会降低连铸过程的稳定性,从而增加坯料发纹裂纹的风险。
为了减少连铸坯发纹裂纹的发生,可以采取以下措施:1.优化坯料的化学成分,减少夹杂物的含量,控制硫、磷等元素的含量。
2.合理调整连铸工艺参数,包括拉速度、浇注速度、结晶器冷却剂的喷射速度等,以减小坯料表面的应力。
3.对结晶器进行检修和维护,保持其表面的光滑度和均匀度。
- 1、下载文档前请自行甄别文档内容的完整性,平台不提供额外的编辑、内容补充、找答案等附加服务。
- 2、"仅部分预览"的文档,不可在线预览部分如存在完整性等问题,可反馈申请退款(可完整预览的文档不适用该条件!)。
- 3、如文档侵犯您的权益,请联系客服反馈,我们会尽快为您处理(人工客服工作时间:9:00-18:30)。
一钢厂4#连铸机中心裂纹的研究攻关
摘要:对一钢厂4#连铸机方坯中心裂纹的成因进行了研究,分析了钢水过热度、二次冷却强度、拉速等对铸坯中心裂纹的影响,根据分析所得的结论,采取了合理的工艺措施并进行了适当的技术改造,使中心裂纹发生率降低到0.5%以下。
关镇词:连铸机方坯中心裂纹
1.前言
韶钢一炼钢厂4#连铸机投产于1997年,该机为R6m,3机3流全弧形连铸机铸坯断面为160 mmX 160 mm,结晶器长850 mm,二冷段采用单管式表面喷淋冷却方式,火焰切割,中间包采用塞棒控制或采用长寿包定径水口浇铸。
敞开式浇注,生产钢种主要为Q235、Q215、HRB335.
该连铸机投产以来生产的160 mm ×160 mm铸坯一直存在的中心裂纹缺陷。
随着韶钢的发展,高线厂将替代三轧四轧制,高线在轧制时出现冲钢事故,严重影响生产的顺行。
为此对我厂生产的铸坯提出了较高的的质量要求。
2008年由于中心裂纹挑废的占坯产量的5%。
,严重影响了一钢厂企业形象和经济效益。
为解决这一问题,一炼钢厂于2008.11月成立了攻关组。
目标是要把挑废率降到0.5%。
我们结合了当前的生产形式和现场实际进行了公关,并取得了预期效果。
2. 中心裂纹的形态及对轧制产品的影响
2.1中心裂纹的形态
﹙图-1 ﹚
4#连铸机铸坯中心裂纹在断面上是呈不连续的岛状(点状)分布(如图-1),有时有两到三个点。
点之间的连线往往是线状的肉眼可见的中心线裂纹,严重时则沿整个铸坯长度方向连续分布并贯通,并伴随着中心偏析疏松。
单个点直径在5—15mm之间,裂纹长20^50mm 在铸坯处于发红状态时中心裂纹不易察觉,铸坯冷却至室温时则清晰可辨,给在线控制带来很大困难。
2. 2对轧制产品的影响
线材厂对中心裂纹铸坯进行的轧制表明,轧制过程轧成品裂纹不能焊合,经常出现断裂冲钢。
3.中心裂纹形成机理及原因分析
3.1 形成机理
通过查阅大量的专业书籍和现场跟踪生产总结,认为4号机方坯中心裂纹形成的机理是多种因素综合作用的结果,从钢的高温变形理论,结合钢的高温力学性能.中心裂纹形成的机理主要有以下几个方面。
3.1.1搭桥形成由于凝固坯壳的不均匀形成。
在凝固末期.凝固前沿搭桥,将钢液封住,上部钢液无法填充,这样被封住的钢液继续凝固时就会形成缩孔,这种缩孔在断面上有时呈现出中心裂纹形态。
3.1.2 铸坯在二冷段纵向冷却不合理前期二冷水过大,造成铸坯表面
冷却速度过高,后期冷却水量相对过小,造成表面温度回升大。
这样,由于热应力的作用,使铸坯中心部位撕开,形成中心裂纹。
对于浇注温度偏高,柱状晶发达的铸坯,它将进一步促进中心裂纹的形成。
试验研究表明:铸坯表面冷却速度应控制在200 ℃/m内,温度回升不超过100 ℃/m,否则,形成内裂的几率大幅度增加.从一钢厂的生产情况看,上述2种情况均存在。
3. 2 裂纹形成原因分析
4#连铸机铸坯中心裂纹形成的原因主要有:
3.2.1 钢水过热度高我厂是一个老厂,转炉设备落后,一次命中率低后吹严重,造成出钢钢水温度温度波动很大,往往偏高。
据统计,跟踪期间平均过热度达4 7℃,高于50℃的炉占43%,高于30℃的炉占87%。
大大高于连铸正常生产要求的控制范围(30C以内)。
钢水过热度高,使铸坯的柱状晶粗大、发达,加剧了晶间裂纹产生,同时减小了结晶器出口处坯壳厚度,造成拉漏增加,液相线延长。
有研究证明过热度每提高10℃,坯壳厚度减小2mm,因而高温钢在连铸生产中极有害。
3.2.2拉速偏高,且波动大一炼钢厂为实现全方坯生产的组织模式,要达到炉机匹配,实际生产过程4#机拉速一般控制在 1.8-2. 2m/min内,其结果是造成有时带液心矫直。
3.2.3二次冷却不合理 4#连铸机原来是按连铸合金钢来设计二冷段的,其冷却情况不适应于连铸普碳钢高拉速的需要,主要表现在:二冷段采用的喷嘴雾化程度差,造成铸坯中心冷却弱,角部冷却过强,
四面冷却不均匀,应力增大,且易形成搭桥;且各段水量分配不合理,足辊、I段、II段的水量分配比例为30%, 50%, 20%,足辊水量偏小,造成铸坯在足辊段不能获得强冷,而I段冷却过强,致使该区段内铸坯温降过大,II段冷却过弱,使铸坯在段产生较大“回温”,增大凝固前沿的热应力,产生中心裂纹。
3.2.4 据研究指出:方坯普碳钢ω(S)≤0.035%,同时ω(Mn)/ω(S)>15,才能避免铸坯出现裂纹。
众所周知硫会造成钢的“热脆”性,而Mn能有效地防止钢热加工过程的“热脆”。
我们厂钢中的硫含量一直很高,并且Mn/ S在1—2之间。
3.2.5操作工操作不规范的现象比较普遍主要是拉速控制不稳定,不能较好地根据钢水温度、拉速、铸坯温度状况调节水量。
设备维护不理想,未能及时检查更换堵塞的喷嘴,主体设备校弧较差等。
4 .采取的措施及效果
针对4#连铸机连铸坯产生中心裂纹的原因,攻关组决定采取了如下措施,取得了明显效果。
4.1降低浇注温度,保持合理的过热度
对炼钢工序采取刚包降温措施,加强高温钢的考核,务必到连铸平台的钢水温度保证在1560℃—1630℃之间。
中间包钢水温度控制在1530以下。
在不死流的前提下越低越好。
4.2 提高操作水平,保证设备完好率
(1)及时发现和更换堵塞的喷嘴。
(2)针对塞棒包和长寿包控制的特点,对主要浇钢工加强培训,以稳
定操作。
(3)加强对周检的验收考核,保证检修质量,在这方面重点抓了校弧工作。
4.3完善二次冷却工艺
研究成果已证明了Q235实施强冷就极易产生中心裂纹(包钢院的研究人员就有这方面的成果论文)。
我们到冷水江钢厂出差时也了解到他们对Q235也是采取弱冷。
基于铸坯前后的情况变化和理论依据确定调整二冷水为主攻方向,我们。
Q215现行配水表与我们06年适应性改造后使用的配水表比水量差别不大,只是在各段分配比例上有略微的调整。
Q235配水表属强冷的配水表有9个,属弱冷的配水表有3个,强冷的配水表的比水量一般为1.9~2.1L/Kg,弱冷配水表的比水量为 1.72~1.75L/Kg,现行的配水表是弱冷,比水量为1.73L/Kg,使用看来情况较好,特别是在工艺控制稳定时(中包温度控制在1530℃以下)基本上没有锈点(即没有内裂和严重偏析)出现,说明新使用的Q235配水表(二冷制度)是较适合Q235这种钢的凝固特性的。
4.4 中间包钢水液面和拉速的控制
现在4#机基本上都是使用长寿包,中间包液面的稳定控制显得尤为重要。
我们对长寿包液面控制的要求是>500mm,其意义在于:首先,中间包液面的稳定是拉速稳定的基础;其次是>500mm的满足操作,有利于钢水温度成分的进一步均匀,再就是有利于夹杂物的上浮;为什么拉速波动问题提出要求呢?因为我们现行的二冷配水模型是一个静态的而非动态控制的模型,大转炉的是动态控制模型,在拉
速波动频繁、波动大的情况下,会造成铸坯各段的冷却不均匀的现象,而冷却不均匀对铸坯内部的晶体形成会产生不良影响,会加大铸坯内部的热应力及其作用分部的不均匀,不平衡性,从而易导致铸坯产生内裂、偏析和疏松等内部质量问题,因此,要求台上拉速控制要稳定,尽可能少的波动,避免大幅度波动。
4.5 对炉前成分的要求
钢中ω[Mn]/ω[S]比对钢的热塑性影响很大,从低碳钢高温下的拉伸实验结果可以发现提高ω[Mn]/ω[S]比可以提高钢的延展性,一般ω[Mn]/ω[S]≥7时不产生热脆。
因此要求将ω[Mn]/ω[S]之比大于2作为一个指标进行控制,且尽可能的把硫控制在0.03%以下。
还要做好吹氩搅拌操作和大包温度的合理控制。
4.6 对结晶器水流量进行进一步的调整,以控制其流速,实现结晶器弱冷。
根据理论C含量低于0.2%的钢种在结晶器冷却过程坯壳凝固收缩快,宜采用结晶器弱冷;相反C含量高于0.2%的钢种在结晶器冷却过程坯壳凝固收缩慢,宜采用结晶器强冷。
对于我们的Q235钢种如果结晶器冷却过强,坯壳凝固收缩快会导致坯壳过早的脱离结晶器铜板,反而削弱了结晶器冷却。
通过一段时间的摸索总结,把结晶器水压减小到0.6Mpa。
4.7 效果
通过近一年的运行,4号连铸机连铸坯中心裂纹的控制取得了明显的成效。
挑废率达到了我们原定的目标,特别是从6月份以来,由于我们在一些细节上的优化,现在的挑废率达到了0.2%。
5.结语
通过对4号连铸机连铸坯中心裂纹问题的攻关,我认为控制好以下几点极为重要。
(1)控制好二次冷却强度的均匀性,实现各冷却段水量分配的优化,结晶器采用弱冷。
(2)提高钢水质量,确保合理的过热度。
(3)稳定操作,协调好温度、拉速和水量的匹配关系。
保证设备状况的完好性。
总之,通过以上的措施的逐步实施,虽然也走了不少弯路,但最终还是取得了很好的成绩,为我厂创造了较大的经济效益。