关于大型预焙电解槽过热度控制的探讨
320KA特大型预焙电解槽生产技术管理探索

320KA特大型预焙电解槽生产技术管理探索时光荏苒,岁月如梭。
自铝电分公司320KA系列电解槽投产至今,已经走过了600多个日日夜夜。
目前,铝电分公司电解槽技术条件稳定,生产状况平稳,经济指标良好,电流效率实现94.72%,生产直流电耗完成13100kwh/T-Al。
这是全体铝电人求真务实、奋发向上、开拓进取、不断探索的结果。
一路上,他们迈着坚实的步伐,踏着辉煌的足迹,走出了一条320KA 特大型预焙铝电解槽生产技术探索的特色之路。
管理创新融入新的观念“变则通,通则达”。
为了充分调动车间基层管理人员的工作积极性和主动性,明确职责,提高管理效率,公司打破行业常规,针对大型预焙槽管理实行专业管理和交叉管理。
专业管理,即专业负责制,就是根据车间生产工艺技术特点,在同行业率先实行电解工技能管理,先后围绕电解技能工、阳极操作工等设置多个班组,并细化分工,明确职责,专业班组专职专责,各司其职,各尽所能。
同时各专业班组实行工作票制度和“一问负责制”。
通过实行专业管理,提高了员工专业知识水平和业务技能,避免了推诿扯皮、踢皮球现象,增强了班组之间的争先创优意识和团结合作意识,大大提高了专业技能操作质量和工作效率。
交叉管理,即工区纵向管理和横班横向管理相结合,就是把车间据槽数纵向划分为工区、依工作时间横向划分为班组,在某一工区的所有人员都归工区长管理,在某一时间段的所有人员都归班长管理。
同时实行横班专责槽负责制,专槽专责,分散了工作量,实现了工区有指标、横班有专责的管理形式。
通过实行交叉管理,使工区管理纵向到底,横班管理横向到边,排除了死角和盲区,实现了双向管理,取得了双重效果。
技术创新实现质的跨越一年多来,在借鉴同行业先进经验的基础上,铝电分公司结合生产和管理的实际,大胆实践,不断探索,终于形成了一套适合自己的独具特色的管理思路。
第一,认识生产曲线,更新管理观念投产初期,由于刚刚接触大型槽管理,对生产曲线认识不深、关注不足,对用计算机生产曲线分析、判断槽况感觉无从下手。
浅谈300kA预焙电解槽的技术优化控制

铝电解专业技术总结考生姓名: xxxx申报职业(工种): xxxxx申报级别: xxxx浅谈300kA预焙电解槽的技术优化控制摘要: 本文分别从300kA电解槽对其焙烧启动、后期管理及正常生产期的参数控制及优化进行了阐述。
焙烧启动阶段采用焦粒焙烧,通过合理控制各项技术指标,焙烧启动阶段顺利进行。
后期管理阶段主要是根据迅速降电压的指导思想,对各项技术参数的调整进行了合理尝试,取得了较好的效果。
正常生产期通过提高氧化铝浓度控制精度和技术管理创新,降低了电解槽炉底压降和阳极效应系数,各种能耗明显降低,电解槽稳定性增强,提高了电流效率。
关键词: 铝电解槽焙烧启动后期管理技术优化受世界金融危机冲击,有色金属国内外市场需求萎缩,价格暴跌,铝价也随之大幅下跌,电解铝企业的生存面临着前所未有的威胁,加之国内节能降耗的大趋势要求,降低生产成本已成为刻不容缓的问题。
鸿骏铝业300KA电解系列通过对技术管理创新和新技术的运用,逐步摸索出了低电压下,电解槽稳定高效运行的方法,各种能耗明显降低。
1.焙烧启动管理鸿骏铝业300KA电解槽256台电解槽采用的是沈阳铝镁设计院设计的电解槽,公司通过对启动及后期管理的摸索,探索出了一套合理技术管理思路,取得了较好的成绩。
1.1 焙烧过程管理我公司300KA电解槽采用的是焦粒加石墨焙烧,无效应湿法启动。
焦粒与石墨的配比采用的是8:2,角部采用7:3,铺设厚度为2cm,焦粒与石墨碎的粒度要求为0.2cm~0.4cm。
装槽料有所改变,把边部冰晶石用电解质破碎块替代,达到减缓热冲击的目的,极间缝不装物料、中缝添加电解质块达到加强热对流的效果,使电解槽各部位升温平衡。
焙烧时间控制在120h以上,温升梯度则按表1进行控制,在此温升梯度条件下,使阴极内衬充分焙烧焦化,避免温差过大造成阴极表面和内部裂纹的产生, 防止电解槽早期破损槽的产生。
表1 各阶段温升梯度控制温度控制范围/℃所处阶段温度提升速度/℃·h- 1温升梯度/℃· h- 1≤200软化阶段主要排出水分15左右10~13 200~700挥发分大量排出的阶段5 7~10>700粘结剂的焦化过程基本结束10~15 9~12在实际生产过程中,为了避免电流分布不匀对电解槽寿命产生影响,就要求从焦粒粒度选择、焦粒配比、铺设厚度、座极、拆除分流片等方面入手进行严格把关,同时在焙烧期间要按照公司制度对阳极电流分布进行测量,并对偏差过大的阳极电流进行调整。
400KA铝电解槽焙烧及启动关键控制点浅析
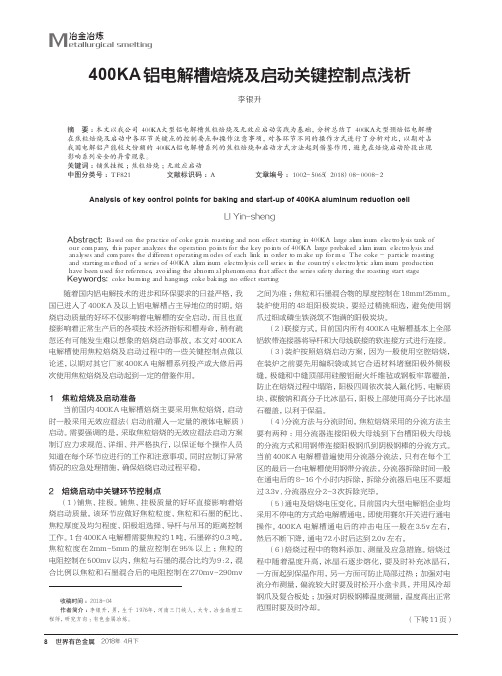
冶金冶炼M etallurgical smelting400KA铝电解槽焙烧及启动关键控制点浅析李银升(陕西有色榆林新材料有限责任公司铝业分公司,陕西 榆林 719099)摘 要:本文以我公司400KA大型铝电解槽焦粒焙烧及无效应启动实践为基础,分析总结了400KA大型预焙铝电解槽在焦粒焙烧及启动中各环节关键点的控制要点和操作注意事项,对各环节不同的操作方式进行了分析对比,以期对占我国电解铝产能较大份额的400KA铝电解槽系列的焦粒焙烧和启动方式方法起到借鉴作用,避免在焙烧启动阶段出现影响系列安全的异常现象。
关键词:铺焦挂极;焦粒焙烧;无效应启动中图分类号:TF821 文献标识码:A 文章编号:1002-5065(2018)08-0008-2Analysis of key control points for baking and start-up of 400KA aluminum reduction cellLI Yin-sheng(Shaanxi nonferrous metals Yulin New Material Co., Ltd. aluminum branch, Yulin 719099,China)Abstract: Based on the practice of coke grain roasting and non effect starting in 400KA large aluminum electrolysis tank of our company, this paper analyzes the operation points for the key points of 400KA large prebaked aluminum electrolysis and analyses and compares the different operating modes of each link in order to make up for me. The coke - particle roasting and starting method of a series of 400KA aluminum electrolysis cell series in the country's electrolytic aluminum production have been used for reference, avoiding the abnormal phenomena that affect the series safety during the roasting start stage.Keywords: coke burning and hanging; coke baking; no effect starting随着国内铝电解技术的进步和环保要求的日益严格,我国已进入了400KA及以上铝电解槽占主导地位的时期。
对350kA铝电解槽焙烧控制的思考与探索

对 3 5 0 k A铝 电 解 槽 焙 烧 控 制 的 思 考 与 探 索
张 宁
( 国家 电投 宁夏 能源 铝业 青铜 峡铝 业 分 公 司 3 5 0 k A电解 车 间 , 宁夏 银川 7 5 0 0 0 4)
摘
要 : 对 于铝 电解 槽 焙 烧控 制 系统 的 开 发 , 在 满足 焙 烧 过 程控 制精 度 的 同时 , 还 可 以不 断 的 延 长 铝 电解 槽 的 寿命 ,
耗 能指 标以及 使用 效率 等产 生直接 的影 响 ,其本 身也 是进行
铝 电解 生产的一个重要环节 ,需要注重其 合理 的控 制。
1 3 5 0KA铝 电解槽工 艺要求
第一 ,确保 合理 的设 定电压 以及稳 定 的电流 强度 ,这是
最基 础 的能 量平衡 要求 。第二 ,保证 稳定 的保温 料厚 度 、铝 液水 平 以及规 整 的炉膛 内型 。第三 ,确保 电解质 水平 、电解 质温 度 、规整稳 定炉 膛等 ,才能满 足高 效低耗 以及 电解 生产 平稳 运行 的要 求 。第 四 。满 足阳 极效 应系数 要求 ,能 够正 确
第一 ,两台铝 电解槽 的温 度在升 高环 节的波 动较 大 ,会 有反复 ,尤其是在焙烧 7 2小 时前会直接被拆 除分流器所影 响。 第二 ,第 二个 阶段的 升温 速度较 快 ,并 且最大 升温速 度 达到 3 5 . 5 0 ( 2 / h以及 5 5 . 5 0 ( 2 / h,对于焙烧质量 有较大 的影响 。 第三 ,进 入第三 阶段 之后 ,温度升 高 的速度减 缓 ,延 长 焙烧 时 间,且在焙烧 末期 呈现 温度下 降的趋 势 ,影 响铝 电解
对 于 节能 减 排 有 着 直接 的 意 义 。 所以, 本 文在 阐述 3 5 0 k A铝 电解 槽 工 艺要 求 的 基 础 上 , 通过 3 5 ( ) k A铝 电解 槽 焦床 焙烧 温度 控制 。 希 望 可以 对铝 电解 的 生产 流程 焙 烧 有 更加 全 面的认 识 和 了解 。
铝电解槽温度控制方法与优化
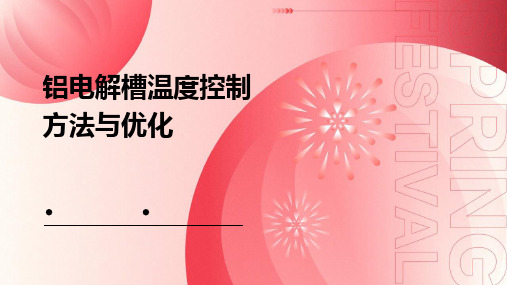
增强材料保温性能
选用保温性能更好的材料 ,降低热量散失,保持温 度稳定。
提高材料耐腐蚀性
选用耐腐蚀性能更好的材 料,提高电解槽的使用寿 命。
引入智能温度控制系统
实时监测温度
01
通过安装温度传感器,实时监测电解槽温度,为控制策略提供
数据支持。
智能调控算法
温度数据自动调整控制参
新型热管技术在铝电解槽中的应用案例
总结词
新型散热技术
详细描述
新型热管技术在铝电解槽中的应用,有效解 决了传统散热方式存在的问题,提高了电解 槽的散热性能和稳定性,进一步提高了铝产 品的质量和产量。
感谢观看
THANKS
02
铝电解槽温度控制方法
直接冷却法
直接冷却法是通过在电解槽周围设置冷却设备,如风扇或水 冷系统,直接将热量从电解槽带走。这种方法降温效果明显 ,但需要大量的冷却介质和能源。
直接冷却法适用于大型电解槽,可以快速降低槽温,但需要 定期维护和清洗冷却设备,以防止堵塞和腐蚀。
间接冷却法
间接冷却法是通过在电解槽的侧壁或底部设置热交换器, 利用循环冷却水或其他冷却介质带走热量。这种方法结构 简单,易于维护,但降温效果不如直接冷却法。
高效能冷却技术还可以通过优化冷却水流量、温度和压力等参数,实现对铝电解槽温度的精确控制, 减少能源浪费和环境污染。
新型热管技术的研发
热管技术是一种高效的传热技术,通过热管 将热量快速传递并分散,实现对铝电解槽温 度的有效控制。新型热管技术正在研发中, 以提高传热效率和降低能耗为目标。
新型热管技术可以应用于铝电解槽的冷却系 统,通过优化热管的设计和布局,提高冷却 效果和降低能耗,为铝电解槽温度控制提供
数,实现快速响应和精确控制。
浅谈我国大中型铝电解槽热损失分布特点

浅谈我国大中型铝电解槽热损失分布特点本文由全球铝业网 () 编辑,转载请注明出处,十分感谢!1 概述铝电解槽热损失分布是槽工况表现的重要特征,通过铝电解槽热损失分布测量、计算和分析,区域能量分布特征、工艺技术条件和加工操作制度合理性进行定量分析和科学评估,为提高铝电解生产主要技术经济指示而采取有针对性的技改措施提供科学依据。
现阶段,我国铝电解槽槽型有很多种,本文主要讨论我国200KA至300KA级大中型铝电解槽的散热特点。
2 电解槽热损失测量方法电解槽热平衡体系选取铝电解槽和环境之间形成的封闭物理界面,即槽顶-槽罩-槽壳-槽底,包括界面上参与传热的筋板和摇篮架,热流计算以单位时间传输的电功千瓦(Kw)为单位。
为了准确测量铝电解槽体系散热损失,需要在槽体系表面上,按照经-纬线划分虚拟区域,布置测点。
按纬度方向将阴极槽壳侧部表面划分成熔体区(电解质+铝液)、阴极碳块区和耐火保温区,以摇篮架为经线形成测点区域。
对于槽罩、槽底和槽顶采用同样的方法进行区域划分和布点测量。
此外,测点还包括凸出或露出体系表面的摇篮架、阳极导杆、阴极钢棒以及槽沿板等散热部件。
根据测得的热流密度和测点区域面积,可以计算槽体系表面散热损失;根据测得的烟气流量和温度,可以计算烟气通过烟道带走的热量。
3 我国大中型预焙铝电解槽散热基本特点3.1 基本特点近两年来,通过对我国20多家铝厂电解槽的热平衡测量得知,我国大中型预焙铝电解槽散热损失具有如下两个显着特点:(1)我国大中型预焙铝电解槽热损失相当2.0V左右,与10年前相比,热损失降幅有200mV 左右。
(2)现阶段我国大中型铝电解槽热损失上下两部分的比例为55.0%和45.0%。
如图所示。
与过去自焙槽热损失的上下比例50.0%和50.0%相比略有不同,造成差异的主要原因在于,自焙槽的阴极炭块较薄(400cm)左右,阴极钢棒一般为方钢,伸出槽壳较长(40cm左右),因而阴极钢棒散热所占比例较大(7%左右)。
电解槽过热度交流材料

电解槽过热度交流材料
在电解槽过热度交流材料中,我们将讨论电解槽过热现象及其相关影响。
电解槽过热是指电解槽中的电解质溶液温度超过了正常的工作温度范围。
通常情况下,电解槽运行时会产生一定的热量,但过热意味着热量无法有效地散发出去,导致温度升高。
过热度会对电解槽的稳定性和效率产生负面影响。
首先,过热会导致电解质的蒸发,减少了电解槽中的溶液量,从而降低了电解槽的电导率。
其次,过热会引发电极表面的气泡产生,这些气泡会附着在电极上,形成电解质的非均匀分布,影响了电解反应的进行。
此外,过热还可能导致电解槽结构变形,破坏设备的正常运作。
为了解决电解槽过热问题,可以采取以下措施。
首先,可以增加电解槽的散热面积,提高散热效率。
这可以通过在电解槽外部增加冷却装置或优化电解槽的设计来实现。
其次,可以控制电解槽的电流密度,避免过载运行。
此外,可以适量添加一些抑制过热的添加剂,例如表面活性剂和防腐剂,来提高电解槽的稳定性。
综上所述,电解槽过热度是一个需要关注的问题,对电解槽的稳定运行和效率具有重要影响。
通过合理的措施和设计,我们可以有效地控制电解槽的温度,确保其正常运行。
浅析电解质过热度与铝电解生产的关系及技术控制思路

浅析电解质过热度与铝电解生产的关系及技术控制思路作者:杨仲生来源:《中国科技博览》2015年第09期[摘要]本文阐述了电解质过热度在铝电解生产中的重要作用,分析了电解质过热度与电解槽炉帮及电解生产中电流效率的关系,同时结合我厂实际生产情况,提出了电解质过热度的技术控制思路,进一步提高铝电解槽的电流效率,降低能耗,提高大型预焙槽炼铝的能量利用率。
[关键词]铝电解槽;电解质过热度;电流效率;物料平衡;能量平衡中图分类号:TF82 文献标识码:A 文章编号:1009-914X(2015)09-0297-021 前言电解质过热度是铝电解体系的一个重要性质,它与电解槽电解质温度有直接的关系。
铝电解生产过程中,电解质的成分,对铝电解生产的各项经济技术指标有重要的影响。
电解质过热度是电解质温度与电解质初晶温度之差,我厂过热度一般控制在10~15度左右,一直以来我们对过热度的控制并没有引起足够的重视。
Solheim的最新研究指出,较低的过热度可以在铝阴极表面沉积一层冰晶石壳膜,因而可阻止铝的溶解损失,提高电解槽的电流效率。
然而过热度太低时也会引起过多的冰晶石沉积和沉淀,而导致电解槽的不稳定,最佳的过热度的大小应与电解质的分子比、电解质初晶温度有关。
分子比较低时,需要适当提高一点过热度,因为在此时,电解质的初晶温度的变化受电解质分子比变化的影响较大。
2 电解质过热度与铝电解生产的关系2.1 电解质过热度与电解槽炉帮厚度的关系电解质过热度控制着边部炉帮和炉底结壳的形成,电解槽边部碳块和氮化硅结合碳化硅砖必须有一层侧部炉帮保护,以避免电解质的腐蚀(如图1).为了形成炉帮,必须有足够的热量从槽侧部散失掉,从而使侧部的液-固两相界面的温度降到凝固点温度,以使炉帮变厚 X:Q=hAΔT;X=KA(Tl-Ts-QRw)/Q上式中Q表示散失的热量;h表示热传递系数;A表示界面面积;ΔT表示过热度;K表示凝固电解质的传递热;Tl表示炉帮表面温度(初晶温度);Ts表示槽壳表面温度;Rw 表示槽壳表面的热阻(Rw=Rs+Rl+Rc),如图2。
- 1、下载文档前请自行甄别文档内容的完整性,平台不提供额外的编辑、内容补充、找答案等附加服务。
- 2、"仅部分预览"的文档,不可在线预览部分如存在完整性等问题,可反馈申请退款(可完整预览的文档不适用该条件!)。
- 3、如文档侵犯您的权益,请联系客服反馈,我们会尽快为您处理(人工客服工作时间:9:00-18:30)。
关于大型预焙电解槽过热度控制的探讨摘要:在国际上,有的电解工作者提出了对铝电解槽的过热度的控制,而且取得了不错的效果,国外许多先进铝厂电解槽过热度控制在8—10℃,效率达到95%以上,而我国对过热度的控制还不够重视,一般控制在15—20℃,本文针对过热度控制的要点,详细控讨了怎么样通过调整物料平衡和热平衡控制好过热度。
关键词:过热度初晶温度电解质成分极距热平衡物料平衡一、我国工艺技术控制现状从我国引进日轻160KA大型电解槽后,逐步开发了“四低一高”的铝电解生产工艺制度,并为现代电解槽工艺技术管理所广泛采用。
“四低一高”也就是低电解温度,低分子比,低AE系数、低氧化铝浓度,高极距。
随着电解槽设计软件的不断开发更新,电解槽的磁场设计得到了很好的改善,所以现在也有“五低一高”的理论,也就是低电解温度、低分子比、低AE系数、低氧化铝浓度和低铝水平,高极距。
无论“四低一高”还是“五低一高”工艺制度,都是要求用尽可能低的电解温度实现的高的电流效率。
低温电解一直指导着我们的生产,有些文献报道,电解温度每降低10℃,可使电流效率提高1%~2%。
实验研究表明,降低电解温度会使电流效率连续升高,然而,过低的电解温度容易在槽底产生沉淀和造成槽膛不规整,易引发槽子不稳定,从而影响电流效率,造成能耗的增加。
而且从目前的电解质体系来说,要想达到低温电解且保持电解过程稳定高效进行,还有待改善电解质成分,不断优化电解质体系。
二、过热度控制的提出国际著名的铝冶金专家Haupin对大量的电流效率数据的统计分析表明[1],电解槽的电流效率更依赖于过热度,而不是电解质温度。
在国际上,有的电解工作者提出了对过热度的控制,国外有的大型电解槽过热度控制在8—10度,而且取得了不错的效果。
过热度是电解质温度与电解质初晶温度之差,我国一般控制在15—20度左右,一直以来我们对过热度的控制并没有引起足够的重视。
下表是法国彼斯涅电解槽的一些技术数据情况统计表:从上表可以看出,尽管电解质的初晶温度高,但只要控制好电解质的过热度,仍能得到很高的电流效率,这也是我们提出对电解质过热度控制的原因,从电解发展情况来说,以后控制好电解质的过热度,可能会是电解槽大幅提高电流效率的突破点。
三、最佳过热度的机理Solheim研究指出[1],较低的过热度可以在铝阴极表面沉积一层冰晶石壳膜,因而可阻止铝的溶解损失,提高电解槽的电流效率。
然而过热度太低时也会引起过多的冰晶石沉积和沉淀,而导致电解槽的不稳定,最佳的过热度的大小应与电解质的分子比、电解质初晶温度有关。
分子比较低时,需要适当提高一点过热度,因为在此时,电解质的初晶温度的变化受电解质分子比变化的影响较大。
四、过热度的控制方法过热度的控制,主要是要控制好电解槽物料平衡和热平衡。
物料平衡也就是要做好电解质成分的调整,控制好电解质的初晶温度;做好电解槽的热平衡也就是控制好极距(热收入)和控制好热量的损失。
a、控制好电解质成分电解温度的高低对电流效率和电能消耗有很大影响,而电解质的初晶温度随其成分变化而变化,影响电解质初晶温度较大的成分有分子比、氧化铝和氟化钙等。
1、分子比的影响冰晶石是电解质中主要成分,中性冰晶石其熔点为1008℃,但在工业生产中,我们都采用酸性电解质进行生产,下面是含有8%Al2O3,4—6%CaF2的电解质[2]其初晶温度和分子比的变化情况:从上表可以看出,分子比降低,其初晶温度也相应的降低,但分子比愈低,氧化铝的熔解度也相应降低,使槽内产生大量沉淀,影响电解正常生产。
2、氧化铝浓度的影响氧化铝熔点为2050℃,但当氧化铝熔解在冰晶石熔体中,不但不增加电解质的熔点,反而使熔点降低。
据实验证明[2]:当冰晶石中熔解有4.8%(重量)的氧化铝时,其熔点为938℃,在分子比2.4—2.6,4-6%CaF2的电解质体系中,当含有8% Al2O3时,其熔点为940-950℃,当Al2O3含量降到5%时,初晶温度为955-960℃,当Al2O3含量降到1.3-2%时,初晶温度为970-975℃。
3、 CaF2含量的影响随着CaF2的增加,电解质的初晶温度降低,但工业上只在通电装炉时加上适量CaF2,正常生产一般不添加,因为构成电解质的原料和氧化铝中都含有CaO 杂质,CaO 在电解过程中与冰晶石作用生成CaF2,所以在工业电解质中并不添加CaF2,也能保持电解过程中CaF2的稳定。
总的来说,电解质的初晶温度随分子比的降低而降低,随氧化铝浓度的降低而增加,随氟化钙的增加而降低;而氟化钙的一般不作添加,槽内氟化钙含量较稳定,其含量主要受原材料影响,对电解质的初晶温度影响也较小。
那么对电解质初晶温度的影响最大的可能就是AlF 3和Al 2O 3了。
近年来,随着科技的发展,我国自行开发出了测量电解质初晶温度的仪器,某电解厂对电解质的初晶温度做了详细的测量[3]:9209309409509609701.1 1.12 1.14 1.16 1.181.2 1.22 1.24 1.26分子比初晶温度图1、分子比和初晶温度散点关系图从图1可以看出,相同的分子比值,其初晶温度也有很大的差别,分子比与初晶温度的线性不明显。
我们对同一分子比的数值进行平均后得到图2:9259309359409459509559601.12 1.13 1.14 1.15 1.161.17 1.18 1.19 1.2 1.21分子比初晶温度图2、分子比与初晶温度趋势图通过图2我们可以看出,电解质的初晶温度还是按分子比降低初晶温度降低的规律在变化,随分子比的升高而升高,随分子比的降低而降低。
940942944946948950952954135791113151719212325272931333537394143图3、Al2O3过欠加工与初晶温度趋势图从图3可以看出,在过量加工时,电解质的初晶温度呈下降趋势,欠量加工时,初晶温度逐步上升,在下一个过量加工期内电解质的初晶温度又呈下降趋势。
至于为什么会出现同一分子比值初晶温度相差过大,结合图1、图2、图3可以得出:初晶温度的影响受AlF3和Al 2O 3的添加影响很大,现在大型预焙槽都采用AlF3和Al 2O 3自动下料系统,AlF3和Al 2O 3的加料制度对电解质的初晶温度影响很大,当AlF3和Al 2O 3下料时,电解质中的AlF3和Al 2O 3量增加,初晶温度降低;随着物料不断的消耗和挥发,电解质中的Al 2O 3和AlF3量减少,初晶温度升高。
也就是说电解槽的下料加工制度,使电解质中的AlF3和Al 2O 3浓度在一个范围内变化,从而使初晶温度的保持也是一种动态的相对变化,在加料制度不变的情况下,其变化范围应是相对稳定的。
这就造成同一分子比时初晶温度有所不同。
另外不同电解槽的电解质成分不同、电解质质量不一样,即使在分子比相同时,初晶温度也会有所不同,这也可能也是造成图1这种现象的原因之一。
b 、热平衡的控制在加工下料制度不变的情况下,电解质成分相对稳定,初晶温度相对稳定的情况下,控制好过热度的高低,主要取决于电解槽热平衡,也就是说热收入和热损失决定着过热度的高低。
1、 热损失控制要减少电解槽的热损失量,可以增大槽底部和阴极钢棒导出部位的保温能力,加强槽面特别是阳极碳块上的保温。
图4、槽面氧化铝覆盖层厚度对热损失量的影响槽底的保温性能与槽底的保温结构有关,这是电解槽的设计因素,8.817.626.435.24452.8510152025氧化铝覆盖层厚度/cm单位面积热损失量/M J .(m 2.h )-1而在生产中,我们一般通过调整阳极上氧化铝保温料的厚度来减少热损失,从图4可以看出[4],随着氧化铝保温料厚度的增加,电解槽的热损失大大的减少。
工业上在正常生产电解槽上,阳极上保温料厚度一般保持在18—20cm左右,只要管理到位,这部分对过热度的影响应该能尽量减小。
2、热收入控制热散失和电解槽设计以及日常生产作业管理有很大的关系,而电解温度的高低又很大程度上取决于热收入的高低,也就是说电解温度的高低,极距的高低起着决定性的作用。
在电流恒定的情况下,极距越高,则电解槽的热收入就越多,我们通过调节极距来调整电解槽的热收入,从而达到对过热度的控制。
以前四低一高理论认为,电解生产的极距尽可能的高,高的极距才有高的电流效率,但在生产中发现,极距对电流效率的影响,只有在极距较低时才较明显,而在极距超过一定的限度后,虽然极距增大,但电流效率提高不多。
所以我们在对极距的控制上要尽量控制在电流效率高且极距达到过热度控制要求的位置为宜,以免能耗的增加。
通过控制电解槽的物料平衡和热平衡,从而实现对过热度的控制。
电解槽的物料平衡可以通过对电解质成分也就是Al2O3和AlF3的合理加料制度来实现;电解槽的热平衡是通过凋整电解槽的极距也就是能量输入以及减少热散失来实现。
但是对铝电解槽来说,热平衡和物料平衡是相互关联,相互配合的。
电解槽中物料添加时使电解质的初晶温度降低,过热度升高。
过热度增加又导致槽侧部的散热量增加,影响到热平衡,使槽帮结壳及伸腿熔化,AlF3的浓度降低。
如果极距增加,输入到电解槽中的能量就会增加,直接的影响就是使电解质的温度增加和过热度增加。
电解质温度增加时,也会使沉淀和槽帮结壳熔化,电解质的初晶温度上升,这反过来又使过热度降低。
所以我们在控制时要综合的考虑。
五、结语(1)要控制较好的过热度,就要控制好分子比,做好AlF3的添加;(2)要控制较好的过热度,要制定科学合理的Al2O3下料制度;(3)要控制较好的过热度,要做好电解槽的保温,减少热损失量;(4)要控制较好的过热度,就要保持合理的极距,调整好电解槽的热收入。
参考文献:[1]冯乃祥,彭建平.再谈我国铝电解技术与国际先进水平的差别兼论铝电解生产中的新技术[2]铝电解,贵州铝厂职业教育学院内部教材.1998[3]秦卫中,铝电解生产中电解质初晶温度变化分析。
第五届铝电解专业委员会2005年学术交流会论文集,2005.9[4]邱竹贤,预焙槽炼铝[M](第三版).冶金工业出版社.2005。