粉末冶金学课件
粉末冶金ppt课件
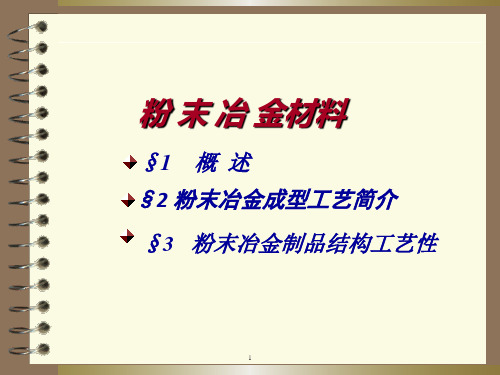
(1)雾化法
粉
末 冶
• 特点:
金
– 生产效率高,成本低,易于制造高纯度
成
粉末;
型
– 合金粉末易产生成分偏析以及难以制得
小于300目的细粉。
• 应用
– 制造Fe 、Pb、Sn、Zn、Al、青铜、 黄铜等低熔点金属与合金粉末;
– 18-8不锈钢、低合金钢、镍合金等 粉末。
23
(2) 机械粉碎法 是靠压碎、击碎和磨削等作用,将
– 用回弹率表示,即线性 相对伸长的百分率,其 大小与模具尺寸计算有 直接关系。
33
• 称粉 就是
称量成型一 个压坯所需 的粉末的重 量或容量。
近两吨重大型坯料(用热等静压法)
18
粉末冶金成型
粉
§2 粉末冶金成型工艺简介
末
冶
金 成
粉料制备
压制成型
烧结
型
粉末冶金成品
烧结后的处理
19
§2 粉末冶金成型工艺简介
粉
一.粉料制备(粉末冶金原料)
末
冶 金
粉末冶金原材料(粉末)
成
型
纯金属
纯金属
种类
非金属 化合物
合金 化合物 复合金属粉末
制取方法选择:
• 特点:
从固态金属氧
– 该法简单,费用低 化 物 或 金 属 化 合 物
• 应用
中还原制取金属粉
– 目前铁粉大部分 由还原法生产。
末,是最常用的生 产方法之一。
26
(4)电解法
从金属盐水溶液中电
粉 末
解沉积金属粉末。
冶
• 特点:
金 成
– 电解末高纯度,高密度,高压缩性;
型
粉末特性-粉末冶金页PPT课件

铁粉性能的比较
Green strength (MPa)
生坯强度
0.6% Kenolube
40 35 30 25 20 15 10
5 200 300 400 500 600 700 800 900
压制压力(MPa)
MH80.23 NC100.24 SC100.26 ABC100.30 ASC100.29 AHC100.29
150-212 45-150 <45
铁粉性能的比较
g/cm3 s/50g
松比和流动性
3.5
40
3.0
35
2.5
30
25 2.0
20 1.5
15
1.0
10
0.5
5
0.0
0
ABC100.30
ASC100.29
AHC100.29
SC100.26
NC100.24
H80.23 M
松比 流动性
铁粉性能的比较
粉末性能
• 冶金性能
化学成分与杂质 显微结构 显微硬度
• 几何性能
颗粒尺寸分布 颗粒外部形状 颗粒内部结构(颗粒孔隙度)
• 机械性能
流动速率 松装密度 压缩性,生坯强度和弹性后效
性能间的相互关系
• 显微结构 化学成分 • 显微硬度 化学成分 • 压缩性 显微硬度, 孔隙度 • 压缩性 粒度 • 流动性 颗粒形状和尺寸 • 生坯强度 颗粒形状
Green density (g/cm3)
压缩性
润滑阴模
7.6 7.4 7.2 7.0 6.8 6.6 6.4 6.2 6.0 5.8 5.6
200 300 400 500 600 700 800 900
粉末冶金PPT课件
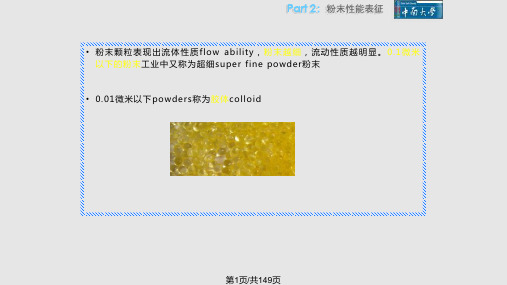
第8页/共149页
Part 2:粉末性能表征
2、化学性能 ChemistryFeatures
• 原材料成分elements与组成 compositions,纯度标准,粉末国家及部 级标准GB and BB
第15页/共149页
Part 2:粉末性能表征
Particle shape and the suggested qualitative descr第i1p6页t/o共1r4s9页
Part 2:粉末性能表征
• The equivalent spherical diameter can be determined from surface area, volume project area or settling rate measurements.
第21页/共149页
Part 2:粉末性能表征
• 球形度sphere ability :与颗粒相同体积same volume的相当球体的表面积对颗粒的实际表面积real surface area之比称为球形度。它不仅表征express 了颗粒的symmetry对称性,而且与颗粒的表面粗糙 程度有关。一般情况下,球形度均远小于1。
• Usually,coarse particle 颗粒以single 单 颗 粒 存 在 , fine particles 由 于 表 面 big surface发达而结合binding together,以二 次颗粒形式存在。 第6页/共149页
Part 2:粉末性能表征
• 颗粒的内部结构:与颗粒的外部结构比较, compared with out surface structure, 颗 粒 的 very complicated structures in particles,内部结构非常复杂
粉末冶金原理简介课件
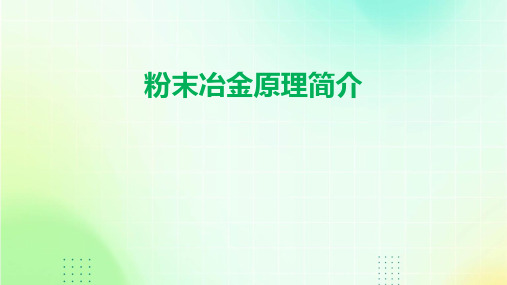
化学共沉淀法
总结词
通过化学反应使金属离子共沉淀形成均匀的金属氧化物或硫化物粉末。
详细描述
化学共沉淀法是一种制备金属粉末的方法,通过化学反应使金属离子共沉淀形成 均匀的金属氧化物或硫化物粉末。在沉淀过程中,控制溶液的pH值和浓度等条 件,使不同金属离子同时沉淀,形成成分均匀的混合物粉末。
喷雾干燥法
定义
粉末烧结是一种通过加热使粉末颗粒 间发生粘结,从而将它们转化为致由烧结和压制烧结。
烧结原理与过程
原理
烧结过程中,粉末颗粒通过表面扩散、粘性流动和塑性变形等机制相互粘结, 形成连续的固体结构。
过程
烧结过程通常包括加热、保温和冷却三个阶段,其中保温阶段是粉末颗粒粘结 的主要阶段。
能源领域
粉末冶金多孔材料可用于制造 燃料电池电极、核反应堆控制 棒等能源相关领域。
医疗器械
粉末冶金材料具有生物相容性 和耐腐蚀性,适用于医疗器械 制造,如人工关节、牙科植入
物等。
粉末冶金的发展历程
01
02
03
早期发展
粉末冶金起源于古代金属 加工技术,如青铜器时代 的铜合金制造。
20世纪发展
随着科技的发展,粉末冶 金在20世纪得到了广泛研 究和应用,涉及领域不断 扩大。
05
粉末冶金材料性能
力学性能
高强度和硬度
粉末冶金材料通过细晶强 化等手段,表现出较高的 硬度和强度,能够满足各 种复杂工况的需求。
良好的耐磨性
由于粉末冶金材料的晶粒 细小且均匀,其耐磨性优 于传统铸造和锻造材料。
抗疲劳性能
由于材料的内部结构均匀 ,可以有效抵抗疲劳裂纹 的扩展,提高零件的寿命 。
特点
粉末冶金具有能够制备传统熔炼 方法难以制备的合金、材料纯度 高、材料性能可调范围广、节能 环保等优点。
《粉末冶金学new》课件
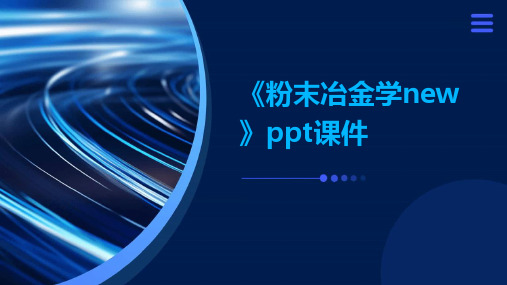
03
CATALOGUE
粉末成形技术
压制成型
总结词
通过施加压力将粉末压制成一定形状和密度的制品。
详细描述
压制成型是粉末冶金中最常用的成形技术之一,通过将粉末装入模具中,施加压力将粉末压制成所需 形状和密度的制品。压制成型具有生产效率高、成本低等优点,广泛应用于制备各种金属零件。
注射成型
总结词
将粉末与液体粘结剂混合后,注射入模 具中冷却固化而成形的工艺。
汽车工业
粉末冶金制品广泛应用于汽车 发动机、变速器、悬挂系统等 关键部位。
航空航天工业
用于制造高性能的航空发动机 、飞机零部件等。
其他领域
如建筑、医疗、化工等,也广 泛应用粉末冶金制品。
02
CATALOGUE
粉末制备技术
机械合金化
总结词
通过高能球磨使金属粉末反复变形、破碎和冷焊,从而实现粉末的细化、合金化 和组织均匀化。
表面处理技术
表面处理技术不断改进,以提高粉 末冶金产品的耐磨、耐腐蚀性能。
市场发展前景
01
02
03
汽车工业
粉末冶金零件在汽车工业 中广泛应用,如发动机、 变速器等,市场前景广阔 。
航空航天领域
粉末冶金材料具有轻质、 高强度的特点,适用于航 空航天领域,市场潜力巨 大。
3D打印技术
粉末冶金与3D打印技术结 合,可实现复杂结构零件 的快速制造,开拓新的应 用领域。
VS
详细描述
注射成型是一种快速、高效的成形技术, 适用于制备形状复杂、精度要求高的制品 。粉末与液体粘结剂混合后形成膏状物, 通过注射机注入模具中,冷却固化后脱模 得到制品。注射成型制品具有尺寸精度高 、表面光洁度好等优点。
粉末冶金课件
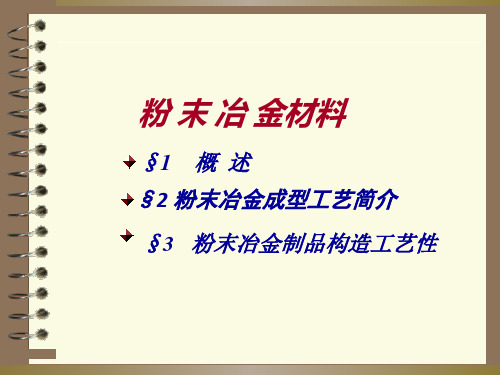
•塑耐性腐变蚀形性能等
•表面状态
•表面张力等
粉末冶金成型
§2 粉末冶金成型工艺简介
3.粉末旳预处理与混合
(1)粉末旳预处理 (2)粉末混合
• 混合 – 两种以上化学组元相混合 (相同化学构成旳粉末旳混合叫做合并。)
• 目旳 – 使性能不同旳组元形成均匀旳混合物, 以利于压制和烧结时状态均匀一致。
为何预处理? a.虽然在同一条件下制造旳同一粉末,其纯度和粒
• 应用 – 制造Fe 、Pb、Sn、Zn、Al、青铜、 黄铜等低熔点金属与合金粉末; – 18-8不锈钢、低合金钢、镍合金等 粉末。
(2) 机械粉碎法
是靠压碎、击碎和磨削等作用,将 块状金属或合金机械地粉碎成粉末。
粉末冶金成型
(2) 机械粉碎法 • 特点:
– 既是一种独立制粉措施, – 又常作为某些制粉措施不可缺乏旳
▪ 据作业旳连续性分 – 间歇式烧结炉—坩埚炉箱式炉 – 高频或中频感应炉
– 大气环境
– 连续式烧结炉
• 产生“过烧”废品
– 烧结温度过高或时间过长,使压坯歪曲和变形,其晶粒也 大;
• 产生“欠烧”废品
– 烧结温度过低或时间过短,产品结合强度等性能达不到要 求;
粉末冶金成型
§2 粉末冶金成型工艺简介
粉末冶金成型
§1 概 述
五、应用
板、带、棒、管、丝等多种型材
成批或 齿轮、链轮、棘轮、轴套类等多种零件 大量生产 重量仅百分之几克旳小制品
近两吨重大型坯料(用热等静压法)
粉末冶金成型
粉末冶金成型
§2 粉末冶金成型工艺简介
粉料制备
压制成型
烧结
粉末冶金成品
烧结后旳处理
§2 粉末冶金成型工艺简介
粉末冶金学(全套课件325P)
粉末冶金的特点(续2)
1)高合金粉末冶金材料的性能比熔 铸法生产的好。 2)生产难熔金属材料或制品,一般 要依靠粉末冶金法,如钨、钼等 难熔金属。
粉末冶金的不足之处: 粉末成本高 粉末冶金制品的大小和形状受到一定的限制 烧结零件的韧性较差 但是,随着粉末冶金技术的发展,这些问 题正在逐步解决中,例如,等静压成形技术已 能压制较大的和异形的制品;粉末冶金锻造技 术已能使粉末冶金材料的韧性大大提高等等。
0-7 粉末冶金专家—黄培云1
粉末冶金专家—黄培云2 技术职称 : 教授 院 士 : 中国工程院院士 出生日期 : 1917-08-23 出生地点 : 福建 福州 专业领域 : 金属材料 ; 粉末冶金 外 语 : 英语 ; 德语 ; 俄语 ; 日语 通讯地址 : 湖南省长沙市中南工业大学 工作单位: 中南工业大学 职 务: 学术顾问
学和力学性能。
0-3 粉末冶金发展历史 公元3000年前,埃及人已经使用铁粉 公元300年,印度德里铁柱是用大约 6.5t 还原铁粉制成的。 19世纪初,为制铂,粉冶重焕青春 20世纪初,粉末冶金制取W 20世纪40年代,欧洲开始生产Fe粉 汽车工业推动了现代粉末冶金技术的进步 新材料新工艺—金属陶瓷、弥散强化材料、 高速钢、超合金
粉末冶金专家 学 历: —黄培云3
时 间: 1934-1938 学 校: 清华大学 所获学位: 学士 国 别: 中国 时 间: 1941-1945 学 校: 麻省理工学院 所获学位: 科学博士 国 别: 美国
粉末冶金专家—黄培云4
我国粉末冶金学科的主要创始人之一。
创立了著名的粉末压制理论和烧结理论。研制成 功多种用于核、航天、航空、电子等领域的粉末冶 金材料。
粉末冶金专家—黄培云7
【培训】粉末冶金PPT课件
.
34
粉末特性
成形性 粉末成形的难易度。 测定成形后压粉体之强度或边缘强度。 成形性与粒形、成形压力有关。 烧结性 烧结时希望以较低温度、较短时间,得到高强度、
高密度的烧结原件。 粒度、粒度分布、粒形及表面积,皆会影响烧结
性。
.
35
粉末冶金流程图
粉末的制造 烧结
粉末的预处理 加压成形
.
36
粉末的预处理
.
43
最简单的加压方式:使用圆筒形压模。 石墨作为润滑剂,以减低密度差。
.
44
机械强度
粉体的机械强度主要由粉体相互纠缠所造成。 纠缠度 ,机械强度
.
45
如何增强粉体的强度?
1、增加粉末的表面积。 2、减少粉末的氧化程度及污染。 3、增加压粉体的密度。 4、减少某些添加剂的用量,如石墨的用量。
缺点: 1.粉末不规则状,堆积性差。 2.盐浴的化学性非常敏感,污染物可阻止阴极
生成产物。 3.仅有元素粉末适用。 4.产品须经后续处理及清洗。
.
21
三、雾化制造法
雾化法法提供了大部分的粉末,因为化学性 及形状均可被掌握。
以下介绍气雾法、水雾法。
.
22
气雾法
.
23
气雾法
需加热超越熔融
.
24
.
52
CIP的优点
1、压粉体可获得组织均匀而密度值高的成品。 不会产生扭曲变形的不良现象
2、几合形状不受任何限制。
3、粉粒体和模间无摩擦现象,故形成铁、铜等 软质粉时无须加润滑剂。
.
53
烧结
借着加热使压粉体收缩、致密化之过程称为烧 结。而烧结的物体称为烧结体。
烧结的原因? 在烧结后可使体积收缩、应力松弛、扭度的消 退和表面积的缩减。
粉末冶金概论PPT课件
机械合金化制备的合金粉末具有优异的综合性能,如高硬度、良好的耐磨性和耐腐 蚀性等,广泛应用于航空航天、汽车、能源等领域。
化学共沉淀法
化学共沉淀法是一种制备金属或金属氧化物粉末的常用方法。
电子工业
粉末冶金材料可用于制造电子元件和 集成电路的封装外壳、散热器等。
国防工业
粉末冶金技术对于国防工业至关重要, 用于制造高性能的武器装备和军事器 材。
05
04
航空航天
粉末冶金材料具有高强度、轻量化的 特点,在航空航天领域中广泛应用于 制造飞机和火箭的结构件。
粉末冶金的发展历程
20世纪初
粉末冶金技术开始发展,主要用于制造含油轴承 和硬质合金。
粉末冶金在新能源领域的应用 主要包括风能、太阳能等领域
。
粉末冶金零件如粉末冶金轴承 、粉末冶金齿轮等在风力发电 机组中广泛应用,提高了风能
利用率。
粉末冶金材料在太阳能光伏电 池的制造过程中也发挥了重要 作用,提高了光电转换效率。
随着新能源技术的不断发展, 粉末冶金在高效储能、绿色能 源转换等方面的应用将具有广 阔前景。
在喷雾干燥法中,首先将原料溶液或悬浮液送入雾化器, 在雾化器中经压力或旋转作用形成细小液滴,然后在热空 气中迅速蒸发干燥,得到固体粉末。
喷雾干燥法制备的粉末具有粒度均匀、形状规则、流动性 好等优点,广泛应用于陶瓷、涂料、医药等领域。
热分解法
1
热分解法是一种通过加热分解含有目标产物的化 合物来制备金属或非金属粉末的方法。
05 粉末冶金材料
硬质合金
硬质合金是由硬质相和粘结剂 组成的粉末冶金材料,具有高 硬度、高耐磨性和良好的化学 稳定性。
粉末冶金学课件
粉末冶金学课件1. 粉末冶金学概述粉末冶金学是一种通过冶金方法来制备和加工金属和非金属粉末材料的工艺学科。
它通过将金属或非金属材料粉末冶炼、成形和烧结等工序,制备出具有特定性能和形态的制品。
粉末冶金学具有高效、节能、环保等特点,被广泛应用于各个领域。
2. 粉末制备在粉末冶金学中,粉末的制备是首要步骤。
常见的粉末制备方法包括机械研磨法、化学还原法、物理化学法等。
2.1 机械研磨法机械研磨法是一种通过机械能将块状原料加工为粉末的方法。
常见的机械研磨设备有球磨机、高能球磨机等。
这种方法适用于金属材料和部分非金属材料的制备。
2.2 化学还原法化学还原法是通过反应使原料从溶液中析出成粉末的方法。
常见的化学还原方法有电沉积法、溶胶-凝胶法等。
这种方法适用于某些无法通过机械研磨法制备的材料。
2.3 物理化学法物理化学法是一种通过物理或化学方法控制实验条件,制备粉末的方法。
常见的物理化学方法有气相沉积法、溅射法、激光烧结法等。
这些方法可以制备出高纯度和特殊形态的粉末材料。
3. 粉末成形粉末成形是将粉末材料制备成所需形状的工艺步骤。
常见的粉末成形方法包括压制成形法、注塑成形法等。
3.1 压制成形法压制成形法是一种通过加压将粉末压制成所需形状的方法。
常见的压制成形设备有压力机、挤压机等。
这种方法适用于制备密度较高的金属和非金属制品。
3.2 注塑成形法注塑成形法是一种通过将熔融的粉末注入模具并冷却固化形成制品的方法。
常见的注塑成形设备有注射成型机、挤出机等。
这种方法适用于制备形状复杂、尺寸精确的制品。
4. 粉末烧结粉末烧结是将成形好的粉末制品进行高温处理,使其颗粒相互结合,形成致密材料的工艺步骤。
4.1 烧结机理烧结过程中,粉末颗粒之间发生了多种物理和化学反应。
主要有金属颗粒扩散、晶粒长大、颗粒之间的结合等过程。
通过控制温度、压力、时间等工艺参数,可以控制烧结过程中的颗粒结合和晶粒成长。
4.2 烧结设备常见的粉末烧结设备有热压烧结机、烧结炉等。
- 1、下载文档前请自行甄别文档内容的完整性,平台不提供额外的编辑、内容补充、找答案等附加服务。
- 2、"仅部分预览"的文档,不可在线预览部分如存在完整性等问题,可反馈申请退款(可完整预览的文档不适用该条件!)。
- 3、如文档侵犯您的权益,请联系客服反馈,我们会尽快为您处理(人工客服工作时间:9:00-18:30)。
金属粉末中预先混入少量低温下挥发的有机物粉末或易挥发低熔点金 属粉末,控制一定的压制压力、烧结温度、时间,易挥发金属或有机物 挥发形成孔隙。
5.粉末冶金的优缺点
缺点 1.昂贵的粉末 要控制粉末形状、粒度、粒度分布等。 2.昂贵的模具 要承受更大的压力。 3.压机 吨位要足够大。
制备方法:化学法、物理法及机械法 粉末种类:铁粉、不锈钢粉、低碳钢粉、合金粉、铜粉、铝粉、非金 属粉等 粉末形状:光滑形、不规则形
粉末混合 (mixing)
混合:不同种类的金属或合金粉末与非金属粉末混合 自润滑轴承:铜粉和锡粉混合 多孔材料:金属粉和有机物粉混合 硬质合金:金属粉与碳化物粉
合批:将相同种类而粒度不同的粉末混合
雾化法
雾化:将熔融金属或合金直接破碎成细小液滴,然后冷凝成粉末。始于第 二次世界大战生产铁粉。
方法:二流雾化(水流、气流)、离心雾化、真空雾化、超声波雾化等。 流程:金属→熔化→破碎→液滴→冷凝→粉末 原理:熔融金属借助介质(水、气、离心力、真空、超声波能量)的作用 破碎成液滴,然后凝固成粉末。整个过程只要克服液体金属原子间的结合力 就能把液体金属分散成液滴。相比较而言,机械法要克服固体金属原子间的 结合力。因此,从能量消耗来看,雾化法是一种简便且经济的粉末冶金方法。
7.粉末冶金的发展史
硬质合金(cemented carbides)
时间:20世纪20年代,1925年获得专利 特征:硬度高、耐磨损,作为切割工具、模具或轧辊等 材料:金属碳化物(TiC、TaC、WC)、金属粘结剂 生产方法: WC粉+Co粉→混合→→烧结→硬质合金 烧结温度:1400 ℃; 烧结气氛:氢气 微观结构:粘结剂基体中弥散着碳化物颗粒
借助离心力破碎熔融金属流。
图2-1离心雾化示意图
第一章粉末的制取离心雾化来自式 a. 旋转圆盘:利用机械旋转产生的离心力将金属流击碎成小液滴,然后
冷凝成粉末。制备铁粉、钢粉。 b.旋转坩埚雾化:有一固定电极和一个旋转水冷坩埚,电极和坩埚内的
金属之间产生电弧时金属熔化,在离心力作用下,,熔融金属在坩埚出口 处被破碎成液滴。制备铝合金、钛合金、镍合金粉末。
P.M可生产特殊性能产品,例:高熔点金属、多孔材料、摩擦材料、 磁性或电性能材料;
F.M只能生产普通产品。
4.粉末冶金与熔化冶金的区别
生产工艺不同
P.M工艺 a.传统方法:金属→化学法、物理法、机械法→不同形状、粒度的粉 末→混合→压制→烧结→制品→后处理 b. 先进技术:热固结——压制和烧结同时进行(热压、热挤压、热等 静压、锻压等) F.M工艺 金属→熔炼成锭→轧制、拉伸、挤压、锻压、机加工→线材、棒材、 型材等不同形状、不同性能的产品
2.粉末冶金生产流程
压制成形 (pressing and forming)
定义:将混合均匀的粉末按一定量(体积或质量)装入模具后,用 压力机压制成所希望的形状、尺寸的坯块。
模具:耐高压 压机:吨位大 坯块:各种形状
烧结 (sintering)
定义:把坯块或松装粉末体加热到基本组元熔点以下温度,并在此温 度下保温,从而使粉末颗粒相互粘结在一起,改善其性能,这种热处理 过程叫烧结。
2.化学法(chemical methods) 借助化学作用改变原材料的化学成分而获得粉末的工艺过程;
3.机械法(mechanical methods) 将原材料机械地粉碎而化学成分基本上不发生变化的工艺过程。
制粉原材料:纯金属、合金、有机物、碳化物 选择方法的依据:粉末性能、成本
第一章粉末的制取
7.粉末冶金的发展史
最先进的技术——热固结(hot consolidation) 热固结:压制与烧结结合起来同时进行的一种技术 时间:20世纪40年代后 热固结方法:热压、热等静压、热挤压、热锻等 热固结产品:工具钢、超合金、钛合金等 产品特征:全密产品
第一章粉末的制取
粉末的制取方法
1.物理法(physical methods) 借助物理作用改变原材料的聚集状态而获得粉末的工艺过程;
闭的锥体,交汇于锥顶点,将流经该处的金属流击碎; e.旋涡环形喷射:压缩气体从切想方向进入喷嘴内腔,然后以高速喷
出形成一封闭的锥体,金属流在锥底被击碎。
第一章粉末的制取
图2-5二流雾化形式
第一章粉末的制取
图2-7V形水喷射形式
第一章粉末的制取 (2)二流雾化喷嘴
作用:使雾化介质获得高能量、高速度,稳定雾化效率和雾化过程。
5.粉末冶金的优缺点
优点 1.经济 烧结后制品可直接应用;金属损耗低(1~5%),大规模生产更经济。 2. 可制备其他方法不能生产或虽能生产但很困难的制品 (1)高熔点金属或化合物
5.粉末冶金的优缺点
(2)高纯材料 粉末冶金不熔化材料,在保护气氛或真空中烧结,只要粉末纯度高即
可生产高纯产品。 (3)互不相溶的粉末制品
7.粉末冶金的发展史
结构件(structural parts)
时间:20世纪30年代后期 最早的结构件:油泵齿轮,由铁粉和石墨粉混合烧结而成,基体为共 析合金钢,有25%孔,性能类似于铸铁 结构件种类:铁基零件、低碳钢、不锈钢、铜、青铜、黄铜、镍、 铝、钛、银等 特点:数量大、用途广,自动压制、连续烧结炉烧结 生产方法:传统方法→再加工(浸渍、热锻、淬火和回火、渗碳、渗碳 氮)→结构件
粉末冶金学
Powder Metallurgy
➢ 绪论 ➢ 第一章:粉末的制取 ➢ 第二章:粉末的性能及测定 ➢ 第三章:成形 ➢ 第四章:烧结 ➢ 第五章:粉末冶金材料和制品
➢ 绪论:
1.粉末冶金定义
2.粉末冶金生产流程 3.粉末冶金制品后处理 4.粉末冶金与熔化冶金的区别 5.粉末冶金的优缺点 6.粉末的应用 7.粉末冶金的发展史
第一章粉末的制取 1.二流雾化(水雾化或气雾化)
借助高压水流或气流的冲击来破碎熔融金属流。
图2-2水雾化和气雾化示意图 (a)水雾化;(b)气雾化
第一章粉末的制取
(1)二流雾化形式 a.平行喷射:气流与金属流平行; b.垂直喷射:气流或水流与金属流成垂直方向; c.V 形喷射:气流或水流与金属流成一定角度; d.锥形喷射:气体或水从平均分布在圆周上的小孔喷出,构成一个封
1. 粉末冶金定义
定义:把先制取金属或合金粉末,并将这些粉末装 入模具里加压成形,然后在低于熔点的温度下烧 结固化,即烧结成金属制品或金属坯的制造工艺。
依据:Fusion metallurgy Powder metallurgy
2.粉末冶金生产流程
图1 粉末冶金工艺流程
2.粉末冶金生产流程
制备粉末 (podwer preparation)
3.粉末冶金制品后处理
熔渗(infiltration)
定义:采取一定方法使低熔点金属或合金渗入到多孔烧结制品的孔隙, 以改善制品性能的一种方法。
目的:提高密度、硬度、塑性和韧性。 方法:将小片状低熔点金属或合金放在坯块上,达到一定温度后小片 熔化,然后借毛细管现象渗入到坯块孔隙内,同时与坯块一起烧结。
(7)影响二流雾化粉末性能的因素: a. 雾化介质 气雾化可得球形粉末,水雾化得不规则形粉末,水冷却能力强且廉价,用于
含氧化物的金属或合金,气用于制取易氧化金属或合金粉末。 b. 金属流 金属的表面张力、粘度、过热度及金属流直径; c. 雾化装置 金属流长度、喷射长度、喷射角度。
第一章粉末的制取 2.离心雾化(离心力)
烧结温度:主成分金属熔点的三分之二或 0.7~0.8T(绝对温度) 保护气氛:氮气、碳氢气体等,防止制品氧化或发生反应。
3.粉末冶金制品后处理
再加工(reworking)
定义: 将烧结件再施以大吨位压力加压(精整或整形)。 目的:使制品的加工面和尺寸精度更好。
浸渍(impregnation)
定义:采取一定方法使液态润滑剂或非金属物质或金属渗入到多孔烧 结制品的孔隙内,以提高制品性能的一种方法。 目的:得到耐腐蚀、耐磨损、高密度,能润滑的制品。 方法:将烧结制品与浸渍剂置于高压釜内,在一定温度下施加一定压 力,浸渍剂渗透到制品的孔隙中。
其他方法
电镀、涂层、机加工或蒸气处理。
4.粉末冶金与熔化冶金的区别
Powder metallurgy :P.M; Fusion metallurgy : F.M
产品成分、结构不同
P.M最终产品成分未变,只是粉末固结在一起; F.M最终产品组织结构发生变化,例:开始是两种金属,最后是合金。
产品性能不同
图2-6二流雾化喷嘴结构 α—气流与金属流间的交角;A—喷口与金属流轴间的距离;
D—喷射宽度;P——漏嘴突出喷嘴部分
第一章粉末的制取
(3)气雾化 雾化介质:高压惰性气体 粉末形状:球形
图2-9气雾化粉末形成过程
图2-8气雾化装置
第一章粉末的制取
(4)水雾化 雾化介质:高压水 粉末形状:不规则形 粉末粒度:
6.粉末的应用
直接应用 颜料、油墨、试剂、炸药、燃料、食品添加剂;
结构件 烧结铁基零件、不锈钢零件,烧结铜、铝及其合金零件
特殊材料及制品 多孔、磁性、超导材料,自润滑轴承,金属陶瓷,电极, 石墨电刷,硬质合金
7.粉末冶金的发展史
海绵铁粉(sponge iron) 时间:公元前3000年前,最早的粉末冶金技术,生产的粉 末是海绵铁粉。
高熔点金属( refractory metal)
Mo、Nb、Ti、Ta、Zr 时间:1940年前采用粉末冶金方法,1940年后采用真空电弧、电子束
7.粉末冶金的发展史
自润滑轴承或含油轴承(self-lubricating bearing)
时间:20世纪20年代 特征:孔的体积占轴承体积的15~30%,润滑剂贮存在孔内 材料:90%Cu粉,10%锡粉,无机物粉 生产方法:Cu粉+锡粉+无机物粉→混合→压制成轴承形状→烧结→多 孔轴承→浸渍(油) →含油轴承 与自润滑轴承相关的产品 多孔过滤器、金属电刷(Cu粉和石墨粉)、摩擦材料等。